
11 minute read
Resource-efficient business
New ideas reduce energy consumption Climate-smart raw material Sustainable transport Our portfolio Culture and colleagues Resource-efficient business
One of Setra’s core sustainability goals is to reduce energy consumption. The plant in Heby is busy hunting down leakages, reviewing diesel use and switching to LED bulbs. In 2019, employees managed to cut electricity consumption by a whole 4.5%.
IT IS MONDAY morning and at Setra Heby a new and hectic week as begun. As Mill Manager Jan-Erik Johansson-Vik and his right-hand man Olle Johansson tour the plant, they are quick to pick up on any new ideas.
“With motivated and committed employees, there is never any lack of suggestions for improvements. Often, the bottleneck ends up being at management level,” states Jan-Erik Johansson-Vik humbly. Before he was recruited by Setra in autumn 2017, he ran a consultancy firm specialising in Lean, constant improvements and organisational development. Now he uses his expertise to fine-tune production within Setra.
“Our approach involves the senior managers being part of daily operations. We need to be experts in listening, asking the right questions and understanding what it takes to run this plant even more smartly,” he asserts.
Much of that work boils down to measuring and cutting electricity consumption per cubic metre of sawn timber produced.
On the right path The forest industry as a whole set a target of reducing electricity consumption by 20% between the years 2010 and 2020. This is a target that Setra also signed up to and is well on the way to meeting.
“Here at Heby, we’re currently conducting a major energy survey. This includes breaking down electricity consumption into smaller units and measuring what draws power in the different departments,” explains Olle Johansson.
The main challenge lies in the kiln drying department, where the ambition is to optimise kilowatthours by making the drying process more efficient. “Drying the timber is the most energy-intensive process in the whole mill, but we’ve changed the control system and are conducting rolling maintenance work to reduce heat leakage,” explains Jan-Erik Johansson-Vik.
Alongside the large-scale investments, employees at Setra Heby have also overhauled the lighting, with LED bulbs replacing incandescent bulbs in both the office and the large warehouse on site.
Fuel-efficient driving However, the focus is not just on electricity use. Other measures are also under consideration, not least cuts in diesel consumption. One way is to coordinate the warehouses to make the forklift trucks’ journeys shorter. Another is to provide training in eco-driving for improved fuel efficiency, and to gradually switch to more energy-efficient vehicles. Some ideas come out of the daily briefings, at which each department reports on the status of production and any non-compliances and disruptions. “The key is to identify and eliminate our noncompliances as quickly as possible, so that we can design out everything that doesn’t create value. There is a great deal to be gained, for example, by repairing things before they break down. It’s an effective way to avoid production stoppages,” says Jan-Erik. He stresses that success breeds success. New working practices and greater flexibility within the organisation have gone hand-in-hand with both energy savings and increases in productivity.
“When the employees see that they can have some influence over the details, their commitment improves. More ideas are being generated than we have time to implement, and we also make sure that we exchange experience with our other units.”
Jan-Erik Johansson-Vik, Mill Manager Setra Heby
We work systematically to improve the efficiency of our flows, make maximum use of the raw material and reduce the environmental impact of Setra’s business.
Our opportunities and challenges
The main environmental impact from the sawmills relates to energy use, noise and emissions to air from internal transport and biofuel boilers. Many stages of the sawmill process are heavily reliant on electricity, but there is scope for improvement. We can make our production more efficient and reduce its environmental impact through improved working practices and smart investments.
Another major opportunity for Setra is that the bark, chips and sawdust generated during manufacture can be used as biofuel in our own boilers or to benefit the local community. We have energy partnerships in place in several locations, whereby surplus energy is used to heat premises and homes nearby.
Governance
Climate and the environment are an important focus area in Setra’s sustainability policy, which puts aspects such as resource efficiency, energy consumption and climate impact front and centre. Setra’s sawmills and processing units are certified according to the environmental management standard ISO 14001.
Our operations require an environmental permit and are subject to extensive environmental legislation.
How we work
Supply Chain keeps things rolling 2019 saw the creation of a new department – Supply Chain – whose role is to plan and guide operations within the value chain from raw material to delivery of finished goods as efficiently as possible. Supply Chain ensures that each sawmill receives the right amount and quality of timber to manufacture their product mix. They check that customers receive the right goods on time, that we have the right volumes in stock and that our portfolio is in line with customer demand.
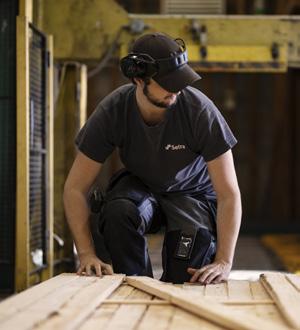
All production centred on the customer Setra’s units plan their production to create flows that are as efficient as possible from the customers’ perspective. This approach requires the production organisation to always improve their working practices, informed by the needs of the customers.
Implementation of this approach across the whole organisation has been ramped up over the past two years. We are already seeing improved results due to faster and clearer management of non-compliances. At the start of every new working day/shift, a status update or briefing is held, addressing safety, quality, delivery and efficiency. All the units have now been trained in this way of working.
Over the longer term, there are several potential benefits from a sustainability perspective: less stock and shorter lead times, which means increased customer satisfaction and reductions in quality damage, for example from blue stain.
Work to reduce stoppages Maximising availability – the time that our sawmills and processing units run without interruption – is clearly linked to efficiency. Fewer stoppages lead to higher availability and higher production, which in turn results in lower energy consumption per produced volume. It also means that employees need to spend less time on operational disruptions and emergency maintenance, jobs that can be risky. To understand what lies behind a production stoppage, we break down non-compliances into their root causes and work on solutions to prevent a repeat of the problems. Our experience shows that production stoppages due to faults in machinery and equipment or existing working practices can be improved. The starting point is to first ensure that tasks are being done in the best way possible, before we replace equipment. Another element of this work is to exchange experience between the units and ensure that everyone follows the working practices that have proven to work best.
Software for visualising stoppage time measurements was tested in 2019 and will be introduced at all units in 2020. The aim of the software is to facilitate continued work on non-compliances by clarifying the cause of the stoppage and so improving availability. We are also working on reducing downtime during
Fuel consumption within Setra has fallen by 11% between the years 2010 and 2020. -11%
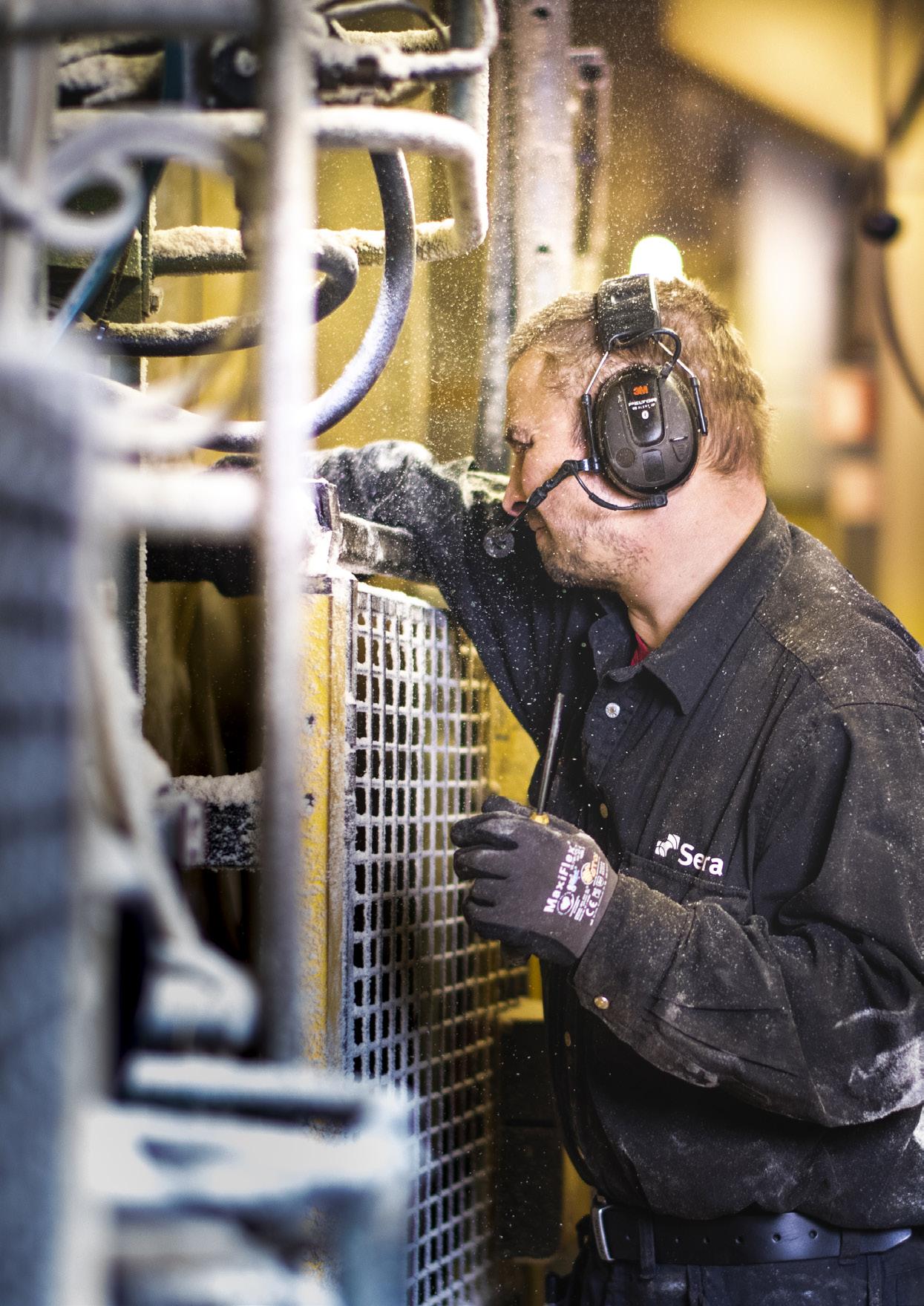
retooling and making maintenance more efficient by involving operators in the care of the equipment, giving the maintenance mechanics more time for preventive measures.
The whole log is used Making use of the whole log comes naturally to Setra, due to its importance for both profitability and sustainability. We strive to attain a high saw yield, i.e. a high volume of sawn product in relation to the volume of incoming timber raw material. The saw yield is affected by the dimensions of the log, the sawing technology and the choice of sawing the log into planks or boards depending on the economic value of the end products. In 2019, the saw yield came in at 49.5%, which is the same as in 2018.
The residual material generated by our production is used as cellulose chips, biofuel or animal bedding. The quality of the bioproducts is important; they are an important raw material or fuel in the customer’s processes.
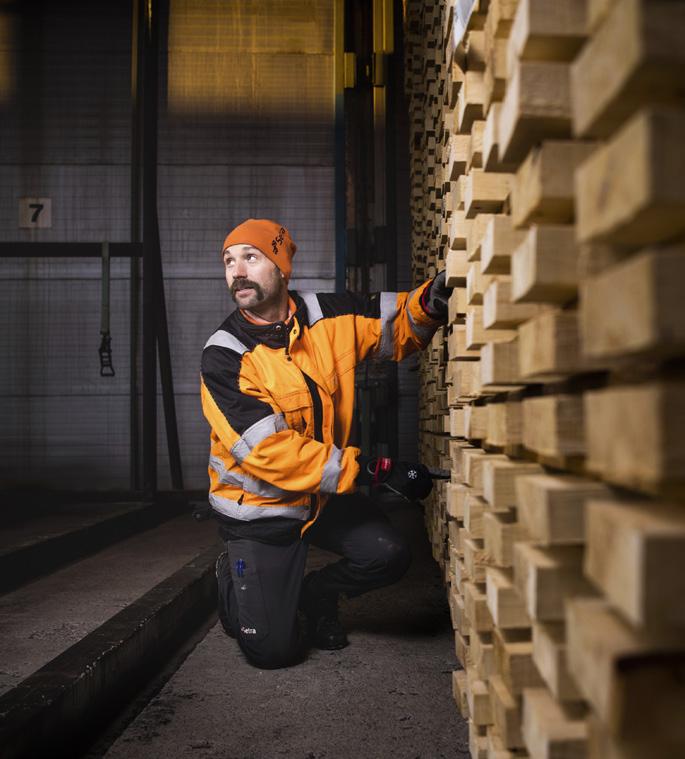
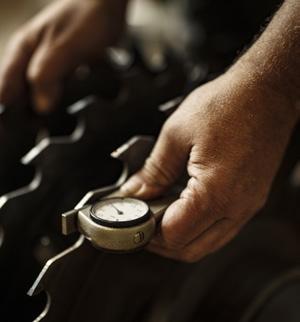
Goals for cutting energy consumption Many elements of the sawmill process require large amounts of energy, making reductions in consumption a priority issue. Setra’s overarching goal is to cut electricity consumption by 20% and fuel consumption by 15% per cubic metre of sawn timber between 2010 and 2020. Electricity consumption is steadily falling at our units, having already been brought down 10%. We are conducting energy-saving measures, while also working to improve availability and thus productivity. This will lead to a reduction in specific emissions, since we report our electricity consumption in relation to the volume produced in cubic metres. However, electricity consumption was slightly higher in 2019 than in the previous year. At a couple of units, we had problems achieving our planned productivity levels over the course of the year, in part due to a shortage of timber and sawing of fire-damaged timber. This has had a negative impact on our key indicators.
Fuel consumption has fallen by 11% since 2010, which is good news. We see this as a sign that, despite reduced production levels and high stocks, we have managed to make our forklift use more efficient.
Setra’s total energy consumption amounted to 651 GWh in 2019. Thermal energy accounted for 78%, electrical energy just under 18% and fuel consumption a little over 4%.
Energy survey reveals opportunities Setra is conducting systematic work on surveying our energy consumption, in order to identify potential savings. We are subject to the Swedish Act on Energy Audits in Large Enterprises (EKL), and since 2016 we have surveyed consumption at all the production units except one, although this is expected to be completed in the first quarter of 2020. The results give an indication of the measures with the greatest potential impact in terms of energy savings and are reported to the Swedish Energy Agency. Our conclusion is that the greatest potential lies in improving the efficiency of kiln drying the timber. The drying process accounts for 50% of the company’s electricity consumption and 95% of our thermal energy consumption. A report drawn up at Kastet sawmill in 2019 outlines concrete measures that could give us the capacity to dry significantly more timber of the same quality for the same or even lower energy consumption. The conclusions from the report will be applied at all our units.
Other savings could potentially be made by investing in new, energy-efficient equipment and developing new working practices and procedures. In 2019, Setra decided to invest in a more modern dryer in Hasselfors and a new saw line in Nyby, all of which will be implemented in 2020. We are continuing to replace light sources with LED lighting and systems that run on hydraulic oil are gradually being switched to electric power. Other ongoing projects include installing occupancy sensors to light fittings, reviewing the maintenance temperature in our premises and extending eco-driving training.
Renewable energy and energy partnerships Over 98% of Setra’s thermal energy is produced using renewable fuel. Bark and sawdust from our own production is combusted in boilers and the heat is used in the drying kilns. In several locations, we also have energy partnerships with the local community. Malå, Gävle and Skinnskatteberg use biofuel from Setra in their district heating boilers, with some of the generated energy then supplied back to our industrial plants.
In Nyby we produce district heating for the residents of nearby Björklinge using our own boiler. The breakdown of the biofuel boiler in Nyby meant, however, that we were forced to burn fossil oil in the back-up boiler for a few weeks of 2019. Since 2018, Setra has purchased ecolabelled electricity produced using hydro power, wind power and bioenergy.
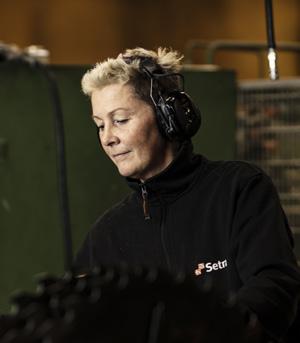
Reduced emissions from internal transport Setra’s forklift trucks mainly run on diesel, with the exception of those at the unit in Färila, for which we use HVO. As the result of a new procurement drive, all the forklifts will be replaced with newer models with better environmental performance over the course of 2020. Setra has also tested electric forklifts and concluded that we are well placed to increase their use in the future. Electrically powered forklifts are used indoors at the new crosslam factory in Långshyttan.
Noise Disruptive noise is always a priority issue when making new investments and operational changes. Noise assessments enable us to determine how a new operation will affect local residents and how the plant should be designed to avoid unnecessary disruption. 29
Energy consumption 2019 Total consumption amounted to 650,704 MWh
499,492 MWh Bioenergy district heating or own boiler
18,527 MWh Internal transport (diesel)
9,050 MWh Internal transport (biodiesel)
115,274 MWh Electrical energy
8,361 MWh Heating oil district heating or own boiler
Electricity consumption 2010–2019
(kWh/m 3 sawn timber)*
75
70
71.1
65
60
55
50
2010 66.7
2016 63.1
2017 62.4
2018 63.7
2019 Targets 2020 56.9 kWh/m 3 (-20% compared with 2010)
Setra’s electricity consumption has been cut by 10% since 2010. However, consumption rose slightly in 2019, due to productivity not reaching planned levels at a couple of units.
Diesel consumption 2010–2019
(kWh/m 3 sawn timber)*
18
16
14
17.6
15.9
15.1 16.0
12
15.7
Targets 2020 15.0 kWh/m 3 (-15% compared with 2010)
10
20192018201720162010 Diesel consumption has fallen by 11% since 2010, thanks to more efficient driving.