
11 minute read
Waste Not, Want Not
by SeafishUK
Waste Not, Want Not
By Ana Witteveen
Advertisement
Identifying opportunities to improve efficiency and reduce cost
While financial factors will always be of vital importance to any business, there is an increasing trend – and expectation – for businesses to adopt a triple bottom line approach, where social and environmental performance indicators are considered alongside economic ones. Cutting Edge investigates how processing businesses can improve resource efficiency, benefiting people, planet and profit.

But what is resource efficiency and what can UK processing businesses do to improve it?
Resource efficiency is about getting the maximum benefit from resources, while minimising waste and the costs of waste disposal. Savings could come from improving insulation and heating systems, switching to renewable energy, reducing water use and making better use of processing by-products.
According to the Waste and Resources Action Programme (WRAP), waste could be costing businesses in the food and drinks sector as much as 4% of annual turnover.
Energy is another key operating cost for seafood processing businesses around the UK, costing a further 1 to 2% of annual turnover, on average.
“Those that improve efficiencies can make significant cost savings, improving business profitability,” asserts Jimmy Buchan, CEO of the Scottish Seafood Association. “Any savings from increasing resource efficiency can then be used for further development and growth of the business.”
Across the UK there are numerous programmes available to help businesses improve resource efficiency. However, it can often be difficult to identify and implement innovative savings opportunities, especially as support and funding options can vary by business size and location.
To learn more about business support available to seafood processing businesses, Cutting Edge spoke to individuals involved in three very different and exciting projects in Scotland.
Resource Efficient Scotland
Resource Efficient Scotland (RES), a Zero Waste Scotland programme, was launched by the Scottish Government in 2013 to deliver on its commitment to help small and medium-sized Scottish businesses reduce energy and resource costs by improving resource efficiency.
The RES programme is free for businesses to access, and in the 2018–2019 financial year, it delivered 1,050 projects to approximately 800 small-to-medium enterprises (SMEs) across Scotland, with many of these in the food and drink sector.
“Reducing operating costs not only improves your margins but can help make you more competitive,” emphasises John Murray, Programme Manager of Resource Efficient Scotland.
Estimated cost savings for different measures ranged from £2,000 to almost £40,000.
“If you qualify, RES assigns you an expert framework consultant who will review your business’s current situation and assess potential opportunities for resource efficiency savings, no matter where you are located in Scotland,” he confirms.
As a result, projects have been carried out in every single local authority area of Scotland, with particularly good uptake from the Highlands and Islands region.
A quick snapshot of the typical RES process shows that in under a month from first contact, your business can have a qualifying RES report in hand.
The report includes unbiased cost and carbon saving estimates associated with different measures based on the business’s financial and technical information.
“Once they have a completed report, businesses can apply for government funding to help with implementation,” explains Lisa Bertrand, consultant at Beyond Green, a RES framework contractor.
Government funding is available as an unsecured interest free loan of up to £100,000; 15% cashback may also be available to help SMEs implement identified resource efficiency measures.
Funding comes from the EU and Scottish Government and is distributed on a first come, first served basis each financial year.
The loan can be used to implement resource efficiency measures related to energy, waste, water and raw materials:
– Insulation
– Lighting and heating
– Waste reduction
– Renewable energy
– Water efficiency
“Sometimes businesses come forward with ideas, but consultants also discuss the wider business to make sure they’re not missing any opportunities,” notes John Murray. “It’s more of a general audit if the business doesn’t have specific ideas in mind.”
Lighting, heating and insulation are the most common areas identified for improvements. “In the food and drinks sector, this extends to include refrigeration and water use as well,” he explains.
Jimmy adds,
So far, RES has worked on 15 projects with seafood businesses around Scotland. “I recently delivered three projects for seafood businesses covering measures from energyefficient refrigeration, electric vehicles and LED lighting to renewable energy options including solar PV, wind turbines and heat recovery. One business even installed an automated plastic crate washer based on the report recommendations!” comments Lisa. “Estimated cost savings for these different measures ranged from £2,000 to almost £40,000, with payback periods usually less than eight years.”
J H Milne, a Peterhead-based processing business run by the Milne family, was one of the first Scottish processors to engage with RES.
“We already had an idea of what changes we could make within our business, but going through RES confirmed our ideas and now gives us access to the government loan,” says John Milne. “Now that we’ve got the RES report, we’re hoping to access loan funding for solar panels and a heat reclaim system within the factory.”
He explains that because businesses in the sector often operate with tight margins, they can be reluctant to spend money to invest. “But,” he says, “anything that can cut costs in the long term helps, especially during periods when the price of fish is up, and any savings can be reinvested in the business.”
John confirms that he would recommend the RES programme to other businesses. “It makes it much easier to justify practical investment,” he concludes.
On average, 70% of businesses involved in RES go on to implement at least one identified resource efficiency measure.
RES’s John Murray also confirms that nearly 50% of identified cost savings (by value) go on to be implemented: “Some businesses even implement one change now, then in a few years come back and implement another one, with RES supporting them throughout this process.”
RES can also provide business support through the implementation phase, which lasts, on average, four years. John adds, “We can help businesses with things like evaluating tenders and identifying local suppliers.”
Case studies from other Scottish seafood businesses that have been involved with the programme are available on the RES website.
Call Resource Efficiency Scotland for free on 0808 808 2268
Circular Economy Business Support Service
The Circular Economy Business Support Service, provided by Zero Waste Scotland, also offers resources, advice and funding support to Scottish SMEs. Similar to RES, this service is funded by the EU and Scottish Government.
The service offers free consulting to help business owners explore new circular economy concepts or applications for their businesses. The Circular Economy Investment Fund is then available to help businesses take development ideas forward to the implementation stage.
“The service provides expertise to support the development of new circular economy solutions in Scotland,” explains Peter McCafferty, Circular Economy Business Support Framework Manager at Zero Waste Scotland.
Through the programme, Zero Waste Scotland has worked with a number of seafood processors to explore circular economy models based on increasing the value of, or ‘valorising’, waste streams and by-products under the bioeconomy sector umbrella.
One company that has received Circular Economy Investment Funds is Pennotec, a biotechnology company working to commercialise the extraction of chitin from crustacean shell waste. Chitin is a fibrous substance that makes up 20 to 30% of shells, giving them their flexibility and shape.

Dr Jonathan Hughes with a water clarifier product made from chitin.
Dr Jonathan Hughes, Managing Director of Pennotec, explains. “We’re now working to bring science and industry together to create new and exciting chitin products, getting the maximum value from materials.”
Through the iCRAB (integrated Chitin Ryegrass Acid Biorefinery) project, Pennotec is working to bridge the gap between seafood processors, which consider crustacean shells as a waste, and other industries, like the nutraceuticals industry, which value the products that can be extracted from shells.
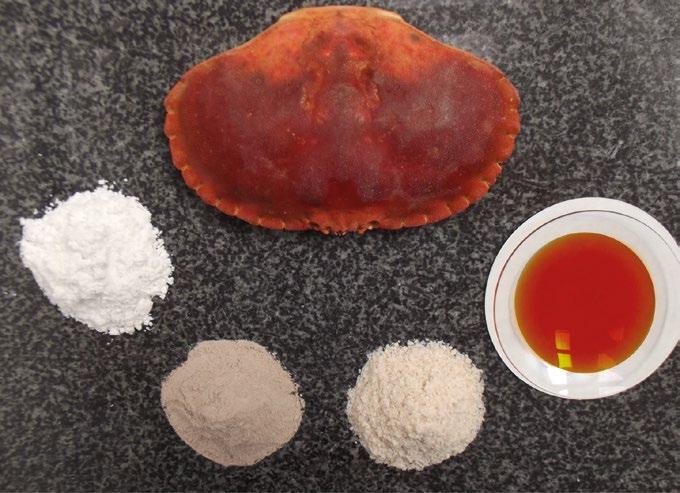
Crab shell components, from left to right: Calcium salt, protein, chitin and astaxanthin.
The idea is that chitin can be used in applications like cosmetics, surgical stitches and as a food thickening agent, adding value to a previously worthless processing by-product. Jonathan says:
As Peter points out:
What was once seen as a waste stream from shellfish processing now presents commercially lucrative circular economy business opportunities. Processing businesses around the UK have the opportunity to get involved in innovation like this to increase the value of processing by-products.
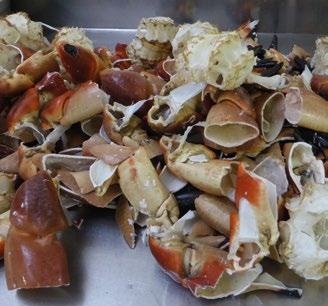
Crab shell waste.
“Our programme primarily supports SMEs but also wider supply chains and other collaborative circular economy projects where the lead is an SME. This enables larger businesses to get involved,” adds Peter. “And regardless of business size, we’re always happy to have a conversation about opportunities and resources available through other programmes.”
Contact Zero Waste Scotland Circular Economy Business Support Service and online acceleration centre at circulareconomy@ zerowastescotland.org.uk
Dawnfresh
The triple bottom line approach also brings people, and especially staff wellbeing, into the business performance equation.
Dawnfresh, a large Scottish-based seafood processor supplying both UK retailers and global markets, is keen to engage its 650+ employees in resource efficiency training as part of its new well-being strategy.
To find out more, Cutting Edge spoke to Fiona Anderson and Liz Gemmell at Dawnfresh.
“We have organised two employee engagement days at our Uddingston site this summer,” says Fiona. “The first ‘Love Food Hate Waste’ day is to raise awareness about easy practical everyday things people can do at home and work to reduce food waste and increase recycling. The second, ‘Home Energy Advice’ day, run by Home Energy Scotland (HES) and Scottish Water, is about highlighting ways to save on electricity, water and heating.”
“It’s important for us to empower staff and encourage everyone to think about resource efficiency and cost savings as part of our well-being programme, especially from a financial perspective,” adds Liz.
In addition to helping staff reduce waste and save money at home, Dawnfresh also expects the training outcomes to translate to the workplace, improving the business’s resource efficiency and reducing operating costs.
As HES is government funded, these training days are free of charge to the business. Fiona concludes:
Call Home Energy Scotland free on 0808 808 2282
_____________________________________
Seafish is also working with Seafood Scotland on its new Seafood Industry By-Product Stakeholder Working Group as part of Seafood Scotland’s new Changing Tides action plan launched in May 2019.
“The working group aims to bring readymade circular economy solutions direct to industry,” advises Patrick Hughes, Head of Seafood Scotland.
Seafood Scotland is currently working with experts at Zero Waste Scotland, Aberdeen & Grampian Chamber of Commerce, Scotland Food and Drink, local councils and Stirling University, amongst others, to build an understanding of current by-product streams in seafood processing and the potential for these streams to generate value add opportunities.
“There’s a lot we can learn from other countries and parts of the food and drink sector,” stresses Patrick. “Now we need to pull this information together and approach the sector with tailor made solutions. This will help businesses reduce waste management costs and increase the value of processing by-products.”
Lewis Cowie, Marine Sustainability Manager at Seafish, agrees, commenting that moving from a linear to a circular economy has been shown to benefit businesses by capturing more value from raw materials, reducing running costs and increasing competitiveness.
“Supporting the seafood sector to respond to supply chain integrity and reputation issues is a key area of Seafish’s work,” confirms Lewis. “Our Responsible Sourcing team is currently undertaking a project with industry partners to explore how a circular economy can be established in a seafood industry context.”
Consideration for people and the planet, as well as profit, has pushed businesses to work at the cutting edge to meet social, environmental and financial business needs.
Other resources
Fortunately, there are already numerous programmes and resources available to engage with, helping businesses tackle challenges head on and develop innovative solutions to industry-wide problems.
The UK Seafood Innovation Fund calls for applications for either small feasibility studies or large full-scale R&D projects to kick start sustainability and productivity improvements across the UK seafood supply chain. The threeyear, £10 million programme was launched in July 2019 by the Centre for Environment, Fisheries and Aquaculture Science (Cefas), an executive agency of DEFRA.
Innovate UK offers UK-based businesses the opportunity to compete for government-backed funding to research and develop a process, product or service, test innovation ideas and collaborate with other organisations.
Waste and Resources Action Programme (WRAP), founded as a charity in 2000, works with businesses, individuals and communities throughout the UK to achieve a circular economy by helping them reduce waste, develop sustainable products and use resources in an efficient way.
Advance London is a three-year programme which places London’s SMEs at the heart of the circular economy, offering a community, business support advice and financing. T: 020 3963 0675, E: info@advancelondon.org
TFuture Peterborough aims to apply circular economy principles at the city level. The programme is focussed on making the most of local resources, supporting economic resiliencies, developing strong communities and increasing environmental sustainability. T: 017 3331 7417, E: info@opportunitypeterborough.co.uk
Useful reports
Seafish Introduction to resource and waste management
WRAP Reducing waste in the fish sector
WRAP Self-assessment review for food and drink manufacturers
For more information, please contact Stuart McLanaghan, Head of Responsible Sourcing on Stuart.McLanaghan@seafish.co.uk