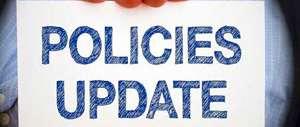
25 minute read
Modules
World’s Module Capacity to Grow in ’21; Southeast Asia 2nd Top Supplier
Up to 400 GW of nameplate solar module manufacturing capacity and nearly 325 GW of nameplate cell capacity could be online by the end of 2021, says a new report. Southeast Asia is the second top production location for cell and module suppliers, following China and Taiwan, which are at the top.
Advertisement
Clean Energy Associates (CEA), a leading solar and storage supply technical advisory, has released its Q2 PV Supplier Market Intelligence Program (SMIP) report for 2021, which includes insights gathered from interviews and analysis of many of the industry’s leading solar supply chain manufacturers.
According to the forecasts, sizable pipelines for new polysilicon expansions will continue to be built with over 1.2 million tons expected to be online by 2023. Although the majority of expansions (72%) are planned for outside of Xinjiang, China, the vast majority (89%) of global polysilicon production is still expected to take place within China. Non-Chinese-based polysilicon capacity is expected to exceed 130,000 tons by 2023 (11% of global capacity), with the majority located in Germany and the United States.
Most major Chinese polysilicon providers are looking at expansions exceeding 100,000 tons; only Daqo has not detailed a significant boost in new production capacity. Small expansions from incumbents such as OCI, Ordos, Youser and others are also underway, although these suppliers are eclipsed by the scale of major market players. Xinjiang Jingnuo, a new supplier, announced intentions to develop polysilicon production in Xinjiang this past quarter and will target 100,000 tons of production capacity if permits are approved by government bodies. 400 GW of Nameplate Solar Module Capacity Expected to Be Online by End of 2021
Through surveys with leading module suppliers, CEA believes that around 400 GW of total nameplate module manufacturing capacity and nearly 325 GW of nameplate cell capacity could be online by the end of 2021. China and Taiwan are expected to remain the top production locations, together accounting for over 85% of global cell manufacturing capacity and around 75% of global module manufacturing capacity. Southeast Asia is the second top production location for cell and module suppliers, holding around 9% and 13% of the global cell and module production capacities, respectively.
Despite this large production potential, wafer, cell, and module suppliers faced difficulties due to persistent shortages of polysilicon and a subsequent rise in its price. Furthermore, rising prices of steel, aluminum, and copper, along with surging freight charges further led to increased project costs, creating weak demand during the first half of 2021 for most markets. Even with these challenges, global supplies of both cells and modules are expected to expand throughout the forecast period. Large developers have already started construction on large manufacturing complexes and most maintain plans to bring new capacity online.
Strong Environmental Policies and Regulations in Conjunction With Ambitious Carbon-Neutrality Goals Makes Europe An Attractive Destination For Solar PV Cell And Module Manufacturers
Despite COVID-19 pandemic, demand for solar in the European Union region increased to 18.2 GW in 2020 from 16.2 GW in 2019. The region is revising several policies and regulations to achieve its carbon-neutrality goal by 2050 which is expected to offer strong advantages to solar and other renewable energy sources. Increasing focus on building a resilient domestic solar PV supply chain while reducing the reliance on Chinese imports is expected to attract suppliers to set up their facilities in this region.
However, Europe’s solar manufacturing ecosystem is currently limited by wafer and cell production which accounts for less than 20% of total module production. Wacker remains the sole producer of polysilicon in the region, with few ingots or wafer producers situated in Europe to buy its polysilicon outputs. The lack of cost-effective wafer and cell production is also increasing module imports from China.
With module production capacity around 25% of module demand in the European Union, most of all installed capacity in Europe can be traced back to China.
Although solar PV cell and module suppliers keep announcing new capacity expansion plans, with polysilicon suppliers still needing several quarters to bring new production online, and logistics challenges not expected to abate in 2021, solar projects in many key markets are at risk of being pushed to 2022 and module manufacturers may not reach desired shipment figures this year, says the report.
MNRE Releases Updated ALMM List With 3 New Additions
The Ministry of New and Renewable Energy (MNRE) has issued an updated list of approved manufacturers in its ALMM (Approved list of module manufacturers) list. The List is effective August 17, 2021, with the certifications valid to August 16, 2023, or two years. While broadly in line with the previous list, the fresh list has three new additions, in the form of Central Electronics Limited with a capacity of 35 MW, Patanjali Renewable Energy Private Limited for 70 MW, and finally, Jakson Engineers for 80 MW capacity. Interestingly, all the three new additions are based in and around Western Uttar Pradesh, in Greater Noida and Sahibabad respectively.
Power and MNRE Minister R.K. Singh has repeatedly gone on record to say that the ALMM list will be one of the tools to drive faster domestic manufacturing, as even foreign firms will be allowed in only if they set up domestic manufacturing. Overall domestic capacity available as per the new list is now at about 8350 MW spread over 26 manufacturers. With a large amount of capacity (around 7 GW by our estimates) coming up by March 2022, assuming quick certification for those, domestic capacity available post March next year, when the 40 % customs duty will kick in, could be close to 15GW, adequate to meet all domestic demand, but for the manufacturers who also service export markets. Of course, a significant proportion of legacy capacity is for multi crystalline modules, considered obsolete or close to it by many developers today.
How Adani Solar Is Gearing Up
For The Next Wave Of Growth
RE Manufacturing in India has a crucial role to play in achieving RE targets of 175 GW by 2022 and 450 GW by 2030.
Adani Solar being India’s largest integrated solar Cell & Module Manufacturer, is geared up to ensure the Energy Security of the country with planned expansion up to 3.5 GW of solar Cell & Module Manufacturing capacity from current 1.5 GW.
Adani Solar’s cutting-edge technology, scale of operations, cost leadership and reliability, sets up apart from all other global competitors and supporting utilities.
Let’s take an in-depth look at the technologies, behind the innovations of its recently announced High Efficiency ultrahigh-power modules designed for applications in small to utility-scale power plants with
• Power output up to 540W and 660W • 21%+ efficiency • SHINE Series - Module size of 2266×1135mm with 182mm Cell • PRIDE SERIES - Module size of 2390mm X 1303mm with 210mm cell.
Adani Solar’s R&D and Technology team has optimized the gallium-doped M10 standard silicon wafers (182mm) and G12 standard silicon wafers (210mm) that produce P-Type Mono PERC module with the lowest LID and LETID performances. It has also been proven that Galliumdoped silicon wafers shows lower LID performance with stable, long-term power generation as compared to borondoped ones.
Adani Solar’s Gallium-doped wafers are coupled with Non-Destructive cell cutting Technology that delivers superior performance.
With these gallium-doped cells, Adani Solar modules have increased annual generation performance, power performance and long-term reliability. The 1st year power warranty is an industry-leading 98% and linear annual degradation is within 0.45% after Year 1.
Adani Solar has also adopted a superior soldering technology on its modules that has increased the module conversion efficiency by 0.3%. This technology uses wires that maximize light capture and reliably connect cells with reduced gap distance. More importantly, soldering reduces the tensile stress of the cell and ensures higher reliability.
If we see the current trend in India’s Solar industry, many Indian manufacturers are still trying to migrate from Poly/ Multi manufacturing to Mono manufacturing, while our overseas contemporaries have already migrated to high efficiency Mono.
Adani Solar has already developed the infrastructure to manufacture the M10 (182mm) and G12 (210mm) design with high efficiency cells of 23% and above reaching power class bins of 540Wp and above, making it an early adopter in Global Solar technologies in India.
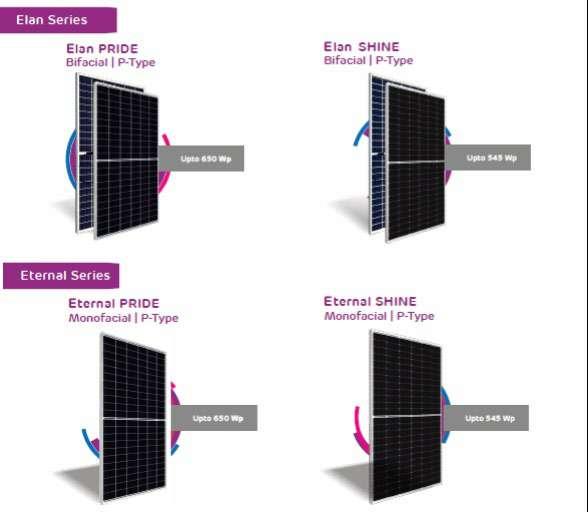
Product design based on industry insights and real-world applications
The initial point in the development of Adani Solar modules was well planned after extensive insights from the PV industry and analysis of customer inputs and voices globally. Adani Solar further considered real-world applications to come with its new – Elan Pride (Bifacial modules with G12 cells) & Elan Shine (Bifacial modules with M10 Cells) and Eternal Pride (Monofacial modules with G12 cells) & Eternal Shine (Monofacial module with M10 cells) modules in the logistics chain.
The new world class modules from Adani Solar save 4.1% on BOS cost, 20% on Labour, 5% on Land & Logistics and 3% on LCOE.
The working current of Adani Solar modules are as high as 13-17A, including the bifacial gain. The operating current
remains within the maximum input current range of the inverter, with no power generation losses. The module length is compatible with 1P and 2P horizontal single axis tracking systems.
Adani Solar modules come with “Double glass with frame" design that provides exceptional strength for high load capacity. The strength of the frame negates the need for a crossbeam, hence no shading losses at the back of the module.
In terms of BOS simulations using fixed brackets and centralized inverters, Adani Solar modules can reduce BOS costs by more than (US$1.5 cents/W) when compared to mainstream products in the market.
With string inverters, Adani Solar modules can improve the capacity ratio of the power plant, reduce AC equipment cost, and bring about the lowest LCOE for large power plants.
Adani Solar is partnering with more than 20 global customers to verify the BOS savings, lowest LCOE and high performance of its Elan (Bifacial)/ Eternal (Monofacial) modules in real world applications.
Driving the Solar PV industry forward with breakthrough innovation in volume production
Adani Solar firmly believes in continuous innovations that can be quickly brought into volume production delivering true value for its partners and customers.
The module production capacity of Adani Solar is expanding from 1.5 GW to 3.5 GW in 2021. Elan (Bifacial) and Eternal (MonoFacial) series will be produced in volume and receive IEC/UL certification shortly in the next few months during 2021. The Company is also planning to expand its manufacturing capacity to up to 6 GW in 2023-2024.
Adani Solar Product Portfolio Presenting
Adani Solar‘s Elan and Eternal range includes 66C and 72C formats, in bifacial and monofacial applications. The 72C (M10) version deploys the traditional 6 rows design in a 72-cell layout with frontside power up to 540W, which is the optimal choice for the ultra-large power plants worldwide. The 66C (G12) module has front power of 660W and a smaller footprint that broaden its applications.
Currently, Adani Solar’s Elan Pride & Shine (Bifacial Modules) and Eternal Pride & Shine (Monofacial modules), launching in 2021, will continue to enhance its product portfolio and are the most competitive products suited for residential, C&I and utility-scale power plants.
About Adani Solar
Adani Solar continues to lead the Indian solar PV manufacturing industry to new heights with product innovations and optimized power-cost ratio with breakthrough High Efficiency monocrystalline technologies. Adani Solar leads the Indian solar cell and module manufacturing industry by producing the highest cell efficiencies and highest module power bins produced & made from India. Do visit the website at www.adanisolar.com to know more about the company and their products.
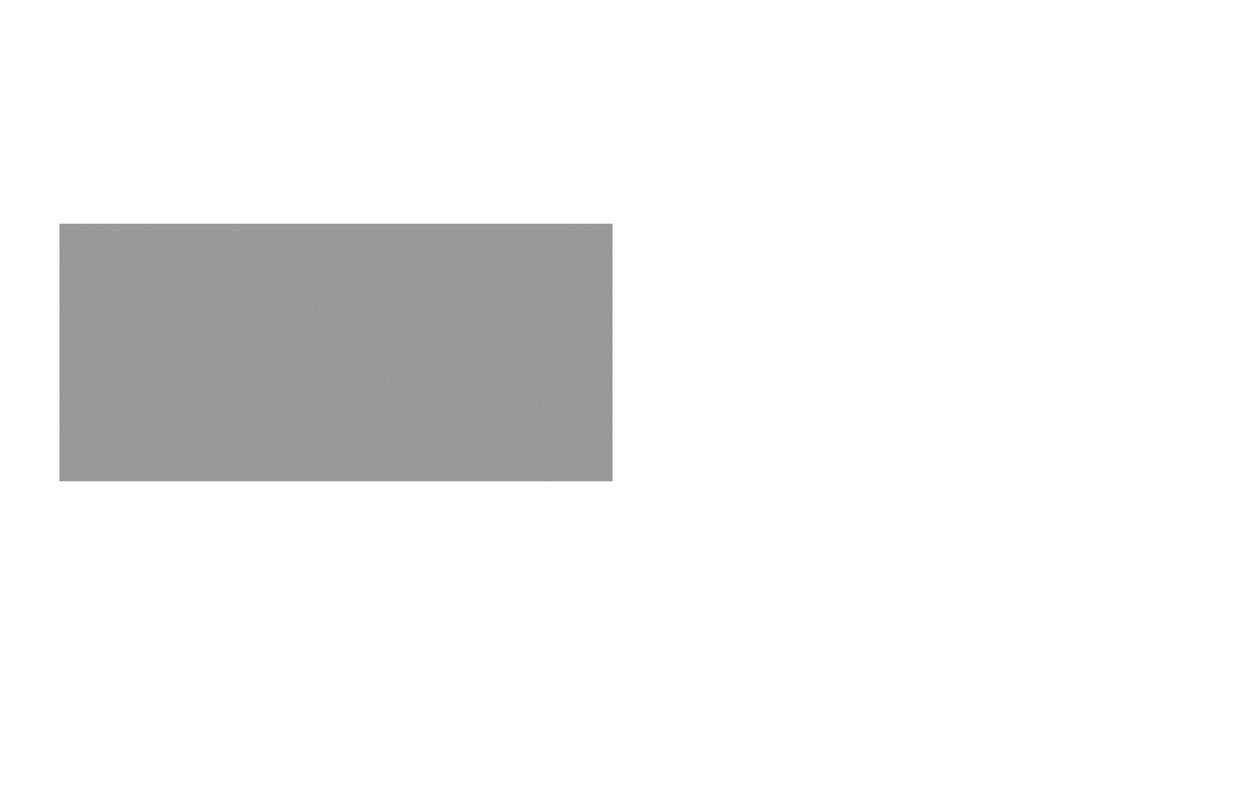
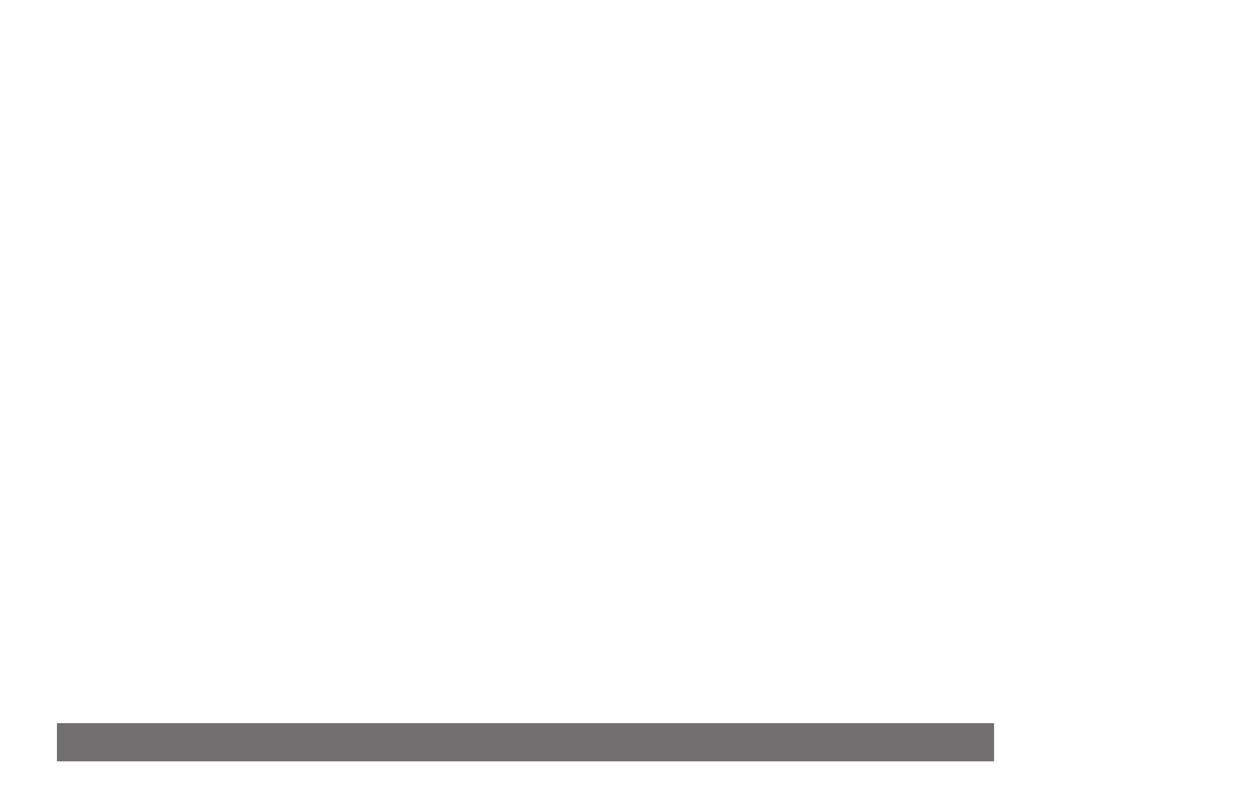
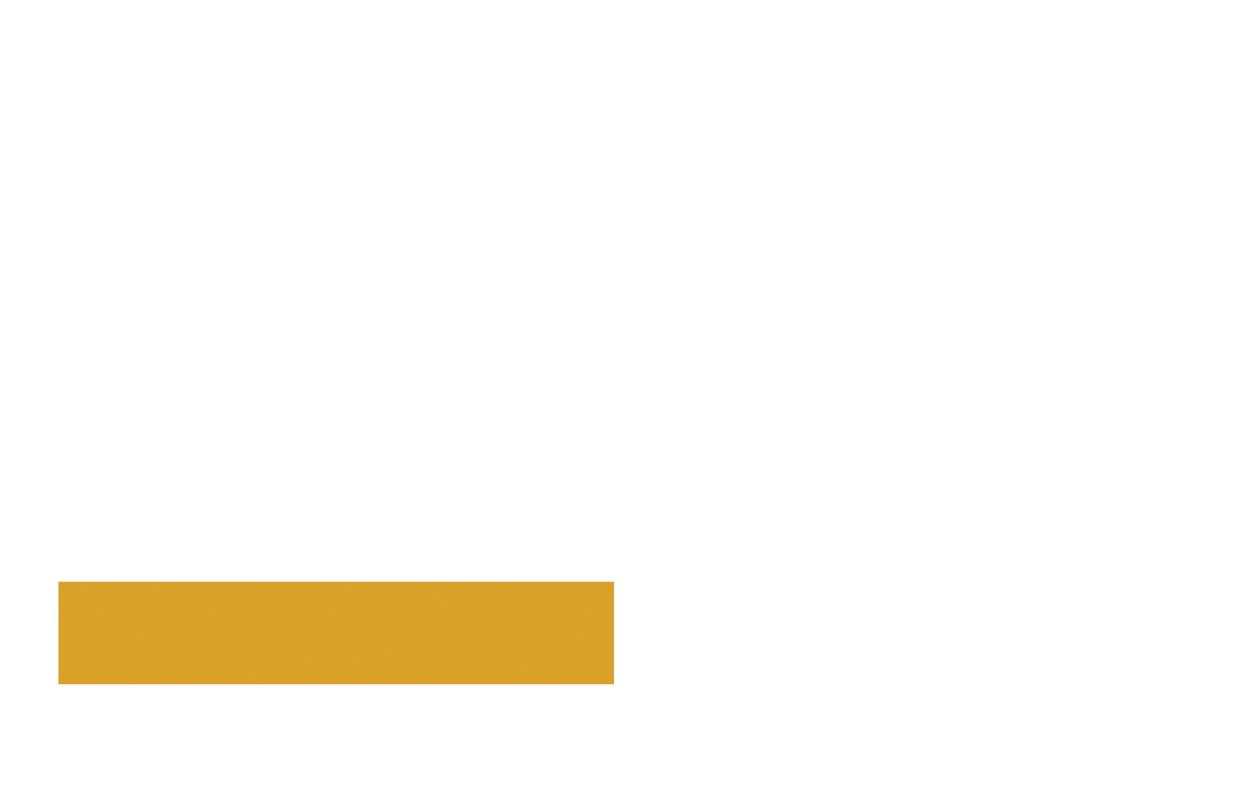
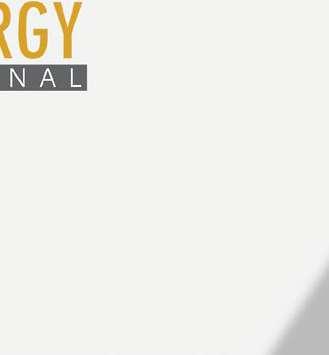
Fill Solar Jobs
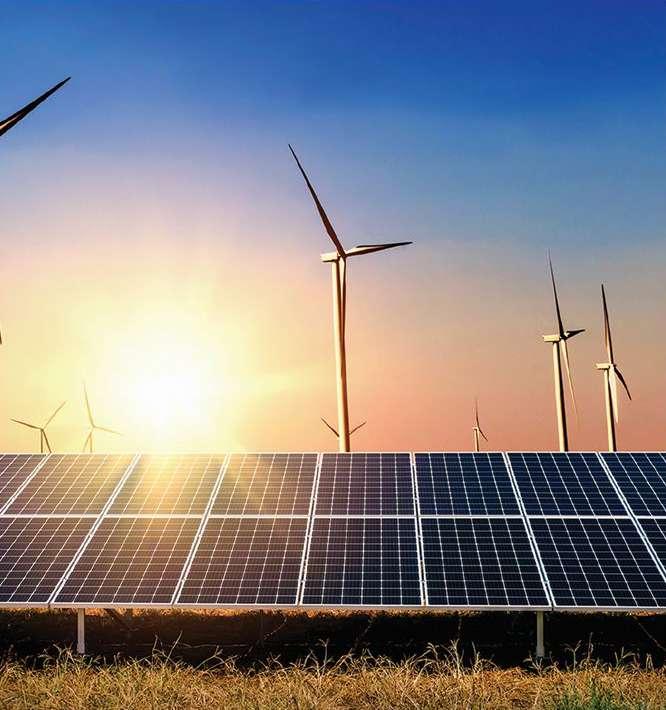
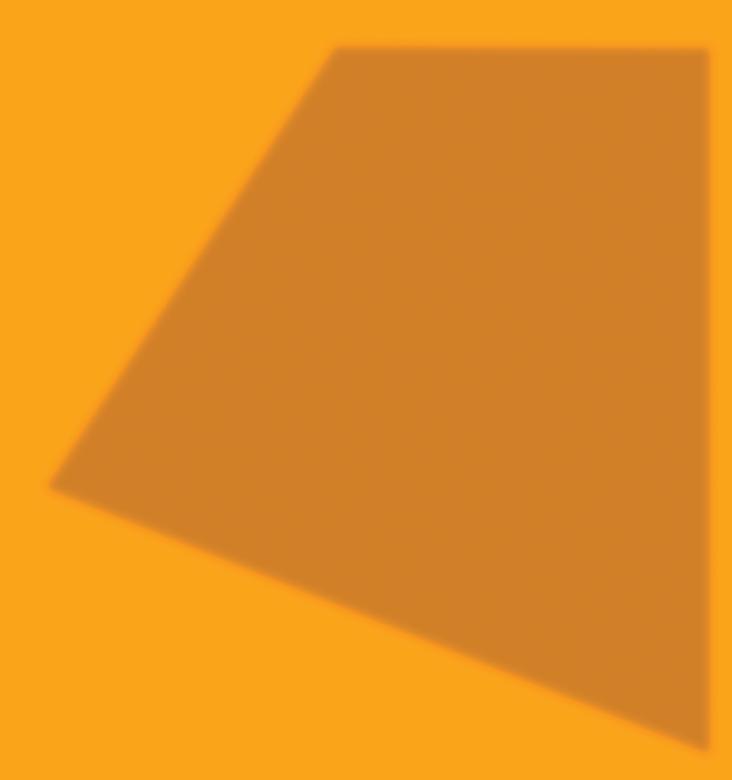
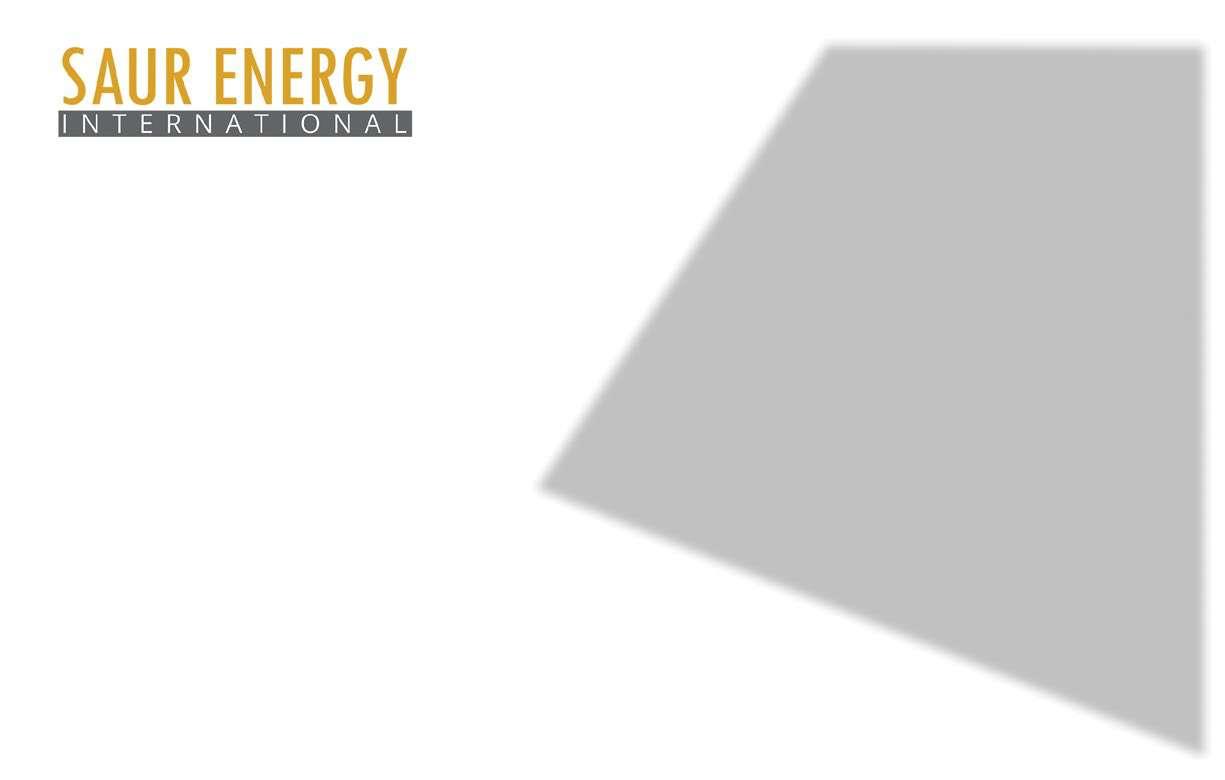
Advertise with the most read solar magazine in India.
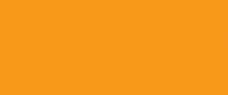
Hydrogen is not the optimum option for fuel
storage in India because of costs, safety issues.
Bengaluru-based Log 9 Materials shot into the limelight (again) recently after Amara Raja batteries, a leader in the domestic automotive battery market, invested in the firm. Log 9 Materials is using its core competence in Graphene nanotechnology to develop advanced energy storage technologies from electrode materials, cell to pack level. Their rapid charging battery packs solve the challenges in adoption for the 2W and 3W electric vehicle platforms while their Aluminium Fuel Cell technology research is targeted towards the electrification of long haul, heavier vehicles. Log9 has successfully collaborated with major companies in the last mile B2B intracity delivert sector like Amazon, Shadowfax, Delhivery, Porter, Vogo, EBikeGo, ITC, Zoom Cars, etc for its battery pack solutions .Group Editor Prasanna Singh caught up with Akshay Singhal, Founder and CEO, for a chat on the firm’s plans and hopes going forward.
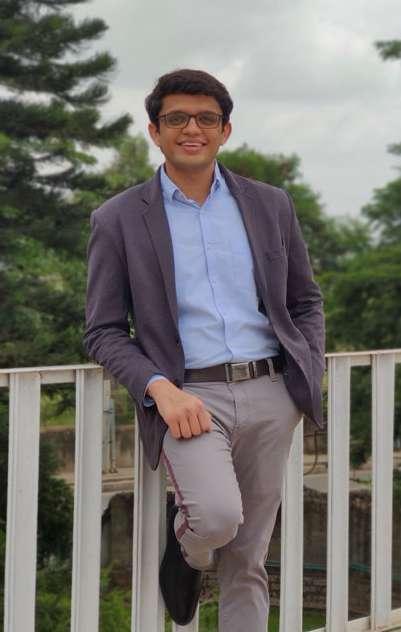
DR. AKSHAY SINGHAL
Founder, Log 9 Materials
Prasanna. Let’s start with the Log 9 in the company name. Where did that come from? Akshay: So, because we primarily are a material science company and in that we are dealing with nano materials like graphene and carbon nano materials. So nano is 10 to the power minus nine meters (One billionth of a metre). So that's the reference from logarithmic 9, log nine.
Now of course we see log9 materials in many areas, right from rapid charging to the oil spill products, battery... Akshay: Yeah. The enabler for all of the different products and technologies that there are in the market from log 9 is basically nanotechnology. So the competency of log 9 around nanotechnology and nano materials is what helps us build these revolutionary products and put them in the market.
Which one of your products has you most excited for the future? Akshay: So although the focus of the company is towards batteries and electric vehicles, it’s purely from a battery perspective. That's the focus of the company. We did have a lot of other products like you spoke about. Those are more of our side development and side technology that we have come up with over time, the focus and excitement remains around energy storage itself.
Okay. So when you say energy storage, we are talking about the aluminium battery? Akshay: So we are talking about two technologies here. One is the aluminium fuel cell, or as you call it aluminium air battery, that is one aspect technology and the other one, being our rapid charging battery packs. So, these are two distinct technologies: aluminium fuel cell is a refilling concept, which consumes aluminium as a fuel and provides energy and that technology is targeted more towards your long-haul vehicles, whereas a rapid charging battery
technology is a charge-discharge-based technology like any other lithium-ion technology, but provides you benefits of very rapid charging time and at the same time, very long life and very high performance vehicles .So this technology is targeted towards the intra-city segment: two-wheeler, three-wheeler, four-wheeler for the intra-city commercial fleet applications. So that's how we are kind of positioning these two technologies in the market.
And what are the plans in terms of taking these technologies to market? How far would they progress over the next two years? Akshay: So rapid-charge is already in the market. We have already, done a lot of the successful pilots with various last-mile fleet operators. We also have made announcements with OEM partners for launching the vehicles in the market. We have received ARAI certifications on our battery packs and the commercial rollout, wherein we’ll start deploying on a regular basis is due for October this year.
You were in the news recently for the investment from Amara Raja batteries. Amara Raja is of course among the leaders in the lead acid battery segment. How do they see your segment? Akshay: If you look at the way our organization is structured, we are very good at innovating new kinds of products and technologies. And the idea is that whatever we are able to make that has a product market fit, post that Amara Raja’s experience and resources can help us scale up. Setting up large-scale manufacturing, last scale distribution.
One of the key things that you stressed on is the fact that whether it is the aluminium cell battery or any other product right now, it's all about the circular economy for you, you know, it's completely recyclable. Even lead asset battery firms stress on how lead is completely recyclable and lead recycle rates are almost 85-90% worldwide. That, combined with the extremely lower cost of lead acid batteries, how will that play out in a market like India? Akshay: So that is not going to play out well in the future because lead acid batteries and the technology is obsolete now in that sense. In terms of battery technology, when it comes to your total energy that can be stored per kg of battery pack, which is what we call as energy density. At the same time, the cycle lives are far higher now, even with the worst of lithium-ion as compared to your lead acid battery. So from that perspective, although the upfront cost definitely is higher, but your cost per unit of electricity stored or cost per unit time the battery is being used for is far, far lower in the advanced technologies. And also a lot of times we have a tendency, at least in India, to kind of ignore the maintenance costs and the replacement hassles associated with any technology or product. But market is now changing with more structuring happening across use cases when it comes to vehicles and otherwise, and people are doing these calculations, especially your fleet operators, commercial users which is because every penny is important when it comes to per kilometre cost. So from that perspective, lead acid doesn't play out at all in mobility long term or even in case of stationary backup.
We have seen how you shared the challenge of convincing people about your own Aluminium fuel cell battery. How have you managed to get investors to buy in finally? Akshay: So the thing is that where aluminium fuel cell as a concept, plugs in is when basically positioned for long-haul mobility. And the reason I say that is because with any kind of battery technology where you're charging and discharging, you can't really go for a thousand kilometres or fifteen hundred kilometres at a stretch, right? And in many cases, if you do the math, it turns out that if you actually build a vehicle with a thousand kilometre range, then you will only be carrying the battery and not load in the vehicle. And that's the reason why even the government has pushed for using some kind of a fuel cell for long haul mobility. The hydrogen mission and all of those kinds of things. We are saying that hydrogen is an option, but we don't think hydrogen is an option for the Indian economy. Because the upfront cost is very high. At the same time, there are a lot of safety risks associated with it, especially when it comes to the Indian conditions, because hydrogen requires pressurized tanks. It is very explosive and all of those challenges are there. So that is one side of the story. In case of Aluminium, it is basically a solid fuel, so you don't need any kind of infrastructure to store it. You can take a warehouse throw aluminium inside it and it will be there as long as you want it. Right? So, that is easier distribution for the fuel itself. At the same time, the upfront cost is definitely far cheaper than hydrogen and all the materials, components required for making aluminium fuel cells are available within the country. Moving on to our rapid charging battery pack that we are putting forward we are able to offer not only very, very rapid charging. So your fleet can run for a longer time on the road than waiting for the vehicle to be charged. But at the same time, again, safety is a very big parameter over there. So irrespective of temperature, whether you're running it in Bangalore or whether you're running it in the peak heat of Delhi, or even Siachen, there is no impact on battery performance or there is no risk of any kind of catastrophic failure in the battery pack. You would've already heard of even Tesla’s battery packs catching fire and all of those things. We are coming up with a bunch of safety-related videos around our
battery packs, where if you do any kind of accidental damage to the pack, or even throw it in an open flame, nothing is going to happen unlike the other batteries which are out there.
So how do we make aluminium fuel cells green like Green Hydrogen is being discussed? After the battery has converted, it has to be reprocessed back to aluminium, right? Akshay: In the case of aluminium fuel cell the aluminium hydroxide that is generated now, that can be converted back into aluminium metal using green energy. And if you look at it, it can be far more efficient because right now, the reason we have these aluminium smelters located where they are is because the mines are closer to that place. So it's the mines that are defining where the smelter will come up. But when you have vehicles running on this and producing what the mine is giving you- so aluminium hydroxide is what will come from the mine first from smelting, right? It's the same thing, which you get out of the aluminium fuel cell as well. In that perspective, there can be decentralized smaller smelters in every, district or every state to start with. And then you can kind of power it up with a solar installation or the wind installation in that. And that's similar to your hydrogen economy concept of using renewable energy to split water and create hydrogen. So it's the same concept.
But what about use cases in large scale storage? Is there a possibility there? Akshay: Coming to another aspect of solving intermittency in the solar and wind site is from our rapid charging-based solution. So what we are putting as the rapid battery charging solution in the market, the same technology can be used as a power backup or a storage battery pack also on the grid. And when you do that, what happens is because in case of lithiumion also typically you will look at a life of two to three years’ time because that's when you'll be able to use up the entire cycle of the battery packs. Whereas in our case the battery life would be at least 15 years and potentially up to 30 years. So from that perspective, if you look at our RTC (Round the clock) solar project today, right? What happens here is that your battery cost, the cost of storage alone is around five rupees(per kWh)). Whereas cost of generation would be somewhere around two rupees but two plus five becomes seven rupees, which is not viable, right? Whereas in our case, you will have the cost of storage at only two, or around two and a half rupees. So, club that with the cost of generation, which is two rupees, and you have RTC at a much lower cost. And that is very valuable because then you can sell round-the-clock power at six rupees, seven rupees in the market. That is something which we are already coming up with. We will have a pilot plant also combined with solar sometime early next year.
SO in your case for the aluminium fuel cell, once the aluminium is oxidised, we swap the battery? Akshay: Well, you don't swap the entire battery, just refuel it. So basically instead of just putting in liquid fuel that I could do today in your vehicle, you're basically putting a solid plate fuel.
So in your case, you would have to set up enough centres to replace those? Akshay: Yes. Even existing fuel stations could be used. In this case, all you need is the physical space to kind of store aluminium plates, then manually you can put in a new plate set and just remove the previous one.
Okay. And what, when you raised this money from investors, what is the big promise there? The aluminium fuel cell or the rapid charging battery pack ? Akshay: Both. The idea is to indigenize more and more on the rapid charging side. We are possibly the first company, which has cell level competency, local cell-level technology and competency to produce sales at the local level in India right now. And the idea is that within 24 months, we will set up a commercial cell level production line on our high power lithium sets which are going in the rapid charging battery pack. Okay. At the same time, the aluminium fuel cell is something which will be optimized over that two, two to threeyear period, before launch in the market.
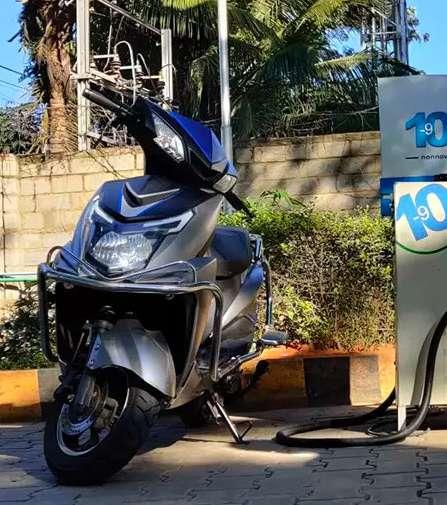
What do you think of Tesla? Do you think they offer lessons for firms here Akshay: Tesla is a great example of a firm that that has disrupted massively, even as incumbents kept ignoring it. Our own auto makers need to take lessons from that, or risk becoming redundant in time. People must set aside their ego and consider the changes that are happening. In EV’s today, you have Chinese firms dominating the market, firms that barely existed a decade ago. Simply because many of the erstwhile leaders refused to change in time.
Going aside for a moment, tell us about the Corona oven. You had some commercial success there I believe. Akshay: So that was a great thing that we were able to contribute towards the pandemic. And I'm happy that instead of just sitting on our hands at home during the first year of the pandemic, we were able to deliver that product and launch it in the market. Kudos to the team for being able to do it in flat 15days time from idea to the first shipment going out. Definitely we had a lot of sales happening last year. This year, the retail sales have definitely gone down. This project is now emerging as a more B2B product wherein, seeing a lot of interest in this product for general sanitization needs of your first responders like hospitals, ICUs, Police etc. We are even sending these to other countries now.
So do you have separate team to market the corona over? Akshay: No, we don't have a separate team, particularly for Corona oven. We are looking for partners who can acquire this technology and take it forward. We have set up partnerships in place. We have distributors, and this is more global in that sense right now.
Among all the battery chemistry’s/ technologies that are around right now, which ones do you feel have been really innovative and have high potential? Akshay: So the thing is that one of the key things that we missed out generally, and I've seen this across the ecosystem itself is a quest to find the ultimate battery technology, which is never going to happen. There cannot be a one-size-fits-all solution, which will suffice your stationary needs, your mobility needs. And in mobility also all sort of different kind of vehicle requirements and use cases. So there will be a play of four, five technologies that the market will consolidate. Some technologies have their very niche play, be it long haul for aluminium fuel cells, or very short hauls for some others.
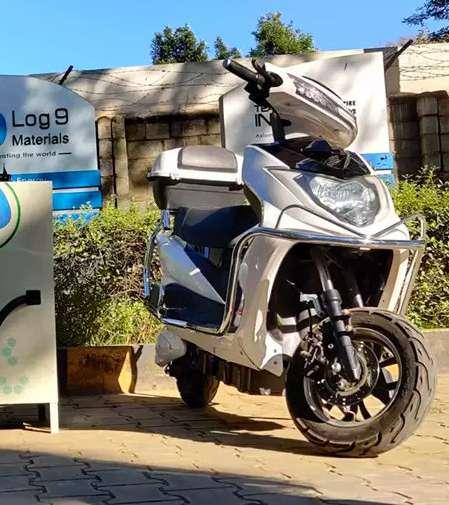
Could you give me a benchmark price right now that, where you expect this to be on a per, per kilowatt basis, aluminium fuel cells? Akshay: So if you do a kilowatt hour kind of an equivalent, then on a kilowatt/hour basis purely, it'll come up to be around $17, $20 per kilowatt hour.
How has being in Bengaluru helped you? Akshay: Bangalore had made a difference to us in many ways, not just one at a business level, but personal level too. One of the things, like slightly on a side note, I think the problem with places like Delhi and Bombay, especially Delhi and the North is that half of the year we are cribbing about the heat. And half of the year we are cribbing about the cold. Whereas if you have a climate like Bangalore’s, then you are more peaceful and then you can focus on your work. I think that that has been a very wonderful experience. And that's why I always like the city when I used to visit Bangalore before, even before moving here Also, if you look at the traditional R&D centres of hardcore technologies, many R&D centres are in Bangalore. For example, you have AstraZeneca here, you have ISRO here, you have IIS, which is already there. The DRDO has an R&D centre here. So all of these new age technology development centres have been in Bangalore. And when you have these centres here, you also get the talent pool, which is basically popping up in this city. At the same time, you also get a lot of support-structure because, because these centres are there, there will be a lot of vendors who are supplying stuff to these centres, and hence you can tap into that entire ecosystem. So that has been very beneficial for Log 9, because when we were developing our tech, and when we are doing prototyping and all of it, so vendors, talent, pool, everything was available in the city, and we didn't have to kind of go to Mumbai or go to Chennai or whatever.