
6 minute read
Custom Solutions That Last
More than twenty years in the business, and this local machine and tool shop remains on the cutting edge.
By Matthew St. Amand
Off-the-shelf, cookie-cutter solutions might be easier to provide, but they are certainly not more interesting. Nor do they serve the needs of businesses in an increasingly competitive and technology-driven economy. At Trillium Machine, there is no interest in easy solutions.
“All of the work we do is custom,” says Trillium Machine co-founder Mike Hamelin. “Each customer has their own challenges, and Trillium continues to provide solutions.”
Founded in 2001, Trillium is a turnkey solutions company specializing in designing and building custom automated machines for a range of industries, including automotive, food processing, and consumer products.
Because the challenges coming through the door are as singular as the customers who bring them, Trillium lives on the cutting edge of technology.
“Right now, we’re starting to work with ‘cobots,’” Mike explains, “which is short for ‘collaborative robots.’ These are robots that people can work safely with, side by side.”
Anyone who has been in the manufacturing environment is familiar with the myriad safety precautions taken to separate human beings from robots. Light curtains, area scanners, Safety interlock assembly cells, are but a couple of the safety measures to ensure a traditional robot ceases moving the moment a person is within its proximity.
“It took some getting used to,” Mike says, “but we’re finding that cobots are great for repetitive pick-and-pace tasks. They are reasonably new to the industrial field, but we are finding that they are safe, they’re very reliable. They can undertake the monotonous, repetitive tasks while the person working beside them can do the more intricate, complex tasks.” six-axis robots found in most manufacturing settings. At the present time, they are working with a compostable materials company from British Columbia that is setting up shop in Windsor. This company produces compostable single-serve coffee pods, similar to K-cups.
“It all happens under one roof,” Mike says. “They roast the beans and fully package them at the end of the line. We’re in there at the ground level. This company is one hundred percent plant-based— everything they’re based on is plantbased. Once discarded, their coffee pods biodegrade in less than a month.”
One area that Trillium has gravitated toward is ultra sonic welding. Trillium has teamed up with industry leader, TELSONIC Canada Inc., and is quoting on building machines incorporating TELSONIC’s ultra sonic welding capabilities.
“They make the weld controllers and welding horns,” Mike explains, “and Trillium integrates them into our assembly machines. Right now, we are doing this mostly for the automotive and food and beverage products. We have made one-offs throughout the years, but this is something we’re hoping to do more of. It’s opening doors to new customers and to new industries.”
He continues: “Each product, each different plastic is different. Every product we weld together has its own challenges. Telsonic has an office in Windsor and has excellent support.”
Trillium counts success one project at a time. One such successful project recently revisited them.
“The first machine Trillium designed and built was a stainless steel Tig welding machine that welds the top collar onto fire extinguishers,” Mike recalls. “We built the machine for a local company, Flag Fire Equipment, which was eventually purchased by Johnson Controls of Wisconsin. After twenty-one years of continuous use, the customer submitted a Request to Quote a duplicate machine. The original will continue being used, and they need another just like it because business has picked up.”
Not only does Trillium design and build custom solutions, but they deliver solutions that have staying power. -To learn more about what Trillium does, visit them online at trilliummachine.com.
Navacord is one of Canada’s largest commercial insurance brokers with over $1 Billion in premium and teams of industry specialized advisors. As a Navacord Broker Partner, one of Canada's largest commercial brokers, Ives Insurance offers increased Manufacturing sector expertise, expanded product offerings and stronger relationships with insurance companies.
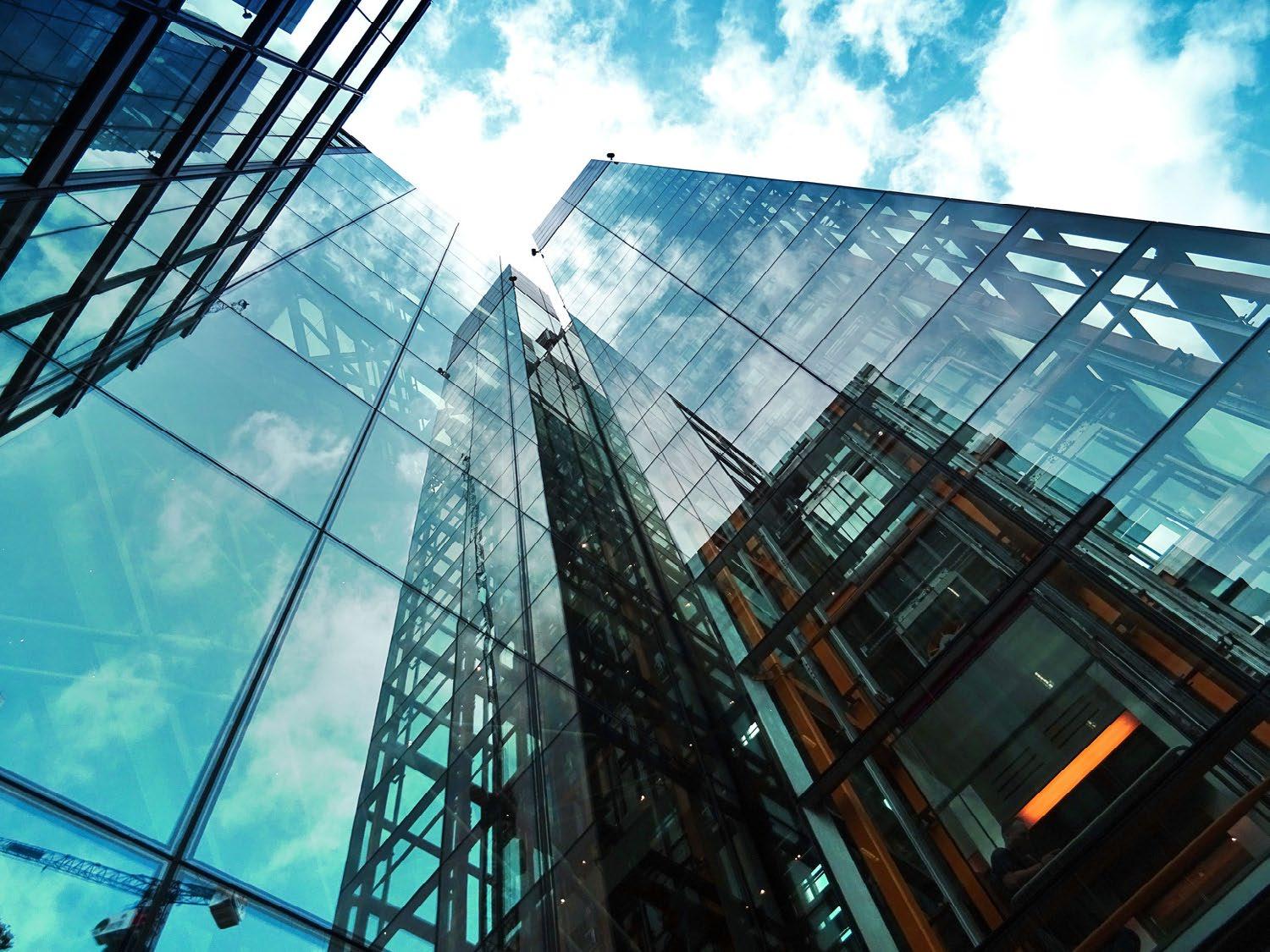
Chris Lewis , Member of Parliament for Essex Shadow Minister for Labour
I’m excited to represent Essex during this next chapter of growth . The future is bright. The new battery plant , the Gordie-Howe Bridge and all the investments they bring only build on the current tool and die and auto -manufacturing industries. These developments will need to be stewarded well. Of course, with this growth we must be prepared to gear up for a different set of jobs. Training new workers and re-training experienced workers to take on those new jobs , in a level of manufacturing we have never witnessed before, will be central to that stewardship This is vital, to guard against experienced workers losing their jobs in the changeover to electric vehicles.
I have always thought that skilled trades need to be taught right from a child’s early years. That is why I continue to encourage our future generations that a career in skilled trades and manufacturing is something in which they can be proud of and be paid well. These jobs are among the best in the country. The developments in electric vehicles, hydrogen power, auto -mobility and so many other advancements in technology will create a s teep learning curve, however the benefits will reap reward and our country will excel with fresh thinking and young minds to carry the torch into the next era of manufacturing.
In 2019 I was honoured to become the Member of Parliament for E ssex. Recently I have been tasked with the role of Shadow Minister for Labour. Further, I work with a group of MPs as Chair of the Conservative Auto -Caucus. This keep s me up to date with developments in my riding, the Labour world , and the auto-sector, to better plan for what Conservatives can do for our region and nation. It’s the perfect combination of responsibilities for me. As a member of the Transport, Infrastructur e and Communities Committee gives me the opportunity to speak to those decision s that are being made in areas like air, rail, roads and of course our international bridge and seaports. Ultimately, my greatest responsibil ity is to serve the people of the riding of Essex The decisions I make on a national level are always top of mind to the impacts they will have in our region.
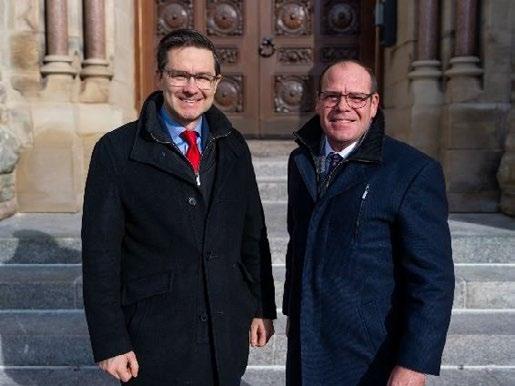
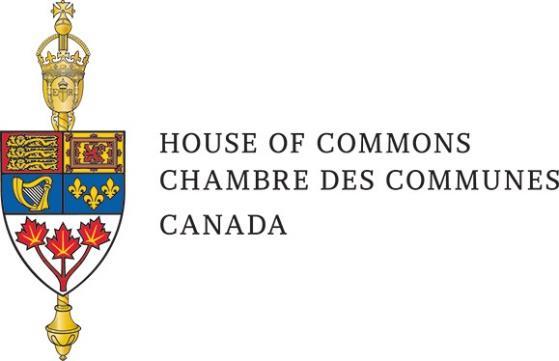
I have introduced a Private Members Bill (C-241) which would allow for a tax deduction for a tradesperson’s travel expenses, such as meals, lodging, mileage, or flights This is only the beginning of what can be done for our trades people in Canada. Supporting this bill along the way , with many organizations were Tomi Hulkkonen, the Coordinator of UBC Local 494 and Pierre Poilievre, our CPC Leader Pierre understands that we must support skilled trades, to which in turn supports our manufacturing industries. We continue to meet with both union and non -union skilled trades and manufacture rs across the country to further understand what is needed to support and build Canada in the future.
Looking forward, I am mindful that there are many areas of need in our country. Families and business es need relief from the pain of the current cost-of-living, inflation and supply issues that are impacting every single industry and worker My goal is to turn that pain into hope so manufacturing will be on solid ground and prepared for the developments ahead . I look forward to what the future holds and working together to make the world a better place than we found it! It is an honour to serve Essex.
Sincerely,
Chris Lewis - Member of Parliament for Essex & Shadow Minister for Labour
Longevity is not about doing the same thing over and over, and checking off the weeks, months, and years on one’s calendar. In fact, achieving longevity—particularly in business—means being most adaptable to change. The crew at Cunningham Sheet Metal (Windsor) Ltd., know something about this. With a history that goes back to 1908, they have not stayed in business by just doing the same thing over and over.
“You have to adapt with the changes of the times,” says Cunningham Sheet Metal co-owner, Justin Marchand. “We’ve always been known as a custom fabrication shop, but our actual trade is sheet metal, HVAC, and duct work— “tin knocking.” Things shifted over the years as we responded to customer demand, so we are doing more of that type of work.”
Justin, himself, is no stranger to change. He began with Cunningham in 2009 as a second-year apprentice and rose through the ranks where he is now a part-owner.
Nobody at Cunningham rests on the laurels of their 115 years in business. Just recently, the company decided to make a major capital investment, bringing in a state-of-the-art laser welder.
“This cutting-edge laser welder… there are only a handful this side of the
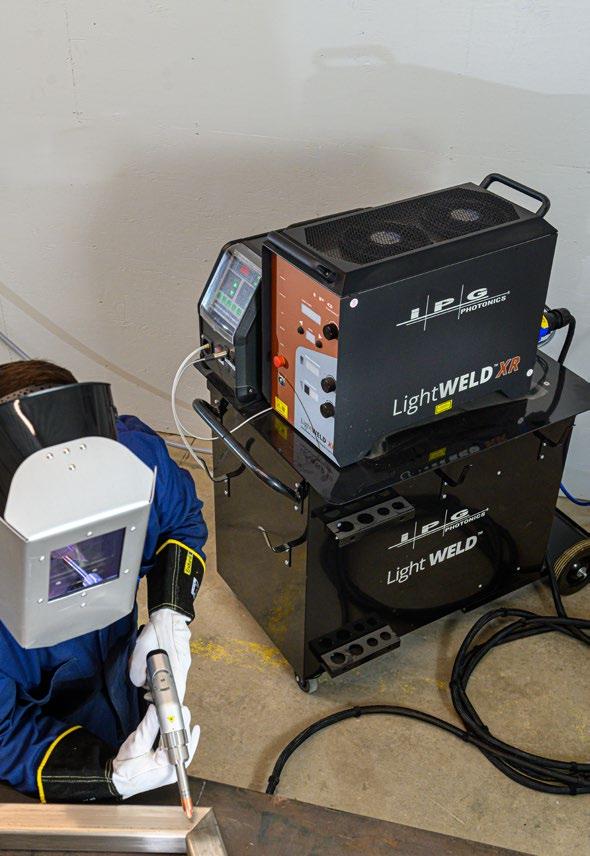