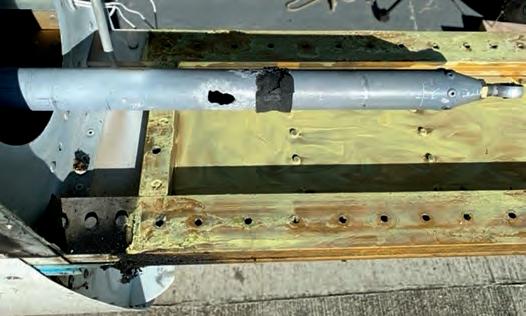
15 minute read
Engineering Matters
Including: Ikarus C42 wing spar fretting, aileron pushrod corrosion, communicating with your Inspector, ACAM Audits, and changes to the Permit revalidation process
Welcome to Engineering Matters – the section of Light Aviation that is dedicated to discussing all manner of topics concerning both technical and operational aspects of the LAA fleet. We all learn by sharing information, so if you have anything to say that you think would benefit others, or have experienced an interesting technical issue or component failure, then please contact us with a description of what you encountered and include accompanying pictures. Send your submissions to LAA Engineering at engineering@laa.uk.com
TLAC TIN-05-2022: Ikarus C42 series wing spar fretting
The Light Aircraft Company Ltd have issued Technical Information Notice TIN-05-2022 for the Ikarus C42 Series of aircraft.
This concerns the inspection of the lower wing battens to ensure that the ‘Duck Bill’ plastic batten tips are installed and positioned correctly.
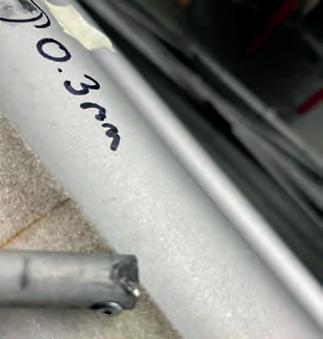
An aircraft was stripped down for the replacement of the wing coverings and it was discovered that a number of the Duck Bills had broken, allowing the battens to fret against the leading edge wing spar.
From the TIN: ‘Not all the broken tips could be found within the wing void indicating they had either fallen out or been removed during wing inspection. On fabric removal it was found that those battens without tips had fretted against the leading-edge spar.
‘Clear fabric reinforced duct tape had been applied in some positions to mitigate fretting but this had been worn through and material had been worn away from both batten tips and, more significantly, the lower side of the wing spar.
‘On measuring the depth of the damage, it was found to vary between 0.35mm and 0.07mm.
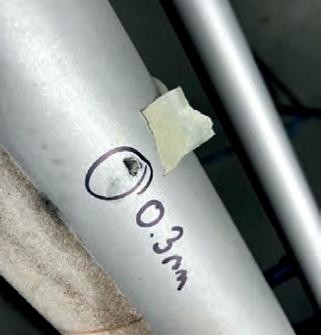
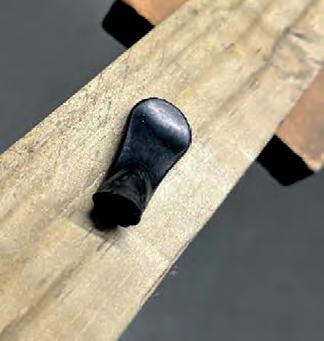
‘The abrasion damage degrades the structural integrity of the wing spar, both in strength and risk of fatigue cracking. The discovery of this damage may be indicative of a failure to perform proper maintenance and inspection of the aircraft concerned.
The Maintenance Manual contains type-specific inspection checklists of which item 89 of the current issue, Issue VIII Rev 1 refers to inspection of this area.
‘It is highly unlikely that damage of this severity occurred between the 50hrs inspections scheduled for this area.’
For further information download the TIN from the TLAC website.
Jon Viner: Chief Technical Officer
Permit revalidation process changes
In last month’s Light Aviation I outlined the changes that we’re making to the Permit revalidation process to modernise it and hopefully improve things for all those involved. This article expands on that and gives more details of the process. Technical Leaflet TL 2.00 has been published on our website (search for ‘Engineering’ / ‘Data library’ / ‘Technical Leaflets’), which contains more detail, including some of the less common scenarios that you might find yourself encountering, as well as detailed advice on how to complete each part of each of the forms described below. At initial issue, this contains all the basics but I expect to be up-issuing it as the process matures.
Firstly, it’s worth mentioning that the process initially only applies to aeroplanes: gyroplanes will continue to use the old process until the system for aeroplanes has bedded in and we’ll then look to apply the same principles.
Secondly, we’re aiming to go live with the new system on Monday 13 February – we’ll put an item in the ‘news’ section of the website to confirm this a week or so beforehand. All revalidation inspections started after that date must use the new forms. However, where inspections were started before that date and check flights have yet to be completed, we’ll accept the old forms (by post only, as per the current system).
The new process is based around three new forms, one for each of the participants in the process outside of LAA Engineering:
• A check flight form (form LAA/CFS-1) to record a check flight completed by a check pilot at some point in the 12 months prior to the Permit revalidation application being received by LAA (as long as it’s carried out after the previous revalidation application). This can be submitted any time after the check flight has taken place, but to be received by the LAA no later than one month after the date of the airworthiness review inspection.
• A Permit revalidation application form (form LAA/PTF-REVAL) which is submitted by the owner, to be received by the LAA within one month of the date of the airworthiness review inspection.
• An airworthiness review report (form LAA/ARR-1), which documents an airworthiness review inspection, is submitted by the Inspector, and to be received by LAA within one month of the inspection.
All the forms are available to download from the LAA’s website (search for ‘Engineering’ / ‘Data library’ / ‘Forms, checklists & worksheets’). The forms may be submitted by:
• Printing them out, completing them by hand, signing and posting them to LAA Engineering.
• Completing electronically, printing them out, signing and posting to LAA Engineering.
• Printing them out, completing by hand, signing, scanning and emailing to LAA Engineering.
• Completing electronically and emailing to LAA Engineering.
It’s not necessary for each of the three forms to be submitted using the same method. For instance, your Inspector might prefer to complete their form electronically, while you might prefer to complete your forms manually and post them in. The three forms are reviewed by LAA Engineering and if all is in order a new Certificate of Validity is generated and emailed to the owner.
A special note on submitting documents electronically If submitting any or all of the forms electronically, the forms must be submitted with each form as a separate multi-page PDF document. This is so that the process at LAA Engineering can be kept as slick as possible.
I’m afraid that submissions made using a separate PDF file for each page or submitted as images will be rejected – it simply takes too long for us to assemble the document into something that we can easily read and store. We’ve created a new email address specifically for submitting Permit revalidation forms: permits@laa. uk.com. Please use engineering@laa.uk.com for all enquiries, whether relating to Permit revalidation applications or otherwise.
PDF documents may be submitted by scanning paper documents using a scanner and creating a multi-page file for each form, and emailing these as attachments. Alternatively, the forms may be completed electronically, saved and attached to an email. When forms are emailed by the signee from their email account, it is acceptable not to include a signature on the form – sending the form by email indicates the sender’s confirmation that the declaration on the form is agreed with.
PDF documents may also be created by scanning paper documents using one of the following mobile phone apps listed in the Technical Leaflet, and emailing the resulting files to LAA Engineering.
Many parts of the process remain the same, including:
• The check flight schedule is essentially the same as before, with a couple of minor adjustments.
• Any pilot with appropriate minimum experience may carry out the check flight.
• Your Inspector will still need to visually inspect the aircraft and its paperwork.
• Inspectors may still issue PFRCs to enable check flights if the previous Certificate of Validity has expired, provided it’s not expired more than 12 months (although this has been moved to a standalone form rather than being incorporated in other forms).
• LAA Engineering will need to issue a PFRC if the previous Certificate of Validity has been expired for more than 12 months. There are a few changes in the inspection paperwork: it’s all stuff that should have been going on anyway, so hopefully no surprises, but it’s more formally laid out to help record what the CAA expects us to do at the time of the Permit revalidation inspection.
It would help your Inspector a great deal (particularly prior to the first inspection under this new regime) to make sure your paperwork is all in order before you pass it to your Inspector
These include:
• Making sure that the airframe and engine logbooks are up-to-date, including the ‘pink pages’ that record mandatory actions (MPDs, ADs, etc).
• That you have the Permit to Fly document and its associate PFA/LAA Operating Limitations document available.
• The weight and balance report is available and reflects the current configuration of the aircraft.
• You have a maintenance programme/schedule for your aircraft and a record of it having been actioned (TL 2.19 discusses how to put together a simple one and the website has sample schedules available – search for ‘Engineering’ / ‘Operating & Maintaining’ / ‘Aircraft maintenance’). The Inspector’s form (LAA/ARR-1) gives a list of the documents they need to check, so it’s worth reviewing that.
Our IT system is also being revised to support the improved process. These changes may not be quite ready to go online for the launch date, but in due course the ‘My aircraft data’ page (viewable when you login to the website) will show owners the status of each of the three elements of the revalidation application.
This data page will also show a field called ‘configuration notes’, which contains some additional data that we note for some aircraft beyond the powerplant, modifications and repairs. For instance, we might note whether the aircraft is the taildragger or nosewheel version of a type that can be configured either way, or we may note whether a Standard Modification has been incorporated. Slightly further down the line, we’re intending for Inspectors to be able to access the ‘My aircraft data’ page for any aircraft, to help them review the configuration of an aircraft before they visit it.
Please take the time to read Technical Leaflet 2.00 and the new forms well in advance of your Permit revalidation being due and perhaps get in touch with your Inspector slightly ahead of when you normally might, so you can discuss how you’ll approach the task.
No doubt there will be a few teething issues, but we’ll aim to resolve those as quickly as possible. We hope the new process will bring benefits all round.
Lucy Wootton:
Chief Inspector Aircraft Continuing Airworthiness Monitoring surveys (ACAM Audits)
Since I started my new LAA role, I have carried out six ACAM audits. Some of you might be familiar with them as your aircraft has been the subject of an ACAM, either by myself or my predecessor, Ken Craigie. However, the majority of owners and many Inspectors will not yet have been involved in the ACAM process. Therefore, here is a summary of what it involves, so you know what to expect if your aircraft is selected.
What is an ACAM? Under the terms of the LAA’s CAA A8-26 organisation approval, LAA Engineering is required to carry out a number of physical inspections of LAA-administered aircraft and their associated documentation.
These inspections are known as ‘ACAM surveys’ – Aircraft Continuing Airworthiness Monitoring surveys. Normally, they are carried out by the LAA Chief Inspector, but may be by one of the other LAA Engineering staff members. The CAA is also required to carry out ACAM surveys and these may be done with LAA Engineering or by themselves.
Normal practice is to have the aircraft owner (or operator) present and also the LAA Inspector who oversees the maintenance of the aircraft.
Most ACAMs are carried out on aircraft holding a current Permit to Fly, although some aircraft ‘in build’ or refurbishment will also be surveyed. It may be that an aircraft is surveyed during its Permit to Fly revalidation inspection, although most will be looked at in-between scheduled servicing requirements.
The surveys are rarely carried out without good prior notice, to enable all parties to be present. Very occasionally, an ‘intelligence led’ ACAM is required at short notice, where there are concerns about a particular aircraft.
Physical Survey
This is somewhere close to a ‘Check A’ inspection, but slightly more in depth. The engine compartment will need to be accessed, for instance, which may require the engine cowlings to be removed if they are not of the opening kind, which allow good visual access to the engine bay.
The airframe is inspected ‘externally’, which means, normally, without removing access panels or disturbing the airframe in any way. The cockpit/cabin is checked for having all mandatory placards and instrument markings present as required. The engine compartment is inspected to ensure that there are no major defects, oil or fuel leaks, and so on.
If any modifications or repairs have been carried out on the aircraft, these will be checked against the files held on record by LAA Engineering, to ensure that they have been embodied as agreed.
Documentation
The aircraft records are checked to ensure compliance with the requirements. The records checked include the airframe and engine logbooks (and propeller logbooks where required), Airworthiness Directive/Service Bulletin compliance statements and associated workpacks. The aircraft document check also includes the Permit to Fly, Certificate of Validity, Operating Limitations, weight and balance etc – all the documents that are normally kept in the aircraft for reference purposes.
LAA Technical Leaflet TL 2.02: Permit Aircraft Paperwork Checklist, details what documentation is required to be kept for an LAA-administered Permit to Fly aircraft.
ACAM Report
After the ACAM has been completed, a report is produced and sent to the aircraft owner and the Inspector who is normally associated with the aircraft.
Woodcomp propeller bolts – update
Following on from the piece in last month’s Engineering Matters, Kevin Dilks (UK importer of Woodcomp propellers) called to say that the new bolts were not actually ‘fully-threaded’ (i.e. technically ‘screws’), but did have a threaded portion of the bolt contained within the hub.
Kevin has been working with Woodcomp to source some screws that are ‘better’ than those currently supplied by Woodcomp from an engineering standpoint, in that, only an unthreaded portion of the bolt shank will be within the propeller hub.
Van’s RV-6A aileron pushrod corrosion
Following a landing incident where a Van’s RV-6A ended up on its back, the aircraft was dismantled for recovery and repair.
Nick Stone, a local (to the incident) LAA Inspector, who was carrying out the task was somewhat shocked to discover one of the aluminium aileron pushrods, severely corroded just inside the fuselage.
It is uncertain what caused the corrosion, but it may have been due to some kind of gaiter/bellows arrangement fitted to prevent an in-rush of (relatively) high pressure air from inside the wing into the cockpit. Whether it created a moisture trap or there was a dissimilar metal corrosion issue between the pushrod and, perhaps, a hose clamp used to secure the bellows/gaiter.
This issue is not one to only affect RVs or even aileron pushrods, and it highlights the problem of inspecting aircraft thoroughly during an inspection where parts of the airframe and components are difficult to access or are covered up.

Standards of riveting
While carrying out the Permit to Fly revalidation annual inspection on a ‘new to him’ Van’s Aircraft RV-7, LAA Inspector, Aaron Cole, discovered some questionable riveting and in one place, found that there was no rivet used at all – it had instead been substituted with a blob of black sealant.


The issues have since been rectified and it demonstrates that even UK-built aircraft may not be constructed as well as they might.
During an engine ground run, prior to an intended first flight, the propeller hub failed resulting in the propeller parting company with the crankshaft. The pilot, co-owner Gary Priestley, reacted very quickly and shut down the engine without it overspeeding.
The propeller flange was fitted to the ‘back’ end of the crankshaft. A Woodruff key on the untapered shaft drove the flange, which was retained by a central bolt.
A thread cut on the outside of the flange collar served to encourage oil not to exit the engine.
The flange became detached, as the Woodruff key slot in the flange had failed, probably due to overload and fatigue.
The key slot in the crank was found to be damaged and may well have been before the ultimate failure, leaving part of the key driving the flange. Additionally, the thread on the collar of the flange may have encouraged fatigue failure.
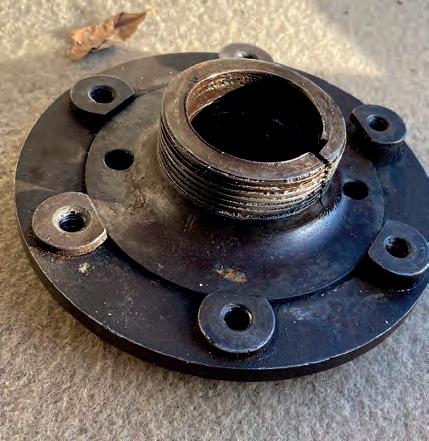

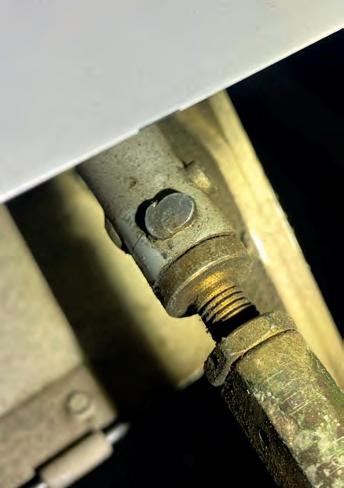
The engine is to be fitted with new crankshaft and propeller flange.
The aircraft’s other co-owner, Mike Laundy, said that had the failure happened a little later when he was planning to fly the aircraft for the first time, it would have presented him with a somewhat hazardous situation, if it had happened immediately after
The report will list any ‘findings’, detailing areas that must be rectified (within a stated timescale) and ‘observations’.
‘Observations’ are items that are considered advisory actions with which to be complied.
Common Errors
One of the most common problem areas are missing mandatory placards. The mandatory placards are listed in the aircraft’s specific Operating Limitations document, with further information found in LAA Technical Leaflet TL 2.11: Aircraft Placards, Labels and Registration Marks.
Logbooks are another area where owners and Inspectors tend to struggle to keep everything up to date. It is well worth spending an evening going through the logbooks to ensure all the relevant information is present, which includes the initial pages, the green pages (scheduled maintenance record), and pink pages (nonscheduled maintenance tasks, modifications and repairs).
I intend to provide some online tutorials in the coming months for Inspectors to provide further guidance on how to complete the various sections of the logbooks.
Recent ACAM findings
Spinner cracked and stop drilled.
VNE placard missing from the P1 cockpit.
Main landing gear tyre perished.
Loading limitation placard was for a nose wheel variant – the aircraft was tailwheel equipped.
Mainplane fabric failed a strength test.
Flexible oil line chafing on the oil tank.
‘Occupant Warning’ placard missing.
Logbooks incomplete.
Airworthiness Directive compliance statement incomplete.
Recent Alerts & AILs
Please refer to the Engineering section of the LAA website for the most current information.
Andair fuel pumps and ethanol-based fuels Service Alert Issued 06/10/22: Fuel Pumps
‘This service alert applies to Andair fuel pump models PX375-TC#7 & PX375-TC28v#7. Andair now has a solution so ethanolblends are no longer an issue and ethanolbased fuel can now be used with our pump models. This coincides with some changes in product design and manufacturing processes which were implemented to greatly increase durability, performance, reliability and to incorporate changes needed for ethanol-based fuels, as per service alert (October 2022). Therefore, the revision number has now
LAA Engineering charges
LAA Project Registration
Kit Built Aircraft £300
Plans Built Aircraft £50
Initial Permit issue
Up to 450kg £500
451-999kg £600
1,000kg and above £700
Permit Revalidation
(can now be paid online via LAA Shop)
Up to 450kg £190
451-999kg £240
1,000kg and above £275
Factory-built gyroplanes* (all weights) £285
*Gyros note: if the last Renewal wasn’t
Liaising with your Inspector
It is paramount that aircraft owners work closely with their Inspector to ensure that their aircraft is maintained to the highest standard of airworthiness available.
LAA Engineering recently received a report where an aircraft suffered a propeller strike and the syndicate was hesitant about involving their Inspector. Eventually, the correct procedures were followed.
Maintaining an LAA-administered aircraft is very much a team effort between the aircraft owner(s) and their appointed Inspector (and even LAA Engineering!).
LAA Engineering housekeeping
LAA PO Box/G-INFO Facility As previously reported, the LAA PO Box/G-INFO facility has been withdrawn. Any owner still using the LAA PO Box as the registered address for their aircraft must notify the CAA of a new registered address immediately. Any post sent to the now defunct LAA PO Box number will no doubt be returned to the sender. LAA Engineering Fees Please consult the relevant page in Light Aviation and the LAA website for the revised LAA Engineering fees. Placards Various placards are available through the LAA online shop on the LAA website. Previously, these were available free of charge but the increased production costs have to be covered.
changed and PX375-TC#8 and PX375-TC28v#8 will be distributed as of December 2022.
We are also in the process of retrofitting new components or modifying existing components that incorporate the necessary changes needed for ethanol blends and encourage customers who are concerned they may be affected to contact Andair for guidance on this matter.’
Andair has confirmed that only pumps manufactured to the ‘#8’ specification or that have been returned to Andair for an upgrade should be used with ethanol-based fuels.
Garmin G3X, G3X Touch and G5 with GSA 28 autopilot servos connected to trim actuators administered by the LAA, an extra fee of £125 applies
Modification application
Prototype modification minimum £60
Repeat modification minimum £30
Transfer
(from C of A to Permit or CAA Permit to LAA Permit)
Up to 450kg £150
451 to 999kg £250
1,000kg and above £350
Four-seat aircraft
Manufacturer’s/agent’s type acceptance fee £2,000
Project registration royalty £50
‘Mandatory’ Service Bulletin No 22112: Automatic Trim/GDU 4xx Reset
In G3X, G3X Touch, and G5 systems with GSA 28 autopilot servos connected to trim actuators, an uncommanded automatic trim runaway may occur when the autopilot is first engaged.
WARNING: Engagement of the autopilot with this condition may result in an uncommanded deviation from the intended or desired flight path.
The G3X Touch display may intermittently reset during flight.
Description: This Service Bulletin contains instructions to load G5, G3X, and G3X Touch (updated) software. All installations must incorporate this update as soon as practical.
Category change
Group A to microlight £150
Microlight to Group A £150
Change of G-Registration fee
Issue of Permit documents following G-Reg change £55
Replacement Documents
Lost, stolen etc (fee is per document) £20
PLEASE NOTE: When you’re submitting documents using an A4-sized envelope, a first-class stamp is insufficient postage.