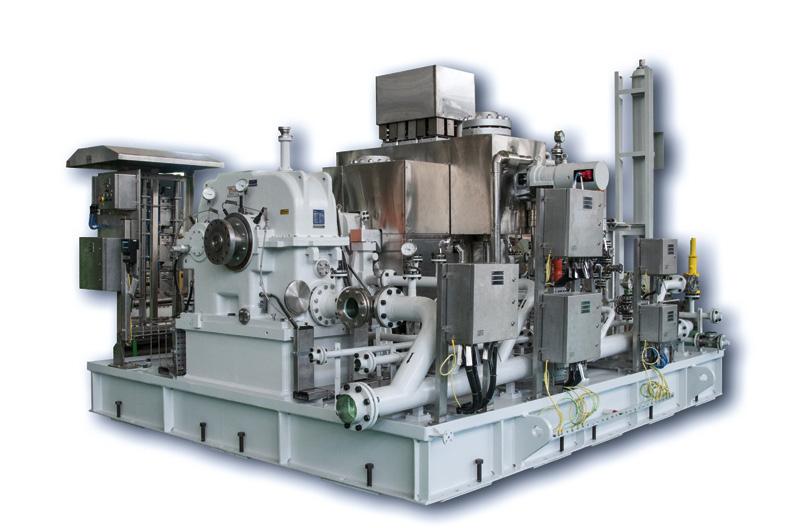
7 minute read
Addressing Efficiency Challenges Faced by the Oil and Gas Industry
By: Arun Mote
Advertisement
The global oil and gas industry is facing challenges due to modern energy processes. This is leading the industry to scout for technologies that maximize the energy efficiency of the production process. This drastically helps petroleum refineries and chemical and petrochemical plants to reduce their carbon footprint and operating costs.
In order to be competitive and constantly evolving, end-users want to achieve plant efficiency enhancement through energy-recovery technologies to reduce energy waste.
In this context, steam turbines play a vital role in achieving that goal, from driving powergeneration turbines in an old generation refinery to driving almost all rotating equipment starting from 10 kW in a modern-day refinery.
Triveni’s pre-qualification with OEMs, EPCs and consultants augmented its capabilities, starting from pre-order feed engineering to one-time supply and installation of API steam turbines. Through its innovative product portfolio and aftermarket services, it has been helping companies manage their power and drive solutions in various areas, such as petroleum refineries, petrochemicals, chemicals, fertilizers, steel, cement, process co-generation and many more, globally.
With the introduction of modular design concepts and implementation of its steam turbines, Triveni Turbines is fully equipped to meet the multiple operating scenarios of its customers and to address the challenges and ever-changing needs of tomorrow:
• Flexibility in terms of design and engineering and special capability for “made to order” turbines
• Capability to comply with stringent design codes
• All steam turbines manufactured by Triveni
Turbines are subjected to live steam trials • A large network of technical field advisors supervise the installation and commissioning of steam turbines anywhere in the world • Faster delivery period of steam turbines owing to high throughput from two world-class manufacturing facilities • Benchmark after sales and post warranty support for annual maintenance, operation and maintenance, lifetime support for spares.
Requirements of Steam and Usage of Steam Turbine in the Oil and Gas Industry
As the world is moving toward more energyefficient ways of operation, most licensors and designers of modern petroleum refineries and chemical and petrochemical plants are having to keep this in mind. As a result, steam balancing and extreme utilisation of steam becomes a key design factor.
This has put pressure on existing plants to look at their steam headers for available steam and increase utilization by replacing pressurereducing stations and dump condensers with steam turbines to save their electrical power and reduce their carbon footprint.
In the past few decades, this pushed steam turbine manufacturers to adapt to various levels of steam conditions ranging from very lowpressure steam inlets (4 Bar) to supercritical steam (140 Bar) and power ranging from 10 kW and up to 30 MW or more according to the plant size.
Triveni’s expertise in handling high-pressure and low-pressure steam helps the end-users recover energy from various steam headers by completely eliminating the pressure-reducing stations and dump condensers.
Challenges Faced by the Oil and Gas Industry
Challenge 1: High cyclic loads and the utilization of multiple pressure steam into a single steam turbine
Many chemical plants have cyclic loads by virtue of the processes involved in manufacturing the end product. Certain exothermic reactions occur in the course of chemical manufacturing that can generate steam at a lower pressure and temperature than is normally vented or dumped in a condenser since they are not generated continuously.
Triveni offers injection – condensing/injection – back-pressure steam turbines where the intermittent generation of steam can be injected into the turbine to add more flow to the low pressure (LP) section of the turbine generating more power at the terminal. Triveni’s steam turbines are equipped with new generation speed – load – extraction control electronic governing systems that can provide a seamless operation to benefit the user.
Challenge 2: Utilizing unconventional header pressures (VHP to HP and LP to Condensing)
Triveni Turbines provided one of its customers (a mid-scale petroleum refinery overseas) with energy savings by offering very high pressure (VHP) to high pressure (HP) turbine drive solutions. This saved them almost 17 MW of electrical power, an enormous power cost savings.
With these design capabilities, a steam turbine manufacturer can increase the extent of variable adaptation. By doing so, all sizes of critical equipment like process pumps, water pumps, small lube pumps, fans, blowers, air compressors and process compressors, etc. can be driven by steam, thus enhancing the saving of energy (by reducing losses during generation, transmission and utilization) and steam utilization.
Case Study 1:
Turbine Details: 4 X 1.5MWe & 4 X 2.7MWe steam turbines as per API 612 + Shell DEP (Design Engineering Practices) + AMEC FW project variations
2.7MW Steam Turbine
1.5MW Steam Turbine

Project Highlights • Steam turbines, designed, manufactured and tested as per API 612 6th edition + Shell
DEP + AMEC FW Project Variations • 4 X 1.5MWe & 4 X 2.7MWe steam turbines drive 4 No’s each combustion air blower and flue gas fans for the world’s largest reformer package • Project executed with approved deviations to complete project specifications • Turbines designed for outdoor installation with MDMT suitable for -3℃ • Steam turbine constructed in full compliance with Shell DEP / AMEC PV requirements for human factor engineering • Steam turbines constructed for a long service life of 30 years and six years of uninterrupted operation • Electrical hazard area zone 1,II C,T3 • Steam turbines, gear units, lube oil units, unit control panels and gland steam condensers in Triveni’s scope of supply
To complement the above new product portfolio, Triveni’s refurbishment arm Triveni REFURB steps up to provide an aftermarket solution for the complete range of rotating machinery across the globe. From steam turbines and compressors to the gas turbine range, we have adapted ourselves to ensure that customers find a onestop solution.
We have noticed a trend toward refurbishing turbines to meet varied parameters. They may have grown in size and scale, necessitating a change in process parameters, or it could be due to the age of the turbines.
This change in operating parameters has led to increased specific steam consumption, leading to increased cost. Triveni REFURB has positioned itself as a niche, working with customers to improve the efficiency of operations of their existing turbines without replacing the entire turbine.
With rising costs, operating turbines efficiently is necessary for cost-saving and creating a smaller carbon footprint. With age, the turbine becomes inefficient, increasing the cost of producing power. Our team works with customers to understand their current needs. We will redesign the existing turbine across all brands to meet the new parameters ensuring the customer savings by making the turbine efficient.
Our engineers study the process change requirements of the customer and redesign the existing turbine by modifying the steam flow path to the new parameters. This re-engineering process is carefully done to ensure the existing system (i.e., casing, civil foundation, lube oil system, etc.) is retained. The only modification will be the turbine internals (i.e., new rotor, diaphragms and bearings subject to design requirements) to suit the upgraded blade path.
The re-engineering will ensure the old rotor and stator can be reused within the existing casing once the price of power improves, thereby giving the customer flexibility to choose an option based on the fluctuation of power pricing and enhancing the efficiency in either scenario.
Case Study 2: Triveni REFURB — Aftermarket
A Fortune 500 petrochemical company had been operating its 17-stage direct-drive condensing steam turbine for over 40 years. They envisaged change in their process requirements which could be met by converting their existing “double extraction condensing” to “single extraction back pressure.”
Triveni REFURB offered a cost-effective solution by modifying the existing steam flow path and replacing only the turbine internals (rotor, diaphragms and bearings).
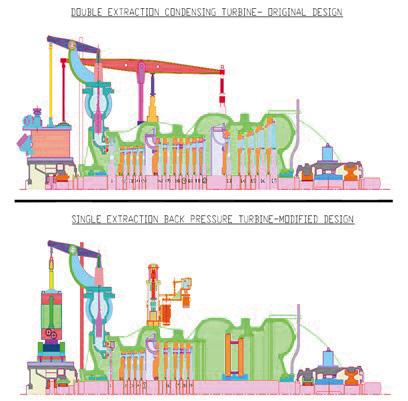
The existing casing and base frame were retained to ensure no modification in the foundation.
The existing mechanical governing system had to be adjusted at regular intervals to avoid risk to the turbine. This was upgraded to an electronic type governing, which was much simpler and reliable.
About the author: Arun graduated from the Indian Institute of Technology Bombay with a Master’s degree in Technology in Mechanical Engineering, and he also secured his Master Degree in Business Administration from Jamnalal Bajaj Institute of Management Studies, Bombay University. He joined Larsen & Toubro Limited as a Management Trainee looking after the Caterpillar product line. Subsequently, he changed over to SKF Bearings Limited and was looking after automation and electrical segments. He rejoined the Caterpillar Joint Venture associate company to establish an engine business in India. Subsequent to that, he worked with a Central Air Conditioning Company called Blue Star Limited. For the last 20 years, he has been with Triveni Turbines looking after the turbine business. Under his leadership, the turbine business has turned around and has grown many times and established leadership in Industrial Turbines in domestic and also in overseas markets.