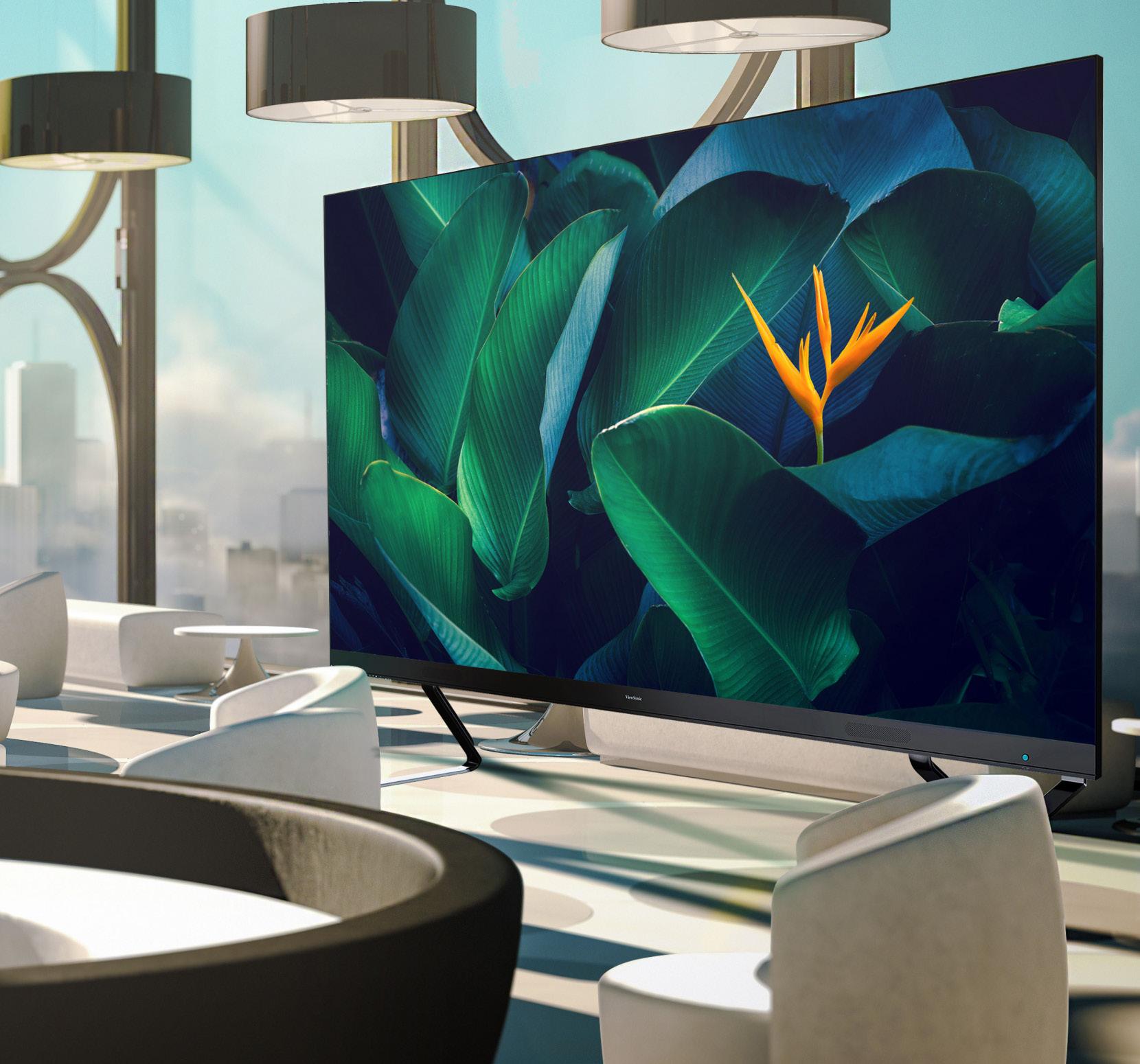
77 minute read
Worldwide Engineering Magazine
ViewSonic Corp., a leading global provider of visual solutions, is introducing its latest All-inOne Direct View LED Displays, a brand-new addition to the large-size presentation display sector. Different from traditional LED displays, these new displays integrate display, image stitching, power supply, and control systems into one device that offers easy installation, operation, and maintenance. The elegant design of the All-in-One Direct View LED Display elevates the seamless viewing experience and easily merges with the surrounding environment in spaces such as lobbies, auditoriums, boardrooms, and conference rooms.
“As a leading visual solution provider, we are pioneering new trends in the LED projector and presentation display markets and moving the development of LED technology forward by achieving this new milestone in LED displays,” said Dean Tsai, the Head of the Projector & LED Display Business Unit of ViewSonic. “We created a whole new product category, and market sector with All-in-One Direct View LED Displays, which come in sizes of up to 216”. The complete product line-up delivers large-sized presentation displays for a wide array of usage scenarios and proves that we remain at the cutting edge of innovative applications in the display world.” Traditional large-size display solutions still have many limitations. LCD video walls have many LCD panels that are difficult to install, calibrate, and maintain. The panels are heavy with thick bezels, which can result in problematic image grids. Also, the size of a single LCD panel has a limitation of 98”. Although traditional LED displays constitute a significant improvement over LCD solutions and do not come with image grid issues, they still use separated systems for display, power supply, image stitching, and control, making them too large and difficult to maintain and operate. The brand-new ViewSonic All-inOne Direct View LED Display resolves all the pain points of traditional large- sized displays by providing innovative LED technology and integrating different systems into one device. Moreover, it supports wireless presentation and can operate as a large interactive display through being coupled with ViewSonic’s ViewBoard or
Advertisement
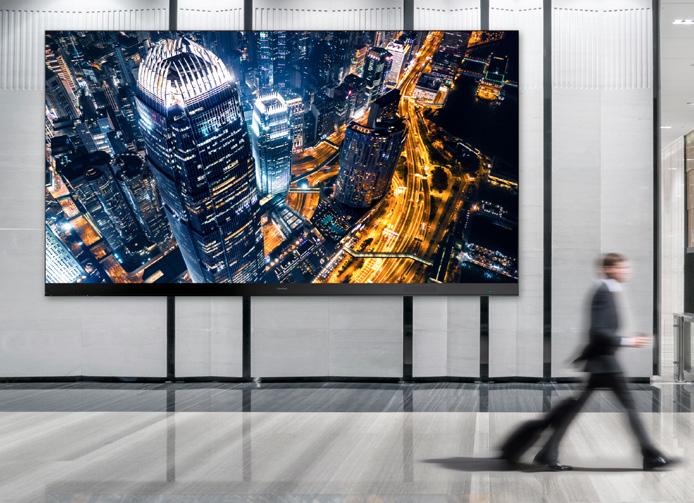
touch monitor. Overall, ViewSonic’s All-in-One Direct View LED Display delivers a fantastic visual experience, and harmoniously blends in with its surroundings due to its elegant design. Because of its all-in-one design, it features easy installation, operation, and maintenance with a low total cost of ownership in the long run.
Fantastic Visuals For the magnificent viewing experience, the All-in-One Direct View LED display is available in four different sizes—108”, 135”, 163”, and 216”. It has a stunning and vivid 120% Rec.709 wide color gamut and up to 600 nits of brightness with eight levels of adjustment. Therefore, users can fine tune the brightness based on the environment.
Elegant Design Achieving a natural and perfect merger with the surrounding environment, the ultra-thin and lightweight display features a thickness of only 35 mm. It’s as thin as a mural on a wall and blends in harmoniously with almost any interior design style. The super-slim bezel of only 10 mm provides an even more immersive viewing experience.
Worldwide Engineering Magazine | 11
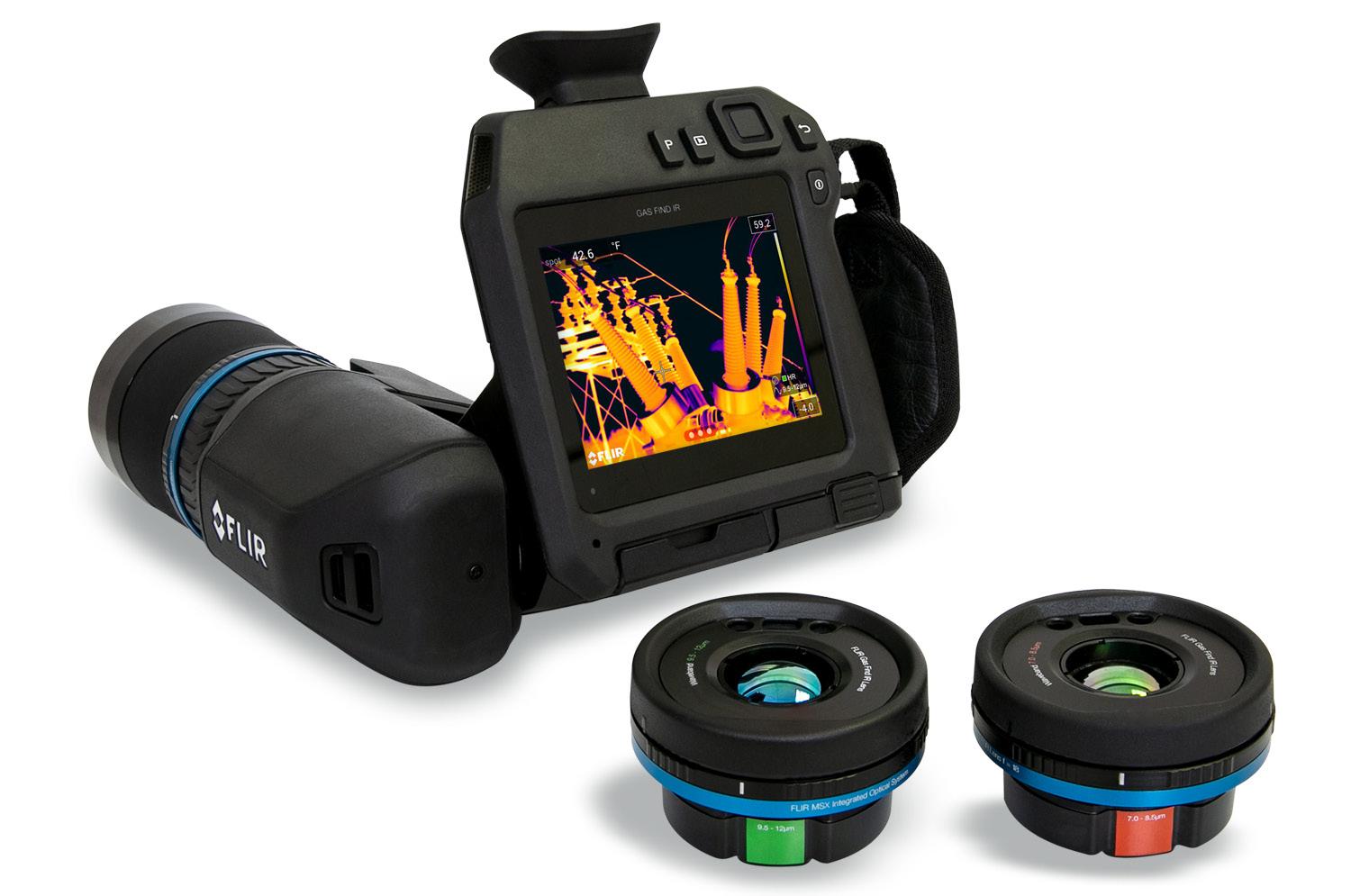
Building on the previous methane-detecting GF77 camera release, FLIR now offers two lens types for finding a wider variety of gases with just one camera.
The new FLIR GF77TM Gas Find IR Series provides professionals with the flexibility to use one uncooled gas detection camera for gas detection and thermal inspections across chemical and industrial manufacturing, electric power utilities, natural gas supply chain, food and agricultural, and public safety. The most notable feature updates include visualizing a completely new category of gases in sulfur hexafluoride, ammonia, and ethylene. The GF77 Series also offers IR high-temp ranges, increased temperature measurement accuracy and improved inspection flow/reporting with optional add-ons for FLIR Thermal Studio Pro and FLIR Route Creator. ergonomic, easy to use camera is calibrated for IR temperature measurement, so inspectors can use it as part of predictive maintenance programs, such as verifying tank levels and searching for electrical or mechanical issues without the need to change a lens.
Professionals have the option to purchase the lens combination that meets their needs, the GF77-LR, the GF77-HR or the
GF77 with both the LR and HR lenses. Further, each lens is calibrated to a specific camera body at the time of purchase to visualize the gases of interest and measure temperature accurately. For customers who already own a GF77 and would like to expand its capabilities, the FLIR service center can calibrate any new lens purchased for that specific device. Improved Camera Options The GF77 Gas Find IR Series now includes a broader temperature detection range, from -20 °C to 500 °C, with improved accuracy of +/- 3 °C, down from +/- 5 °C, within the full temperature range. The optional on- board routing capability, Route Creator, allows end-users to simplify surveys by pre-planning the route that includes a list of assets that need to be inspected at each location, reducing the risk of missing an asset that could lead to an unexpected failure. The reporting add-on, Thermal Studio Pro, offers an easy final comprehensive report option. The GF77 Gas Find IR Series is available globally. For more information, including options for purchasing, visit: www.flir.com/GF77-series.
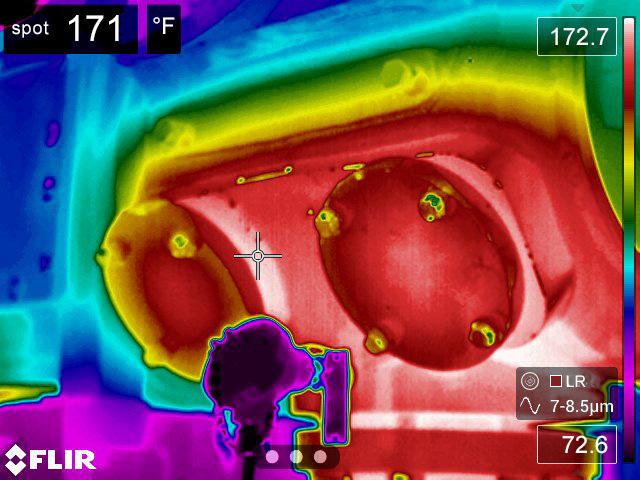
Herga’s Modular Footswitch System Now Has individual 60601-1 Medical Approval: Herga Announces A Flexible And Globally Unique Approach For Medically Approved Footswitches
The Medical Footswitch Design Platform is an attractive and ergonomic solution for medical equipment manufacturers offering wide flexibility for application-specific switching. OEMs can easily accommodate their specific switching requirements for a single machine or range of machines with varying functionality through seamless range expansion. The base system consists of moulded thermoplastic single and double plinths that mechanically lock with joining spacers to provide electrical connections for 1-, 2-, 3- 4-, or 5- plinth configurations. Each single plinth can accommodate a single footswitch as well as one or two puckswitches. Complementing the Medical Footswitch Design Platform, Herga’s IEC 60601/UL 60601 medically approved range of footswitches include the well proven 6226 series that can be selected with environmental protection options EN60529 IPX7 or IPX8 on request. Whilst the electrical ratings for each complete base unit are determined by the application, the typical electrical switching range for each footswitch is up to 3 A at 24V AC/DC with momentary function for SPST, N/O or SPDT. Medically approved 6241 puckswitches, 6244 haptic puckswitches and Otto switches can also be included with typical ratings of 0.1 A at 24V DC for SPDT/DPDT switching. with a raised divider built into the joining spacer. Steel base plates are available for added durability. The switch components can be suppled in a range of standard colours and customer logos included. Additional options include LEDs, screen printing and USB connection. Fully customised base systems are available in

OEM quantities. The Modular Base System is also suitable for industrial and commercial machinery switching tasks where medical approval is not essential. Herga has developed a comprehensive range of standard variants that use the new modular base system to combine commonly specified 6226 series footswitches and single 6241 puckswitches. With a series of detailed datasheets including reference dimensions and ordering information available from the Herga website, this range covers straightforward selection in eight combinations that span a single footswitch to a multiple switch combination including 4x footswitch plus 4x puckswitches switch configuration. This range can of course include Herga’s medically approved foot and puckswitches switches allowing a fully medically approved product on-
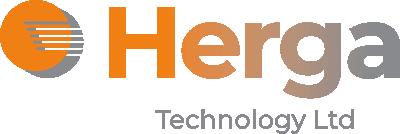
All of the electrical switching functions for the Medical Footswitch Design Platform are typically output via a single cable for straightforward machine connection, with flying leads and stripped cable cores or with a preferred connector as required, or alternatively via our closed network Bluetooth Full details of the Medical Footswitch Design Platform are available on request from the switching and sensing solutions specialist with sales and applications staff on-hand to discuss specific requirements at sales@herga.com or by calling +44 (0)1284 701422. connection. A wide range of modular accessories may be included such as tubular steel carrying handles, open guards or roll bars. For improved operational safety, each foot switch may also be separated Visit www.herga.com for complete information on Herga’s wide range of medically approved and industrial grade single- or multi-pedal foot and hand controlled switches. delivery.
Worldwide Engineering Magazine | 13
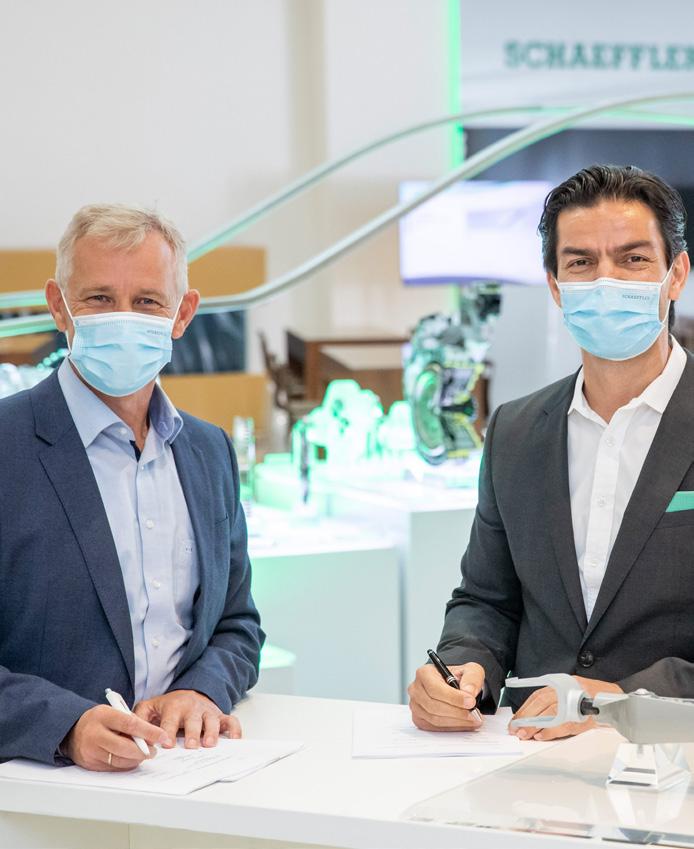

• New development partnership with Bosch Automotive Steering • Intelligent mechatronic Rear Wheel Steering system delivers improved ride comfort and safety as well as superior energy efficiency • Matthias Zink: “A key milestone in our journey to becoming the technology partner of choice for chassis systems”
Global automotive and industrial supplier Schaeffler is embarking on a development partnership with Robert Bosch Automotive Steering GmbH to expand its intelligent Rear Wheel Steering (iRWS) portfolio. The aim of the partnership is to grow the market by offering integrated solutions for Rear Wheel Steering systems. Under the partnership, Schaeffler is providing mechatronic iRWS systems, and Bosch Automotive Steering is contributing software and electronics in the form of steering control units. “Combining the strengths of both companies enables us to create integrated systems that deliver superior added value to our customers,” commented Matthias Zink, CEO Automotive OEM at Schaeffler. “Intelligent Rear Wheel Steering technology is a key milestone in Schaeffler’s journey to becoming the technology partner of choice for chassis systems.”
Rear-wheel steering technology: a mechatronic evolution
Schaeffler successfully launched its mechatronic intelligent Active Roll Control system (iARC) back in 2015. “The lessons we learned from that process flowed directly into the development of mechatronic Rear Wheel Steering,” said Dr. Keiwan Kashi, President Business Unit Mechatronic Systems at Schaeffler. “By combining our expertise in mechatronics with our core competencies in the industrialisation of mechanical and mechatronic components, we created a highly efficient product that can be tailored to customer requirements.”
The mechatronic iRWS unit improves ride comfort and safety which offers several key benefits in today’s rapidly urbanising world. By turning the rear wheels in the opposite direction to the front wheels, it reduces the turning radius, significantly increasing maneuverability in tight spaces, such as when parking in busy urban settings. Moreover, the rear axle’s assistive steering action enhances handling, stability and ride comfort and improves vehicle safety. Schaeffler’s Rear-Wheel Steering system uses lightweight technologies and features a maximum overall weight of just eight kilogrammes. At the heart of the system is a planetary roller gear that performs a self-locking function, ensuring that the rear wheels do not change direction without steering input from the driver. The planetary screw drive also delivers superior efficiency. Moreover, the system’s design is acoustically optimised, making it particularly well suited for use in low-noise electric vehicles.
Bosch steering control unit supports safer driving
Bosch’s contribution to the partnership is the steering control unit, an integrated module comprising control electronics, an electric motor and software. Scalable and modular in design, this unit is fundamental to many of the driver-assistance functions in Schaeffler’s new rear-axle steering system. Already a proven performer, the steering control unit has been successfully implemented in millions of front-axle steered vehicles. It features Bosch security for robust protection against cyber attacks. Functions and updates are supported by over-the-air (OTA) technology. “Our third-generation steering control unit was launched just last year and is already doing very well in the market for frontaxle steering control systems,” said Dr. Stefan Waschul, head of passenger car steering systems at Robert Bosch Automotive Steering. “Under this partnership, we will apply our expertise in this area to rear-axle steering systems and contribute the wealth of experience and technical know-how in software and E/E architecture that has made us the market leader in steering control systems.”
Development partnership to expand the intelligent Rear Wheel Steering (iRWS) portfolio: Dr. Keiwan Kashi, President Business Unit Mechatronic Systems at Schaeffler and Dr. Stefan Waschul, Head of passenger car steering systems at Robert Bosch Automotive Steering signing the contract.
For more information on Schaeffler please visit: www.schaeffler.com/fork/

PNeumatic coNveyiNg short courses for iNdustry

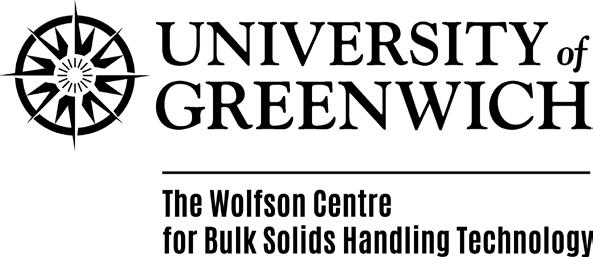
Commissioning and Troubleshooting ‘Hands-on’ Pneumatic Conveying 2 – 3 November 2020
Practical challenges of starting up systems on site and ensuring they work as the designer intended
Pneumatic Conveying of Bulk Materials 16 – 20 November 2020
Components of pneumatic conveying systems, selection and design techniques (delivery on-line over 5 sessions)
Pneumatic Conveying System Design 1 - 2 December 2020 (on campus) / 7 – 11 December 2020 (on-line)
In-depth exploration of detailed calculations for design of pneumatic conveying pipelines and specifying plant
Who should attend?
*plant designer *plant manager * maintenance staff * operational staff * senior management *anyone actively involved in design or troubleshooting of pneumatic conveying systems *
These courses will improve your ability to deal with the design and troubleshooting of different systems. They aim to provide a better understanding of potential problems and how to make your plant as efficient and trouble-free as possible
Book Now Places are limited to enable discussion wolfson-enquiries@gre.ac.uk +44 20 8331 8646
16 | Worldwide Engineering Magazine
Short courses for the Process Industry:
Bulk SolidS Handling TecHnology
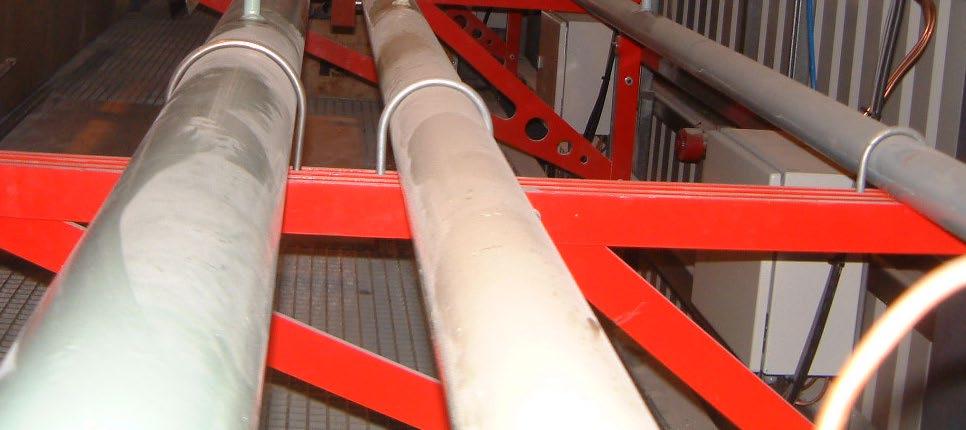



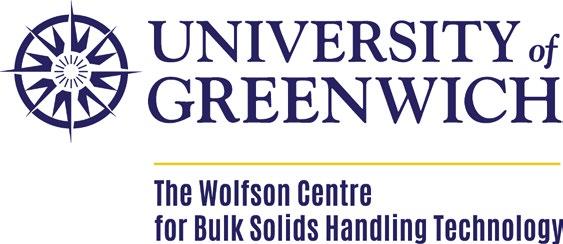

ConSultanCy ServiCeS
Some of our Consultancy services include advising on:
» Storage and Discharge of bulk materials » Pneumatic Conveying of bulk solids » Spoiling of materials in storage and in transit » Plant and Equipment design/redesign » Ship Unloading/ quayside operations » Control of plant wear » Dust control » Bulk Materials characterisation » ATEX/DSEAR compliance » Expert Witness services
Short courses for Industry

We also provide a range of short courses to help delegates identify potential bulk materials handling problems and advise on how to avoid and/or overcome these issues. They fall under 4 main categories
Pneumatic Conveying:
» Pneumatic Conveying of Bulk Materials » Pneumatic Conveying System Design » Rotary Valves; Design, Selection and Operational
Issues » Commissioning and Troubleshooting ‘Hand’s On’
Pneumatic Conveying Systems
Storage of Bulk Materials:
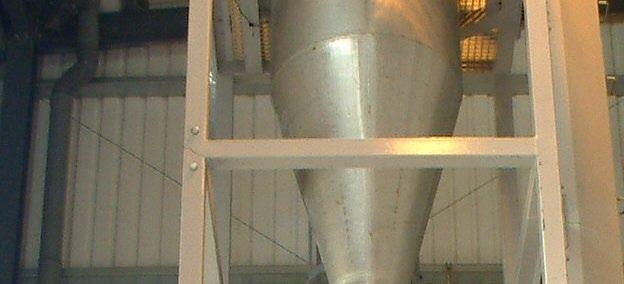
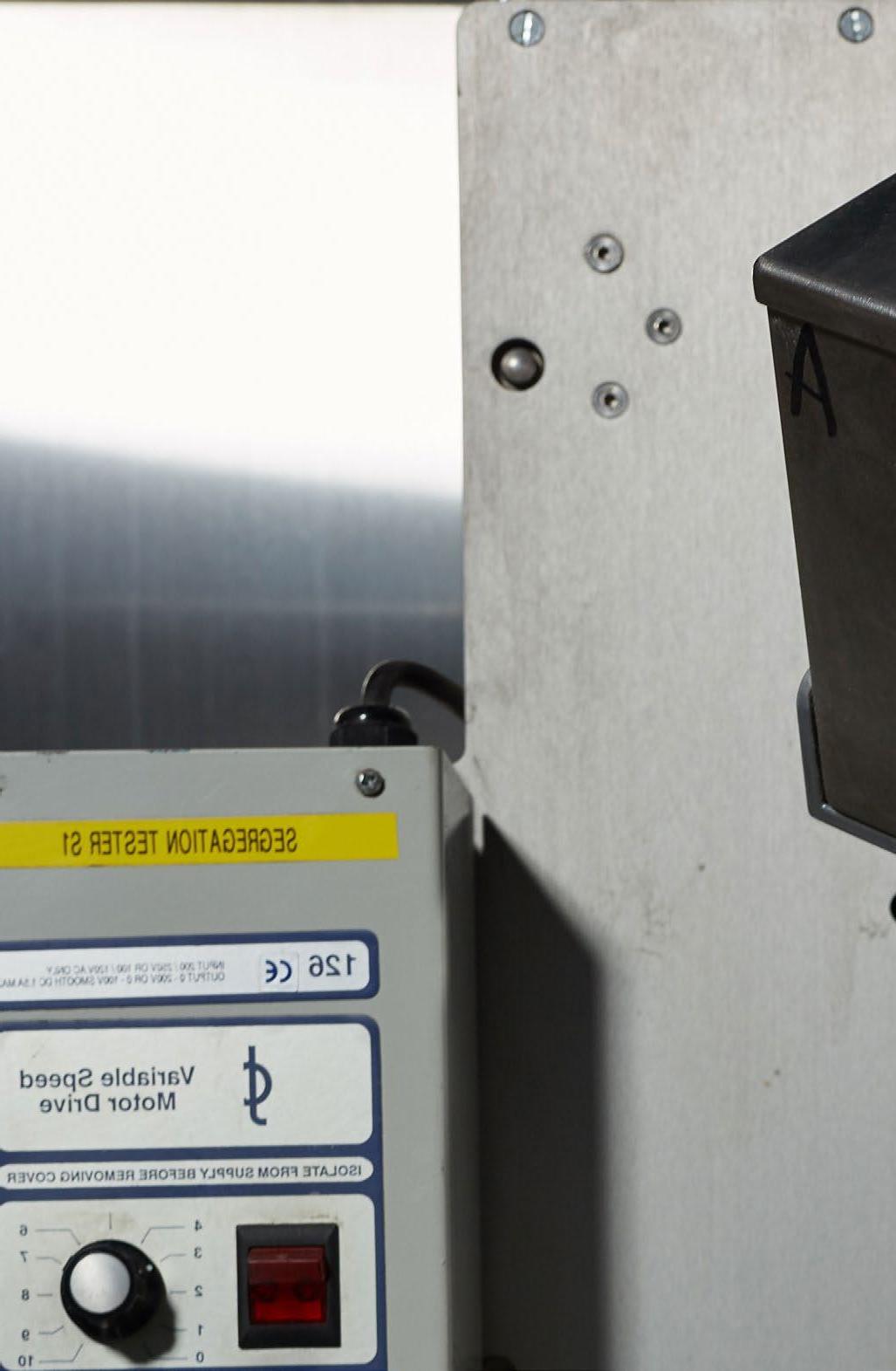
» Storage and Discharge of Powders and Bulk Solids » Design of Equipment for Storing and Handling Bulk
Materials » Biomass Handling, Feeding and Storage (can be adapted to other materials such as waste, recycled goods, pellets)
General bulk materials handling:

» Overview of Particulate Handling Technology » Dust Explosions - How to demonstrate DSEAR/
ATEX Compliance » Port and Terminal Operations for Bulk Cargoes
Measurement of the Properties and Bulk
Behaviour of Particulate Materials » Introduction to Processing Dry Solid Materials
Specialist areas of concern:
» Caking and Lump Formation in Powders and Bulk Solids » Undesired De-blending and Separation in
Processes and Equipment » Electrostatics in Powder Handling » Numerical Modelling of Solids Handling and Processing » Dust Control in Processes Powder Handling and
Flow for AdditiveManufacturing
Pickering Interfaces, the leading The phase relationship between supplier of modular signal the input and output signals switching and simulation is automatically adjusted to solutions for use in electronic lag one cycle, so the phase test and verification, today delay can be negated. Where launched its model 41-670, a this is not acceptable, one of single module that can function the outputs can be used to as an LVDT, RVDT or resolver propagate the input signal simulator. Occupying just resulting in an in-phase signal one PXI or LXI chassis slot, the with the output, which can programmability of the module then be used for demodulation. means that it minimizes the With the addition of builtamount of hardware required. in relays, the 41-670 can also Also, since it sits in a PXI chassis provide short or open circuits alongside a customer’s other for each channel’s inputs and instruments, additional control outputs, reducing the need protocols/interfaces are not for external switching for fault necessary, simplifying operation. insertion requirements. The The 41-670 can handle up to can also be used for simulating four channels of 5/6-wire LVDT/ imperfect sensors and cabling, RVDT or resolver, or eight artificially offsetting single or channels of 4-wire LVDT/RVDT multiple outputs. simulation. Each VDT bank has programmable phase delay an independent excitation input, Comments Paul Bovingdon, as well as the ability to use an Simulation Product Manager, internally generated excitation Pickering Interfaces: “We believe signal. It can operate with a that the model 41-670 LVDT, shared excitation signal to each RVDT or resolver simulator is channel for synchronous test. more versatile than competing Several models are available products which are usually that support excitation voltages limited to just one function. So, ranging from 0.25 VRMS to 38 we replace multiple products VRMS and frequencies from with just one module, which 300 Hz to 20 kHz, meaning the fits in a single PXI slot. We have 41-670 family can simulate a listened to our customers and wide range of LVDT, RVDT, or delivered a full-featured solution Resolvers. with innovative features that
18 | Worldwide Engineering Magazine
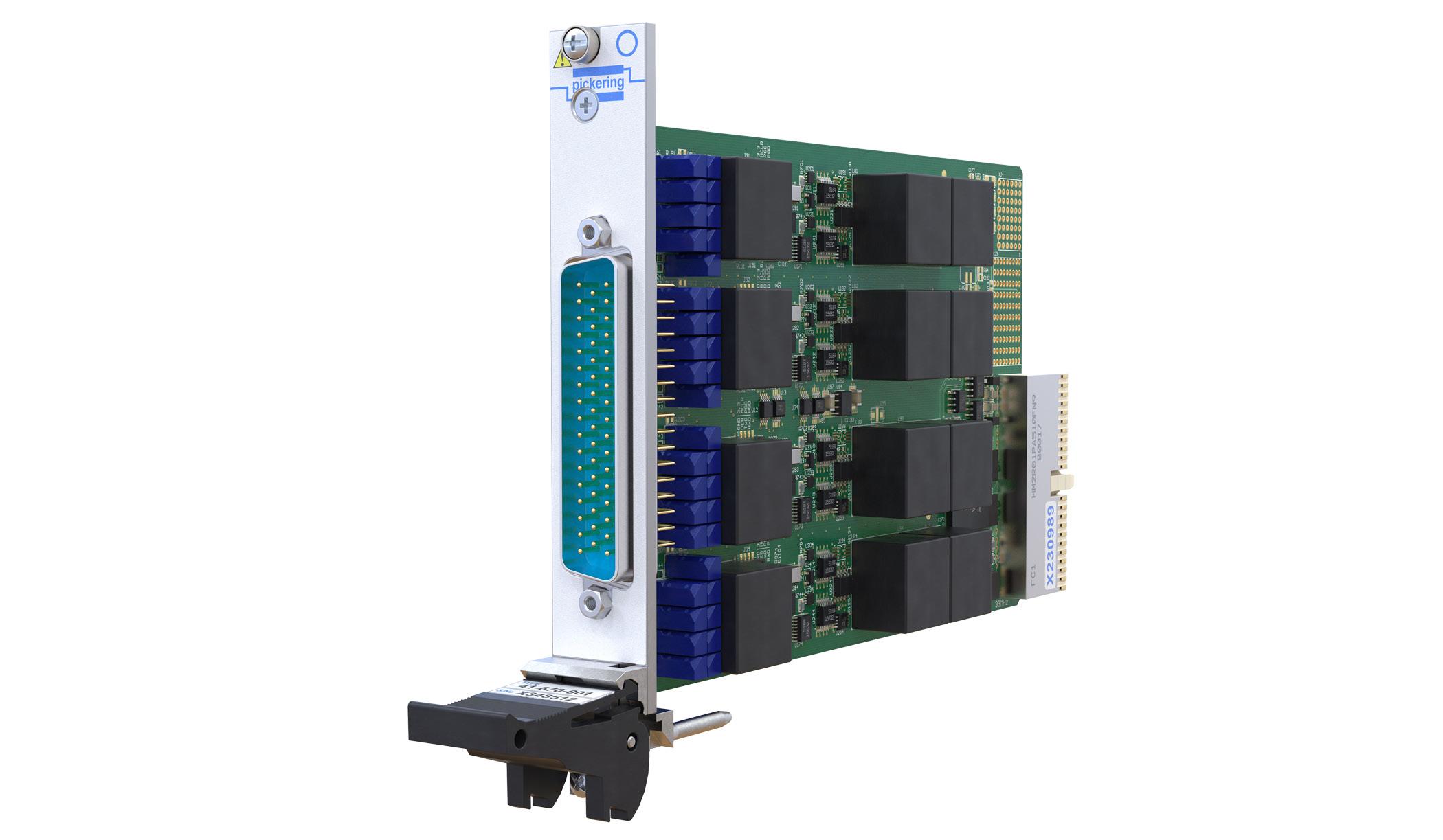
make it easy to use, such as intuitive drivers and a graphical soft front panel for simple manual control.”
The module also features input and output isolation transformers, a wide operational frequency band and the ability to measure and display each input frequency and amplitude. The model 41-670 targets applications including aircraft wing and landing gear control, gun/missile launcher targeting, satellites, motion control for industrial automation, and turbines and nuclear reactors. A PXIe version is available upon customer request. Pickering also provides a full range of compatible cables and breakouts. More details can be found at
www.pickeringtest.com
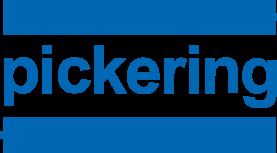
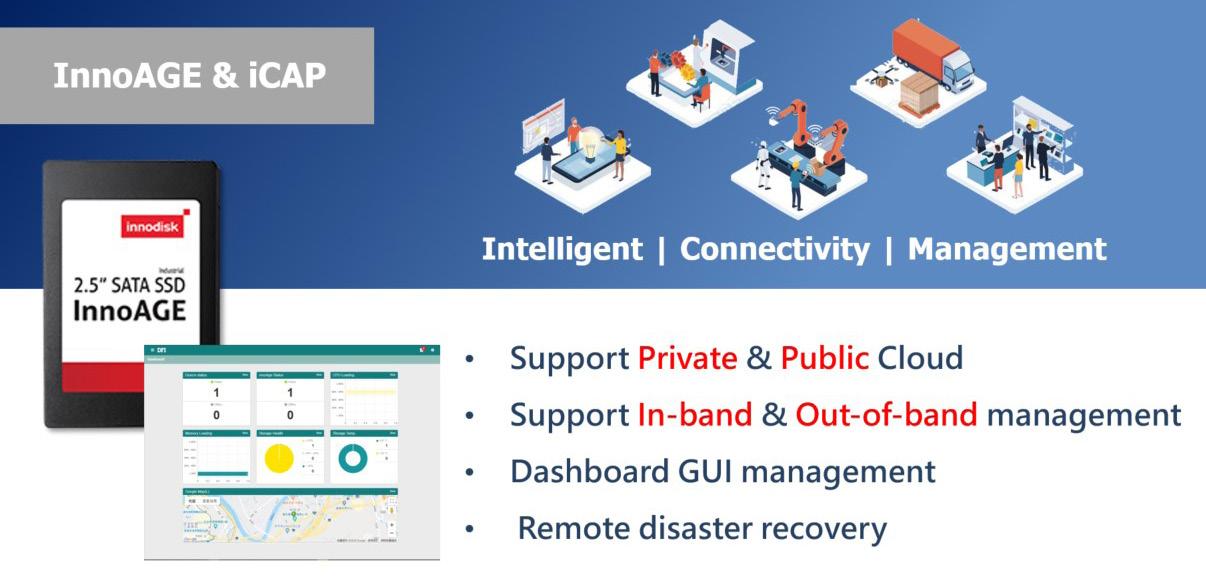
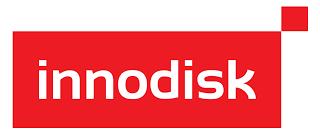
The exponential growth of IoT devices brings a new challenge: how to effectively manage and monitor large numbers of connected devices that may be hard to access in widelyscattered remote locations?
To answer this challenge, Innodisk, the leading industrial storage company, has combined its expertise with embedded technology specialists, DFI, to bring DFI’s RemoGuard remote management system to its customers. DFI joins Innodisk’s growing network of partners who incorporate Innodisk technology to provide a complete storage solution based around Innodisk’s IoT solutions.
Thanks to the integration of Innodisk’s iCAP and InnoAGE dual-band management technologies with DFI’s hardware design, RemoGuard can reduce maintenance staffing costs and response timesand prevent service downtime with features like real-time monitoringand one-button recovery. These advanced features add up to the world’s most comprehensive device management system. “Created in collaboration with Innodisk, a leader in the industrial Solid-state drive (SSD) market, DFI has launched RemoGuard to provide not only high-performance embedded solutions but also an advanced remote management solution. This add-on service helps customers to get through this difficult period and lets us look into a prospective future of cooperation,” said Steven Tsai, President of DFI. iCAP Innodisk’s cloud management

platform, iCAP, provides easy access to monitor and control local and remote devices. This management product detects and collects data, sends reports and alerts operators if the device crashes or experiences other problems.
InnoAGE SSDs are increasingly dominant in responsive enterprise storage. Their unbeatable blend of speed, low power consumption, small size, and low maintenance lets us put SSDs almost anywhere. InnoAGE SSD is Innodisk’s out-of-band managementenabled flash storage solution, equipped with a Microsoft Azure Sphere. InnoAGE enables multifunctional management, smart data analysis and firmware updates, data security, and remote control through the cloud.
Kennametal has introduced a new face milling platform for cast iron applications, the KCFM 45. With fixed and adjustable pocket seats, the new milling cutter provides the option for semi-finishing as well as fine-finishing applications, exceeding the highest surface quality requirements. With carbide, ceramic and PcBN inserts, this new tool is a flexible, cost-effective and user-friendly solution that is ideal for any type of CNC machining center.
Insert offering Carbide inserts are ideal for machining at lower RPM, or in thin-walled workpieces and less stable conditions, while ceramic inserts (KY3500 grade) provide elevated surface speeds resulting in higher productivity. Both offer excellent performance. For fine finishing operations, PcBN inserts will deliver the best possible surface finish, tool life, and throughput.
“With the KCFM 45 face milling cutter, users can mix and match different insert options to suit the application requirements and machining conditions,” says Michael Hacker, Product Manager, Kennametal. For example, you might use PcBN finishing inserts in the adjustable pockets and ceramic or carbide inserts in all other pockets for wet machining or lower volume applications. Regardless of the configuration, the KCFM 45 exceeds the highest surface requirements.

Wave killer The inserts are positioned at a positive axial angle, but with a slightly negative radial angle for better tool life. That creates significantly lower machining forces than competing cast iron face mills, helping to eliminate chatter and further improving surface finishes.
“The KCFM 45 with its adjustable pocket seats can generate surface finishes of 0.8μm Ra (32 μin.) or better, and waviness lower than 10μm Wt (400 μin.),” says Hacker.
The KCFM 45 is ideal for gray cast iron, CGI applications, semi-
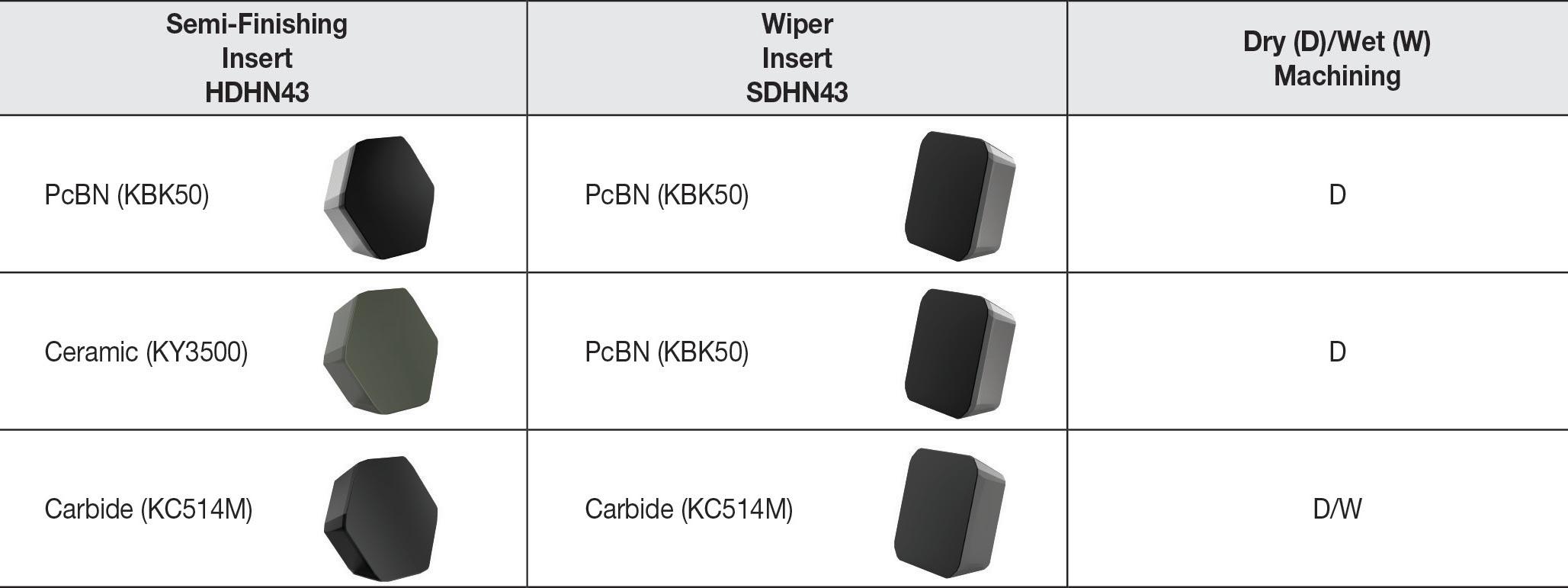
finishing and fine-finishing operations.
The KCFM 45 uses a combination of hexagonal semi-finishing inserts in the fixed pockets together with square finishing inserts in the adjustable pockets with cartridges.
Recommended insert configuration for dry and wet machining. Carbide inserts: Ideal for machines with lower spindle capabilities. Ceramic inserts: For highest productivity, ideal for semi-finishing. PcBN inserts: For highest productivity, ideal for fine-finishing.
For more information on Kennametal please visit: www.kennametal.com

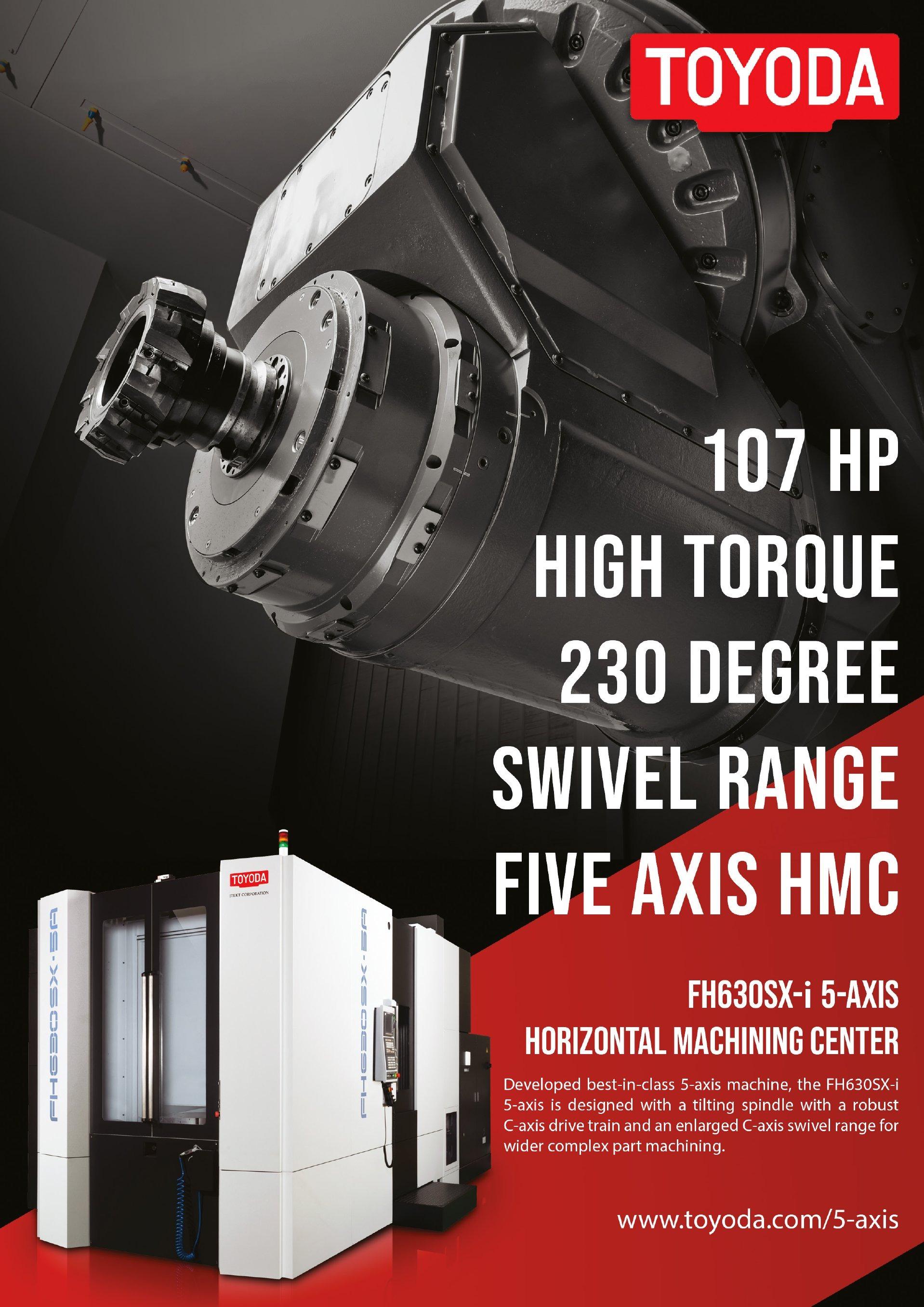
Cognex image-Based Barcode Readers in Flensburger Brewery’s Logistics Center Aging handheld laser scanners are considered outdated technology: When the forklift drivers load trucks at the Flensburger brewery with filled kegs or beer crates, a Cognex barcode reader mounted on the mast recognizes the pallet label and scans the barcode. This not only saves time, but enhances safety in congested forklift and truck traffic, and has proven its worth since the technology was installed. In beverage logistics, operations centers require large amounts of goods to be handled at high speed. This is particularly true for the Flensburger brewery, as the company has achieved growth in a virtually stagnant market and sold a record of 628,000 hectoliters of beer in 2018. In other words: 172,000 liters of beverages were brewed and bottled per day, and divided into 17 kinds. The bulk of the beer brewed continues to be the legendary Flensburger Pilsener with the distinctive swing top. The non-alcoholic beverage segment is also seeing strong growth, which has facilitated a business decision to build a new, larger logistics center. A new code-reading solution for pallet identification For the present, the logistics managers are working closely with Jetschke GmbH & Co. KG to optimize the flow of goods and information in the existing building. Jetschke is the licensed dealer for Linde forklift trucks in the far north. The company with over 270 employees provides and services the fleet of robust and high- performance multi-pallet forklift trucks that convey the “Flens” to the trucks. In addition, Jetschke is responsible for incorporating mobile scanning solutions into the information flow, i.e. into Flensburger brewery’s merchandise management system. Historically, the forklift drivers were equipped with a handheld scanner, with which they recorded the pallets to be loaded. A terminal in the forklift truck cabin displayed which lorry was to be loaded with the respective pallet and once the pallet was scanned and put on the lorry, the system registered the item as “loaded.” This is a common practice in many

companies.

In beverage logistics, the technical equipment must withstand a lot. Thanks to their robust design, the DataMan readers from Cognex consistently achieve extremely high read rates over time
However, Jetschke’s experts aimed for an even faster solution that was comfortable for the operators. The idea: An image processing system is mounted on the forklift truck’s mast, which automatically recognizes the palette’s EAN code. The driver simply activates the scan at the touch of a button, and is otherwise able to fully concentrate on driving and lifting the pallets; eliminating the need to handle the scanner. This saves time and enhances safety with the high volume of forklift trucks and trucks in the goods issue area.
Wanted: Robust identification technology
While the idea of installing fixed mount barcode readers to the forklift truck masts seems good
in concept: It
22 | Worldwide Engineering Magazine
Fortunately, the logistics operations team evaluated Cognex DataMan 360 Series image-based barcode readers. They are ideally suited for robust industrial barcode reading applications — as they have no moving parts and are designed from the ground up to withstand tough environments.
Image-based barcode readers prove themselves Christian Ludwig, a Business Solutions specialist at Jetschke, chose to use the DataMan 360: “Because the software is already integrated into the reader, the devices are robust, easy to install, and are easy to adapt to the individual requirements of the application. The large depth of focus of the optics and the very high read rates, even under unfavorable conditions, are also advantageous.” The labels with the codes on them are often creased or partially torn due to the harsh environmental conditions. Nonetheless, the barcode readers at Flensburger brewery achieve continuously high read rates thanks to Cognex’s robust decoding algorithms. Even creased, torn or reflective codes can be read with the image processing-based devices’ robust decoding algorithms
Flensburger brewery uses additional numeric coding on their pallet markings next to the barcode, so minor adjustments were required and were quickly completed. Christian Ludwig: “We also equipped the readers with a splash guard as they are used outdoors.”
The forklift drivers no longer need to read the codes with handheld scanners, but only need to push a button to trigger the scanning process. This new solution brought huge time and cost savings, both through the modified scanning process, as well as eliminating the additional expenses associated with fixing damaged, unread codes. The masts of six Linde forklift trucks in the logistics center have been fitted with Cognex’s DataMan readers and the solution is proving a success.
For more information visit: https://www.cognex.com/

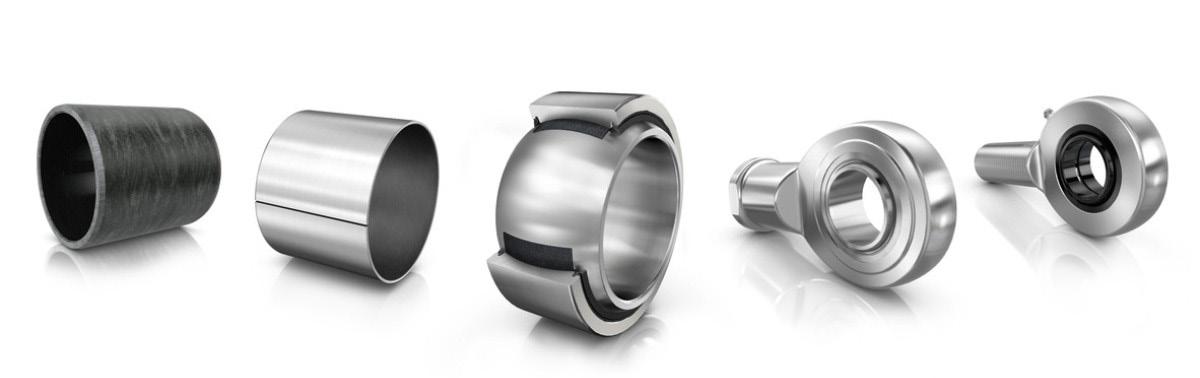
• Schaeffler, a technology leader in the field of plain bearings, looks back on decades of development and consultation experience • Broad and proven portfolio of standard and special designs for a wide range of different applications • Plain bearings with ELGOGLIDE fabric make cost savings and eco-friendly designs possible thanks to freedom from maintenance
This year marks the 75th anniversary of Schaeffler’s plain bearings: Helmut Elges founded “Mechanische Werkstätten Helmut Elges GmbH” in Bielefeld on August 1, 1945. The company began focusing on spherical plain bearings and plain bushes early on, and was responsible for developing many of the products now available as standard on the market, as well as several of today’s valid plain bearing standards. From 1984 onwards, INA and FAG – then separate companies operating on the market – held equal shares in Helmut Elges GmbH until its complete integration into the Schaeffler Group in 2002. The ELGES product brand was retired in 2017, and plain bearings from Schaeffler have been available on the market under the INA brand since then.
“Plain bearings are an indispensable part of our extensive portfolio, and there are a great many applications that could not run stably and reliably without them. We also work closely with our customers from the early stages of the design process onwards in order to generate added value for every bearing position,” explains Marcus Eisenhuth, CEO Industrial Europe at Schaeffler.
Extensive and proven portfolio – and everything from a single source
With its extensive range of sophisticated products, Schaeffler has been one of the technology leaders in the field of plain bearings for many years: this range includes spherical plain bearings with bore diameters of up to 1,500 mm, plain bushings and rod ends with bore diameters of up to 200 mm, and customer-specific solutions. During the 1960s, Schaeffler succeeded in making two important developments: the first of these was the creation of the sealed spherical plain bearing design, which brought about the company’s breakthrough in the construction machinery and commercial vehicle industries. The second was the development of the ELGOGLIDE PTFE fabric, which allowed maintenance-free spherical plain bearings to be made. At the same time, ELGOGLIDE also offers specific damping properties that enable it to withstand both high static shock loads and alternating loads. The continuous further development of Schaeffler’s plain bearings opened up one new application area after another. The option of freedom from maintenance allows users to create eco-friendly designs and to reduce construction and operating costs by minimising size and eliminating maintenance outlay.
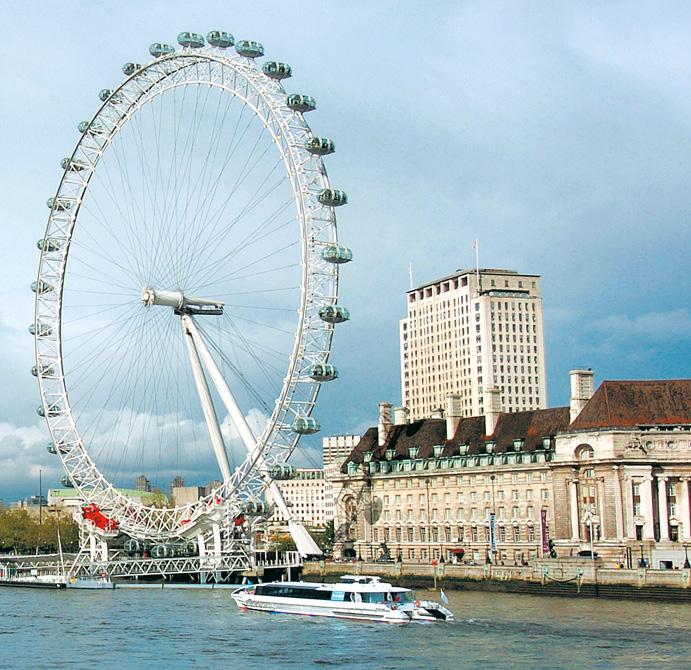
Safety and stability: not restricted to the construction industry Hydraulic cylinders for moving construction machinery, grinding rolls in cement mills, continuous casting plants in steel mills, rotor blade adjustment drives in wind turbines, pivot joints for optimum steering capability in road rollers, train doors and bogeys, escalators, and airport baggage retrieval belts: all of these applications require plain bearings. In construction projects, plain bearings are implemented at particularly sensitive interfaces such as the glass roof of Berlin Central Station. This roof structure, which covers around 300 metres of railway platform, is comprised of trussed frames into which countless spherical plain bearings and bolt systems from Schaeffler are integrated. These provide the necessary length compensation in the steel structure when external influences (particularly the wind) act on it. At Wembley Stadium, on the other hand, the weight of the roof structure rests on just two bearings: these each support 7,500 tonnes and have been designed for an operating life of 100 years. Turkey’s Osman Gazi Bridge went into operation in 2016. Schaeffler supplied 109 spherical plain bearings and 72 bushes for the points at which the individual bridge segments and bridge cables are connected to the foundations. The region to the south of Istanbul is known for its particular susceptibility to earthquakes. The bridge was therefore designed to continuously compensate for any vibrations, motions, and loads that might occur. The London Eye ferris wheel was raised from its horizontal assembly position across the river Thames into its vertical operating position with the help of two large-size spherical plain bearings from Schaeffler – with contact pressures reaching up to 450 N/m2. In operation, these bearings compensate for the micro-movements caused by the wind – a job they have been doing now for more than 20 years. The spherical plain bearing manufactured by Schaeffler in 2019 – with an outside diameter of 1,900 mm and weighing 4.7 tonnes – was the largest spherical plain bearing in the company’s history to date. It was installed in a cutter dredger – a working ship that is used to remove solid material from the bottom of a body of water and transfer it onto land. Because this application presented such special requirements, a customised bearing was designed.
August 2020 marks the 75th anniversary of Schaeffler’s plain bearings (shown here from left to right: An ELGOTEX plain bush, a metal-polymer composite plain bush, a spherical plain bearing with ELGOGLIDE, a maintenance-free rod end, and a rod end requiring
maintenance). The trussed frames of Berlin Central Station’s glass roof are equipped with countless largesize spherical plain bearings and bolt systems from Schaeffler. These provide the necessary length compensation in the steel structure when external influences (particularly the wind and temperature fluctuations) act on it.
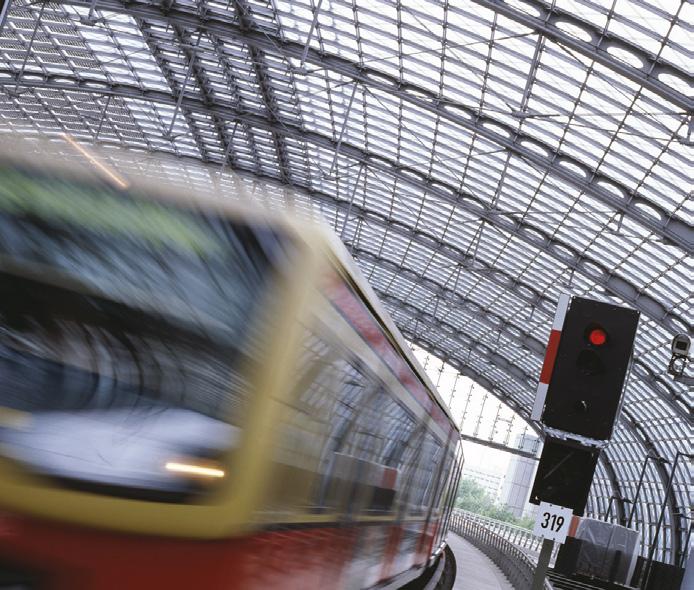
The London Eye ferris wheel was raised from its horizontal assembly position across the river Thames into its vertical operating position with the help of two large-size spherical plain bearings from Schaeffler. In operation, these bearings compensate for the micromovements caused by the wind – a job they have been doing now for more than 20 years.
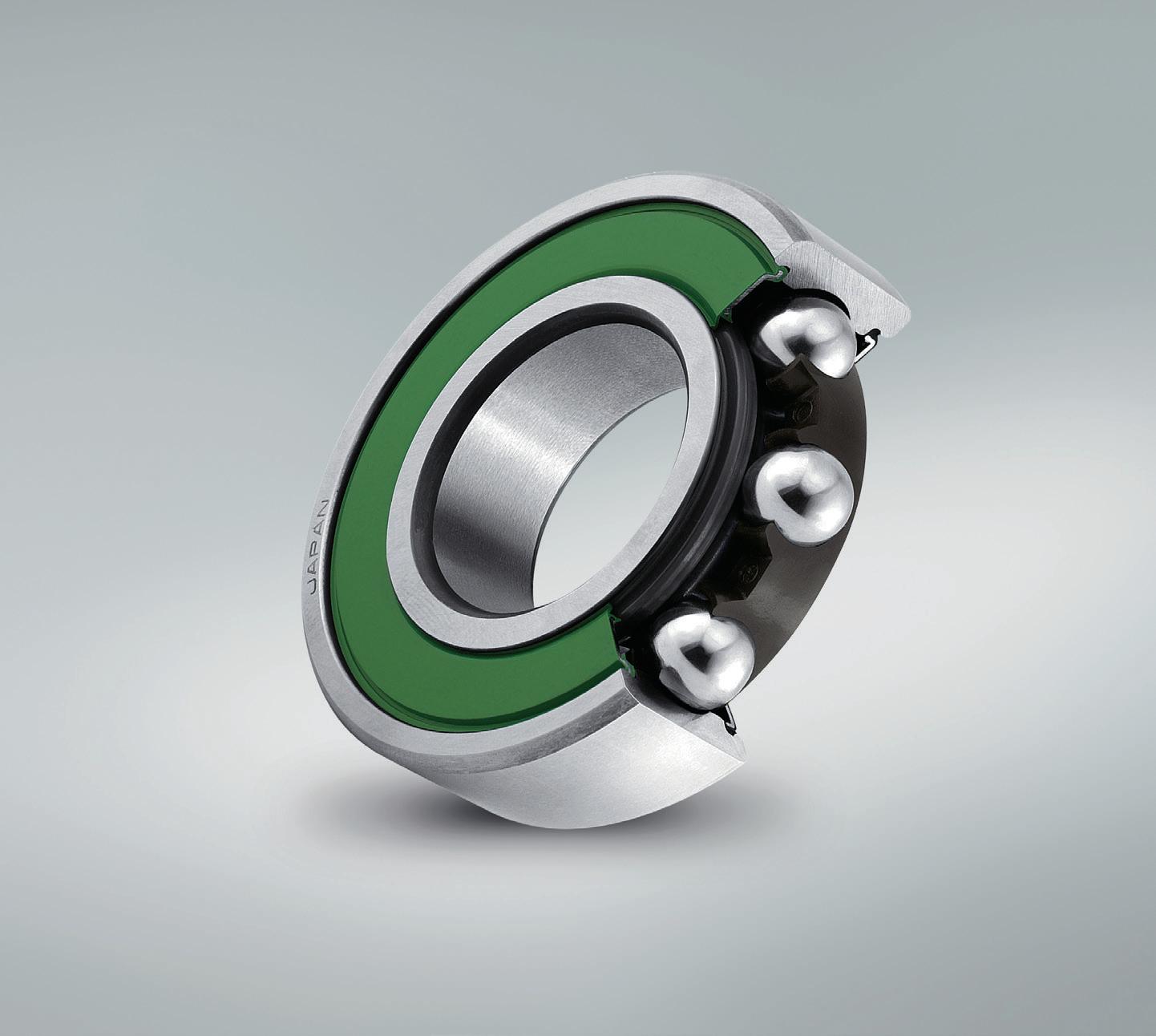
Available from NSK is a range Potential consequences include of deep groove ball bearings the generation of local microadapted to the specific friction points on the raceways. requirements of servomotors. This friction is caused when the Thanks to the development of lubricant film is insufficient and special greases and a highly metal-to-metal contact occurs effective, low-friction seal, between the raceway and ball. NSK solutions overcome the limitations of conventional electric motor bearings when used in servomotor applications. To surmount these issues, NSK has developed a special grease known as EA7. Compared with conventional greases, EA7 offers For rolling bearings, servomotors present a challenge. With their frequent start, stop and reversing operations – as well as tiny corrective movements prompted by the sensor system – the typical motion profile of servomotors places bearings under intense stress. Furthermore, the frequent reversing and associated microvibration cause the lubricant improved lubricating properties when subject to microvibrations. The grease also helps to ensure that the bearings operate with low frictional torque and correspondingly minimal power loss. In practice, the use of EA7- lubricated bearings in servomotor applications leads to longer operating life and the doubling of service intervals. film between the rolling Another factor that increases element and running surface the service life of servomotors to be wiped away (without the is cleanliness during operation. opportunity for after-flow re- If the bearing grease releases lubrication) to a greater extent particles (such as metal or than would be the case with sulphur) that migrate to continuous rotating bearings surrounding components, the used in conventional electric encoder may become dirty. Over motors. time, this contamination
26 | Worldwide Engineering Magazine
will render the motor incapable of detecting precise position. A further consequence of escaping lubricant can be slippage during braking, which again might promote inaccurate positioning.
To provide a solution to the contamination issue, NSK has developed another grease for servomotor applications, called LGU. Compared with lithium soap grease, LGU emits around 90% less sulphur and metal particles, thus contributing to the long-term cleanliness of the bearing environment. The result: service intervals are extended by a factor of 1.5.
Companies building or integrating servomotors can choose whichever grease is most suitable. EA7 extends the service life of deep groove ball bearings when subjected to the micro movements typical of servomotors, while LGU minimises the release of particles on to surrounding components, preventing imprecise positioning. These two high-performance greases are available as an option for the deep groove ball bearing series that NSK has developed for use in servomotors.
A further feature of these bearings is NSK’s DW seal, which offers a combination of exceptionally good sealing and low frictional torque. With DW seals, the company’s designers have developed an effective solution to the conflicting requirements of reliable sealing and energy-efficient bearing operation.
The range of deep groove ball bearings for servomotors is described in a new catalogue entitled ‘Bearings for Electric Motors’, which is available in print or as a PDF download at:

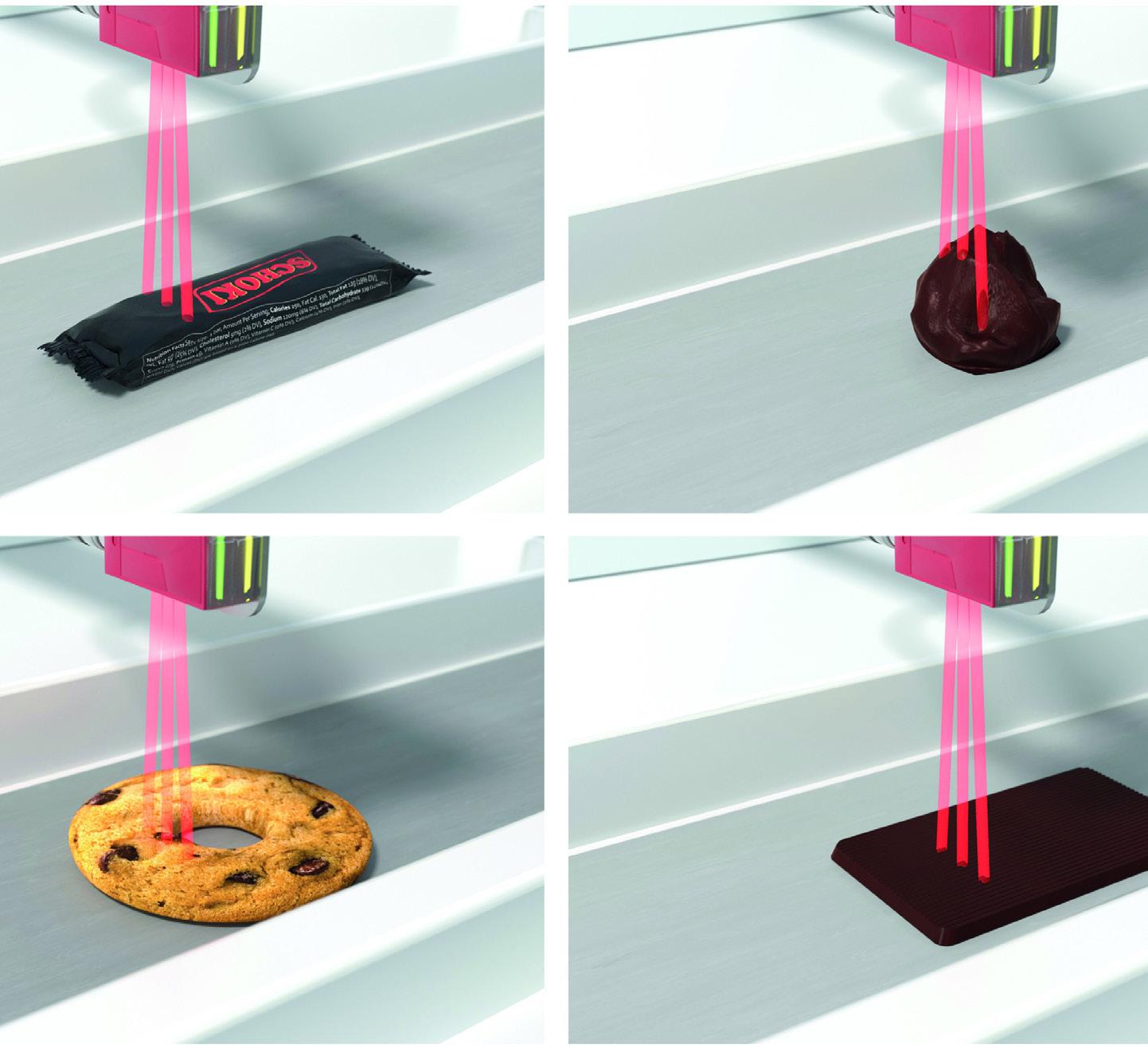
With the DRT 25C dynamic The more than 1,200 Sensor reference diffuse sensor, Leuze People worldwide view has brought a new operating themselves as forerunners principle to the market in the for their customers. Leuze area of optical sensors. At the has registered more than 200 heart of the invention is the patents in the last 10 years innovative CAT technology, alone. This all with the goal of which transforms a simple ensuring the lasting success of diffuse sensor into a highly their customers in an industry intelligent device. This can be that is ever evolving. Not only do seen in the DRT 25C’s clever the Sensor People have decades mode of operation: it is taught of experience but also in-depth in on a reference surface at the application know-how in their press of a button which allows specific focus industries. One of it to reliably detect nearly every these is the packaging industry, object – independent of shape, which, with throughputs of color and surface structure. several hundred thousand The reference surface can be a products per day and finely machine wall, a piece of sheet tuned process steps, places metal, or even a vibrating, extremely high demands on the moving conveyor belt. This optical sensors. Clear-glass retromakes the sensor particularly reflective photoelectric sensors well suited for use in packaging require less maintenance systems, especially in the area of through smart tracking. Thanks confectionery and baked goods. to line-shaped light spots, laser No readjustment is necessary diffuse sensors detect objects when changing objects. – no matter how complex – on their front edge. Extremely Leuze developed its first powerful through-beam optical sensor almost 60 years photoelectric sensors detect ago. Numerous technological the chocolate bar in its outer milestones and innovations have packaging with completely followed since then. harmless infrared
28 | Worldwide Engineering Magazine
light. The intelligent CAT technology, which the new DRT 25C dynamic reference diffuse sensor uses, continues the idea of the clever sensor. Our goal: detection on a running conveyor belt Packaging and the objects to be packaged vary widely in color, shape and surface structure: flat, glossy, transparent, with gaps or holes – the entire spectrum. As a result, they are not so easy to detect. However, that is the task of optical sensors in packaging systems. The challenge in object detection is in detecting as quickly and reliably as possible and ideally directly from above. At the same time, the working environment poses a challenge as well: the objects that are to be detected are usually on conveyor belts that move and vibrate and which may become soiled or wet. The sensor solutions currently on the market have so far only been able to perform this task to a limited extent. Thus, there was a need for precisely such an intelligent model. CAT Technology: Contrast Adaptive Teach This market requirement led to the development of the CAT technology at Leuze. CAT stands for Contrast Adaptive Teach. The underlying idea is simple: if the object can change at any time, use its environment instead as a constant reference surface. In packaging systems, this is the conveyor belt. This serves as a teachable reference. Once the sensor has been taught the contrast information of the conveyor belt, it only needs to be intelligent enough to adapt this knowledge to a possible change of environment. This is precisely what CAT technology does. Operating principle of dynamic reference diffuse sensors The new DRT 25C dynamic reference diffuse sensor uses
the CAT technology in a new operating principle: it learns the signal parameters of the conveyor belt at the press of a button and stores them as the “standard zero.” Every object that is transported on the conveyor belt now generates a signal. If this deviates from the zero state, the DRT 25C reliably detects the object as a “deviation from the reference.” The performance of the device is optimized through the choice of teach level. There is, for example, a teach routine for conveyor belts that become heavily soiled over time. Another teach level exists especially for the detection of very flat or even transparent objects. Once the sensor has been “taught,” no additional settings or readjustments are necessary. Not even if the object is changed, as the sensor operates together with the conveyor belt as a reference. Reliable detection increases the throughput If, for example, a chocolate bar is not reliably detected, a failure quickly occurs in the subsequent, precisely cycled packaging, which must then first be removed and cleaned. The more reliably the sensor detects the product, the less frequent unplanned maintenance needs to be performed. Herein lies the strength of the DRT 25C dynamic reference diffuse sensor, which operates reliably even with difficult shapes and surfaces. This increases the machine throughput, the production quantity and avoids downtime. Because no adjustment work needs to be performed on the sensor when changing products or changing the packaging materials, setup time is also reduced, further increasing output quantities. Up to now, a format change – such as from the classic 100 g bar of chocolate to a mini chocolate cube – meant that sensors had to be readjusted. However, because the DRT 25C uses the conveyor belt as a reference, this is no longer necessary. Even if the color, height or contour of the packaging changes, no settings need to be made at all on the dynamic reference diffuse sensor. The all-rounder based on CAT technology The DRT25C dynamic reference diffuse sensor represents a new operating principle that is based on the new intelligent CAT technology. It thereby sets new technological standards on the market and is another milestone in the innovation history of Leuze. Once again as forerunners, the Sensor People thereby precisely meet their customers’ requirements for reliable detection and make them successful in an industry that is ever evolving. After all, the success of their customers is their aspiration and goal. Reduced downtimes, increased machine throughput as well as higher production quantities, all with maximum flexibility without readjustment when changing objects – that means increased cost effectiveness for their customers.
For more information visit: www.leuze.com/drt25c
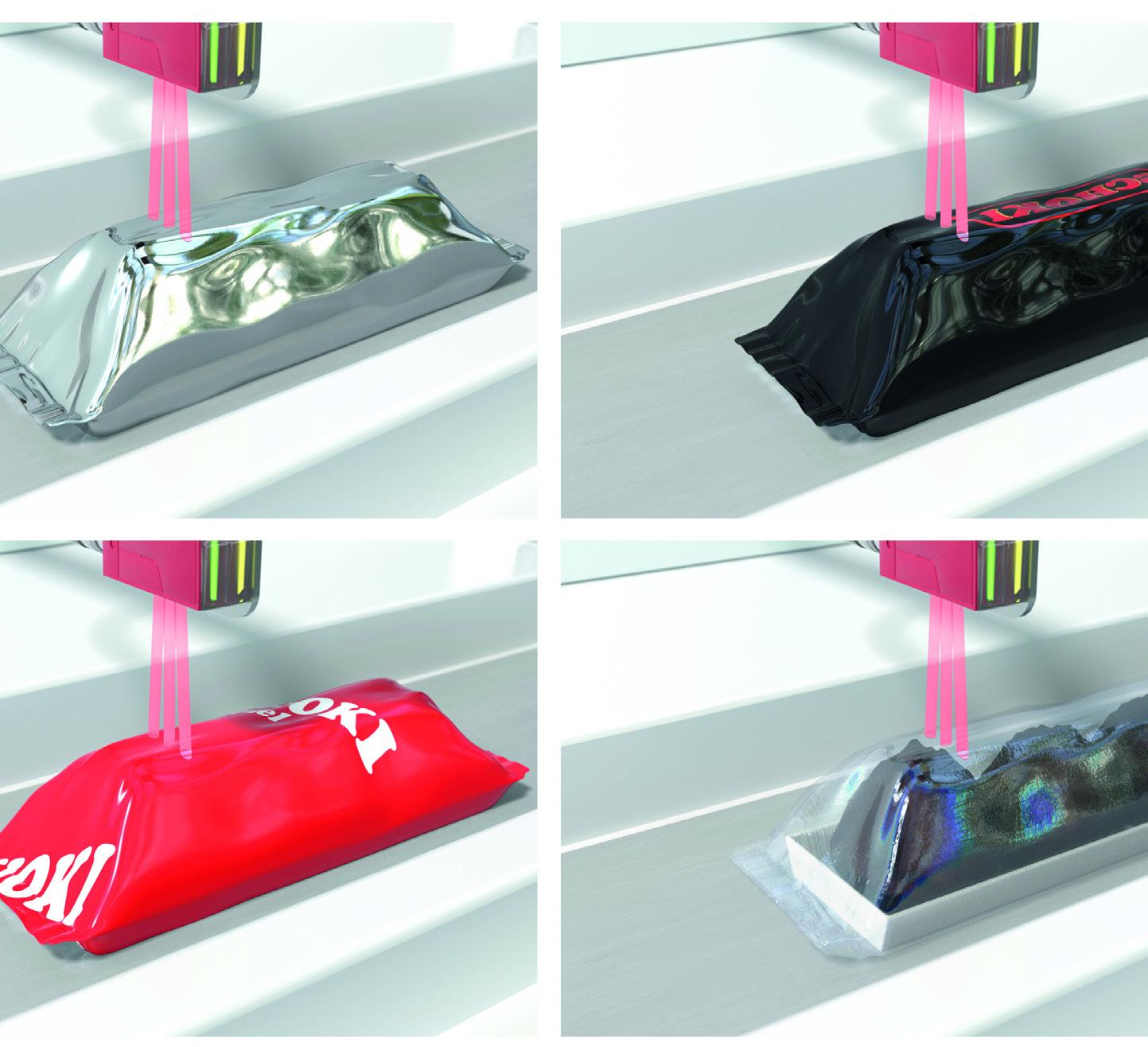
ACEINNA, one of the world’s leading developers of inertial based guidance and navigation systems for autonomous vehicles and devices, today announced the availability of their new ACEINNA OpenIMU ROS Driver for developers of robots and robotic applications. “This new ROS driver makes it simple to integrate a wide variety of ACEINNA IMUs (Inertial Measurement Unit sensors) into almost any robotics applications (warehouse robotics, autonomous vehicles, last mile deliver robotics, etc.), which uses ROS,” says James Fennelly, Product Marketing Manager – Inertial Systems at ACEINNA. “When combined with our IMU’s industry leading reliability and accuracy, as well as very competitive pricing (under $100), developers of robotic solutions finally have an easily integrated, rock-solid solution for their navigation and localization challenges.” Available on the Sensors Page at ROS.org and GitHub this new driver enables robotic application developers to quickly and easily integrate highly accurate (<1.5/hr) IMU’s into their navigation guidance systems. versatile OpenIMU family, which includes the OpenIMU300ZI, OpenIMU300RI, and OpenIMU330BI. Each sensor has its own distinct hardware features, allowing the user several options for their unique application. The open-source nature of this architecture makes each device highly configurable as well. ACEINNA’s OpenIMU’s have several software applications available, with source code available via Github and the ACEINNA Extension on Microsoft Visual Studio Code. Software applications include IMU, VG-AHRS, and INS.

Extremely compact, ACEINNA’s IMUs integrate a tripleredundant architecture, that, when combined with their small, low-cost packaging, meets the challenging performance, reliability and cost requirements of the robotic and autonomous market.
The Robotic Operating System (ROS) is a set of software libraries and tools that help developers create robotics applications. It can be described as a software development kit (SDK). As stated on ROS.org : “The ROS user community builds on top of a common infrastructure to provide an integration point that offers access to hardware drivers, generic robot capabilities, development tools, useful external libraries, and more.” This allows users to get their robotics projects up and running a lot faster than starting from scratch.
Combining the architecture of the ROS environment with the versatility of the OpenIMU platform the possibilities are endless and at the users fingertips.
For more info on the ROS Driver, please visit this page: wiki.ros.org/aceinna_openimu
For more on the OpenIMU family, please visit this site: www.aceinna.com/
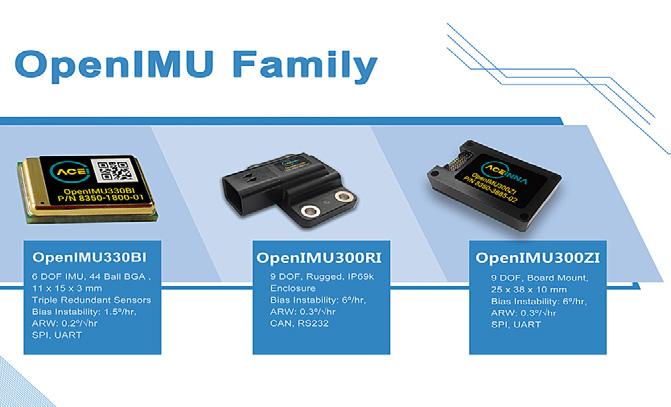
Nexperia, the expert in essential semiconductors, has introduced four new TrEOS ESD protection devices that are AEC-Q101- qualified for automotive use and high temperature capable up to 175°C. In common with all TrEOS components, the new parts combine extremely low capacitance ensuring high signal integrity, extremely low clamping and high robustness for modern automotive interfaces. Specific automotive applications include infotainment, multimedia and ADAS systems featuring USB 3.2, HDMI, LVDS, SerDes and SDcard interfaces.
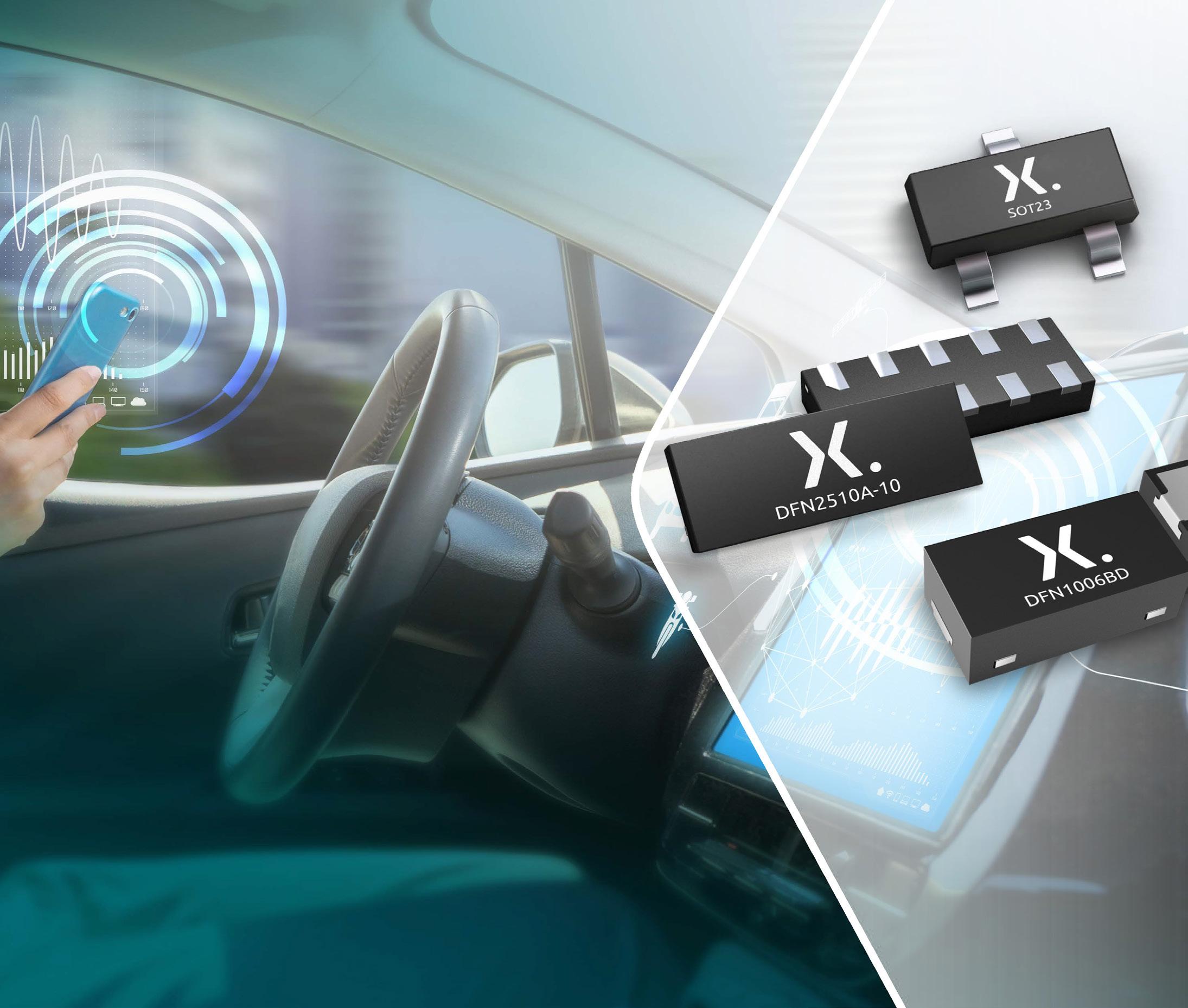
controlled rectification to overcome the traditional protection trade-off challenge. Capacitance is kept down to 0.5 pF, clamping voltage is just 3 V and devices can withstand surge and ESD pulses up to 10 A 8/20 µs. This industry-leading performance in all areas is delivered in the extensivelyproven SOT23 package.
Lukas Droemer, Nexperia product manager commented: “Our TrEOS technology has set the industry benchmark for mobile and computing ESD protection since its launch in 2015. Now, as there is a demand for more and more connectivity in vehicles, Nexperia is continuing to qualify its TrEOS ESD protection portfolio for the automotive sector. With these new parts, automotive design engineers can empower their new systems with the efficiency of TrEOS ESD protection while improving system-level robustness.” The first four PESD2USBx-T series AEC-Q101-qualified TrEOS ESD protection devices are in mass production now. More information including product specs and datasheets is available at www.nexperia.com/automotiveinfotainment-serdes

Since partnering with Inovaxe a year ago, Altus Group, a leading supplier of capital equipment in the UK and Ireland, has seen increasing interest for the company’s smart storage solutions which offer ultra-lean material handling processes, particularly in light of the ongoing pandemic.
Altus distribute Inovaxe’s entire range of products which includes hardware and software to streamline material handling and accuracy issues in electronics’ manufacturing operation. The equipment can easily pull kits in minutes, reduce errors, increase machine uptime, and importantly help to reduce man hours, an important feature as companies look to increase remote working and build on safe working practices for employees.
Mike Todd, Quality and Operations Manager, Altus Group said: “Covid-19 has meant manufacturers have had to think on their feet and look
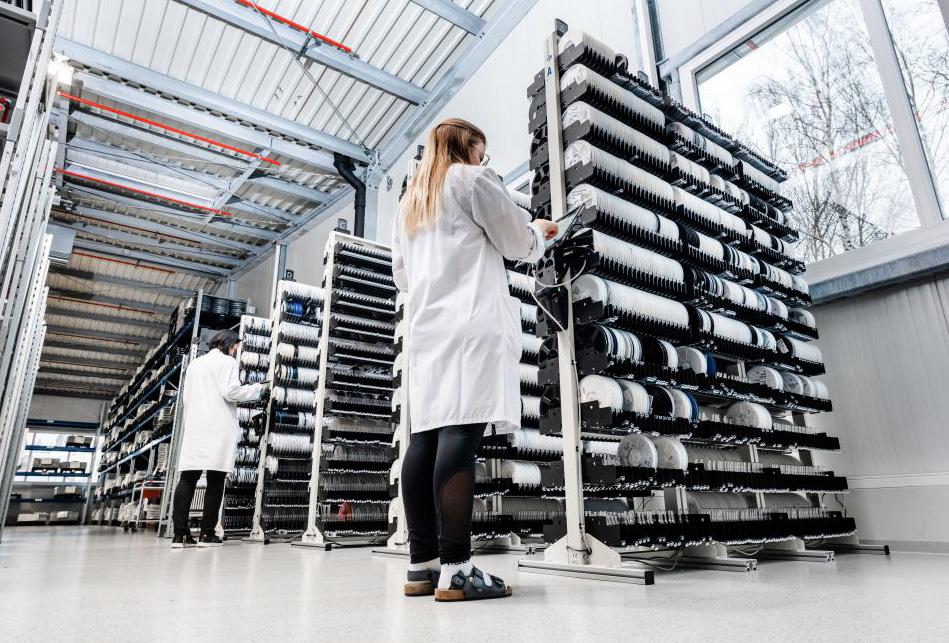
at ways to streamline their manufacturing processes. They have had to make it even smarter and adapt their business strategies to work with a reduced workforce. Thanks to companies like Inovaxe, we are able to offer solutions to help the electronics industry continue to manufacture products effectively and efficiently.
“As a world leader and provider of innovative material handling and inventory control systems, OEM and EMS providers can not only increase their accuracy, but also reduce machine set-up times, decrease load times and easily recognise any shortages. There is also the extra benefit that the equipment helps to reduce parts handling, an important safety feature in today’s production process.”
Inovaxe has a total production and inventory management solution that addresses business issues that directly impact bottom-line revenue as well as minimise business risk. The innovative equipment has been designed work within a number of industry sectors including electronic manufacturers, CNC machine shops, plastics manufacturers, as well as a variety of assemblytype houses. Inovaxe’s smart storage solutions store hundreds of reels per square foot with the capability to access parts in seconds. Each smart location is configured to fit a specific reel size, therefore reducing storage space. Only one operator is required to utilise the smart reel storage solutions which detect when reels are added or removed, and light up required parts for retrieval using sensors and LEDs found at every location. The InoAuto software used with the system tracks each individual reel, providing enhanced inventory accuracy and full traceability.


In modern processing centers, inductive sensors are the components of choice for monitoring the motor spindle clamping process. Integrated into the spindle, they must be exceptionally small and offer high repeatability to ensure smooth tool changing at all times. Baumer offers a high-performance portfolio of miniature sensors for the intelligent design of effective spindle solutions. This can either involve a classic design with three switching sensors or a smart design with one measurement sensor.
Tool change in fully automated processing centers, from removal until the insertion of the new tool in the spindle, takes less than a second. To achieve maximum system effectiveness, this process must function with ultimate reliability. The error-free functioning of the smallest inductive sensors plays a major role in ensuring this. For the processing center to function error-free, the machine control requires the following key information regarding the status of the collet chuck: open and no tool clasped, closed and no tool clasped, or closed and tool clasped. The answer to this challenge are inductive sensors. The task can be handled using either one measurement sensor or three switching inductive sensors. Largest portfolio, smallest sensors
In drive and clamping solutions, the sensor technology is integrated in the motor spindle. Given this confined space, the sensors must therefore be as small as possible, yet very powerful – characteristics found in the sensors from Baumer. The Swiss sensor manufacturer offers the market’s largest portfolio of miniature and subminiature inductive sensors with micrometer measuring accuracy. One example is the inductive proximity sensor IFRM 03 with a diameter of only 3 mm. It is available in various lengths starting at a mere 12 mm. Yet its miniature housing contains the complete evaluation electronics that are responsible for the high-repeatability switching points as well as the precise analog measurement values. In addition, these industrial-grade sensors are robust, EMC-stable, and comply with the protection class IP 67. The sensors remain unaffected by heat, oily environments, and vibrations that normally occur in tooling machines. This is where the decades of experience of Baumer in miniature sensor technology come to play.
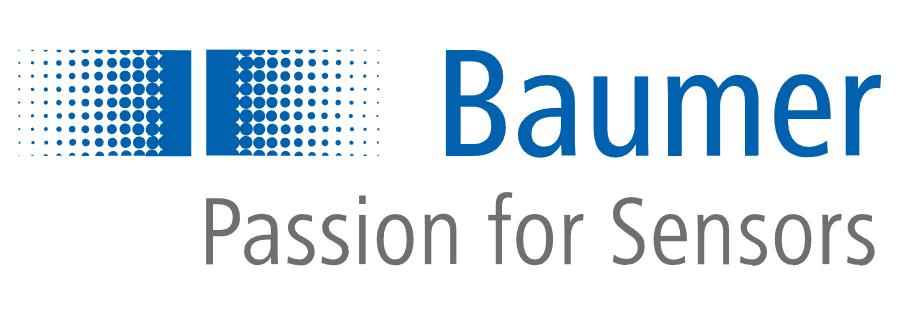
Measuring instead of switching Rather than detecting the three positions of the drawbar with switching sensors, an analog inductive distance sensor offers an alternative solution. It requires a steep angle taper on the drawbar rather than a retainer. With a steep angle taper connected to the drawbar, it is possible for the measuring sensor to detect the position of the drawbar and thus recognize the state of the collet chuck. The distances or the respective clamping values that are evaluated by the control can be allocated to the three positions of the bar. The use of a measurement sensor offers a number of advantages – on the one hand, the sensor requires less space than three individual switching sensors and also less mounting effort. On the other hand, the sensor constantly monitors the state of the tool clamp. This makes it possible, for example, to detect when the tool becomes loose or is not clasped centrally. This may happen if chips fall between the spindle and the tool. It can result in damage to the tool or quality problems of the machined part. The precise sensors from Baumer optimize the repeatability of the tool clamping. This minimizes a potential lack of concentric runout of the used tool or detects it early on. A measuring sensor improves the reliability of the clamping system while ensuring both the quality of the processing as well as system availability, which is reflected in increased overall system effectiveness. This requires micrometer precision
of thesensor, a detection range that is as large as possible, and a limited temperature drift. In this regard, AlphaProx, the smallest inductive distance sensors from Baumer, offer the highest performance on the market. The reliable measured values and high precision ensure users a maximum reproducibility for tool tensioning. Baumer has introduced one of the smallest distance measurement inductive sensors on the market – the inductive analog sensor IF08. This product series has a box-shaped housing measuring 16 x 8 x 4.7 mm. Nevertheless, it contains the entire evaluation electronics and a drilled hole for flexible mounting even in confined mounting spaces. Its measuring distance is 2 mm with an output signal of 0 – 10 VDC. Flexible with IO-Link Even greater flexibility is offered by the miniature distance measurement inductive sensor of the IR06 series with digital IO-Link interface with a housing that is only 6.5 mm thick and 46 mm long. The standardized interface allows the easy integration of the clamping process into the control. The collected data can be recorded and evaluated via a histogram. This allows the early detection of measurement deviations and facilitates required error analyses. For example, the smallest changes in the process can be detected via the vibration and addressed before the machined part is damaged. The sensor also provides additional diagnosis data, for example, the temperature of the sensor, which the tooling machine designers can use to indirectly recognize the heating up of the spindle. In addition, the sensor offers all the advantages of IO-Link, such as easy parameterization and quick commissioning of a replacement sensor, by downloading the parameters

from the IO-Link master based on the parameter server function.
No restrictions with sensors from Baumer
The comprehensive portfolio of miniature inductive sensors offers users maximum flexibility for reliable solutions in the tool clamping process. The customer can choose whether the clamping process is monitored by switching sensors or a measurement sensor – without restrictions or limitations. The miniature analog sensor records the position of the drawbar through different distances or clamping values from the steep angle taper that are evaluated in the control. This way, the three states of the collet chuck are transferred to the control.
For more information visit: www.baumerencoders.co.uk
New Laser Triangulation Sensor Offers Unique Combination Of Size, Speed And Accuracy For A Wide Range Of Control And Automation Tasks
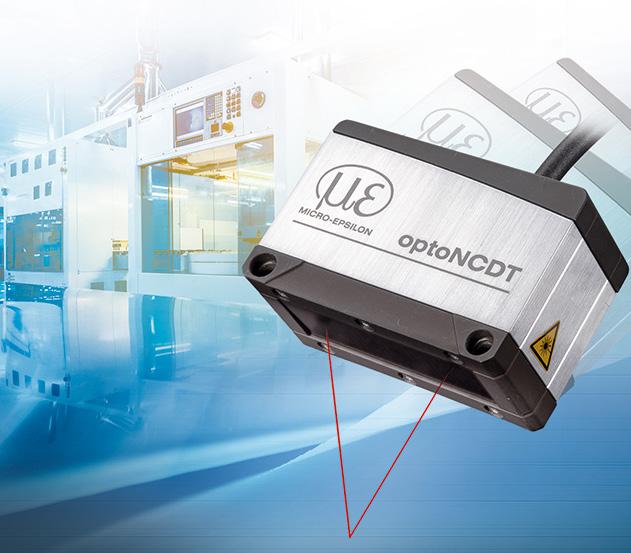
Precision sensor manufacturer Micro-Epsilon continues the development of its comprehensive laser triangulation sensor range with the addition of the optoNCDT 1900. Ideally suited for both dynamic and high resolution measurement tasks, it features a completely new compact sensor housing with innovative mounting sleeves that ensures a repeatable sensor position and alignment to the target. This new performance class of laser sensor is perfect for high speed distance, displacement and position measurements in a wide range of automation tasks, including machine building, robotics, automotive production, 3D printing and coordinate measuring machines. The new optoNCDT 1900 laser triangulation sensor offers a unique combination of speed, size and performance. The sensor itself has dimensions of 70 x 31 x 45mm and weighs just 185g. The measuring rate is continuously adjustable up to 10kHz and can be individually adapted to suit each measurement task. Newly developed, high performance optics create a small spot size onto the target, which enables tiny objects and surface details to be measured. A new larger aperture for the receiver ensures greater accuracy and repeatability when compared to other sensors of similar measurement range. The sensor itself is also extremely robust with the ability to withstand high shock and vibrations, like those seen in vehicle testing, as standard. Two-stage averaging For the first time, a two-stage measurement average is available for signal optimisation. This enables the sensor to provide a clean signal output at edges and steps. The high performance averaging ensures a stable, precise signal output and is particularly suitable for high speed measurements of fast moving parts. The sensor uses the newly developed Advanced Surface Compensation (ASC) algorithm that allows it to operate almost regardless of the target material and colour. The exposure time or amount of light produced by the laser sensor is optimally matched to the reflection characteristics of the target surface, which enables reliable measurements even of difficult, changing surfaces. The sensor is extremely resistant to ambient light interference and so can be used in high illumination environments including those situations where lasers are combined with Vision Systems and their associated LED lighting. The new software algorithms compensate for ambient light up to 50,000 lux, which means operation in direct
sunlight is also improved.
Mounting sleeves and highly
flexible cables Mounting the sensor is also fast and easy, with new fitting sleeves provided that automatically align the sensor in the correct position. This enables both easy sensor replacement and ensures continued high precision measurements to be taken with confidence that the new sensor is looking at the same point on the target. Highly flexible cables and a robust IP67 protected aluminium die cast housing make the sensor ideal for industrial use.
New advanced features for peak separation and peak width determination enable reliable measurements on coated materials, measurement objects located behind glass and on film-sealed components. Data output is via analogue or digital RS422 interface. By using the Micro-Epsilon IF2030 interface module, EtherNet/IP and PROFINET are also available.
For more information please call the Micro-Epsilon on 0151 355 6070 or email info@micro-epsilon.co.uk
FPT Industrial A Key Partner Of The Imperium Project Targeting 20% Fuel Consumption Reduction In Truck Transportation
Fuel economy is a key aspect to reduce operating costs and improve the efficiency of long- haul trucks, thus increasing truck competitiveness in the transport industry. A matter of great importance to FPT Industrial, as demonstrated by the Brand’s numerous inventions, innovations and patents, including the exclusive and unbeaten HI-eSCR2 aftertreatment system.
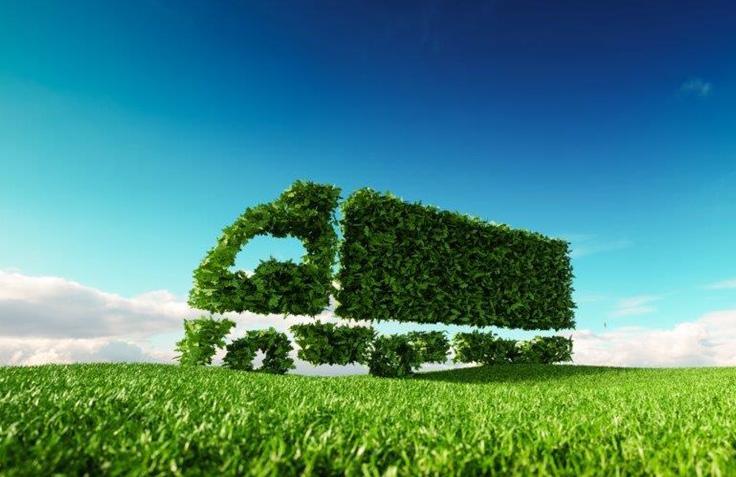
With higher efficiency in mind and under the aegis of the European Commission and the European Green Vehicles Initiative EGVI, a contractual Public Private Partnership (cPPP) dedicated to delivering green vehicles and mobility system solutions of the future, the IMPERIUM project (IMplementation of Powertrain Control for Economic and Clean Real driving EmIssion and ConsUMption) was created.
The project’s main objective was to achieve a 20% fuel consumption (diesel and urea) and consequently CO2 reduction compared to modelyear 2014 vehicle, whilst keeping the vehicle within the legal limits for pollutant emissions. This demanding challenge was taken up by the IMPERIUM consortium, grouping major European players: leading trucks and engine manufacturers, including FPT Industrial, systems and services providers, Universities and Research Centers.
The IMPERIUM consortium is responsible for 45% of the heavyduty vehicles manufactured in the EU and can provide a 100% European value chain for the development of future powertrain control strategies for trucks. The specific approach relied on a three-stage improvement of the control strategy: exhaust after-treatment, transmission, waste heat recovery, e-drive) to maximize performance. - Global powertrain energy management to coordinate the different energy sources and optimize their use depending on the current driving situation. - Providing a more comprehensive understanding of the mission, so that the different energy sources can be planned and optimized on a long term.
Since fuel consumption is directly linked to and influenced by the mission, the traffic and the environment, a simulationbased validation strategy was developed to better take into account these different scenarios. The overall objective is the development of new means of predictive and comprehensive powertrain control in an optimal way, exploiting the full potential of the individual systems for each vehicle application and mission. The newly developed components have been first validated on various platforms such as Hardware in the Loop (HiL), engine testbed and demonstrator trucks, including an IVECO STRALIS powered by FPT Industrial, and then further integrated into this environment for evaluation of their impact on the complete system. The IMPERIUM project developed and demonstrated optimal powertrain control and advanced powertrain concepts for heavy-duty vehicles, integration thereof into test beds and demonstration vehicles and proof of compliance with fuel economy targets (20% improvement compared to the same vehicle with conventional control with consequent CO2 reduction) and Euro VI standards under real driving conditions. IMPERIUM also developed a methodology to determine the fuel efficiency of heavy-duty vehicles and the compliance with Euro VI under real driving conditions based on a smart combination of simulations, measurements and tests.
For further information on this project
www.imperium-project.eu/ .
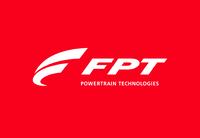
Delta Collaborates With Microsoft And The Consortium For On-Board Optics To Develop A POC 12.8Tbps Open Networking Switch
Delta, a global leader in power and thermal management solutions, today announced it has worked with Microsoft and the Consortium for On Board Optics (COBO) on the successful development of a leading-edge proof of concept (POC) open networking switch featuring 12.8Tbps bandwidth capacity as well as the seamless integration of five different optical module form factors in a single 4U rack, including eight ports with the highly promising COBO standard — offering up to 800G transmission speed and up to 30 percent energy savings. This innovative POC open networking switch underscores Delta’s capabilities regarding the research and development of next-generation data center infrastructure with leading transmission speeds and energy efficiency for the nascent 5G era.
Mr. Brad Booth, Microsoft’s Principal Network Architect and COBO’s President, said, “We are pleased to see Delta’s expertise in high-efficiency power electronics and in networking systems. Being capable of integrating COBO and other form factors into a single platform has been an

integral contribution to this POC project to enable end users to perform hands-on evaluation and testing. Cloud data centers will require the support of networking systems featuring increased transmission speeds and low carbon footprint, and COBO represents a prime opportunity to deliver on these essential requirements.”
Mr. Victor Cheng, Delta’s Senior Vice President and General Manager of its Information & Communications Technology Business Group, said, “With the development of this highly innovative POC COBO open networking switch, we have completed the first phase of a new chapter in the successful collaboration story with our long-time partner Microsoft.
The promising energy savings offered by the COBO optical form factor standard align perfectly with Delta’s longterm commitment to energy conservation and lower CO2 emissions, and therefore, we look forward to cooperating with Microsoft and COBO to accelerate the growth of the 5G megatrend with this inventive technology.” Delta is a Microsoft Gold Certified Partner and Azure Cloud Solution Provider. This collaboration is a great achievement after Delta and Microsoft launched a 5G smart manufacturing solution in June. Delta continually cooperates with Microsoft for the interaction of technology.
Delta leveraged its expertise in telecommunications systems to develop the 12.8Tbps COBO POC open networking switch with five different optical module form factors into a compact 4U rack. These include sixteen ports with the new COBO standard, which boasts up to 800 Gbps transmission speed (16 x 50Gbps) and energy savings as high as 30% when compared to similar peer technologies. The system also includes two 400G QSFP-DD, two 400G OSFP and sixty four 100G QSFP ports. Intel’s 8-core 2.0 GHz D-1548 Broadwell high-performance chip sits at the core of the Delta COBO switch.
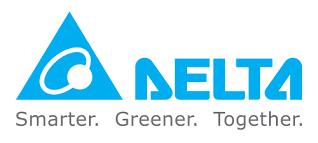

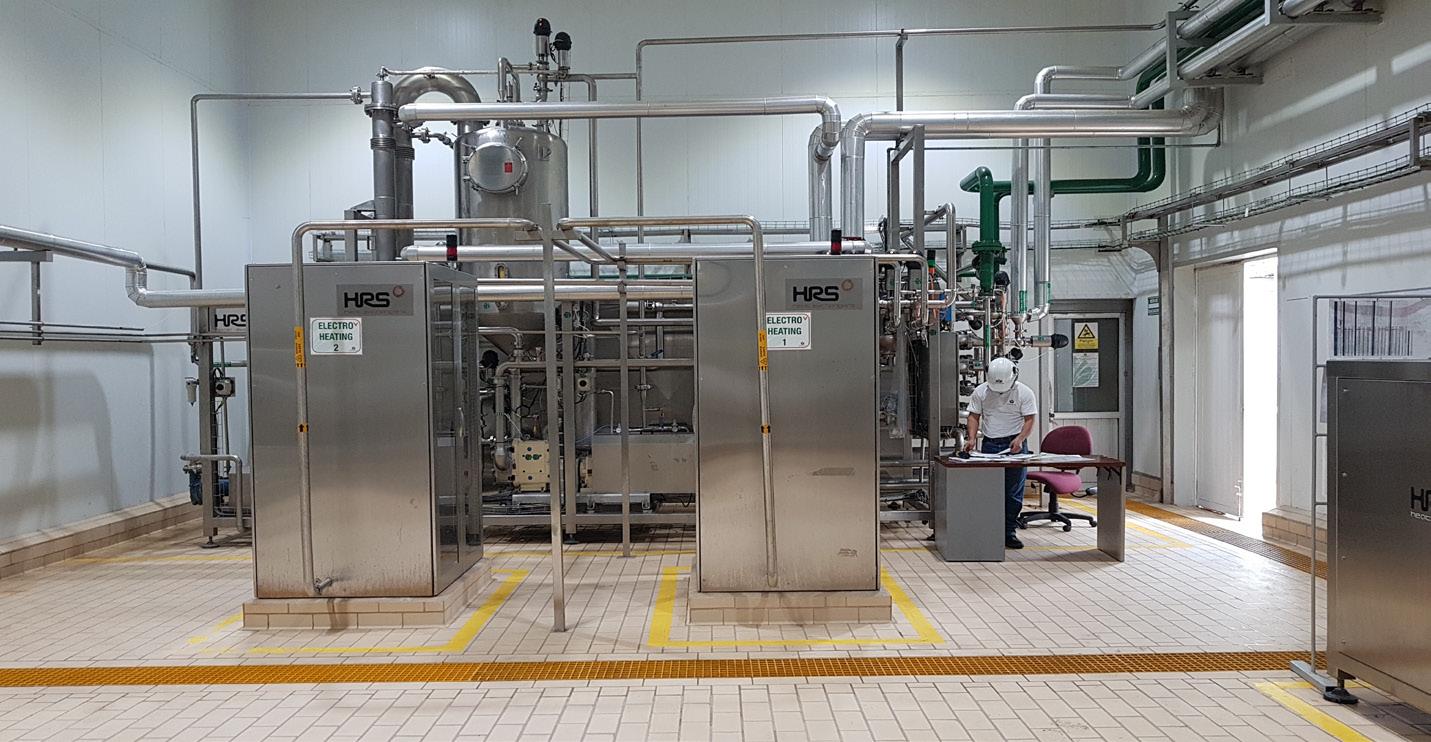
Modular process skids have • Ease of installation. Because become popular in the food the system is built at the industry due to their ease of manufacturer’s factory, once transportation and installation. it arrives on site it usually only HRS Heat Exchangers has needs connecting to the existing produced skid-mounted infrastructure and services, with versions of numerous products a minimum of in situ assembly. and systems, for a wide range This also reduces the disruption of applications including and down time required when pasteurisation, cleaning in place the skid is installed. (CIP), aseptic packing, heating, and cooling to name a few. • Quality of construction – Fabricating the skid in the What is a modular process skid? workshop means that all aspects of production can be controlled. It is not dependent on vagaries A modular process skid is a processing system which is contained within a frame, making it easier to transport and install. Individual skids can contain anything from a single heat exchanger and ancillaries such as weather conditions or working around the client’s existing production schedules. Therefore, no compromises are needed in terms of welding technique or the order of assembly. to complete and complex • Ease of transport – With systems where the skid typically everything contained in a contains process equipment, single unit, transport to the controls and monitoring site becomes much easier. It equipment, and ancillaries. also creates the potential to Process skids provide a ‘plug production lines or operating & play’ solution and multiple sites. skids can be combined into move smaller skids between larger systems. For example, a • Small footprint – By layering food pasteurisation and filling key components, skids can be system may contain separate made to a specific size and the skids for the pasteurisation heat overall footprint can be kept to a exchanger, the cooler, filler, and minimum. additional heat recovery heat exchangers. • Testing and approval – Factory acceptance testing (FAT) can be completed by the manufacturer Benefits of process skids before the skid is shipped to the client, helping to reduce startSome of the reasons that up and commissioning times. process skids have become so These numerous advantages popular include: deliver customer benefits
40 | Worldwide Engineering Magazine
in terms of saved time and money. In addition, process skids provide a combination of flexibility and robustness compared to traditional on-site building methods. Skids can be supplied in multiple sizes, from a typical 1x1.2 m pallet, up to a full 2.43 x 12.2 m shipping container. (CIP) system. Key elements were supplied on process skids to facilitate quick installation and ease of operation. • The HRS AF Series of aseptic fillers are supplied skid mounted as standard. • HRS has a range of trial units from heat exchangers to pilot plant evaporation skids, which are available for clients to prove the suitability of a particular model or technology prior to full system design. These are all skid mounted to enable easy transportation and quick set up on site. Examples of HRS process skids HRS is experienced in producing skids for food and beverage use using high quality stainless steel and frequently supplies systems built around process skids. Some recent examples include: • An orange juice pasteurisation system for a Mexican company which is comprised of a series of skid-mounted units which together form a turnkey pasteurisation, cooling and aseptic filling solution.
• Spanish social enterprise Nutripeople turns surplus fruit and vegetables into finished highly nutritional food pouches for use by organisations such as UNICEF and Oxfam. HRS provided the company with a new production line which includes tanks, mixers, pumps, a homogeniser and R Series scraped-surface heat exchangers for pasteurisation. These elements were supplied on process skids which were combined into a finished production line at Nutripeople’s factory in Murcia.
Implementing multi-channel system control or signal outputs using Digital-toAnalog Converters (DACs) in today’s portable and handheld industrial, communications, consumer and medical systems has been difficult to do without significant processor overhead for device configuration during power-up. Microchip Technology Inc. (Nasdaq: MCHP) today announced a solution to this problem with its MCP47/48FxBx8 family of octal 12-bit DACs, the first of their kind to include nonvolatile memory and an integrated Voltage Reference (Vref) source so they can be pre-configured for safe and efficient power-up without relying on the system processor.
“Handhelds and other portable systems are expected to deliver more capabilities in smaller, simpler designs,” said Bryan J. Liddiard, vice president of Microchip’s mixed-signal and linear business unit. “We help achieve this goal with the first DACs that eliminate processor overhead during power-up and provide the channel density, low power consumption and integrated features that today’s compact systems need so they

can operate over longer periods using smaller, lighter batteries.”
Unlike DACs that do not feature nonvolatile memory, the MCP47/48FxBx8 DACs can store user-customized configuration data even when powered down. At power-up, all eight channels are then configured to the pre-defined state without burdening the system processor with this overhead. Integrating a Vref source into the DACs reduces overall system size and complexity while providing the necessary control to meet critical timing needs for safely driving all power outputs. In addition, the device family offers both SPI and I2C serial interfaces to provide the designer with the most flexibility for device communications.
With an operating voltage range of 1.8V to 5.5V, the DACs’ low minimum operating voltage and high level of power efficiency combine to improve thermal performance and reliability. The DACs also provide power-on/ brown-out reset protection and one of the industry’s fastest settling times at 5 microseconds and operate in the extended (-40 °C to +125 °C) temperature range required for industrial and automotive applications.
Pricing and Availability The MCP47/48FxBx8 family of DACs is available for volume orders. The family includes 8-, 10- and 12-bit resolution devices in a 20-lead VQFN 5 x 5 mm package and a 20-lead TSSOP package. Pricing starts at $2.47 each, in 5,000-unit volumes.
For additional information, contact a Microchip sales representative, authorized worldwide distributor, or visit Microchip’s website: www.microchip.com.
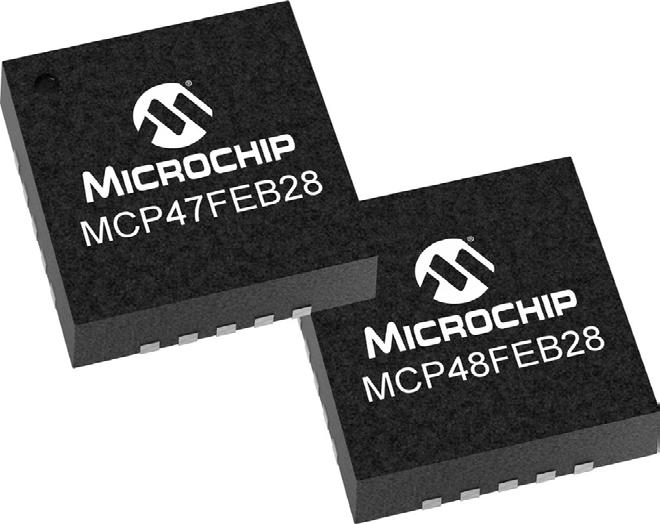
Monroe® Intelligent Suspension Technology Featured On New Volkswagen ID.3 Electric Vehicle
Lake Forest, Illinois – Owners of Volkswagen’s new ID.3 electric vehicle can benefit from a variety of innovative technologies, including an advanced semi-active suspension from DRiV that senses and adapts to changing road conditions for a more controlled and comfortable ride. DRiVTM is a Tenneco Inc. (NYSE: TEN) division and leading global provider of aftermarket and OE ride performance products and services. The ID.3 model can be equipped with a Continuously Variable Semi-Active suspension with external valve (CVSAe), one of several electronic suspension technologies available through DRiV’s Monroe® Intelligent Suspension portfolio. The system senses and continuously adapts to changing road and driving conditions via four electronically controlled dampers. An electronic control unit (ECU) processes various sensor inputs and controls the electronic valve on each damper. The driver can select a preferred driving mode, either Comfort or Sport, to experience the desired ride and handling characteristics. “The ID.3 is engineered to give drivers a very personalized and enjoyable ride,” said Henrik Johansson, vice president and general manager, Advanced Suspension Technology, DRiV. “We are excited to bring these benefits as an option to the owners of this appealing new vehicle from Volkswagen.”
The ID.3 is the first vehicle built on Volkswagen’s new modular all-electric platform. Designed to be both efficient and affordable, it offers a connected driver experience in a compact package that includes voice- activated controls, an “augmented reality” display projected onto the windshield, wireless device charging and extra interior space. Tenneco is one of the world’s leading designers, manufacturers and marketers of automotive products for original equipment and aftermarket customers, with 2019 revenues of $17.45 billion and approximately 78,000 team members working at more than 300 sites worldwide. Our four business groups, Motorparts, Ride Performance, Clean Air and Powertrain, deliver technology solutions for diversified global markets, including light vehicle, commercial truck, off-highway, industrial, motorsport and the aftermarket.
CVSAe suspension technology from DRiV is featured in more than 40 popular vehicle models. To learn more, visit www. monroeintelligentsuspension. com
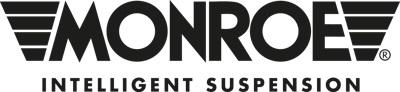
Compact, economic and quick to install, SICK’s CQF16 capacitive level sensor has been developed to provide a universal, non-contact solution wherever the fill level of water-based liquids must be detected in nonmetallic vessels, tanks or pipes.
The robust, ECOLAB-certified SICK CQF16 level sensor is supplied with a one-clip mounting bracket that can be fastened securely to the wall of any pipe or container. Using the capacitive measurement principle, it accurately detects water-based media regardless of foam, moisture or deposit buildup on the inside of the vessel.
The SICK CQF16 is a costeffective alternative to continuous analogue measurement with a diverse range of fill-level detection uses. For example, it is ideal for detecting levels of oils, milk
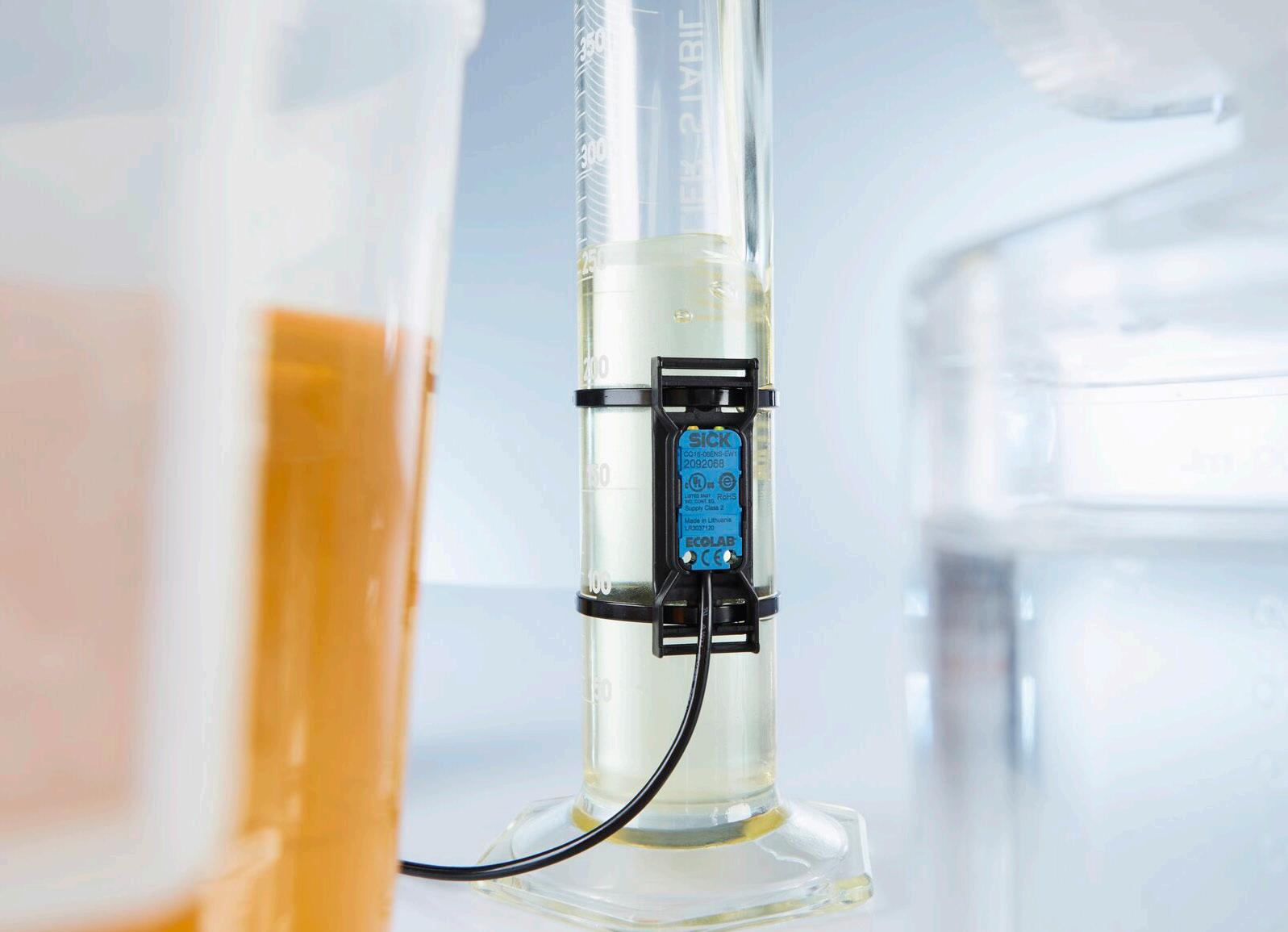
or honey in food processing machinery, or for checking condensate water in freezers. It will prove useful for detection of ink-cartridge levels in printing and packaging machinery. In medical and pharmaceutical machinery, it could be used to monitor levels in the storage vessels for filling vials or processing blood products.
Said David Hannaby, SICK’s UK Product Manager for presence detection: “The CQF offers an economical new alternative for a wide range of level sensing duties. Wherever there is a requirement for on/off or low/ high switching, for example, the CQF offers all the reliability and flexibility you would expect from a SICK device.
“For most applications, the factory-calibrated version is all you need to get started. Just clip the sensor into the bracket supplied and you are ready to go. For more demanding applications, the sensor can be simply taughtin via the cable connection. Easy commissioning is assured thanks to the two on-device LEDs showing power-on and output status.”
The compact CQF16 measures just 16 mm x 34 mm x 8 mm and has a sensing range up to 6 mm. With a robust housing rated up to IP69K, and the option of M8 male connector or integral cable connection, the rugged CQF16 level sensors avoid the risk of fluid penetration in process environments. With a 100mA signal, the sensors offer a flexible choice of PNP/NPN or NO/NC switching outputs.
For more information call 01727 831121, email: andrea.hornby@sick.co.uk. or visit: www.sick.co.uk
It is true to say that if you put me in a Formula 1 car I would be unlikely to match up to Lewis Hamilton around Silverstone. The equipment would be the same, but there would be a slight difference in driving experience and aptitude!
When it comes to the area of advanced design and engineering, the situation is much the same. When it comes to the niche area of micro molding, the situation is almost identical. Exceptional micro molders have the best equipment, but much of their time is spent pushing this equipment to or beyond its limits, and when it cannot do what is needed to fulfil a complex micro molding project, they adapt it or develop new technology solutions.
The “driver” behind this is experience. It is only through experience that you are able to truly wrestle a micro molding challenge to the ground and move mountains to achieve what may be perceived by less experienced practitioners as impossible goals.
MICRO MOLDING – THE STRATEGIC PLAY Many commentators erroneously suggest that micro molding is simply scaled down macro molding which is about as remote from the truth as it is possible to be.
Even a partial understanding of molding from a practitioner or customer perspective will illuminate the fundamental differences between traditional molding and micro molding.
First, let’s consider the relationship.
Imagine that a molder is being used by a customer to produce 1,000,000 plastic fasteners about 1 inch by one inch. The customer will put the job out to

tender, and the fundamental concern beyond a basic view of competency will be price per part and speed of delivery. The least expensive and fastest molder will most likely be selected, the order processed, and the parts delivered. End of story. Here the molder is essentially a job shop, not particularly strategic in the scheme of things, and instantly replaceable by another vendor for the next job if out-bid.
By contrast, consider a customer looking for 1 million thinwalled tiny plastic tips used in pacemaker and neurostimulator leads. Here, the parts are super critical, and must be produced to the most exacting of tolerances in the best material for the application. Now supplier selection is based significantly upon competency as well as price and speed of delivery, and the nature of the relationship is much more strategic.
At this level of precision and complexity, very few OEMs have the in-house capabilities to fulfil production, so they necessarily reach out to micro molding experts, and as soon as they do they will understand the need for a partnership relationship rather than a job shop relationship. The micro molder will necessarily be required to influence and optimise design, through experience and knowledge to advise on material choice, understand the repercussions of design on tooling and assembly, and therefore be seen as a strategic partner in product development.
MEETING THE CHALLENGE The micro molding space is an exciting place to be. The trend towards miniaturised parts or larger parts with micron features is constantly gathering pace across industry, and the challenges in terms of exacting applications are an everyday experience. While technology is constantly evolving to meet these challenges, Accumold maintains that the real value for customers partnering with us or any other micro molder is in the extent of, values of, passion of, and experience of the micro molding team.
For more information visit: www.accu-mold.com

Softing Industrial releases version v1.20 of edgeConnector Siemens. The software module is based on container technology and connects Siemens controllers with industrial IoT applications. In addition to SIMATIC S7-1200 and S7-1500, the new version also supports SIMATIC S7-300/400 controllers.
edgeConnector Siemens enables access to SIMATIC S71200 and S7-1500 data including optimized data blocks. Version v1.20 additionally supports SIMATIC S7-300/400 controllers. Client applications have access to data via the interoperability standard OPC UA. The product can be configured locally via a built-in web interface, or remotely via a REST interface. It seamlessly integrates with Azure IoT Edge and AWS IoT Greengrass and is made available via online repositories such as Docker Hub.

Users benefit from flexible deployment and ease of use which comes with virtualization and container technology. Valuable process and machine data are made available for innovative IoT applications without any changes to controller or automation network configuration. Advanced security features such as the management of access right for individual client applications increase the security of the entire solution.
“edgeConnector Siemens is the first strategic expansion of our dataFEED product family to include virtualization and container technology”, says Wolfgang Wende, Senior VP Sales at Softing Industrial. It leverages Softing’s extensive experience with brownfield connectivity and OPC UA technology and makes it available for new and highly efficient IoT solution architectures.”
Softing connects disparate automation components to feed data from the shop floor to the cloud for control and analytics. The company’s products enable the monitoring and diagnosis of communication networks and thus ensure a reliable data flow. In this way, they create the basis for the optimization of production processes. For more information, please visit industrial.softing.com/de.html


Will Dick-Cleland, Process Technology Team, Alloyed
The aerospace sector has long been recognised as an early adopter when it comes to cutting-edge technology inventions, and as such it is unsurprising that the use of additive manufacturing (AM) as a production tool is relatively familiar in many of the leading aerospace OEMS and their supply chains.
The sector is typically not a mass production industry, but is instead characterized by complex low-volume manufacture which plays directly to the strengths of metal AM (and specifically the Laser Powder Bed Fusion (L-PBF) process) when compared with traditional metal manufacturing processes. In an area that is highly competitive, where conventional manufacturing processes are costly — especially for metal components produced in relatively low volumes — and with supply chains constantly under pressure to conform to ever more stringent environmental performance restrictions, the aerospace sector needs to become more agile. Metal AM processes, with the ability to manufacture innovative geometrically complex parts in a timely, local, and cost-effective way, have a huge part to play.
AM IN AEROSPACE AM’s disruptive for potential for the aerospace sector is widely acknowledged, holding out the opportunity to break the typical compromise between scale and scope in manufacturing first by reducing the capital expenditure required to achieve economies of scale, and second by increasing the variety of designs that a given amount of capital expenditure can produce. One AM platform can at the same time build a number of complicated parts with variable designs, and this means that large centralized factories with assembly lines are not always required, and with AM complexity, production change overs, and customization are cheaper. As AM technologies continue to develop and secure a stronger foothold in production scenarios, there is simultaneous development ongoing across the sector to refine associated parts of the AM ecosystem, with a great deal of emphasis being placed on in-process monitoring for traceability and validation purposes, as well as automated post-processing technologies. A further, vital area of development is materials, particularly metal powders for AM that meet — and exceed — the functionality and performance of existing production materials as well as meeting the requirements of specific applications. ALLOYS FOR HIGH TEMPERATURE APPLICATIONS It is fair to say that, to date, metal AM processes have not performed well with the highest temperature materials — that is to say, materials for components that operate at the top of the temperature range within jet turbines. In the aerospace sector such applications would include, but are not limited to the critical areas of a turbine engine such as the back-end of the compressor, the combustor, the high and low
pressure turbine areas, and the exhaust. All parts in these areas of the engine are exposed to high temperatures and higher levels of oxidation.
For such high temperature applications, the aerospace sector typically uses nickel (Ni) alloys such as IN738, IN713 and MarM247. However, these alloys are incompatible with welding techniques due to their chemistry, as they do not respond well to rapid thermal gradient changes and it is virtually impossible to control the amount of cracking during the weld process. Therefore, these alloys have historically been processed using casting methods where the cooling rates are relatively low.
This is the conundrum facing users of metal AM within the aerospace sector looking to capitalize on the advantages that the process has to offer for high temperature applications. It is this that has driven further exploration of alternative materials that could replace traditional high temperature alloys without compromising structural integrity while at the same time being compatible with AM. The advantages of AM-compatible alloys for high temperature applications derive from the fact that the components assembled in hot sections of engines are usually some of the most expensive, and due to the harsh environment in which they work have short life-cycles. Using the L-PBF process with high temperature alloys offers manufacturers the opportunity to benefit from better inventory management, reducing late penalties due to tooling delays, and creating more intricate shapes, often allowing the integration of several components in a subassembly into one.
It was to address this requirement that Alloyed worked with leading aerospace OEM Honeywell to test a new high temperature nickel alloy — ABD®900AM — with the L-PBF process, to determine if it could serve as a replacement for existing high temperature casting alloys. The purpose of this effort was to discover at a high level if ABD®900AM showed promise and warranted further development.
HONEYWELL & ALLOYED COLLABORATION Honeywell Aerospace has a long and rich heritage of innovation that spans more than a century. The company has one of the industry’s broadest and most advanced portfolios including world-class engines, cockpits, cabin design, wireless connectivity and enterprise performance management services. Honeywell first engaged with metal AM processes in 2007 when the company had several prototype parts manufactured by external vendors. Over the ensuing years, the company has continued to assess and implement the technology for applications where there is a need for a rapidly manufactured metal parts, including for test bed components. In 2014, led by the efforts of Engineering Fellow Donald Godfrey, the company opened its first $5 million AM facility in Phoenix, AZ, USA, with a focus on L-PBF and electron beam PBF technologies. In the same year AM facilities were also opened in Bangalore and the Czech Republic. Today, the Honeywell AM operations have grown significantly in both size and capacity and incorporate tensile, LCF, and creep testing equipment, powder characterization equipment, and a vacuum furnace for stress relief and heat treatment. In Arizona, more L-PBF machines were added in 2020, and now the lab is fully equipped to manage end-toend powder and mechanical characterization, pre-production builds, and a full range of R&D activities. Honeywell is using the pilotproduction facility as a means to either develop parts for production that will be sent to a supplier for manufacturing or working with a supplier to cooperate in the development of components for production.
As an organization, Honeywell collaborates with universities and companies around the world with the intent of developing new technology and exploring new technologies as they emerge. After an initial introduction to Alloyed by a third party, Honeywell recognized the potential of the Alloys By Design (ABD) system brand developed by highly respected metallurgists from Oxford University and this stimulated further interest in the ABD®900AM material and its potential for high temperature aerospace applications as it was not prone to cracking.
The result of this initial collaboration was a dedicated project that would see Honeywell build a limited number of test specimens in its additive manufacturing laboratory located in Bangalore, India. Honeywell would build and test the material to determine if the results merited continued investment and development.
ABD®900AM
ABD®-900AM is an agehardenable, nickel-based superalloy designed specifically for use as feedstock in the L-PBF process. It is optimized for environmental resistance and high-temperature tensile strength, with a working temperature range up to 900°C (1652°F) in its age-hardened state. ABD®900AM not only offers a higher operating temperature but also significant long term stability. You can access the datasheet here.
Exhibiting excellent creep strength, ABD®-900AM has also demonstrated superior resistance to cracking during manufacture and heat treatment, enabling complex
part design. It is designed to be free of solidification, liquidation and strain-age cracks, and showcases exceptional printability for a 40% ’-phase strengthened alloy. The ABD®900AM alloy also shows high asprinted part density of >99.9%.
TEST RESULTS The scope of the collaborative project between Alloyed and Honeywell was the assessment/ qualification of the ABD®900AM Ni-alloy powder for the next generation of additively manufactured high temperature applications. Honeywell has undertaken a series of tests to confirm and optimise the properties of the alloy with some extremely positive results.
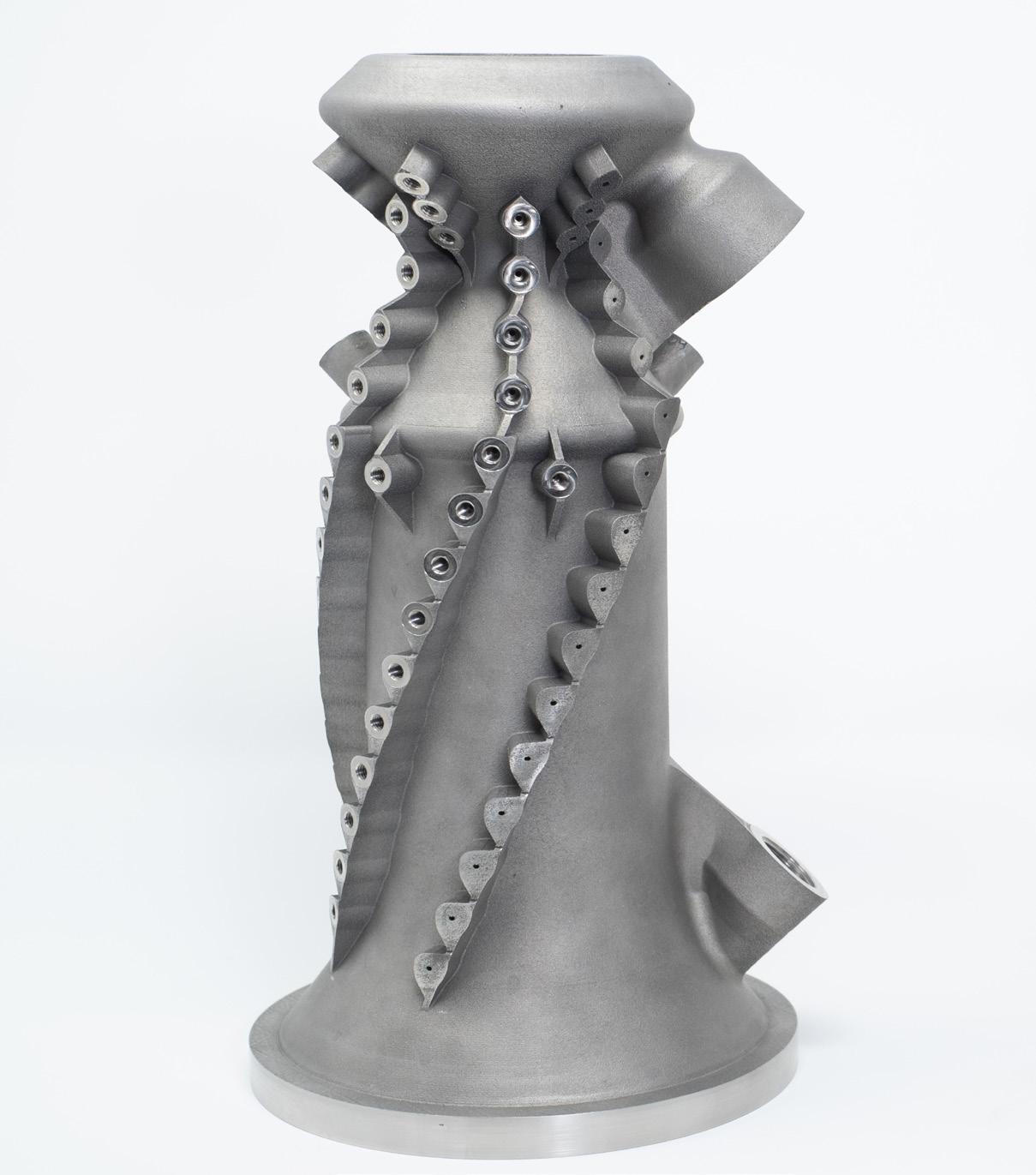
From a broad perspective, the project provided a manufacturing assessment and a mechanical property assessment of the alloy:
Manufacturing Assessment Post processability. It is often the case that parts must Additive manufacturability. It undergo a variety of postwas important to assess how the processing activities after the alloy behaved when processed AM build, which can affect on a L-PBF machine, and the mechanical properties of whether the welding operation the material and therefore, involved — with all this implies the functionality of the part. in terms of rapid thermal To assess how ABD®-900AM gradients — would deleteriously behaved parts were subjected effect the integrity of the final to vacuum heat treatment and part. Various test geometries Hot Isostatic Pressing (HIP) were trialled on an EOS metal often used on metal AM parts to system, and component scale eliminate internal voids. There testing was undertaken. It was was no “post-weld” cracking found that there was no part detected on parts made from distortion on cracking in the ABD®-900AM. “as-printed” condition, there was good surface finish, and a wide processing window. Mechanical Property Assessment Tensile testing. ASTM standard Powder Recyclability. The ability tensile tests were undertaken to be able to re-use unsintered on the ABD®-900AM parts material from build-to-build is measuring tensile strength, obviously an important factor breaking strength, maximum when looking at the economics elongation and reduction in of using metal AM processes. area between 427 oC and 927oC Because of this, it was decided in both build directions. The to manufacture and test parts test showed good repeatability made with “used” powder, and of test points, with high it was found that there was no temperature strength of the significant change of properties ABD®-900AM comparable with in the parts made with used “legacy” cast Nickel alloys which powder compared with virgin cannot be manufactured crack ABD®-900AM powder. free in AM.
48 | Worldwide Engineering Magazine
Low cycle fatigue testing. Low cycle fatigue (LCF) is low-cycle endurance testing, where components are subject to mechanical cyclic plastic strains that cause fatigue failure within a short number of cycles. ABD®-900AM was subjected to LCF testing at 650oC, the results showing that Non-HIPed ABD®-900AM had superior performance to HIP-ed alloy 718.
SUMMARY The results of the work between Alloyed and Honeywell show that ABD®-900AM is an alloy that demonstrates great potential for high temperature applications. The material welds and fuses extremely well, particularly when compared with other high temperature nickel alloys. While ABD®900AM is not a replacement for CM Mar-247 in most cases due to the oxidation capabilities, it does exhibit very good mechanical properties at high temperatures when compared with Mar 247 or IN792 or IN713 or IN738.

The partnership between FPT Industrial and Aprilia Racing Team, which began last July, is spotlighted in a double interview with representatives of the two brands, who are united by a passion for racing, speed and engine performance, as well as profound commitment to the technological pursuit of excellence.
The journalist, anchorman, and iconic MotoGP commentator Guido Meda will conduct the interviews with Paolo Bonora, Aprilia Racing MotoGP manager, and Alessandro Mazza, Marine Engine and Power Generation Engineering manager for FPT Industrial. The two technical experts will reveal the numerous ins and outs of the powertrain sector and will demonstrate how two worlds that seem distant - that of engines racing on MotoGP circuits and industrial engines equipping boats or tractors - have in fact, a lot in common.
“Through the insights from my two interviewees, I was able to discover that these two environments are quite similar. It is always exciting to compare two people and two worlds who consistently push hard to be the first to reach the finish line, develop a brilliant idea, or achieve excellence,” commented Guido Meda.
This unmissable interview will take place on the 21st of September at 11 a.m. CET on the FPT WEBCAST platform available at this link. This new digital platform was created to give the public, motor enthusiasts, dealers and customers, the opportunity to meet in a new and safe way and to share information, ideas, and passion in the new digital normal.
“Power to connect” is the slogan chosen by FPT Industrial to summarize the intentions and potential of the webcast platform, which will host very different events that are, nonetheless, united by a passion for engines, sustainability, and power. The FPT WEBCAST, which has been developed to guarantee immediate and userfriendly usability - is the ideal “location” where live events, innovation talks, webinars, virtual tours, and podcasts will be available and will target different audiences, such as OEM producers, dealers, end customers, journalists, and employees. The platform does not require you to download any application and is accessible from both PC and mobile devices. The intent is to enrich communication and interaction between people, by adapting to recent changes and provide each participant with the opportunity to be not only a spectator but also a player. With this project, the brand further values its communication strategy and reaffirms its focus on the digital sphere, in a historic moment where communication and live events have undergone a paradigm shift. For further information, visit www.fptindustrial.com.
