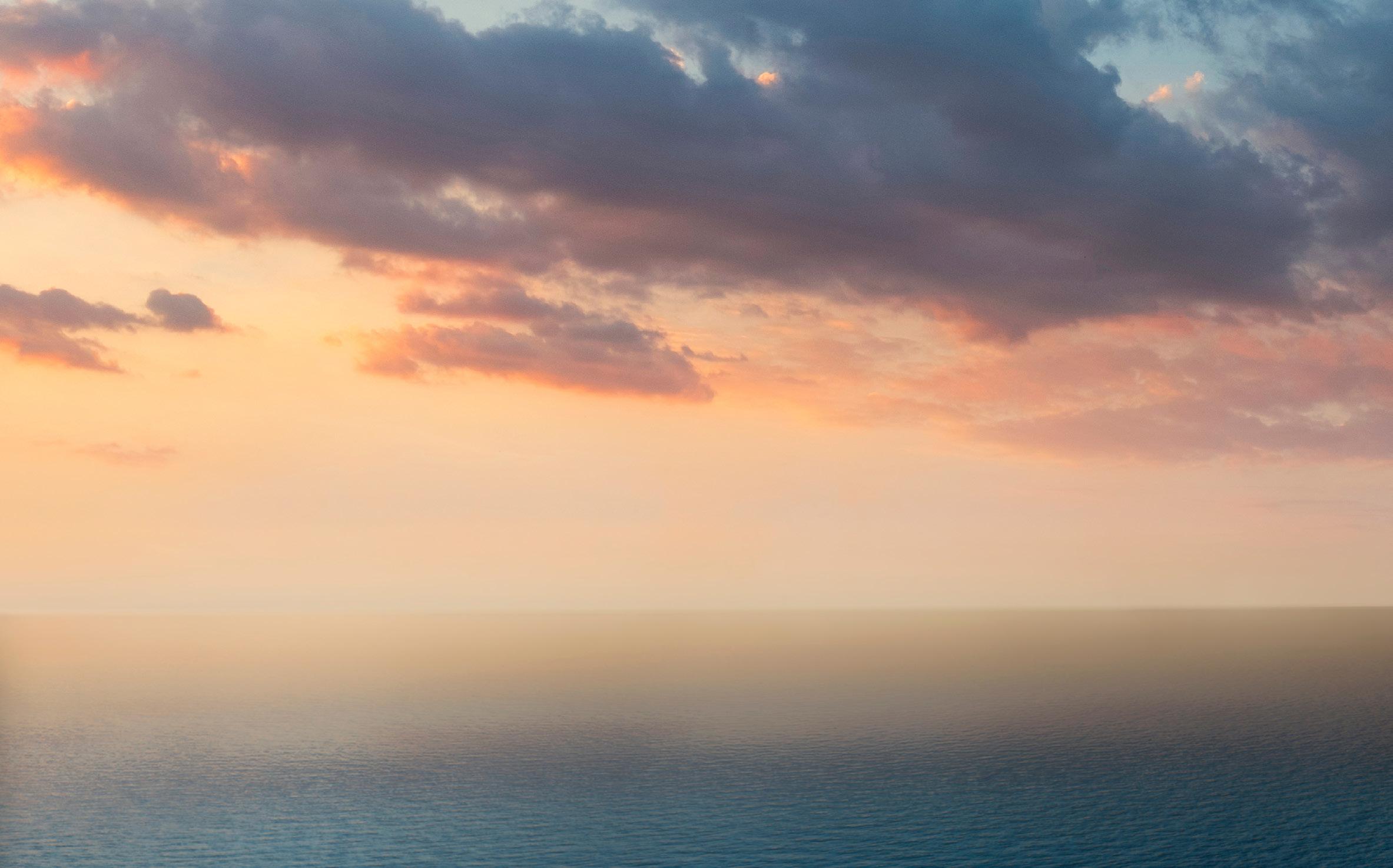
5 minute read
With High-Impact Oil Exploration Returning To the Game with a Boom, There’s Never Been a Greater Need for Technology Solutions
High-impact oil exploration has returned to the scene following a bleak 2021, which saw a relatively low success rate in discovering new oil and gas resources. In fact, it was one of the lowest on record. But this year is seeing a much higher success rate with high-impact offshore drilling returning to the game. Right now, amid an apparent unprecedented energy crisis unfolding, it makes sense that exploration, development and production (E&P) companies will be plowing forward with new projects that could pump oil for years.
Advertisement
Just this year, E&P firms discovered more than 1.7 billion barrels of oil equivalent at high-impact wells. That number is quadruple what was discovered for the entire 2021 year. At this rate, global spending in offshore oil and gas engineering, procurement and construction (EPC) is expected to total out to around $276 billion between 2022 and 2026 – a 71% increase.
While offshore production sites can be more expensive to build than onshore, they can return profits at lower prices once they are up and running. According to Reuters, the deep offshore projects could yield oil for decades and at lower breakeven costs when the rig is pumping due to the sheer scale of the vast developments.
When it comes to drilling in the oil and gas industry, there are always inherent risks, so with the expansion of offshore drilling, it is a critical mission to have effective field support, which will lead to better service execution. This translates to a need for digital alignment – a purpose for technology and a framework for the application. The benefits of technology solutions, including advanced end-to-end enterprise asset management (EAM) solutions, can ensure maximum availability, reliability, and performance in the field.
Managing maintenance remotely
Drilling offshore can present its own set of unique risks, including heavy and dangerous equipment miles from shore. Keeping rig workers safe means providing in-depth training on
equipment use and maintaining all equipment assets to ensure they are safe to work with.
To properly maintain these assets, there must be a clear picture of their historical condition, status and location. EAM solutions are critical to keeping assets operational. They provide process and intelligence for physical assets that can bring increased equipment reliability, routine preventive and predictive maintenance and efficient inventory management. Offshore workers and technicians often perform equip-
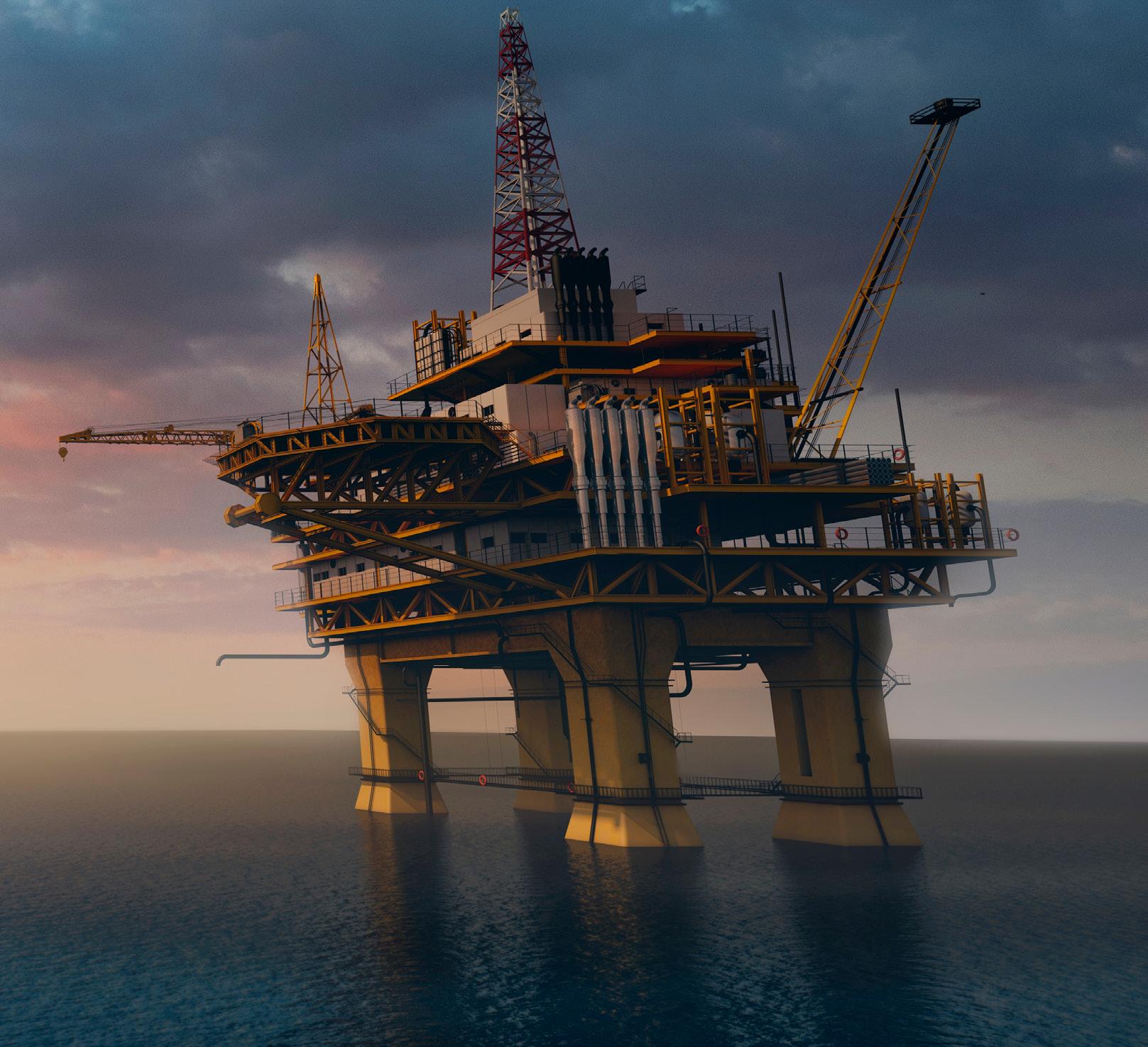
ment maintenance and repairs using hand-held devices that might not be Wi-Fi enabled, resulting in a lack of access to job-specific information. Utilizing end-to-end EAM solutions that tie field processes to equipment maintenance is a more efficient way of managing the care of assets in remote locations.
The use of EAM solutions also simplifies the execution of work orders by providing work order templates at the asset or asset category level – online or offline – for each designated job. These templates can include parts, forms, labor, direction and predicted cost and are easily configurable to reflect a rig’s current processes, allowing for successful user adoption. Not only are files and documents easily managed and attached to work orders, but managers can compare forecasted costs to actual costs, giving a clearer view of maintenance spending metrics. This lends itself to a more strategic approach to planning through data collection.
Preventive maintenance will always be a better route than reactive maintenance. When performed regularly, it improves performance, reduces downtime, provides greater visibility into projected costs, and increases service quality. EAM solutions provide process intelligence to preventive maintenance through a calendar, equipment meters, event-based schedules, and detailed work instructions. This is a critical part of business, including having a clear view of which pieces of equipment are available and where they are located. Knowing whether an asset has been properly maintained or is due for service greatly enhances the scheduling of assets – enabling strategic planning for parts and labor and facilitating compliance and reporting.
Integrating and reporting the data
Integrating data is necessary for any company going through a digital transformation, as nearly any company with field service workers must be able to transfer data in and out of their field operations management platform. Because companies often require this vital data to feed in from other locations, an EAM
Keeping rig workers safe means providing in-depth training on equipment use and maintaining all equipment assets to ensure they are safe to work with.
solution can make the data actionable. It can also make a report on any data point within the solution, which means field data from tickets, financial data from an enterprise resource planning (ERP) software and costing data from a maintenance system can be readily available. This gives O&G managers a complete view of operations and valuable insight into every critical business detail.
Supporting growth for the long haul
Working on oil rigs comes with many risks and hazards unique to offshore drilling. No O&G company can afford to run these rigs with antiquated technology. The work is too important and dangerous. Implementing an end-to-end EAM solution can ensure any and every task, including all preventive maintenance, is done in a way that ensures maximum safety, reliability and performance in the field. This approach to field support fulfills the need for digital alignment, with a framework for the application and focus of new technology that will support a safer environment for oil rig workers, ultimately leading to better service execution.
About the author: Matt Danna is the Senior Director of Product Strategy at ServiceMax and has worked in software for over 25 years. Mr. Danna’s background brings a depth of knowledge in software engineering, sales engineering, and product management. He primarily works with customers, key stakeholders, implementation managers, account executives, and developers to ensure alignment across all parties.