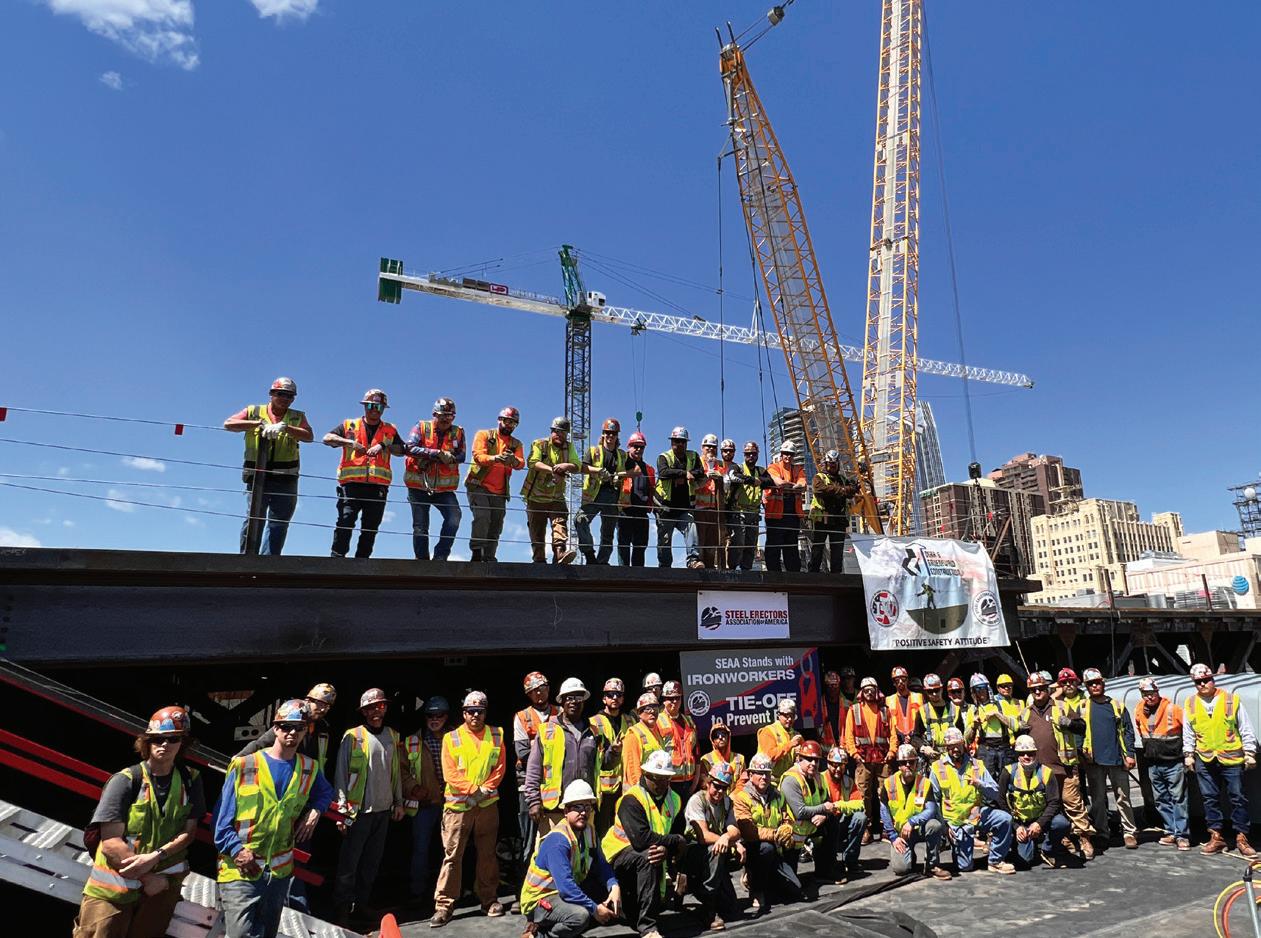
5 minute read
Connector - Winter 2022
Getting Engaged: Training & Safety Go Together
Best Practices of World Class Companies
COVER STORY By Bryan McClure
Cover Photo: Derr & Gruenewald Construction was one of several SEAA members that held Safety Stand Downs during Fall Prevention Week. Find resources for your own stand-down event at seaa.net/standdown.
Companies that invest in training and safety initiatives understand the cost benefits of doing so. Studies show that for every $1 spent on safety, there is a savings of 4 to 6 times that by reducing direct costs associated with incidents.
SEAA members who received World Class recognition in the association’s 2022 Craft Training Excellence and Safety Excellence awards programs embrace safety at the high est levels of their organizations. But it is more than a philosophical involvement—these are people who are actively engaged. During a panel discussion with these companies at the 2022 Convention & Trade Show in Charleston, S.C., we heard from one executive who took it upon himself to re-take rigger training so that he understood what he was asking from his employees. Another saw the need to balance the responsibilities being put on field foremen and instead to support them with full time safety professionals.
I encourage SEAA members to take the two hours needed to submit an application for either the Craft Training Excellence or the Safety Excellence award. The information requested should all come from documentation that you already have. The reward for recognition is more than just a trophy. Past winners will tell you it makes a difference in setting you apart from competitors, especially for subcontractors competing on price. Submissions for the 2023 awards are due January 31. Learn more at seaa.net/awards.
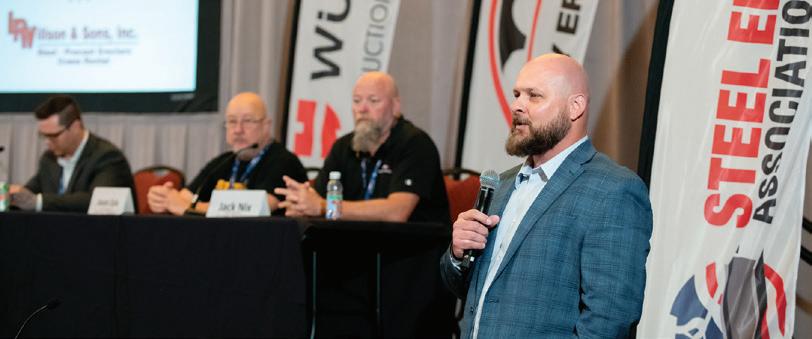
World Class award winning companies are invited to participate in a panel discussion at SEAA’s Convention.
The following Q&A is excerpted from the panel discussion. These best practices demonstrate that training and safety go hand-in-hand.
How has your company maintained your safety culture with the challenge of a high turnover rate in the steel erection industry?
Ed Valencia: New employees go through evaluation, orientation, and then they are teamed up with other employees who serve as mentors.
Jason Kulvinskas: The first introduction to our company is to our safety team. New employees see from the beginning the importance we put on safety. We believe this has reduced turnover—now 60 to 70 percent of our guys have been with us at least five years.
What are some strategies your company uses to keep employees engaged in safety?
Ed Valencia: We have safety meetings with all employees every day, then we split up into individual team meetings, which encourages them get talking because it’s a smaller group. We also have a behavioral safety program, where workers can turn in cards identifying both positive and negative actions that they’ve identified. One is drawn and we give out gifts to the person whose card we drew.
Jason Kulvinskas: We have meetings at the start of every day, to make sure the team is focused on safety. We also have meetings that focus on training employees that may need certifications, such as OSHA 10 or OSHA 30.
Pay raises are tied to achieving safety certifications. We also create awareness about accidents we learn about in the field (not necessarily GW projects) and we share this information with our crews so that they are aware of the potential risks and the measures that can be used to avoid those dangers.
John Ross McCartney: I don’t know that there is a magic answer to keeping employees engaged in safety. I believe that those strategies vary from company to company. Regardless of your trade or industry it all comes down to the people you employ and their willingness to buy into the company safety culture. It’s our obligation as owners and managers to get know our employees and their families, which creates a level of accountability for both the employer and employee to ensure everyone makes it home safe from work every day. Keeping those val ues at the core of our safety culture is what we strive to maintain on a daily basis.
You are a World Class Safety in Excellence winner; what are your plans to make your program even better this year?
Ed Valencia: Every year we evaluate our injury lists and incidents to look for areas that need improvement. For example, we are using a new drop test tower to look for better ways to tie off.
Jason Kulvinskas: We look for trends and then modify training to address those trends.
Jeremy McAllister: To add to that, we are doing more training with safety managers
Jack Nix: Employees who complete online training courses receive a financial stipend attached to successful completion. That’s something we do to incentivize our employees to continue to do additional online training.
John Ross McCartney: Our affiliation with the Delta Indemnity Group Captive Insurance Program has been a great tool to challenge us as a company to continue to improve our practices and avoid complacency within our safety culture.
Click the article to read the full Q&A and to learn more about the 2022 Safety Excellence Award Winners.
Panelists
• John Ross McCartney, President Derr & Gruenewald
• Austin Reiner, Safety Manager
• Ed Valencia, Corporate Safety Director
• Jason Kulvinskas, Vice President
• Jeremy McAllister, Director of Safety Operations
• Jack Nix, Chief Operating Officer
• Jason Zyla, Safety Manager
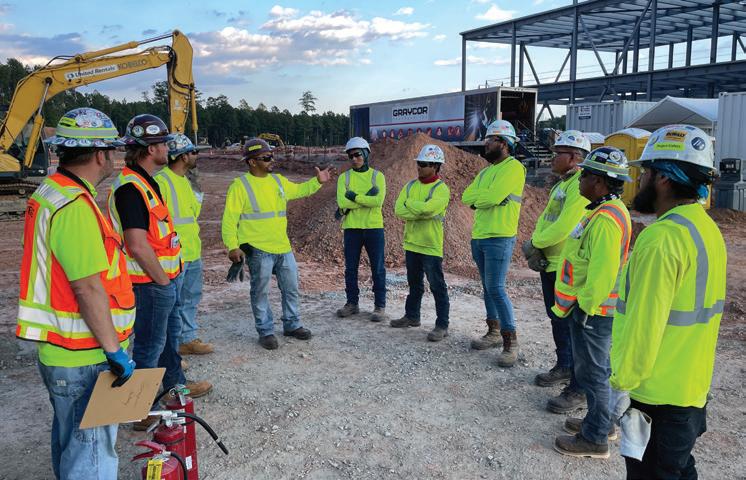
Daily safety meetings at Gardner Watson allow team members to share information about accidents they’ve heard about in the industry. They discuss potential risks and measures that can be used to avoid those dangers.