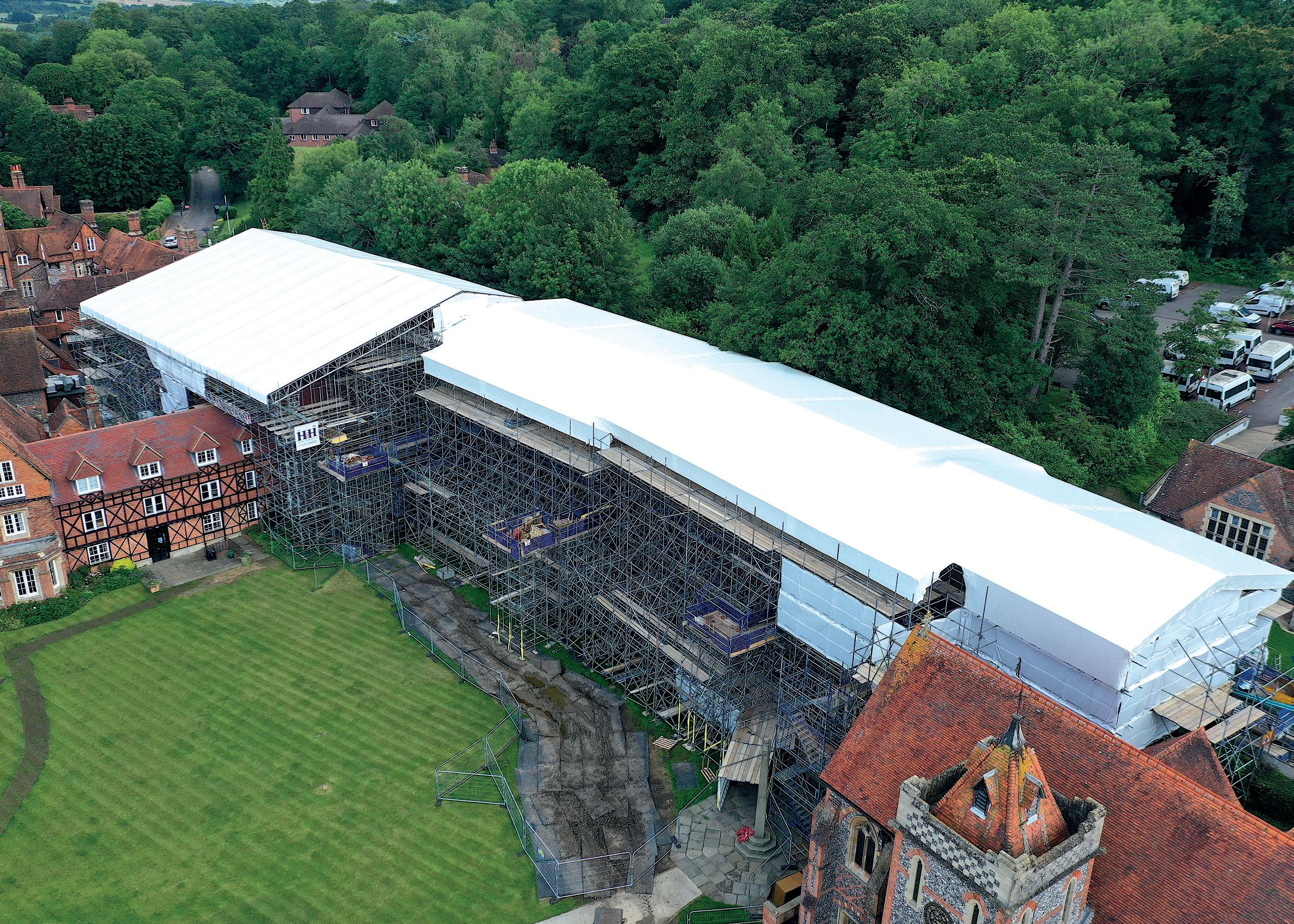
5 minute read
SOUND SYSTEM
from Scaffmag Issue 14
by ScaffMag
For decades system scaffold has been seen as having its place in the market – fine for prestige jobs but ‘too expensive’ to be considered by the majority of scaffold companies. Proponents of system scaffold have banged on about the ‘hidden costs’ associated with tube and fittings and the safety advantages of system scaffold, but these arguments were diluted by the ready supply of labour and a largely buoyant sector that removed the need for creative solutions. Then Covid struck and at a stroke the arguments for system scaffold became even more persuasive
March 2020: The month the world stopped.
Advertisement
No one can say with any degree of honesty that when that first lockdown was announced they could accurately predict the future. We were almost at year zero.
Then, gradually, with a slow return to normality, a pattern began to emerge. Nationally we saw a shift in the pattern of demand. The construction sector recovered quickly, but the forces that drove that recovery reshaped the type of projects that were undertaken: increased government funding was driving growth in the education, health and civil engineering sectors; housebuilders would enter a race to complete mothballed sites and take advantage of the demand created in part by the reduction in stamp duty, while the seismic change in shopping habits would mean that there would be a need for new warehouse and logistics facilities while existing retail units would end up being repurposed.
We also noticed that, nationally, there was a marked geographical shift in levels of activity. Some areas that were buoyant pre-pandemic were slower to recover, while other areas saw exponential growth.
At a site level, things had changed, too. On-site working restrictions to contain Covid-19 transmission rates (ie the continued need for social distancing on site), the need to reduce costs to help companies recover from the lockdown, the shortage of labour for some trades – including scaffolders – and the increased costs of materials, forced companies to take a long, hard look at the way they did things.
The pattern of recovery was also reflected in the projects that UKSSH was involved in.
MARKET LEADING PRODUCTS.
The benefits of the HAKI Bridge System and Public Access Staircases were well documented long before Covid hit. Time and time again, projects were returning remarkable comparisons. The HAKI Bridge System is quicker to erect – reducing man hours by an incredible 90% compared to the tube-and-fittings alternative, there are fewer components (reducing transport costs by 50%) and the completed bridge is 60% lighter than one constructed in tube and fittings.
Given the government’s investment in infrastructure projects to kick-start the economy, it was no surprise that the HAKI Bridge System and Public Access Staircases were the first products to leave the yard once the UK started getting back to work.
CUTTING COSTS FOR HOUSEBUILDERS
However, it wasn’t long before other products became the focus of attention, too.
Faced with fewer workers on site, yet with increased demand, housebuilders suddenly appreciated the benefits of systemised loading towers. The fact that a single lift in system scaffold takes 15 minutes to erect, compared to 90 minutes in tube and fittings (not surprising when you realise that a single lift in tube and fittings requires 144 fittings while in system scaffold it requires none at all) meant that a ubiquitous structure that had been taken for granted for years, suddenly became an area where significant cost and time savings could be achieved.
Safety and site-management benefits also came into play – loading towers are a designed scaffold and must be erected in accordance with a TG20 drawing, UKSSH’s loading towers are a generic design, fully systemised and can only be erected correctly.
YARD MANAGEMENT – A VITAL ROLE IN CONTROLLING COSTS.
At UKSSH we also realised our role in helping customers achieve social distancing, cutting costs and reducing the number of scaffolders on site. Late in 2020 we opened a new distribution hub to ensure that we could efficiently cope with increased demand.
Because the HAKI system is based around a 3m ledger beam it automatically means that scaffolders operate beyond minimum social distancing requirements. That resulted in an increased demand from scaffold companies involved in large construction projects particularly in the education and logistics sectors.
LEFT: Temporary roof at Bradfield College in partnership with H and H Contract Scaffolding. BELOW: Temporary buildings for Covid testing provided more business opportunities.
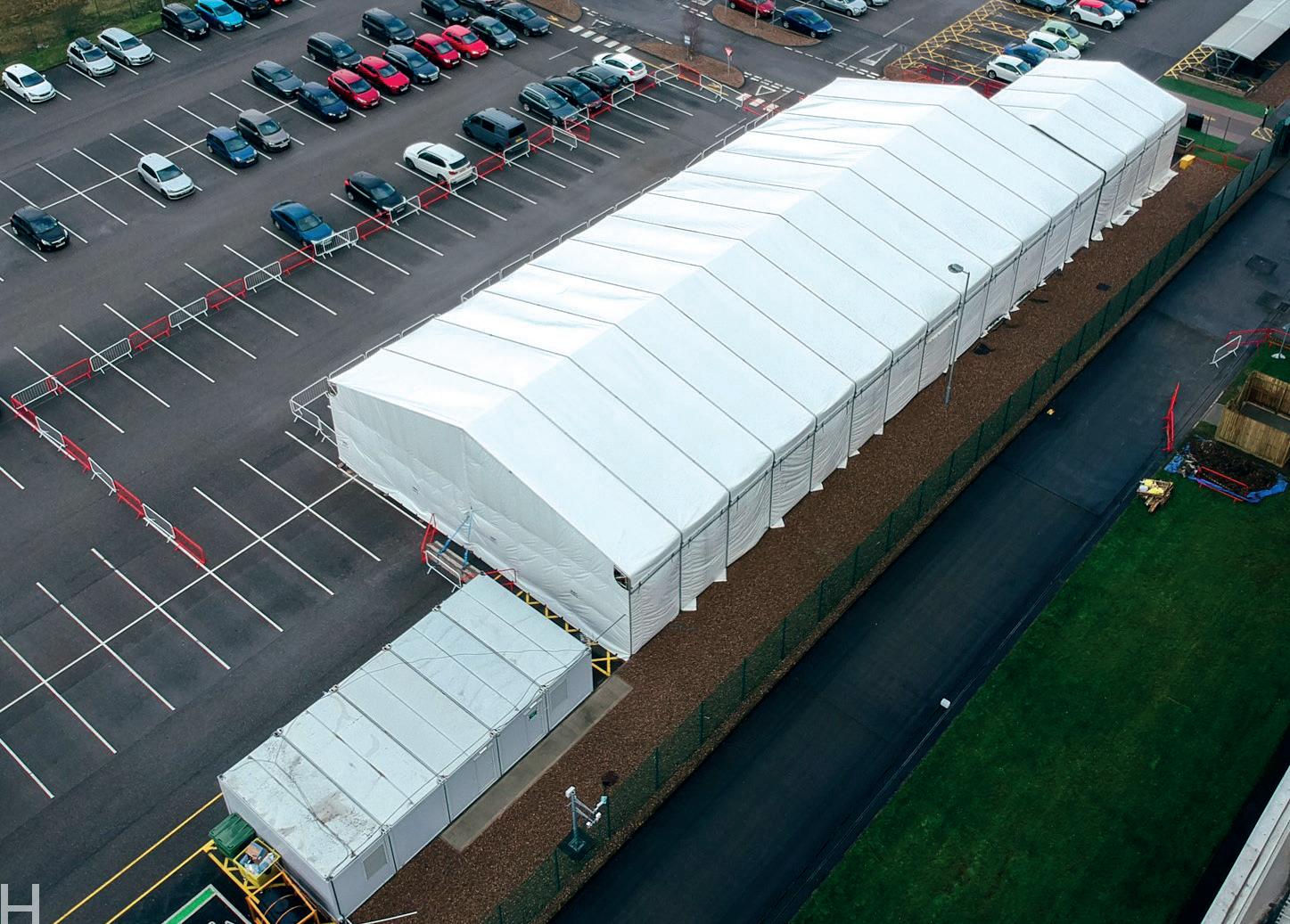
However, we have long realised that it isn’t just the products that deliver the benefits – equally important is the way those products are delivered to site. By being proactive with delivery schedules, our own distribution hubs are pivotal in enabling customers to optimise their labour on site.
It is more critical than ever to schedule component deliveries in accordance with the build programme rather than by the lorry load and to ensure that when the components do arrive on site they are in good working order.
Accurate deliveries means that the process of getting materials to the correct location on site requires fewer operatives.
As scaffold contractors, the greatest cost on any job is the wage bill for skilled scaffolders – and the greatest drain on profits is the amount of down-time when highly trained scaffolders are waiting for the right materials to be delivered. At a time when labour is at a premium and material costs are rocketing, attention to detail is the key to optimising profitability.
TRY BEFORE YOU BUY
The final piece of the jigsaw is flexibility. The majority of the projects in which we are involved are a combination of sales and hire. It’s an approach that not only means customers can supplement their own stocks (often resulting in projects being a combination of system scaffold and tube and fittings), but also means that customers can trial a ‘system solution’ on a hire basis and then choose to buy the equipment if that proves to be the most cost-effective solution.
BELOW: TR Scaffolding’s work on M4’s Bray Bridge infrastructure projects have been key to the sectors recovery.
