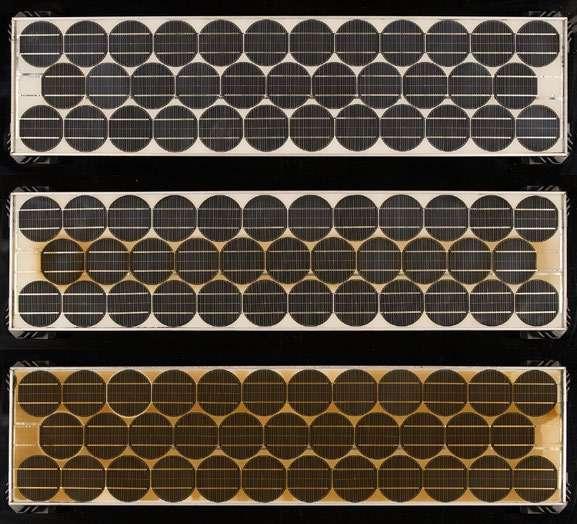
21 minute read
Module
PVEL Flags Serious Issues With Module Quality
Solar's huge rise has been matched with an even bigger expansion in capacity, primarily in China, and now, the rest of the world too. With manufacturing capacities rising from 25 GW in 2015 to over 400 GW today. These have driven costs lower, even as incremental innovations across the value chain have also helped. For modules, perhaps the most obvious indicator has been higher output, and hence, larger sizes. Now, PV Evolution labs, (PVEL), a leading independent test lab for the downstream solar and energy storage industry, has rung the alarm bells on a possible risk to the sector, from quality issues.
Advertisement
Its 2021 PV Module Reliability Scorecard which came out last week, names 117 model types of PV modules from 26 manufacturers as Top Performers in PVEL’s testing. While applauding the widespread adoption of technical advances that increase PV module power output and reduce the cost of solar power, it flags reliability issues that could trip up performance gains, if not fixed early. One in three participating manufacturers failed to implement basic quality controls that protect end users from safety failures.
“An unprecedented expansion of PV module manufacturing capacity is underway. New factories and production lines are vital as demand for solar power soars, but buyers must be vigilant to avoid the risks inherent to rapid growth,” commented Jenya Meydbray, PVEL CEO. “The preventable safety failures observed in this year’s Scorecard underscore the complex challenges that manufacturers face as they race to meet demand in a highly dynamic global market.” The output comes from the PV Module Product Qualification Program (PQP), a comprehensive testing regime established by PVEL in 2012 to provide empirical data for PV module supplier benchmarking and project-level energy yield and financial models.
“As PV manufacturing capacity expands, mega-scale, 100+ MW projects financed by risk-averse traditional investors are the new norm. Yet the most innovative technologies are unproven in the field. We trust PVEL for the technical data we need to de-risk Primergy’s 2GW project pipeline,” said Adam Larner, Chief Operating Officer of Primergy Solar, a wholly owned subsidiary of Quinbrook Infrastructure Partners, a global investment manager with $8B invested in 19GW of power generation.
Notable findings in the 2021 Scorecard include:
Twenty-six percent of the bills of material (BOMs) eligible for this year’s Scorecard had at least one failure as compared to 20% in 2020. One in three manufacturers tested experienced safety failures due to junction box defects versus one in five in 2020. The majority of these failures were observed prior to testing.
Five manufacturers received their first Top Performer listings in this year’s Scorecard.
The report includes two new Top Performer categories that showcase modules with superior results in PVEL’s mechanical stress sequence and minimal susceptibility to light-induced degradation and light- and elevated- temperature induced degradation.
The greatest number of failures occurred during the mechanical stress sequence, a test PVEL recently added to the PQP to address durability concerns, especially for extreme weather.
“From glass to junction box, PVEL’s latest Scorecard again demonstrates that the quality of a PV module depends in part upon the materials it contains – yet many buyers never request BOM details from suppliers,” noted Tara Doyle, Chief Commercial Officer of PVEL. “Between supply chain instability and the ever-present push for lower prices, one cannot assume that every module sold under a given model type uses tested BOM components. Buyers must specify their desired BOM in supply contracts to achieve this.” Participation in PVEL’s PQP and Scorecard is voluntary for manufacturers and only topperforming module model types are named in the Scorecard. To date, PVEL has tested over 450 BOMs from more than 50 manufacturers for the PV Module PQP.
The views underscore the fear among many industry veterans that the new projections built by developers and private equity investors leave very little margin for errors, or delays caused by issues beyond policy impact. That can be dangerous, as an overwhelming part of the PV capacity in existence has been built in the past 6 -7 years, which means we will start seeing issues vis a vis warranties only now, and in the coming years.
PVEL has highlighted how they are seeing degradation rates of upto 15 percent in cases. Similarly, while modules with one type of encapsulant degraded just 4.9% on average after 35 years, modules with two other encapsulant formulations exhibited much higher mean degradation rates of 19.1% and 26.1%.
All this, when expectations are of a minimum useful life of 15 years , going up to 25 years. A significant performance degradation could seriously impact those projections.
Longi Claims 3 World Records For Cell efficiency
Xi’an-headquartered major solar PV manufacturer LONGi has consolidated its leading role in R&D innovation in the global PV industry by setting new cell efficiency records for N- and P-type TOPcon and HJT.
The company announced in April its record of 25.09% for N-Type TOPCon solar cell efficiency and, one month later, testing at the Institute for Solar Energy Research (ISFH) in Hamelin, Germany, has confirmed that the conversion efficiency of N-type monocrystalline bifacial TOPCon solar cells developed at LONGi’s Cell R&D Center has now reached 25.21%.
The Cell R&D Center has also achieved an innovative breakthrough in highefficiency P-type monocrystalline solar cell product technology. Again tested by ISFH (Calibration Mark: 001592), the efficiency of a commercial size P-type monocrystalline bifacial TOPCon solar cell exceeded 25% for the first time, setting a world record of 25.02% in the process.
ISFH has also been able to confirm that the conversion efficiency of a commercial size monocrystalline HJT solar cell produced by LONGi’s New Technology R&D Centre reached a record of 25.26%, additionally placing the company at the forefront of HJT related technology.
“With the ambitious goals we have set for ourselves, our approach is to stay close to the essence of technology by selecting the best technical route, maximizing product performance potential and proactively ushering in the changes needed to achieve the technical transformation,” commented Dr. Li Hua, Vice President and Head of LONGi Solar’s Cell R&D Center.
The development of new energy technology is one of the critical factors in achieving China’s two goals of ‘peaking’ carbon by 2030 and achieving carbon neutrality by 2060 and LONGi’s highefficiency cell and module technology and resultant products enable the company to maintain its leading position in the industry in terms of efficiency, performance, quality and cost, contributing significantly to reaching these objectives LONGi produces monocrystalline silicon wafers and modules, delivering solutions for distributed and ground mount power station systems, promoting the development of the global PV industry and driving energy transformation.
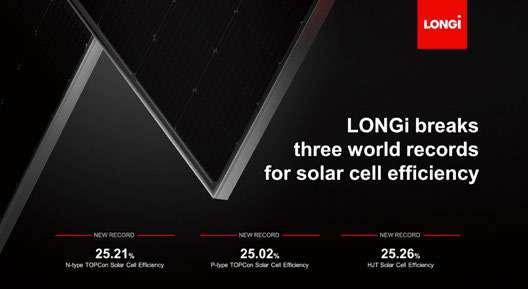
Former leader Yingli Solar Strives For Comeback
Yingli Solar, which was once the largest manufacturer of solar panels in the world and the first Chinese company to sponsor the FIFA World Cup TM, has announced plans to make a serious comeback.
The Hebei province-based firm, which slipped from a peak turnover of over $2.4 billion in 2011 to less than $650 million by 2018, was declared technically bankrupt in 2018, with a huge debt overhang and falling sales. The deficit attributable to shareholders of Yingli Green Energy amounted to US$ 1.9 billion in 2018, while its deficit in working capital amounted to US$1.7 billion. This, while not counting multiple bank loans where the firm had defaulted.
Yingli Green Energy, the holding company that was listed on the New York Stock Exchange (NYSE), was liquidated, unable to repay long-term debt owed to Yingli China. Now, in April 2021, the restructured company’s first general meeting of shareholders and directors was held, and a new board of directors and management team was announced and approved. As a sign of the company’s change in direction, its debt-to-asset ratio has dropped to 59.26%. This ratio will continue to decline, as new capital injections are expected. The debt with financial creditors has been converted entirely into equity. The local government owned investment platform has contributed US $ 312.8 million. The company has also engaged with strategic investors who are willing to invest US $ 625.6 million.
“After the restructuring, Yingli Solar has become financially healthy again,” said Xulong Yin, Chairman of the Board of Directors, who also added “Even during the most difficult periods of debt, Yingli Solar still maintained high sales volumes, delivered with all the guarantees, and offered an exceptional level of customer service. This is solid proof of the incredible caliber and dedication of the Yingli Solar staff, and we see a bright future for the business.”
In 2020, the firm claims that Yingli Solar has distributed 2 GW of modules around the world and has continued to invest funds in R&D. It has announced expansion of its cell production capacity to 5 GW and photovoltaic modules to 10 GW, with a two year plan to take it to 15 GW.
The firm now faces a tough market, where its erstwhile smaller competitors have all grown manifold while it slumped, and the market is back to being volatile, with prices see-sawing. In its second coming, it should be instructive to see how Yingli thrives.
First Solar To Expand US Manufacturing
The leading American manufacturer of solar panels and PV power plants, First Solar Inc. has announced its plans of expanding its American domestic photovoltaic (PV) solar manufacturing capacity by 3.3 GWDC (gigawatt direct current) annually, with an investment of USD 680 million. This investment is representing an implied capital expenditure of approximately USD 0.20 per watt. The move follows nudges from US admin officials to firms to cut dependence for solar imports on China.
The company is initiating the construction-based developments of its third new manufacturing unit in America’s Lake Township, Ohio. This new manufacturing is expected to take the company’s Northwest solar portfolio up to 6 GW in the future. The Ohio factory is expected to start production by the first half of 2023, after getting permissions of pending approval of the various state, regional, and local incentives.
Speaking of their new developments, CEO of First Solar, Mr. Mark Widmar stated, “This facility will represent a significant leap forward in photovoltaics manufacturing, a true factory of the future. It will leverage our advantaged position at the intersection of efficiency, energy yield, optimized form factor, and cost competitiveness while leading our manufacturing fleet in delivering the highest efficiency and wattage, and the lowest cost per watt.”
As per the company’s claims this facility will be one of the most advanced of its kind in the solar industry, allowing it to produce an anticipated average of one module roughly every 2.75 seconds across its three-factory Ohio footprint once it achieves its full production capacity. Designed and developed at its research and development (R&D) centers in California and Ohio, First Solar’s advanced thin-film PV modules set industry benchmarks for quality, durability, reliability, design, and environmental performance. Each module features a layer of Cadmium Telluride (CadTel) semiconductor that is only three percent the thickness of a human hair and the company continues to optimize the amount of semiconductor material used by enhancing its vapor deposition process.
Additionally, Besides its Ohio manufacturing facilities, First Solar also operates factories in Vietnam and Malaysia.

JinkoSolar’s N-Type Mono-Si Solar Cell reaches Record 25.25% Efficiency
Shanghai-headquartered solar panel manufacturer JinkoSolar Holding Co., Ltd. announced yesterday that the maximum solar conversion efficiency of its large-area N-type monocrystalline silicon solar cells reached 25.25%, setting a new world record for large-size contact-passivated solar cells.
This result has been independently confirmed by the National Institute of Metrology, China (NIM). It is the third time that JinkoSolar has broken this world record since July 2020.
Dr. Hao Jin, Chief Technology Officer of JinkoSolar Co., Ltd., said, “We are very proud to have set three world records for the most advanced large-area N-type cell in the world in less than one year. Maximum cell conversion efficiency improved from 24.79%, to 24.9%, and now to 25.25%”
The company states that it has made industry-leading iterations in silicon wafers, solar cells and solar modules over the years. Material upgrades integrated into the cell process and fabrication on a practical size of 267.4cm2 of high quality monocrystalline Czochralski (CZ) silicon substrates allowed JinkoSolar to produce 25.25% cell efficiency.
To attain this extremely high solar cell efficiency using ultrathin polysilicon, several advanced technologies have been implemented including JinkoSolar’s high quality N-type wafer, passivating contact technologies, advanced diffusion system, surface passivation, metallization of crystalline solar cells and other innovative technologies. The company believes that this breakthrough will allow it to mass produce N-type TopCon cells.
Mr. Limin Xiong, Researcher of NIM, said, “As China’s highest research facility of measurement science, and CNAS Capability Verification provider for solar cells and modules in Electrical Parameter Testing, NIM is committed to providing consistent, accurate and reliable data for scientific and technological progress. At present, it has accounted for 80% market share in thirdparty calibration services for standard solar cells and innovative solar cells (including perovskite cells).”
He added, “China aims to reach carbon emissions peak before 2030 and achieve carbon neutrality by 2060, so the PV industry has been gearing up for even faster growth with LCOE and solar cell efficiency being the most important factors. I am glad to witness this new world record, and our teams will continue to cooperate and contribute to the industry through R&D.”
India’s Three Battles To Lose
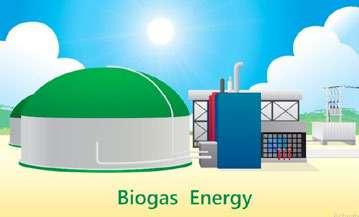
What, and how India sets about achieving climate goals in the decade to 2030 matters. Not just for the impact it will have in contributing to our impact on global warming, but also for what it does to shift the country decisively away from our current energy pathways. The decade to 2030 also seems to be growing more relevant due to the rate at which the world is being forced to reconsider targets set for say, 2050. Suddenly, those targets don’t seem ambitious enough, considering the damage extreme events linked to climate change have started causing. Consider the unprecedented assault on coal and thermal power, where, thanks to developments in solar, wind and storage, many countries will achieve their goals to reduce by 2025 by 2022 itself. That means the pressure will soon shift, as it has by way of restrictions on financing fresh coal projects, to developing countries like India.
The good news is that India’s performance, outlined by Prime Minister Narendra Modi, based on the estimated present reduction of emissions intensity by 21% over 2005 levels is on track, for now. Even the Emissions Gap Report 2020 of the United Nations Environment Programme(UNEP) includes India among nine G20 members who are on track to achieve their unconditional commitments under the Paris pact, based on preCOVID-19 projections. These targets are based primarily on twin pillars of renewable energy and expanding our forest cover to act as a carbon sink of 2.5 to 3 billion tonnes by 2030.
But challenges loom. As the country seeks to kickstart a massive effort to industrialise, urbanisation has picked speed, even as agricultural land continues to command a premium to feed a vast population. That means higher energy needs, and targets like expanding forest cover will be increasingly harder to reach.
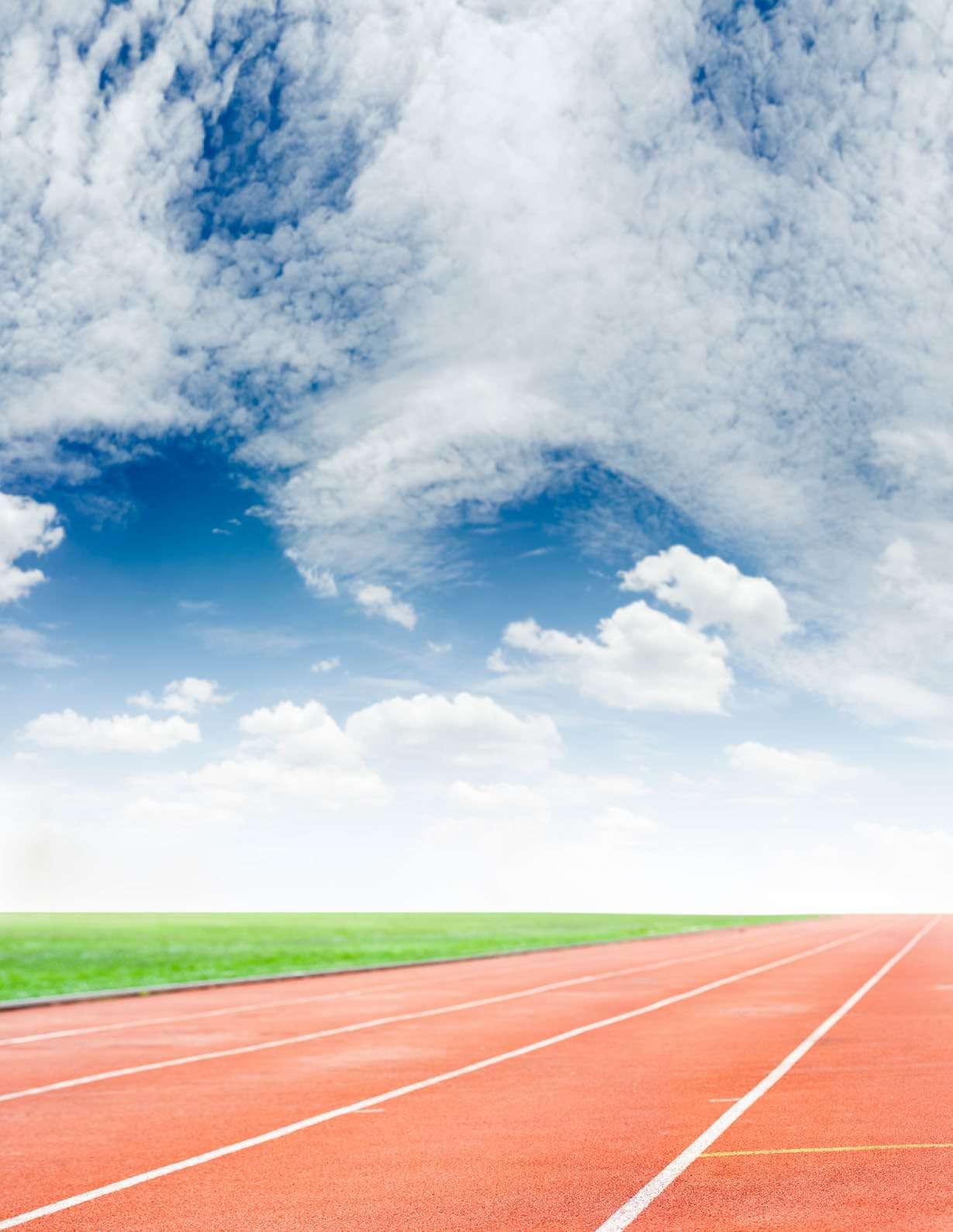
DEMAND PROJECTIONS
According to the International Energy Agency (IEA), energy use has doubled in India since 2000, with most of that demand met by coal and oil. This is set to grow about 35 per cent until 2030, down from 50 per cent before the coronavirus pandemic. IEA predicts primary energy consumption almost doubling to 1,123 million tonnes of oil equivalent as the Gross Domestic Product (GDP) expands to USD 8.6 trillion by 2040. By 2030, India will overtake the European Union by 2030 to move up to the third position in energy consumption, worldwide. With imports accounting for 84 percent of its oil consumption for fuels and related sectors, for the country, finding greener, better options is not just good for the environment, but a very strong economic case too.
India’s Response
Today, it has become clear that India is responding to the challenge with a mix of strategies. Right on top is the ascendance of solar power, which, together with wind, will be competing on equal footing with thermal power for share of contribution to the national power mix. Second, and equally important, are two multi billion dollar initiatives, that seek to not only cut down the country’s dependence on fossil fuels and its import bill, but also achieve multiple objectives along the way. These are the Ethanol blending targets for 2025, and the Compressed Bio Gas (CBG) initiative to have 5000 CBG plants by 2025. Track progress on these three, and it’s safe to say, you have a marker on India’s overall progress towards its climate goals. So let’s go right in.
Solar Power: Why It Matters, and The Risks
According to the Ministry of New And Renewable Energy (MNRE), India’s solar capacity at the end of May was at 41.09 GW, with Wind Energy at 39.44 GW. The report adds that 50.89 GW of projects are under implementation, while 29.52 GW are under bidding process. Those numbers bely the actual state of affairs by a margin. A significant part of the projects under implementation are suffering from huge delays, while projects under bidding process are in even deeper trouble. Readers will notice that adding up all the numbers above takes us very close to the 160 GW that was the original solar+wind target for 2022. That target, which was looking eminently doable in 2017, 3 years after being declared, is now simply not going to be met. Blame that on a huge miss in the rooftop solar category, where, against a target of 40 GW , we stand at barely 6 GW today.
That is not the primary cause for concern though. The bigger issues that we have covered extensively in previous issues, is that the underlying reasons for the delays have yet to be tackled in any meaningful way. This includes our policy on protecting and encouraging domestic manufacturing , while not doing it at the expense of solar growth. Or weeding our inefficiencies in
the existing power purchase environment, which has forced discoms to try an beat down solar prices beyond levels that would have been considered impossibly low when solar targets were set. That is taking its own toll on long term quality and sustainability. These issues, along with various state level issues, have combined to make financing for large solar projects difficult for all but the largest developers, domestic or foreign, forcing a consolidation in the sector that is too early , and unhealthy. Fewer players, be it on the developer side or the manufacturing side, risks making policy making hostage to their needs, at the cost of the end consumer. That will never be an optimum solution.
With almost 20 GW per annum of fresh capacity and installation needed for the next 10 years, solar’s challenges for the next decade need to be fixed now, before the 2030 target also looks ridiculously over-ambitious.
Compressed Bio Gas
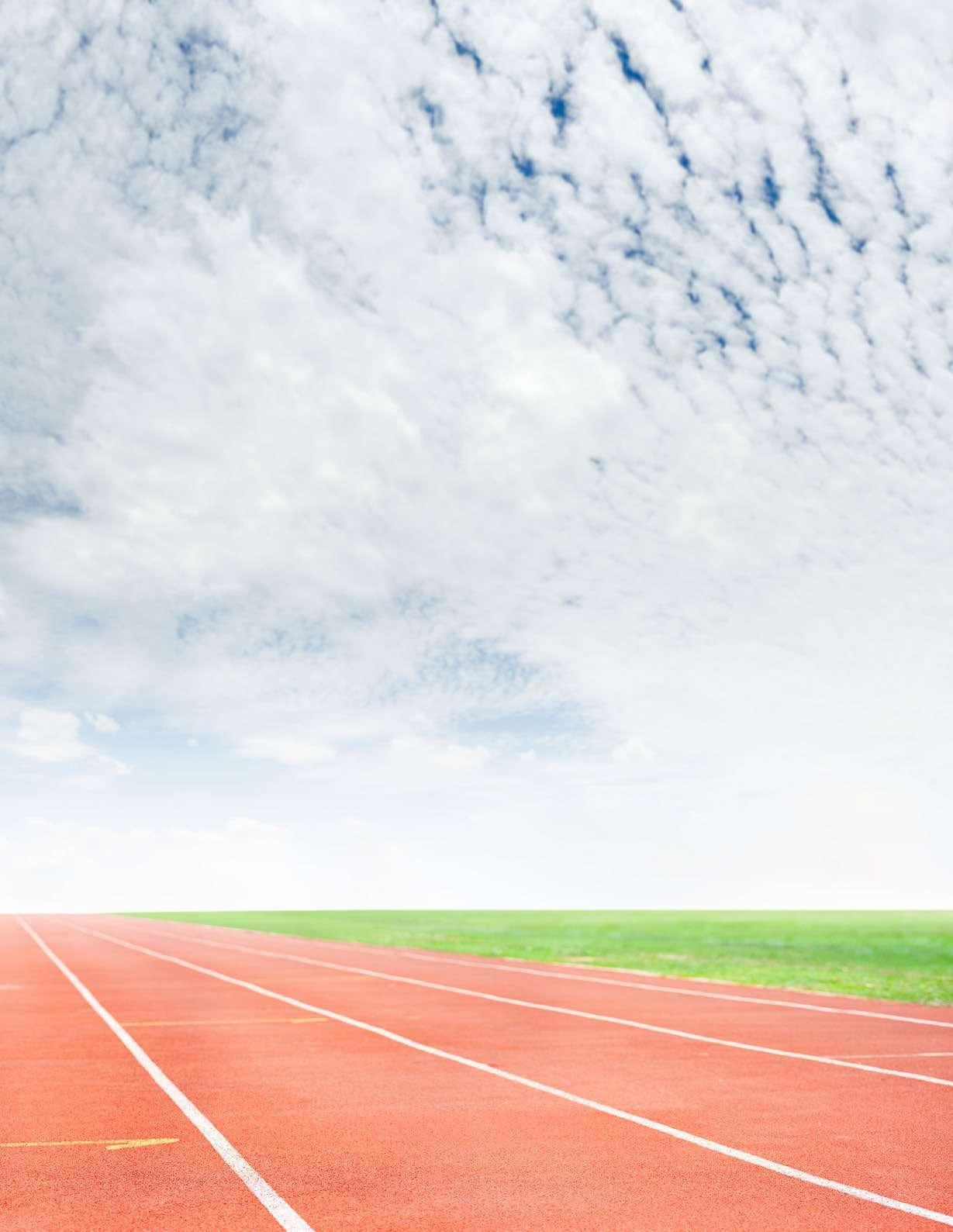
If Ethanol attacks India’s dependence on petrol, CBG tries to take the battle to that other automotive fuel, Diesel . On paper, the government has set a very ambitious target of 5000 CBG pants by 2025, entailing an investment of 200,000 crores, or Rs 40 crores per plant. To produce 15 MTA of the gas, which is about 40 percent of current CNG consumption, generating direct employment for 75,000 people and producing 50 million tonnes of bio-manure. Being equivalent to CNG, where we already have a well developed ecosystem and infrastructure, CBG integration is likely to be the easiest to manage. A huge bonus from an optics perspective on CBG is that it can also use up residues that are otherwise burnt, and cause very visible air pollution.
CBG, though similar to CNG, offers better calorific value and can be used as green fuel in automotive, industrial and commercial sectors. With a procurement price of Rs 46 per unit till 2024, along with a buying commitment for 10 years, it has a lot going for it. All of this is under the National Biofuels Policy 2018 and Sustainable Alternative Towards Affordable Transportation (SATAT) initiative.
CBG production necessarily is expected to be lower cost, lower scale and more spread out. By using agri residues and other bio waste, it also promises to make a serious contribution to the Swachh India Movement. However, this segment has probably taken the biggest hit from the covid pandemic. That means the existing targets are not going to be met. Even though the Petroleum and Natural gas ministry reports that Letter of intent for 600 CBG plants have already been given and MoUs for 900 more plants signed, a total of 1500 CBG plants are at various stages of execution. Rs 30,000 Cr of investment is envisaged in these 900 plants.
A typical period for manufacturing these plants would be 15-18 months according to industry players we spoke to. This includes the time taken to get environmental clearances, which can go upto 6-9 months. One area where the government can work more proactively to speed up the process. Like Ethanol, CBG has the advantage of enough firms that can supply the machinery, and the technology. Be it Indian firms like Praj Industries, to global experts like Evonik, which has a large Indian presence. The Reserve Bank of India has done its bit too, by making financing of CBG plants part of priority sector lending .
The Ethanol Rush
The Ethanol blending program, which just saw a major push after Prime Minister Modi brought forward the target to achieve 20 percent blending with petrol to 2025, from 2030 has two key objectives. To cut down imports of fossil fuels, and to provide a remunerative option for farmers from agricultural residues, especially sugarcane. Of course, ethanol, when used as a blend with petrol, also helps cut down pollution, since it does not release any carbon.
The current blending level for ethanol in India has crossed 7.4% .The new target is expected to create a demand of additional 10 billion litres of ethanol per annum. On a current production base of 4 billion litres. In a key move to encourage ethanol production, permissible feedstock options have been expanded by adding starchy feedstocks to the list in the form of surplus grains. That means, states like Bihar and Chhattisgarh have introduced state specific ethanol production policies to attract investments. That is welcome in a situation where just three states, Uttar Pradesh, Maharashtra and Karnataka were looking set to dominate ethanol production. More importantly, it changes the nature of the industry from a location driven, seasonal production sector to one that is potentially more spread out, with supplies through the year. A huge plus for the ethanol push is the fact that it has been entrusted to the Oil Marketing Companies (OMC’s) to establish production as well as support other producers with long term purchase agreements. Prices, at Rs 62 per litre are also considered remunerative enough to raw in investors willingly, although interest subsidies have also been provided. The OMC’s, that are usually cash rich, provide a strong measure of comfort to the biggest investors , sugar firms that will expand or build fresh capacities now. With clear demand visibility for the next 5 years, the pathway is really clear, and in this case, has every chance of being achieved, with significant positive impact across states . Surprisingly, a challenge might come from the third key pillar of self sufficiency, namely CBG. With CBG plants being much more cheaper to build, and using up a large part of the same residues, Ethanol plants might find themselves outpriced in time. Already , the OMC’s have shifted from trying to build massive 2G ethanol plants to 1G plants, which are much more low cost to build. 1G plants are optimised to use sugarcane residues better, while 2G plants can use cellulose and hemicelluloses. These are found in feedstocks such as wheat straw, corn, wood, agricultural residues and municipal solid waste. This extra flexibility comes at a much higher cost though. Oil firm officials inform us that the cost for a 1G plant are around Rs 120 crores for a 5000 litre per day capacity. As opposed to that, a 2G plant can cost over Rs 1000 crores to set up, distorting the reward-returns matric significantly.
Conclusion
We fund it worthwhile to highlight, and place on record the importance of these three initiatives, as a proxy for India’s progress on its climate goals. All three are linked deeply to sectors that are decisive to ensure India moves ahead. All three make their own case for support, and offer benefits that go beyond just cost savings, import substitution, or a cleaner environment. Interestingly, with Ethanol and CBG impact primarily on the transportation sector, they will eventually run by, possibly as early as 2035 or before, against another key transition into its early days here. The move to electric transportation. In the intervening period, that means their impact on fossil fuels will only accelerate with time, if they deliver on their promise.