
5 minute read
INTRODUCTION TO EV BATTERIES
As the world shifts to address problems of climate change and air pollution, the transportation industry is moving quickly to find alternatives to gasoline-powered vehicles. Decreased dependence on fluctuating oil prices, fewer emissions, and an all-around smoother ride has increased demand for electric vehicles (EVs). EVs have lower emissions, making them better for public health and the environment, and also provide increased economic opportunities.
Nearly 18 million EVs are expected on U.S. roads by 2030, compared to one million at the end of 2018. EVs can be powered by several types of batteries, such as solid-state, aluminum-ion, or lithium-ion. The battery is the most important, controversial, and expensive part of an EV. The battery determines a vehicle’s range, power, and cost. Lowering the cost of a battery is the most effective way to lower the overall costs of EVs and allow them to reach cost parity with gasoline-powered vehicles. Most of today’s EVs are powered by a lithium-ion battery, which has the highest energy density, making it the most powerful option. It is also the cheapest battery with no required active maintenance.
Battery Production
Most of the world’s EV battery supply is manufactured in Asia. The top five battery companies are China’s Contemporary Amperex Technology (CATL), Japan’s Panasonic Corporation, China’s BYD, South Korea’s LG Chem LTD, and South Korean’s Samsung SDI. Less than 3% of the global demand for EV batteries is supplied by companies outside of China, Japan, or Korea. Even battery manufacturers that originate in countries outside of these three eventually tend to move to these countries, because of existing infrastructure and low permitting costs.
Despite this geographic concentration of battery production, car manufacturers, policy makers, and potential battery suppliers have powerful economic and strategic incentives to strengthen local battery production. In areas of high demand, such as Europe and the United States, dependence on Asian battery manufacturers puts auto manufacturers at a disadvantage with competitors that are closer and better able to access battery supply. The emergence and spread of COVID-19 has negatively influenced the battery supply chain, decreasing supply and increasing prices, and causing logistical and production delays. In February 2020 alone, the price for lithium hydroxide increased by more than 3%. With the supply chain located far from consumers, these complications will further affect battery production oversight. Lithium-Ion Batteries
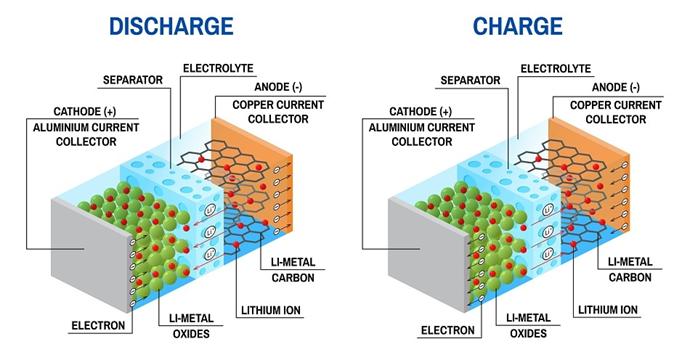
Source: Let's Talk Science
The most popular type of electric vehicle battery is made of lithium-ion. In this type of battery, the lithium flows between the anode and the cathode, which generates charge. In 1980, the American physicist John Goodenough invented the current lithium battery model in which the lithium travels from one electrode to another as a positive ion. This was a groundbreaking invention, as lithium is very light and also has a large electrochemical potential. This innovation meant this new battery could be extremely powerful while staying compact, which is central to increasing an EV’s range and performance. Lithium-ion has a low self-discharge rate, which allows the battery to retain maximum stored energy for many years. Unlike other battery alternatives, lithium-ion batteries do not require any active maintenance, which reduces consumer cost.
Alternatives to Lithium-Ion Batteries
Despite the dominance of lithium-ion batteries in the EV market, researchers and auto manufacturers are looking for alternatives in response to some of the issues in lithium-ion battery production. One alternative on the horizon is solid-state batteries. This battery replaces the liquid or polymer electrolyte with a solid electrolyte. The solid electrolyte allows the battery to retain energy with increased density, which some researchers believe could allow EVs
to have a range of over 500 miles. Because of the increased durability of solid-state batteries, this would also decrease the number of batteries being disposed or recycled.
Major automakers like Ford, Hyundai, Nissan, Toyota, and Volkswagen are investing in solidstate battery research, and some believe that solid-state batteries will come to market as early as 2020. There are some doubts about this model, which could limit its commercial success. Solid electrolytes are less conductive than liquid electrolytes. Since conductivity is dependent on temperature, solid-state batteries risk lower performance in cold weather climates. Solidstate batteries are also incredibly expensive. A few manufacturers have developed models that overcome their temperature issues; however, they are far too expensive to appeal to consumers.
Another option closely related to lithium-ion is an aluminum-ion battery. The structure of this battery is the same as lithium-ion, except it contains an aluminum anode rather than a lithium anode. Aluminum is the most common metal on Earth with an established industry and recycling infrastructure, which makes the use of aluminum very cost-effective. Some research shows that aluminum-ion could one day have twice the energy density of lithium-ion alternatives. However, the research on aluminum batteries is limited, and there are no options on the market as aluminum-ion batteries have issues overheating and are twice as large as their lithium-ion counterparts.
Two other alternatives are nickel metal hydride and lead acid batteries. Neither are powerful enough to fuel all-electric vehicles, but some researchers believe they could get there. Nickel metal hydride batteries are traditionally used in hybrid vehicles. They regulate temperature well, and they degrade at slower rates than lithium-ion. Lead acid batteries are mostly used to supplement battery loads in EVs, or in vehicles where speed is not an issue, like golf carts or forklifts. They are still fairly high-powered, inexpensive, and safe. However, both models will require a lot of refining to allow them to power an all-electric vehicle. Because lithium-ion batteries are powerful and cost-effective, there have been efforts to find an alternative to using cobalt and ensure that any cobalt used is mined ethically. Reducing or eliminating cobalt use also lowers overall cost, as it is the most expensive ingredient of an EV battery and its price continues to rise. Tesla’s battery producer, Panasonic Corp, announced a goal to develop an EV battery without using cobalt. They have already produced a battery that significantly reduces cobalt by increasing nickel content while still maintaining thermal stability. Apple and Samsung have joined the Responsible Cobalt Initiative, which pledges to address the environmental and human rights issues associated with using cobalt. Apple has started to purchase cobalt directly from those who mine it to ensure that acceptable safety practices are being followed.
The reality is that lithium-ion batteries that contain cobalt are currently the cheapest and most powerful EV battery option on the market. Battery prices are down 85% since 2010, largely due to innovations in lithium-ion batteries. As the demand for EVs grows, it will be difficult to find an alternative that is so cost-effective.

Source: Rocky Mountain Institute