
8 minute read
Vicor DC Regulation Vital to Success of Hydrogen Fuel Cell Power
By Tom Williams, Contributing Editor
The potential for hydrogen power in electric vehicles has been underestimated and certainly underpublicized. However, it actually has great potential—a potential that can profoundly change our technical and transportation environment. One misconception has been that such vehicles are powered by burning hydrogen. In reality, hydrogen is combined with oxygen in a controlled environment called a fuel cell to produce electricity and . . . water. The electricity, which manifests as DC current, is used to power the vehicles.
Each hydrogen atom consists of one proton and one electron and exists in its gaseous form as H2. In the fuel cell, compressed hydrogen flows out of the secure storage tank where it meets a platinum grid where its electrons are separated and only the protons get through to cross through an electrolyte membrane and meet up with the O2 molecules in the air, which is brought in on the other side. The electrons are brought over via a conductor which they flow through in the form of electric current. On the other side, they can then combine with the protons from the hydrogen molecules and the oxygen atoms to form water. The current produced from the electron flow is used to power the vehicle (Figure 1).
All major vehicle manufacturers are exploring hydrogen power and some even have products on the commercial market, albeit in extremely limited supply. In contrast, battery-powered EVs have progressed much further and major manufacturers have already announced huge investments and introduced product lines that are gaining popularity. Researchers in this arena, however, say that there will be no “winner” between hydrogen fuel cell vehicles and battery vehicles. Both will have a place in the transportation industry of the future.
Formerly, one of the biggest disincentives about hydrogen for powering vehicles has been its high volatility and nature as extremely explosive. This has led to a great deal of research and effort aimed at safe storage and has resulted in the development of tanks that are both relatively light-weight and are super strong. The current storage tank design consists of three layers: an inner plastic-lined layer of plastic-lined to prevent hydrogen leakage; a middle structural layer of carbon-reinforced plastic; and an outer glass-reinforced layer. They have been subjected to strenuous tests including crash tests, heating in fires over 800 degrees, and dropping from considerable heights. So far, only a direct hit from an armor-piercing bullet has been able to damage them enough to leak hydrogen.
The weight-to-energy ratio along with the now well-developed safety has allowed the development of hydrogen-powered vehicles in addition to such things as robotic aerial drones and even hydrogen-powered big-rig trucks. Vicor is looking at an active role in the implementation of the DC power systems that control and distribute the electrical energy throughout such vehicles as all ranges of their functionality from drones to rail and ship transport.
High-Density Conversion and Control for Drones and Beyond
One of the characteristics of fuel cells is that their output can be highly variable and thus needs to be tightly controlled and regulated for use in real-world systems. Vicor Power has been working with Doosan Mobility Innovation to develop highly efficient and safe power systems for that company’s commercialized hydrogen fuel cell power pack that delivers breakthrough energy density, about 4 – 5 times that of a battery, enabling drones to

One of the characteristics of fuel cells is that their One of the characteristics of fuel cells is that their output can be highly variable and thus needs to be tightly output can be highly variable and thus needs to be tightly controlled and regulated for use in real-world systems. controlled and regulated for use in real-world systems.
fly for up to 2 hours. With the extended range that the hydrogen fuel cell power pack provides, DMI is delivering global humanitarian relief. Their drones have transported masks and emergency supplies between the US Virgin Islands and delivered medical AEDs to the top of Mt. Hallasan, South Korea’s tallest mountain on Jeju Island.
The hydrogen fuel cells developed by DMI offer an output voltage that can range from 40VDC to 74VDC and this output must be delivered to the vehicle’s systems in two tightly controlled power trains, namely 48V at up to 12A to the rotor motors and 12V at up to 8A to the drone’s controller electronics and its cooling fans (Figure 2).
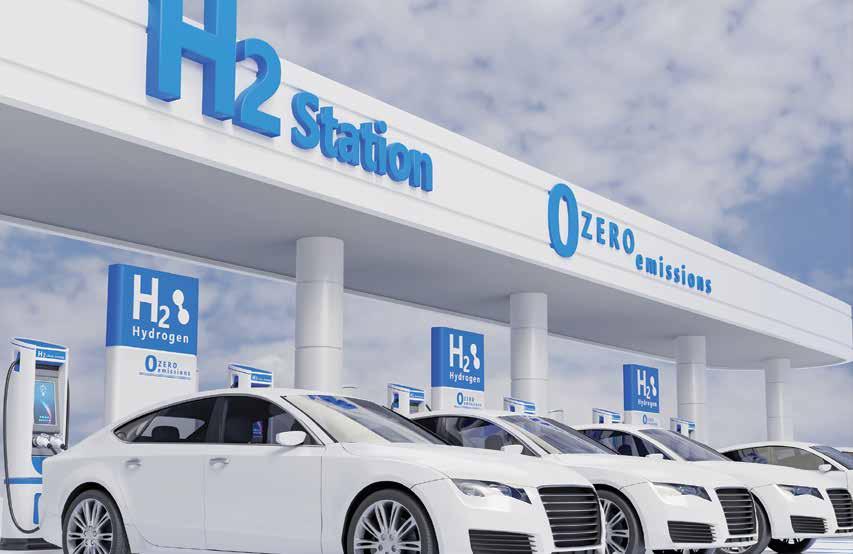
To achieve high efficiency and high energy density in the PDN, DMI selected Vicor PRM buck-boost regulators and a Vicor ZVM buck regulator. The PRMs support the up to 74V open-circuit voltage (OCV) of the hydrogen fuel cell stack and perform stable voltage regulation to 48V. In the drone’s rotor-side PDN, two PRM buck-boost regulators (PRM48AF480T400A00) are configured in parallel to supply the 12A required by the rotors. The PDN for the digital controller board in the stack uses a lower-power PRM (PRM48AH480T200A00) followed by a 48V – 12V ZVS buck regulator (PI3546-00-LGIZ).
One big advantage of a hydrogen power system is that its capacity can be adjusted (with considerations for weight, size, and cost) to provide hybrid battery backup. This can be an important option, especially for airborne systems. For example, extra power may occasionally be required for takeoff and landing. Or, if for some reason the stack’s output should unexpectedly drop, the converters can supplement the stack’s output with the batteries. In case of complete stack failure, in the case of the DMI drone, the battery can enable an

emergency landing with up to three minutes of operational power.
The success of the DMI drone, along with successful developments taking place in the automotive and other industries, indicate a bright future for hydrogen power, which it is predicted will be a factor alongside battery power, wind, and solar in the energy world of the future. DMI is planning on expanding its product lines along with the need for additional power regulation technology. In addition, automotive and other systems will all require the same sort of regulatory elements for success, albeit in many different outputs and power delivery configurations. Compared strictly to batteries, hydrogen fuel cells, despite many other advantages, demonstrate a lower efficiency. Therefore, maximization of their actual efficiency is vital to the success of the overall system.
DC-DC Regulation
Vicor offers a family of isolated, highly efficient, regulated DC-DC converters utilizing high-frequency zero-voltage switching (ZVS) topology, operating from an unregulated, wide range input to generate an isolated output. The modules come in two packaging options. The ChiP packaging is a low-profile module that offers several thermal management options in a compact size with throughhole mounting for circuit boards, etc.
2V, 24V, or 48V direct to point-of-load regulators
The PI33/PI34/PI35xx ZVS Buck switching regulators offer board-level designers maximum power density and flexibility for high-efficiency point-of-load DC-DC regulation. The integration of a high-performance zero-voltage switching (ZVS) topology increases point-of-load performance, providing best-in-class power efficiency up to 98%. The ZVS regulators are highly integrated with control circuitry, power semiconductors, and support components, in a high-density System-in-Package (SiP). The devices can also be configured to operate in constant current mode.
In addition, a series of buck-boost regulators offers integrated controllers, power switches, and support components, all within a high-density system-in-package (SiP). The PI37xx series requires only an external inductor and a minimal number of capacitors, to form a complete DC-DC switching mode buck-boost regulator. The high switching frequency reduces the size of the external filtering components, improves power density, and enables a very fast dynamic response to line and load transients. The PI37xx regulator sustains high switching frequency up to the rated input voltage without sacrificing efficiency and supports large DC-DC conversion ratios. The device can also be configured to operate in constant current mode.
A Full Line of DC-DC Control
In addition to the switching regulators used in the hydrogen fuel cell applications, Vicor also offers a full line of DC-DC converters, the DCM series. These are isolated, highly efficient, regulated DC-DC converters utilizing high-frequency zero-voltage switching (ZVS) topology, operating from an unregulated, wide range input to generate an isolated output. The VIA modules, for example, are chassis-mount with additional integrated EMI filtering, tight output voltage regulation, and a secondary-referenced control interface while retaining the fundamental design benefits of the conventional brick architecture (Figure 3).
The DCM5614, for example, can accept a nominal 270 V DC input (180V min to 400V max primary source) and convert it to an isolated, regulated 28V to supply 46.43A or 1300 Watts at that voltage. The DCM5614 is available in a chassis mount or PCB-mount form factor and can act as the primary source of regulated power for a given device or system. In this regard, it also has an optional PMBus control interface that can provide access to the DCM’s internal controller configuration, fault monitoring, and other telemetry functions. A selection of different output power levels, mostly in ChiP packaging, is available. These also offer different output voltage selections.
Up to eight DCM5614s can be connected in parallel for a staggering total of over 10kW available power. Up to four have been proven so far in an array, offering 5.3kW. Thus, multiple DCMs may be paralleled for higher power capacity via wireless load sharing, even when they are operating off of different input voltage suppliers. A wide selection of ChiP-packaged controllers that take the 28V output of the 5614 is available for configuring the exact system desired. A variety of such controllers can be connected to the 48V output of the 5614 to supply the needed input voltages to internal devices and subsystems.
The technology is scalable and expandable. In response to the success of the 2.6kW power pack currently in production, DMI plans to expand its product line with several other units, designed to serve a wider range of applications. The family will range from the 1.5kW hydrogen-fuel-cell power pack that’s scheduled to be released next year to a unit capable of producing up to 10kW. DPI also intends to further expand its product line with a series of drones, each designed to be easily integrated with one of the new power packs. The implications for further hydrogen=powered vehicles are clear.
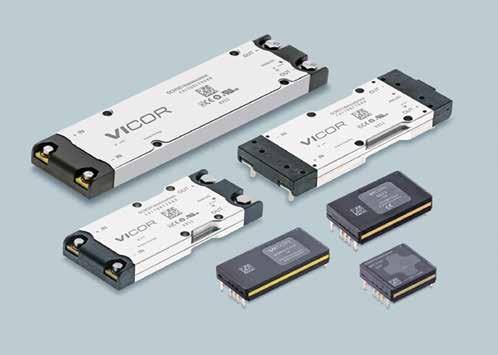
Figure 3: DCM converter modules are available in two basic packaging options. The ChiP, which is a through-hole mount, and the VIA, which is a chassis mount with additional features.
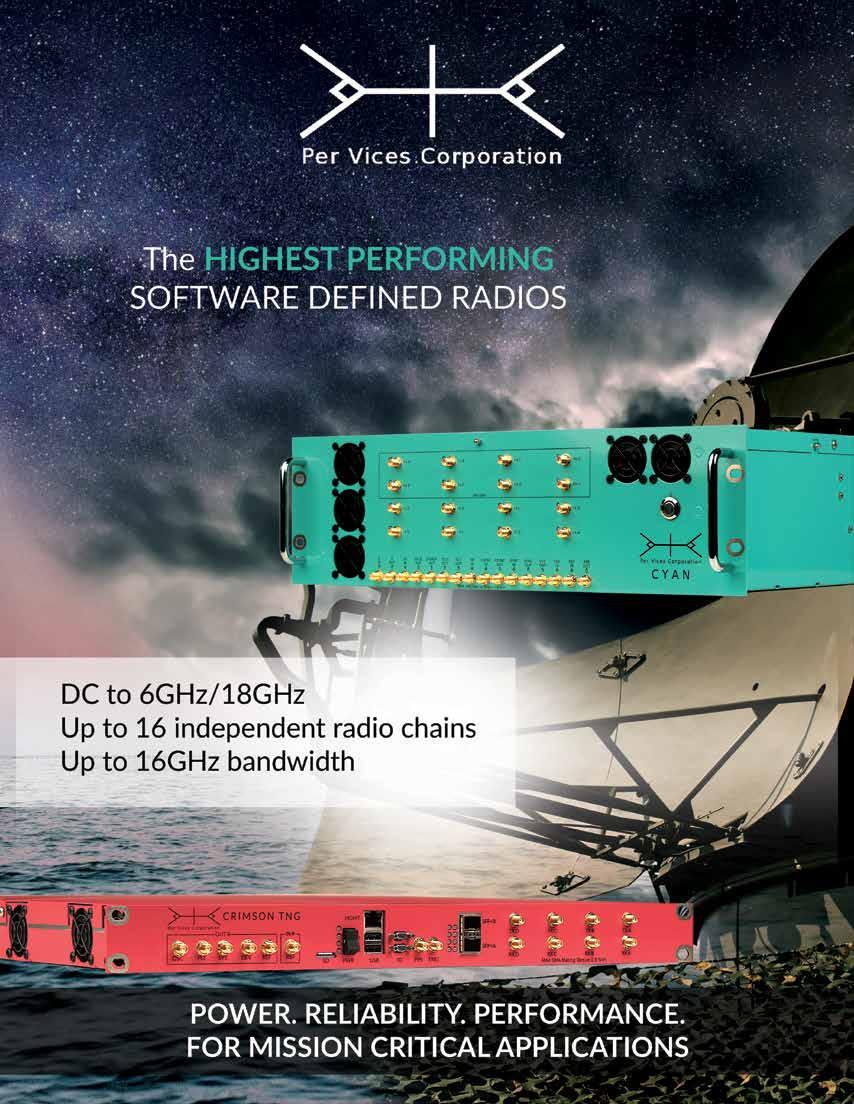