
11 minute read
Design professionals urged to join SASFA
Industry association, the Southern African Light Steel Frame Association (SASFA) argues that by joining its ranks, architects, engineers and design professionals may tap into the growing light steel frame building (LSFB) knowledge base and market, staying abreast of new trends and technologies in a very affordable and practical way. SASFA is a member association of the South African Institute of Steel Construction (SAISC). SASFA was established in 2006 by interested parties as an industry representative association.
Southern African Light Steel Frame Association
John Barnard, Director of SASFA.
‘P rofessionals in the industry - from building and construction contractors and sub-contractors to designers, power tool manufacturers, architects and engineers - find value in SASFA membership, in what is undeniably a challenging time of economic constraint and change for the construction, steel and building sectors locally. The active demand for LSFB in South Africa is one of the most exciting developments in recent times,’ says John Barnard, Director of SASFA.
‘While this method of building has been used in the United States, Europe and Australia for decades, it was only relatively recently introduced to our shores. The speed of construction, accuracy, excellent thermal properties, logistical cost advantages and design flexibility are all factors which have made LSFB the building method of choice for a growing number of construction projects.
‘Today, the Association embodies the collective wisdom of its members and serves as a valuable reservoir of knowledge for professionals and practitioners in the industry. SASFA’s management of codes and standards, its strategically neutral and advocacy role as an industry voice across many construction-related industries
Milestones achieved
The Association has achieved many significant milestones since inception. For example, it has drafted the SASFA Building Code for LSFB in South Africa and taken the Code through the South African Bureau of Standards (SABS) certification process, to form the national code SANS517 for Light steel frame building. SASFA also obtained acceptance of LSFB from the South African banks for bonding of LSF houses; and acceptance from the NHBRC for enrolment. The Association has arranged awareness-raising seminars in the major centres of South Africa, involving several overseas speakers and obtained representation on the relevant SABS committees.
Membership options
The following categories of membership ar e available to members of industry wishing to join SASFA:: • Major material suppliers to the light steel frame building industry • Other material suppliers to the light steel frame building industry • Manufacturers of light steel frame building systems, and light steel trusses • Designers (architects, engineers, quantity surveyors) • Merchants and service centres • Erectors and builders • Student Associate members (building authorities, educational institutions, other associations) BUILDING SYSTEMS STEEL FRAMING
and authorities, and its training programmes are unsurpassed,’ says Barnard.
The Institute’s and SASFA’s library and databases of companies and people associated with the industry are readily available to members, as is its up-to-date technical advice and specification changes relating to LSFB.
SASFA also offers members training courses on demand, to further develop the skills available to the LSFB industry. In addition, membership serves as a form of certification which is deemed useful by finance providers, building authorities and the National Home Builders Registration Council (NHBRC).
‘The Association forms a strong vehicle for advocacy, education, and professional networking. Listing on SASFA’s website boosts members’ exposure online and generates referrals. Furthermore, members have the opportunity to network with clients and professionals through access to all SASFA events,’ Barnard advises.
SASFA www.sasfa.co.za
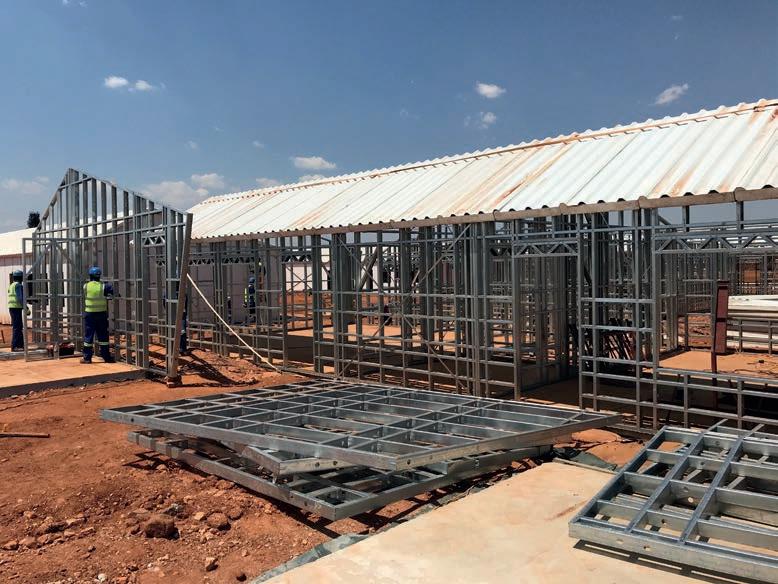
SAISC Steel Awards winner in LFSB category, Protea Glen School.
70 ADVERTORIAL CROMMELIN WATERPROOFING & SEALING
Making asbestos safe – in-place encapsulation
Asbestos surfaces undergo a weathering process after ma of exposure and a loose surface layer develops which, becomes colonized with dark coloured lichen. The lic the cement causing exposure of the asbestos fibres. Th becomes unstable, the asbestos sheeting is weakened and the darkened colour causes a substantial increase in roof temperatures. The traditional process for coating asbestos roofs was to clean the roof with high-pressure water to rem and loose asbestos fibres. This procedure was eventually ban health grounds, creating a need for a system that could straight to the degraded asbestos without disturbing the su
So, what’s the big deal with asbestos? It’s a naturally occurring silicate and handy reinforcing material commonly used in asbestos sheeting. Here’s the problem: weathering erodes the cement, The unstable nature of weathered asbestos surfaces i some concern in the community and the Fibroseal System been developed to minimise the danger of hazardous fibres and provides an attractive durable finish.


releasing asbestos fibres. Older industrial buildings where such roofing is predominant, and those along the coast, are more susceptible where chemical fallout or sea air speeds the process along. E nter asbestosis, a dreaded lung disease caused by inhaling asbestos particles, resulting in severe fibrosis which can lead to cancer of the pleura. It’s these hazardous airborne fibres that are the primary concern presenting critical health risks and the reason why asbestos has become such a hot topic.
The preferred method of dealing with asbestos sheeting is to encapsulate it, effectively nullifying the erosion process and extending the roof’s lifespan. Crommelin Fibroseal is the leading solution for in-place encapsulation of asbestos sheeting using a direct painton application. Crommelin’ s specialised training equips contractors to apply the product, ensuring certified application from start to finish.
It meets the highest international standards of approval and Crommelin Fibroseal strictly adheres to the Australian Paint Application Scheme, specifically “APAS 1702” as follows:
Crommelin Fibroseal Primer is applied directly to the untreated asbestos sheeting requiring no initial preparation, fully penetrating through any moss and lichen, binding the encapsulated material to form a single solid material. It prevents any regrowth and renders the coated surface non-friable. It can be re-coated and requires no maintenance to retain this integrity for five years. Annual inspections can be carried out for a nominal fee of R3 000 a year.
The Crommelin Fibroseal Topcoat system adheres to the stabilised surface, providing UV protection and maintaining an effective finish that requires no further treatment for five years. binds and encapsulates asbestos fibres and eliminates costly downtime. Furthermore, it reduces in-roof cavity temperatures significantly, resulting in savings on cooling costs.
It is water-based with low volatile organic compounds, making the product environmentally-friendly and extending the service life of asbestos structures. It’s also far cheaper and quicker than the costly process of removing and replacing asbestos sheeting. All round, we present great savings. Crommelin Fibroseal asbestos sheeting encapsulation stops any further risk of asbestos fibre fallout in its tracks. In adhering to the highest of international standards, it presents the most cost-effective solution to the question: ‘What can I do with my hazardous asbestos roof?’
Crommelin Fibroseal, make the right choice today. Lichen Loose Asbestos Fibres & Air Asbestos Base Fibroseal Primer Lichen Loose Asbestos Fibres & Air Asbestos Base Over 25 years ago, Crommelin addressed this proble developed the Fibroseal System to achieve the foll • The binding and encapsulation of asbestos fibres. • Avoiding costly downtime associated with replacement of asbestos roofs. • A significant reduction in roof cavity temperatures resulting in savings in building cooling costs. • An extension of the service life of asbestos structures. • A completely water based and truly environmentally friendly system. • Provides a rejuvinated appearance in a range of decorative colours. Through extensive research and development, Crommelin developed Fibroseal Primer. The primer soaks through the l and degraded asbestos down to the sound base mater the se unstable elements. Fibroseal Topcoat is then applied to the primed surfac provide a durable, decorative, UV resistant protective Active ingredients in Fibroseal Topcoat also resist th moss and lichen. The Fibroseal System has been specified and used extensively throughout Australia for over 25 years in areas such as government, local councils, commercial industry and schools etc. Project certification and references are available upon request. The Solution The System Before After
93 Westview Drive, Mill Park
Let’s talk economics In most cases, it’s only the side exposed to the weather that needs treatment. Crommelin Fibroseal has been developed through extensive research and development and successfully implemented for decades. It effectively
Crommelin Waterproofing & Sealing +27 728325682 stewart@crommelin.co.za
FibrosealFibroseal
The ProblemThe Problem
Asbestos surfaces undergo a weathering process after many years of exposure and a loose surface layer develops which, on roofs, becomes colonized with dark coloured lichen. The lichen attacks the cement causing exposure of the asbestos fibres. The surface becomes unstable, the asbestos sheeting is weakened and the darkened colour causes a substantial increase in roof cavity temperatures. The traditional process for coating asbestos roofs was to clean the roof with high-pressure water to remove all lichen and loose asbestos fibres. This procedure was eventually banned on health grounds, creating a need for a system that could be applied straight to the degraded asbestos without disturbing the surface. Asbestos surfaces undergo a weathering process after many years of exposure and a loose surface layer develops which, on roofs, becomes colonized with dark coloured lichen. The lichen attacks the cement causing exposure of the asbestos fibres. The surface becomes unstable, the asbestos sheeting is weakened and the darkened colour causes a substantial increase in roof cavity temperatures. The traditional process for coating asbestos roofs was to clean the roof with high-pressure water to remove all lichen and loose asbestos fibres. This procedure was eventually banned on health grounds, creating a need for a system that could be applied straight to the degraded asbestos without disturbing the surface.
The unstable nature of weathered asbestos surfaces is a cause of some concern in the community and the Fibroseal System has been developed to minimise the danger of hazardous airborne fibres and provides an attractive durable finish. The unstable nature of weathered asbestos surfaces is a cause of some concern in the community and the Fibroseal System has been developed to minimise the danger of hazardous airborne fibres and provides an attractive durable finish.
The SolutionThe Solution


Lichen Loose Asbestos Fibres & Air Asbestos Base Over 25 years ago, Crommelin addressed this problem and developed the Fibroseal System to achieve the following: • The binding and encapsulation of asbestos fibres. • Avoiding costly downtime associated with replacement of asbestos roofs. • A significant reduction in roof cavity temperatures resulting in savings in building cooling costs. • An extension of the service life of asbestos structures. • A completely water based and truly environmentally friendly system. • Provides a rejuvinated appearance in a range of decorative colours. Lichen Loose Asbestos Fibres & Air Asbestos Base Over 25 years ago, Crommelin addressed this problem and developed the Fibroseal System to achieve the following: • The binding and encapsulation of asbestos fibres. • Avoiding costly downtime associated with replacement of asbestos roofs. • A significant reduction in roof cavity temperatures resulting in savings in building cooling costs. • An extension of the service life of asbestos structures. • A completely water based and truly environmentally friendly system. • Provides a rejuvinated appearance in a range of decorative colours.
The SystemThe System
Lichen Loose Asbestos Fibres & Air Asbestos Base Fibroseal Primer Through extensive research and development, Crommelin developed Fibroseal Primer. The primer soaks through the lichen and degraded asbestos down to the sound base material, binding the se unstable elements. Lichen Loose Asbestos Fibres & Air Asbestos Base Fibroseal Primer Through extensive research and development, Crommelin developed Fibroseal Primer. The primer soaks through the lichen and degraded asbestos down to the sound base material, binding the se unstable elements.
Fibroseal Topcoat is then applied to the primed surface to provide a durable, decorative, UV resistant protective coating. Active ingredients in Fibroseal Topcoat also resist the growth of moss and lichen. Fibroseal Topcoat is then applied to the primed surface to provide a durable, decorative, UV resistant protective coating. Active ingredients in Fibroseal Topcoat also resist the growth of moss and lichen.
The Fibroseal System has been specified and used extensively throughout Australia for over 25 years in areas such as government, local councils, commercial industry and schools etc. The Fibroseal System has been specified and used extensively throughout Australia for over 25 years in areas such as government, local councils, commercial industry and schools etc.
Project certification and references are available upon request.Project certification and references are available upon request. Lichen Loose Asbestos Fibres & Air Asbestos Base Lichen Loose Asbestos Fibres & Air Asbestos Base
UntreatedUntreated
Fibroseal PrimerFibroseal Primer
ApplicationApplication
Fibroseal Topcoat Fibroseal Primer Fibroseal Topcoat Fibroseal Primer
EncapsulatedEncapsulated
voc LOW voc LOW
Before AfterBefore After


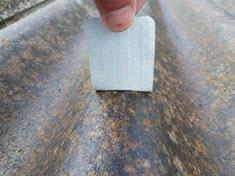
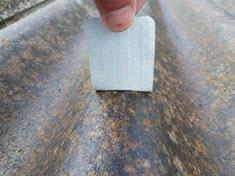
93 Westview Drive, Mill Park Port Elizabeth 6001 93 Westview Drive, Mill Park Port Elizabeth 6001