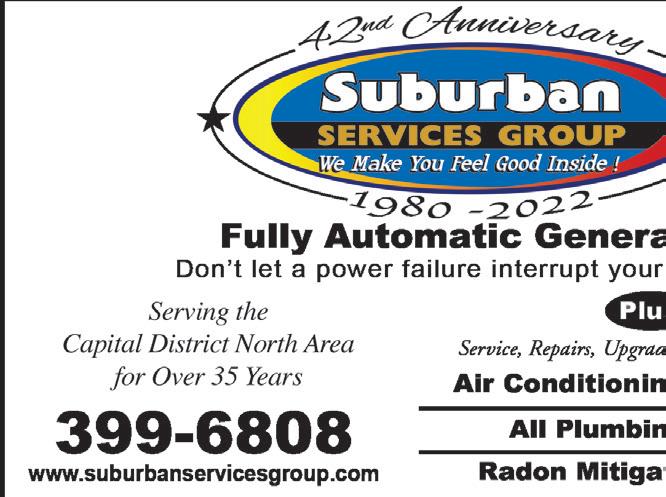
2 minute read
SARATOGA BUSINESS JOURNAL
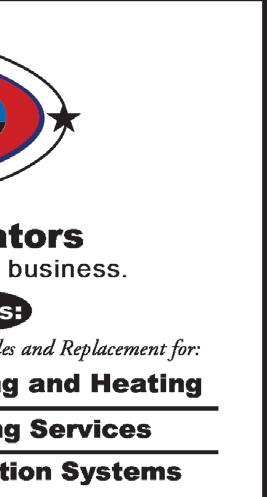
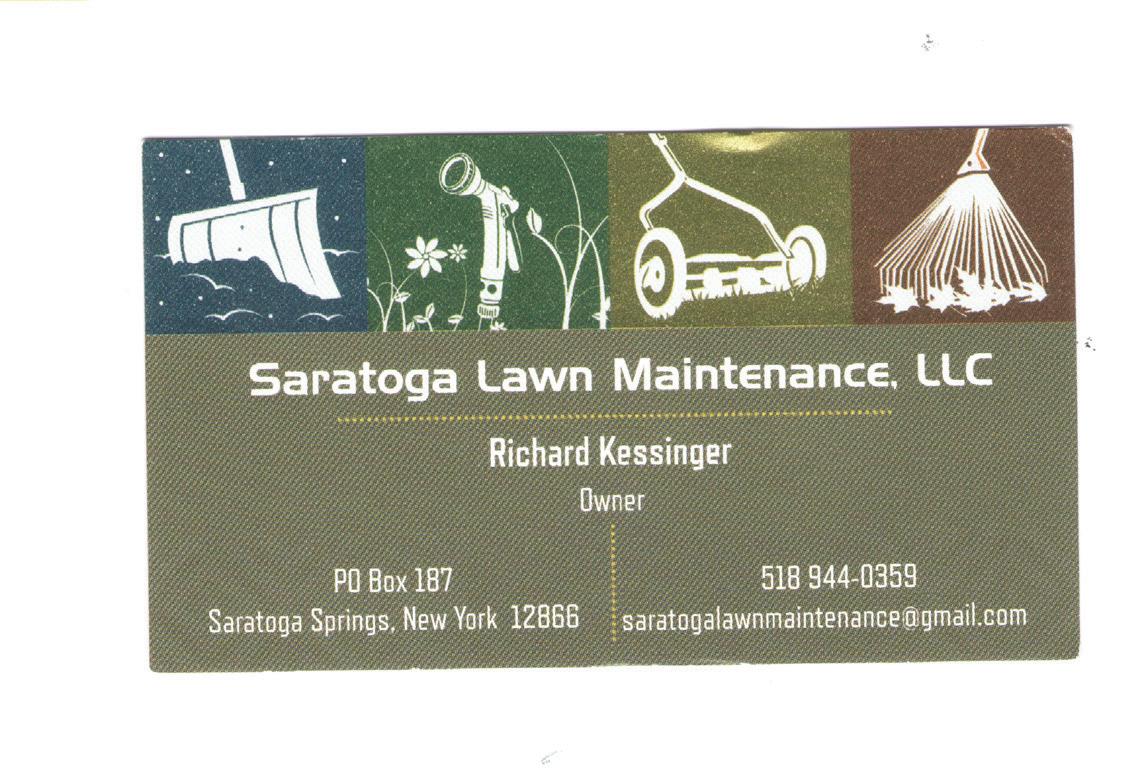
Advertisement
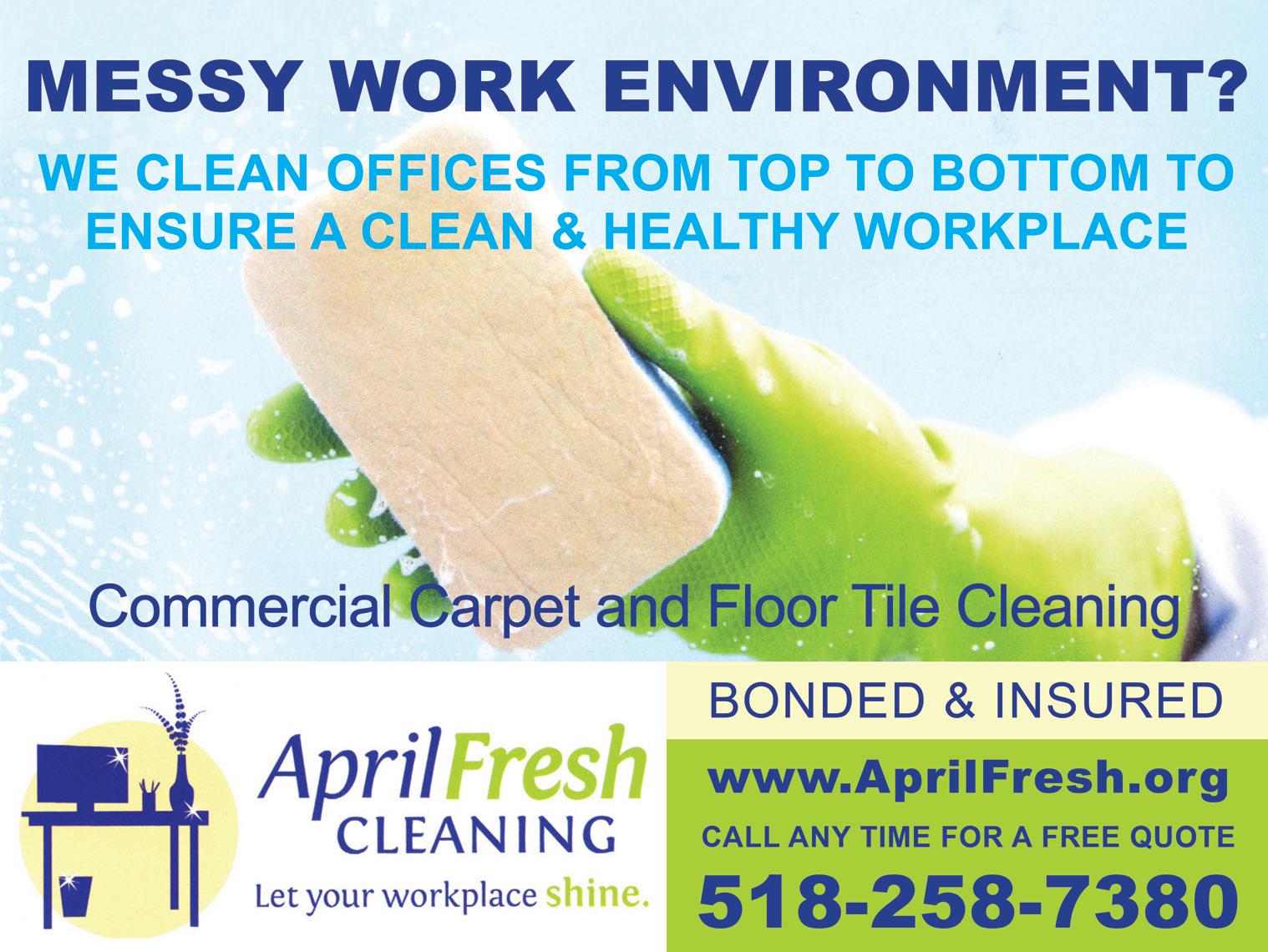
“There are national and international companies that have to set up a local source of ser- vice, and provide parts and labor to support GlobalFoundries, both during initial construction and ongoing operations,” MacElroy said.
But demand for business space was strong even before GlobalFoundries announced plans for a new plant.
“Th is is only going to heighten it,” said Tori Riley, Saratoga Economic Development Corporation vice president. “We’ve lost a few projects because we don’t have ‘spec’ space readily available. We’re also seeing huge demand for smaller spec space, around 1,800 square feet from folks starting small businesses. It’s gone from a hobby to business model and they can’t operate out of a garage any more.”
Others such as Clifton Park-based M.J. Properties and Luther Forest Corp. President Cailean Mackay and investment partners are pursuing plans for spec space, too.
“They’re developing different size facilities for different needs based on inquiries they’re receiving,” Riley said.
Outside fi rms seeking to locate in Saratoga County typically lease space and establish a market presence before expanding and building facilities of their own. Projects such as DCG’s makes it possible for them to pursue such plans, Riley said.
The Clifton Park IDA’s incentive package was for $262,500 in sales tax exemptions, $57,720 in mortgage tax exemptions and a payment-inlieu-of-taxes agreement worth $958,160 over 10 years. The package is expected to save DCG almost $1.2 million, which it says is critical in the face of rapidly increasing construction costs.
By offsetting such costs, DCG said it can keep rental fees down, making the project competitive with similar facilities in the area.
Earlier in its history, DCG did a number of multi-family developments, but sold its residential portfolio in 2005. The company is now focused on retail, office and light industrial projects. It developed Congress Plaza in Saratoga Springs, Malta Gardens near Northway Exit 12 and owns four Hilton Hotels along the I-87 corridor.
HDPE Pipe Manufacturer Continued
estry and agriculture applications
Products are made for culverts, catch basin and manholes, surface draining systems, treatments systems, infiltration basin and retention systems and many other applications. They also make and sell all manner of amenities for those systems
Robitaille told the board that in Saratoga, the company plans to make pipes it is currently not producing at other plants. These pipes will be anywhere from 48 inches in diameter, to 12-14 feet in diameter.
The piping is “leak free, sustainable, flexible and customized for specific application,” he said.
In its manufacturing process, Soleno uses recycled plastics, including bottles, that are shredded and incorporated as one of the raw materials, said Robitaille.
Where manufacturing standards allow, a significant part of the raw materials come from post-consumer recycled content. Those materials, routed through the Soleno Recycling plant in Yamachiche, Quebec, come largely from the prod-

From Page 1 ucts placed in recycling bins each week.
HDPE piping systems have been used for municipal and industrial water applications for over 50 years. They are used for ground source geothermal applications, also known as earth energy or geoexchange systems.
According to the Plastic Pipes Institute, HDPE is a tough, durable piping material with unique performance properties that allow for its use in a broad range of applications, utilizing a variety of different construction techniques. In the ground source geothermal industry, HDPE was one of the earliest piping materials utilized, thanks to its combination of characteristics which meet the specific demands of these applications, as listed above.
HDPE piping systems are approved for geothermal ground loops in all model codes across the United States and Canada.
Soleno’s mission is to design, manufacture and distribute HDPE, products for controlling and mastering stormwater.