
9 minute read
Coluna: Lubrificantes
Henri Strasser
Lubrificante de Matriz – 16 Resolvendo problemas com lubrificante Premium
Advertisement
Para ilustrar a incrível capacidade de solução de problemas do lubrificante de matrizes Premium vamos mostrar alguns casos que só puderam ser realizados com a sua aplicação. Nada melhor do que mostrar como e devido a que problema ele foi criado. E não foi como “de matriz”.
A origem do lubrificante de matrizes está profundamente atrelada à invenção da lâmpada incandescente de Thomas Edison que depositou a 1ª patente da lâmpada incandescente em 1882 com filamento de bambu carbonizado, que, apesar de se tornar incandescente com a passagem de uma corrente elétrica, era muito frágil. Edison pesquisou materiais para o filamento e concluiu que o ideal seria um filamento de tungstênio, material extremamente resistente ao calor. Porém ele precisava que o filamento tivesse apenas algumas frações de milímetro de diâmetro para que pequenas intensidades de corrente fossem capazes de tornar o filamento incandescente e produzir luz. Infelizmente este material também é extremamente duro e na época estava disponível em arames de grande diâmetro e precisaria ser trefilado para uso na lâmpada. Porém, ao invés de ter o seu diâmetro reduzido, a fieira de trefilação é que aumentava de diâmetro!
Então Edison encomendou uma solução para o problema da trefilação do tungstênio ao Dr. Edward Goodrich Acheson. Ciente da extrema severidade do processo, Acheson criou o DAG® (Defloculated Acheson Graphite) constituído de um grafite sintético (artificial) de altíssima pureza e granulometria ao redor de 1μm depois de moído, que ele obteve depois da grafitização completa de carvão vegetal. Em seguida ele dispersou este grafite em água com a ajuda de um extrato de trigo torrado. Não há registros de onde ele tirou a ideia do sistema de dispersão das partículas de grafite em água, mas foi perfeito, com uma temperatura de molhamento (formação de camada) em altíssima temperatura e uma cobertura excepcional. As partículas de grafite aderiam ao arame incandescente e formavam um filme seco e homogêneo de alguns micra. O grafite aderido ao arame entra junto com ele na fieira, permite a redução de diâmetro protegendo a fieira, tornando possível a trefilação do tungstênio e a conclusão do invento de Edison com o depósito da patente definitiva em 1907. Enquanto se produziu filamentos de tungstênio no mundo, este produto foi usado na sua fórmula original.
Esse produto e seus derivados foram a base da empresa Acheson Colloids, criada por Edward G. Acheson em 1908. Estes produtos se mostraram adequados para operações de processos de conformação de metais a quente incluindo o forjamento, em substituição a óleos, asfaltos, graxas, sais, serragem, pós de grafite e outros materiais exóticos. Inicialmente, o sistema de aplicação utilizado foi o mesmo da trefilação do tungstênio de Edison: um sistema de recirculação usado normalmente na aplicação de fluido refrigerante em usinagem. Um tanque de armazenagem e uma bomba que bombeia o líquido para o ponto de uso. Outra bomba recirculava o lubrificante escorrido para o tanque de trabalho. Este sistema ficou conhecido como “flooding” (inundação) e ainda está em pleno uso nos dias de hoje. Interessantemente, o lubrificante de matrizes Premium tem uma imunidade bastante
Figura . Thomas Alba Edison, inventor da lâmpada incandescente, depositou a 1ª patente em 1882
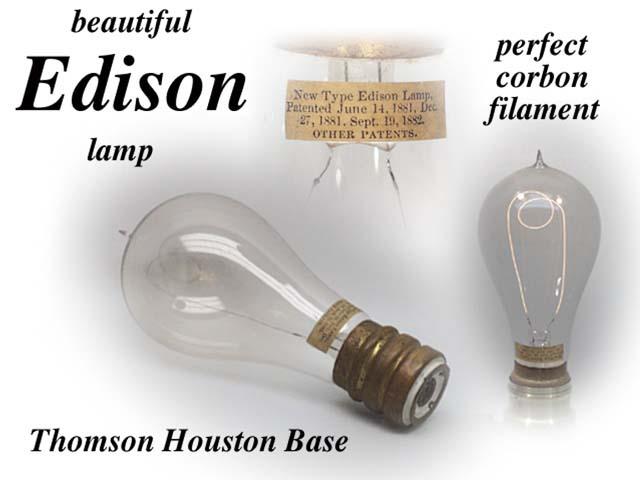
Henri Strasser
conveniente aos contaminantes de um banho de recirculação de “flooding”, como os óleos lubrificantes das máquinas, carepas, óxidos e os restos de lubrificantes, e que não afetam demasiadamente a estabilidade das partículas de grafite, ao contrário dos grafites naturais que são fortemente afetados pelos contaminantes.
Pode-se dizer que o lubrificante de grafite sintético se adequou perfeitamente aos sistemas mais primitivos até os modernos sistemas de pulverização de atomização externa. A boa estabilidade da dispersão de grafite sintético mesmo em situação diluída garantia um bom desempenho do banho de recirculação.
Inicialmente a única referência de desempenho é que havia, sem dúvida, uma enorme diferença entre usar ou não usar o lubrificante.
Por exemplo, num processo em que, tradicionalmente, não se usava lubrificante nenhum, um forjamento em martelo de um alicate universal, a vida de matriz, de 2.500 peças, passou a 35.000 com o lubrificante Premium.
Vida útil das ferramentas, matrizes e punções
Onde havia o monitoramento da força de prensagem nota-se uma redução considerável, garantindo ao equipamento uma melhor preservação. O motivo é o baixo coeficiente de atrito da camada lubrificante que possibilita um melhor fluxo metálico e um alívio das tensões dentro do fluxo. A consequência é um fácil enchimento da gravura que por sua vez possibilita uma redução do peso do billet ou do tarugo e um aumento de vida de ferramentas.
O baixo coeficiente de atrito ainda proporciona um excelente acabamento superficial das peças forjadas e uma cópia fiel de inscrições e marcas nas peças.
Forjamento a morno
No processo de forjamento a morno com temperaturas do billet abaixo de 900⁰C a tendência de oxidação do aço aquecido é bastante reduzido, possibilitando peças forjadas com menor sobre-metal e necessidade de usinagem reduzida, conhecido como “near net” ou “net shape forging”. Nesse processo também é utilizado o lubrificante de grafite Premium como lubrificante de matriz e como billet coating, produzindo um invólucro impermeável sobre os tarugos que resiste a alta temperatura para evitar/reduzir a formação de carepa garantindo os melhores resultados.
A peça grande demais para a prensa
Há cerca de 40 anos um cliente que operava uma prensa de forjamento a quente horizontal de alta velocidade (60 a 100 peças/ minuto) recebeu um pedido de uma peça que era um pouco grande demais para a prensa e a peça não era totalmente preenchida. O projeto da prensa não previa nenhuma lubrificação de matriz já que o tempo disponível para isso, com menos de 1 segundo por peça, era praticamente inexistente. A prensa previa uma refrigeração através de jorros de água de grande calibre aplicados continuamente no forjamento. Um dos técnicos envolvidos teve a ideia de aditivar a água de refrigeração com um lubrificante de matrizes Premium disponível e com apenas 0,4% de grafite na água de refrigeração a


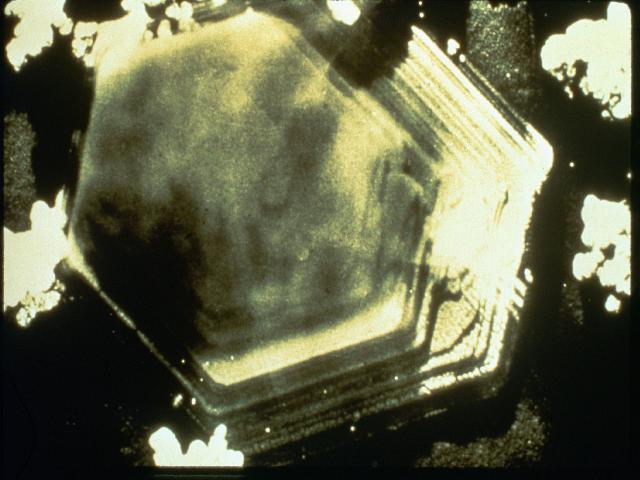
Figura 2. Dr. Edward Goodrich Acheson que tornou possível a trefilação do filamento de tungstênio com a sua invenção, o DAG®.
Henri Strasser
peça era formada corretamente. Aplicando a mesma solução em peças menores constatou-se uma elevação da vida de matriz.
Há alguns anos, uma tentativa de usar um lubrificante de grafite natural de granulometria acima de 4μm mostrou que um resultado simular só seria possível com quantidades 3x maiores de grafite e enormes problemas com a manutenção do banho de lubrificante, entupimento de bicos e acúmulo de “build up” nos mecanismos e nas ferramentas.
Temperaturas de superfície de matriz ao redor de 400ºC
Prensa transfer (30 batidas/minuto) a quente, frações de segundo para a lubrificação, ocorrem regiões com temperaturas superficiais de matriz perto de 400ºC com problemas de baixa vida útil, faltas de preenchimento e dificuldades de extração. Se não houver tempo disponível para a refrigeração das matrizes para que a temperatura chegue na temperatura de molhamento do lubrificante, ele terá que formar camada naquela temperatura alta.
Apenas um lubrificante de matrizes Premium é capaz dessa façanha.
Redução do tempo de lubrificação de matrizes para aumento de produtividade
Prensa para forjamento de virabrequins com lubrificação de matrizes automático usando um lubrificante de matriz com grafite natural com uma temperatura de molhamento máxima de 270ºC. Temperaturas de superfície das matrizes acima de 400ºC levaram a tempos de aplicação extremamente longos para que a temperatura fosse reduzida a ponto de tornar possível a formação de camada. Com um lubrificante de matrizes Premium o tempo de aplicação pôde ser reduzido à metade, tornando possível o desejado aumento de produtividade.
Custo vs. Benefícios
Em empresas onde os argumentos econômicos (custo) conseguiam se sobrepor aos argumentos técnicos (benefícios) os forjadores precisaram se adaptar às novas condições oferecidas pelos lubrificantes de grafite natural. Pouco a pouco os lubrificantes de grafite natural foram conquistando processos mais exigentes e prensas maiores.
E, devido a unidades de aquecimento antigas, máquinas de forjaria com necessidade de recuperação de energia, havia tempo no ciclo de forjamento, para se aplicar o lubrificante de grafite natural e refrigerar as matrizes.
Em todos estes processos já havia se instalado a prática da aplicação de lubrificante através de sistemas de pulverização manuais, o que, sem dúvida era muito propício ao grafite natural.
Novos métodos de planejamento de produção reduziram os estoques o que levou ao forjamento de lotes menores, em geral, bastante abaixo da vida útil das ferramentas o que mascarou a verdadeira vida útil, um dos principais argumentos de uso de um lubrificante de grafite sintético. Também tem que ser considerado que, os usuários, uma vez acostumados ao desempenho de um lubrificante qualquer tornam difícil de provar porque um lubrificante de matrizes Premium é tão bom e merece ser pago tão caro. O custo é claro e pode ser consultado na nota fiscal, já o benefício é mais difícil de justificar e encontrar quem se responsabilize. Por isso, as chances de sucesso do lubrificante de matriz Premium estão onde realmente pelo menos um dos seus predicados for decisivo, sine qua non para o processo.
Benefícios do uso de lubrificantes de grafite Premium
• Menor consumo de lubrificante (com menos faça mais) • Vidas mais longas de ferramental, necessidades de reparação são postergadas. • Desempenhos excelentes do processo, maior produtividade. • Qualidade ótima das peças forjadas. Excelente capacidade de cópia da gravura. • Baixos coeficientes de atrito das camadas permitem ótimo fluxo metálico e rápido preenchimento da gravura da matriz • Economia de matéria prima devido ao melhor enchimento. • Os baixos coeficientes de atrito permitem baixas forças de prensagem poupando o equipamento de conformação
Conclusão
O lubrificante inventado há 115 anos para viabilizar a lâmpada incandescente já possuía os atributos necessários e suficientes para atender forjamentos atuais de alta velocidade de peças near net e net shape de hoje em processos de forjamento a quente e a morno. A capacidade de formação de camada a alta temperatura e a grande velocidade de formação são atributos que tornam o lubrificante de matriz interessante para operações com peças e máquinas grandes com enormes vantagens.
Normalmente o uso de lubrificante de matriz Premium, para ser usado no lugar de outros lubrificantes não requer nenhuma modificação/adaptação do sistema de lubrificação, apenas pequenos ajustes reversíveis. O impressionante é que o lubrificante de matriz Premium também pode ser aplicado por meios realmente primitivos tais como pincéis, bonecas de pano e vassouras.
Henri Strasser é engenheiro e sócio-diretor na Strasser Consultoria de Projetos Ltda. Ele pode ser contatado em: henristrasser@uol.com.br.