
5 minute read
Cours Bayview Yards
COURS BAYVIEW YARDS OTTAWA, ON
1. The front entrance. The project retains over 85% of the existing structure, and sets a precedent for the repurposing of abandoned municipal buildings.
Advertisement
Hobin Architecture
Existing Building Upgrade Award
Jury: This conversion of a 1940s City Works Yard building into an Innovation Hub demonstrates how the careful and pragmatic adaptive reuse of an unprepossessing building can transform the dynamics of a neighbourhood, create a sense of place, and at the same time support social and cultural continuity. The act of preservation conserves embodied energy in the existing structure and avoids that associated with a new building. The LEED Gold certification is exemplary for an adaptive reuse project.
Also known as The Innovation Centre at Bayview Yards, Cours Bayview Yards is Ottawa’s epicentre for entrepreneurial programs and services. The centre was developed within a 4,460 m2 (48,000ft2) industrial building, originally constructed in the 1940s as a City Workshops facility, and now having historical importance as one of the few survivors of a once sprawling industrial area.
Site plan
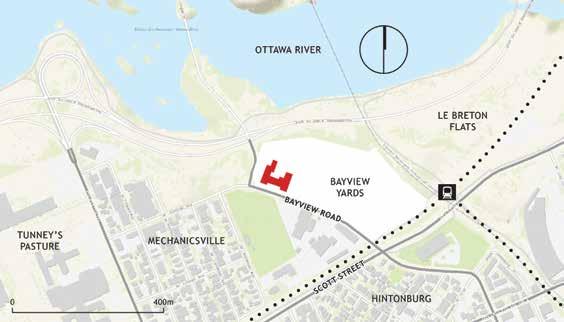
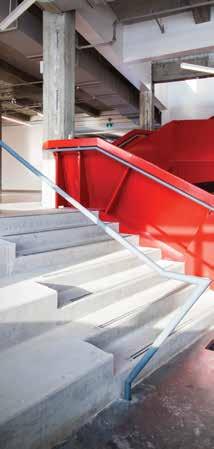
5
Additions (circa 1950’s)
Original Building (1941)
Recent additions
4
3
2
1
First floor
Electrical/Telecom Washrooms Shaft Media Lab Maker space Concourse Incubator
6 15
8
2
8 9 10 11 12 13 14
Elevator Janitor Rooftop patio Link Stair Accelerator Front entry
14
15 16
Outdoor plaza Terrace
7 2
3
9
3 2
1 10
11
16 8
12 3
13
Second floor
The project showcases the potential for the adaptive reuse of vacant industrial buildings and demonstrates that such adaptation can be done both affordably and sustainably. Aside from retaining more than 85% of the original structure, the project integrates a broad spectrum of design strategies that address issues of economic, social and ecological sustainability.
2. The ground floor is organized around a dramatic central stair. High efficiency LED lighting adds life to the former industrial interior. 3. Interior with restored service bay doors. System furniture and partitions are Greenguard Certified. High performance, thermally broken, argon-filled gas glazing units were installed throughout.
3
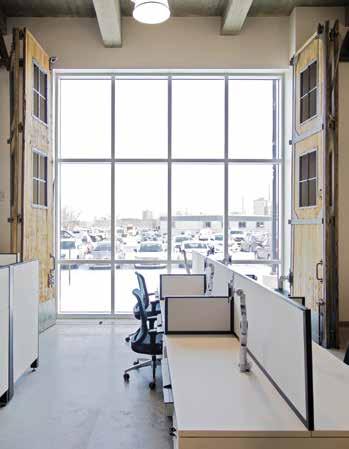
These include maximizing thermal performance through the use of premium insulation and fenestration, achieving an envelope performance twice that required by the MNECB; specification of high-efficiency mechanical and electrical systems, supplemented by a comprehensive building automation system that modulates equipment runtimes to varying building loads and not fixed schedules; embracing alternate modes of transportation and urban agriculture.
PROJECT CREDITS
OWNER/DEVELOPER Invest Ottawa ARCHITECT Hobin Architecture DESIGN/BUILDER Morley Hoppner Limited CIVIL ENGINEER D. B. Gray Engineering Inc. ELECTRICAL/MECHANICAL ENGINEER Bouthillette Parizeau Inc. STRUCTURAL ENGINEER Adjeleian Allen Rubeli Limited COMMISSIONING AGENT Arborus Consulting INTERIORS 4Té Inc. HERITAGE ARCHITECTURAL PLANNING Commonwealth Historic Resource Management PHOTOS Steve Clifford (photos 1 and 3); Invest Ottawa (photo 6); MIV Photography (photos 2, 4, 5 and 7)
4. The Incubator is an open, collaborative space with casual seating options. 5. The addition at the ground floor doubles as a café and connecting link.
In its effort to acknowledge the industrial heritage of the building and the Bayview Yards area, the design of the repurposed spaces retains over 85% of the existing structure and contributes to an engaging dialogue between old and new. Fittingly, the Innovation Centre is emblematic of the reinvention and regeneration of the surrounding area. More broadly, Cours Bayview Yards sets a precedent for the repurposing of obsolete or abandoned public buildings, reinforcing the important goal of sustainability through repurposing and reuse.
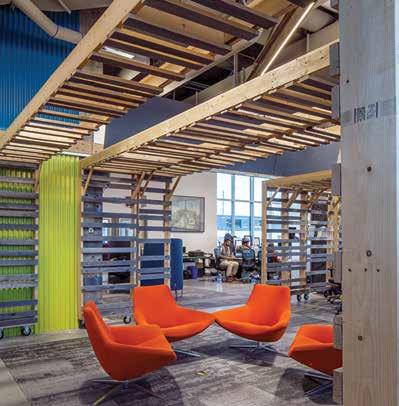
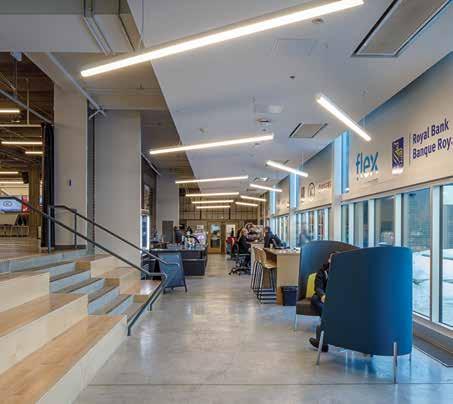
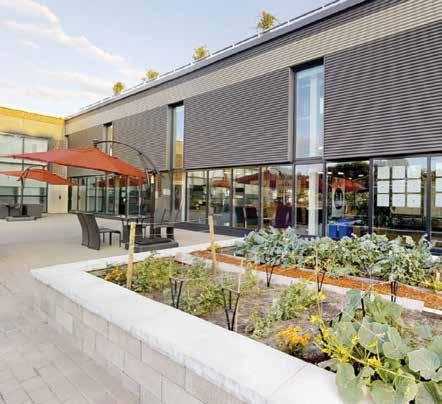
Internally, the design takes advantage of the exposed interior structures and surfaces of the building, with unfinished concrete beams and floors much in evidence. These elements embrace the raw, gritty heritage of the Bayview Yards area. This aesthetic is further reinforced with the retention of industrial artifacts such as the cantilevered hoists and pulleys, metal cage structures and wooden garage doors.
The creative reuse of the building and its diverse spaces support the Centre’s role as a hub of innovation, industry and discovery, all within a framework of sustainability. It supports free thinking, and offers opportunities for spontaneous conversations and unscheduled meetings.
PROJECT PERFORMANCE
Energy intensity (building and process energy) = 78.3KWhr/m2/year Energy intensity reduction relative to reference building under MNECB = 47.2% Reduction in water consumption relative to reference building under LEED = 41.5% Recycled material content by value = 9% Regional materials (800km radius) by value = 30.47% Construction waste diverted from landfill = 76.4%
6. The courtyard plaza and community garden is overlooked by a rooftop terrace. 7. The Well, a multipurpose space for events, parties and exhibitions, is also accessible for casual use when not in use. Daikin supplied the Maverick roof-mounted air handler unit, and SmartSource water source heat pumps.
The ground floor is organized around a dramatic central stair and a sun-filled café link. The lobby, link and stair are key organizing elements through which all users and visitors pass daily. Other spaces include: The Incubator, an open, collaborative space with casual seating options, and The Well, a multipurpose space with an integrated seat-stair that is freely accessible for casual meetings when not in use. There is also a rooftop terrace.
Outside, the previously contaminated site has been remediated and now supports an apple and pear orchard as well as a community garden. Since its completion, the project has been widely recognized for its “outside the box,” unconventional approach to what is essentially an office building, recognizing the many qualities that were born purely out of the adaptive re-use philosophy. The project achieved LEED Gold certification in 2018.

PRECAST CONCRETE BUILDS ON... PREFABRICATED & MODULAR CONSTRUCTION!
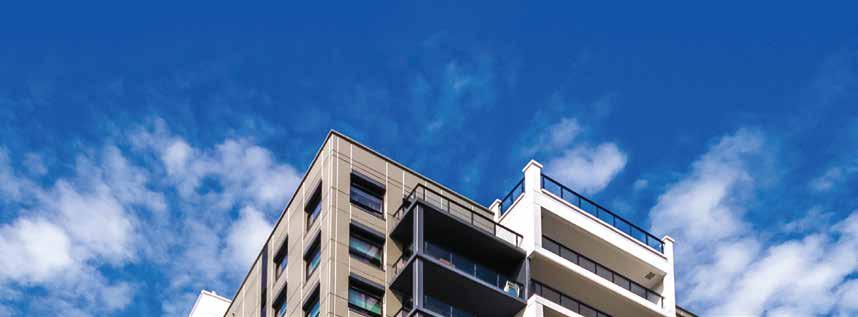

Precast Concrete Prefabricated Building Systems outperform other systems in: · Greatly reduced construction schedule · Exceptional building envelope system · Faster sequence of construction · Less material wastes · Superior quality structural & architectural components · Wide array of design opportunities · Durability & long life


The Belmont Trio, Kitchener, ON | Owner: HIP Developments Inc | Architect: ABA Architects, Inc.
Photo: HIP Developments Inc.
Visit www.cpci.ca/publications CPCQA to download your free copies of the Structural Solutions Technical Guide and