
4 minute read
SPACE PROGRAM
2.Container Freight Stations (CFSs)
•It is a distribution facility/ warehouse where import and export shipments are consolidated and de-consolidated. CF’s are key component in any supply chain, moving interior point intermodal (IPI) freight.
•IPI freight is used to define inbound freight moves from a port to a shipper’s door within the interior of the country via a domestic or international intermodal container.
•Freight - goods transported in bulk by ship.
4.Parking lot of container chassis and tractors
•Required no of container chassis – 210 and tractors – 110
•Chassis – length : 12.4m, width: 2.5m
•Tractor – length : 12.19m, width: 2.44m, height: 2.9m
7.Area of Cargo-Handling Machines and cargo storage -5,569 square meters
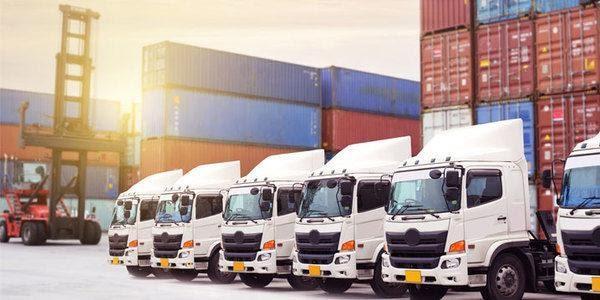
8.Parking Lots
•This is at the gate
•2590 passenger cars
•420 trucks
•80 tractors – chassis units
9.Area for Offices near Checking Post 1
•Fire Station and common use building – floor space
– 2550sqm
•Site Area of 892 sqm to be left
5.Repair Shop and Cleaning Area
•A repair shop of damaged containers with site area of 1500sqm planned to be prepared within storage yard for empty containers at this port.
•Cleaning Area is also allocated at the same yard.
6.Terminal Offices
•Floor space area of 600sqm (at gate3)
10.Required Numbers of machines for handling conventional cargoes
•Forklifts (5 to 10 tons) – 28
•Forklifts (5 tons) – 14
•Forklifts (3 tons) – 18
•Tractor – trailer/trucks – 33
11.LCL Reefer Yard
•Reefer Yard – Big fridges that are used to transport temperature controlled cargos such as fruits, meat, fish, etc.
•LCL – Less than Container Load

•FCL – Full Container Load
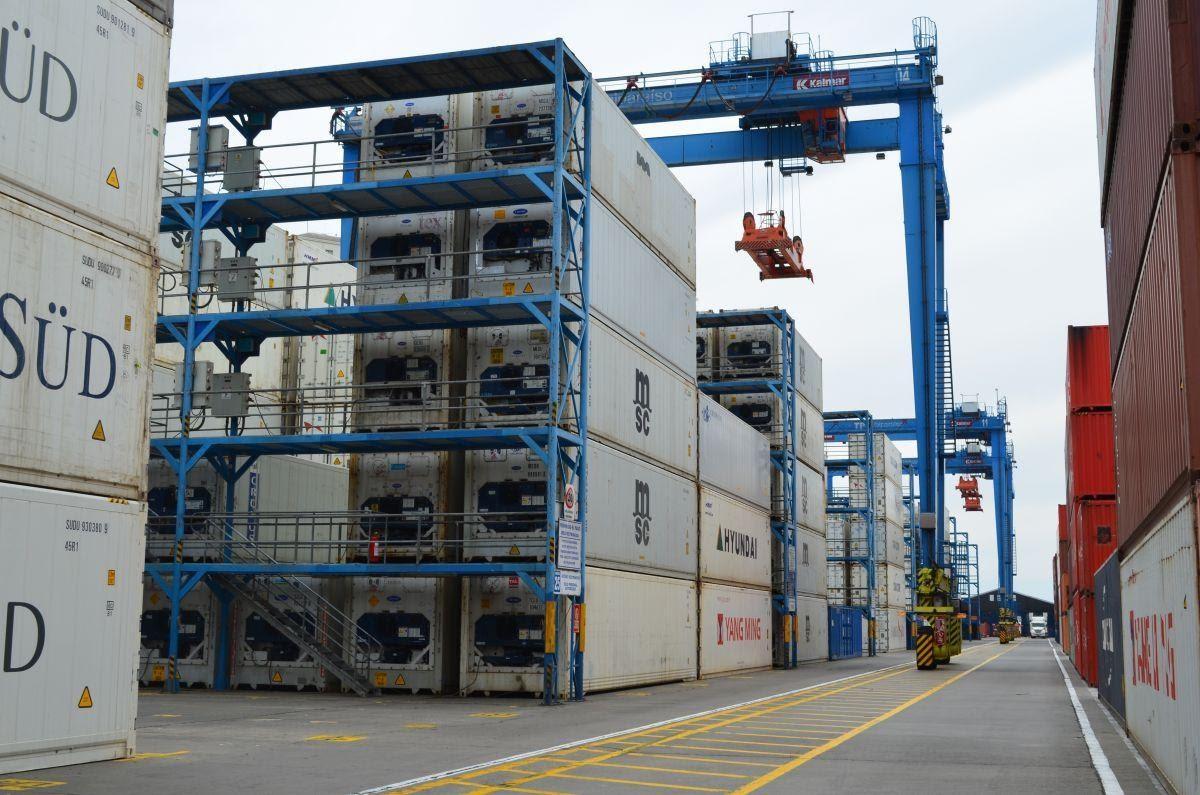
•This area needs plugs. (340 estimated for Bangkok port )
12.Required Number of Lanes at the Terminal Gate
•Designed according to the result of the simulation in terms of daily traffic volume through the terminal gates
•7 lanes at each gate
• Port warehouses have some unique requirements that inland warehouses do not.
• Warehouses in and around ports often need appropriately surfaced, open yard areas to accommodate the handling of heavy containers. These warehouses frequently specialize in heavy lifts, and abnormal cargo, meaning their architectural design and material handling equipment requirements differ from inland warehouses.
• Forklifts, front-end loaders, reach stackers and gantry cranes facilitate the handling of a variety of commodities at the ports.
A port warehouse needs to consider the use of overhead gantry cranes to lift heavier items and/or containers and it is often necessary for an on-site rigger to be employed to oversee special lifting jobs.
Due to the nature of the goods being imported and exported, fumigation, lashing and dunnaging services are often needed, while private rail sidings are used to assist in the movement of bulkier items.
Requirements Of Waterfront Warehousing
• GOODS-INTAKE
• SORTING
INCOMING
PROCESSING
• BULK STOCK STORAGE
• STOCK PICKING
• ORDER ASSEMBLY
• CHECK-OUT LOADING
OUTGOING
STORAGE OPERATION
Warehouse building selection depends on scale and type of storage operation.
Different methods of storage unit loads imply various levels of efficiency in building volume and accessibility to load.

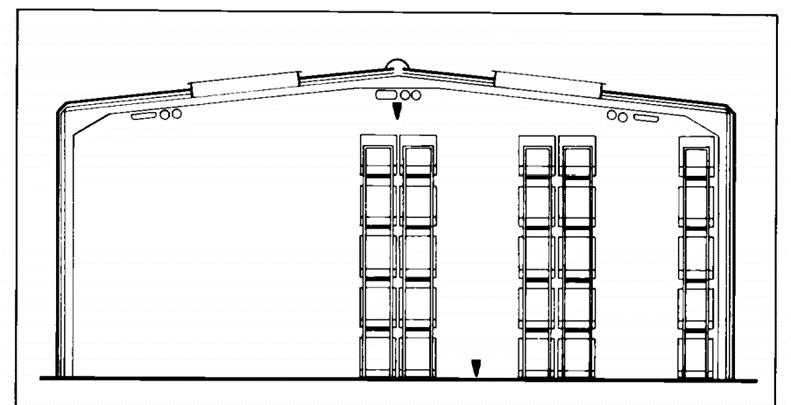
This also affects selection of mechanic handling equipment
Usually 1/3rd area is given to high bay area and 2/3rd is given to lower bay area for order picking and assembly.
A gross area of 70,000 to 90,000 square feet can be provided for a port warehouse.
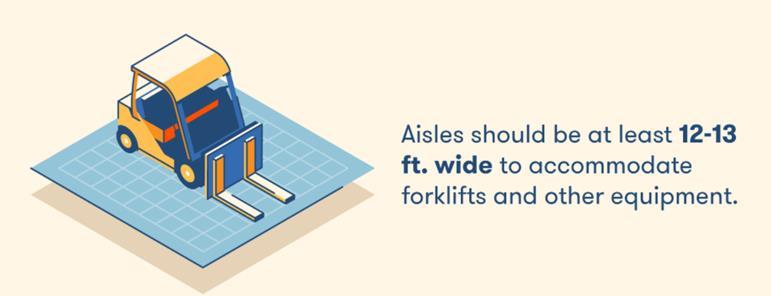
The width and length can be determined from the dimensions of the site and the space required for access roads and railroad sidings.
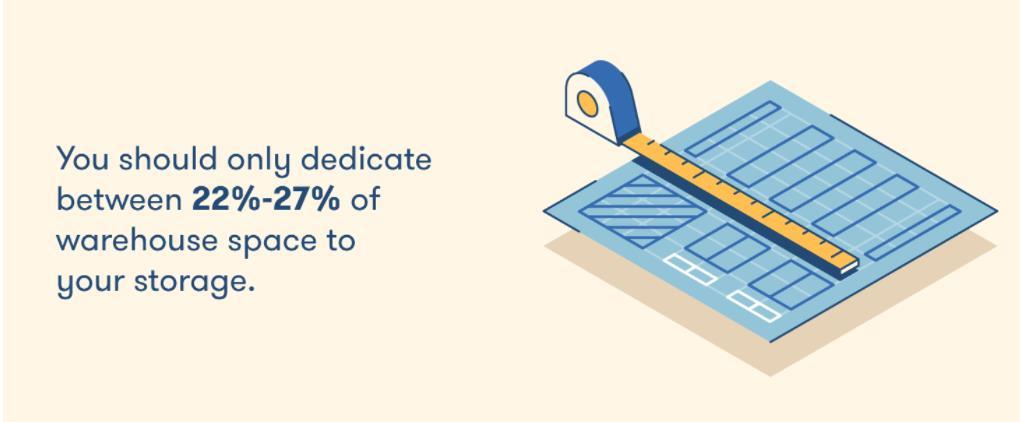
A clear height of 22 to 24 ft should be given
It would be ample to allow for automatic sprinklers for fire protection and pendant electric lights .
Bay spacing of 20 to 40 ft appears to be common practice.
Standards Of Waterfront Warehousing
MIN.REQUIREMENTS OF WATERFRONT WAREHOUSING
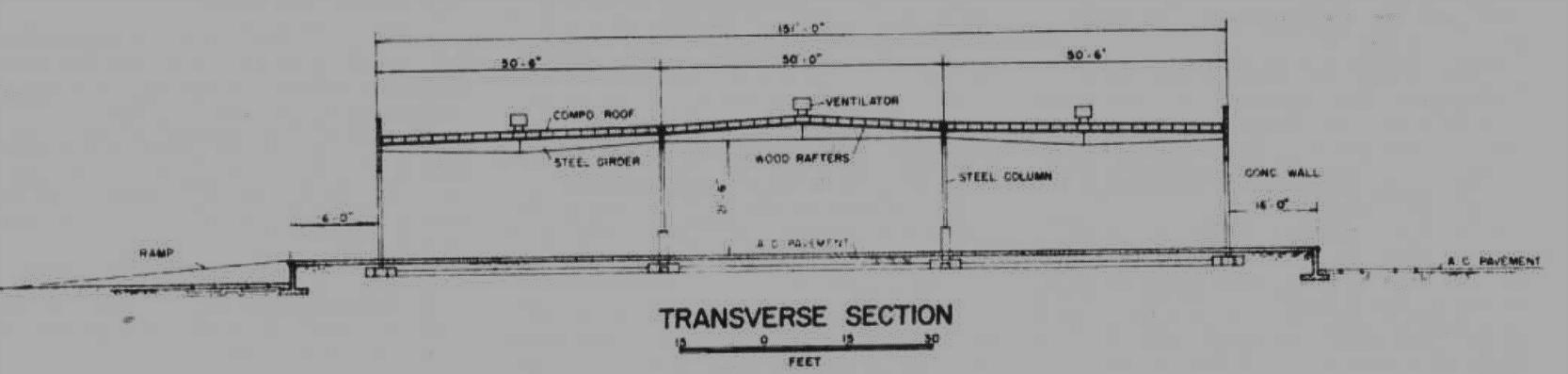
It can be divided into three separate and approximately equal storage areas by 12-inthick precast reinforced concrete transverse fire walls.
Columns at the exterior walls and fire walls should be preferably reinforced concrete, poured-in-place.
Interior columns should be structural steel spaced 50ft apart, and column bays to be spaced 40 ft apart.
Steel doors measuring 16 ft wide by 16 ft high .
