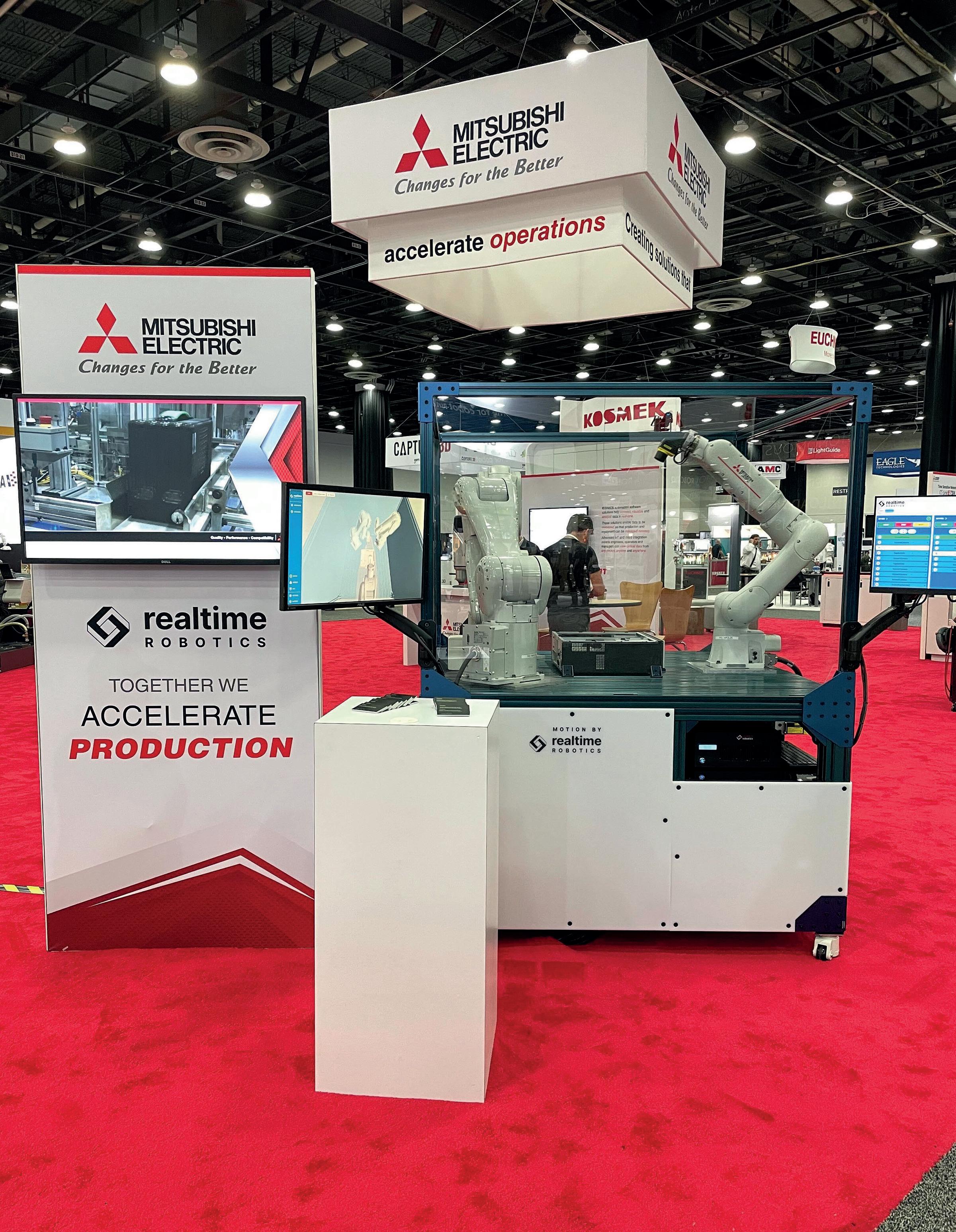
6 minute read
Automation
Change is here
Unleashing the next phase of robotic automation. By George Konidaris
Despite what you might have read in the popular press, robotic automation is stuck; useful, but much too hard, because we’re still doing things the same old way. New AI technology is set to finally change that.
Industrial automation is one of the key reasons the world is getting better: widespread consumer access to an incredible range of astonishingly complex manufactured goods is only possible because of the scale and cost-effectiveness it supplies. Very few of us know how to build a microwave, and it would take even an expert weeks or months to craft all the parts from scratch by hand, but the average consumer can nevertheless walk into a store and buy one for less than $100.
One tool in the industrial automation toolbox, however, is not living up to its potential. Industrial robot arms have done a lot of good for the world, but mass deployment has been restricted to the automotive and electronics sectors. Even in those industries, their contribution has been important but limited: most of the work assembling a car is still done by humans, with the robot contribution staying in the same lane for the past few decades. Today’s industrial robots are marvels of mechanical engineering, in most cases just as physically capable as a human, and much more precise. So why have they been stuck in the same gear (so to speak) for so long?
The primary reason is stupidity. Robots are stupid; exquisitely engineered, but stupid, and the average industrial robot sold today is no smarter than it would’ve been 20 years ago. As a result, putting them to work is much harder than it should be. Today’s industrial workcell is a mechanical engineering marvel that expends tremendous effort to bring every workpiece to the exact same position (down to the millimeter) every time, over and over again, so that the stupid robot that actually does the work can stupidly repeat the same trajectory, over and over again, to get the job done. Not only that, but the trajectory itself must be engineered by hand, every rotation or adjustment planned and coordinated by a trained engineer. Repeatable patterns must be established and followed exactly, in order to avoid collision or disaster. The situation is even worse when multiple robots must operate in a single workcell; every move must be tightly timed and coordinated, a pre-planned high-speed ballet enacted in the dark, replayed endlessly without variation.
All that engineering is expensive, so much so that the ROI on an industrial robot only really makes sense for high-volume, high-value products. Industrial roboticists are so used to all these restrictions and all this complexity and all that cost, because that’s just the way things are done; it’s the way things have always been done. Robot workcells are complex because they have to be designed to get around the stupidity of industrial robots. We’ve been in this box for so long that we don’t even see the box anymore; we’ve just come to believe that this is all that robotic automation can accomplish.
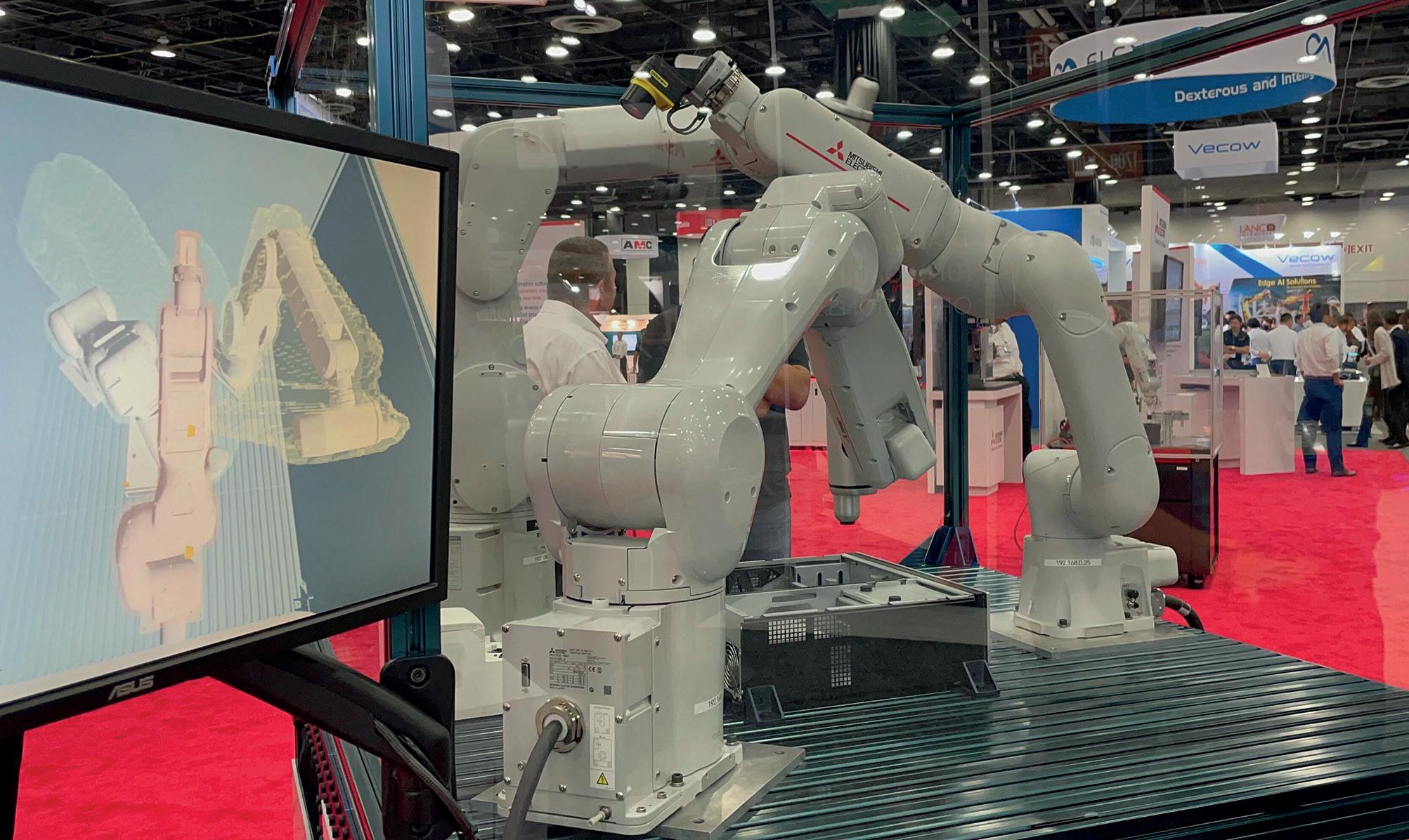
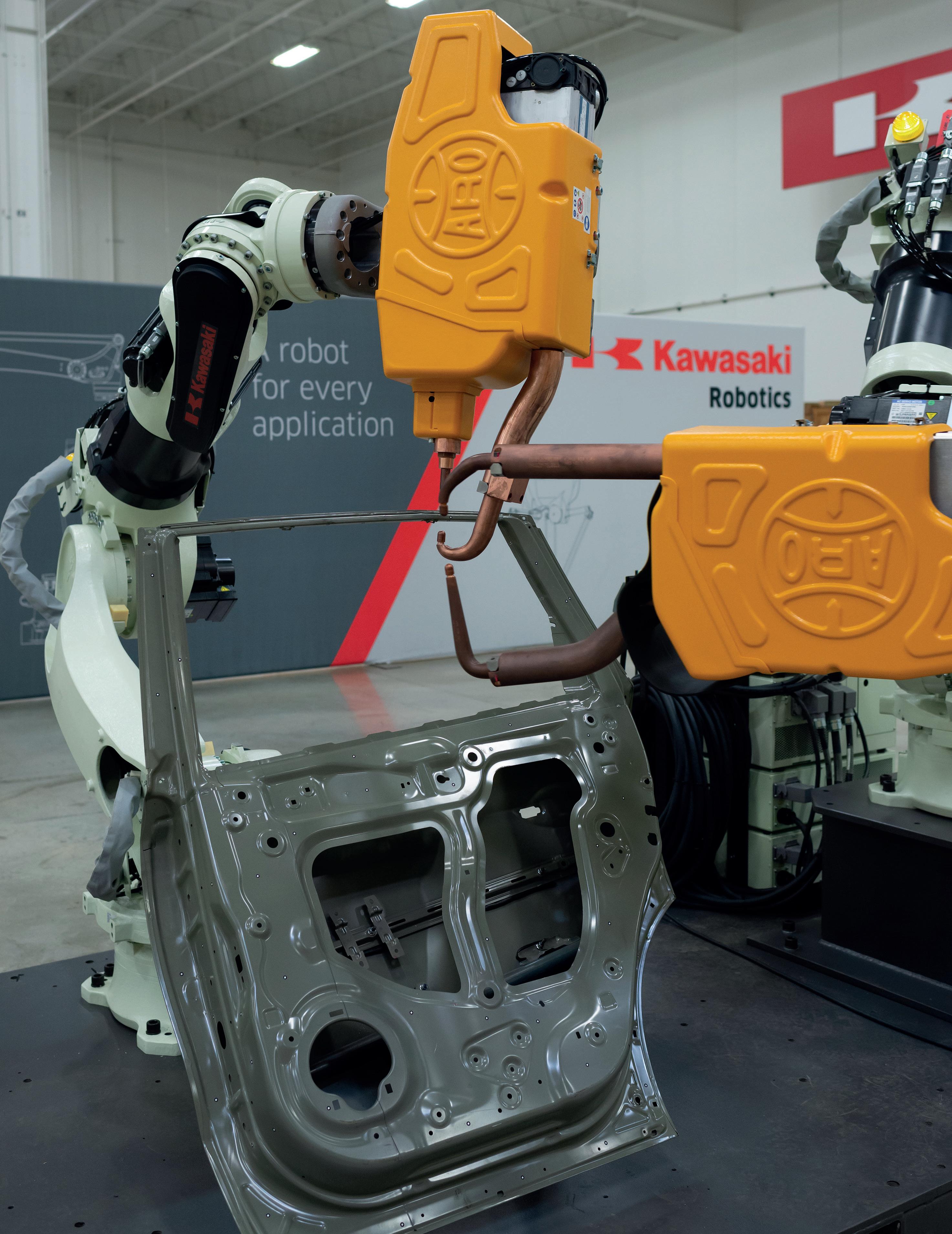
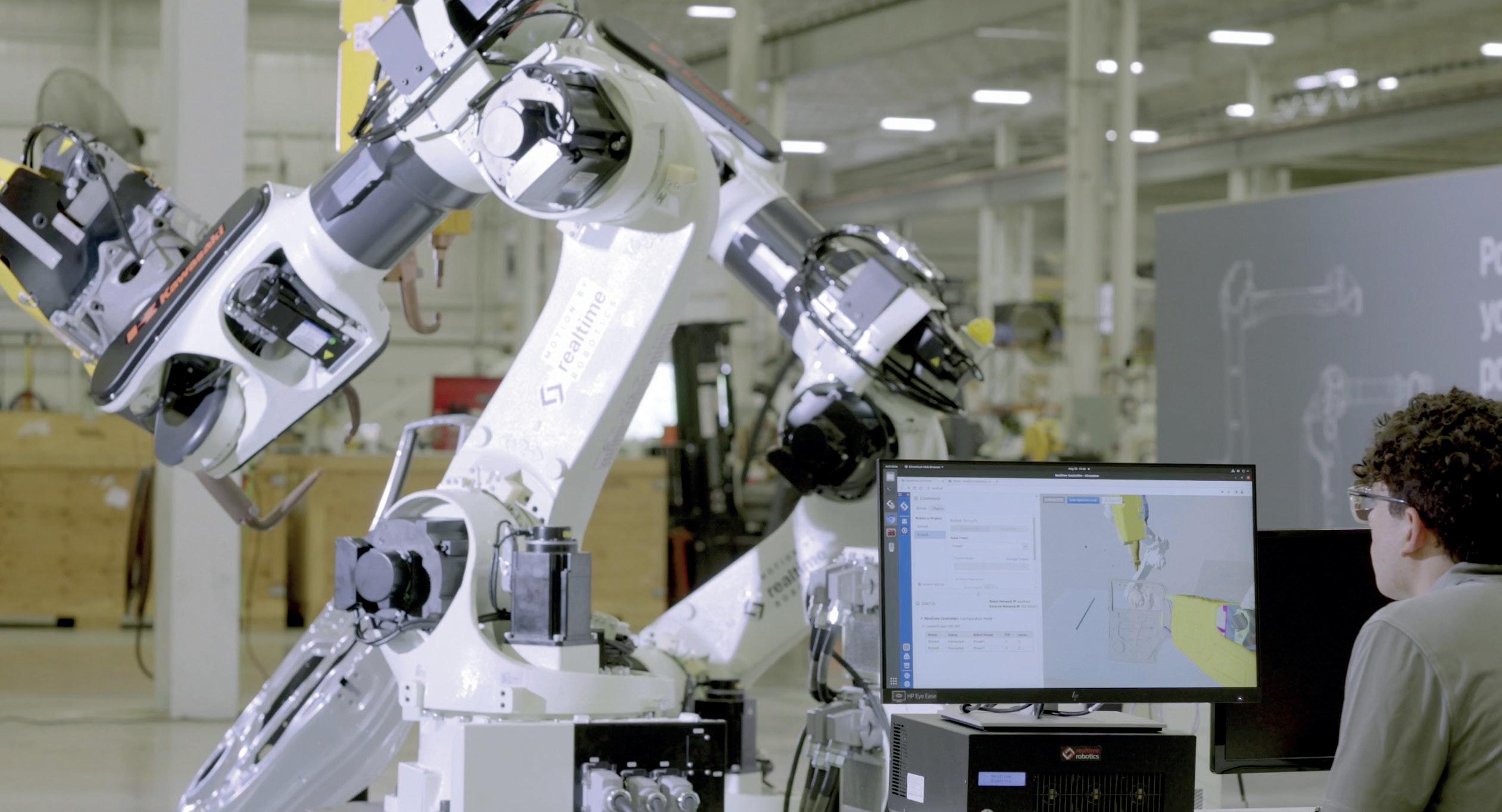
Now imagine a person working on a factory line. A welder doesn’t need what they’re working on to be in the exact same place every time; it would be almost laughable if they were unable to adapt to their workpiece shifting a few inches to the left. Someone screwing bolts into a workpiece is perfectly capable of picking up a bolt from a big pile in a box. And three people working in the same space will take a little while to adapt, but very shortly will have learned to work around each other. You simply put people in a factory, give them some desks and the parts they need to do their jobs, and they figure out how to do the thing right. In short, humans are endlessly flexible, and most important for us here, they’re able to react to and deal with minor variations in the world around them.
This example suggests that the industry’s current focus on ever more precise robot arms, able to ever more quickly repeat preprogrammed motions down to the tenth-of-a-tenth of a millimeter, is not just misguided, it’s holding us back. We find ourselves squeezing the last few drops of ROI improvement from the things we can already automate. But we can instead break out of our box by designing robots with a little more intelligence. Not the chess-playing, schedulemaking, essay-writing kind of intelligence, but the simple practical intelligence of how to sense the world, and how to move around without smashing into it.
Just imagine if all you had to do was show a robot what a workpiece looked like and tell it what to do with its business-end - and then the robot would generate all the relevant motion itself, on the fly and at a high-speed, carefully avoiding not just the rest of the workcell but the other robots working in it too. Think of how much less expensive everything would be, how much easier and cheaper robot factories would be to build, how many applications robots would suddenly make sense for. All that in exchange for just the ability to move around in the world, as competently as even the simplest insect.
Unlocking this next stage of robotic automation will require the development of robot controllers capable of displaying the basic physical intelligence required to deal with the world as it is, rather than as it can be engineered to be (at great expense). A new generation of robotics companies are, today, building on recent gains in AI technology to deliver just this, with the goal of making robots just a little less stupid and a lot more applicable, and so breaking the industry out of its decades-old doldrums.
Manufacturers - especially in these post-pandemic days where supplies are rare and demand remains high - tend to be very conservative towards new technologies, for the simple reason that they’re running businesses with low margins and hard throughput targets. It’s natural to not want to take too many risks when you have to deliver the things people use in their lives every day. But that conservatism is a dead-end, a recipe for finding yourself left behind. Now is the time for manufacturers to begin embracing new technologies - the type that can dramatically improve automation and have a long term effect on throughput, productivity, efficiency, and optimization - in short, your competitive advantage.
The factory floor of five years from now is not going to look like it does today. They will be less expensive, more reliable, and more flexible. Change is here - and you don’t want to be the last manufacturer to realize the benefits. v
George Konidaris
George Konidaris is the co-founder and Chief Roboticist of Realtime Robotics, a Boston-based startup that helps companies deploy smart automation faster, reduce cost, and improve productivity. He is also an Associate Professor of Computer Science at Brown, where he is the recent recipient of an NSF CAREER award, young faculty awards from DARPA and the AFOSR, a DARPA Director’s Fellowship, and the 2020 IJCAI-JAIR Best Paper Prize. Realtime Robotics technology generates collision-free motion plans in milliseconds for industrial robots and autonomous vehicles. Its solution empowers robots to function together in unstructured and collaborative workspaces, as well as to react to dynamic obstacles the instant changes are perceived. Its solutions expand the potential of automation.