
10 minute read
Influência do Uso de Anéis de Contração no Encarcaçamento de Matrizes de Extrusão a Frio
from IH + FORGE jun 2022
by SF Editora
Taxas de Resfriamento Otimizadas de Aços Microligados (Parte II)
James Miller, John Walters – Scientific Forming Technologies Corporation (SFTC); Columbus, Ohio, EUA; Chester Van Tyne – Colorado School of Mines; Golden, Colorado, EUA
Advertisement
Aprimeira parte deste artigo foi publicada na edição de Abril 2020 da FORGE Brasil. Ele deu uma visão geral de um desafio para forjadores de aços microligados – resfriamento controlado! Agora que o problema do resfriamento controlado de microligas forjadas foi modelado e solucionado, outros desafios ficam claros e presentes para a indústria de forjamento. Mas antes de contabilizar essas oportunidades, vamos apresentar os dados e as soluções para o problema em questão – resfriamento controlado de aços microligados.
Coeficientes de Transferência de Calor
Os processos de transferência de calor transiente podem ser facilmente simulados usando modelos de elementos finitos (FEMs – finite element models) implícitos e não lineares para prever a resposta térmica de uma peça ao aquecimento e resfriamento. Tais modelos representam um uso rotineiro de uma tecnologia muito madura. Na conclusão de uma simulação de forjamento a quente, a temperatura de cada nó na peça de trabalho é conhecida. A taxa de resfriamento pós-forjamento pode ser prevista por simulação se o processo de resfriamento for conhecido
Para um forjamento de aço microligado, o resfriamento controlado por ar forçado é típico. Forjados a quente são resfriados à medida que são transportados em um transportador blindado através da(s) zona(s) de resfriamento com um ou mais ventiladores de resfriamento. Não é prático medir experimentalmente a taxa de resfriamento em uma região subsuperficial desses forjados. No entanto, um modelo FEM pode facilmente prever essas taxas de resfriamento se o coeficiente de transferência de calor (HTC heat-transfer coefficient) ou o coeficiente de convecção for conhecido.
Valores típicos de HTC estão disponíveis na literatura, embora sejam valores aproximados na melhor das hipóteses. Eles são normalmente estimados na ordem de grandeza mais próxima. Também é incomum ver qualquer dependência de temperatura incluída na literatura. Assim, os dados públicos são razoáveis para uma estimativa inicial, mas não para um modelo preciso. Para obter um modelo preciso, o forjador precisa identificar os coeficientes de transferência de calor para resfriamento contínuo.
Os códigos de dinâmica de fluidos computacional (CFD computational fluid dynamics) são muito sofisticados e podem prever a resposta térmica em sistemas altamente transitórios. O CFD é maduro, mas extremamente tedioso e demorado. Usar o CFD para modelar uma aplicação simples de resfriamento por ventilador é provavelmente excessivo, com um alto custo de tempo e dados.
Figura 5. Forjado do cubo da roda e colocação do termopar
Uma abordagem prática de engenharia para extrair o coeficiente de convecção da superfície de um processo real envolve uma mistura de dados experimentais e simulações. Um experimento de resfriamento controlado é realizado com termopares embutidos próximos à superfície de uma peça de trabalho. A saída do experimento é um conjunto de dados de temperatura versus tempo para cada termopar. Uma estimativa aproximada para o HTC é fornecida por um modelo de computador inicial, que é executado posteriormente para corresponder ao experimento. O rastreamento de ponto é usado para extrair uma curva de temperatura versus tempo para cada termopar.
Após a conclusão do modelo, as curvas são comparadas e as diferenças reconciliadas. Usando uma rotina de otimização, uma simulação subsequente é executada com os dados HTC atualizados, que são uma função de temperatura e localização. Após várias iterações, a solução converge quando a previsão de tempo-temperatura do modelo corresponde ao experimento. Este é um modelo empírico, que é prático em um ambiente de forjaria.
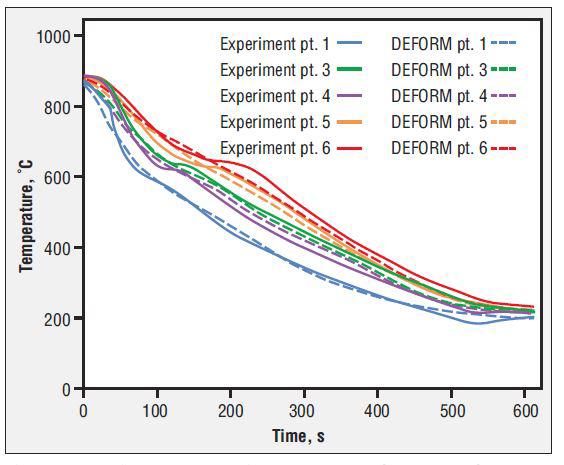
Figura 7. Valores previstos e experimentais dos coeficientes de transferência de calor
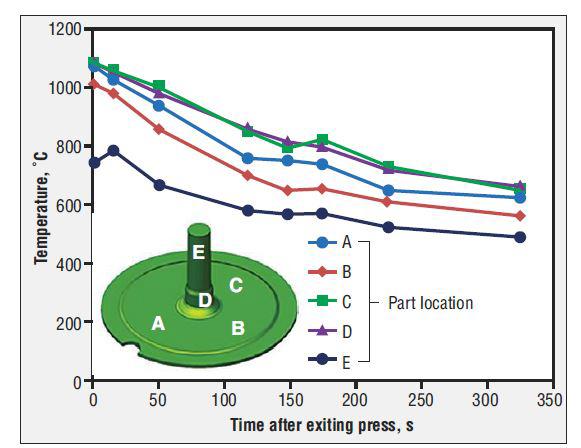
Figura 8. Dados do pirômetro pós-forjamento em locais específicos de peças
Figura 9. Taxas de resfriamento regionais de peças
Zona 1
Mais rápido para esfriar
Zona 2
Mais lento para esfriar
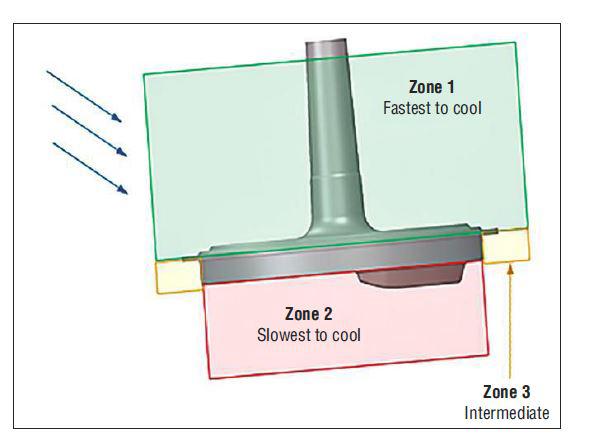
Zona 3
Intermediário
Experimentação
A Jernberg Industries financiou um trabalho experimental para determinar esses HTCs. Um forjado de cubo de roda automotivo feito de aço microligado foi equipado com seis termopares em locais específicos do subsolo. Uma foto do forjado e dos termopares é mostrada na Figura 5. O forjado foi então aquecido em um forno a gás a uma temperatura logo abaixo de 1093˚C, conforme mostrado na Figura 6. Em seguida, foi resfriado por um único ventilador semelhantes aos ventiladores usados na linha de produção real.
Os dados foram processados pela SFTC utilizando o módulo HTC inverso do sistema DEFORM. Os resultados deste trabalho foram HTCs de superfície em função da temperatura. Coeficientes únicos foram definidos para cada uma das três regiões do forjamento. As taxas de resfriamento foram associadas a porções ou zonas do forjamento (ou seja, taxas rápidas, intermediárias e lentas). Com os dados HTC disponíveis, a SFTC criou um modelo para comparar o resultado de tempo e temperatura do modelo e do experimento. A Figura 7 compara os dois resultados em cinco locais.
A correlação foi excelente e validou os HTCs de engenharia reversa para o ventilador de amostra. A expectativa era que esses HTCs fossem adequados para prever a taxa de resfriamento de um forjamento, com um perfil de temperatura conhecido, em uma configuração de resfriamento de produção.
Simulações de Produção
As empresas simularam seus processos de forjamento a quente por décadas com excelente sucesso. Os modelos
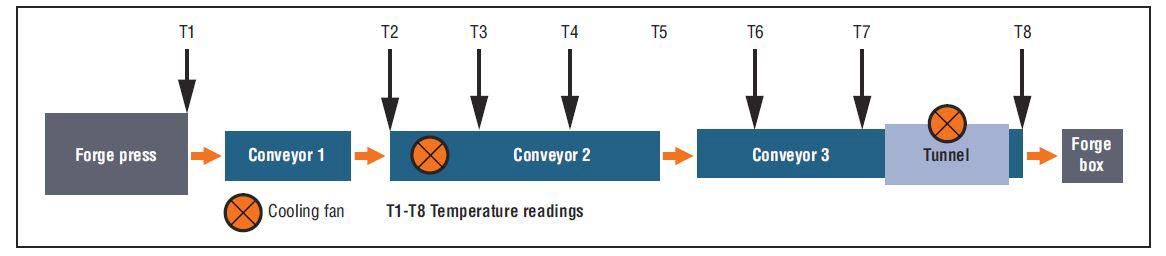
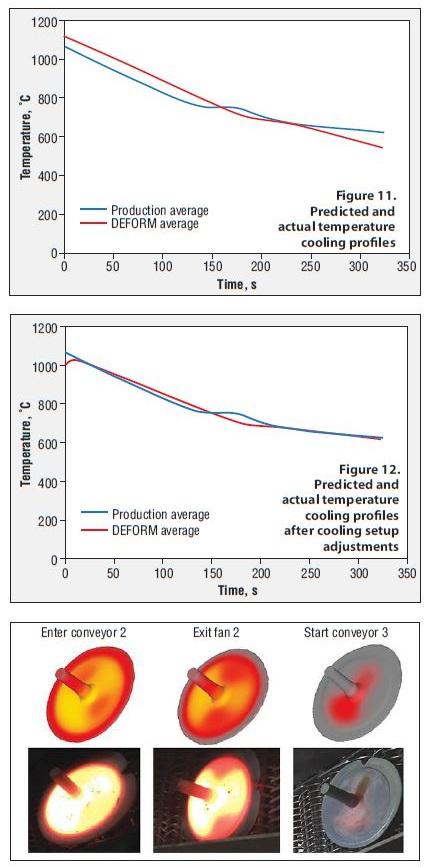
Figura 11. Perfis de resfriamento de temperatura previstos e reais
Figura 12. Perfis de resfriamento de temperatura previstos e reais após ajustes de configuração de resfriamento
Figura 13. Perfis térmicos modelados e reais em três pontos no sistema de transporte
de forjamento normalmente incluem a transferência de calor na medida em que influenciou o processo de forjamento. Simulações de forjamento envolvendo múltiplas operações levaram em conta a resposta térmica antes do forjamento, durante as transferências e quando apoiadas em ferramentas. Uma abordagem similar de simulação de múltiplas operações foi usada para modelar o processo de resfriamento pós-forja para uma das peças de produção de aço microligado da Jernberg.
Para validar a modelagem, Jernberg capturou e compilou dados de produção relacionados ao comportamento de resfriamento de peças forjadas em 15V30M. As medições do pirômetro foram feitas em cinco locais (A-E) imediatamente após o forjamento e em vários momentos ao longo do sistema de resfriamento do transportador (Fig.8). Cada ponto de dados representou a média de 10-14 medições individuais de temperatura de superfície coletadas em diferentes partes.
As simulações de resfriamento pós-forja foram executadas pela SFTC usando dados HTC do estudo anterior do ventilador. Assim como o forjamento experimental, o forjamento de produção foi assumido como tendo três zonas HTC. Essas regiões foram responsáveis por diferentes taxas de resfriamento (Fig. 9). O esquema mostrado na Figura 10 representa a configuração do transportador modelado. Nenhum ventilador estava presente nos transportadores #1 e #3. Os ventiladores foram montados na entrada do transportador nº 2 e no túnel de saída após o transportador nº 3. O esquema indica os locais ao longo do transportador (T1-T8) onde foram feitas as leituras de temperatura (Fig. 8).
Os resultados iniciais médios de resfriamento pareciam razoáveis (Fig. 11), mas havia preocupação com a inclinação da curva de resfriamento após a transformação. A inclinação representou a taxa de resfriamento, que foi o foco principal do estudo. A equipe então decidiu reavaliar a configuração e as premissas do modelo.
Diferenças de fluxo de ar foram identificadas entre a configuração do ventilador experimental e certas seções do sistema de resfriamento de produção. O julgamento de engenharia foi usado para ajustar os HTCs para as seções do transportador2 e do túnel. O modelo final de resfriamento (Fig. 12) obteve um melhor ajuste geral à média dos dados experimentais.
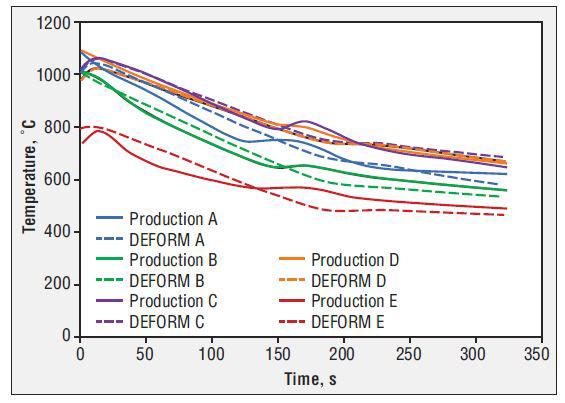
Figura 14. Comparação das temperaturas reais e simuladas em cinco locais da peça
Figura 15. As medições de dureza foram feitas em dois pontos específicos na peça de trabalho
O modelo de resfriamento final correspondeu razoavelmente às observações de produção. A Figura 13 mostra os perfis de calor no modelo e na peça de produção em três pontos ao longo do transportador. A Figura 14 compara as medições de produção com as temperaturas simuladas em cinco locais da peça. Houve um alto nível de confiança nas previsões da taxa de resfriamento. A dureza foi medida em dois locais do forjado: a haste e o centro (Fig.15). As taxas de resfriamento previstas foram extraídas dos mesmos locais no modelo de forjamento. A dureza medida e as taxas de resfriamento previstas foram então plotadas juntas no gráfico de taxa de resfriamento crítica de 15V30M da CSM (Colorado School of Mines) (Fig. 16).
Embora uma gama mais ampla de condições de processo possa divergir, o “ponto ideal” de produção correspondeu bem aos experimentos de laboratório. Tanto o estudo CSM quanto a experiência de produção de Jernberg identificaram as taxas de resfriamento necessárias para obter uma dureza ideal.


Oportunidades de Pesquisa Futuras
Este projeto é o primeiro ensaio publicado desse tipo. Melhorias futuras foram discutidas pela equipe do projeto, algumas das quais estão resumidas aqui. Desenvolvimentos adicionais permitirão que os métodos de teste sejam aplicados a uma gama mais ampla de aplicações.
Testar o HTC para várias configurações de ventilador em função da localização, temperatura e velocidade do ventilador forneceria um modelo de resfriamento pós-forjamento mais preciso. As variações podem incluir transportadores blindados versus dutos, velocidade do ventilador e velocidade média do ar ao longo do transportador. Conhecer o efeito desses fatores na taxa de resfriamento permitirá que o forjador ajuste ainda mais o resfriamento para obter microestrutura e propriedades ideais.
Desenvolver um banco de dados de dados de taxa de resfriamento versus dureza para um conjunto mais amplo de ligas é desejável. Ele pode ser acoplado a ferramentas de análise de dados para refinar a taxa de resfriamento desejada e a probabilidade de atender aos requisitos de propriedades mecânicas. Refinamento adicional pode ser possível com a inclusão da química e do fornecedor do
material.
Como leitor deste artigo, você também pode participar de projetos futuros! Entre em contato com Jim Miller da SFTC sobre o interesse de nossa empresa em melhorar continuamente seus processos para seus clientes que necessitam de aços microligados.
Os autores agradecem a Jernberg Industries por suas contribuições nos experimentos, testes de produção e relatórios de projetos envolvidos nesses esforços. Markus Knoerr, vicepresidente de engenharia da Jernberg na época, é creditado com o conceito original do projeto FIERF. A equipe também agradece à Forging Industry Education Research Foundation (FIERF) por apoiar os esforços da CSM e apoiar a transferência de tecnologia em todo o setor, pois fornece peças acessíveis e de alta qualidade para aplicações exigentes.

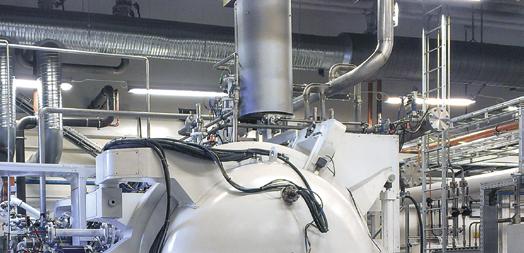

PARA MAIS INFORMAÇÕES: James Miller, John Walters – Scientific Forming Technologies Corporation (SFTC); Columbus, Ohio, EUA; Chester Van Tyne – Colorado School of Mines; Golden, Colorado, EUA O co-autor James Miller é Diretor de Vendas e Marketing e colaborador frequente do FORGE, John Walters é Vice-presidente da Scientific Forming Technologies Corp. (SFTC), Columbus, Ohio. Jim pode ser alcançado em sales@deform.com ou em +1 614-451-8330. Co-autor e colaborador frequente da FORGE, Chet van Tyne é Professor Emérito, Engenharia Metalúrgica e de Materiais, Colorado School of Mines, Golden, Colorado. Ele pode ser alcançado em cvantyne@mines.edu
PORTAL AQUECIMENTO INDUSTRIAL
Confira as mais recentes notícias do Portal Aquecimento Industrial e tenha informações sobre a indústria metalmecânica no brasil e do mundo.
The International Journal Of Thermal Processing Jan a Mar 2019
Benefícios da Sinterização a Vácuo 42
Como Cortar Custos com Datalogger 34 Tratamento Criogênico Profundo 38 Oxidação Intergranular: Castigo ou Vantagem? 46 BRASIL CONFORMAÇÃO ESTAMPAGEM &
Stamping & Forming Magazine Brazil
Revista de Corte, Estampagem e Conformação de Chapas, Arames e Tubos Maio 2019
Estudo Virtual de Processos de Conformação
17 Vendido o Maior Forno a Vácuo da América do Sul 16 Seminário de Processos de TT em Abril na Delphi, em Piracicaba (SP) 16 Seminário de Manutenção e Segurança de Fornos em Junho na Combustol Fornos, em Jundiaí (SP)
A maior e mais conceituada revista da REVISTASTÉCNICAS indústria térmica • www.sfeditora.com.br
Embalagens Metálicas: Estampabilidade Aço x Alumínio
In uência do Prensa-Chapas no Springback Otimização de Processo de Clinching em Chapas
EXPOMAFE 2019 - Destaque Expositores Estampagem & Conformação
LEIA ONLINE
Notícias | Revistas técnicas Atigos Técnicos | Colunas
Site: aquecimentoindustrial.com.br E-mail: contato@aquecimentoindustrial.com.br Fone: +55 (19) 3288-0677 ou 3288-0437