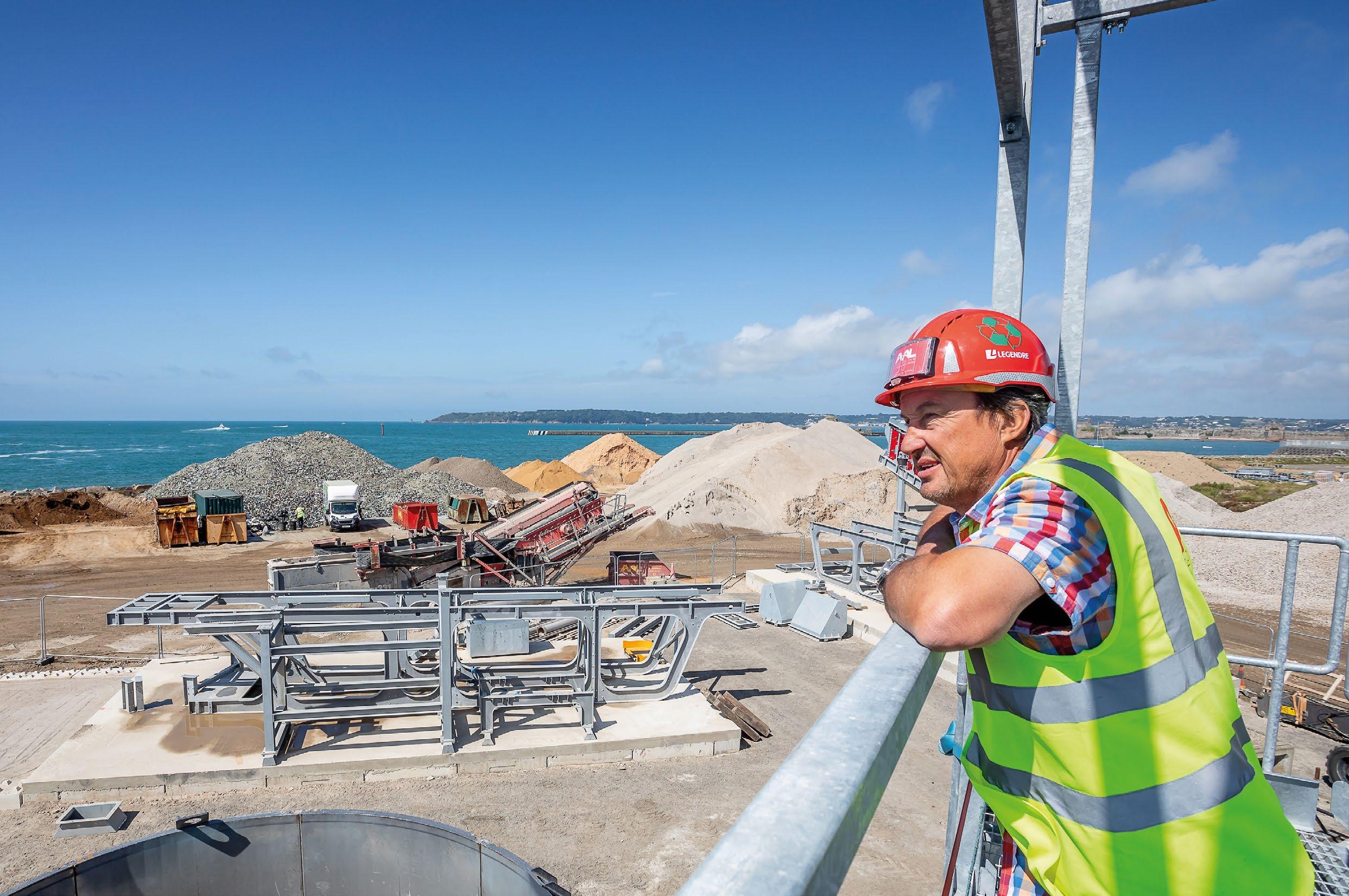
5 minute read
When the landfill has to stop
When the landfill
has to stop
Advertisement
AAL Recycling is literally ‘cleaning up’ Jersey’s construction waste. Alasdair Crosby visited the managing director, Alan Langlois, at the company’s operational base at La Collette, where a new aggregate washing plant can clean waste and recycle it on a grand scale
Remember the days - not so very long ago, really - when the coastline was at La Collette power station? When all the areas now beyond there and on the southern side of the Esplanade was all foreshore, and when at high tide on stormy days waves would crash over the seawall? All these reclaimed areas were created from landfill - the waste products of the construction industry.
But now the landfill has to stop. There are no plans to extend the Island any further into the sea. Yet the waste keeps on coming and there is only a relatively small area that can still be filled. What will happen then when the available area is chock full?
The answer can be expressed simply and briefly: ‘recycle’. And Alan Langlois’ company, AAL Recycling Ltd, is at the forefront of the drive to clean up waste and give it a new life by recycling it, rather than extracting or importing fresh supplies to further clog up the Island.
AAL Recycling operates from an area at the far end of the La Collette reclamation area: a mountainous kingdom of clay, rubble, old glass, soil... waste coming in from the construction industry and recycled material awaiting delivery and reuse in the next stage of its existence. ‘In 2006 when I first got the recycling contract,’ Alan said, ‘the recycling rate was approximately 17,000 tons of building waste a year. We are now recycling 100,000 tons a year. It has been hugely successful, but the same quantity again - another 100,000 tons - is still going to landfill. Now, it’s almost full.
‘In essence, we are trying to recycle waste so it can be used again. But although recycling is rightly seen as “green”, there is still in many quarters a prejudice against recycled material, in that the perception is that it is of inferior quality to fresh material.’
So his company is on a mission to convince Islanders - be they construction companies, engineers, or landscape gardeners looking for topsoil - of the merits of recycled material.
This mission is helped by the acquisition last year of a giant ‘aggregate washing and grading machine’ imported from an Italian manufacturing company, Matec. They design and manufacture complete plants for many sectors, including aggregates, gravel, sand, stone, concrete, ceramic and glass.
After some inevitable delays due, as usual, to Brexit and Covid, the equipment is getting assembled and will be in commercial production this autumn. The La Collette energy recovery plant will supply the electricity, i.e. waste will power the process to deal with waste. The washing plant reuses 97% of the water within the closed system.
Alan said: ‘You throw everything into it. It’s like making a stew, then deconstructing it: it takes mud, dirt - the lot. Not only does it give us clean, crushed stone (which is our core business), it gives us sand… which, with gravel and crushed stone, is a major component of the aggregate used in the production of concrete.
‘That is important because there is a query over the availability of future domestic supplies of sand. If that were to dry up, we would have to import it. This machine can give us supplies of sand from washed glass and rock, so we can supply sand for different applications, such as equitation arenas or trench fills for utility companies.
‘We will also be able to supply recycled small stone for landscaping projects rather than the Island having to extend existing quarries to extract fresh supplies.
‘At the moment we are recycling 30% of every 100 tons of waste received; the Matec washing plant will enable us to recycle 70%. And the remaining 30%? Our plan is to mix this with organic material and create a top soil mixture to make sure we avoid any material going to landfill.’
One of AAL’s projects at the moment is the deconstruction of the Nightingale Hospital; once the building materials have been removed for recycling, the land beneath it can be returned with the help of soil mixture.
AAL also now creates large interlocking concrete blocks, a bit like Lego pieces, known as Kelly blocks. The multi-purpose blocks have a wide range of uses and are ideally suited for barriers and retaining walls. Buying a Kelly block from a quarry is expensive, so now AAL have bought moulds and are making them ‘in-house’- utilising the Island’s waste glass as a key ingredient for the concrete. He continued: ‘Everything that goes into landfill could be recycled. We now produce 250 tons of concrete a week from waste; we need to let people know that Jersey can produce its own; these products need not be imported. Landfill components are not hazardous: it can all be recycled, remade and reused. Even ceramics can be converted back into the sand that composes it. The advantage of that for the Island’s construction industry and purchasers of concrete speaks for itself.

‘I want to stop landfill, or at least to slow it right down. Even if you just re-use recycled material once, it saves on something being extracted from the ground. You name it - we can recycle it.
‘This washing plant, powered by the energy derived from household waste, turns discarded building and demolition aggregates into viable, construction quality materials. It is a major step towards the Island’s ambition of reaching carbon neutrality by 2030.
‘I am proud to be at the forefront of this change. This is our Island, and we all need to make sure it remains as beautiful and unspoilt as possible for the next generation.’
“Everything that