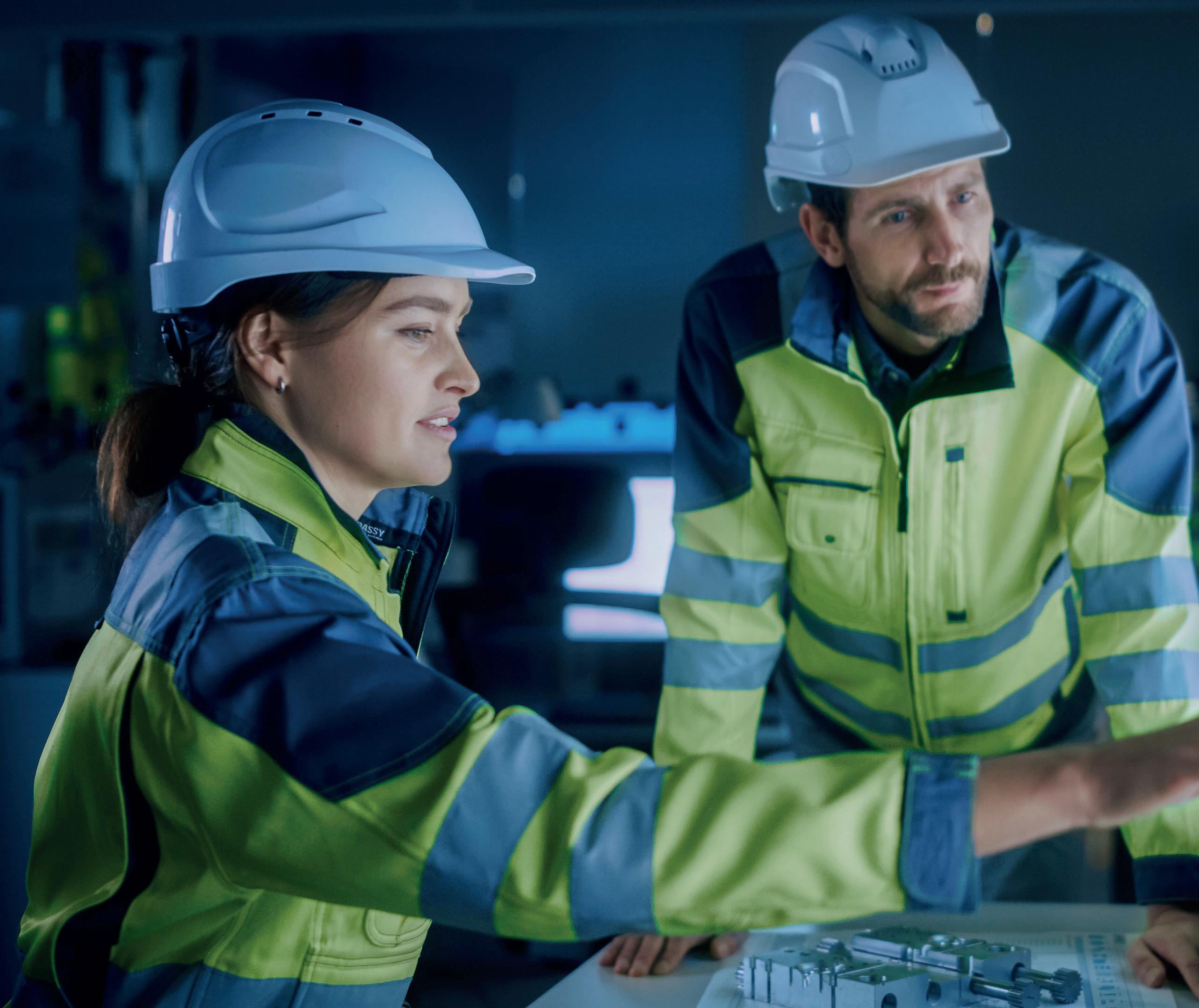
4 minute read
Smart manufacturing
Smarter communications
With the Government’s new data innovation hub set to accelerate digital technology
in manufacturing, Mick Goulding explores the role of connectivity and private
networks in securing sites, protecting people and supporting digital transformation in manufacturing
Manufacturers are moving to smarter and more automated operations to stay efficient, competitive and profitable, and there are many support systems in place to facilitate this.
Earlier this year, the UK government announced a £50 million data innovation hub as part of the £300 million UK R&I Made Smarter Innovation Challenge, to support manufacturers with the development of digital technologies to help to boost productivity, growth and sustainability.
The connectivity problem
In an industry which relies on communications - whether its backend business systems, production-line sensors, automated vehicle guidance apps, or team members across a site – connectivity is key.
For many manufacturers, it’s vital that communication networks are secure, simple to manage and, above all, always-on. But even the smartest of manufacturers will struggle with coverage not-spots, dropped connections and high cost, complex systems.
Typically, the largest manufacturing sites will often face the bigger issues. The scale and complexity of these sites means that conventional public networks and WiFi options often struggle to meet connectivity needs.
Facilities that are based in rural, hard to reach, or more remote settings will also face difficulties as public mobile coverage can be limited; whilst operations that are based in urban areas are forced to compete with thousands of consumers and businesses for wireless bandwidth. Unreliable connectivity has created a communications gap for businesses around the country that are looking to maximize the use of
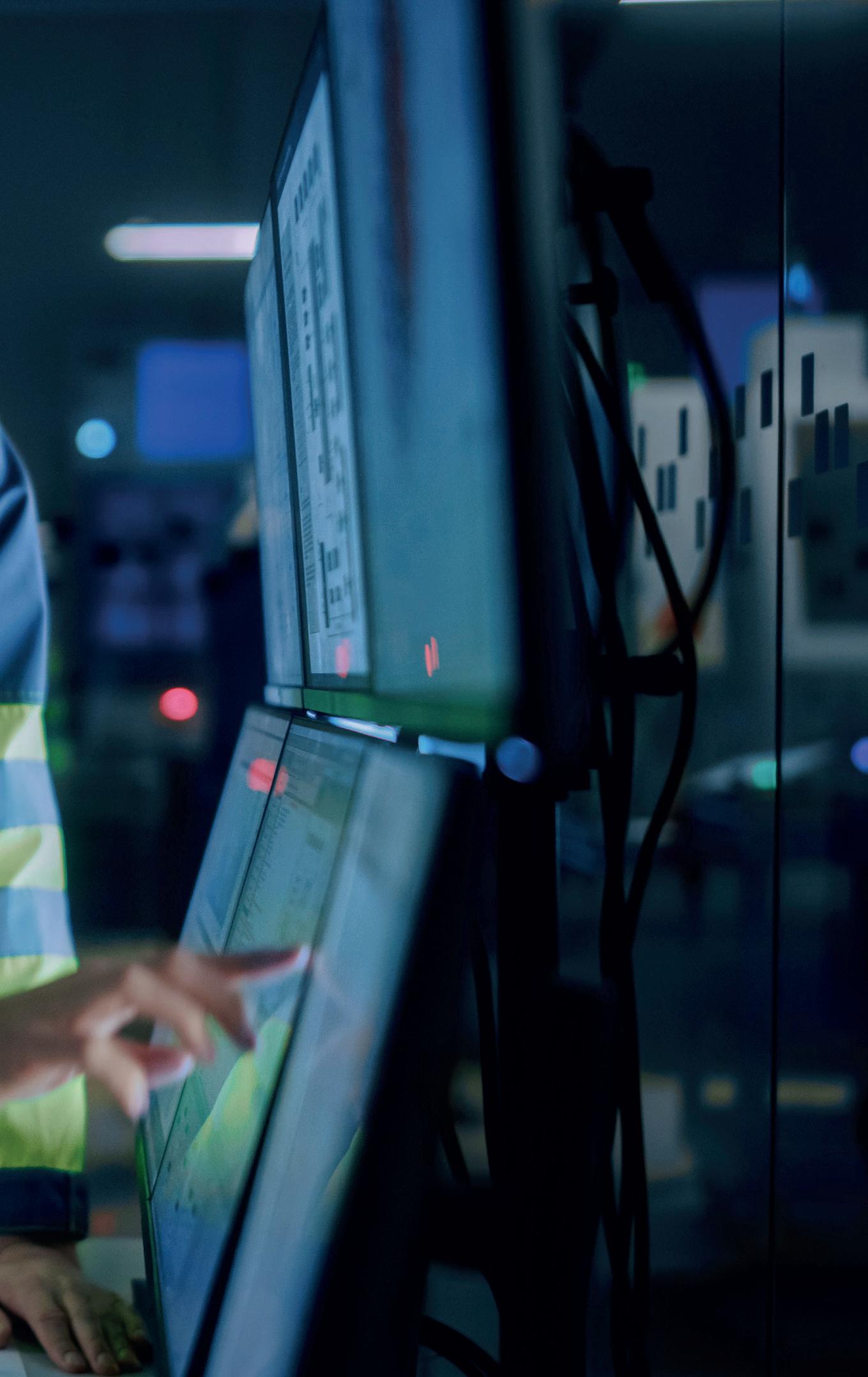
their data analysis and create a deeper and wider view of operations to increase efficiency. One area that manufacturers can be smarter with regards to their communications is by building and deploying their own private mobile network.
What is a private network?
Private networks are bespoke 4G or 5G mobile communications networks that help meet the specific needs of manufacturing sites, applications and existing coverage challenges. They provide guaranteed, always-on connectivity, tackling unplanned outages and ensuring operational continuity.
The private network system is designed around the specific needs of manufacturing sites and existing coverage challenges to offer a range of operational applications, like real-time data, that enhance worker safety and allow for in-depth asset tracking.
Enhancing safety
Private networks also enable a range of applications to support workers on site. For example, personal health devices can be used to continually monitor and provide health checks in hazardous or highstress environments. Where hazardous materials may be used, digital sensors connected via the network will constantly assess air quality and detect contaminants to prevent potentially harmful toxins impacting worker health.
Better connectivity will also enhance video surveillance and provide more accurate geolocation monitoring to track the location of assets, removing people from perilous locations entirely through task automation and remote control.
Tackling downtime
Unplanned downtime, which has the potential to lead to significant and costly delays, is an ongoing challenge for the manufacturing sector.
The low latency, high bandwidth, round the clock guaranteed connectivity of a private network provides manufacturers with the opportunity to enhance their connectivity and boost applications like data analysis. This allows for a deeper and wider view of operations, enabling real-time site monitoring and remote operations, which makes tackling downtime and increasing efficiency within the industry easier.
Transforming operations
Along with tackling downtime and ensuring worker safety, private networks provide manufacturers with the ability to utilize transformational digital technology, and upgrade key applications, including data analytics, asset tracking, automation, predictive maintenance and asset localization.
Faster connectivity will provide enterprises with detailed data analytics, enabling the monitoring of operational communications in real-time. This smart sensor data, in combination with machine learning, allows machinery to make swift and informed operational decisions.
Enhanced connectivity means manufacturing can also be made more efficient with asset tracking and asset localization, which enable autonomous vehicles and software guidance systems to provide 360° situational awareness of mobile assets, improving production lines by using geolocation to increase traceability of parts and tools. Once situated on-site, machines and robots can be automatically and independently monitored, enabling the removal of manual repetitive tasks, with predictive maintenance ensuring the operational continuity of key assets to create smarter manufacturing production. With levelling up high on the UK’s agenda, the manufacturing sector has a pivotal role to play in boosting productivity, creating skilled jobs and supporting local economies. Key to success will be secure, enhanced connectivity, and the industry must act now to ensure it has the capacity to apply novel digital solutions to manufacturing challenges. By leveraging initiatives like the government’s data innovation hub, the industry can invest in private networks and become a frontrunner in the race towards smarter production and Industry 4.0. v
Mick Goulding
Mick Goulding is Commercial Director, Enterprise at Cellnex UK. Cellnex is Europe and the UK’s largest and fastest-growing independent owner and operator of neutral wireless telecommunications and broadcasting infrastructures.