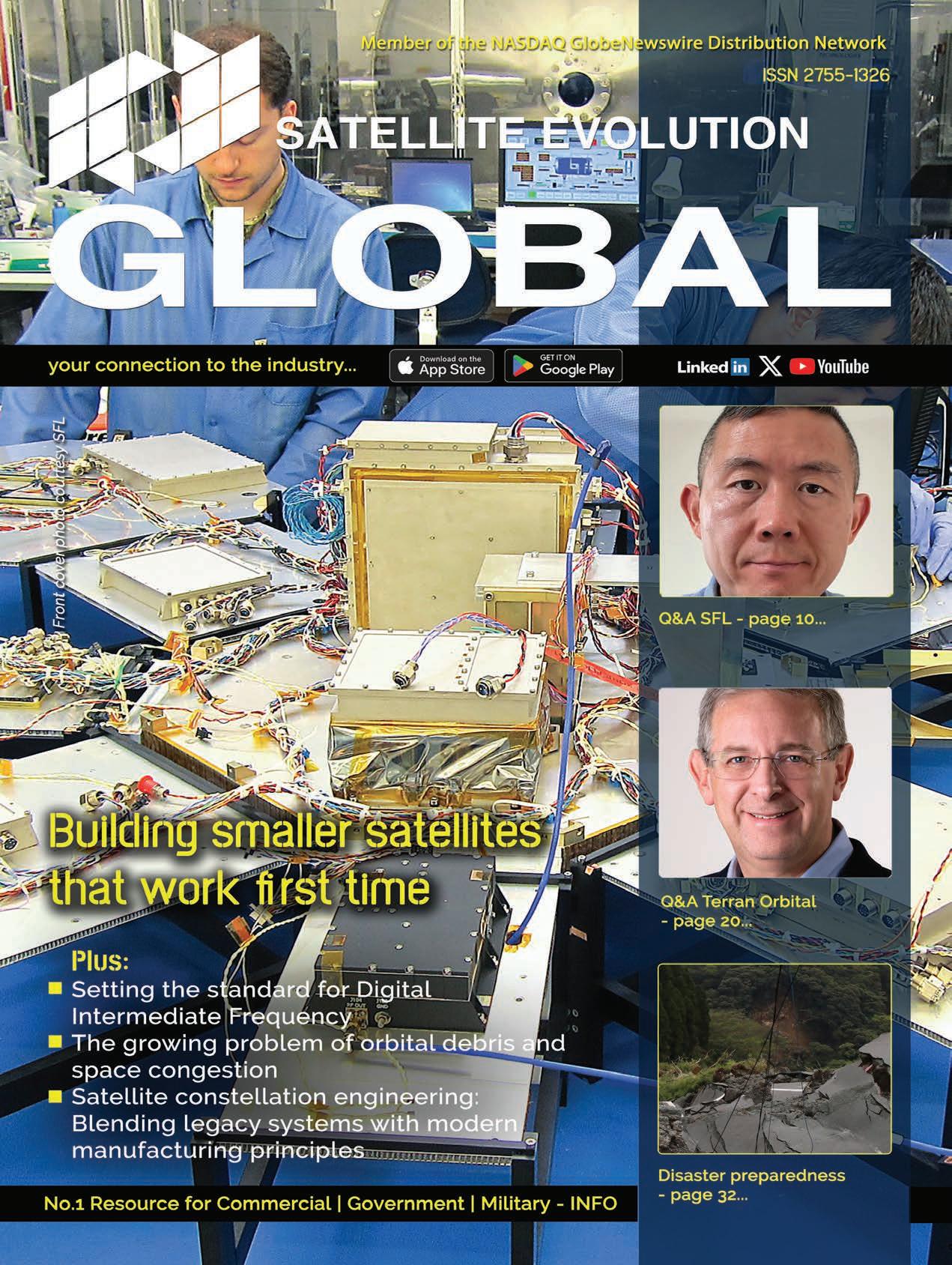
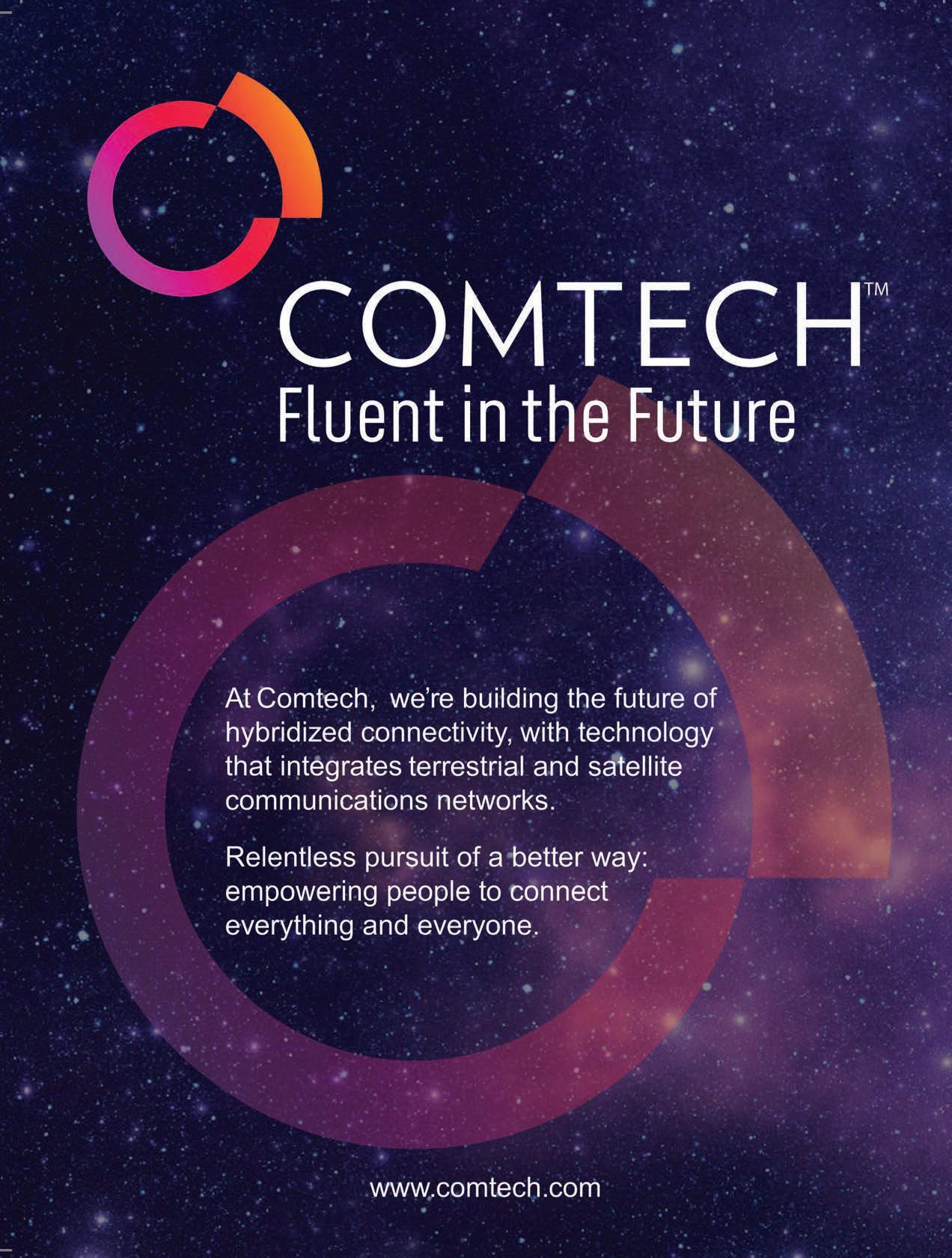
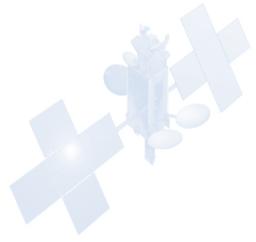
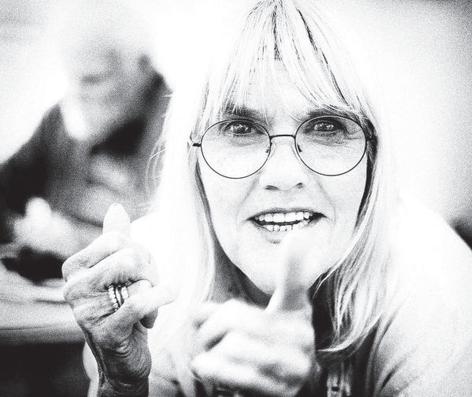
When NASA scientist Donald Kessler first warned of collisional cascading due to space pollution in low Earth orbit 46 years ago, there were only 300 operational satellites in space. Today there are more than 10,000 satellites in orbit with an estimated 75,000 expected by 2030, according to the European Southern Observatory (ESO).
Last year, scientists and researchers from NASA, the University of Plymouth, the Arribada Initiative, the University of Texas at Austin, the California Institute of Technology, Spaceport Cornwall, and Zoological Society of London called for a legally binding treaty that would address the staggering amount of space debris which is already orbiting the planet seven times faster than a bullet.
Although the majority of sovereign space agencies and many global regulatory entities recognize the dangers of space debris and underscore the importance of space situational awareness, we still have no large scale, globally accepted, enforceable laws in place to mitigate the problem. No wonder space is littered with a trillion bits and pieces of spacecraft.
At present, the only global agreement in place is the UN’s 1972 Liability Convention which is a nonbinding convention that assigns responsibility for damage caused by space objects either in space or falling to Earth to the launching party. Thus far, the convention has not been tested in court, even though there have been a number of high-profile incidents. One of the latest two involved the reentry of a fragment of a battery pallet from the ISS which crashed through the roof of a Naples Florida resident. The other incident happened in Canada when several sizable chunks of a cargo trunk for a SpaceX Crew Dragon spacecraft landed in a Saskatchewan farmer’s pasture. SpaceX voluntarily sent a van to collect its errant space garbage and gave the farmer a donation for an ice-skating rink, but there was no mechanism in place for the Floridian to seek compensation from NASA. As Isaac Newton confirmed in 1666, “What goes up, must come down.”
No one really knows how or if we’ll avoid the Kessler syndrome, but it’s comforting to hear that there are a number of NewSpace companies that are working hard to develop ways to address the removal of space debris and defunct spacecraft; to supply operators with reliable situational awareness tools; and to build spacecraft that will indeed burn up in the atmosphere as intended. These are wildly inventive individuals who have their eye on the prize: a safe and sustainable environment in space and on Earth.
In this summer issue of Satellite Evolution Global, Joe Chan, Director of Flight Dynamics at Intelsat delves into the growing problem of orbital debris and space congestion. Kevin Dunne, CEO of ETL Systems explains why close collaboration between solutions providers is essential for establishing a new open standard for Digital Intermediate Frequency. Managing Director of Atheras Analytics, John Yates, shares his thoughts about the critical role that satellite communications play in disaster preparedness and Brian Ippolitto, Senior Director of Business Development of Space Business Unit at Marotta Controls discusses satellite constellation engineering. The Space Flight Laboratory’s Director, Dr. Robert Zee gives us an in-depth look at his organization’s accomplishments and future plans. Finally, we hear from Marc Bell, Co-Founder and CEO of Terran Orbital who provides insight on how he has navigated the ups and downs of bringing the company public and is now charting an ambitious growth trajectory.
EUROPE: The successful first launch of the European Ariane 6 launcher is a milestone in MT Aerospace's corporate history. As the largest German supplier, MT Aerospace is responsible for the development, design and manufacturing of the metallic aerostructures of the new European launcher. The production of the tanks and structural components for the upper and core stages is a significant part of the Augsburg-based aerospace company's production and represents a work share of around 10% of the total launcher. MT Aerospace has introduced several innovations to increase the performance and reduce the costs of the European launcher. These include new manufacturing technologies such as the introduction of shot peening using AI processes to form components and the use of aluminum lithium as the material for the new launcher.
MT Aerospace is well prepared for the upcoming rampup, as the components for the launched flight model were already delivered in 2020. The company will deliver the 13th flight model in 2024 and the successful launch of
Ariane 6 will lead to a continuous increase in production volumes for MT Aerospace over the coming years.
"As a partner of the Ariane program since the very beginning, we are proud of our contribution to the successful first launch. Ariane will be the backbone of European access to space well into the next decade. The gateway to space will thus remain open for Europe - with a major contribution from Augsburg. My special gratitude goes to the MT Aerospace team who has contributed significantly to this positive result. This success will give us the necessary tailwind for future growth in our space business," says Ulrich Scheib, CEO of MT Aerospace AG.
EUROPE: In a landmark achievement to strengthen European security, CNS Solutions & Support, as a member of the Frequentis Group, has announced the completion of the CBRN Reconnaissance and Surveillance System (RSS). In response to evolving threats, the Frequentis Group has developed an innovative data fusion cell (DFC) to integrate sensor and uncrewed systems data, through its incident crisis management (ICM) technology. The DFC serves as a centralised hub, seamlessly integrating
information from various sources including sensors and drones, therefore enabling comprehensive analysis and rapid decision-making.
"Our DFC has transformed CBRN defence in Europe, empowering military personnel with real-time intelligence to respond swiftly and effectively to emerging threats," said Peter Skiczuk, Frequentis Vice President Defence.
The adoption of state-of-the-art technologies, including drones equipped with sensors and uncrewed robotic vehicles heralds a new era in CBRN defence. These uncrewed assets swiftly detect and assess hazardous substances, mitigating risks to human personnel. By leveraging data fusion and real-time analysis, commanders gain critical insights to make informed decisions, ensuring the safety of both military personnel and civilians.
EUROPE: Cobham Satcom has unveiled its most advanced maritime satellite TV antenna yet. Designed primarily for use on cruise ships and mega yachts, the 3.7 meter Sea Tel 370s TV is a groundbreaking solution designed to expand onboard access to the highest quality
programming anywhere in the world, while significantly reducing lifetime technical costs.
The Sea Tel 370s TV leverages the newest generation Sea Tel Integrated Marine Electronics (IMA) platform, which is already proven in the world’s most flexible and powerful marine VSAT antenna systems. New technology helps unlock several advantages for cruise and yacht charter companies by automating the manual processes that have until now been needed to make some of the most popular television channels available globally at sea.
Cobham Satcom’s new flagship TVRO antenna features automatic C-band switching between circular and linear polarization, ensuring uninterrupted viewing and
continuous availability of live television such as ESPN, which is one of the most popular cruise ship channels especially when major sporting tournaments are playing.
The introduction of the Sea Tel 370s TV advanced automatic switching alleviates the shipowner of having to undergo the costly and time-consuming work previously required when an engineer had to board the ship and manually convert antennas between circular and linear polarization when entering a new region served by incompatible satellites.
Further advances come from an innovative new technology that mitigates the recent phenomenon of 5G interference with satellite TV on board, when getting closer to land. Cobham Satcom has applied its decades of radio frequency engineering expertise to ensure that the Sea Tel 370s TV provides the best viewing experience under extreme atmospheric conditions as well as 5G signal interference.
Additionally, Cobham Satcom will be offering a feed upgrade which will be compatible with many of the existing Sea Tel 2.4 meter and 3.7 meter TVRO antennas already operating on cruise ships and mega yachts globally. The ability to upgrade these existing systems to the new Circular/Linear 5G filtered feed will save the customer considerable capital and operational expenditure.
Henrik Fyhn, VP & Product Line Director, Maritime, Cobham Satcom said: “While the ability to deliver high quality television on board is a key factor in guest satisfaction scores in the cruise sector, removing the need
for regular engineer visits to manually modify an antenna for ships traversing between incompatible satellite regions, can deliver at least six figure savings over the lifetime of a vessel.”
The Sea Tel 370s TV is Cobham Satcom’s second new TVRO launch in as many months. The company also released its all-new SAILOR XTR TVRO antennas in May this year. Consisting of 1 meter and 1.2 meter antenna systems, the focus is on a smaller onboard footprint, while offering class-leading global programming and interference free reception for improved viewing on a wide range of vessel types.
targets high reliability space-based
NORTH AMERICA: Teledyne e2v has announced the successful Space qualification of its 8GB space DDR4 memory as part of its edge compute solutions for space. This announcement marks the conclusion of Teledyne e2v’s DDR4 initial qualification. These include all the upscreening activities (temperature cycling, construction analysis, C-SAM / confocal scanning acoustic microscopy, preconditioning, Temperature Humidity Bias, …) and Radiation tests. As demand for compact, high-density memories surge, Teledyne e2v stresses that its latest memory chip is compatible with all contemporary highend space processing components. This long list of processors includes offerings from AMD/Xilinx VERSAL® ACAP, space FPGAs, MPSOCs, Microchip RT PolarFire®, as well as many proprietary ASICs.
Ultra-fast, high-density 8GB DDR4 memory provides the same form factor and pin compatibility of the smaller 4 GB DDR4 option – an ideal option for next generation designs.
Modern satellite payloads shift vast amounts of data minute by minute, hour by hour. Moreover, modern Microand Cube-Sats place huge constraints on system size and power. In general, space missions such as Earth observation require tens of GB of storage. Consequently, space missions stress current memory solutions in terms of memory bandwidth, access time, power consumption, physical size, and storage capacity.
"Fast memory is a critical component in modern dataintensive satellites. The new 8GB part doubles storage density in the same compact form factor of our previous 4 GB. Furthermore, with multiple temperature grades and qualification variants up to NASA level 1, Teledyne e2v has a diverse, ruggedized and versatile space grade portfolio," said Thomas Guillemain, Marketing & Business Development Manager, Data processing products.
The new fast 8GB DDR4 memory supports a transfer rate of 2400 MT/s. It is single-event latch-up (SEL) immune up to 60 MeV.cm²/mg. Moreover, the device provides 100 krad total ionizing dose (TID) and we have SEU data up to
60 MeV.cm²/mg. Physically, the 8 GB device is supplied in a package form factor matching the previous 4 GB version (i.e., 15mm x 20mm x 1.92mm) – thus doubling storage density whilst maintaining pinout compatibility.
EUROPE: ICEYE, the global leader in Synthetic Aperture Radar (SAR) satellite operations for Earth Observation, and the Ministry of Defense of Ukraine have signed a Memorandum of Cooperation to further strengthen their cooperation in remote sensing of the Earth in the interest of Ukraine's national security and defence.
The Memorandum of Cooperation builds on ICEYE’s unwavering support for the Government of Ukraine since 2022. In the Memorandum, ICEYE continues to constantly ensure that the imagery captured pertinent to Ukraine’s territory is used in the interests of ensuring the security and defence of Ukraine in conditions of armed aggression and not shared in any circumstance with hostile countries or entities.
The Memorandum also outlines ICEYE’s and Ukraine’s Ministry of Defense partnering to strengthen Ukraine’s
space defence capabilities even further and provide SAR expertise to support defence activities. The Memorandum focuses on advancing remote sensing technology, improving data use for security, and supporting Ukraine’s integration into the global space economy.
In August 2022, ICEYE announced signing a contract with the Serhiy Prytula Charity Foundation to provide the Government of Ukraine with ICEYE’s SAR satellite imaging capabilities. As part of the agreement, one of ICEYE’s SAR satellites is designated for the Government of Ukraine’s use over the region. In addition, ICEYE provides access to its constellation of SAR satellites, allowing the Ukrainian Armed Forces to receive radar satellite imagery on critical locations with a high revisit frequency.
Dr. Robert Zee, Director, SFL
The Space Flight Laboratory (SFL) is focused on delivering quality low-cost satellites and missions to customers around the world. To date, SFL has developed 76 successful satellites and has a total onorbit heritage of 318.8 years operational. We met with Dr. Robert Zee, SFL’s Director, to discuss technological breakthroughs; the microspace approach to building satellites; and some exciting projects on the horizon.
Crispin Littlehales, Executive Editor, Satellite Evolution Group
Question: What prompted you to establish Space Flight Laboratory, and how has the organization evolved over the last 25 years?
Robert Zee: The Space Flight Laboratory (SFL) was established in response to the opportunity to contribute four of the six subsystems for the MOST satellite and to integrate and test the satellite. MOST stands for Microvariability and Oscillations of STars. It was a space astronomy microsatellite, 57 kilograms, for the Canadian Space Agency. We provided the onboard computers, the communication subsystem, the structure, and thermal subsystems. Not only did we integrate the satellite in our lab, we also supported the launch campaign, commissioning and operations. We put together a team of about five staffers at the time and we got some money from the provincial government to set up some initially modest facilities. At the time, we were a one project team.
After MOST launched in 2003, we had to find a reason for being and think about how we were going to continue as a fledgling organization.
Production Program, SFL develops the
spacecraft
That’s when I started to reach out to people both within Canada and internationally to see whether they had any novel mission ideas for high performance nanosatellites and microsatellites. Until the advent of MOST, such miniature satellites were very immature and didn’t really have a lot of capabilities. But we were now at the start of a revolution and SFL was at the tip of the spear.
We started selling highly capable nanosatellites and microsatellites and that’s how we grew from five staffers to 70 members today, including engineers, technicians, engineering technologists, and administrative staff. We also currently have around 20 graduate students in our program in any given year. Today, we deliver spacecraft ranging from 3 to 500 kilograms.
Question: SFL has developed 76 successful satellites. What would you say are the most notable technological breakthroughs?
Robert Zee: The most notable breakthroughs include developing high performance, reliable, results-backed attitude control. Having excellent attitude control is very important. It enables you to point instruments at various targets, in space or on Earth—whatever the specific mission calls for. We also broke technological barriers by developing low-cost formation flying technology and algorithms. This is what allows spacecraft to control their relative position in space. They can have various configurations—positions relative to one another in orbit— so that, collectively, they can accomplish a mission that one spacecraft on its own cannot. An example is geolocating RF emissions where you need three spacecraft to trilaterate where the signal is coming from.
Another innovation was the development of miniaturized reaction wheels for small spacecraft, which didn’t really exist until we started working with others in the industry 25 years ago. Reaction wheels are nothing
more than flywheels on motors that you spin up and down to impart torques on your spacecraft that allow you to control your orientation in space. We also pioneered the use of miniature star trackers—sensors that image star fields and then compare those to onboard maps so that you can figure out what your orientation is in space to a very high degree of precision. It’s important to note that we flew both the reaction wheels and star trackers in collaboration with some key suppliers in the industry.
Over the last 10 years, we also created a modular power system that we use at SFL. We can scale this system up or down, depending on the power needs of a given satellite. We can use the technology for one-watt missions, or for one-and-a-half kilowatt missions using the same core approach with scaling. One more important breakthrough was the development of advanced radio technology with higher data rate radios that are small enough to fit in nano, micro, and small satellites. Last, but not least, we’re very good at making custom deployables for nano, micro and small satellites. Having deployable technology, whether it’s for antennas, solar panels, or what have you, allows us to accomplish many more missions than we could otherwise.
Question: SFL uses a “microspace approach” to small satellite development. Can you elaborate on that concept?
Robert Zee: We didn’t invent the microspace approach, but we learned it 25 years ago, and we’ve made our own additions to it along the way. As a result, we now have our own enhanced proprietary version of the microspace approach that we use on all our missions. What it boils down to is using a tightly integrated small-team approach to building spacecraft for a specific mission and focusing on those things that will result in on-orbit reliability. We have six to 10 people who work very closely together,
The NEMO-HD satellite successfully collects highdefinition multispectral imaging and video for Earth observation using a 60-kg satellite at low cost.
constantly communicating and focusing on the essentials necessary to build a small satellite in the shortest amount of time and at the lowest cost possible. There is reduced formality within the team. We don’t write a lot of documents that no one will read but instead stick to just the documentation that allows us to reproduce designs and understand analyses. This is different from the traditional space approach which follows a formula and is both process-driven and certification driven. The microspace approach concentrates on understanding the environment, developing good design, and testing at all levels. It is a distillation rather than an elaboration, and it requires great insight to get it right.
Question: Over the years, SFL has built satellites for clients in government, commercial, and academic/ research sectors. What are some of the most exciting projects to date?
Robert Zee: NEMO-HD is a 70-kilogram high performance, multispectral Earth observation mission that we developed in collaboration with the Slovenian Centre of Excellence for Space Science and Technologies. It has a highdefinition imaging payload consisting of two instruments. The primary instrument is capable of imaging in four spectral bands at a pan-sharpened resolution of 2.8 meters and covers a swath width of 10 kilometers. The secondary instrument produces images at 40-meter resolution and a much wider field of view. NEMO-HD was launched in 2020 and is still in operation. It has broken some barriers in terms of what an Earth observation satellite could do in such a small box.
Another interesting project was the CanX-4 and CanX5 formation flying mission in low Earth orbit that we did in 2014. We demonstrated different formations ranging from 50 meters to one kilometer in separation. The advancement was to bring down the cost of formation flying technology so that it could be incorporated into commercial missions like the one we are developing for HawkEye 360, a US company that sells radio frequency (RF) geolocation services. They geolocate RF emitters on the surface of the Earth to support security as well as
search and rescue applications. We’ve developed 27 satellites with HawkEye 360 thus far.
Two exciting projects that we’re working on right now— StarBurst and Aspera—are funded by NASA’s Astrophysics Pioneers program. StarBurst is a 350-kilogram satellite being developed for NASA’s Marshall Space Flight Center. It will be detecting gamma ray bursts from neutron star mergers in our galaxy to help us better understand the galaxy’s evolution as well as the origins of heavy elements. We are also providing the platform and the spacecraft integration for Aspera, which is being developed for the University of Arizona. Aspera will carry a small telescope that will perform highly sensitive far-ultraviolet observations to study the intergalactic medium.
Question: These missions are so varied. Do customers tell you what they want to accomplish and SFL does the rest?
Robert Zee: We don’t typically make or specify the payload, although, in some cases we do develop payload solutions if the customer doesn’t have one of their own. Our main efforts are in developing the platform and spacecraft integration, and test. We use a heritage core and customize the rest for each specific mission. We don’t push our own agenda. Our objective is to service the entire world in whatever missions are necessary. We serve all the sectors and all the different application areas—Earth observation, communication, surveillance and monitoring, technology demonstration, astronomy, and science. Our strength is in our ability to adapt to very different requirements and to be able to develop a solution that not only has heritage but also is efficient. We are able to develop a one-off satellite or a constellation and be cost effective. We have a strong track record with a very high success rate. We’ve lost only a few satellites to launch or separation failure. Our satellites work the first time. That’s why we have such a strong reputation in the industry whereby customers come to us.
Question: You have 23 microspace missions underway at your Toronto facility. Can you give us a preview of what you’re working on?
Robert Zee: We’re doing more work with HawkEye 360 on their RF geolocation missions. Their satellites, massing about 30 kilograms each, operate in clusters of three that fly in formation trilaterating signals to pinpoint their location. We currently have several more clusters under development, but they are not all the same. There are upgrades from cluster to cluster and always new innovations to include to provide the satellites with more payload capabilities. HawkEye 360 does the payloads, but we are the ones to enhance the satellites to support those new payloads.
We are also doing a mission called Gray Jay for the Canadian Department of National Defence’s science and technology organization, Defence Research and Development Canada (DRDC) to support an Arctic surveillance technology demonstration under the AllDomain Situational Awareness (ADSA) program. Launching later this year, Gray Jay consists of three 30-kilogram satellites flying in close formation in low Earth orbit to allow
for the timely detection of surface or airborne targets. Also scheduled for launch later this year is NorSat-4, a 30-kilogram spacecraft for the Norwegian Space Agency. It’s a ship tracking satellite, equipped with an Automatic Identification System (AIS) ship tracking receiver and a lowlight imaging camera capable of detecting light coming from ships on the nightside of Earth. The whole idea is to enable noncooperative ship detection. It is possible to spoof the AIS signals, which are RF signals that ships over a certain size must broadcast. It is also possible to turn off a ship’s AIS transponders. This makes it very difficult to identify the ship or know its location or where it is heading. Bad actors, for example, will do that, but having a secondary means to detect ships, like a low light imager will help with noncooperative ship detection.
As mentioned previously, we are working on the two NASA-funded projects, StarBurst and Aspera, both of which are currently in the assembly integration and test phase, and we are also doing more GHGSats. This constellation of 15-kilogram satellites is used to detect, monitor, and report on greenhouse gas emitters worldwide.
Question: Are some of these software-defined satellites?
Robert Zee: All our satellites have software, and we can reconfigure, update, and change the functionality of the satellite using that software so it’s a very important component. There’s been a lot of attention recently on software defined radios—that is, using software to generate the RF carrier and the modulation that you need. It’s essentially using a digital signal processor inside a radio to replace discrete components. We do have softwaredefined radios in some of our missions which provide great flexibility in certain cases where you’re able to change the modulation, the data rate, and the frequency on the fly.
Question: SFL has created a “Flex Production Program” to support the NewSpace sector. How does that work?
Robert Zee: NewSpace companies are those that want to sell data services or some kind of data product based on what they are collecting in space. They want to sell the data, but they also want to bring down infrastructure costs. If you’re talking about constellations, those companies often want to bring satellite production in-house to keep the costs down. The SFL Flex Production Program was created specifically for assisting these NewSpace companies by leveraging the expertise, technology, quality, and performance of SFL satellite designs. The idea is that SFL perfects the design and develops the first or first few spacecraft. From there, we can transfer the system integration knowledge to the customer to enable them to reproduce that same high-quality satellite to fill out their constellation. They would then integrate the spacecraft within their own facility and thereby keep the overall costs down.
We are doing a blend of that with HawkEye 360, for example, where we are still designing and building some satellites for them in-house, mainly whenever there are innovative design changes required. When it comes to repeat builds of the same spacecraft, HawkEye 360 is building and integrating those at their own facility. There are different tiers to this program. The simplest
is having SFL build the whole constellation, but another choice is that the customer builds out their constellation through technology or knowledge transfer. There’s another option where a third-party mass manufacturer is enlisted if the customer doesn’t want to do it themselves.
Question: What do you see as your biggest challenge now and how will you tackle it?
Robert Zee: Our biggest challenge is competition from new entrants in satellite development making misleading claims or exaggerating their capabilities and cost effectiveness. We address this issue the same way we’ve done for 25 years—by being patient and staying focused on what we do. We continue to build high-quality satellites at low relative cost and eventually people learn about the difference between what SFL delivers versus what others fail to deliver.
Question: In what ways do you see SFL changing five years from now?
Robert Zee: Many companies have certain growth targets. They want to attack certain markets and they have a business model with a targeted agenda. In contrast, SFL is market responsive in that we go where the demand takes us versus us pushing our agenda upon the market. We want to enable other companies and other organizations to achieve their goals in space. That’s our business model. We adapt to where the application users are going.
New applications are being generated, especially by NewSpace companies that want to build their business around a certain data product. There’s also a growing demand for exploration missions to the Moon or Mars. We are seeing that with the Artemis program and Lunar Gateway. There is opportunity for SFL to move into exploration missions using small spacecraft as well.
We will continue to do research in higher efficiency power systems, bringing more power and more capacity to bear for larger missions. We expect there to be new and better propulsion systems on the market that will enable us to do a broader range of missions. There will also be innovations and improvements in high data rate communications and optical communications. We plan to capitalize on all of these emerging trends in the future.
As innovations in Digital Intermediate Frequency (DIF) continue, close collaboration between solutions providers is essential for establishing a new open standard.
Kevin Dunne, CEO ETL Systems
So fast is the pace of innovation in the NewSpace industry that it’s on track to be worth around $1.8 trillion by 2035 from the current $630 billion, according to the World Economic Forum. One of the biggest drivers for this is the booming IoT market, which is expected to be worth US$947.50 billion globally this year, and grow by almost 10.5 percent annually until 2029.
It’s great news for the organizations already using IoT and the many more that could benefit from it. Automotive, industrial and consumer sectors are among the most enthusiastic adopters of IoT but there’s set to be steady growth in areas like healthcare too.
The limitation on all this is bandwidth—at the moment, the ground segment doesn’t have the capacity to scale fast enough to satisfy such a rapid increase in demand. While the convergence of Radio Standards such as V/HTS multi-orbit satellites, Wi-Fi, 4G and 5G has been an important step forward, it is not enough by itself. Many in the space sector recognize these limitations, which is why interest in Digital Intermediate Frequency (DIF) has surged in recent years.
Bridging the gap between traditional RF technology and the virtualized ground segment, DIF offers similar benefits to the ones we’ve seen in broadcast and telecoms: better performance and scalability, and lower costs for the user. Distance is no longer a barrier either, since digital signals can be transported anywhere in the world using secure private IP networks. In comparison, RF signals transmitted over fiber start to degrade as soon as they are transmitted, and conditioning can only mitigate this degradation, not stop it completely.
DIF is particularly valuable in the defense and security sector, as it enables the antenna to be physically decoupled from the modem. Similarly, potentially targeted RF emissions can be located away from personnel, enhancing their security. Governments benefit from enhanced security because encryption equipment can be managed in home territory instead of in hostile environments. There are also efficiencies and cost-savings that come from removing the distributed network of modems, encoders and decoders, and maintaining everything in a single location instead. Digitization would also mean software can be reconfigured at need remotely, reducing the investment of time, manpower, and equipment required to achieve operational flexibility.
If it hadn’t been for the introduction of a standard gauge railway system in the UK 180 years ago, it’s unlikely that the Industrial Revolution would have gained the momentum that it did. Today, in the New Space era, we’re facing similar questions about interoperability. Excitement about the opportunities space-based technologies bring is fueling innovation and investment, yet both are in danger of drying up unless there’s also greater certainty in the market. Specifically, we need an agreed open standard to ensure that solutions providers work together to avoid poor performance, vendor lock-in, and costly equipment (both hardware and software) becoming obsolete and incompatible with other systems.
There’s a fine balance to strike between being overly prescriptive and being too flexible: if solutions providers
are too rigid in their approach then innovation may be dampened, yet trying to meet the needs of every possible use-case can mean they end up satisfying none. So what’s behind the lack of standardization?
The Digital Intermediate Frequency Interoperability (DIFI) Consortium points to the almost ‘infinite number of ways to encode digital IF bits into a standard IP packet’ –something that isn’t the case with analogue IF. It adds that, “standardization has not advanced beyond the framework level and cannot offer interoperability across vendor systems.” This, it warns, could halt the digital transformation of the ground segment.
ETL has taken a leading role in DIFI since January 2022 because we too recognize that standardization is critical to a strong and resilient satellite sector. We’re helping to shape the DIFI open, interoperable Digital IF Interoperability standard – and applying it to our own product development. Following an intensive R&D period, we are now able to support organizations who want to use DIF to translate analogue RF signals to digital and vice versa with our new DIF product, Genus Digital 5000.
Having been in this industry for more than 35 years, we know that change doesn’t happen overnight; analogue RF isn’t going to disappear in the short or even the medium term. We believe that interoperability should include compatibility with existing and legacy RF equipment. This approach enables organizations to turn investment in equipment like modems from CAPEX to OPEX, reducing both barriers to entry and the risk.
Also lowering the barrier to entry is the emergence of ground segment as a service (GSaaS), which allows users
to access the ground station network on a pay-as-you-go basis. Standardization is crucial here too, enabling operators to plug in and downlink data from satellites in the most efficient and effective way possible. Two of the leading cloud providers, Microsoft Azure and Amazon AWS, are investing in technologies to support DIF. This is already starting to create new ecosystems of space solutions providers – for instance, the satellite telco SES has previously announced plans to co-locate four satellite ground stations at Microsoft data centers.
One of the best things about NewSpace is its diversity: the big global players rubbing shoulders with ambitious start-ups, and hardware and software solutions providers all working to solve some of the biggest global challenges we face. Along with defense and security, the technology could pave the way for highly accurate weather forecasting which has multiple applications, not least proactively monitoring climate-related events such as hurricanes.
Collaboration and strategic partnerships are now firmly embedded in NewSpace. What’s crucial is that they’re all working to agreed standards to halt any divergence and fragmentation that results in users being left with obsolete systems. There’s a clear commercial incentive for NewSpace companies to do this in order to future-proof their products, but there are social and ethical reasons too, particularly where the quality of the signal transmission could have a direct impact on human life. Fortunately, we are moving in the right direction. A number of standards are now in operation, including the European Cooperation for Space Standardization (ECSS) and the well-known ISO. Together with the DIF standard, these will ensure that the many technologies born of the New Space industry deliver here on Earth
Marc Bell, Co-Founder and CEO, Terran Orbital
Despite a rough ride on Wall Street, Terran Orbital is soaring to new heights. With a second state-of-the-art manufacturing facility soon to come online and an impressive backlog of orders, the company’s future looks bright. We sat down with Marc Bell, Co-Founder and CEO of Terran Orbital to get an inside look at how he has navigated the ups and downs of bringing the company public and is now forging a decisive growth trajectory.
Crispin Littlehales, Executive Editor, Satellite Evolution Group
Question: You have a fascinating and incredibly successful track record as an investor. What prompted you to found Terran Orbital and how has the company evolved over the last decade?
Marc Bell: My partners and I both grew up as science fiction nuts. Partially thanks to Star Trek, we’ve always been fascinated with anything and everything space. When the opportunity arose to purchase the company that popularized the CubeSat, Tyvak Nano-Satellite Systems, we did. One of my partners, Tony Previte, had a degree in Aerospace engineering, so we decided he should run the company. He ran it for 10 years and just under four years ago he asked me if I would take over for him. I was more than happy to do so, but I didn’t want to run a small CubeSat manufacturing operation, I wanted to build another unicorn.
Within three years of becoming CEO, we went from building a few CubeSats a year to being able to produce more than 200 space vehicles a year. In the next year, we expect to be able to manufacture over 1,000 space vehicles annually, complete with payloads and solar panels, largely using our own components and controlling our supply chain. Today, 90 percent of the components we use are manufactured in house, which is
a huge deal. It plays out very well in the satellite industry where everyone has been having supply chain problems. I always say that “if you control your supply chain, you control your destiny.” The more control you have over your supply chain, the better chance you have of success because you rely less on outside vendors. We’re able to avoid common issues because they’re limited to just a few things that we don’t make in house yet, but eventually will.
Much of our focus has historically been on space vehicles in LEO orbit. We’re now expanding and starting to focus on all orbits and mission. The days of big satellites in GEO are over and there’s no reason to build the massive behemoths that used to take up to 10 years and US$ 1 billion to create. We are creating a much smaller size—up to 1000 kilograms at a better price point and at a much faster pace. It’s better to spend less money, replace the satellite sooner, keep the technology current, and get more bang for your buck.
We’re seeing high levels of interest from both foreign telecoms and militaries who are migrating from traditional GEO satellites to small sat LEO, MEO, and GEO. Every military wants what United States has. They want a transport layer, a tracking layer, and all the other things that we do here. At present, we are talking to a lot of people around the world about this technology.
Question: You took Terran Orbital public in March 2022 and the share price has fallen steadily. Still, Wall Street analysts believe in Terran Orbital and predict a strong comeback in the market. What do you see in terms of the company’s potential over the next 12 months?
Marc Bell: My partner and I decided to take Terran Orbital public and merged into a special purpose acquisition company (SPAC). Between us both we had already taken 17 companies public, more than six of which were unicorns. Then, the SEC issued guidance shortly before we merged into a SPAC which prevented companies that go public through a SPAC from filing a shelf registration statement and issuing equity for one year. This undermined our ability to access the capital markets immediately.
Because SPACs are usually around for a year before they merge into a company, the prior ability to typically be able to file a shelf immediately upon going public to access the capital markets and raise as much money as you need
was a great benefit. By removing that, those who were investing in SPACs ran away because all the upside was taken away. Because we were a capital-intensive business, we ended up putting on a lot of debt when we “de-SPAC’d”. We went from US$ 20 million in revenue initially to US$ 94 million in 2022 and US$ 135.9 million in 2023 and we are continuing to grow revenue wise. As predicted, we are growing into our company and in the not-too-distant future we will become EBITDA (earnings before interest, taxes, depreciation, and amortization) positive, then net income positive, then free cash flow positive. We always look at companies from the top down. We start with revenues, then we want gross profit margins. Critics point out that Terran Orbital has a lot of SG&A (selling, general, and administrative expenses) but that’s a fixed price regardless of our growth now.
Question: CAPSTONE was a huge success. What was it like working on such a high-profile project with NASA and Advanced Space?
Marc Bell: CAPSTONE is the ‘Energizer Bunny’ of satellites. As of today, it has surpassed 2 years in operation and still phones home every week. The satellite’s robust design and our engineering expertise have enabled it to operate flawlessly for even further enhanced NASA tests.
The goal was to show and test the communications network for the eventual permanent Moon base and station. We needed to prove how they could communicate and always stay in contact with home even on the dark side. Ultimately, there will be a constellation of satellites so whomever is up there can always phone home.
NASA was a pleasure to work with, as was Advanced Space. They made good partners on the program. We we’re able to spend a lot of time with Advanced Space throughout the program. The vehicle continues performing beyond expectations and NASA and Advanced Space are considering even more updates and missions for the vehicle.
Question: You’ve spoken recently about “responsive space”. Can you expand on that concept and tell us how the company’s suite of standard space vehicles comes into play?
Marc Bell: Back in 2005, Vice Admiral Arthur Cebrowski
and then Colonel Jay Raymond, who would become Chief of Space Operations for the US Space Force, wrote a paper called “Operationally Responsive Space” which was far ahead of its time.
Responsive space is about getting an order and delivering it at warp speed. The world is becoming more dangerous, and space is becoming a new domain of warfare. We need to be prepared so that if our satellites get knocked out by our adversaries, we can replace them very quickly. The Department of Defense (DoD) is spending a lot of time figuring out both the launch and the satellite side. At Terran Orbital, we are focusing on how to build satellites faster while lowering the cost and increasing the functionality so that we can be truly responsive to the needs of the customer.
We do this by controlling the supply chain and by making the components and modules in-house. Soon we’ll have a new facility opening and we’ll begin inventorying all the components and modules. In September of last year, we announced a new set of standards, and released a new set of buses that are based on those standards. The components inside don’t really change, it’s just a question of how many batteries and how many reaction wheels are used for a particular model.
We use the same batteries and the same reaction wheels regardless of which model is selected. It’s rather like Legos—mix and match making them quick and easy to assemble.
Question: Terran Orbital is changing the game when it comes to manufacturing satellites. Can you share some details about your current and future mass production capabilities?
Marc Bell: We have facilities in several places in California. We are completing a 94,000 square foot state of the art manufacturing facility in Irvine, CA to expand upon our existing 60,000 square foot facility there. We expect to reveal more details about what we’re doing later this year.
Question: The company is now billing itself as an “endto-end mission provider”. This is quite different from the strategy you were pursuing in early 2022 which was centered around PredaSAR. What inspired you to shift your priorities so dramatically?
Marc Bell: A few years ago, I wasn’t involved with Terran Orbital as much. I was on the Board of Directors, but I had a separate company that I was running called PredaSAR. When I became CEO and we took Terran Orbital public, we merged the two companies together.
Terran Orbital now sells SAR (synthetic aperture radar) satellites, based on the PredaSAR product line. We’re currently in the next generation of SAR panels. The product is a lot more sophisticated and has higher resolution than the original PredaSAR product. Since there are restrictions on what resolution you can sell on the commercial side, most of the customers are government.
Question: What are the key challenges facing Terran Orbital and where do you see the company five years from now?
Marc Bell: The biggest challenge is managing growth. We have 44 satellites on the floor being built right now, a steady workflow that keeps that plant busy, and we look forward to the new facility to be operational. We do a lot of work for US customers, but we also have a company in Italy called Tyvak International which continues to grow. There we work predominantly with foreign entities such the European Space Agency (ESA) and numerous European foreign governments.
Five years from now? The world is changing very quickly. Look at the opportunities in space. The FCC is dealing with 50,000+ applications for satellites and that’s just the United States. It’s a big planet and every country wants to become a space power. As a result, we’re seeing the market expand exponentially. Terran Orbital is here to not only keep pace with this cosmic expansion but to lead the charge into the final frontier.
We depend on satellites for our global wellbeing. Without them, civilization as we know it would quickly disintegrate, leaving us in chaos and uncertainty. Space debris and congestion are posing a double threat to orbital safety, and we need to address it now.
Joe Chan, Director of Flight Dynamics at Intelsat
Imagine a world where satellites are no longer operational. Essential services would quickly fail, and global society would begin to crumble. Communication systems would collapse as mobile networks and the internet fail. Power grids, unable to coordinate distribution, would suffer frequent blackouts, plunging cities into darkness. Aviation and maritime navigation would become untenable, causing trade to grind to a halt. This would then lead to widespread shortages of food and other essential supplies. Financial systems would break down, triggering economic chaos and rampant inflation. Civil unrest would erupt, and governments would struggle to maintain order.
As societies regressed to more rudimentary technologies and solutions, communities would need to adapt quickly to survive in a fragmented, disconnected world.
While this vision of the future could be deemed sensationalist, it at least conveys the point that if we don’t address the growing problem of orbital debris and increased space traffic, we’re heading towards a bleak future. If left unchecked, these issues pose significant risks to operational satellites and other space missions. ESA’s Annual Space Environment Report illustrates how if we continue to act in the same way as we currently are, some orbits will become unusable due to the high density of space debris. For continued and future use of space, satellites must be able to operate safely and avoid collisions. However, as the number of objects in space increases, this will become more and more difficult.
There have been a growing number of headlines around space debris in the mainstream media of late, which perhaps indicates a growing interest and awareness around orbital debris and space safety in general. This year, we’ve had headlines about the infamous toolbox dropped by a NASA astronaut during a space walk around the International Space Station (ISS), as well as the case of the debris object that hit a house in Florida which has since been identified as the remains of a pallet of batteries jettisoned from the ISS three years ago.
As we know, orbital debris is not a new phenomenon. It has been accumulating since the first satellite, Sputnik I, was launched in 1957. Now, some 67 years, 6,500 rocket launches, and 16,900 satellites later, ESA estimates that there are over one million pieces of space debris in orbit measuring over 1cm. Add in even smaller pieces and you’re looking at a number somewhere over the 131 million mark. ESA has also calculated that even if no new missions were launched from now on, the number of debris objects would continue to increase because larger pieces would still break up at a typical rate of four to five per year.
These days, it’s not unusual for operators to perform on average two collision avoidance manoeuvres per year for every satellite in operation. ESA reports that it performs three to four of these manoeuvres per year with each of its Earth orbiting spacecraft. These manoeuvres are costly for operators in terms of time spent assessing the risk, fuel used to move away from the object, as well as downtime because of the avoidance manoeuvre. As orbital debris increases, there will undoubtedly be calls for more of these manoeuvres which will have significant cost implications for operators.
Cost implications aside, if left unaddressed, the accumulation of space debris could lead to a cascade effect known as the Kessler Syndrome, where collisions between objects in space create more debris, leading to further collisions and an exponential increase in debris. This scenario could render certain orbits unusable, severely limiting space activity. At best this means higher costs and risks associated with operating satellites, increased insurance premiums, and potential disruptions to services. The worst-case scenario is the dystopian future described at the beginning of this piece.
To protect the future use of space, we need to reduce the risks associated with debris and prevent collisions. This is a complex challenge. At its most basic level, we need to stop creating new debris, improve Space Situational Awareness (SSA) systems and develop ways to actively remove existing debris.
1 - Prevent new debris from being added by adopting responsible satellite life cycle management
Although the number of debris will increase even without further launches, it’s critical that we prevent the creation of new debris from being added to orbit. To do this, the entire industry needs to manage satellite life cycles more responsibly, including implementing adopted best practices, and improving deorbiting strategies. Ensuring that satellites are designed with end-of-life disposal plans, such as controlled re-entry or moving to a graveyard orbit, is crucial.
This approach significantly reduces the potential for future debris generation. Recognizing this, the US FCC moved from a 25-year orbiting rule to five years for all FCC licensed LEO satellites. Similarly, ESA LEO missions have also moved from 25 to five years.
A recent NASA report on the cost and benefit analysis of mitigating, tracking, and remediating orbital debris highlighted that rapidly deorbiting defunct spacecraft is one of the best measures for managing orbital debris. The analysis found that changing from a 25-year rule to a loweryear rule is a cost-effective way to reduce risk to space operators. It also concluded that more net benefits could be gained by reducing the deorbit timeline further than five years; moving all the way to a 0-year rule could result in nearly US$9 billion in net benefits. This is certainly something to aspire to.
Improving SSA is essential for tracking and monitoring space debris so that we know the location of debris as well as where it will be soon. When this information is accurate, it’s possible to predict potential collisions so that operators can decide how to respond. Tracking and monitoring all the debris that can cause harm is a huge undertaking for obvious reasons. The number of debris pieces is in the millions, some pieces are very small and difficult to see, pieces are moving at high speeds, and their orbit paths can be difficult to predict.
Technology in this field is advancing all the time. Developments are making it possible to assess potential collisions (conjunctions) with more accuracy, as well as locate and monitor smaller pieces of debris than was feasible in the past. Modern SSA systems may employ ground-based and space-based sensors to detect and track objects in space, alongside pooling data from various sources.
There are several different public and private SSA systems in operation, and the accuracy of conjunction assessments varies enormously. The Space Data Centre (SDC), run by not-for-profit member organization Space Data Association (SDA), is one such platform that provides conjunction assessment and warning services. Supported by COMSPOC, the SDC ingests flight dynamics information from the member companies as well as other available sources of space object information. It utilises member provided ephemerides, with integrated manoeuvre information and fuses this with TLE (Two Line Elements) and SP (Special Perturbation) data from the public catalogue to accurately assess the possibility of a conjunction.
In addition to preventing the creation of new debris and improving SSA, debris remediation is required to reduce the risks of existing debris. This could mean moving debris to prevent a collision, removing it completely from orbit, or possibly even reusing and recycling it. A number of technologies are being developed in order to move debris out of the pathway of spacecrafts. For example, research currently being carried out by West Virginia University and funded by NASA is exploring whether the process of laser ablation and photon pressure performed by a network of space-based lasers, is a viable option to remove debris of varying sizes. This approach targets the debris with a laser beam, or multiple laser beams, to vaporise a small part of it, in order to generate a high-velocity plasma plume that changes the trajectory of the debris. Another method that is attracting a lot of interest is the deployment of micron scale dust to enhance the drag of debris, to move it to a different path, or to force re-entry.
The market for space debris removal solutions and services is rapidly expanding and there are a number of commercial companies working to develop ways to actively remove debris. Japanese company Ex-Fusion is developing a ground-based fusion laser system that uses powerful lasers developed for nuclear fusion power, but at an order of magnitude lower, to remove or redirect debris. The company reportedly aims to test the technology at the EOS Space Systems observatory near Canberra in Australia.
Swiss company ClearSpace has developed a capture system that uses robotic arms to target and capture debris for safe removal. ESA has commissioned the company to target and remove a defunct 112kg Vespa upper stage rocket part from orbit, under the ClearSpace-1 mission.
ClearSpace is also leading the Clearing the LEO Environment with Active Removal (CLEAR) mission, which is funded by the UK Space Agency, and aims to remove two UK satellites from orbit that are both roughly the size of a washing machine. Japanese company Astroscale is another private company working in the field of debris removal. It has developed and successfully trialed a magnetic capture system (the ELSA-d mission) for retrieving defunct satellites or other objects, for removal and for on-orbit servicing. The company is also undertaking another mission, ADRAS-J, commissioned by the Japanese government, to safely approach and characterise an existing piece of large debris, a prelude to capturing and removing debris.
Managing and mitigating the risks associated with both space debris and increased space traffic is an incredibly complex challenge and we don’t yet have all the answers. It does however feel like the momentum is building, and we’re starting to make some headway. Public-private partnerships like those highlighted above are clearly going to be critical in developing effective debris mitigation and removal technologies.
A number of sustainability initiatives and guidelines for mitigating the impact of debris have also recently been introduced by organisations and agencies such as ESA, NASA, and the UK Space Agency.
These are a welcome step in the right direction, as are the growing number of collaborative and industry led initiatives being launched to improve space safety and protect the future use of space. Now that we’ve started to make some progress, it’s critical that we keep this momentum going.
As the number of active satellites in orbit continues to grow at a rapid rate, heritage components evolve to bridge the gap between cost, mass production, and performance.
Brian
Ippolitto,
Senior Director, Business Development of Space Business Unit, Marotta Controls, Inc.
Propulsion systems onboard space vehicles are not typically characterized by high-volume, low-cost development, engineering, and production. Built for specialized missions, these high-reliability systems are manufactured in very small numbers, typically dozens at a time, or less. While that was once the nature of space itself – a vast frontier with relatively few pioneers blazing new trails – today the landscape is much different. The proliferation of Low Earth Orbit (LEO) satellite constellations represents a new opportunity, both commercial and military, featuring hundreds or thousands of satellites per constellation. Working together, these systems solve remote sensing challenges, gather and transmit data, monitor weather and climate patterns, provide affordable
internet services to rural areas, and enable fast and reliable global communications.
Constellations are recognized for low latency, with swarms of small units (<500 kg) designed to be cheaper and faster to deploy. Propulsion systems, once designed for production of one, five, ten, or one hundred, now need to be manufactured by the thousands in certain cases. This demands an entirely new design and development model, one that must leverage existing systems, components, and expertise proven for spaceflight. As illustrated in Figure 1, NewSpace customers are willing to sacrifice some mission capability in order to prioritize cost and schedule. With planned constellations now routinely consisting of many hundreds or thousands of satellites, as opposed to a dozen or less on a legacy program, operational success can be achieved while minimizing the impact of single-unit failures.
Industry options are slowly evolving to address this challenge. Modular designs tap into the heritage of proven components, now supported by Design for Manufacturing (DFM) principles that balance quality against costs and scalable production.
Traditional space heritage technologies are exceptional in every way – but their extremely low volume production, extended development timelines, and high costs do not meet the mission needs for new space innovators working to beat the odds with successful mega-constellation development. At the other end of the spectrum are inkjet printer companies or hobby rocketry firms, providing lowcost, low-quality materials. Neither approach meets the need for quickly and competitively delivering massive numbers of space-proven components optimized for LEO constellation development.
Designing with a lower-priced, non-heritage component and working to increase its quality is a risky approach for constellation developers. Alternatively, the strategic ideal is to access proven quality but identify other
In this pressure-reducing valve assembly design, the mechanical regulator valve is the Marotta RV001. Isolation and pulsecontrol solenoid valves are Marotta PLV015 units . The RV001 was developed specifically for satellite constellation electric propulsion applications with krypton or xenon media. The solenoid valves were developed for use in combination with the RV001 and have been repurposed to act as primary bang-bang pressure regulating valves. Photo courtesy Marotta
opportunities to reduce costs. To achieve this, system developers and their component providers must be willing to work in close partnership – evaluating potential design trades early in the development cycle. How will the system really be used? Can design trades accommodate a minor percentage drop in performance parameters? The smallest adjustments can make all the difference in balancing cost and manufacturability, with limited impact on overall performance. The same close cooperation can also help aerospace suppliers and their manufacturing partners redefine production techniques, reducing costs and enabling manufacturing at scale.
Heritage components often demand more complex machining operations, with multiple steps and tool paths increasing complexity and cost. Collaboration and new technology are helping to streamline manufacturing, often allowing components to be created using a single machine. Heritage developers must work closely with a new set of suppliers, refining and retooling machine operations for the most cost-effective solution. This simplicity, coupled with the ability to produce large numbers of a certain part already proven in a spaceflight system, creates immediate economies of scale. Parts can be generated much more effectively and used in a variety of building block designs, enabling a streamlined, modular approach to developing propulsion subsystems.
This is demonstrated in the manifolded configuration of an electric propulsion system recently developed by Marotta Controls for use in a LEO constellation application.
In contrast to chemical propulsion, electric propulsion is typically fueled by a noble gas such as krypton or xenon with very low flow rates. Such systems are used for minor adjustments and station keeping, controlling flow through tiny, pinhole-sized openings. Using existing Marotta components, the system required only minor design modifications to meet overall performance criteria. The company drew from its extensive catalog of spaceflightqualified components, designing the assembly in accordance with component capabilities using heritage data. Subcontractor-designed components selected are all commercial-off-the-shelf items with no significant changes.
A manifold arrangement was selected to minimize assembly time and complexity. The manifold design also offers modularity such that the system can be configured as mechanically regulated or bang-bang pulse-controlled. Subassemblies are assembled and tested prior to integration. The manifold is manufactured from a single piece of aluminum, all flow paths and connections are directly machined into the body. The manifold is similar to other Marotta valve bodies and can be manufactured at high production rates with ease. Consideration was given to machining optimization and producibility during the design.
In the use case presented above, low cost and high performance were achieved with component simplicity, and system architecture is largely focused on design for manufacturability. Common components are utilized wherever possible. Piece part count is kept to a minimum, and assembly complexity is considered and optimized. The regulator described contains just seven machined parts and is designed for a manifolded assembly interface. It features an adjustable setpoint and a high turn-down ratio
in a compact, lightweight, and low-cost package. The solenoid valve contains just five machined parts and features an integrated filter and latching option.
The maturity of launch vehicle design is 60 years in the making, while the constellation business has progressed over the last handful of years and is only beginning to take shape. Here, new space stands on the shoulders of legacy space flight innovation. The same advancements that took mankind to the Moon and beyond are critical in constellation strategies – they just can’t be developed and delivered in the same way. Modular concepts leverage existing capabilities to develop or springboard propulsion
systems. Development is accelerated overall and furthered with a DFM focus that features simplicity at the heart of the manufacturing process.
Even as cost is a consideration in a new space market focused on constellations and their associated volume production, systems must perform in space. System providers must understand the unique impact of physical rigors such as lack of gravity, extreme temperatures, and environmental contaminants.
Heritage expertise and product data allow providers to leverage this expertise and take a critical eye to component design. As NewSpace evolves, quality must remain the design starting point as industry players determine new ways to proliferate LEO systems affordably and quickly.
Connectivity is now an integral part of our day-to-day lives, with consumers and businesses alike utilizing connected applications to enhance daily routines as well as to access and manage essential services. It’s also a critical component of disaster preparedness, response, and recovery, and in these situations, satellite networks are often the only infrastructure that can be relied upon to provide critical communication.
John Yates, Managing Director, Atheras Analytics
Satcom provides connectivity across entire countries or regions. User terminals can be rapidly deployed, and networks can operate without dependence on local infrastructure which may be damaged or overloaded. These features make it extremely well suited for establishing connectivity in disaster situations.
As reliance on connectivity increases across all domains, so too does the importance of reliability. For reliable, continuous satellite connectivity, effective and efficient ground segment infrastructure is essential. However, as satellite operators know only too well, weather can significantly impact the spectrum, and this can hugely hinder an operator’s ability to provide seamless connectivity.
In a disaster situation where the stakes are incredibly high, having uninterrupted lines of communication could well save lives.
IMPROVING RELIABILITY AND RESILIENCE
Disaster planning goes much further than just having a plan; it also involves ensuring that reliable and resilient infrastructure is in place before disaster strikes. It pays to invest in disaster planning.
According to the UNDRR (United Nations Office for Disaster Risk Reduction), every dollar spent reducing risks posed by disasters can save US$15 in post-disaster recovery costs.
To ensure continuous connectivity post-disaster, networks need to be reliable and resilient. To achieve this, operators need to mitigate the effects of weather and manage the spectrum effectively. Getting this right is the key to increasing throughput, minimizing signal degradation, and reducing downtime. Efficient ground segment management not only benefits customers across the board who depend on seamless connectivity, but
crucially, when incorporated into disaster preparedness, it can also make the response and recovery process more effective.
Without effective mitigation, wet weather events can cause signal strength and quality to reduce. This attenuation causes interruptions and potentially loss of service. Rain fade is nothing new and satellite operators have a range of tools and techniques at their disposal to mitigate its effects. However, while these fade mitigation techniques are effective at managing the impact of weather in traditional satellite networks that use lower frequency bands such as C, X or Ku-band, they’re less effective when networks use Ka and Q/V-bands, which are becoming increasingly widespread. Used with High Throughput Satellites (HTS) and Very High Throughput Satellites (VHTS), these higher frequency bands can deliver much faster data transfer rates but are also much more susceptible to rain fade than lower frequency bands. Ka or Q/V-band VSAT terminals are increasingly being employed in mission-critical applications such as defense, security, and disaster response.
To manage the effects of weather with these types of networks, it has been common practice to set up a dedicated diversity gateway for each primary gateway so that the two gateways can be kept synchronized. If the primary gateway is impacted by weather, the operator can seamlessly “hot switch” to the diversity gateway that is operating in a different location that is unaffected by the same weather conditions. However, with the increasing use of HTS and VHTS satellites requiring dozens or even hundreds of gateways it becomes economically prohibitive to put in place a dedicated diversity gateway for each primary gateway and operators are increasingly turning to the use of Smart Gateway Diversity whereby a few diversity gateways are shared between many active gateways, thus saving up to 40 percent in ground segment costs.
However, such an approach requires pro-active network management and gateway switching to maintain high levels of network availability and so the ability to
predict these outages before they occur becomes very desirable if not essential. Many companies are now looking to AI to improve weather management, by leveraging it to optimize network design. They are using AI-techniques to predict which gateways would likely be affected by weather before the event occurs.
Weather forecasting is a complex field which has advanced greatly over the years. Forecasting today uses supercomputers and AI techniques to assimilate huge volumes of historical and real-time data for enhanced accuracy and specificity of predictions. AI improves prediction models by analyzing vast amounts of data to identify complex patterns that traditional models might miss.
As well as providing precise, short-term predictions for specific locations, AI also strengthens early warning systems for extreme weather events, enabling better disaster preparedness and management.
When AI’s capabilities are applied to ground segment management, satellite operators can pro-actively manage simple two-station diversity gateways as well as more complex smart gateway diversity arrangements. Operators can use AI techniques to predict outages several hours ahead; to analyze weather predictions at available diversity gateways; and to automatically transfer traffic to alternate gateways before outages occur.
Similarly, AI techniques can be used to forecast outages for a Ka-band or Q/V-band VSAT terminal at a specific location so that appropriate mitigating action can be taken.
The ability to predict outages for users of these terminals will be of significant operational benefit because it will enable lines of communication to remain open during mission critical situations such as disaster response.
Utilizing AI for network design and management allows operators to implement contingency plans well in advance, which can prevent service disruptions and ensure continuity of connectivity, whatever the weather. Not only does this enhance operational resilience, but it also optimizes resource allocation, bringing cost benefits. With the ability to accurately forecast weather events, operators can manage traffic proactively, maximizing the utilization of available spectrum.
The benefits associated with using AI-based tools for weather management extends beyond operational efficiency and customer satisfaction. In a disaster situation, having reliable and resilient lines of communication saves lives because if outside agencies can communicate effectively and coordinate with partners on the ground, response efforts are much improved.
The key to overcoming many of the challenges that operators face when delivering continuous connectivity in disaster scenarios lies in having the tools to effectively design ground networks during the planning phase, as well as the ability to accurately predict outages hours ahead to enable pro-active management of gateways. Continuous connectivity needs to be planned for as part of disaster preparedness and AI is fast becoming a key component in improving reliability and resilience.
Innovative Rocket Technologies Inc. (iRocket) has announced the former Chief Technology Officer of RollsRoyce has joined the iRocket Board of Directors. Paul Stein, who also spent several years as Director General for Science and Technology of the UK Ministry of Defence (MoD), and is a current member of the UK Prime Minister’s Council for Science and Technology, brings experience in technical oversight, engineering discipline, and insight into the rapidly expanding UK space program. As a member of the iRocket board he will help guide the company in the development of its next-generation fully reusable Shockwave launch vehicle and facilitate its entry into UK opportunities.
“As a strategic visionary and board member to iRocket, Paul brings invaluable insight as we establish our presence in the UK,” said Asad Malik, founder and Chief Executive Officer of iRocket. “iRocket has made exceptional progress in advancing our technology and extending our reach with a growing number of government organizations. Having Paul on our Board of Directors provides us with a fresh perspective based on his depth of experience and success in guiding technology organizations.”
Mr. Stein has a portfolio of activities in aerospace, energy and nuclear technologies. Currently he is CEO of Floral Energy, a US - UK start-up energy company. He is also an advisor to a US fusion company and assists with business strategy for a large aerospace corporation. In
addition to his role on the UK’s Council for Science and Technology he also lectures on aerospace and defense at Cranfield University, where he is a visiting Professor
During his time as Chief Technology Officer at RollsRoyce, Mr. Stein had oversight of technology strategy and investment for Rolls-Royce technologies including defense and civil aerospace propulsion, nuclear energy, and power generation. While he was Director-General, Science and Technology for the MoD, he was accountable for Science and Technology investments across land, sea, air and space.
“iRocket’s innovative engine and launch technologies are set to transform the cost of access to space for both civilian and defense customers,” said Paul Stein. “I’m quite selective about the companies that I advise and iRocket captured my attention because of the many new defense capabilities their technologies will enable at a time when it is very important for the free world to boost its advantage.”
Max Space founders Aaron Kemmer and Maxim de Jong have announced the appointment of Kirsten Whittingham as President of Max Space. Kirsten brings to the company a history of accomplished leadership in spaceflight, aerospace, and defense in commercial, military and government sectors. Within her purview, Kirsten will lead Max Space business development as it enters these markets.
“Kirsten has the engineering, business, and financial acumen to bring Max Space to the forefront of space station deployment in the next 4-5 years, as the International Space Station (ISS) is decommissioned,” stated Kemmer. “Her most recent experience in a leadership role at Axiom Space, a privately-funded space infrastructure developer, to contracts with international governments for missions to the ISS, will be a great asset to Max Space.”
“Max Space is an exciting new innovative and entrepreneurial private venture with the ability to change the direction of the space economy through low-cost and high-performing inflatable space stations,” remarked Whittingham. “I immediately envisioned how I could lead the company to the next level, given my solid background in spaceflight, customer support, and business operations.”