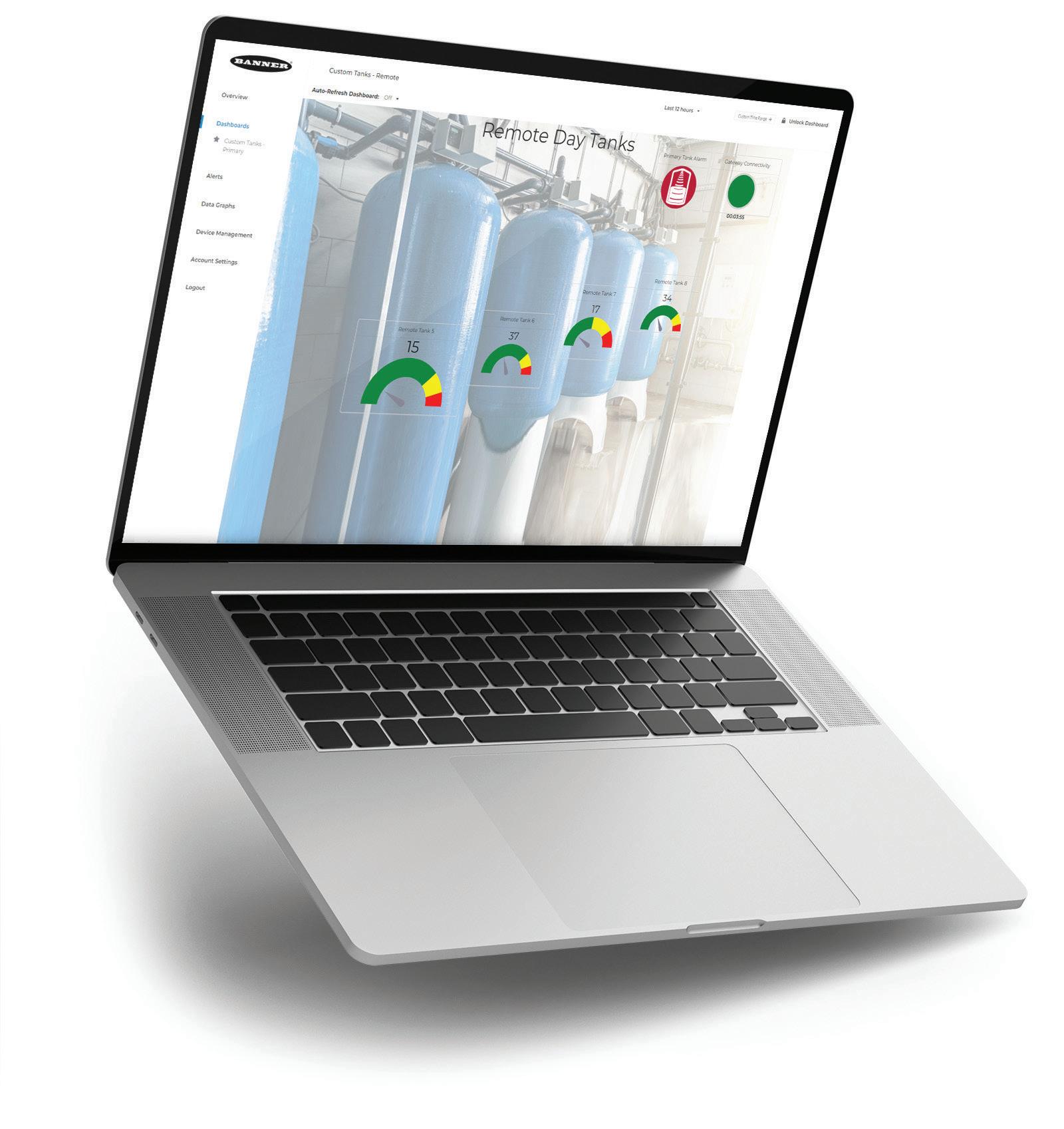
5 minute read
automation SMARTER
other products for customers worldwide provides the strong foundation on which Banner’s IIoT portfolio has been built.
Data-driven decision making
Smart automation goes far beyond sensors recognizing objects on a conveyor belt and turning on a light to tell an operator a part is not where it needs to be. Smart automation means taking data from the sensor and turning it into information that is useful far beyond the narrow scope of part presence. This information can be used to help users make critical decisions, such as when to order materials, employee, production, and maintenance scheduling, determining if and when production lines need upgrades, and more.
For example, a metal-stamping operation with limited data intelligence capabilities can be transformed to collect and interpret previously inaccessible information to understand machine availability, performance, and quality, which are the essentials of OEE. Quality and performance can be monitored by photoelectric sensors counting good parts exiting the press, and pressure measurements from the press’ nitrogen cushions can be analyzed to correlate low pressures with a reduction in quality. Machine availability is easily monitored via current-monitoring sensors installed on the motor power cables.
Current-monitoring data also creates the ability to track energy usage on equipment. By combining the current measurement with the supply voltage and monitoring this result over time, plant managers can more accurately understand the costs of running their equipment. Not only can this data show which equipment is the most cost effective to operate, but also it can inform future equipment decisions via comparing the costs of maintaining and running existing equipment versus the costs of new equipment that uses less energy.
Data predicts maintenance needs
Traditionally, large manufacturers would have a vibration expert analyze motors and bearings on a monthly or quarterly basis, tracking readings and trying to proactively correct issues before failures occur. Other companies conduct maintenance at scheduled intervals or replace equipment when it fails. However, rich sensor data can be used for predictive maintenance: recognizing when maintenance is needed and proactively addressing issues before equipment breaks down.
Another example is using data to improve the efficiency and uptime of compressed air systems. By adding vibration, temperature, and current sensors to the compressor motor, along with pressure sensors downstream, data may be analyzed over time to track trends. If sensors recognize a motor temperature starting an abnormal rise, a technician can be dispatched to the compressor immediately to check on it. Or, if the motor begins to run more often and system pressure varies too much, it may be a sign of an air leak. Technicians can track down the problem immediately and avoid excess energy consumption and expense.
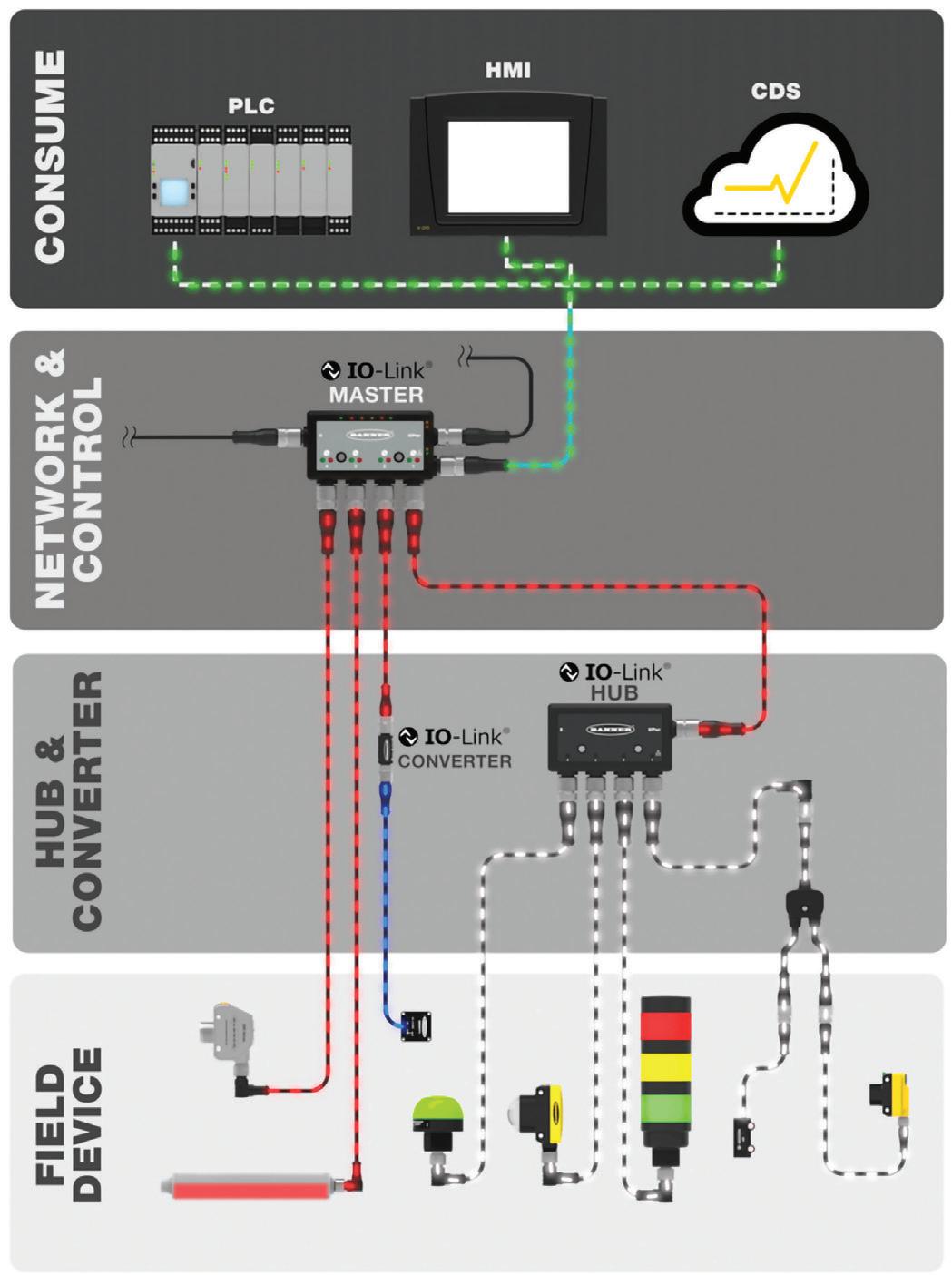
Access from anywhere
Using a cloud platform, such as Banner Cloud Data Services (CDS), sensor data can be stored and visualized remotely via intuitive on-screen dashboards. Individual alerts can also be sent via email or text that instantly notify operators of any changes detected. Remote system monitoring is one of the greatest benefits of smart automation. Depending on need, complete end-toend IIoT solutions deliver data via wired Ethernet connections, wirelessly via cellular connectivity, and through cloud services to reach necessary personnel wherever they are. Production and maintenance decisions can be made based on real-time information, even if users aren’t physically present with the equipment. This is especially useful for improving risk management in hard-toaccess or potentially hazardous areas, such as remotely monitoring long pipelines for leaks or tracking proper placement of items conveyed through dark and dirty locations.
IO-Link standardizes device communication
To make smart automation a reality, Banner offers a large selection of devices that incorporate IO-Link, an industry-standard communications protocol. This protocol allows devices and software from different manufacturers to easily communicate and share data, enabling seamless interoperability across industrial networks. Because Banner’s IO-Link devices also send discrete signals, they can use standard unshielded 3-pin M12 cables. These readily available cordsets are cost-effective and install quickly, varying only by length. Standardized cabling also eliminates wiring and pinout errors and reduces installation time.
IO-Link devices are designed for simple device replacement without requiring extensive technical knowledge. With Data Storage mode, sensor device configuration can be saved on a port of the IO-Link master. If a sensor is damaged, even an untrained operator can quickly swap the damaged sensor with a new one. The correct device configuration is loaded automatically, and the new sensor is ready to go. No manuals, configuration documentation, or firmware updates are needed.
Another cost-reduction tactic made possible by IO-Link technology is to replace passive junction blocks with stackable space-saving IO-Link hubs. This method simplifies connections by sending IO-Link signals back to one industrial controller, which aggregates and outputs all signals via a single Ethernet connection to a control cabinet. It reduces wiring, cost, installation and troubleshooting time, complexity, and allows for a smaller control cabinet. Hundreds of individual cable runs to a control cabinet can be replaced with six Ethernet cables.
For those users with non-IO-Link devices, legacy hardware can be connected to IO-Link masters using Banner IO-Link converters. These converters change various types of signals to IO-Link, giving operators access to sensor-level data without having to completely retrofit expensive and complicated machinery.
Unlocking potential with Snap Signal®
At the heart of Banner’s IIoT portfolio is Snap Signal, a suite of modular hardware and software that delivers actionable machine data. Data signals are captured from virtually any new or existing source, regardless of manufacturer, and converted to an industry-standard protocol. The data is then distributed locally, on a company network, or to the cloud for easy consumption. This enables and simplifies the complex task of data collection, analysis, and visualization. With Snap Signal’s ability to incorporate nearly any sensor signal found on a factory floor, Banner can build I/O systems that fully make use of rich data from both new and legacy equipment.
To accomplish this, Snap Signal taps into a device’s data stream, whether discrete, analog, or another type of signal. Even if device types are typically incompatible with each other, converters take their data streams and change them to matching industrial standards; think IO-Link or Modbus. By converting disparate signals to a unified standard, legacy sensors can be easily incorporated, and data can be seamlessly transmitted across multiple IIoT ecosystems.
Snap Signal combines performance data with predictive information. For example, a radar sensor that is monitoring the volume of liquid in a tank can display this level via an indicator light bar on the side of the vessel. When the tank level gets low, a connected controller can set the entire indicator to flash and notify an operator or send a text message to operators elsewhere that the tank needs to be filled to avoid disrupting production. A temperature and humidity sensor can be tied into the same system to monitor a nearby enclosure to ensure it does not overheat and cause the PLC or other electronics to fail. Indicators, sensors, connectivity, and logic can all be used together to enhance efficiency and reduce downtime.
Processing on the edge
The intelligence that drives smart automation systems is found in Banner’s DXMR90 series of controllers. These compact, programmable devices consolidate signals from multiple connections, process data, and provide a gateway to the IIoT. Built-in logic controllers provide local processing of action rules and scripts for data analytics, condition monitoring, predictive maintenance, OEE analysis, diagnostics, and overall troubleshooting. With these forward-thinking solutions, Banner is empowering smarter automation and delivering the promise of IIoT to companies of all sizes around the world. ■ www.bannerengineering.com

Banner Engineering is a US-based designer and manufacturer of innovative and industrial automation products, including sensors, smart IIoT and industrial wireless technologies, LED lights and indicators, measurement devices, machine safety equipment, as well as barcode scanners and machine vision. Since 1966, Banner has been an industry leader with more than 10,000 products, operations on five continents, and a worldwide team of more than 5500 employees and partners.