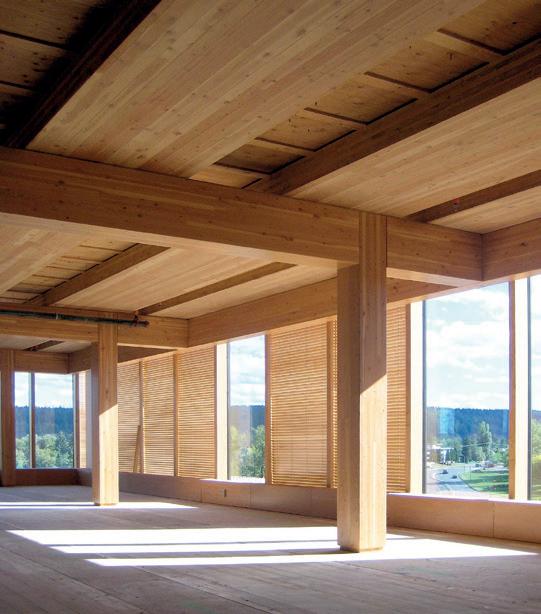
4 minute read
DIY timber frame
Stick build describes a method of creating structures that are built up on site from individual pieces of timber. The main architectural objective is to create a home that uses timber in ways that are not readily perceived as being factory produced.
In reality, you can build the whole structural frame in sections in a factory or shed to make sure that all the connection joints fit properly, then reassemble it on site. This is not necessarily the time consuming task that it might first appear to be, as it allows the opportunity to make adjustments which would be difficult to achieve on site.
It also borrows from the factory controlled offsite construction benefits of prefabricated timber frame manufacture. One well known example of how large timber structural frames can be erected in a day can be seen by checking online for examples of Amish barn raising.
The stick build approach is a bit of a misnomer nowadays in that the term ‘stick’ no longer refers to what we would normally think of as sticks, but can be any size of timber element from small diameter roundwood poles to large section engineered timber beams.
The main idea of the stick build method is that you start with a structural frame or skeleton, which can be filled, encased or left exposed according to the design objectives. In a similar way to the prefabricated type of timber frame structure, the external wall panels will need to be well insulated and would have an exterior facing of brick, blockwork, stone or cladding. The method also lends itself well to the use of interesting roof trusses which can be as simple or as complex as they need to be.
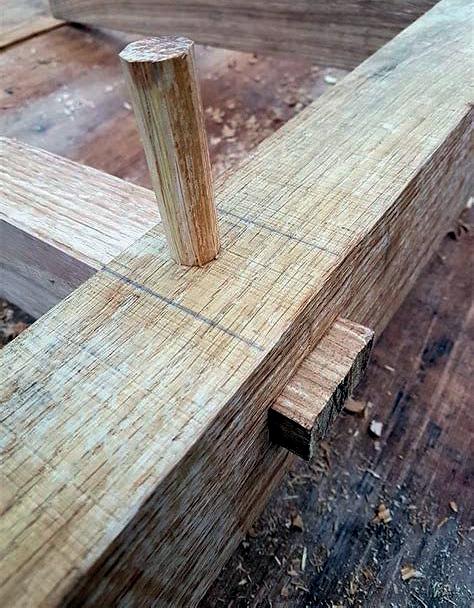
This type of timber frame is often the basis for what many refer to as an eco build, that is where the walls are lined with a renewable insulation product such as straw bale. With shuttering, timber frame is also the structural base for hemp-lime or rammed earth construction. Steel frame is an alternative but is more expensive and harder to work with than timber.
The standard building regulations in use in the UK and Ireland do not specifically include dwellings built by stick build methods, but neither do they rule them out. The European and national standards for timber structures, where they apply to solid timber, only cover regular rectangular or circular section members or poles and not irregular shaped members.
Whether you choose to use standardised strength graded timber or engineered timber from a timber merchant or roundwood from a local woodland, this method of building does not have industrial certification or quality assurance so it is vital that it is designed and certified by a structural engineer. It may also be a good idea to sound out the opinion of your mortgage lenders before embarking on the project.
Oak frame example
The general stick build method is still used in oak framed building, where the construction is based around a structural skeleton of oak framing using tried and tested jointing techniques. Traditionally built by skilled craftsmen using mainly hand tools, the stick build methods can be adapted for more modern methods of construction. Usually for reasons of economy, prefabricated factory produced timber frame homes tend to follow a restrictive standards based set of methods and processes, whereas a stick built home can have more flexibility in its approach to design.
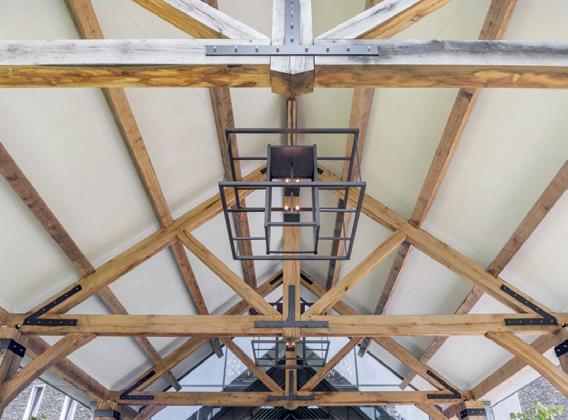
One such approach would be to take the example of traditional oak framed structures and follow a layout such as the aisled frame. This layout consisted of a series of frames which were formed to create bays which supported the roof, but the rafters were extended down onto external walls set outside the main frames. Such a structure would remove most of the roof loads from the external walls and the external timber wall panels.
Another solution would be to adopt the ‘post and beam’ structure which consists of horizontal beams carried across two or more uprights. Each set of posts and beams are then repeated in bays along the length of the building and as these frames carry the roof, open plan spaces are easy to create. Either of these frame types will require timber bracing to provide racking resistance.
Importantly, you do not have to build this type of design in oak but can use more economical or readily available alternatives. In all such timber that has been sawn into squared planks, beams or columns, the most often used joint is the pegged mortice and tenon joint, whereby a hole for a peg is drilled across the midpoint of the tenon where it slots into the mortice.
The peg is tapered so that when it is driven into the joint it locks in. Usually the hole for the peg in the tenon is offset slightly from the hole through the mortice so that when the peg is hammered in, it pulls the shoulders of the tenon tightly into the mortice joint.
The Segal method
For the more adventurous and environmentally friendly selfbuilders, perhaps the best known building method which would fall under the title of stick build is that attributed to Walter Segal, a Berlin-born architect who moved to England in the 1930s.
He has been quoted in many construction related publications but his innovative rethinking of standard building processes is well worth remembering. The methodology for making large savings in build costs that he developed in the 1960s can be summarised as follows:
� Base the building structure on a bolt jointed timber post and beam framework.
� Make everything as simple as possible.
� Accommodate tolerances and thermal movement without complex construction details.
� The structure should be buildable by someone with basic carpentry skills, although installation of services would be completed by a plumber and electrician.
� Only basic hand tools should be required.
� Make maximum use of materials in their standard sizes to reduce waste and cutting, through use of a design based on a simple grid.
� Support the posts on simple concrete pad foundations, the holes for which can be excavated by hand and the concrete mixed on site. (Segal’s original house used paving slabs as pad foundations.)
� Raise the ground floor so that oversite concrete is not required.
� Avoid the use of wet trades such as bricklaying and plastering.
� Make it easy to insulate to a high standard.
� Make the building easy to adapt and extend if necessary.
� Can be constructed up to three storeys if required.
� Passivhaus or zero carbon levels of energy usage must be