

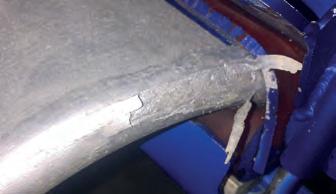
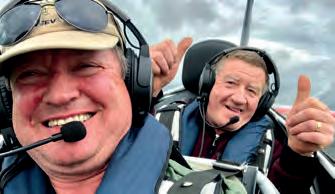
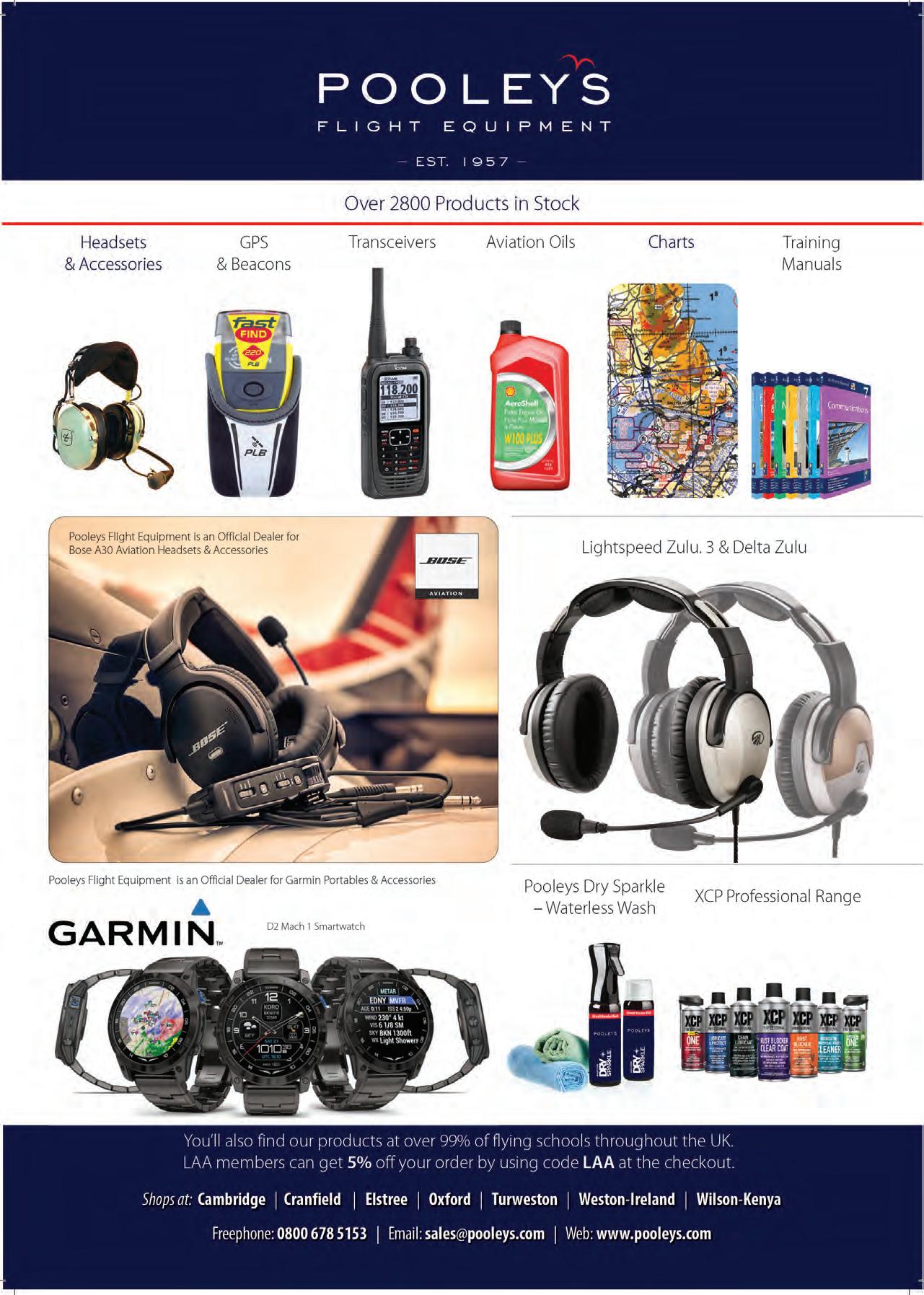


One thing I hadn’t necessarily planned to do as part of the work to get my Super Cub flying again was remaking the instrument panel. Looking at it after it first arrived in my hangar, I had figured a strip out of outdated vacuum instruments was definitely on the cards, plus a four in one set of engine instruments was already known to be partially faulty, so that was in the firing line too.
The panel itself had been enlarged as part of a 1988 rebuild and the glareshield that sat on top of it was now a partially vinyl affair which had long seen better days. As the instruments came out, I began to think of how the new items – a uAvionix AV30, and a Trig TT21 compact transponder – might be installed. Eventually, I figured I was just toying with a panel that was looking increasingly ugly… so with the encouragement of my Inspector, who just happened to be visiting so he could have a good look at the bottom end of the engine, we disconnected the various engine control cables and pulled out the panel. With that out, a few layers of redundant wiring from previous generations of nav and comm units were exposed – a few snips later they were gone, too. While it looked a bit bare, it felt like a good starting point to build back.
With an equipment list decided – ASi, altimeter, AV30, RPM gauge, Trig comm and transponder, a combined oil temperature and pressure gauge and a good old compass –panel layout began.
A temporary plastic panel and masking tape instruments, while laughably basic, quickly helped establish a very functional
layout which was pleasing to the eye. There was even space left in the middle for an iPhone running SkyDemon. Sitting with it mounted in the aeroplane confirmed that it was ‘just right’
Finding a fix for that ugly glareshield took a bit longer, taking at least half a dozen mock-ups in plastic to find the right shape to fit the inside of the bottom of the windscreen and around the fuselage frame tubes that reach from inside the fuselage up to each wing root. But it was proper homebuilding problem solving and reminded me how much I enjoy challenges like that… and why I love a good project.
Right, I had better start looking for some metal to cut!
13 PROJECT NEWS
A Hummelbird gets its Permit to fly, the ups and downs of a Van’s RV-7 project, and Cleared to Fly.
20 FLIGHT TEST
Toni Ganzmann headed to Italy to fly the M26 Victor, the first enclosed tandem two-seater from Magni Gyro…
26 WISE UP TO WOOD: PART 7
More secrets of building with wood. This time Dudley Pattison revels his tips for fitting D box plywood…
30 ROLL YOUR OWN
In the sixth part of this occassional series on designing your own aeroplane, Mike Roberts looks at calculating loads in the fuselage structure.
34 ENGINEERING MATTERS
This issue we look at understanding, preventing and treating corrosion. Corrosion in wheels and wheel bearings, and investigating modified structures.
44 MEET THE MEMBERS
Derek Pake relishes a challenge, and having scooped the top prize in last year’s Pooleys Dawn to Dusk competition, he’s already making plans for 2024! He also loves the camaraderie and ‘can do’ attitude of the LAA.
51 LAA PHOTO COMPETITION
Fantastic photos celebrating the joy of operating LAA Permit aircraft - have you entered yet?
LAA CTO Jon Viner says, “The LAA first approved the Aeroprakt A32 Vixxen as a homebuilt ‘Single Engine Piston’ type (Group A, in old terms) back in February 2019. With the advent of the revised microlight definition, Dragon Aviation asked us to also approve the type as a microlight aircraft, which was completed in December 2022. The two variants are identical in design, with the only differences being some of the interior placards. The microlight version is known as the ‘A32-M’, to distinguish it from the SEP version. To date, 17 of the SEP version and three of the microlight version have gained Permits to Fly through the LAA.
“Following on from our approval of the microlight version, the next step was for Dragon Aviation to seek CAA approval of its factory as a design and production organisation under BCAR Section A8-1, and get the type cleared as a Type Approved microlight. LAA has been able to provide Dragon Aviation with initial advice on the process, arrange meetings with the CAA and review draft documentation ahead of submission to the CAA. In addition, LAA has been able to assist CAA with its review of the type design, providing it with an insight into the approach taken on the homebuilt approval.
“With the anticipation of the first
Help avoid infringements in the Stansted area with these new hot-spot narratives and easy-access guidance, including everything you need to know to navigate the Stansted Transponder Mandatory Zones (TMZ). tinyurl.com/ Flysafestansted
This information for pilots is available on a new section of the Airspace & Safety Initiative website airspacesafety.com/ flying-in-the-stansted-area
factory-built example rolling out of Dragon Aviation’s hangar, LAA Engineering is also busy putting in place the necessary processes to get the Permit to Fly issued and validated, along with provisions for ongoing maintenance sign-off and Permit revalidations. Of course, dealing with Type Approved aircraft is not new – we’ve got a large fleet of factory-built gyroplanes on the books – but not having had any new factory-built microlights coming in since the Jabiru UL-D in 2005, this is the time to review and adjust these procedures.”
Ray Everett from Dragon Aviation adds, “We have been working with Aeroprakt since 2000 when we became the UK and Eire importer of the Foxbat microlight in kit form. Following the success of the 600kg microlight Vixxen, we made the decision to apply to the CAA to get Dragon Aviation its A8-1 status. This gives us design approval for microlights.
“The CAA visited our workshop in early March, and is happy with our facilities and procedures. We will now be building and selling the Vixxen ready to fly. This gives the opportunity for flying schools to own Vixxens as training aircraft. The LAA’s involvement will continue as the permitting authority.
“We have also recently built a hangar at Sleap Airfield in Shropshire, to facilitate our test flying.
“We would like to thank Paul Welsh for his support as Quality Manager, LAA Engineering for their input and Joe and Ewan from the CAA.” www.foxbataircraft.com
Guy Valvekens extends an invite to LAA members to attend the 39th Schaffen-Diest Fly-in. This Fly-in is also the 39th gathering, outside Italian borders, of aircraft like the Falco, Picchio, Nibbio and SF260, designed by engineer Stelio Frati.
The invite to members adds, “We hope to welcome, as in the previous years, umpteen aeroplanes from France, Austria, Switzerland, Italy, the Netherlands, Denmark, UK and Germany.
During the weekend, visiting aircraft crews will enjoy the following benefits: a lunch offered to each member of crew, the possibility to stay overnight at the airfield (camping), shuttle transport to and from
different hotels around, and a barbecue on Saturday evening including a live band.
“During the three days of the fly-in, demonstrations will include appearances from Old Timers and Ultralight aircraft. Also, several clubs of Old-timer Cars have agreed to visit and exhibit – we had more than 1,500 vehicles in 2023!”
Amateur-built and certain historic aircraft registered in European Civil Aviation Conference (ECAC) member states no longer require a permit to over fly Belgian territory for 30 days in a calendar year.
For more information, contact: guyvalvekens@gmail.com www.dac.be
News from LAA Kent Strut coordinator Steve Hoskins: “Thanks to RSP (Riveroak), the owners of Manston Airport, we are planning a three-day charity event on the 24, 25 and 26 May this year. This follows our very successful event last May. It’s very unique for this country to have a facility which can host all types and sizes of aircraft. Last year saw multi-million pound executive turboprops down to the smallest microlights – and pretty much everything in between.
“The event is open to all, not just LAA, and fuel is available with prior notice, as is entry / exits direct into Manston cleared by Border Force from Europe. There's been interest this time from Germany, Holland and France so far.
“It’s the real deal on approach! A vast international airport but with air ground radio and rally-style arrivals. At present it’s unlicensed and goes without saying at pilots’ own risk.
“We’ve called it ‘Man’kosh’ last year, which seemed fitting!
“The onsite Nafi attached to the fabulous RAF Manston museum will be catering from early until late for all, including the happy campers. The local area is worth exploring with Margate, Ramsgate and Broadstairs etc all a short bus ride away.”
Contact Steve Hoskins, LAA Kent Strut on 07768 984507.
‘Aerobility Live’ will bring the skills and thrills of aviation into your own home, on Saturday 15 June – this time with a live audience.
The Armchair Airshow, first launched four years ago when pandemic restrictions meant public events were banned, was a huge hit with aviation fans throughout the world who got a unique insight behind the scenes from their living rooms.
This year’s event will again be live-streamed online with a new name: ‘Aerobility Live’, but will also have a limited number of tickets for those who want to watch in person from Blackbushe Airport.
Blackbushe Air Day is an annual event celebrating all things aviation, featuring a static aircraft display, pleasure flights and fun for all of the family. Aerobility will be hosting its own area for the first time this year named the ‘Aerobility Live zone’. This area will feature a big screen showing specially recorded aerial demonstrations, including live commentary from real pilots, providing a fascinating insight into the skills required to perform these flying feats.
The show promises to have fascinating pre-recorded flying displays, insight from high-profile pilots, an exciting aviation-themed raffle with impressive prizes, plus more.
To find out more about the event, please visit www.aerobility.com/ aerobility-live-2024, and if you’d like to buy a ticket and be a part of the live audience, please visit tinyurl.com/ Aerobilitylivetickets
More airfields have been added to the Airspace & Safety Initiative series of Frequency Monitoring Code (FMC) area guides, including Birmingham, Bristol and Gatwick.
Working with members of the Local Airspace Infringements Teams, they highlight areas of operation for each code to help pilots with their flight planning. The series also includes Manchester, Southampton and Solent, and Stansted. airspacesafety.com
Spaces are available on forthcoming LAA Technical training courses being held at our Turweston HQ. The following courses all cost £200 for members.
● Caring for your Gipsy Major – 6 April
● Aircraft carpentry – 23 April
● Electrical Advanced – 28 April
● Electrics Basics – 4 May.
● Aircraft Fabric Covering – 8 May (at Henstridge Airfield)
● Permit Aircraft Avionics – 18 and 19 May Contact Cheryl Routledge on 01280 846786 or email cheryl. routledge@laa.uk.com if you would like to book.
LAA is pleased to announce the removal of fees for enabling modification applications. LAA CEO Simon Tilling said, “The LAA wants to ensure that the wonder of flight is made available to all, especially when it comes to changing lives for the better and getting more people into the air. People living with disabilities face many challenges in their day-to-day lives and adapting an aircraft to make it suitable for an individual’s needs, while making it safe for flight, shouldn’t be one of them. Working with leading disabled flying charity, Aerobility, the Light Aircraft Association has agreed that it will no longer charge fees for modification applications that are submitted which enable a disabled person to fly.
“While this will include items such as hand controls, augmented braking systems etc, it won’t include day-to-day items that are not critical to enable the disabled person to fly. To qualify, owners should make it clear at the application stage that their modification is an enabling modification.”
Ernest ‘Ernie’ Horsfall, a stalwart of the PFA and the LAA and a doyen of all things Jodel, sadly passed away recently. Aged 105, Ernest was just eight weeks short of his 106th birthday, and he remained knowledgeable about, and interested in, aviation almost to the end.
Although most people knew him as ‘Ernie’ he preferred to be called Ernest and his passion for aviation seems to have been triggered almost at birth when he was born only a few hours after the Red Baron, Manfred von Richtofen (German fighter ace), was shot down on the Western Front in WWI.
Born and raised in Bradford, one of six children (all others now deceased), Ernest trained as an apprentice engineer in the textile industry in the 1930s. He joined the Army in early 1940 and served throughout WWII in the REME – the Corps of Royal Electrical and Mechanical Engineers – in North Africa and Italy. The REME is responsible for maintaining the army’s vehicles, including tanks –and was described by Field Marshal Montgomery as the Corps that would ‘keep the punch in the Army’s fist’. Ernest rose quickly through the ranks from Private to Warrant Officer (most senior non-commissioned rank) within a year, and he commanded a Field Workshop for almost the entire time. In Naples in 1943 he provided some vehicle engineering advice to the RAF and in return was given a flight in an RAF flying boat. This sparked his love of aviation. He returned to the UK in August 1945 at the end of WWII, in an RAF Lancaster bomber, further fuelling his interest in aviation.
A few years after leaving the army Ernest moved to the car industry, working for Jowett Cars in Bradford, followed by Vauxhall at Luton in 1951. Initially an experimental engineer, he graduated to being a senior development engineer in Luton and Lancashire.
Taking his first flying lesson on 4 September 1962, Ernest went on to amass more than 3,000 hours flying, going as far afield as the Mediterranean, more than once, and North Africa. On the way to his grand total, Ernest found time to be on the PFA / LAA Council and to establish the Lancashire Strut as its first Chairman. His real aeroplane passion was for Jodels, importing around 60, which would significantly expand the UK fleet, and led to his extensive engineering expertise with the type which he was keen to share.
Ernest quickly became an expert in light aircraft engineering, particularly for wooden construction aircraft. He remained an active licensed LAA light aircraft Inspector / engineer for 51 years until he
was 103, and he was also an Inspector for the Icelandic CAA for wood and fabric aircraft. As the then LAA Chief Inspector (Ken Craigie) said during Ernest’s 102nd year – his 50th as an Inspector, “There is no age limit on being an official Inspector, it all comes down to their ability. We check that Ernie is still capable every year and he proves himself every time. He has an incredible wealth of knowledge to call on and is a valuable asset to us.”
Ernest gave up his Inspector’s ‘ticket’ nearly two years later because, as he put it, “I can get down to do the inspections, I just can’t get up again!”
A large number of light aircraft dating from the 1980s, and before, have wood in their construction and they continue to fly safely in the UK and European skies. Indeed, there are six on the UK aircraft register that still carry his initials – EJH or EH.
When not restoring or advising other restorers, Ernest would fly almost anything, and he only stopped flying at 93 years old when insurers refused to cover him as P1. He still flew, though as P2, and had an ambition to fly the Spitfire, but was beaten by the pandemic.
Ernest’s only son died aged over 20 years ago and his wife died just a few years later, but Ernest continued living in his family home and looked after himself, and he drove until he was 103. He moved into a residential home just after his 104th birthday and lived there for almost two years. Until recently, his social circle included a flying group that met every second weekend, another that met monthly, and a couple of other individuals he had known for many years. And he continued to offer aeroplane engineering advice to pilots and owners around the world until late 2023.
Like so many WWII veterans, Ernest was largely ignored until the past few years, when his service and longevity were finally recognised. Before then, though, the aviation world had recognised his talent and expertise and he was awarded:
● The Royal Aero Club (RAeC) Silver award (the Club’s second highest award), and later the RAeC ‘Old & Bold’ award.
● The National Transport Trust Lifetime Achievement Award.
Ernest gained his Angel Wings on 20 February 2024, passing away peacefully. He would not want to be mourned though, rather he would want us all to celebrate his life, whenever we see a Jodel – and especially when we see one with an ‘EJH’ registration. Farewell old friend, veteran, pilot, engineer and mentor… your work is done but your achievements live on. Terry Cook.
Simon Tilling CEO
Iam sitting writing this listening to another deluge outside. Will it ever stop raining? However, there is plenty to talk about other than the weather.
The CAA recently launched the consultation process on the GA Pilot Licensing and Training Simplification review. It’s a lengthy document but well-worth a read, and I recommend you take the time to provide the your feedback. We have all been critical of the CAA in the past for numerous reasons, but on first pass this document offers some very sensible and thought-out improvements to the current complicated, and often confusing, rule set. If this is a sign of things to come from the CAA, then it’s a very welcome improvement!
General Aviation is a broad church encompassing many different areas from balloons to biz jets. To protect the freedoms of each of these types of GA and to ensure the interests of these varied sectors a number of different organisations have been formed e.g. GAA, GAAC, GASCo, to advocate on our behalf. These groups, advocate and lobby on behalf of GA for airspace, airfields and other regulatory issues. They provide valuable resources, support, and guidance for all those involved in general
Eryl Smith Chairman
Like many members I am looking forward to getting back in the air. The lay-off has been a combination of circumstances; weather, serviceability and personal. So how confident and competent do I feel?
I’ve just returned from my annual ski trip. As an average skier I know my limitations, set my boundaries and have equal measures of excitement and trepidation anticipating my time on the slopes. My wife’s words ‘enjoy but come back in one piece’ ring in my ears. I wonder how many partners and friends privately express those thoughts as we go off to fly?
The slopes and runs may be familiar, but the conditions are always variable, and it takes a day or two to find my ski legs! I still start back on the same green run on which I learned, getting the feel of the snow under my skis and practising my basic techniques. For good measure there are a couple of lessons along the way to ensure my techniques are correct, and give me the confidence to push on. It’s not long before I am progressing and enjoy the thrill of higher slopes, more speed and greater technical challenges. Just as with aviation there is the satisfaction
aviation activities. They are, however, somewhat independent of each other and this creates a degree of overlap and duplication.
With the pressures we all face on time and cost perhaps now is the time for all these organisations to come together and harness the undoubted benefit of a common voice, shared resources, and an agreed set of objectives?
Permit renewal performance
Our technical training programme for 2024 is well underway and we have already run a number of courses. The demand has been so great that a lot of our courses are fully booked and we are now planning more dates throughout the year. Feedback from attendees has been really positive and its clear that this is meeting a need, not just of LAA members but also the wider GA community. A full list of our curriculum is available on the LAA website, and new courses will be added as we get them arranged. If you think there is a topic you would like to see us cover then please let me know and we can investigate. ■
of the day’s achievements and the opportunity to share the moment with others over a beer or two at the end of the day!
So what parallels for my return to the air? I know that I need to refresh my basic skills, something I try to do at the start of each flying season. It may require some more instructor or coach time, but it is time well spent to ensure I feel confident and competent to safely maximise the enjoyment of my flying over the coming months. It would be easy to say ‘that’s it’, but I know that I will need to build my confidence as I gradually expand my flying envelope and push my boundaries. Thankfully, as a syndicate owner, I have the benefit of fellow group members with whom I can share the flying and the workload as I undertake more demanding flights.
If, like me, you are returning to the air after a break, take time to consider your personal boundaries, invest in some additional coaching, take advantage of fellow pilots to share the workload as you extend your flying envelope, and build up your confidence. That way you can fly safely and enjoy your time in the air!
Oh, and what of my skiing exploits? Thankfully, I returned in one piece, with only one tumble but a soft landing and the satisfaction of having successfully mastered the more demanding runs of the week.
Confidence restored – and friendships rekindled! ■
We are always pleased to receive your letters, photos of your flying, and your feedback. Please email the editor at ed.hicks@laa.uk.com
Dear Ed,
I was interested to read Clive Davidson’s article on flying the Dyn’Aero CR100, in particular his comments on crosswind landing.
Some may remember my Super Sapphire V6 200hp aero engine, installed in my Chipmunk G-ARWB? I carried out quite a few hours test flying the engine and aircraft installation, all through the CAA. This included high-speed hops on the ground at Shoreham, before getting truly airborne. Then when I started to fly it for real, I was already in the habit of doing a wheelie, which I continued when landing.
Roll on the 1980 Farnborough Airshow, in which I was a flying exhibitor. The drill for a display pilot is to agree a routine in advance with the ATC. Then you take off at, say, 1532, turn left at 500ft and vacate the circuit. Then reappear at the threshold at 1536, perform three minutes of exhibiting your wares, and land at precisely 1539.
On Thursday, at 1532 precisely, a tornado hit Farnborough. Many of the tents blew away, and nobody was watching me. As I took off, the ATC instructed me to start my routine immediately. By the way, you don’t talk back to the ATC, you just listen. Well, of course, I wasn’t in the right place for my routine, but did the best I could and came in to land.
There was a very strong 90° crosswind blowing, but the Chipmunk was well behaved and I did a wheelie as usual. At this precise moment, the Hawker Harrier, which was the slot before me, was hovering at right angles to the runway, as I landed right in front of him.
The Harrier pilot spoke to me afterwards, and told me that as I touched down in front of him, his ASI was reading 70kt.
Do you think that is a bit of a record?
Kind regards,
Bill Bonner.Hi Ed,
As a LAA member and CRI I read the letter from ‘A member who loves to fly’. If you would like to pass my details to him I would be happy to offer a flight in my RV-6 based at White Waltham.
As an aside, I enjoyed the Turb Team article Displaying at Ferte Alais. I retired from the Team in 2022 after nearly 20 years displaying with them and led displays at Ferte Alais in 2003 and 2004.
Regards, Richard Pearson.
Dear Ed,
I read with interest the letter in the March issue from Gerry Knee, ‘New aviators’, and I also share his view on the idea of back-tobasics.
I wouldn’t exactly class myself as the next generation of aviator. I passed my PPL last year at 45, however, when I look at the age of the pilots operating from, or visiting, my local airfields I definitely consider myself one of the younger pilots within the demographic.
For many, cost is the biggest hurdle in aviation, not just gaining your licence but continuing after you have received your blue plastic wallet from the CAA.
The idea of a back-to-basics, plans-built aircraft that can be built to a realistic affordable budget seems like a great way to kick-start the next generation. I’m sure we would all like a shiny new Van’s RV or Sling TSI, but not everyone has £100,000-plus sitting in a tin marked ‘new aeroplane fund’.
The LAA has many types on its approved list of aircraft, however, not enough of them are a realistic option going forward. Plans are unavailable for many of them and the cost of build for a kit aircraft are just two reasons, not to mention the lead times to receive them.
We don’t have to try and reinvent the wheel either, there are many small two-seat aircraft flying that could be looked at and redesigned slightly to allow for more modern engines and construction techniques.
The idea of a low-cost, homebuilt design competition would be a great way to see if the LAA members could come up with a viable aircraft to help continue our hobby for the next generation of pilots.
I for one would definitely get my coloured pencils out and get sketching. Mark Jackson.
Dear Ed,
Re: the letter in the March edition of Light Aviation from Gerry Knee concerning the demographic of LAA members and costs etc, I made similar comments in feedback to the CEO, following the Popham event last year.
The cost of the latest generation of Permit aircraft is comparable to that of super cars and it is therefore no surprise that younger people with spouses, mortgages, kids etc are not flocking to take part in aviation, even through the ‘low cost’ LAA route.
In my feedback I also suggested a design competition for a (genuinely) low-cost aircraft
with a target airframe cost of £10k. With pre-loved Rotax 9 series engines occasionally available for around £6k (other engine options are available), this would bring the total into the same ballpark as Mr. Knee’s proposal.
Hopefully some interest will be sparked within the LAA to progress this idea further. Regards,
David Neill.May I disagree? It seems to me that it is hard to persuade today’s youth that grass roots flying is desirable.
Telling them that they need first to build their aeroplane is pretty much a brick wall.
We need to look firstly at routes to get a licence and secondly at low-cost ways to access an aeroplane.
Small Jodels or shares in them are probably still available under £20k, but we need to think about affordable ways to get a licence and then promote those.
Regards,
Robin Voice.If you go back to around 2007, then in one of the issues of the LA magazine, you will see that I was credited with suggesting a design competition for a low-cost single-seater. At the time, I was flying an own-built MW5, so I knew quite a lot about low-cost flying.
The idea was obviously attractive to the LAA personnel and with no further input from myself, the design competition went ahead.
The winner of the advanced category was the carbon fibre canard e-Go – my memory is hazy, which actually flew. Only two were built as the company building it eventually ceased trading. The aircraft was reviewed in the magazine and was, apparently, a very pleasant aircraft.
Things became a bit less clear in the case of the winner of the basic category. This was won by a fellow, who had built a twin-boom, low-wing aircraft with a pusher prop. The winners of both competitions received a single-cylinder engine as a prize, which were used by both winners. The twin boom design doesn’t appear to have flown.
I wish you well in pursuing such a worthwhile proposal. Obviously, few people want a single-seater, so a twin-seater has much more appeal.
Maybe you should have a chat with Mike
Right Winner of the last LAA design competition, the e-Go while innovative, ended up costing more than intended, and was ultimately only a single seatertwo seats remains more desirable.
Whittaker and ask for his thoughts on the matter, as his single-seater MW10 Plank has successfully flown, and perhaps his thoughts are geared towards building a two-seater version.
Regards, Peter
Gripton.Ed the editor replies: You’re right, the e-Go had great promise, and it was a shame when only two examples were built.
As well as the letters here, I’ve been surprised by the number of people who have spoken to me about instigating another LAA Design Challenge. The seems to be strong interest in a low-cost LAA two-seat aircraft…
Dear Ed,
that economics, greed and bad management never remove the opportunities I had – and still have.
Regarding the YES challenge to get 2,024 young aviators airborne this year, as you know I have already raised the issue of airfields prepared to host these efforts due to circuit flying restrictions and noise abatement etc. But please don’t view my concerns as negativity as this is a first-class idea and one which I know many will support.
As a gyro pilot, sharing the privilege of flying has always been high on my agenda, and as someone who does not enjoy heights or fairground rides, I was very reluctant to take the first step and have a flight experience.
However, just hours after my second flight and with some of my fears averted, I committed to my first batch of flying lessons… and 14 years later I have clocked up more than 1,200 hours of fantastic experiences.
My gyro, Big Nellie, as she is known, has taken me to France and flown me many times from north Hertfordshire, where she is hangared, to the Isle of Wight where many of my family and friends reside.
In 2013, I became membership secretary and events coordinator for the British Rotorcraft Association, and over the years have built up a huge group of friends and associates, both pilots and airfield personnel, members of the LAA, CAA, GASCo, Luton Airport and even NATS.
No matter what walk of life we come from, we all share that passion for aviation and to be part of that is priceless.
Big Nellie has taken almost 300 passengers up for flights and several of those went on to own gyro’s of their own.
I will never be able to express how much of a true privilege being a pilot is and hope
Flying almost 100 hours a year is not much more expensive than running a modern car, the issue for sure is the growing costs of learning to fly and the amount of very valuable airfields that continue to close due to the demand for land for housing.
I am currently in talks with two well-known airfields with the aim of trying to get them on board hosting this challenge. I wish you all the best of luck.
Kind regards,
Steve Paffett.Just received the latest issue of the fantastic LA magazine. More than a little disappointed given the coverage of the Pooleys awards that no mention was given to myself, an LAA member, plus Jason Davidson (non-member) for our ‘Best Video’ award in recognition of our Dambuster commemorative flight last May that raised over £3k for the RBL. We are close friends of Dave Pitman and Gavin Johns.
Were we omitted because Jason is not an LAA member?
Our video can be found here tinyurl.com/ Pforpopsie
Plus an edited version and footage from the evening, with kind permission of FLYER, can be found here tinyurl.com/ Pforpopsieaward
Kind regards,
Simon Shackell.Ed the editor replies: Thanks for the email, and congratulations on the award.
It was a genuine omission, I’m afraid. I can only go on information I am provided, or have learned, so all those identified in the news piece had been notified to me by the winners /
friends of the winners or were people I knew to be members. Looking at the video and seeing the Piper Seminole twin, I wasn’t able to make an obvious LAA connection there either – had it been an LAA type I would have investigated further.
Dear Editor,
I recently attended the weekend ROCC course at Popham Airfield, and was taught by Chris Thompson, LAA National Coach. I write to say that it was time really well spent, and that the considerable time and effort put in by Chris was obvious.
The four of us students were all pilots, with one even an instructor, and we all enjoyed the experience immensely.
It was an excellent refresher on the radio communications we learned for our FRTOLs when doing our pilot licences… all those years ago! We all think ‘we’re good on the radio’, but we aren’t really, are we? There’s a lot of non-standard phraseology going on out there: ‘turning final’, ‘rolling’, ‘understand’ etc!
Despite our previous radio use over years of flying, we learned a heck of a lot and will be better pilots, I’m sure.
The practical / oral exam on the second day showed that talking to several stations in a very short space of time is a whole different ball game from being in an aircraft and just needing to talk to just the one station!
So, a big thank-you to Chris for organising and teaching the course… and for the many wonderful tales of ‘derring-do’ during his illustrious flying career in so many different types, in so many countries and in so many different conditions.
I plan to put my new qualification to use during the coming season, that is, if it ever stops raining!
Also, my advice is grab this course before Chris retires! Goronwy (‘Gron’) Jones.
We look forward to scenes like this at Leicester.
It’s been more than 40 years since we last held the LAA Rally at Leicester. In the intervening time we’ve held the event at Cranfield, Wroughton, Kemble, Sywell, and latterly, as the Grass Roots fly-in at Popham. So it’s doubly exciting to be returning to Leicester for our 2024 event as we look to build back to a full Rally, and respond to the desire of members for a more centrally located venue.
Over the years the various Rally teams have evolved a well-honed event formula, and this forms the basis of our planning for this year’s event. We are working closely with the team at Leicester, which will assume responsibility for all the airside operations, aerodrome procedures and air ground radio. The LAA will be responsible for all the exhibition site activities.
As always the Rally is an annual opportunity for members to gather as a community, renew old friendships and forge new ones. It’s a showcase of our diverse fleet of Permit aircraft, whether that be recently completed, newly restored or merely lovingly owned types.
Once again the exhibition site will play host to a wealth of exhibitors with a wide variety of equipment, parts and services. While there is so much that can now be sourced online there is no substitute to those face-to-face conversations between supplier and customer; experiencing the product first-hand and being able to ask those direct questions. It’s an opportunity valued by suppliers and members alike!
Among the many regular LAA activities you will find a programme of presentations in the Speakers’ Corner, Q&A with LAA CEO Simon Tilling, a full attendance by LAA’s Engineering team ready to provide advice and answer queries, the membership services stand with a range of clothing and merchandise, and the presence of LAA Struts & Clubs, where you can find information on our regional network of events and activities.
Education and training will feature prominently to promote the expanding programme of courses on offer, together with the return of some of the practical hands-on displays, which featured in the previous Homebuilders area. We also anticipate organisations such as CAA, GASCo, and RIN to be present providing briefings on aviation matters for the benefit of members.
As part of our partnership with Leicester Aero Club we are looking jointly at a programme of evening entertainment and catering, which will ensure there is a focus to relax onsite at the end of the day and enjoy each others’ company, as we no doubt recount experiences of past rallies or put our aviation world to rights!
While the Rally is very much our annual gathering, it is also the opportunity to welcome others into our world, be it the non-flying aviation enthusiast, the CofA owner / pilot seeking more affordable means of aviating, or those yet to experience the thrill of flying and aircraft ownership, who are curious to find out more. As we develop our plans we will be seeking to ensure that the LAA Rally 2024 offers something for everyone.
The Rally takes place at Leicester Aerodrome, Friday 30 August to Sunday 1 September. A slot booking system will be in place for flight arrivals commencing from 1200 on Thursday 29 August. Full aerodrome procedures will be published prior to the event via AIC, LAA and LAC websites. Onsite car parking, campsite and catering will all be available and there is a wide selection of accommodation options in the Leicester area. Details of admission charges and arrangements for online pre-booking will be published shortly.
Full details of the programme of events and exhibitors attending the Rally will be published on the LAA website. Look out for regular updates in the news sections of both the magazine and the website. ■
Late last year Allen Haseldine got in touch with Project News to provide an update on his Hummelbird singleseater, which had been finished for a while. As the first of its type in the UK, testing had taken some time, but it had finally received its full Permit to Fly. The design is attributed to the American designer Morry Hummel, in 1980, and is a very compact, all-metal, single-seater aircraft with detachable outer wing panels for storage in small spaces. Power comes from a two-cylinder half VW engine of 42hp. Having never heard of the type, I found some constructional images online and it immediately made me think of the Thatcher CX4 – only smaller. Allen has had the Hummelbird’s plans redrawn and holds the UK rights for the design, he is also the manufacturer of Newton Propellers.
I recently heard from Mike Sweeney who has provided a lovely report on his recent Van’s RV-7 completion – it’s his tale of a 15-year journey to complete his own aircraft. With the exception of the upholstery, he’s done just about everything himself. I think it’s an
excellent read about the trials and tribulations of building an aeroplane – it just happens to be an RV. Do have a look, I thoroughly enjoyed reading it.
In the panel at the end of this column, you’ll find an interesting cross-section of projects that received their initial clearance to begin test flying during February, hopefully we’ll hear from most, if not all, in due course – indeed as mentioned, the report on G-RVMS is below. If you have an ongoing project, then please don’t wait to be asked, do share your progress with your fellow LAA members through these pages, contact details below. Interestingly there were no New Projects registered in February, which is unusual, as typically this time of year sees a rise in project starts. A quick look back over the stats reveal 2.5 new projects registered per month for the last six months, so the passion isn’t drying up just yet.
To get in touch with Project News, and tell your story, report a milestone or just to send a picture, email: projectnews@laa.uk.com Please share your story!
The Hummelbird is a plans built aircraft, the fuselage construction is essentially six bulkheads tied together with an aluminium angle longeron either side, construction starts around a ply box, supported across a couple of saw horses, which is used to initially position the bulkheads in space. These bulkheads give the fuselage its shape by riveting sheet aluminium around them to form a tube or monocoque structure. It’s very minimalist, in fact the aircraft’s mauw is just 253kg. Indeed, the bulkhead that forms the front of the cockpit is installed with the instrument holes already cut into it – there is no separate panel. There are some interesting constructional images and videos online that illustrate this.
The main spar is again made from a couple of pieces of angle as spar caps, with a thick sheet web in between, while the ribs are fairly conventional sheet ribs with an outer flange and lightening holes. Ribs, bulkheads and skinning is all 6061 aluminium, a nice easily formed alloy with little spring back when worked. The ribs and
bulkheads are formed around wooden blanks. The wing is in three sections, with the centre section permanently attached to the fuse and mounting the main gear. The outer panels bolt conventionally to the top and bottom of the spar with the intention of easy removal should it be required. Allen made the canopy from clear sheet, heated and draped over a former.
Tango November is registered as a light aircraft and not an SSDR, as its stall speed was just a couple of mph too fast and, while it may have been possible to reduce this, Allen did not pursue this option. The aircraft stall was very benign with little or no discernible buffet and so the LAA testing regime required that it be fitted with a stall warner.
The project was greatly helped by the late Eric King, who showed a great interest in it with calculations; also the project’s Inspectors, Gil Davies and Andrew Asquith, who were always willing to give a hand. Test pilots were Willy Hackett, Brad Wagenhauser and Dan Griffiths.
Iknow what you’re thinking, “Oh no, not another Van’s Aircraft kit build story… and not only that, another RV-7.” Well, in a way it is, but also it’s not. Actually, it’s a look into the decisions that were made and the reasons behind them.
It all started back in 2008, and I was a member of a group that had just finished an RV-9A. As with all groups, the route had been a compromise and, although that was fine, I felt I was in a position to build something for myself and build it to the spec I wanted.
So, buoyed by an exchange rate of almost two dollars to the pound, I did my mini research and ticked all the options for my order of a quick build Van’s RV-7. The empennage kit arrived and, like a kid in a sweetshop, I started to look at the parts and read the build manual. I’d scoured the forums for tools for sale and managed to buy a fair bit from an RV-4 builder who was emigrating. On top of that, I bought a compressor, a pillar drill, a bandsaw and a number of air tools.
If you buy cheap, you’ll buy again. Always buy the best tools that you can afford, especially those that you will use most often.
Below
domestic circumstances so, only a few months into the build, it effectively stopped. Then with impeccable timing, Van’s emailed to say that my quick build fuselage and wings were ready to ship. I put the order on hold, saying that I would be in touch when ‘I was ready to proceed’.
Three years passed and I was ready to go again, however, the financial crisis had done its worst with the exchange rate. I was now wondering if I could still afford a quick build kit plus have the options, engine and propeller, which I had wanted. My calculations on the choice of quick build vs standard build went into overdrive and I even phoned Van’s Aircraft to talk it through with Gus. I still remember his words, after chatting a fair bit, “If you want to save time, buy a quick build, but if you want to save money, go for the standard build.” He assured me that there wasn’t any skill required over and above that which I had already gained making the empennage, it was just more riveting (by that I mean assembling using clecos, drilling, deburring, dimpling, priming, assembling again and then riveting).
Part way through my empennage, I had a change of
So, in order to save money and proceed, I ordered the standard build. I now also had use of my barn next door, a mere walk of 25ft to work on my project. The kit arrived in late 2012 and I set about doing the inventory of parts.
The wings were straightforward, but they were also very repetitive. I soon became lost in a fog of fluting, assembling, drilling, disassembling and deburring… I called this period ‘wing-rib hell’, as there seemed to be an endless amount of work but no visible progress. With the wings now in their jigs, clecoed but not yet riveted, another ‘pause’ in building… another few years.
When I got back to it after this time, I was determined not to have any more ‘pauses’, and I succeeded. However, now Brexit had loomed and sterling was on the floor. Undeterred by everything, I picked up where I’d left off and started the dreaded fuel tanks.
Proseal gets everywhere… do not attempt any small job with it wearing clothes that you like – and buy plenty of disposable gloves – and I mean plenty. I was changing gloves every other rivet and I still managed to get it everywhere.
The jobs in the build that you dread are not nearly as bad when you actually do them (this applies to building a Van’s Aircraft anyway), and the myth is worse than reality. Tanks now completed, I needed a break from those wings (they weren’t primed nor riveted as yet), so I started on the fuselage, firewall first. I have to say that if the wings are boring to build, the fuselage definitely isn’t. Every job seems to be different to the last and there are
big sub-assemblies that keep the visible progress moving. This was a true delight to build, right up to the point that I cut a slot in the longeron at the wrong angle – I still remember looking at it, rubbing the slot as if to make it better, and then wondering how I could replace such a singularly long item. You can’t buy that profile in the UK, of that fact, I am certain. So, I ordered a replacement from Van’s and, to save me the horrifically high shipping cost, they put it into a kit for someone else in the UK, so, after strapping three four-metre lengths of plastic pipe, bound together for rigidity, to the roof of my car, I set off to High Wycombe to collect it.
Only part of the build process is about building, the remainder is how to solve engineering problems that you come across. With the new longeron installed, I was away.
The upside-down canoe was now full of clecos and needed riveting. This was the first time that I either needed seven-foot long arms or a helper… so, helper it was! I worked on the aircraft alone until my dad visited and helped me join the two halves of the fuselage then, together, we ‘flipped the canoe’.
The work continued apace and, as I was building, my mind drifted to thoughts of avionics and just how spangly it would be. Names like Garmin and Dynon were at the forefront, but I soon settled on Dynon. I’d already decided that this would be a VFR cruiser that could cope with the longest of flights – autopilot, two large screens, four mini modules to help and a back-up Garmin G5 as well. I look at this now, as I type, and I don’t know how I afforded it… after all, I hadn’t even bought an engine or prop yet.
Lost in a world of panel layouts and wiring, I was thinking about the next stage, my engine and prop. By now, Boris was doing his best to ‘sink my ship’ and then, straight after a ski trip, covid hit.
Above
I had already ordered the engine and prop from Van’s. This was after two significant pieces of information. Firstly, my Inspector had advised me ‘…it would be a shame to spoil all your efforts and money by putting in a used engine that could be a duff’. Then, after talking it all through with my dad, he told me that he didn’t want me paying interest on a loan, so he offered to help.
I thought the pandemic would delay everything but, to my surprise, Lycoming asked if I could take my engine six months earlier, which I did. I had now gained my black-belt in currency exchange rates, as depressing as they had become. The engine and propeller arrived together and I now had everything I needed to complete the build, or so I thought…
Just after Brexit, I had bought my interior from Lemke Upholstery in Germany (a top-notch job and isn’t the price of the USA companies). I still had harnesses, stick grips, headset jacks, aerials etc to buy – a financial death by a thousand cuts. However, all these items were relatively small (smaller anyway) in price when bought individually, so I was able to keep going at the pace I could build. I had now built everything myself (apart from the parts of the wing panels, some of the body of the fuselage and the front deck of the fuselage as well). Alison, my wife, had also helped me rivet. The canopy had been a real worry, however, Rule 3 applied again.
I was lucky, in that I could temporarily fit my wings while in the workshop, so I thought that I’d have it more or less finished by the time I shipped it to the airfield. Sleap, home of the Shropshire Aero Club, was just two miles away as the crow flies, six as the lorry that shipped my aircraft had to go.
As ever, during the latter stages of build, I was thinking about paint. Not only… do I paint then fly, or fly then paint, but also who could paint it? Also, what paint scheme? Many RVs have bold schemes and my thoughts were no different. I employed a well-known designer from the States. However, discussing something like this by email and the time difference soon took its toll and so I decided that, after paying half the money, I was on my own, again.
Now, there is a fantastic painter at Sleap, but I had two issues with this (three issues if you include that I didn’t have a design sorted). Firstly, the lead time, which was nearly a year, and secondly, the cost. I had simply exhausted myself, and the thought of another chunk of money was just too much. So, I decided to become both a paint scheme designer and painter.
Like a slow version of Neo in The Matrix, I downloaded all the information I could about painting, while simultaneously drawing design after design and asking friends and family their thoughts. Now here’s a thing, after all those decisions that you’re forced to make during the build about options, modifications, suppliers, layouts, colours (panel and interior), I’d actually become fairly fixed in what I wanted, so the design was more or less sorted and so were the colours.
I started painting after having bought a half-decent paint gun (Rule 1), building myself a paint booth area out of polythene sheeting and using desk fans as extractors (Rule 4). I set about painting the wing – I’ve no idea why I didn’t try a piece of aluminium as a test panel, but it all seemed to work out. I had my share of failures with masking and seeping through blanking paper, but after a couple of re-paints I was getting the hang of it, in fact, I was becoming quite comfortable with it all. In all my painting of the two-pack metallic paint, I never got a run. I stuck to the lessons I’d learned from YouTube and it all
went well. The masking had been a pain but the painting itself seemed to go well. As you might know, the two-pack automotive paints that I was using allowed for a great range of colours but needed a top-coat (a lacquer that gives that showroom shine). Again, I followed my YouTube guru and I was happy with my results, in fact so happy that I thought I’d show it off on social media… error!
Accept peoples comments but don’t always act on them. On seeing my photo, one member of my online group commented that if I added just 8% thinners, my top-coat would flow better and I’d lose any orange peel effect. I looked at his profile and he was, indeed, a painter (it was on Facebook… so it must be true). So, in an effort to get that perfect finish and reach for the heavens, just like Icarus, I thinned the top-coat – and ended up with more runs than India in a Test Match!
Make a note of Rule 5 and stick to your guns. Anyway, I rectified what I could and put the rest down to experience.
After finally finding a hangar space, I transported Mike Sierra the six nervous miles to the airfield. A friend of mine had said, ‘you’ll be surprised how long it takes to assemble it and get it ready for flight, it’ll take about six months or so’. Little did he know that I had been working to re-write that plan by doing much of the preparatory work in my workshop, while I had the wings fitted temporarily – clever me, eh? So, after six months at the airfield (he was right and I was wrong, again) my very own aircraft is ready for its first flight.
Am I pleased with the result of my build? Yes, you bet I am. Could I have done things better or differently? Of course I could. However, there are plenty of builders who get a lot of assistance, and some who you begin to wonder if they ever helped to build their aircraft at all. I can honestly say that, apart from perhaps 200 rivets, I
If your aircraft has featured recently in the magazine and has subsequently completed its maiden flight, Project News would like to hear from you at: projectnews@laa.uk.com
built everything. As with anything like this, I had both physical and emotional support. My family, for either encouraging me or just accepting that it has been my dream to build my own aircraft and allowing me to do it. It’s been an emotional journey at times and one that I thought could fail at a few points, but the result has been nothing short of wonderful, I just hope she flies as well as she looks.
Apart from Alison, my wife, who helped me when I needed it and some of my friends at the airfield, I want to single out my dad, who has inspired me and helped me both physically and financially. His love for aircraft and his time in the RAF led to my passion and my belief that anything is possible, I just hope that he is as proud of the result as I am.
Never give up on your dreams. n
Toni Ganzmann headed to Italy to fly the M26 Victor, the first enclosed tandem two-seater from Magni Gyro…
The ultra-light M26 stands at rest on the apron with the tailboom resting on the ground – it’s the typical parked position for the Italian manufacturer’s gyrocopters when they are unloaded. At the small private airfield on the border of the Milan control zone, it is already 32° in the early morning and at an elevation of 400ft, that makes the density altitude 2,300ft. Undoubtedly, these are tough test conditions for the first and only pre-production machine.
So while it’s not ideal that northern Italy is literally cooking, I am here as the first journalist to try out Magni’s
latest product, the enclosed tandem-seater Magni Gyro M26 Victor.
I had arrived at Magni HQ, 40km north-west of Milan the day before. We had been able to do a technical briefing in the cooler evening, protected in the shade of the factory hall. Company founder Vittorio Magni took time to tell me about how the M26 project came to be. “We had developed a closed tandem seater back in 2003,” says the 84-year-old, who is still involved in day-to-day business. “The project, which was then called the XM-21 Aurora, was not continued because open cockpit gyrocopters were in high demand with customers.”
Above The turbocharged Rotax 915 iS maintains its performance even at high-density altitudes.
Above right A double radiator for the Rotax’s coolant is located within the tailboom. An electric fan automatically augments cooling when needed.
Magni only took up the project again in 2015 because, unlike its competitors, this configuration was still missing from its own product range. Because most of the individual components required, such as the entire rotor including the pre-rotation system, were already used successfully in the other models, the M26 did not have to be designed from scratch. The steel frame was slightly modified in the tailboom area, while the composite fuselage and tail unit was adapted to the desired design. Eighty percent of the M26 is made in-house, with just the Rotax engine, DUC propeller, canopy, and the wheels and braking system purchased from outside suppliers.
“We placed particular emphasis on operational safety with the M26,” explains Magni CEO Luca Magni, as he demonstrates some of the most important features of the aircraft. “If the hood is not properly locked, a warning light will illuminate. If the electric parking brake is not activated, the engine cannot be started. When the brake is locked, a warning light illuminates. The rotor brake also works electrically at the push of a button – the operating status is displayed with a light. A special feature is the mechanical blocking of the control stick in the front position for taxiing with the gyrocopter. This is done using a small lever to the right of the seat. A light on the panel shows the status.
The next day has dawned and the temperatures are already high again. I do the pre-flight check together with Luca. Since fully cowled engines often have thermal problems, I’m interested in how Magni deals with this issue. I found out that the double radiator, which is placed diagonally downwards on the tailboom behind the engine, is supported by an automatically operating electric fan. The intercooler of the turbocharger and the oil cooler receive cooling air through side inlets. It’s very effective – I will later notice that the temperature displays never exceed the second third of the green range during the
“With the M26, 80% is made inhouse. The Rotax engine, canopy, DUC propeller, wheels and braking system are from outside suppliers”
flight. Before I get in, I notice the two red tags on the left side of the cockpit: these are for jettisoning the canopy in an emergency. I had been curious if the M26 was suitable for tall people like me? Getting in via a side step is comfortable, but my legs didn’t fit too well under the instrument panel. “We still have to adjust the panel,” says Luca. I remember this is a pre-production machine, and with a little wriggling get comfortable in the comfortable moulded seat. My feet have enough space, thanks to the adjustable pedals. After closing the canopy there is still plenty of space above my head. WIth the harness done up, all instruments and controls remain easily accessible. Centrally located on the instrument panel is a Kanardia EFIS, and above a Garmin GPS navigator. I noted that the displays are not always easy to see due to the strong sunlight and reflections.
As I roll, I notice how light and precise the steering and brakes work. Positioned on the runway, I hold the gyrocopter with the handbrake, which is located on the left of the power lever as usual. Despite all the electrical assistance talked of earlier, the pre-rotation is still carried out manually using the lever on the control stick. At 1,800 engine rpm I pull it and the bendix switch on the main rotor audibly engages.
When the rotor spools up, it takes a lot of force to keep the stick in the middle. I only need to add a small amount of power to achieve 160 rotor rpm. Now pull the stick to my stomach and add a little more throttle until a sufficient rotor rpm of 210 is displayed at just under 2,400rpm. You can pre-rotate up to 280 rotor rpm. I let go of the brake and pre-rotation levers and gently accelerate. Even though we are fully loaded and with the high ambient temperature, we take off after about 100 metres. The torque now needs to be noticeably balanced with the pedals, and the control stick also requires a definite left-hand pressure in order to stay on the centreline. I consider 115km/h to be the best climb speed and see a rate of climb of 1,300ft per minute.
Since there is Class C airspace above us, I enter level flight at 1,500ft agl. At 110km/h, the Rotax 915 iS rotates at 4,200 revolutions per minute with 28.4 inches of manifold pressure. But the M26 can go faster. At the end of the green range we are at 5,350 revolutions per minute
and 36.8 inches. The GPS now shows 185km/h with no wind.
The M26 feels smooth with no noticeable vibrations and the control pressures can now be compensated for so well with the electric four-way trim on the stick that I can even take my hands off the controls. The M26 also likes to manoeuvre. At different speeds I fly full circles and figure of eights with increasing bank angles up to 60°. Of course, to maintain altitude, appropriate power must be applied, but the control pressures remain noticeably low. In order to remain coordinated in the turns, but also with even small changes in performance, the gyrocopter requires sensitive handling of the pedals.
MPronounced floating behaviour
Trimmed out, I pull the nose of the gyrocopter up 30° at 150km/h and let go of the control stick. After an oscillation, the M26 regains stable level flight again. Still at 1,500ft above ground, I hold the controls neutrally and reduce speed. The descent begins slowly, until the VSI shows a descent rate of 1,450ft per minute. Even at a speed of 10km/h as shown on the GPS, the airflow over the tailfeathers is sufficient to remain directionally stable. When recovering by pushing lightly and using a little engine power, I don’t lose more than 100ft.
Magni uses its own 8.60 metre-long rotor blades on the M26, which store a lot of kinetic energy due to their
agni is an established term in the gyrocopter scene – like Grob for glider pilots or Robinson for helicopter pilots. Company founder Vittorio Magni is now 84 years old, but still holds the reins of his company firmly in his hands. Magni has been involved with aircraft his entire life. He worked as a fitter, designer, consultant and pilot for various aircraft and helicopter companies before he wanted to realise his own ideas. Decades earlier, he had put every free minute into examining the blueprints he had purchased for a Bensen gyrocopter. In 1976 Magni took the step of becoming self-employed. Ten years later, Magni Gyro was the leading company in the field of one- and two-seat gyrocopters, making it one of the forefathers of ultralight gyrocopters in Europe.
Even before the turn of the millennium, Vittorio Magni correctly assessed the hobby
of flying and began mass-producing open tandem two-seaters for countries where autogyros could be flown. When ultralight gyrocopters became eligible for registration in Germany in 2003, the company’s personnel had long been prepared for growing demand. Magni’s sons also got on board early. Pietro has now specialised in the production of composite components. Luca is responsible, among other things, for the technology of the gyros. The third generation has now established itself in the company and taken on its own areas of responsibility. Nevertheless, the company founder still comes to the company every day from 8am-5pm, and actively works in production.
The demand for Magni gyroplanes rose
rapidly, with the main markets being France and the USA. Eventually the original production facility became too crowded, so in 2010, still staying in the town of Besnate near Milan, the company moved to new premises and now has 2,000 square metres for the main production areas of composite materials and assembly, plus a further 350 square metres for office space. The company produces around 80% of each Magni gyrocopter itself – Magni feels this is key for the highest standard of quality control. According to sales manager Chiara Curion, Magni has delivered almost 1,500 gyrocopters so far – and has a full order book going forwards. Customers can expect to wait four months from when they place their order, to taking delivery.
weight. When landing, this has an extremely positive effect creating a pronounced floating behaviour. Even on approaches at 70km/h, which is 30km/h less than recommended, I can keep the gyro in the air for a relatively long time after the flare until it settles down smoothly.
Back on the ground, it’s time to gather my thoughts. The M26 is a sophisticated gyrocopter with plenty of performance, but it’s easy to fly and that performance is accessible to all types of gyro pilot. Importantly, it does not offer any unpleasant surprises that might overwhelm the inexperienced pilot in marginal situations. The ready-to-fly gyro should cost 115,000 euros net. Production of the M26 should be well underway by spring 2024, and approval in Germany should take place in 2024. So some patience is still required. (Ed’s note: Steve Boxall from Magni UK advises me that work is already underway on the M26’s UK approval with the CAA). ■
General characteristics
Cruise 170km/h
Vmin 35km/h
Vmax 220 km/h
Best climb 5. m/s at 110km/h
www.magnigyro.co.uk
Wise up to wood: Part 7
In part seven, Dudley Pattison shares more secrets of building with wood. This time with tips for fitting D box plywood…
Most plywood D boxes, I believe, are three-ply and have the grain of the outer faces running spanwise. I know that the Bucker Jungmann and Jungmeister have the grain chordwise, making the fitting of it much more difficult I would think, and involves boiling the ply coiled up in a bucket. You would have to ask Taff Smith of the Real Aeroplane Company about that as it is outside of my experience.
The first thing to do is establish the overall width of the plywood. Use a strip of thin cardboard and wrap around the nose of a rib and mark the start, the centre of the leading edge, and the finish. The start and finish positions will vary from aircraft to aircraft, but are usually something
like 25mm behind the rear face of the mainspar. In my example you will see that the fished girth of the D box is 420mm and the centre of the leading edge is 212mm from the rear lower edge. I believe it is wise to add, say, 5mm to each edge to give you a little tolerance.
Time for a little experimentation. You can see the principle of the folding box, but the gap of the ‘slot’ has to be established to give you a snug fit of the plywood around the nose of the rib. This is critical and must be correct. If the radius is too small, or too large, you will not pull it in with ratchet luggage straps without breaking a rib.
So how do we arrive at the correct measurement for the slot?
The series of sketches to the right show the basic principles of D box ply fitting.
Cut, say, three strips of ply 30mm wide by the full width of the D box. Mark the leading edge centre line. Soak the strips overnight. Set the jaws of a vice to a gap which you think is about right but slightly on the large side. Push one strip in with the leading edge line in the middle of the invert. Put the second strip in with, say, a 5mm packing between it and the jaw on one side. Put the third in with, say, a 10mm packing. Leave them to dry thoroughly, probably a day. Hopefully, when you try them around the rib nose, one will be good. If not, go through a similar process but, with the knowledge gained thus far, it should be easy to get it right. And it must be right.
So, the next thing to decide is how long to make the first section of D box. It must start and finish on a rib. Start from the wing root and cover as many ribs as possible bearing in mind that you are probably using Finnish Birch, the sheets of which are 1,250mm or 1,270mm square. If you have a complication in the way, such as undercarriage fittings, this may slow you down during the actual glueing and fitting of the ply. If that is the case, shorten it to reduce the workload for that piece. Allow a small overhang of the root rib that can be carved back in the future.
When the length has been decided upon, cut your blank, mark a heavy leading edge pencil line, and soak overnight. When soaked and pliable, pull the two edges together near one end and introduce it into the folding box. Try to get the leading edge line central, but if it is out a little it can be centralised when the plywood is down into the box by lifting one edge and pushing down on the other. Obviously, the thinner the plywood is, the easier is this adjustment.
When dry, pull it out of the box and, because you think about these things, put the next section in that you have previously cut and soaked.
Offer the preformed section to the wing. It should be slightly overhanging the root rib and stopping at the outboard end of another rib. I use ratchet luggage straps to pull a D box in. Use as many as you can for each section of D box ply, but they must be on a rib, or a nose riblet, not in the spaces between. These straps can go around the rear spar or trailing edge (if not too flimsy).
Place the plywood and lightly pull a strap somewhere near the middle of it. Add further straps, working from the centre of the plywood outwards. It is ideal to end up with a strap at each end. When you have evenly pulled all straps a little at a time until they are all tight (but not murder tight), check the positioning of the ply.
Ensure that you have the minimum overhang to the rear of the spar, it fully covers the outboard rib and has a small overhang of the root rib. When satisfied with the positioning you need to ensure that when you have glued up you can put it back on the wing in exactly the same position. I do that by drilling a 1.5mm hole through the ply and into the leading edge approximately 50mm from each end. I then take the ply off and open out the holes in it to 2mm. A pop rivet stem is tapped into the leading edge holes so that they project by 25-30mm. So now I know that when the D box ply goes back on the most it can be
Below Placing the ply in the box, locating on the central line is easily done by pulling on one edge and pushing on the other.
out is 0.25mm which is close enough, I think. I prefer to use Aerolite adhesive but, in this instance, Aerodux is preferable. Why? When building the Z1RA I was concerned about protecting the exposed plywood within the D box. The late Tim Cox, who had been my Inspector for my Jungmann, called in one day to pick up some plywood. I told him of my concern over this issue saying that ‘I could never guarantee the accuracy required to mask off where the ribs, spar and leading edge would be so that I could varnish the inside’. He told me ‘not to be so
silly and use Aerodux, lightly painting the whole of the inside surface’. The spar and rib positions could be marked in pencil for a heavier glue coat to just those areas. Brilliant. So simple, and effective.
So, the glue was mixed, applied as described to the ply and applied to the wing structure where required… and the D box offered up to the wing again picking up the pop rivet stems on the way. The luggage straps are refitted. It is a good idea to get these laid out and in readiness before applying the adhesive as, although the
open time on Aerodux is quite long, it does tend to skin over if left for a time on a component, and I always think it may not meld into the adhesive on the other component properly, but this may be tosh…
The next thing to do is to add sacrificial strips of plywood about 12mm wide (I use 2mm modellers Liteply) to the upper and lower surfaces in line with the spars. These are passed under the luggage straps and stapled about 60mm c/c. It may be that the rear edge of the D box ply will need a small clamp at each rib position to ensure adhesion.
Hopefully by now you will have decided on the length of the next section and preformed the leading edge curve. When the section on the wing is cured a 12:1 scarf is cut on the outer end. As the whole scarf is on an outside curve this is simply achieved by pairing the material away with a carpenter’s sharp chisel. The inboard end of the next section needs to be correspondingly scarfed. I do this with a Dremel type tool with a sanding disc. If the preformed D box is clamped to the workbench and the free ‘leg’ is held up the scarf can be formed up to about 30mm from the leading edge mark. When both legs are done the disc is changed for a small sanding drum and the scarf is continued around the leading edge.
I am often asked two questions about D box scarfing. One is why not scarf the end before preforming it? The other is why not glue the sections together and put it on the wing in one piece? If you scarf the end and then soak and bend it I will guarantee damage to the fragile scarf and, as for glueing them all together before fitting…?
I think you would be very lucky to get the leading edge as straight as it needs to be, and just fitting one section at a time can make you feel like a ‘one-armed’ paper hanger.
As you near the wing tip the D box may change in shape as it reduces to the tip. This was the case on the Z1RA. Plywood will not generally accept a compound curve. When I did one pair of wings for this aircraft, I thought I would get away with covering three rib bays, as there wasn’t much of a compound curve. I was wrong and had to use a little Stits epoxy lightweight Supafil to overcome the problem.
On the next pair of wings, I cut it down to covering two rib bays, and still had a small problem. So if I had my time over again I would have gone from one rib to the next, then the next and then the last. It would give a threepenny bit effect, but it would be neat and not buckled. How did they do the Mosquito?
Shrunken covering
To complete the D box it is necessary to trim the rear edge, which, if you remember, will be slightly further back than required as a little wriggle room was added. This is usually done by curving the junction of the D box ply with each rib. Shrunken covering, whether it be doped Irish linen or of the heat shrink variety, always tries to take a straight line between fixed edges. So coming off the main spar position it wants to go in a straight line to the trailing edge. The fact that it also wants to go straight from one rib to the next creates a small conflict in the corner of the covering panel. This is eased by the curve blending the two together. ■
In the sixth part of his occasional series on designing a light aircraft, Mike Roberts looks at calculating loads in the fuselage structure
Ithink we can all agree how very alarming it would be to have an aeroplane’s structure break up around you in flight, and consequently how important it is for the designer to ensure that this doesn’t happen – and this involves a great deal of diligent thought when calculating loads.
In the last article I gave a narrative overview of the load acting on an airframe structure. A key take away from this is that the loads we need to design for are mostly determined for us by the requirements specified in a design code rather, than from experimental data. We simply apply the formulas given in a design code to the geometric and other data of our design, and this gives us our load cases.
When going about designing an aircraft’s structure, you can work out the various loads in the main structural elements i.e. the wing, tail, fuselage, undercarriage and control system. In the last article, I said I would summarise what these loads are, although I cannot show how each set are determined, as this article would need half the magazine to do so.
Luckily the LAA has a very good breakdown in the ‘Designing Aircraft’ section which gives a detailed overview of how you would go about determining a Schrenk lift
distribution approximation and show how the loads vary along the span both as bending moments and shear force.
In this article, I will go through the loading of the fuselage, how to determine the load in a single longeron (assuming a four longeron configuration, as seen in many homebuilds), and I will touch on how you determine the ‘sizing’ for a given load.
In the last article, I showed how I calculate the varying load items along the length of the fuselage. Very similar to how you would go about finding the CofG of an aircraft from a knowledge of the various individual weight items and their positions, we can work out how the forces acting on the fuselage combine to create forces within its structural elements.
The loads produce shears and bending moments or BMs (which is a force x distance, identical to calculating torque, but we do not call it that in structures because a BM causes an element to bend, while a torque is trying to twist it), which are being imparted on the fuselage structure. It is the sum of these BMs that we can later use to determine the load in a set of longerons. Just to note, you can use this approach to design the spar caps in a wing also.
I’ll break this down into a series of steps to help show the methodology. We will consider our fuselage as a beam projecting ahead of and behind the wing main spar.
1.Table 1 shows the moments acting ahead of the wing mainspar and those acting rearward of the spar. These are used separately as I am essentially assuming the nose and tail are cantilevered from the spar. This data was obtained in previous articles.
2. Ahead of the spar: The sum BM of the items causing the nose to be pulled down (in positive G case) –usually due to the amplified weight of the engine under positive G. Already you get an idea of how much load is being imparted on this little aeroplane from the table…
3. Rearward of the spar: We follow the same approach by attaining the sum BM of the item pulling the tail down (don’t forget the tailplane load – this will nearly always be the biggest item in a normal configuration type aircraft.) Again, this is a load pulling the tail end of the fuselage downwards under a positive G case. From Article 5, we see a load acting on the tailplane of 191.5kg or 1879 Newtons.
4. Negative G BM: From the table, do the same thing to work out the BM in a negative G case. Note, as the positive G case is nearly always more than the negative G case, you can often neglect the negative G stressing, assuming the top and bottom longerons are identical in cross-section and similarly supported against buckling. Meaning, if the longerons are made strong enough for the positive case, they are usually strong enough for the negative case. Sometimes this might not be true if there is a bend put into the longeron, in which case the buckling would need to be considered.
I will stop here to explain that the next step (determining the actual load in a structural element, like a longeron) is entirely dependent on the structural design – in particular, how many longerons you have and the vertical separation between them. If two designs have identical rear fuselage bending moments, but design A has a vertical longeron separation of 0.25m and design B has 0.5m, then obviously to react to a given bending moment, design A will have to carry twice the end load of design B – which means twice the cross-sectional area of the longerons.
Surely this is more weight? Yes, in the case of the longeron, but design B has a greater longeron separation which means lighter longerons… but now our fuselage skins are twice as wide! So now design B has heavier and wider skins, which is further increased because wide skins
Bottom
Left Table 1 Moments acting ahead of the wing mainspar and those rearward of the spar.
create larger unsupported panels, which are more likely to buckle due to the shear loads and need additional support! Just goes to show how far you can go down the rabbit hole in search of an ultra-lightweight design! This design has a vertical longeron separation of 0.405m.
In this instance, I will just account for the tailplane load of 1879 N acting on an arm length of 2.0m
5. Longeron load (due to tailplane loading)1849*2 = 3758Nm
3758Nm/0.405m = 9279 Newtons (dual longeron load)
Dual longeron load /2 = 4639.5N
So the longerons will experience a tension or compressive load of 4639.5 N… this equates to roughly 1,040lb in each longeron!
6. Follow the same procedure for the moment acting ahead of the spar.
7. So now we know our loads in the longerons, both in tension and compression. Note, this assumes you are pulling and pushing on the stick! The rear fuselage can also be put into bending because of the rudder, of course! Imagine you pull the stick hard back while simultaneously applying pedal input… this will put additional loads in the longerons in the corners… i.e, top left / bottom right or top right / bottom left. As the fin is usually mostly situated above the fuselage, this would likely also impart a torque on the fuselage. When accounting for these different loads they are typically called ‘combined loads’. You can work this out by doing the same calculation but assume a sideward load due to the fin. Of course, the separation distance between the longerons is not always the same, unless your fuselage cross-section is a perfect square! While the vertical separation id 0.405m, the horizontal separation is 0.56m.
When designing an aircraft, the primary goal that sits above our design goals is, of course, to minimise the weight of each part being designed. Well-optimised structures are usually achieved at the expense of simplicity. A tapered longeron or wing spar cap is harder to make than one of constant cross-sectional area, so if maximum structural efficiency is the goal, you can work out the bending moment down the fuselage and taper the longerons as the load decreases.
The shear load in a fuselage where the loads are trying to cause the material to slip past itself. You can mimic this by placing a sheet of A4 paper on a desk with one hand on each side and bring one hand down while moving the other up. You will see a diagonal crease trying to form. It is due to the shear load being applied that causes this crease or buckle.
You can combat shear loads in several ways, most aircraft use a rigid skin such as plywood, aluminium or composite structures. Earlier designs used diagonal bracing in the rear and forward fuselage. It is often seen on many LAA types within the wing structure for drag and anti-drag bracing, which is also a shear load but acting in a different plane.
Calculating the shear load is also relatively simple. We can simply sum up all our loads used to determine the bending moments. No multiplying by a distance to give a BM.
The load paths in a structure are not quite as simple as assumed here, but this is giving us a conservative answer, why? Well, when working out the loads in the longerons, I
assumed that only the longeron is providing any contribution to resisting the bending moment being imparted on the structure.
In reality, this is not the whole picture as the side skin is attached to the longeron, meaning that the very top and very bottom of the skins are also contributing to resisting the bending moment, but not anywhere near as efficiently – but it is still contributing!
What this means is by accounting for the loads in this way, the design is slightly stronger than it needs to be.
I could work out the contribution by the plywood skin and reduce the cross-sectional area of the longeron accordingly.
Above left and right
Two excellent reference books for aspiring designers are Flying on your own Wings by Chris Heinz and Design of Light Aircraft by Richard D. Hiscocks.
I will explain stressing in more detail in a future article, but to capture the process here, I will go over a couple points.
1. Stress is not the same as load. Two items can be subjected to the same amount of load, but experience very different levels of stress depending on the geometry or ‘sizing’ of the material the load is subject to. A car resting on its tyres is imparting a lot less stress on the tarmac than the same car sitting on axle stands. If the area bearing the load decreases, the stress will increase.
2. Stress = Force(load) / Area . If you’re working with the load as lbs, your area should be square inches. I wasn’t taught imperial in university so I work with Newtons (kilos * acceleration due to gravity (9,81)) with the area being metres square.
3. Stress does not care what the material is. You determine the stress first and then find a material with appropriate properties, or, pick a material and then alter the cross-sectional area to make the stress fall within the material spec.
Example stressing problem
Let’s say we have a piece of material (see point 3) that is 1,000mm long (the length is irrelevant in tension) and 25.4 breadth & 25.4mm in depth.
This material is fixed at one end with the other being pulled by a load of 9810 Newtons (1,000kgf)
So:
A. Stress = F / A = 9810/ (0.0254*0.0254) = 15205530
Pascals or 15.2E6 or 15.2 Megapascals (MPa) If you’re wondering what makes it a megapascal, search powers of 10 online.
B. As point 3 above states, the material does not care what it is made out of yet, whether the part breaks or not is dependent on the material and what stresses it can tolerate.
C. This design is going to be primarily a wooden structure, so I will start with spruce, and see if this material is strong enough.
D. LAA Technical Leaflet 1.16 Material Allowable Strength Data (a very helpful fact check) states (page 36) that
Sitka spruce has an ultimate, parallel to grain (when it breaks!) strength of 64.8MPa.
So, with a stress of 15.2MPa and material allowable of 64.8MPa, I can determine the Reserve Factor (RF) to be RF = 64.8/15.2 = 4.26
E. With a calculated RF, a value below 1.0 means the part isn’t strong enough, anything above 1.0 is, in theory, safe, although for peace of mind we do like some additional meat, but only a little!
At 4.26, my piece of spruce can take 4.26*1,000Kgf = 4,260Kgf of load before the safety factor becomes 1! In theory, anything above 4,260kgf could cause the material to fail. I could also divide the cross-sectional area by 4.26 to get the amount of material required to tolerate the load…
As the value is 4.26, I can make this test piece less than ¼ of the cross sectional area before failure will occur, this also means the part becomes quarter of the weight and quarter the cost(assuming of course the cost is based on volume, which it often is not).
Just as an addition to this example, I want to show the effect that adding a bolt can have to the stressing here. Browsing social media shows several examples of people drilling holes in parts of a structure that the designer did not intend, and unless someone goes about determining the loads and stress of a structure or has access to a designer’s original design calculations, we are not in a position to make the call as to whether or not it is a sensible thing to do.
Let’s start by assuming a designer at ultimate load got the example part to an RF of 1.0 at ultimate load of
1,000kgf. So (0.0254*0.0254)/4.26 = 0.0001514 square metres.
F. Now let’s say we want to bolt a widget to our airframe. We will now add an AN4 (6.35mm diameter) bolt to the example part. This will reduce the cross-sectional area which we know will increase the stress.
G. So, the new area will be 0.0001514 – (0.00635*0.0123) = 0.00007329 square metres
H. Plugging in the same load the material could support prior to the bolt hole being added we get a new stress value Stress = 9810/ 0.00007329 = 133851821 or 133.85MPa
I. It can already be seen that the new stress exceeds the ultimate tensile strength of the spruce with an RF = 64.8/133.85 = 0.48… over half the required material was removed in the process of adding this bolt hole.
The biggest concern is, of course, that the aircraft will no longer have the reserve that is applied to the aircraft during its design. This would mean that the structure is no longer capable of meeting its loading requirements, i.e, if this part was designed for a 6G ultimate load, it would now only sustain 6*0.48 = 2.88 G. A very strong up gust can cause this sort of loading. Of course, this is all hypothetical, but it is worth thinking about how much a structure can be affected simply by adding one bolt that would have totally compromised the aircraft’s structural integrity.
In the next article, I will go over stressing in more detail, some helpful equations and what the stresses are in the longerons rather than a test piece. ■
Including: Understanding, preventing and treating corrosion, corrosion in wheels and wheel bearings, and investigating modified structures
Welcome to Engineering Matters – the section of Light Aviation that is dedicated to discussing all manner of topics concerning both technical and operational aspects of the LAA fleet. We all learn by sharing information, so if you
have anything to say that you think would benefit others, or have experienced an interesting technical issue or component failure, then please contact us with a description of what you encountered and include accompanying pictures. Send your submissions to LAA Engineering at engineering@laa.uk.com
The LAA has a unique fleet of aircraft owned by members and groups across the UK. Based at a wide array of locations, all these hangar and storage facilities differ vastly and are also dependent on your budget and regional circumstances.
Aircraft corrosion can start slowly, but then builds into something that owners and engineers dread to find.
Aircraft corrosion occurs as it does on any other metal surface which is exposed to the oxygen and humidity present in the environment, as well as being exposed to foreign materials like dust and different types of pollutants.
Of course, metal corrosion is accelerated by certain conditions, such as harsh environments.
Given the nature of LAA aviation operations, aircraft corrosion has the potential and opportunity to become an issue. In the end, our aircraft are exposed to the sometimes harsh, but mainly damp British environment, both when flying and on the ground.
Fortunately, there are ways to control how corrosion affects your aircraft, starting by understanding how it happens, and the different types of aircraft corrosion that can be found.
Aircraft corrosion on ferrous metals is the rust that appears on the surfaces and components of an aircraft when the unprotected metal comes into contact with oxygen in the atmosphere.
However, aircraft surfaces and components are made of a variety of metals, and the rust may not appear in the typical reddish colour as most people are used to identifying it.
For example, aluminium is one metal that corrodes differently. Aluminium alloys first show a whitish or grey dulling of the aluminium surface, which then progresses to more and more severe pitting and, if left untreated long enough, eventually the total destruction of the metal.
Left Corrosion revealed on a pushrod in a difficult to inspect area of an RV-6 wing root, after disassembly following an accident.
Corrosion, as we know, is associated with any metal surface being exposed to the oxygen and humidity of the environment. Also, many people understand that the closer to the sea, the worse the corrosion will be because of the effect of the minerals present in the seawater atmosphere. However, there are more causes for corrosion to appear on airframe structures and other aircraft components.
One common factor that causes corrosion in aircraft is foreign material such as dust and grease, acid-filled batteries, or use of incorrect cleaning solutions. All of these elements can cause corrosion in the airframe if they remain in place for prolonged periods of time.
The resulting corrosion damage potentially causes crack propagation and stress accumulation, and can lead to significantly decreased mechanical characteristics for an aircraft. As a result, unchecked, the aircraft can become unairworthy in a short period of time.
The good thing is that the effect of corrosion on aircraft structure happens progressively, and is something that can be picked up at an early stage during your annual LAA Permit Inspection, consequently enabling corrosion to be treated early.
Unfortunately, sometimes corrosion can be hidden due to the nature of the aircraft construction, for example steel brackets inside fabric-covered wings. In these areas an untreated ongoing corrosion process can result in corrosive destruction, potentially causing an aircraft system to fail.
In order to ensure potential aircraft corrosion in LAA is treated and resolved moving forward, it’s useful to understand the materials used in the construction of your aircraft, as well as the types of corrosion they can be exposed to. This way, regular inspection can be incorporated into your LAA owner maintenance programme.
The process of corrosion formation can differ from one metal to another. The process also depends on other factors, such as the type of pollutant, the type of component, and whether there is a conductor involved or not.
There are five types of corrosion potential found in LAA aircraft. It’s not just solely metal airframes, wood and composite types are affected too, any time where metal brackets and fittings attached or bonded to structure can corrode.
● Dissimilar metal corrosion This is one of the types of corrosion where a conductor is involved, as described above. Therefore, this type of electrochemical corrosion can cause extensive pitting damage. It is called dissimilar metal corrosion because it appears when different metal parts come into contact with each other in the presence of a conductor.
Dissimilar metal corrosion often takes place out of sight, making
it particularly dangerous since it can go a very long time before it is identified and treated. So, during inspection it is recommended to look at parts and components in more depth and if corrosion is suspected, disassemble the parts if possible.
Although basic advice, a precaution that owners and Inspectors can take to reduce the chances of this type of corrosion involves not using steel wire brushes or steel wool when cleaning the surface of the any aircraft parts, because this can result in tiny particles being deposited into the surface of the material, which always increases the chances that dissimilar metal corrosion will occur.
● Stress corrosion This occurs in parts that are exposed to high loads, such as the engine crankshaft or the landing gear. It is usually the result of superficial corrosion or scratches that are undetectable
because finding out about the corrosion is often tricky. Typical causes for stress corrosion on aircraft include tapered bolts, press-fit bushings, external loads applied on the components, cyclic loads, or even the manufacturing procedure itself.
During manufacturing processes, internal stress that may cause stress corrosion can be inadvertently induced. Many manufacturing companies carry out production using stress relief procedures. Nevertheless, there is still tension. Stress is externally introduced by riveting and welding on parts including bolts and rivets, clamping, or press fittings. In the case that a small error is made or a fastened part becomes over-torqued, internal strain can arise, thus inducing loads that could result in stress corrosion.
● Intergranular corrosion This type of corrosion is particularly tough because it affects the microstructure of an alloy, which is why it is often related to a lack of uniformity in the microstructure.
Although intergranular corrosion often exists without surface evidence, it can lead to the lifting and flaking of surface metal over time. Extruded components may be particularly susceptible.
Intergranular corrosion is normally worst on high zinc content aluminium like wing spars, stringers, and other high-strength aircraft parts, but can affect all types of aluminium types used in your aircraft.
It is good to know that this type of corrosion is not frequently found, but is a particularly nasty type of corrosion. It can be difficult to detect, and once you see it, it’s too late – that piece of metal is most certainly unrecoverable.
● Surface corrosion General surface corrosion or uniform attack corrosion are the more common forms of corrosion in aviation. Surface corrosion usually results from roughing, etching, or pitting a surface in metal, often accompanied by a powdery deposit of corrosion product.
Surface corrosion can occur either through direct chemical or electrical attacks. Sometimes corrosion spreads beneath surface coatings and is not detected by the rough surface or the powdered deposit.
Surface attacks (or corrosion) are usually caused by exposing parts of the aircraft to oxygen for longer periods.
The most common causes include, but are not limited to:
● Poor quality paintwork
● Inadequate preparation work by those carrying out the paint job
● Various contaminants and acids
● Constant exposition to very high humidity conditions.
● Filiform corrosion This corrosion is common in aircraft because it mainly occurs on aluminium surfaces that have not been through the
proper pre-painting process or covered with a corrosion-resistant alloy
In other words, the surface is not prepared for the polyurethane paint used on aircraft.
The moment it appears, it looks like fine, worm-like lines of corrosion under the paint that will eventually lead to bubbling and flaking.
Consequently, filiform corrosion is easy to recognise and it is actually easier to prevent than it is to remedy, something which is not common with other types of corrosion.
There are many ways corrosion can occur in aviation, but there are also good practices to avoid corrosion becoming a hazard.
Aluminium and magnesium alloys are frequently used in LAA aircraft, and they do not show the typical colour seen in steel alloys when they corrode. Therefore, light surface corrosion can be disregarded, but the alloy structure may be affected and a bigger issue may appear in the longer term. So, thorough inspections are always recommended.
Also, dissimilar metal parts and two mating surfaces should not be cleaned with a steel wire brush since this may induce dissimilar metal corrosion.
As a general rule, preventing the aircraft surfaces and components from having contact with corrosion-producing agents present in the environment they operate is the best way to avoid corrosion formation.
However, this is not always possible, especially in a corrosive environment like coastlines or damp hangers.
LAA builders and restorers should use good quality paints and surface coatings to avoid surface corrosion, and if a requirement of a build or restoration, stress relief heat treatments to avoid stress corrosion cracking.
It is always a good practice to continue to carry out regular inspections to verify whether any corrosion inhibitors are needed and ensure the airworthiness of the aircraft, in particular when dealing with aircraft that have had corrosion issues in the past.
There are many products available on the UK market to prevent corrosion or the spread of corrosion.
● ACF 50
● LDS3 Rust Inhibitor
● XMP Metal Guard
● Ambersil Corrosion Inhibitor
● XCP Professional rust blocker
The various different manufacturers will give different advice on the use of their products. In the end, use what works best for you and ultimately what stops the corrosion!
Van’s RV-6 main wheel bearing corrosion
Thank you to Inspector Toby Willcox for bringing this issue to our attention. It must be remembered that a great number of the LAA fleet have similar wheel bearing assemblies, so this is very relevant to other aircraft owners, not just those of RVs.
In use, the aircraft wheel breathes and this can potentially affect bearing life, particularly if your aircraft is parked for a couple of weeks, or worse, months which happens more than you think with LAA aircraft.
As most people do not appreciate there is a lot more going on than you think when you take to the air in your aircraft. For example, the wheels of your aircraft breathing! So how does the wheel breathe? This happens due to changes in temperature. When applying the brakes the hub heats up, the air inside the hub expands and breathes out through the seal and when it cools down it breathes in. The air coming in brings in a certain amount of moisture and this moisture will condense on the inner walls of the wheel. There will of course be different heat and cooling levels in drum brakes and disc brakes.
rust etching forms a stress point which dramatically lowers the fatigue life and is most common with a rough running bearing.
Also, what also needs to be remembered is the wheel assemblies and bearings of your aircraft are down in the mud and the damp and are not particularly accessible, even more so if spats fitted. It must be ensured that the wheel assemblies are removed and inspected on a regular basis.
So, what is the solution? There are a couple of simple actions that can reduce the build-up of water droplets on the inner walls of the wheels.
1. The simplest and more enjoyable option is to fly as much as possible so water does not have sufficient time to etch the bearing tracks before it is wiped away by the bearing rollers turning.
When the wheel is heated up again it is not hot enough to vaporise all of the water and on cooling more water is added, until over a few cycles or longer small droplets form and it is these droplets that get into the bearing, which will form small rust lines if left sitting. Commonly visible as dark staining at roller spacing. This
2. By applying a thin layer of grease to all of the exposed inner surfaces of the wheel this will reduce water droplets forming on the surface keeping the moisture suspended in the air.
3. Improper maintenance procedures or using the wrong grease. May have played their part in the damage to the bearing.
It is an important factor that wheel bearings should be checked during maintenance cycles and re-packed with grease on a regular basis. It is also important to ensure that the bearing is properly packed with grease. Not just smeared grease on the outside of the bearing, without packing grease behind the cage.
Also ensure the correct grease for the main wheel bearing application is used, it is important to check the recommended greases as over the years they have changed and, in many cases, improved.
Above Comparison of new bearing and of a bearing removed from service.. Above Corrosion damage to wheel bearing indicating poor maintenance.I am pleased to welcome six new LAA Inspectors – who attended LAA HQ for Inspector Assessment Days in early March.
Ed Stinton: Ed has restored two crash-damaged Avid flyers and one crash-damaged MW7. He also restored a barn-find ARV Super2, including Rotax engine conversion. He has been involved with numerous RV builds, including his own Harmon Rocket (a modified Van’s RV-4). Ed has held CAA approvals for welding carbon steels. He is experienced with fabric, wood and composites, Wankel Rotary and Lycoming engines. Ed has worked with both two-stroke and four-stroke Rotax engines. He has worked for MidWest engines, Diamond Aircraft and numerous maintenance organisations in the past.
Clive Sutton: Clive is ex-RAF, a chartered engineer and a BMAA Inspector. He prefers composite and metal airframes and Rotax four-stroke engines (especially the Europa type). He has little experience with two-strokes or Continentals / Lycomings or wood and fabric aircraft. Clive is ready to travel a maximum of an hour – and Wellesbourne, Bidford and Coventry are within easy reach for him.
Morne Scheepers: Morne has been flying since 2005. He has been involved in tube and fabric, composite and metal kit-building, repairs and maintenance. He is the owner of Ventura Aviation and an independent Rotax Service Centre, specialising in ‘Line’ and ‘Heavy’ Maintenance on 912UL/ULS/ iS, 914UL, 915iS and 916iS. He specialises in the Sling 2/4/TSi and the Sling high-wing aircraft, as well as the KFA Explorer and Safari kit planes. Morne also has a lot of experience in other light aircraft.
Tom Woodhouse: Tom has worked as an aircraft engineer since 2001, with a wide variety of experience on wooden, metal and composite aircraft, as well as Gipsy Major, Rolls-Royce Merlin, Continental, Rotax and Jabiru engines. In particular, Tom has considerable experience in the field of vintage / classic aircraft. He has previously worked as the production and maintenance manager of a GA maintenance company, he is skilled in sheet metal work.
Steve Wilkinson: Steve served for 15 years in the Royal Navy from 1972-87, including a five year engineering apprenticeship. He started gliding in 1979 and became an instructor and BGA Inspector in 1986. Steve obtained a PPL in 1999 and has been flying aerotows in various aircraft, as well as at various gliding
sites since then. He was also a FI(A) TMG for nine years (now lapsed). Steve became a gliding ‘chief engineer/ARC signatory’ in 2008 and subsequently a Part 66 L1 in 2020 for Part 21 sailplanes. Steve has held various gliding club positions including CFI (TVGC) and chairman at Wolds Gliding Club, where he planned the purchase and build of a Eurofox glider tug in 2018. Steve has had much involvement in Eurofox/Rotax/Edge performance engines in the last five years, as well as other Group A tug aircraft and Venture motor gliders previously.
Steve Hodge: Steve has been part of the aviation trade since 1997, when he joined Arrow Aviation Services as a trainee. He pretty much learned his entire trade there and was very fortunate to have worked with a wide variety of components, from engines and propellers, to wheels and brakes, with a lot of vintage aviation thrown in too. He is now the owner and accountable manager of his own company, SOAR Aviation, a CAA Part 145 approved facility. He continues to provide the aviation industry with what he hopes is thought of as an honest, reliable, friendly and cost-effective service. He has always been involved with the LAA and enjoys serving the LAA community.
Inspector training seminars
On 14 March, I ran an Inspector Training Seminar at the National Space Centre, Leicester, with the assistance of my colleagues – Andy Draper (head of flight test) and Miti Ghosh (design engineer).
Sixteen Inspectors were in attendance, as part of the mandatory requirement for all Inspectors to attend training once every four years. We had a great day – lots of knowledge shared and interesting discussions!
It’s always been like that!
The ‘it’s always been like that’ phrase is all too often heard during aircraft inspections. If during an inspection something just does not look right, it may be prudent to look a little harder and do some research.
During an inspection of the internal wing structure of a Taylor monoplane prior to re-cover, it was found that both the port and starboard wings had the lower boom of the rear spar cut away.
From the geometry of the push rod tube it could be assumed that this was done to enable the aileron to achieve its full upper limit. The push rod quadrant had also been adjusted to allow full movement.
It may also be a factor that the aileron pushrod attachment had been fitted too low on the aileron allowing the pushrod to come into contact with the lower rear spar boom.
Recently issued instructions for continued airworthiness. (Please check the LAA website for further details).
Supermarine Aircraft MK26 and MK26b
MTD-01-2024 issue 2
TADS 324 Applicability All Aircraft
Geometry / symmetry checks to be carried out to ensure correct alignment of fin assembly and rigging of rudder.
LAA Project Registration
Kit Built Aircraft
Plans Built Aircraft
Initial Permit issue
Up to 450kg
451-999kg
1,000kg and above
Permit Revalidation
(can now be paid online via LAA Shop)
Up to 450kg
451-999kg
1,000kg and above
Factory-built gyroplanes*
(all weights)
The aircraft was built in 1973 so the information on the original build was quite limited in detail, but the cut away spar boom was suspected to be a field fix!
Two other Taylor Monoplanes were checked and both had clearance with no contact with the lower spar boom. The original build drawings were checked for clarity, the drawings are not very detailed, typical in early home build drawings, but there was no suggestion or notes in the drawing indicating it is appropriate to cut away the rear spar boom at any time.
It is an important factor during inspections that if you spot an unusual piece of construction or damage, that you follow it through and investigate, especially when an aircraft has been flying for many years. It hasn’t apparently been a problem up until now, doesn’t mean that you should ignore an obvious defect!
After a repair schedule was submitted to LAA Engineering, the Monoplane was repaired and continues to fly today, giving the grass roots flying smile on every flight.
It has been found that there is potential for the fin and rudder of the Supermarine Spitfire Mk26 and 26B to be misaligned during build, i.e. so that it is not pointing directly fore and aft, parallel with the aircraft centreline. This could occur due to a build-up of tolerances in the fin and its attachment and the build sequence described in the build manual, possibly leading to a misrigging of the rudder and
failure to achieve the desired range of rudder movement. This could possibly result in degraded controllability in flight and on take-off and landing.
Issue 2 of this MTD was raised to clarify an anomaly in the required rudder deflection figure stated on Supermarine drawing 9-012 and to include a requirement to check and adjust the tailwheel steering break-out angle.
£350
£50
£700
£800
£900
£230
£280
£310
£310
*Gyros note: if the last Renewal wasn’t administered by the LAA, an extra fee of £125 applies
Modification application
Prototype modification
Repeat modification
minimum £100
minimum £50
Transfer (from C of A to Permit or CAA
Permit to LAA Permit)
Up to 450kg
451 to 999kg
1,000kg and above
Four-seat aircraft
Manufacturer’s/agent’s
£280
£320
£360
type acceptance fee £2,000
Project registration royalty
Category change
Group A to microlight
Microlight to Group A
Change of G-Registration fee
Issue of Permit documents following G-Reg change
Replacement Documents
Lost, stolen etc (fee is per document)
£50
£200
£200
£60
£25
PLEASE NOTE: When you’re submitting documents using an A4-sized envelope, a first-class stamp is insufficient postage.
Andrew Caldecott rounds up Struts news and views
Hopefully you are all making good use of the longer days – here’s hoping the weather will be kinder to us than over the past months. As part of a drive to highlight what our UK-wide network of Struts and type clubs can offer LAA members, we are asking every Strut to write 600-700 words on what they are currently doing, and include a selection of photos of their members and the aircraft they operate. With more than 30 groups, this should be a great opportunity to promote the affordable flying opportunities that are on offer. Please send your material to acss@gmx.com
The YES facilitation for ‘2,024 in 2024’ continues – the youngsters we reach out to today are (potentially) our members tomorrow! By introducing aviation to any youngster, we are hopefully opening the door – both to dreams and careers. Can you be a part of this introduction? Do you know a youngster who may be inspired by a visit to your airfield or even a short flight?
Keeping the system simple, Check the YES website and refer to the facilitate pages. Fulfil the ‘safe requirements’ and fly. Complete the ‘flown data’ and email the details to the YES link, and YES will add the numbers to the total – Aim 2024. Please join YES and remember membership is FREE. Being involved costs nothing to help develop our Young Aviators to keep GA alive and progressive. ■
Please contact your local Strut to check the details before attending the calendar events.
Andover Strut: Spitfire Club, Popham Airfield, SO21 3BD. Contact Bob Howarth email: bobhowarth99@ btinternet.com Phone no. 01980
611124
Bristol Strut: Contact: chairman@ bristolstrut.uk www.bristolstrut.uk 2 Apr
CAA Airspace Infringement, TBD May, Fly-Out (Jet Age Museum, Staverton), 4 June – Strut Social Evening, 8/9 June – Strut Fly-In, Oaksey Park.
Cornwall Strut: The Clubhouse, Bodmin Airfield. Contact Pete White pete@aeronca.co.uk 01752 406660.
April 20 Cornish Pasty Fly-in, May 4/5
Scout Weekend: Badges & Flying Saturday. Open Day Sunday
Devon Strut: The Exeter Court Hotel, Kennford, Exeter. Contact: david. millin@sea-sea.com
Evening Events at the Exeter Court Hotel, Kennford, Exeter, from 1930. Please join us for a meal before a meeting starts. 11 April, Allie Dunnington – Record Chasing Balloon
Aviatrix Devon Strut Fly-ins, 2024 Eaglescott, tbc 22 June – Farway Common, 20 July – Branscombe
East of Scotland Strut: Harrow Hotel, Dalkeith. 2000. Contact: Tim Raynor hipe@btinternet.com
East Midlands Strut: Meeting on the first Tuesday of the month on Zoom until further notice due to venue availability. Contact: tonyrazzell2@ gmail.com We also have a Facebook group and upload recordings of some meetings where we have speakers.
Gloster Strut: Contact: Harry Hopkins phone 07902 650619 harry.hopkins@ talktalk.net
Highlands & Islands: Contact: b.w.spence@btinternet.com 01381 620535. Spring Fly-in 5 May
Solstice 22/23rd June
Sollas Beach Fly-in 15-17 August, LAA Highland Strut Fly-in 27/28 JulyLocation to be confirmed (Dornoch or Easter).
Kent Strut: Contact: Steve Hoskins hoskinsltd@outlook.com 07768 984507.
LiNSY Trent Valley Strut: Trent Valley Gliding Club, Kirton Lindsey. pilotbarry1951@gmail. com http:// linsystrut.wixsite.com/website
North East Strut: There are no meetings at present, but if you would like to help to get the NES operational again please get in touch with the Strut Coordinator, David Millin. david.millin@ sea-sea.com
North Western Strut: The Clubhouse, Boysnope. 1400. Third Thursday each month. Contact: cliffmort@btinternet. com 07813 497427.
North Wales Strut: Caernarfon Airport, Dinas Dinlle. First Sunday of the month – HEMS Bistro Café. 1300. Contact: Gareth Roberts gtrwales@gmail.com 07876 483414.
Oxford Group: Sturdy’s Castle Country Inn, Banbury Road, Kidlington, OX5 3EP. Second Wednesday each month. Contact LAAOxford@gmail.com www.oxfordlaa.co.uk April 10 Lucy Wootton: LAA Inspector Update.
Redhill Strut: The Castle, Millers Lane, Outwood, Redhill, Surrey, RH1 5QB. Pub contact- 01342 844491. Third Tuesday of each month, meet at 1900-1930. Contact: david@milstead. me.uk
Shobdon Strut: Hotspur Café, Shobdon Airfield, Hereford HR6 9NR. 1930. Second Thursday of the month. Contact: Keith Taylor bushebiggles@ sky.com
Southern Strut: ‘Longshore’, Brighton Rd, Shoreham-by-Sea BN43 5LD. First Wednesday of the month 1930 for 2000. Contact palmersfarm@sky.com
Strathtay Strut: Scottish Aero Club, Perth Airport, Scone. Scone Clubhouse. Contact: keith.boardman@ peopleserve.co.uk 07785 244146.
Suffolk Coastal Strut: Earl Stonham Village Hall, IP14 5HJ. www. suffolkcoastalstrut.org.uk/flyin/ Contact: Martyn Steggalls events@ suffolkcoastalstrut.org.uk 07790 925142. 17 April Strut AGM
The Joystick Club: Activities throughout the year. Pedal planes and simulators at Old Warden Air Shows. Contact: Mike Clews, m.clews@sky. com. 07775 847914. www.joystickclub. co.uk
Vale of York Strut: Chocks Away Café, Rufforth East Airfield. 1900.
Contact: Chris Holliday 07860 787801
valeofyorkstrutlaa@gmail.com www. valeofyorkstrutlaa.wordpress.com
Wessex Strut: Monthly meetings at Henstridge Airfield Clubhouse See www.wessexstrut.org.uk for details of upcoming events. Local fortnightly walks are also organised. Contact Neil Wilson at chairman@wessexstrut.org.
uk 12 or 19 April Henstridge barbecue, 26 May Wessex Strut fly-in, June Possible fly-out to Sandown.
West Midlands Strut: There are no meetings at present but if you would like to help to get the WMS operational again please get in touch with the Strut Coordinator, David Millin. david.millin@ sea-sea.com
West of Scotland Strut: Various locations in the Greater Glasgow area. Contact: Graeme Park graemepark01@gmail.com
Youth & Education Support (YES)
– YES also available for Strut talks/ presentations. Contact: Stewart Luck captainluck@hotmail.com (Contact 07974 188395 to volunteer.)
• Please contact your local Strut to check the details before attending the calendar events.
OTHER DATES
Beagle Club: 20 Apr Beagles join VPAC in Sleap, 6 May Committee meeting, Gamston
11 May Hot Dogs & Dogs, Blackbushe. Aeronca Club of Great Britain: April 27 Turweston – VAC Fly-in PPR 01280
705400
18 May Bodmin In Bloom Fly-in. PPR
01208 821419
Vintage Piper Aircraft Club: 40th anniversary year, 20 April Sleap, 25 May Perth
Derek Pake relishes a challenge, and scooped top prize with his co-pilot in last year’s Pooleys D2D! And says how being an LAA member has allowed him to hone his aviation skills…
Why aviation, what started your interest?
I can remember being interested in aviation since I was about five years of age. I loved watching aircraft, reading about them in library books, and making Airfix models throughout my childhood. I guess I’ve just never grown up!
Where did you take your very first flight?
My very first flight was when I was 11 years old on a family package holiday in 1973, on a Britannia Airways Boeing 737-200 from Glasgow to Alicante. I was quite impressed that it had my initials on the tail and the nose gear doors: ‘DP’. The aircraft was G-BADP. The first flight in which I got to take control was a RAF Chipmunk T10 from RAF Shawbury, when I was 14 and at Air Training Corps
summer camp. My first solo was aged 16 in a Kirby Cadet T3 glider, also with the Air Training Corps.
Probably just a coincidence but the actual airframe, XA302, is now displayed in the RAF Museum, Hendon. My final ‘first’ flight was going solo in a powered aircraft, a Cessna 150 at Bournemouth in 1982.
Tell us about your personal learning to fly journey?
Like many young men, my ambition was to be a fighter pilot in the RAF, but sadly my eyesight didn’t meet the standards, although it was good enough for a CAA Class 1 Medical. With no airline sponsorship opportunities around in 1981, and an offer from the RAF to become either a Navigator or an Air Traffic Controller (ATCO), neither of which would let me be a pilot, my backup plan was to become an ATCO with NATS, as it offered PPL training as part
of the Cadetship scheme. I would get paid to learn to fly and earn more money than the equivalent RAF ATCO job, so it was ‘win-win’ when I was successful in getting a NATS Cadetship.
After eight months of basic Air Traffic Control (ATC) training, I set off in January 1982 to spend four weeks in some miserable winter weather at Bournemouth Flying Club learning to fly in Cessna 150s and 152s. Fortunately there were enough good weather days to get it all done and I finished the course in a respectable three weeks – with a shiny new PPL.
During my Cadetship, I was streamed for Area Control duties, which meant working at an Air Traffic Control Centre such as London Centre at West Drayton, or Scottish Centre at Prestwick.
My first ‘validation’, which is the ATC equivalent of a type rating, was at Scottish Centre in the summer of 1982.
As I was only about halfway through my ATC College training, I hadn’t done a Radar Control course at that stage, so the validation was for a Planning Controller, responsible for accepting and offering traffic in and out of the ATC Sector with correct separation, as well as coordinating flights by telephone with other units.
I also validated as a Flight Information Service (FIS) Controller, a non-radar position, which was carried out by ATCOs rather than Flight Information Service Officers (FISOs) back in those days.
The following year I successfully passed the Radar Course and was posted permanently to the Scottish Centre as a working ATCO. After several years I validated on all the sectors there, meaning that I could be working traffic within the Scottish TMA one day, perhaps high level trans-Atlantic traffic the next day, or traffic outside Controlled Airspace or FIS the next. I was lucky to maintain validations all the way through my 41-year career, although with the expansion of the Scottish Centre when Manchester Sub Centre and some Swanwick Sectors moved in to the operation, it was impossible to be
valid on everything, so in the end I was only doing TMA and Upper Airspace tasks.
Along the way I also had other roles in the job, including as an Instructor and Examiner, as well as some management roles. The latter involved five years in charge of the ATC Procedures department, with lots of interaction with other ATC units, the Ministry of Defence, Airline Operators, the CAA, and other airspace users such as the British Gliding Association and General Aviation (GA) representatives. On the back of that, I was then seconded to the NATS HQ at CAA House in London for a year, a varied and interesting time, which involved working with bodies such as the CAA and Eurocontrol on projects like Basic Area Navigation (BRNAV) and Reduced Vertical Separation Minima (RVSM) initiatives, both of which I saw through to implementation.
Being a GA pilot, I also worked on changing policy for the classification of Airways and other Controlled Airspace from the Class A, which was everywhere back then, to allowing Class D where appropriate. The first Airways to change were part of a project I was involved in back at Scottish Centre when some of the Airway segments between Dublin and Aberdeen were changed to Class D
until 2019.
to allow access to VFR traffic. Arguably the UK still has a bit of a way to go to a more pragmatic Airspace structure but at least I, along with others, helped to kick start some change.
After the office detachments, I became a Supervisor on a Watch for the last 21 years of my career, albeit with some further diversions in to a project putting together ATC user requirements and working with ATC equipment suppliers in Spain for the new ATC Centre at Prestwick, which became operational in 2010.
I was the last ATCO to make a radio transmission from the old building at Atlantic House, as I transferred it to the ATCO who was sitting in the shiny new Operations Room across the road. My final extra curricular role was spending five years as the NATS Civil Military Liaison Lead, primarily working with MoD staff at RAF Northwood and RAF Waddington to assist them in putting in airspace
Below
and procedures for large scale military exercises, such as Joint Warrior and Cobra Warrior, as well as providing aircrew briefings prior to each exercise start.
It was a really enjoyable side job, with lots of travel and visits to RAF and Naval bases up and down the country.
Sadly, an organised trip in a Hawk T1 from RAF Valley fell through as the Squadron was axed in defence cuts on the day we arrived and all flying was cancelled.
I did get an hour in its Hawk simulator, so at least I got to fly ‘virtually’ under the Menai Bridge and along the Mach Loop.
RAF Lossiemouth was also very kind on my visits and often arranged for me to fly its Typhoon simulator, which was surprisingly easy to fly from a pilot’s point of view. I never managed to crash it, but did really struggle to hook up to the Airbus A330 Voyager air-air refuelling tanker no matter how many times I tried, mainly due to Pilot Induced Oscillation (PIO) as I got the probe within a few feet of the basket. Luckily, there was always enough fuel to get back to base.
How long have you been an LAA member?
Below (right) After a ground loop accident, G-JBTR was expertly rebuilt as G-WEEV, by Toby Willcox and Stephan Meester, at Targett Aviation.
When I bought my Van’s RV-8, in partnership with fellow owner Hamish Mitchell, I joined the LAA. That was around six-and-a-half years ago, and prior to that I flew Cessnas and Pipers, so had no exposure to Permit aircraft operations or LAA privileges.
What has the Association enabled you to do?
The LAA has been a great eye opener for me, as there is
a real wealth of knowledge in the membership, allied with a superb sense of camaraderie and a ‘can do’ attitude along with a willingness from everyone to help their fellow fliers.
Being able to do our own maintenance, assisted by our excellent Inspector when needed, has also been a wonderful opportunity to learn more about my aircraft and practise new skills.
While I’m not sure that I’d have either the competence or the patience to build my own aircraft, I do really enjoy the opportunities to tinker and fettle when required to try and keep everything in good shape. My co-owner also owns a certificated aircraft and comparing our RV-8 maintenance costs with those carried out by licensed engineers is just jaw dropping, so that’s definitely another plus for being under the LAA regulations.
That is of course no criticism of the licensed engineer world. It’s just a totally different and commercial regime.
You and your co-pilot, Kate Turner, have just been awarded the top prize in the 2023 Pooleys Dawn to Dusk challenge. Tell us a little bit about your entry. Will you be entering this year, and what would you say to others who are thinking about entering? Having taken part in the D2D Challenge in 2022 and coming joint third, I just had to enter again in 2023 and try to do a little bit better. It really is an enjoyable challenge and allows you to test your skills, both pre-flight in planning and in managing the tactical execution of the flight during the actual day, including dealing with any untoward events.
For my 2023 entry, we decided to follow the route of a US Army Air Force (USAAF) Boeing B17, which departed from Northern Ireland in WWII, and was carrying the head of the USAAF in Ireland and the head of the neutral Irish Free State Military Intelligence Corps. It flew around the coast of the Irish Free State (also known then as Eire, and now the Republic of Ireland) in a clockwise direction to check on the location of newly erected whitewashed ‘EIRE’ navigational markers located at each of the 83 Irish Coast Watch Service Look Out Posts (LOP).
These markers were put up so that wartime pilots would know that they were overflying neutral territory and, with the addition of the LOP identification number to the marker, they would be able to reference the location on a USAAF produced map to determine their exact location,
Left Wee Vans raises thousands of £s each year via donations from her passengers, in memory of Vanessa Riddle. Vanessa died just before her 18th birthday and was nicknamed ‘Wee V’, hence ‘The Spirit of Wee V’.
Far left G-WEEV raised funds for Aerobility with her ‘Paint-a-Plane’ competition.
navigational beacon at RAF Nutts Corner, near Belfast, to set a course in to Allied airspace and a safe landing. An early form of GPS (Ground Position System) if you like… The remains of most of the LOPs are still visible, however, only about 30 of the ‘EIRE’ markers remain.
Some have been restored by local interest groups and are very easy to see, while others are slowly disappearing as nature reclaims them and are very difficult to see from the air. We did try though.
recommend that you give yourself a reasonable period of time between completing the flight and the competition closing date.
The more time and effort you can put into your entry, the more detailed and polished it can be. Take lots of photos and videos too, if you can, and put a good selection in your log. A picture literally does paint a thousand words. I’ve also heard that at least one of the judges loves Curly Wurly chocolate bars, although I’ve not resorted to the bribery route – yet…!
Our flight was from Prestwick, Scotland, and returned there around 13 hours later. The total flying time was 7 hours 45 minutes airborne, with 1141nm covered at an average ground speed of 147kt. We stopped at Waterford for fuel and breakfast, then visited the three airports on the Aran Islands (Inisheer, Inishmaan, and Inishmore), mainly because they were on the way, are very scenic and it would be a shame not to get them in the log book.
Afterwards we had another fuel stop, this time in Sligo, before dropping in to Enniskillen, and then finally award winning and stunning Donegal Airport for crew rest and some dinner. Our entry log was a 116-page write up of the planning, the flight, and historical and interesting facts about the points overflown and recorded on video and supported by numerous photographs.
I’ve already planned another interesting and challenging task for 2024, so need to start thinking about when to actually do it. Regardless of whether I can win again or not, it will be a tiring but enjoyable day. For anyone thinking about it, I’d say definitely do it. You can find out what’s required on Pooley’s website.
Regardless of what you choose as the topic of your flight or the number of hours required to fly it, you will be setting yourself a challenging but rewarding day, pushing yourself and your aircraft to the edge of the limits with which you are comfortable.
As the entry will be judged on the log and supporting material you present to the judging panel, I’d highly
Top Derek’s favourite part of flying is putting the massive Van’s grin on the faces of passengers, especially those who haven’t flown in a light aircraft. And it appears that Hughie from Ireland concurs!
Above Off to fly in the Spitfire TR9 at Goodwood.
Total number of types of aircraft and (rough) hours you have flown. Around 800 hours total time and seven types flown as PIC. I’ve taken the controls on probably another 15 types as PUT or as part of an experience flight.
Any favourite or less liked types that you’ve flown? If so, why?
I am very biased but can’t see past the RV-8 as my favourite. Reasonable short field performance, long legs and fast cruising speed for away trips, and of course it’s aerobatic. What’s not to like ?
I also enjoyed flying the Spitfire T9 and an Extra 300 at Goodwood. Both are iconic but handle totally differently from each other. I get a grin just thinking about them. I’ve never really experienced a ‘bad’ aircraft. They are all different and if you can manage your expectations, then even a ‘spamcan’ can give you lots of airborne pleasure. I just love being airborne.
Current and past (privately) owned aeroplane(s)
Currently I own a 50% share in a Vans RV-8 G-WEEV, known affectionately as ‘Wee Vans’. Previously I was a shareholder in a group which operated over the years various Cessna 150, Cessna 152, Piper PA28 Warrior, PA28 Archer, and PA38 Tomahawk aircraft.
Your best aviation moment and flight – and why?
First solos are always memorable, of course, but these are really individual moments and you don’t get to share the joy of flying with others. My best aviation moments are always taking up non-pilots and seeing the grins on their faces when we get back on the ground, more often than not followed by a request to do another trip when we can.
I have several ‘frequent fliers’ who keep me company when I’ve got a spare seat going begging. It’s a shame to waste the freedom and satisfaction of being airborne if you can share it. One of my best aviation moments –when I wasn’t the pilot – was on a trip with the US Air Force in a KC135 tanker aircraft from RAF Mildenhall, heading out to refuel F111 fighter bombers over the North Sea. We had a few hours to kill before the ‘customers’
were due to appear, so the pilots flew for about 30 minutes doing parabolic manoeuvres while the rest of the crew and myself spent the time ‘space walking’ up and down the cabin in zero G conditions. Great fun, but probably frowned upon by the top brass I expect… if they had known.
Any aviation heroes? Who and why?
A couple stick out for me. Firstly, Eric ‘Winkle’ Brown for his outstanding skill and dedication as a test pilot. An impressive number of aircraft flown, the first to land a jet on a carrier, and a total number of carrier landings that will never be beaten. His courage in flying undocumented and potentially lethal captured German aircraft, including the ME262 and the ME163 Komet, must have taken nerves of steel.
Secondly, John Farley of Harrier fame. A superbly knowledgeable and expert pilot with a grasp of aerodynamics second to none. A consummate gentleman and a great matter-of-fact raconteur. It was my pleasure to meet and listen to both these heroes of mine several times over the years.
Any favourite aviation books?
Above
Below
Fate is the Hunter by Ernest K Gann is, of course, a real classic which I love reading over and over. Aerobatics by Neil Williams is good for improving aerobatic skills, and then The Killing Zone by Paul A Craig is excellent for lesson learning to try and prevent yourself from becoming a ‘safety statistic’.
Any lessons that you’ve learned from certain moments / flights?
I think the main lesson I always learn (and seem to forget) is that flying activities always take longer than you think! Whether it’s having to clear unexpected ice off the wings, trying to get a cold, or indeed very hot, Lycoming to kick in to life, meeting fellow pilot friends down route and simply chatting for much
longer than anticipated, or just going where the mood takes you while bimbling along, there are always things that are going to add on 10 minutes, 30 minutes, or an hour to your expected schedule. Time to spare? Go by air!
Do you have any ‘fantasy hangar’ aircraft or vehicles that you’d love to own / try?
I’d definitely want a Pilatus PC12 in my hangar for long trips to Europe, a Carbon Cub on bush tires for off-roading in Scotland, a Beaver on floats for fishing and beach days, and a warbird of any description. A big Lotto win might be needed though to keep them in fuel, let alone pay for them.
Do you have other non-aviation hobbies / interests?
I can’t partake as much these days, as my adrenaline junkie days have taken their toll on my knees, but I do enjoy hillwalking and mountaineering as well as skiing. I’m more likely to be found out on long walks with my dogs now, though.
Any advice for other aircraft owners and pilots?
Try and find ways to keep your passion up for flying. I realise that it’s easy to fall into periods of inactivity or lose interest, which could be due to finances, life pressures, or any one of many other reasons.
Aviation is, however, a good place to build up networks and find people with similar interests, so think about flying with others in your aircraft or theirs to share costs and experiences, or by meeting up with pilot friends regularly at other airfields as part of a fly in or other social event.
You could also look at taking non-fliers up and spreading the joy of our sport, especially to the younger generation, either personally or through a dedicated organisation like Aviation Without Borders. Alternatively, think about or using your aircraft and skills to raise money for charities close to your heart. Whatever you choose, fly safe, and if you see me, say hello…
Take part in webinars from experts like Patty Wagstaff, use our free landing vouchers to save hundreds of pounds, read and watch all our content and connect with new people! Join us on our #fly2024 challenge! Fly 2,000
Thanks for your entries for the first month of the LAA photo competition. The competition runs all year and is all about the joy of flight with LAA aircraft.
Email your classified advertisement direct to the LAA: office@laa.uk.com
For all display or commercial advertising enquiries please contact Phil 07770 807035 advertising@laa.uk.com
You can email your classified advertisement direct to the LAA at the following address: office@laa.uk.com
Deadline for booking and copy: 18 April 2024
If you would like to place an aircraft for sale advert please see details below:
MEMBERS’ ADVERTISEMENTS
Up to 30 words: £6; 31-50 words: £12
Up to 50 words with a coloured photo: £45
NON-MEMBERS’ADVERTISEMENTS
Up to 30 words: £22; 31-50 words: £44
Up to 50 words with a coloured photo: £60 www.laa.uk.com
AIRCRAFT APPROVED? Members and readers should note that the inclusion of all advertisements in the commercial or classified sections of this magazine does not necessarily mean that the product or service is approved by the LAA. In particular, aircraft types, or examples of types advertised, may not, for a variety of reasons, be of a type or standard that is eligible for the issue of a LAA Permit to Fly. You should not assume that an aircraft type not currently on the LAA accepted type list will eventually be accepted.
IMPORTED AIRCRAFT? Due to unfavourable experiences, the purchase and import of completed homebuilt aircraft from abroad is especially discouraged.
TIME TO BUILD? When evaluating kits/designs, it should borne in mind that technical details, performance figures and handling characteristics are often quoted for a factory-produced aircraft flying under ideal conditions. It is wise, therefore, to seek the opinion of existing builders and owners of the type. You should also take your own skill and circumstances into consideration when calculating build times. The manufacturer’s build time should be taken as a guide only.
AMATEUR BUILDING
All LAA aircraft builders and potential builders are reminded that in order to qualify for a LAA Permit to Fly, homebuilt aircraft must be genuinely amateur built. For these purposes the CAA provide a definition of amateur built in their publication CAP 659, available from LAA. An extract from CAP 659 reads “The building and operation of the aircraft will be solely for the education and recreation of the amateur builder. This means that he would not be permitted to commission someone else to build his aircraft”. An aircraft built outside the CAA’s definition could result in an expensive garden ornament.
STOL aircraft wanted. Must be in excellent flying condition. Eurofox, Kitfox 7, Zenair 750 or similar. Please contact geffwright@gmail.com
Lycoming IO-360-C1C6, 200HP, 959hrs – sensible offers. Dual certified (FAA & EASA 145 Approved) by Multiflight. Centrilube ‘drilled’ Camshaft and Lifters (320hrs). Refurbished Magnetos. Examined following prop strike, no damage, reassembled with new parts and corrosion inhibitor. Suit Arrows, Mooneys, Pitts, RVs etc. Contact Tim: 07771 725021, timtett68@gmail.com
Pitts S1C constructed USA 1978.Total hrs 830. Engine Lycoming AEIO-320-D1B Total hrs 278 from new 2004. Propellor Hoffman HO23. Electronic ignition r/h. Inverted oil system and smoke tank.8.33 radio, ASI 4 point harness. Permit valid to January 2025. £29,950. Contact Pete 07802 962423
Sportcruiser. 2010 Rotax 912 ULS Permit to 30/11/2024 Engine/ Airframe 740 hours Fuel 17.5 ltrsph, Hangared FSH Woodkomp Klassic Prop fitted 2022 Dynon Glass Cockpit
EFIS-D100/ EMS-D120, AP74 autopilot Trig TY96 Comms Garmin: GPS696 Mode S Transponder, Electronic Flaps/ trim AVEO Navigation/ Strobe Leather High Back seats Offers around £69000 David Turner 07738 930780
FOURNIER RF5 New Limbach 2400 twin plug engine fitted 2016, replacing 1700 original. Greatly improved performance. Engine 117hrs, A/F 3250hrs. LAA permit until June 2024. 8.33 radio, transponder, new seat belts, safety foam cushions, low drag slimline outriggers. Excellent throughout. Based West Sussex. £39,000 Chris Foss 01903 814 080
G-IOWE EUROPA XS TRI-GEAR. Rotax 912 UL. Permit to 28/08/24. 600hrs. All mandatory work signed off. In flight adjustable Woodcomp prop. Trig radio and transponder. AVMap Ultra EFIS. Sky Demon nav set. Grand Rapids EIS and ELBA fuel flow system. Best offer around £30,000 secures. Tel 07720-985011
Evans VP2 less than 10 hours airframe time, fitted with Continental C90 circa 600 hours.Complete aircraft, test flown only. For sale due to owner/ builder illness. Details/photos: flyjt20@gmail.com
Friendly Wellesbourne Chipmunk Group has vacancy for enthusiastic pilot. 1/7th share. Beautiful handling aeroplane. Original 1957 RAF Flight Commodore paint scheme. New Zero time engine and 8,500+ wing fatigue hours. Group instructors for type and tailwheel conversion. £10k of spares and tooling included. 1/7th Share £12,000. Please contact Simon Turner 07802 281983 or email sndt57@gmail.com
RV7 Cowlings, Exhaust system and Airbox for vertical induction Lycoming 320/360 all new ex Vans call Richard 07710 454448 r.h.coates@btinternet.com
Tools for Sale: All my aircraft build tools are for sale including the following which are all in excellent condition: Air compressor, 2 pneumatic rivet guns and hoses, spray gun and attachments, mobile multi drawer tool chest filled with tools, workshop propane heater, workshop flood lights on stands. Hundreds of rivets, clico’s, clamps. Numerous AN nylocs, bolts, washers, jubilee clips, rubber and silicone hoses, flat aluminium sheet etc. Open to offers. inspection EGTO. Call 07941 840553
SERVICES Engine Overhaul. Zero time Major engine overhauls carried out on all types, since 1976, c/w dynamometer run-in and test. Bonner Engineering, Shoreham Airport. Contact Bill Bonner: 01 273 440250. aerobonner@aol.com
Aircraft Weighing - Light Aircraft Weighing Service in East Yorkshire and surrounding area. For details contact Demraview Ltd. Email: Demraview@gmail.com Mob: 07984 810 761
Aselection of flying events you’ll definitely want to add to the calendar for 2024.
Don’t forget, GASCo is always running Safety Evenings up and down the country. We’ll list them here, plus it’s worth keeping an eye on its website, www.gasco.org.uk, for further updates. As always, check the Royal Aero Club Events website for the latest
information and web links for many of the events: http://events.royalaeroclub.org/events.htm
Our thanks to the Royal Aero Club and to Dave Wise for the use of its excellent calendar of events. If you have an event you want to advertise on the list, please email the details to Dave at: dave.wise@ btinternet.com