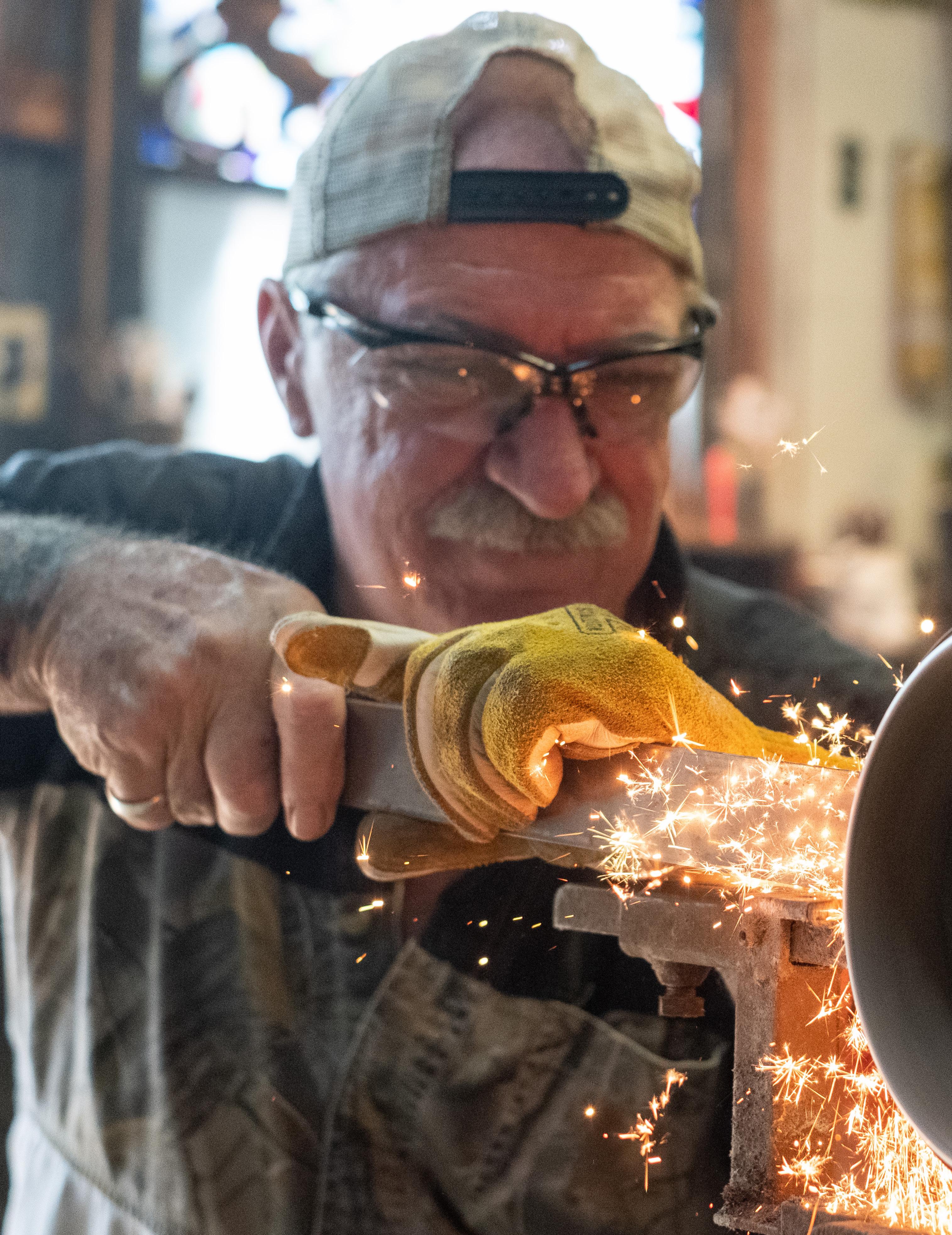
4 minute read
LEVENSAILOR BLADES
Damascus Knives by Levensailor Blades

Story and Photos by Lizz Daniels
Walking into Randy Levensailor’s knife workshop when the furnace is burning feels a bit like taking a stroll on the sun’s surface might. Within moments of the fire coming to life, sweat begins to pour, and the heat becomes almost overwhelming. That’s when he draws a red-hot piece of steel from the forge and dips it in oil to cool. Steam billows up in a whooshing cloud, and that’s when it’s obvious –– Randy Levensailor is the real deal.
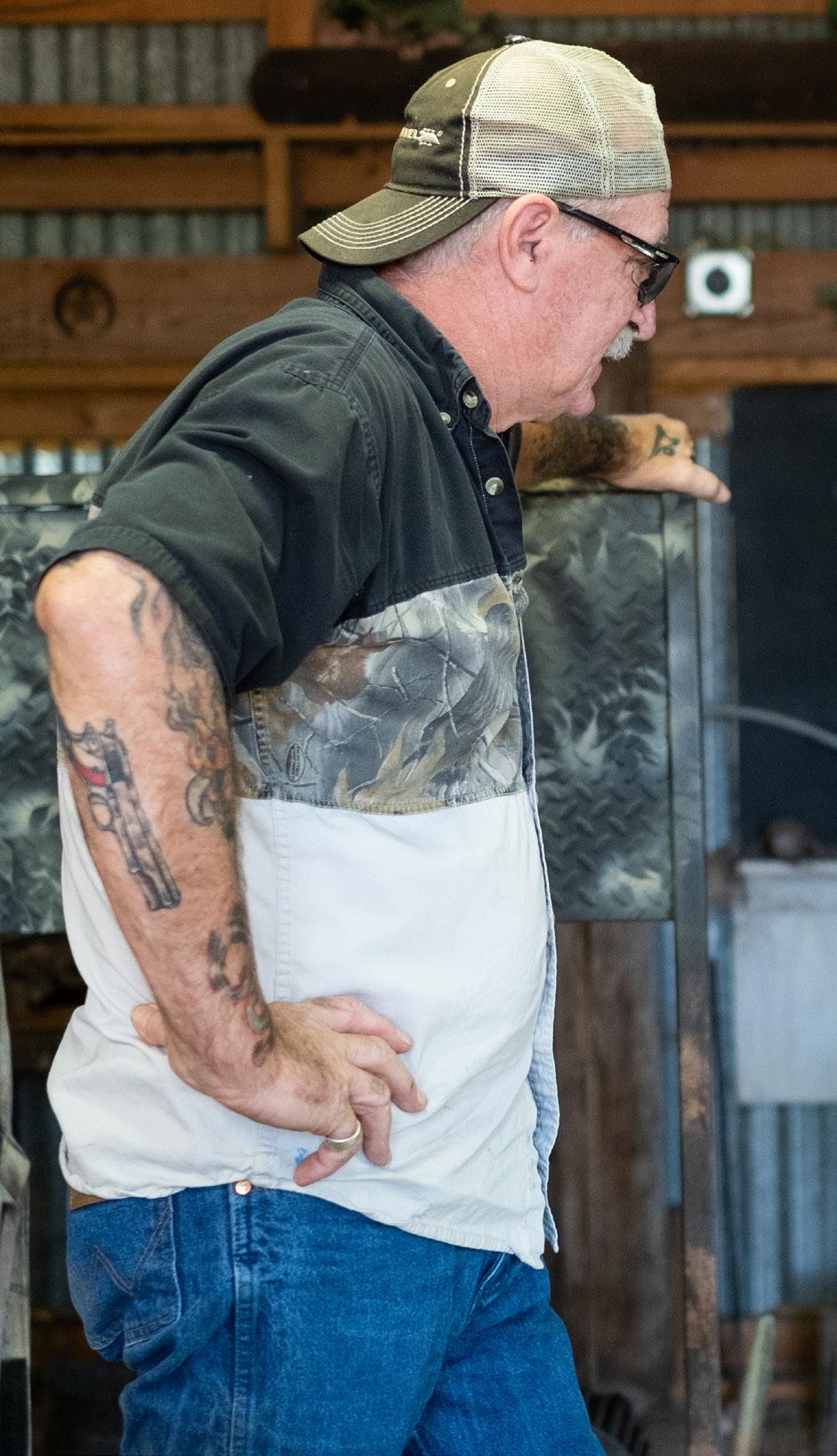
His tin-sided shop sits in a shady patch of trees near his home and was a horse barn before it was remodeled. Levensailor spends countless hours in the heat of his shop, forging Levensailor Blades for clients worldwide.
Levensailor began his metalwork career as a welder handshaping and bending thick steel bars together into gates, banisters, and more.
“Back then, I had a lot of free time on my hands at night, so I started making some decorative art pieces,” he said. “That’s when I really started piddling with knives. I started buying books and reading about Damascus (steel) and knife-making. When I moved houses, my landlord let me and a couple of friends remodel the barn and turn it into my workshop. The rest is history.”
Levensailor’s interest in bladesmithing began during his childhood, where he had unhindered access to the public library. He buried himself in the stacks, taking in all the information he possibly could, dreaming of worlds far from Seguin.
“I always loved Native American art, so much so that I would run around with my mom’s lipstick on my face and feathers in my hair,” he said. “I was making bows and arrows when I was 10 years old. I made my first blade when I was 16 with a piece of stainless steel I found. When I stumbled across Damascus steel, it was beautiful. It became the love of my life.”
Levensailor spent years dreaming of Damascus’ distinct patterns –– swirling banding that looks more like flowing water than hardened steel. Years into his adulthood, he discovered the art of modern-day Damascus.
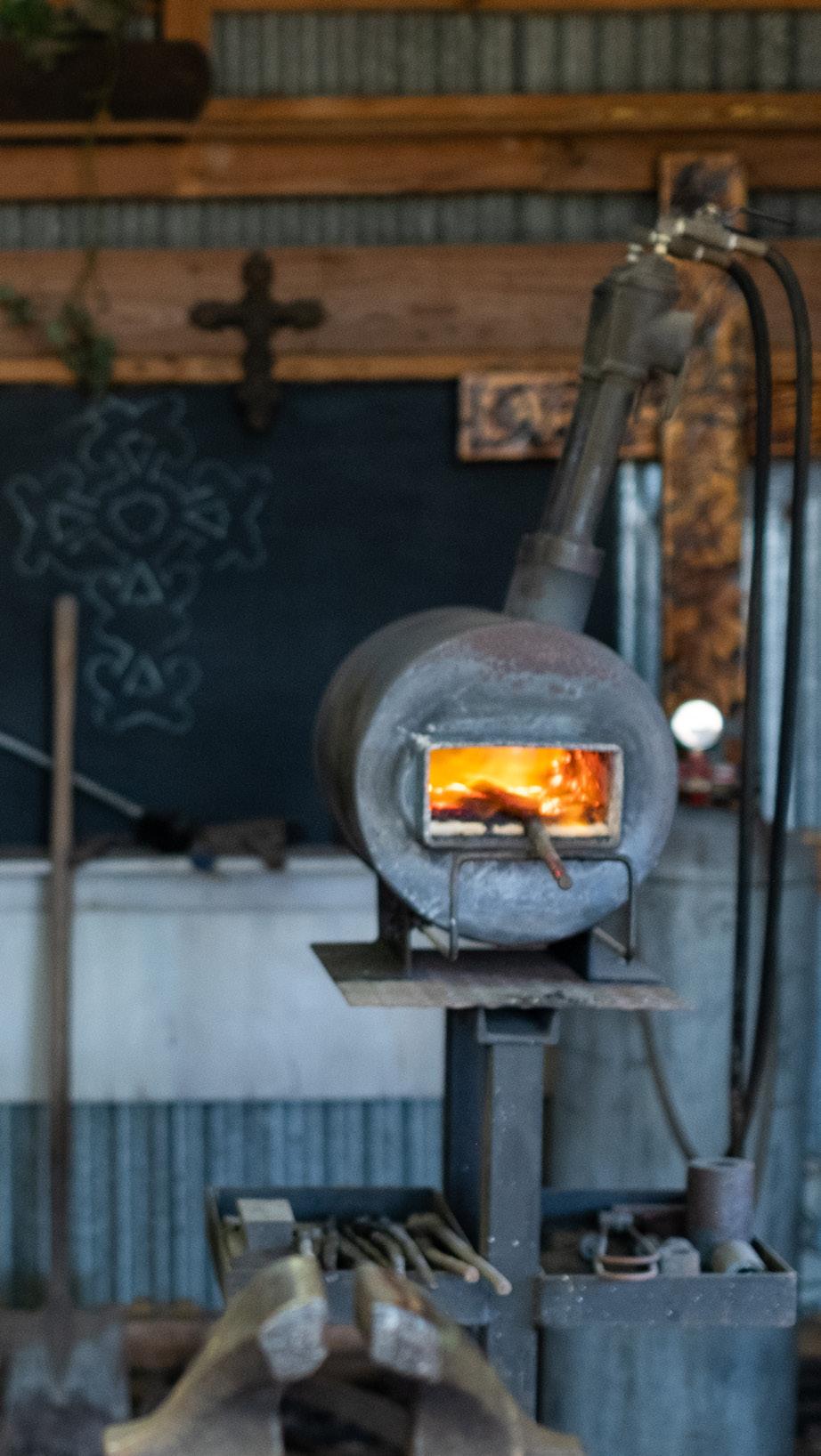
The steel, named for Syria’s capital city, originated in Southern India sometime in the third century. The art of its forging was considered lost by many when changing trade routes in the 1700s caused production to decline. As traditionally forged Damascus blades became more rare, the legend surrounding them grew –– so much so that an internet search in 2020 reveals many online users believe the steel to be nothing more than mere fantasy.
While the metal may have origins worthy of myth, it is very much real and has withstood the test of time. However, forging requires time and patience, even with the benefits of modern tools like a power hammer.
“To make Damascus you’re taking steel that’s already hard and you stack it up, hammer it together, making it harder,” Levensailor said. “You fold it, hammer more, and it gets even harder. It’s a lot like what the Japanese did in making Samurai swords. You fold layers on layers. The process produces a high quality, hard-edged steel.”

The blades require hours of physically demanding work and exposure to intense heat. Despite its clear challenges, Levensailor loves it and puts the same amount of care into his straight carbon knives as his treasured Damascus.
On his YouTube channel, Levensailor demonstrates the strength of one of his knife’s by hammering it through a stainless steel bar on his anvil.
“When I finished, it didn’t have a scratch on it,” he said. “I have people tell me all the time, ‘man, they hold an edge like crazy!’ I mean, if you can take a knife and clean two to three deer and it still shaves hair off your arm, then you’ve got a good knife.”
The entire production process happens from start to finish in Levensailor’s workshop and inside their home, where his wife, Crystal, steps in to help.
“I do the sheaths and Crystal helps me do the wet sanding on the blades because that’s something I just got burned out on,” Randy said, laughing. “She gets all the scratches out; then, we stamp them and heat treat. After that, Crystal polishes them up before they go in the acid etch –– that’s what brings out the beautiful patterns in them. Then we assembled them.”
When he first started the business, Randy said he couldn’t give his knives away. Now celebrities — like singer Ted Nugent — commission his work and game ranches custom order knives as gifts for their hunters.
“Their reputation speaks for itself,” Randy said. “This is old-school, handmade.”
The dark stamp of the Levensailor logo sits in stark contrast with the shine of a sharp edge as Randy slips his knife into its sheath, leaving only its wooden hilt exposed. It is a thing of beauty, forged in blistering heat, with a lifetime of passion in each measured blow required to bring it into existence –– a relic from the past, reimagined for a new generation, brought to life by bladesmith Randy Levensailor.
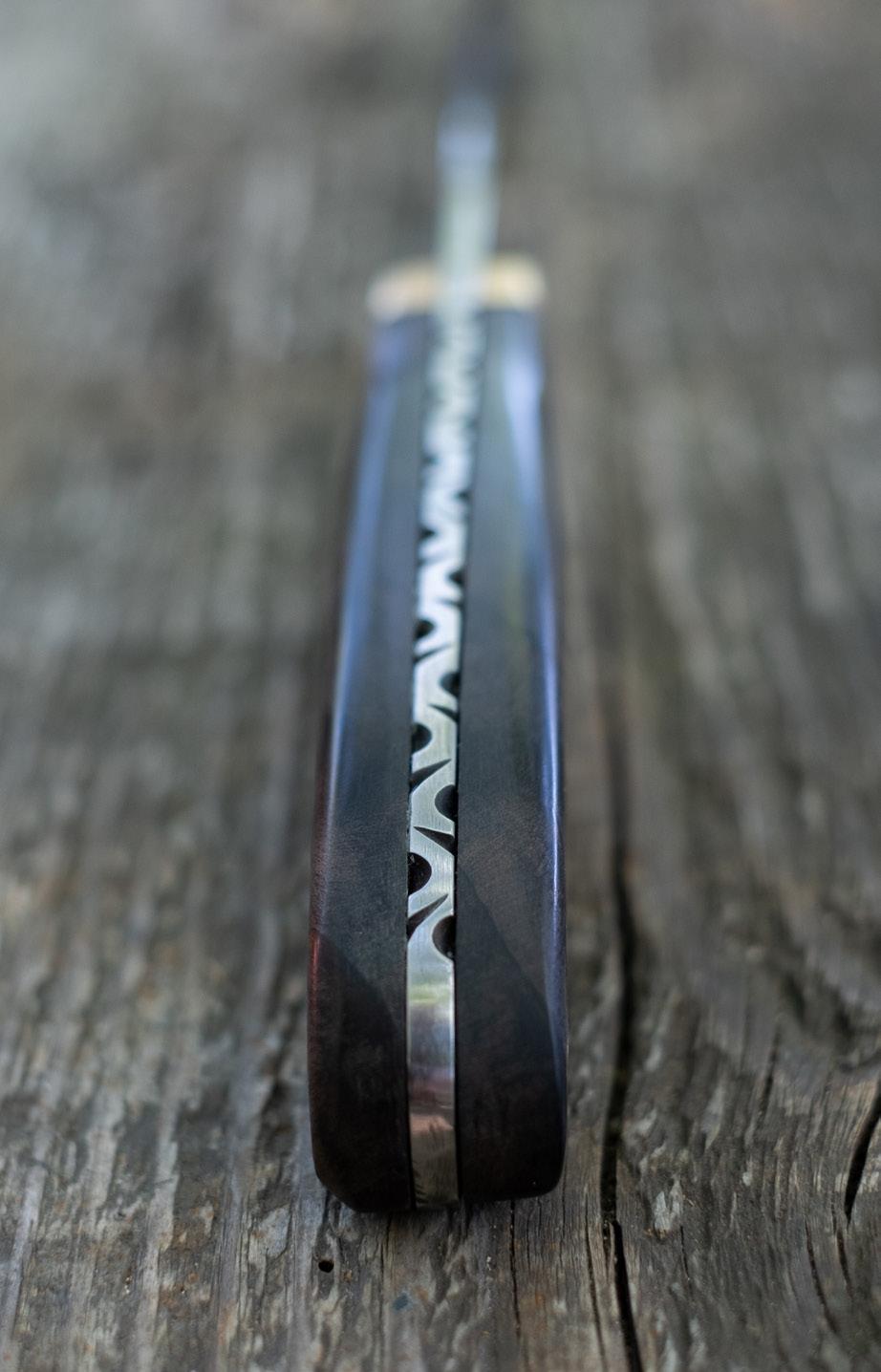