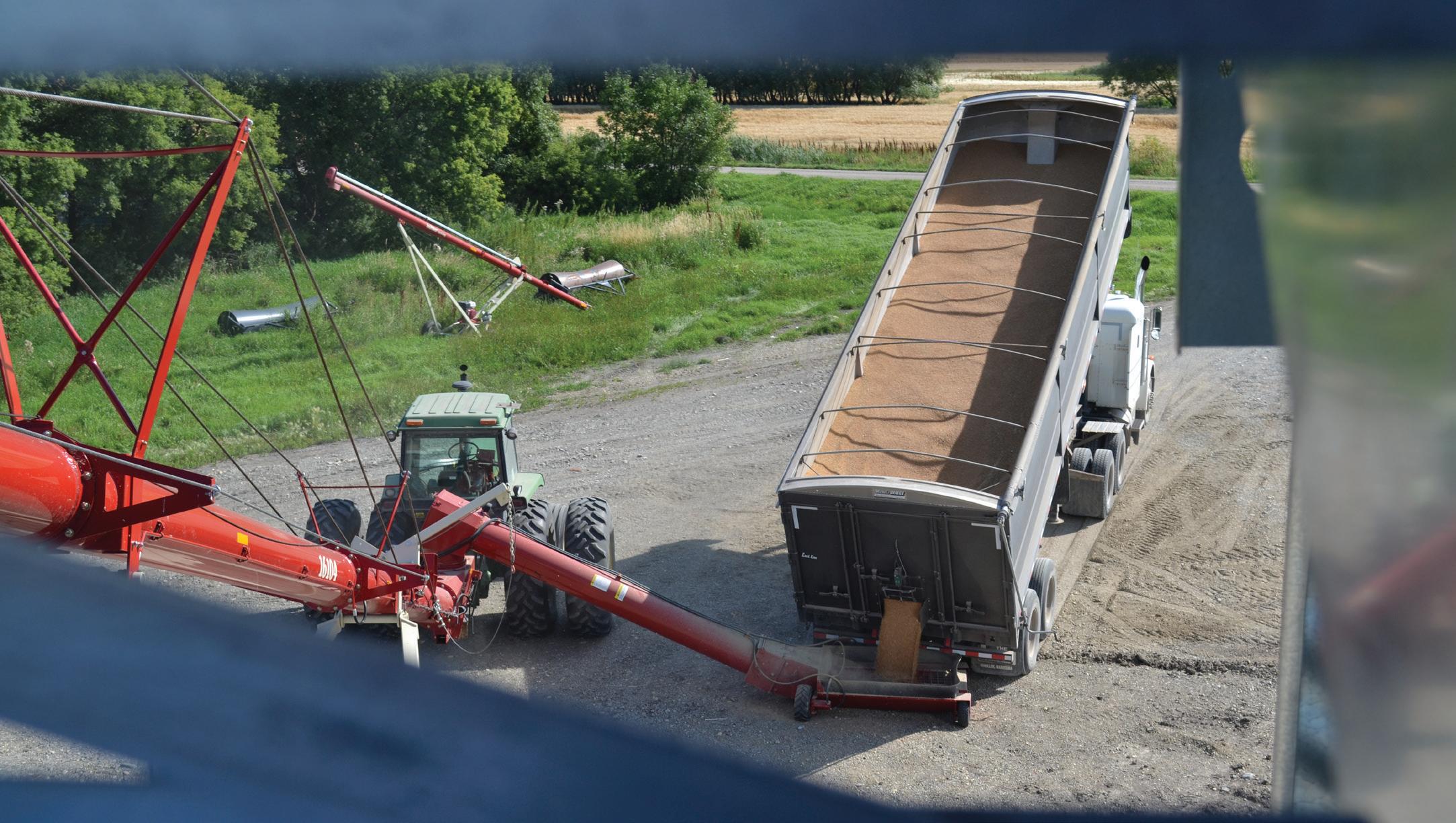
4 minute read
Grain Conditioning
Grain conditioning is the process of increasing the storage life of grain and minimizing grain spoilage and quality loss. The major conditioning operations are in-bin natural drying of grain to reduce the grain moisture, followed by aeration to cool the grain. Sometimes over-dried grain can also be rehydrated to acceptable moisture levels to minimize shrink loss. A conditioning strategy guarantees that you get the most from your grain.
Grain bins equipped with a proper aeration system can be successfully used to dry grain using natural air. Natural air in-bin drying is the highest quality and most energy-efficient process. Appropriate and automated fan control strategies are required to optimize the drying performance with uniform drying, energy efficiency, and minimum under/ over-drying. Continuous fan operation may result in high operating costs (due to excessive energy consumption) and significant spoilage and/or shrink loss.
Grain aeration lowers grain temperature to increase safe storability and protection against mold and insects. Once the grain has reached target drying it must be cooled as soon as possible, and should be uniformly cooled to 1.7-4.4°C or 35-40°F for winter holding. Do not freeze the grain as it may result in significant condensation in the following spring/summer. It is important to ensure that grain temperature is uniform throughout the bin to avoid air current movement and potential condensation.
In a typical bin, dry air passes through the grain from the perforated plenum located at the bottom of the bin and absorbs moisture before exiting through exhaust vents located at the top. A higher airflow rate will remove a larger amount of water from the grain, which results in the faster completion of a natural air drying cycle. The recommended airflow rate for natural air drying is 1.0 cfm/bu for 3-5 point moisture removal.
Fans should be selected specifically to the bin size and grain type to achieve optimal airflow rate against the airflow resistance caused by the packed grain. Wheat and canola, for example, create higher resistance to airflow (static pressure) compared to larger seeds such as corn and soybeans at the same grain depth.
How grain bins are filled has a significant effect on airflow rate and distribution. Immature, fine, foreign material and broken grain tend to accumulate near the central core of bins and block or reduce the intergranular space creating airflow resistance at the core. This resistance forces air to move up through the sides of the bin which causes a longer drying front at the core and excessive consumption of energy. Since the airflow rate is higher near the bin wall, the grain near the sidewall over-dries due to excessive airflow which may result in significant shrink loss.
After filling, bins should be cored and leveled to provide uniform and sufficient airflow throughout. Fill the bin to a shallower grain depth if the moisture content is high or if the airflow rate is less than recommended. Shallower grain depths will reduce the airflow resistance/static pressure and the fan will deliver higher airflow for accelerated drying. Tall bins with small fans should not be used for in-bin natural air drying. Favourable weather conditions are essential for successful in-bin natural drying of grain. Running the fan in highly humid, overly dry, rainy, or cold ambient conditions will consume excessive energy creating poor drying results.
When you are forced to harvest when the grain moisture content is very high, it may be necessary to use high temperature drying with subsequent cool down to achieve safe storage conditions. High moisture grain often has quality concerns, leading to greater storage risks even after drying. Moisture content still needs to be carefully monitored as it is not unheard of for the moisture content of dried grains to rebound creating unsafe storage conditions.
When harvest occurs under extremely dry conditions, grain shrink can greatly reduce the amount of saleable product. Physically adding water to the grain is illegal and considered adulteration. However, moisture can be legally added by blowing natural humid air through the grain bin. There must be sufficient airflow rate and the ambient air must not be too dry. For this strategy to be successful the relative humidity needs to be above 80% for at least 8-10 hours of a 24-hour daily cycle.
Natural air drying is not energy efficient in winter months (mid-November to mid-March) due to cold weather (temperature below 4.4ºC or 40ºF), poor water holding capacity in air, and risk of major grain shrink at the bottom of bins. Avoid running fans in below-freezing temperatures to reduce the risk of condensation, vent freeze, and high moisture grain freezing together. Frozen grain blocks the airflow leading to potential hotspot development and subsequent spoilage.
Team Alberta has a groundbreaking study evaluating the energy efficiency of different on-farm grain conditioning systems. Year 1 observations are now available for viewing. The following article will review the findings of this first year of study.
Excerpts from http://www. advancedgrainmanagement.com/learn-grainmanagement/grain-conditioning/#criticalrequirements-of-successful-conditioning