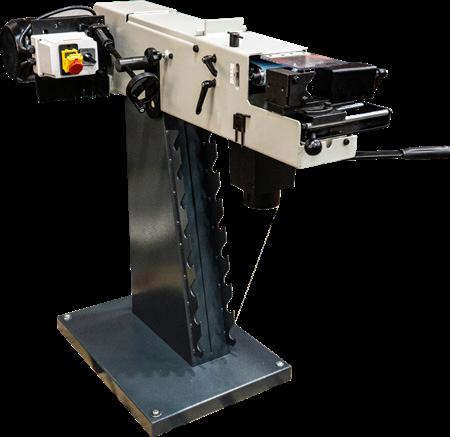
2 minute read
ALMI Manual & Powered Noctchers
The Almi range of pipe notching machines are manufactured in Holland and provide the perfect solution to notching tubes prior to welding.
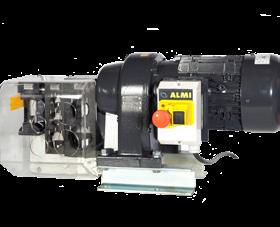
Advertisement
The AL1, AL2 and AL3 manual notchers are an excellent cost effective solution for 90°joins. The AL1-2E motorised model is ideal for intensive use whilst the AL1-2U incorporates a venting slot notch. Large range, fast notching, perfect fit.
Machine Features
• Fast, accurate notching

• No consumables required
• Produces weld ready notches
• Covers range of nominal bore tube sizes
• Vent notch tool for release of galvanising gases (ALU, AL1-2U only)
• Powered production notching (AL1-2E, AL1-2U only)
Technical Specifications
ALMI & RVD Abrasive Tube Noctchers
The Almi & RVD belt driven pipe notching machines achieve a superior notch finish due to the greater accuracy of the roller and belt notching method. A wide range of rollers is available which can be purchased separately, ensuring flexibility of future tube sizes that may arise.
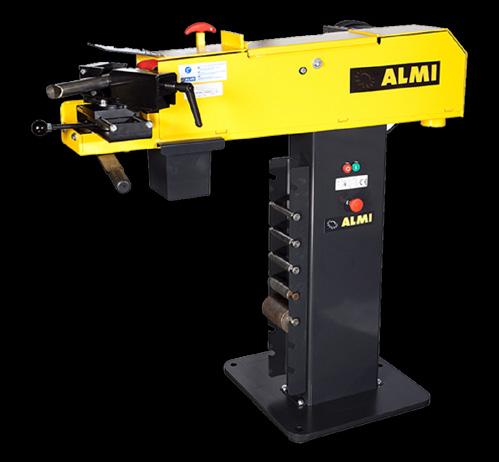
Available in three different configurations, the AL100u & AL150u offers an impressive 2800rpm belt speed (30m/s), while the AL150HS (High Speed) offers an incredible 4300rpm (45m/s) belt speed. The RVD P100 offers an impressive 30m/s speed too.
Al100u
Machine Features
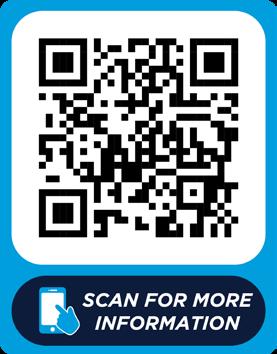
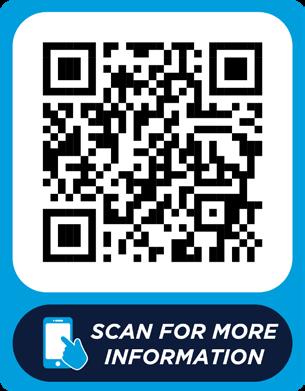
• Stable and accurate working
• Fast and almost heat-free grinding of stainless steel
• No grinding frames and discolouration of the material
• Grinding rolls that can be exchanged quickly without tools
• Quick change of grinding belts
• Handy de-burring by means of a de-burring table
• Left-handed and right-handed use
• Cutting out any desired material
• Grind any angle between 20º-90º (30º-90º on the Al100)
Optional Equipment
• Hand wheel operation (AL100u)
• Length stop
• Dust extraction system
ADJUSTABLE ANGLE VICE
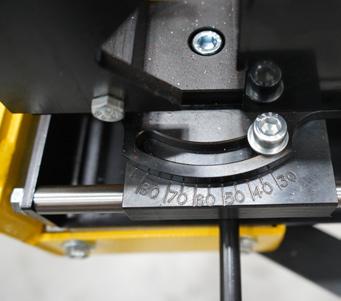
DE-BURRING TABLE
BELT EDGE
INTEGRATED RACK FOR BELT ROLLER STORAGE
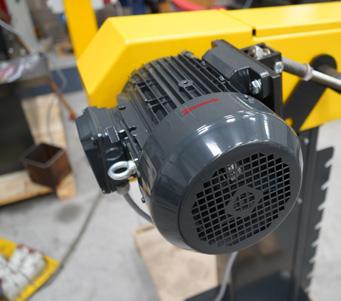
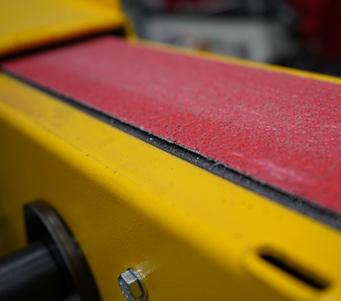
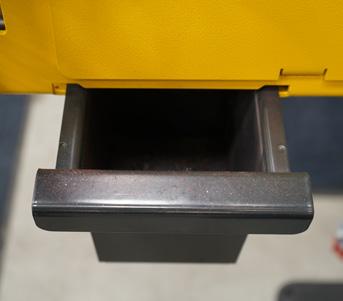

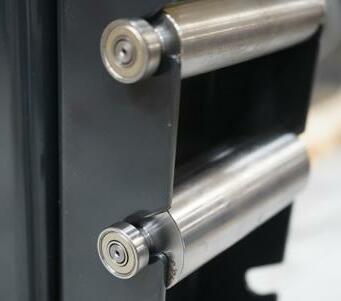
HEAVY DUTY MOTOR
DUST COLLECTOR
Technical Specifications
The RVD 220/6 hydraulic corner notching machine has a cutting capacity of 220mm x 6mm at a fixed angle of 90 Degrees.
Perfect for notching the corners on box and pan blanks, ready for folding.
RVD 220/6 Corner Notcher
Technical Specifications
RVD 220/6
• Rigid head and GS500 cast iron workbench with conical grooves for optimal adherence of the squares
• Cut can start from top of blades or from the base
• Manual adjustment of gap between blades from 1 to 6mm
• Set of goniometric squares
Machine Features Optional Equipment

• Stainless steel cutting blades

Morgan Rushworth Corner Notcher
HFA 220/6
The HFA and HVA hydraulic corner notching machines have a cutting capacity of 220mm x 6mm or 220250mm x 8-10mm at a fixed angle of 90 Degrees.
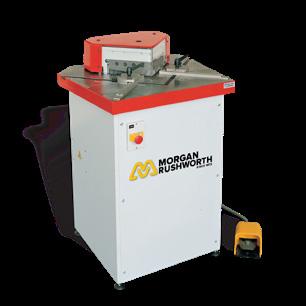

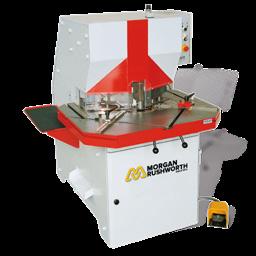
With a rigid head and GS500 cast iron workbench, these corner notchers are designed for a long working life.
HVA 220/6
HVA 250/10
Machine Features
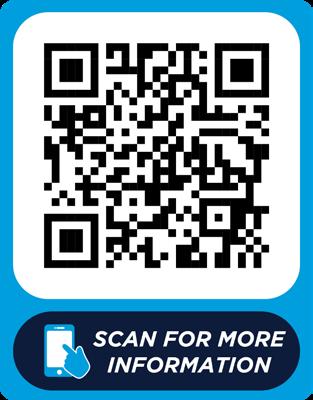
• Rigid head and GS500 cast iron workbench with conical grooves for optimal adherence of the squares.
• Cut can start from top of blades or from the base.
• Automatic adjustment of gap between blades from 1 to 6mm/8mm (patented).
• Set of goniometric squares.
Optional Equipment
• Stainless steel cutting blades
Technical Specifications
The Curvassi PPM 114 Tube round pipe finishing machine is the perfect choice for finishing and polishing round, oval and elliptical tubes. It can be used with up to 114 Ø mm wide pipes to effortlessly polish them to a high shine.
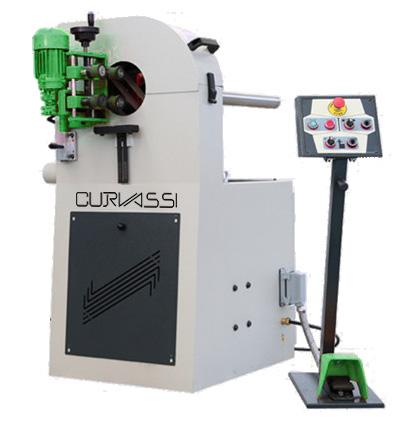
The PPM 114’s planetary system enables the work without rotating the tube, delivering the best results on bent and curved tubes as well.
The auto feeding system transports straight tubes safely and automatically through the finishing station, enabling a consistent and high productive finishing quality.
PPM 114 Tube
Polishing Machine
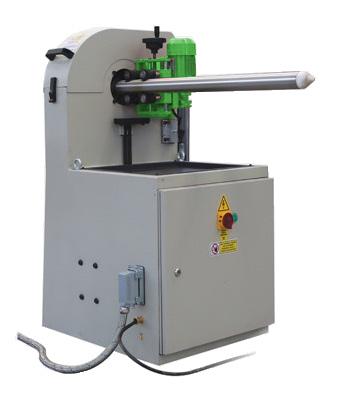
Technical Specifications
Rear View
Machine Features
• Automatic feeding system, allows for minimal operator interaction
• 2 sets of abrasive belts included as standard
• Manual pipe clamping adjustment
• Fixing attachment for motor
• Opening cover for changing of belts, cleaning and maintenance
• Holder for manual feeding
• Can polish bent pipes and tubes at up to 180˚ (angle)
• No need to turn the material on the auto feeder system
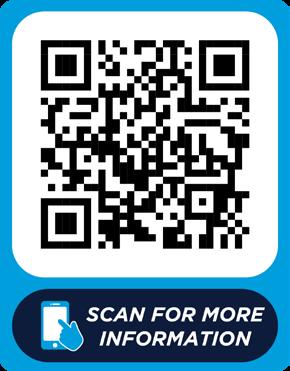