
12 minute read
Revitalizing Communities: Award-worthy projects provide homes for the arts and history
Seven steel erection companies were named as recipients in the annual Project of the Year awards by SEAA. Three of the projects were part of broader redevelopment plans in the local communities where they were built, and five of them house centers for cultural expression—including performing arts, sports, and a museum. (For info on Class I and Class II winners, see Summer 2021 issue, page 32.)
Several of these projects represent jobs with complex sequencing, requiring coordination of cranes. In addition, two of the projects involved multiple roles for the companies. Deem Structural Services delivered turnkey service, including taking lead on connection design. Cooper Steel was the fabricator and managed the steel erection.
■ Complex sequencing in a tight work space
Conversion of a dilapidated ballpark into an amphitheater was part of a larger economic redevelopment plan for the south side of Bridgeport, Conn. United Steel Inc., Hartford, Conn., converted the dilapidated Bluefish Stadium
Tina Cauller is a graphic designer and freelance writer with 30 years of experience reporting for trade and technical publications in building construction and real estate markets. She can be reached at tinacauller@ gmail.com into a state-of-the-art boutique amphitheater. The newly named Harbor Yard Amphitheater will house concerts, graduations, community events, and festivals.
The hallmark of the building is a 125 ft high tensile roof and unique 107 ft high pavilion entrance, which is complemented by a 25 ft oculus. This one-of-a-kind structure required extensive planning and coordination utilizing three cranes working in unison on a tight site to install a 135 ft diameter trussed ring
that supports a 60,000 lb. cable-supported center mast and several cable-supported “flying masts.” United Steel’s structural steel erecting crews installed the intricate roof, which features many components supported only by cable.
The United Steel team successfully addressed and overcame several challenges during construction of this project, an impressive performance that earned the SEAA Project of the Year Award for Class III. In addition to location constraints imposed by an existing baseball field, the project involved complex erection sequencing — 11 steps for the erection of the main columns and 22 steps for the erection of the ring structure of the roof.
Staging cranes
To erect the ring structure, a 170-ton crane and a 120-ton crane had to be placed within the footprint of the ring, which was situated in the infield. During the preplanning phase, a plot drawing was developed to lay out the position of the six pre-assembled ring sections, the cranes, and two 120-foot boom lifts in the tight jobsite.
A third 330-ton crawler crane with 95 feet of boom and 203 feet of luffing jib was positioned outside the ring. First, all three sections of the 60,000-pound center mast had to be unloaded and pre-assembled inside the ring area. All bolts were torqued to optimum value and inspected by a third party. Once all three sections of the 75-foottall center mast were assembled on the ground, the center mast was rigged with six bottom cables and six top cables.
Field Operations Manager Steve Bean recalls, “We tipped the mast upright using a 330-ton crawler crane and a second 100-ton crane. Then the mast was hoisted up over the ring so the six lower cables could be attached to the bottom of the ring and the six upper cables could be attached to the top of the ring. We attached six 1-1/8” cables to the top of the mast and six 1-5/8” cables to the bottom of the mast. The mast was supported by the cables from the ring 50 feet off the ground. Top cables were ratchet-strapped to the mast to prevent them from swinging loose. The bottom cables were ratchet-strapped to themselves so they would not swing loose and bang into each other. Once rigging was installed, the center mast was hoisted into locations off the ground with a ratchet winch hoist.”
Ring installation and column erection
A second significant challenge was the installation of the 135-foot diameter ring 80 feet in the air off columns with pin connections. The six sections of the ring were assembled on the ground. These sections ranged from 85 feet to 75 feet in length and the weight of each section weighed range from 37,000 lbs to 27,000 lbs. Special cribbing was designed to stand up each section to be level and plumb.
The six main columns that supported the ring were 64 feet in length and only had a signal pin at the base and the connection at the top to the ring. Each column was connected to the base on a 20-foot-high concrete pier. United worked with Structural Workshop of Providence, R.I. to create temporary shoring columns with additional bracing that would not impede the hoisting of the pre-assembled ring sections.
To erect the main columns, United brought in two 120 ft boom lifts and placed them in location. All main column sections were carried into the work area with a 12,000 lb telescopic handler. The six columns were assembled using a 100-ton rough-terrain crane.
After eight shoring columns were unloaded and installed with the 100-ton RT crane, 7,000 lbs of concrete blocks were moved into location with the 330-ton crawler crane. Two pad eyes were welded to the existing stage columns before each of the six main columns were installed. Before releasing the columns from the crane, temporary cable bracing for the columns was installed and all main columns were surveyed for plumb.
According to Field Operations V.P. Glen Corneau, “We were excited to be a part of a project that is clearly visible from I-95 and has already enhanced the Bridgeport skyline.”
The newly named Hartford HealthCare Amphitheater promises to bring much needed economic development and vitality to the city’s South End. The venue is expected to host more than 20 concerts per season as well as graduation ceremonies, community events, and festivals. The Hartford HealthCare Amphitheater is a joint venture between the City of Bridgeport and Harbor Yard Amphitheater in association with Live Nation Entertainment.
A significant challenge of the Harbor Yard Amphitheater construction was the installation of the 135-foot diameter ring 80 feet in the air off columns with pin connections.

Complicated sequencing, limited site space, monitoring major truss deflections, and bracing were among the challenges faced by Deem Structural Services on the construction of Buddy Holly Hall.
■ Turnkey steel service
In 2013, the Lubbock Entertainment Performing Arts Association revealed their vision for a world-class performing arts center that was to be the cornerstone of downtown Lubbock’s revitalization efforts. In addition, the center is intended to honor the musical revolution sparked in the 1950s by the city’s most famous resident, Buddy Holly.
After the city council granted a parcel of land for the 120,000 sq ft center, the Lubbock Entertainment Performing Arts Association collaborated with other community partners to ensure financial sustainability.
The original vision blossomed into a massive $154 million, 220,000 sq ft facility with two theaters, event space, and a ballet academy. The main entrance showcases a 13-ton, four-story helical stair modeled after a funnel cloud in remembrance of the tornado that devastated the downtown area in May 1970, an architectural element that adds symbolic meaning to the space. On the south wall of the center, a 120-ft long sculptural installation depicts Buddy Holly playing a Fender Stratocaster using more than 9,000 pieces of cast aluminum-brushed bronze guitar picks to create a pixelated image of the legendary artist.
Deem Structural Services, LLC, Longview, Texas, earned Class IV Project of the Year honors from SEAA for their outstanding performance on this project. Complicated sequencing, limited site space, monitoring major truss deflections, and bracing were among the challenges of the job. In addition, connection design was delegated to the steel team. Adding to the complexity was a project-within-a-project—the erection of the funnel cloud-shaped stair, comprised of double-axis HSS tubing, supported only by cantilevered steel at each floor level.
19 sequences with site constraints
The large auditorium, which was built first utilizing two luffer cranes positioned on either side of the building, was surrounded by low roof structures that would eventually encompass the entire project site. Deem Structural Services erected engineered temporary bracing to supplement the main portion of the bracing and enable work to proceed outside the footprint of the low roof.
The foundation and civil work could not commence fully until the large auditorium erection was complete and the cranes were out of the way. Further complicating things was the 70 ft tall site cast tilt wall panels that were on the perimeter of the small auditorium located on the west side of the structure. As the erection of the large auditorium moved north and foundation work began, laydown and storage area became progressively more limited.
The project was divided into 19 sequences, with the large auditorium divided further into subsequences to accommodate delivery to the respective cranes, located on the east and west sides of the structure. This required total communication and close coordination between the Basden Steel team detailers, procurement, fabrication, and trucking departments to ensure the correct flow of drawing submittals, fabrication, and delivery.
Cantilevered trusses
The end wall trusses for this project required a critical lift using two cranes. While it is typical for trusses to have camber that must be induced during assembly and then monitored as the dead loads accumulate, the T6 truss at the end wall of the large auditorium presented more of a challenge than usual. As well as supporting the typical load of its own weight, roof steel, deck, etc., this truss also supported 46 tons of end wall girt framing and approximately half of the 140 tons of the second floor and roof of the lobby entrance. The lobby steel cantilevered off one column line (line 1e) in both the outward and inbound direction, creating a “teeter” effect as the loads increased.
The challenge was to ensure that the lobby floor and roof as well as the end wall girt framing remained at the correct elevation as metal panel cladding, louvre and window framing installation progressed. The solution was to install shoring under the inbound and outbound lobby steel until all dead loads from steel and deck were applied.
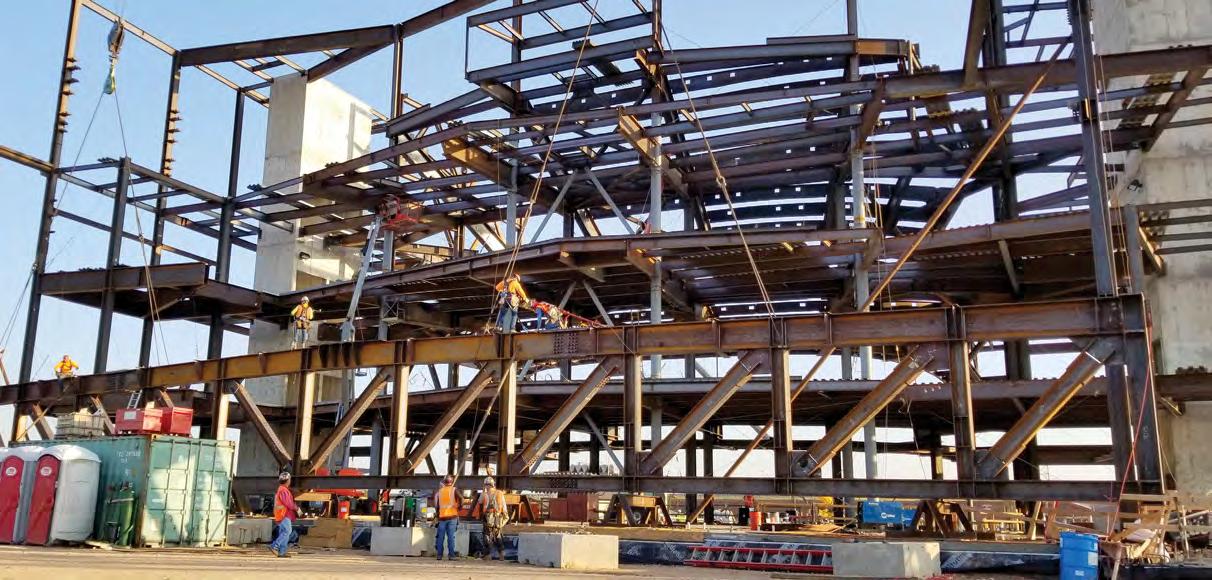

The end wall trusses for this project required a critical lift using two cranes. As well as supporting typical loads, the T6 truss also supported 46 tons of end wall girt framing and approximately half of the 140 tons of the second floor and roof of the lobby entrance.
Steel team leads connection design
Consistent with recent trends in the industry, the connection design was delegated to the steel team. This proved to be a benefit by allowing different options to facilitate preferred methods of both fabrication and erection and the ability to create “erection-friendly” connections. However, establishing a framework of shared understanding with the design team was essential and remained an important focus throughout the project. When information such as preset elevations at raker beams were needed from the design team, Deem’s commitment to straightforward, open communication with the Engineer of Record regarding design criteria and the associated requirements outlined in the AISC Code of Standard Practice helped ensure a successful project outcome.
Utilizing a turnkey steel service approach proved beneficial for this job, enabling the steel team to explore various options to add productivity and safety value. The Buddy Holly Hall of Performing Arts and Sciences stands as a tribute to the performer’s legacy and will be a cultural hub and first-class music venue for many generations to come.
Museum and Performance Center receive Honorable Mention
Two entries, one each for Class III and Class IV, were additionally recognized by SEAA with Honorable Mention—CAS Steel Erectors, Inc., Hendersonville, N.C., for the International African American Museum Project in Charleston, S.C. and Cooper Steel, Shelbyville, Tenn., for Nashville’s Belmont University Performing Arts Center.
■ Hazard zone construction
When the City of Charleston set out to build a museum at Gadsden’s Wharf, the site where enslaved Africans first landed in America, project planners had to mitigate a variety of natural hazards. The state of South Carolina is subject to hurricanes, earthquakes, and flooding, so for this new 41,760 sq ft elevated building, planners designed a seismic load resistant (SLR) system to withstand any potentially destructive events.
The SLR system incorporated connections with hundreds of inches of field welding, 220 standard moment connections, and 110 rigid frame moment weld connections. Box columns were fabricated from steel plate up to 2” thick since HSS columns would not withstand the anticipated forces and loads. Some of the SLR welds required welders qualified in AWS 1.8 Annex C.
CAS Steel erected structural steel and decking and built a temporary canopy where beams cantilevered out toward the waterfront over the boardwalk. They also erected scaffolding to temporarily shore cantilevered beams and hold elevations at the building perimeter until moment welds were completed.
While working under restrictive Covid-19 protocols, CAS Steel met the challenges of tight space constraints, an aggressive schedule, and a complicated design with numerous moment and seismic welds, including some up to 2-1/4" thick that had to be pre-heated in gusting waterfront winds. Maintaining critical tolerances on cantilevered beams and contending with a newly designed zero tolerance brick relief system posed an additional layer of complexity.
Rick Philips, V.P. at CAS Steel Erectors, credits the close collaboration with fabricator Lyndon Steel Company and Turner Brownstone for the project’s success.
CAS Steel executed hundreds of inches of field welding, 220 standard moment connections, and 110 rigid frame moment weld connections in the Seismic Load Resistant (SLR) system required for building the International African American Museum.
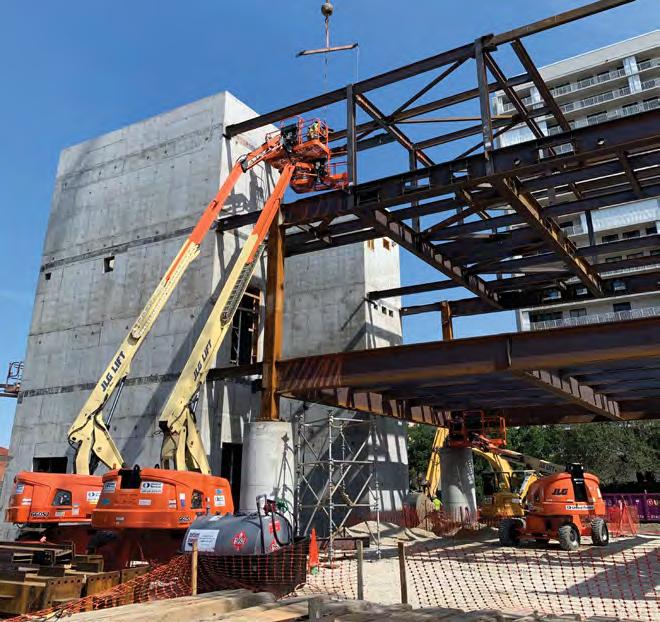
■ Precision and sequencing
The new Belmont University Performing Arts Center in Nashville houses a multi-purpose 1,700-seat theater with two event spaces. Cooper Steel served as the fabricator and managed the erection on the project, which was performed by fellow SEAA member Sentry Steel Service.
In all, 14 trusses were erected. They weighed up to 21.5 tons and measured 91 ft. With minimal laydown area available, the trusses were erected directly off the trailer and delivery times had to be carefully coordinated. To speed up the process, Cooper Steel pre-fabricated large pieces of steel off site.
In addition, the dome—consisting of 400 individual pieces with an accuracy tolerance of 0.5 in—required specific angles, sizing, and erection sequences. The dome’s location above the auditorium limited access, so R.C. Mathews erected a 50 ft platform to access the complex multilevel dome framing. Maintaining the incredibly tight installation tolerances throughout the duration of the project allowed finish trades to keep their established benchmarks with minimal modification to their scope.
This build created exceptional challenges of precision and sequence as each area was contin- Belmont Performing Arts Center, gent on another. Months of planning ensured that the dome ceiling, arch entryways, stage house, Nashville, Tenn. and heavy trusses for backstage and rigging would be structurally sound while also delivering an elegant, breathtaking aesthetic. •