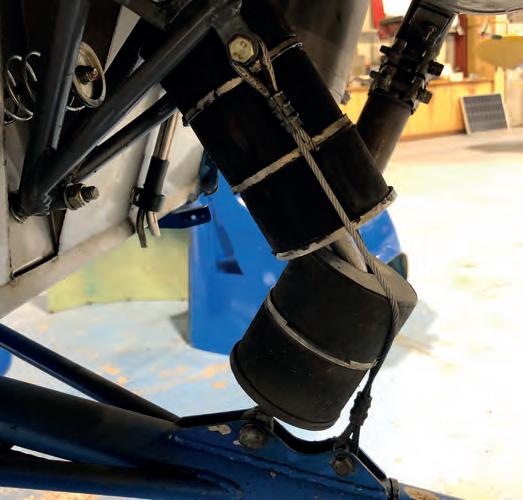
14 minute read
Engineering Matters
Including: EuroFOX noseleg issues, switches, VW pump corrosion and a Europa door mandatory mod
Welcome to Engineering Matters – the section of Light Aviation that is dedicated to discussing all manner of topics concerning both technical and operational aspects of the LAA fleet. If you have anything to say that you think would benefit others, then please email LAA Engineering at engineering@laa.uk.com
EuroFOX Undercarriage
The LAA administered fleet includes a number of EuroFOX aircraft which are used by gliding clubs as tugs. These aircraft work hard and naturally accumulate far more flight cycles than their ‘private use’ siblings.
There have been a few issues recently concerning the nosewheel undercarriage ‘3K’ version of the EuroFOX.
Nose undercarriage shock absorber wear One aircraft had the nose leg suspension unit fail, possibly due to a lack of lubrication of the shock absorber. Fortunately, the check cable worked as intended and prevented any further damage occurring.
The shock absorber unit consists of a number of rubber discs mounted on a central tube which slides over another tube as the nose leg moves.

The wear occurs between the two tubes, and although Aeropro has recommended lubricating the tubes, there is scant information in the maintenance manual regarding this, although the build manual advises to use ‘graphite Vaseline’ on the parts that have ‘relative movement’.
Excessive greasing of the tubes may well exacerbate wear if the grease becomes contaminated with dirt, so some form of dry lubricant may be preferable. What is certain, is that the shock absorber should be disassembled regularly (based probably on flight cycles as well as hours or calendar time) and inspected for wear.
Nose undercarriage leg collapse A EuroFOX glider tug had its nose undercarriage leg fail just below where the shock absorber attachment leg is welded to the nose leg. This occurred while the aircraft was taxying in after landing and resulted in a shock-loaded engine and damage to the propeller and engine cowlings.
It is entirely possible that the nose undercarriage leg had been weakened over the years (it had accumulated around 7,500 landings in seven years of operation) rather than that particular landing being harder than normal.
Below left The failed shock absorber showing wear and failure of the sliding tubes.
Below right The new shock absorber pre-assembly and installation.
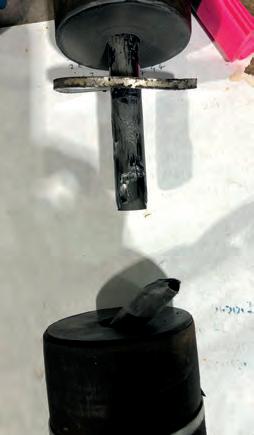
Right Nose leg failed, causing the propeller to strike the ground. Below right This view (without the wheel in the way) demonstrates the correct path of the nosewheel axle).

assembly, it appears that the nosewheel axle may have missed the axle holes in the nose leg fork and the wheel was then only held in place by the clamping pressure of the nosewheel axle bolt and nuts against the fork.
On the next flight, when landing, the nosewheel assembly, including the nosewheel fairing, appears to have been pushed up the leg until the nose leg fork contacted the ground, pitching the aircraft over onto its back.
The EuroFOX maintenance manual does not currently fully describe the installation of the nosewheel assembly. Normal maintenance practices apply and in circumstances such as this where visual access is restricted, it is imperative that the installation is carefully checked prior to releasing the aircraft to service.
This kind of error could possibly occur on many aircraft types, not just the EuroFOX.
Replacing an aircraft tyre is allowed under ‘pilot maintenance’ Further details on this can be found in LAA Technical Leaflet TL 2.05 (https://tinyurl.com/Ptfpilotmaintenance). Such maintenance can be signed for by a qualified pilot who is an owner of the aircraft and a member of the LAA. The pilot’s licence number is the authorisation and should be included with the pilot’s signature and date against the entry in the worksheet and log book.
Switches
Incident one: An incident recently with an engine failure on take-off on a Spitfire Mk 26 fitted with a Isuzu engine (converted car engine). It appears to have stopped because of loss of crankshaft position information to the ECU. The crankshaft position sensor is duplicated, but the indications are that the switch, which allows the pilot to select between the position sensors, had failed internally and gone opencircuit. In other words, an attempt to increase safety by duplicating a critical sensor has in itself created a failure.
Clearly if duplicating a system, particular consideration needs to be given to avoiding single points of failure (e.g. both the feeds to independent electric fuel pumps going through the same plug and socket), or when single points of failure are inevitable, aircraft owners need to be sure the component, which is a single point of failure, is chosen to be of high quality and consideration given to maximising its reliability, for example, perhaps making it a lifed item.
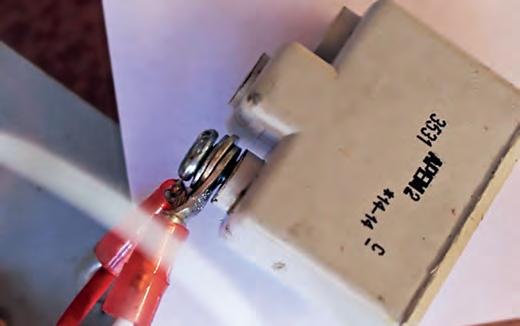

Incident two: Recently, a Turbulent was badly damaged when it suffered an engine failure after take-off. It is possible that the engine failure was caused by a failure in the ignition system as the power connections of the duplicated Leburg ignition systems to the separate ignition switches were both loose and on the point of disconnecting. The switches used a very small screw to connect the ring terminals on the cables to the contacts on the switch, and the screws, supposedly retained by spring washers, were found loose. One, to the extent that it was on the point of falling out, and was looser than could be explained through wrenching of the wiring during the crash sequence.
It seems very unlikely that both ignition systems lost power in the short time between doing the power checks and the crash, but nevertheless, where switches are involved in systems providing a vital service, aircraft owners should be sure that the means of connection is fit for purpose.

The aircraft involved in the second case had recently been re-built to a very high standard indeed and the workmanship was generally beyond reproach. Screwed connections to switches and circuit breakers are quite common, but in this case the screws were very small. It is possible that the way the cables were routed and the way in which they were supported (cable ties) may have a strong influence on whether vibration on the wires can effectively ratchet a screw loose. Soldered and push-on connectors have other reliability issues, but particularly as we move forward with aircraft becoming electrically more complex with ‘glass’ panels and Night/IFR approvals, great care is needed when designing, installing and inspecting all electrical equipment.
Left Terminal screws on electrical switches and circuit breakers are small and fiddly and quite often not easy to torque correctly due to restricted access.
Below The terminal switches are not very long and if you need to attach two ring terminals, with a shakeproof washer in place, the amount of thread engagement may be less than ideal.
Hobbs meter oil pressure switch failure
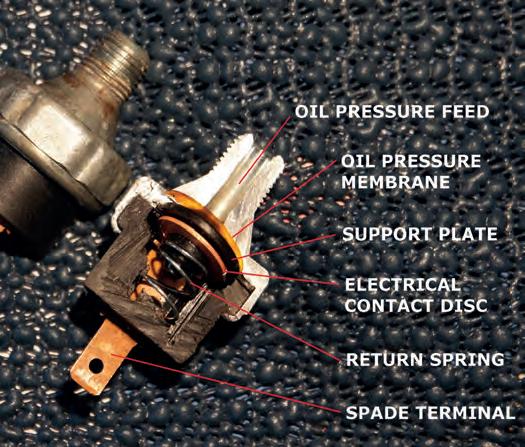
Recently, a Rans S6 was damaged following an off-airfield landing after the engine oil pressure dropped to zero. The decay in oil pressure was as a result of a loss of oil which was caused by an internal failure of a Hobbs hour meter oil pressure operated switch.
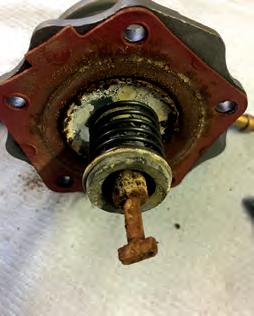
On this aircraft, the Hobbs meter switch had never been connected to a meter but was installed as part of the standard build for the type.
Quite often, older style gauges are of the ‘wet type’, so called as they are fed directly by the fluid in question and, similar to the Hobbs meter switches, are mounted aft of the firewall. As they are often tucked up behind the instrument panel they are not inherently easy to inspect and indeed may not give any indication of an impending failure.
After cutting the oil pressure operated switch in half, there was no visible sign of failure. The switch comprises a metal body swaged around a plastic insert. A thin plastic membrane reacts against a plastic support plate and on the back of that is mounted a copper contact disc. When oil pressure acts on the membrane, the support plate moves against spring pressure and the copper disc contacts the two terminals, completing the electrical circuit. In this case it is possible that after many years of operation, the plastic body had age-hardened and allowed oil to bypass the membrane, which is the only seal in the system, or that there was a minute hole in the membrane itself.
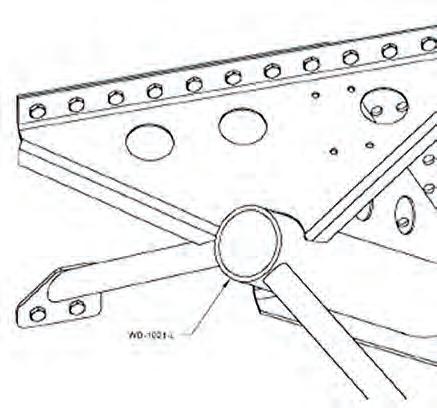
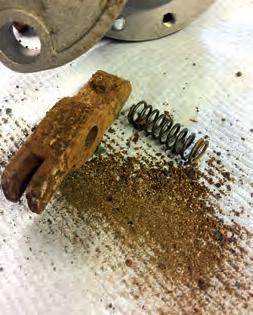
VW fuel pump internal corrosion
LAA Inspector Robin Braithwaite emailed Engineering to say that he was recently satisfying MOD/ENG/VW/001 (see also LAA Airworthiness Alert LAA/AWA/20/24) on a VW engine installation which has been out of service for about a year. The fuel pump did not have a plastic fuel pump rocker arm but the steel components inside the pump lower housing were found to be quite corroded.
According to the VW maintenance manual, the lower housing should be packed with ‘a multi-purpose grease such as Castrol LM’. Clearly, the lower housing on this pump was devoid of grease and Robin’s thought is that condensation has had its part to play. The pump has since been replaced.
Robin went on to ask that while he expected that most VW fuel pumps will have been inspected to satisfy MOD/ENG/VW/001, how many have been refitted without grease?
Van’s Aircraft RV-10 Service Letter SL-00033
Van’s Aircraft issued Service Letter SL-00033 in February 2021 concerning cracks discovered in the company demonstrator WD-1021 main undercarriage attachment weldments and F-1050 forward cabin floor panels. The subject title is RV-10 Landing Gear Field Assessment As this was issued as a Service Letter, it may not have been picked up during normal checking of the continuing airworthiness information published by Van’s Aircraft, which tend to concentrate on Service Bulletins.
If cracks are found, Van’s Aircraft will issue Service Bulletin SB-00007 directly to the applicant. Cracks were discovered in two of the LAA administered fleet of RV-10s that have been inspected.
RV-10 co-owner, Sandy Macfarlane, has carried out the Service Bulletin on the aircraft and is more than happy to pass on guidance (and the lending of a trestle) to other owners before they embark on the job, if needed. Please get in touch with LAA Engineering for Sandy’s contact details.
Van’s Aircraft service information On the subject of continuing airworthiness instructions, Van’s Aircraft has really increased its support in this field over the last 10 years and owners can access information ‘by model’ from the ‘Service Information and Revisions’ section of the Van’s Aircraft website at www.vansaircraft.com, including revisions to the kit assembly instructions. A recent update to their webstore http://store. vansaircraft.com, means you can now register an online account against a specific aircraft kit number, and this will give you access to the most recent digital plans specifically selected service information documents for your RV model. If you have purchased an already flying RV, this is a good reason to contact Van’s to notify it of the change of ownership.
Ken Craigie: Chief Inspector’s roundup
LAA Inspector training seminars
These days, the preferred method for LAA Inspectors to maintain qualification to renew their inspector approval is by attendance at a dedicated LAA Inspector Training Seminar (ITS). This is required every four years, or to be precise, mustn’t be more than four years ago when inspectors renew their approval, annually, at the end of March each year. A variety of aspects are covered, including a recap of an inspector’s role and responsibilities, inspector procedures, experience from incidents, health and safety, human factors, and importantly, a current LAA affairs update.
Seminars usually take place throughout the year at various locations around the UK, but of course, Covid has been a problem over the last 18 months. Since it again became acceptable to ‘meet-up’, catching up has been a priority. One event in October last year, I was gratified that 24 of a total contingent of 28 LAA inspectors based in Scotland were able to attend a seminar event held in a classroom facility at the Falkirk Wheel, in Falkirk (a great place to visit, by the way). The format is always very much a two-way experience, with LAA Engineering learning as much from an engaged audience as we are able to deliver. It’s also a great opportunity for LAA Inspectors to meet each other, sometimes for the first time, putting faces to names and making contacts.
Other ITS events which took place in 2021 were held, during August, at the IWM at Duxford, at the Brooklands Museum in Weybridge, and at the British Motor Museum at Gaydon in Warwickshire, and finally in November at the DH Aircraft Museum at London Colney, Hertfordshire. When added to the Falkirk seminar, these events attracted attendance from a total of 120 LAA Inspectors, which is more than sufficient to keep our schedule on track. Feedback throughout has been upbeat, and I shall soon be planning events for 2022.

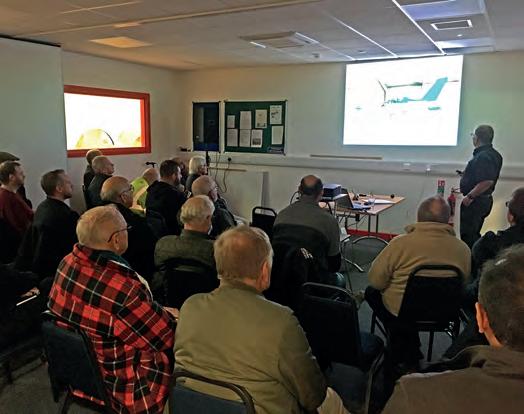
In addition to our ITS programme I occasionally arrange courses designed at providing specific product-based training for inspectors. These usually rely on the goodwill (or more often, enthusiasm) of the various UK-based kit aircraft and product suppliers. That’s usually a day-long event at the host’s premises, but if you missed me at the Rally on the Saturday last year, that’s because I was occupied running a meeting at which 34 inspectors chose to take an hour out of their Rally weekend to listen and learn from Kevin Hyam of CAMit Aero Engines UK Ltd, who gave up his time to pass on his expertise concerning CAMit and Jabiru engines – thank you Kevin.
Comings and goings…
There are 365 LAA Inspectors currently approved on our system, and for the benefit of aircraft- (or project-) owning members I thought it perhaps useful to list those inspectors who, for varying reasons, have stepped down from being approved during 2021, as well as those who became newly approved. Approval and contact details of all current inspectors can be found within the Engineering pages of the LAA website. Stepping down in 2021: Keith Harvey: Andover, Ernie Horsfall: Preston, Barry Smith: Redcar, Robin Dispain: Fordingbridge, Paul Szluha: Cambridgeshire, Ian Charlton: Petworth, Robin King: Axminster, and Humphrey Penny: Tunbridge Wells.
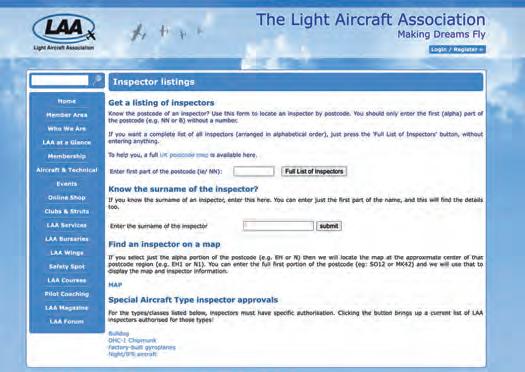
New approved inspectors are: William Kirkdale: Andover, Steven Crombie: Bournemouth, Aaron Cole: Lutterworth, Steven Clayton: York, Amgad Ahmed: Halfpenny Green, Robin Kraike: Devizes, Bruce Ellis: Salisbury, Rob Stephens: East Winch, Tim Richardson: Hook, and Steph Meester: Stroud.
In addition, 2021 has seen the sad passing of Rex Coates of London, Steve Gilbert of Enstone and Reg Stratton of Winchester.
Europa door losses
Over the years, there have been several incidents of Europa aircraft suffering one of its gull-wing doors coming open in flight, some resulting in the window breaking, but more often resulting in the loss of the door due to the hinges failing as the door swings violently open.
Following the first incident which happened on a Europa Company demonstrator aircraft, it was surmised that the most likely cause was due to the pilot having snagged the door latch handle with his shirt sleeve, opening the latch inadvertently. This resulted in the issue of Europa Mod 35 – door handle guard, which was issued as a mandatory mod and was immediately incorporated into the standard kit. However, in subsequent years, inadvertent door openings and losses have continued to be reported. Thankfully, pilots also reported that the aircraft continued to be easily controllable with a door missing, and that no other damage to the airframe was suffered. A recent case where the departing door struck the tailplane of the aircraft, damaging its leading edge, has raised the priority level on the topic, and in early November LAA Engineering issued a modification that’s expected to cure the problem.
It was concluded that the cause of these door opening/loss events was due to the door’s rear shoot bolt not having engaged into its socket in the door surround when the door latch was closed, despite the front one having engaged properly. Whereas the front shoot bolts are in full view of the pilot and crew, to see the rear shoot bolts means twisting round in your seat, and apparently this visual check was sometimes being neglected.
When the door is open on the ground, it is supported by a single gas strut mounted at its rear which results in the rear of the door being pushed outwards slightly, relative to the front, while it is being closed. As the latch is closed and the shoot bolts extend front and back from the door, the front one readily engages into its socket but the rear one would sometimes miss its socket and then slide along the outside skin of the fuselage. To the unwary, the door might seem properly latched and secure, even when being checked by pushing against it from the inside.
In flight, the suction force generated by airflow over the curved window pulls against the door and the rear of it would then flex outwards, eventually enough for the front shoot bolt to disengage from its socket.
After making a few trial fits on Europas local to Turweston, a fixed-door latch shoot bolt stop turned out to be the simplest and most reliable design, and LAA’s engineers have now issued the details of this modification to all UK Europa owners.
Comprising two aerodynamically shaped parts, it is attached to the fuselage outside surface. The ‘working’ part of it is mounted where the
Above The shoot bolt stop installed on the aft edge of a Europa door. The forward part is simply an aerodynamic fairing.
Left You can see how the shoot bolt contacts the stop if the door isn’t fully closed, preventing the latch lever being fully locked rear shoot bolt will contact it, should it fail to engage in its socket when the door latch is operated towards the closed position, preventing the latch lever from fully closing. The forward part of the assembly, attached to the door itself, is simply an aerodynamic fairing. The stop and fairing are available from LAA as SLA 3D-printed plastic parts. Alternatively, they can be self-manufactured from a suitably resilient material such as wood.
The LAA has issued this modification with a mandatory status with a requirement to embody it within five flying hours of the date of issue, or next permit renewal, whichever comes first. Full details of Europa Standard Mod 15833, and the issuing Airworthiness Information Leaflet MOD/247/012 can be downloaded from the Engineering alerts page of the LAA website.
Permit to Fly revalidation check flights
Take-off weight During the period where Covid-19 social distancing regulations were in force, LAA Engineering did relax the rule on Permit to Fly revalidation check flights being conducted within 90% of Maximum Take-off Weight authorised at take-off.
Now that we are thankfully ‘flying free’ again, please ensure that all check flights are flown at a take-off weight in excess of 90% MTWA.
Further information on conducting the check flight can be found in LAA Technical Leaflet TL 2.06
LAA Engineering charges (Note new fees in red)
LAA Project Registration
Kit Built Aircraft £300
Plans Built Aircraft £50
Initial Permit issue
Up to 450kg £450
451-999kg £550
1,000kg and above £650
Permit Revalidation
(can now be paid online via LAA Shop)
Up to 450kg £170
451-999kg £220
1,000kg and above £260
Factory-built gyroplanes* (all weights) £275
*Gyros note: if the last Renewal wasn’t administered by the LAA, an extra fee of £125 applies
Modification application
Prototype modification minimum £60
Repeat modification minimum £30
Transfer
(from C of A to Permit or CAA Permit to LAA Permit)
Up to 450kg £150
451 to 999kg £250
1,000kg and above £350
Four-seat aircraft
Manufacturer’s/agent’s type acceptance fee £2,000
Project registration royalty £50
Category change
Group A to microlight £150
Microlight to Group A £150
Change of G-Registration fee
Issue of Permit documents following G-Reg change £55
Replacement Documents
Lost, stolen etc (fee is per document)£20
PLEASE NOTE: When you’re submitting documents using an A4-sized envelope, a First Class stamp is insufficient postage.
LAA Fleet Summary
Recent Alerts & AILs
(check the LAA website for further details)
Europa Aircraft – All Variants: Door Losses
LAA Alert: LAA/AWA/21/08 Door Losses
LAA AIL: MOD/247/012 Door Latch System Stop
EuroFOX Tricycle Undercarriage (3K version): Fuselage Structure
LAA Alert: LAA/AWA/21/09 Fuselage
Structure Under Seat Pan Weld Inspection
LAA AIL: MOD/376/005
Visual Check of Weld Cluster Under Seat Pan
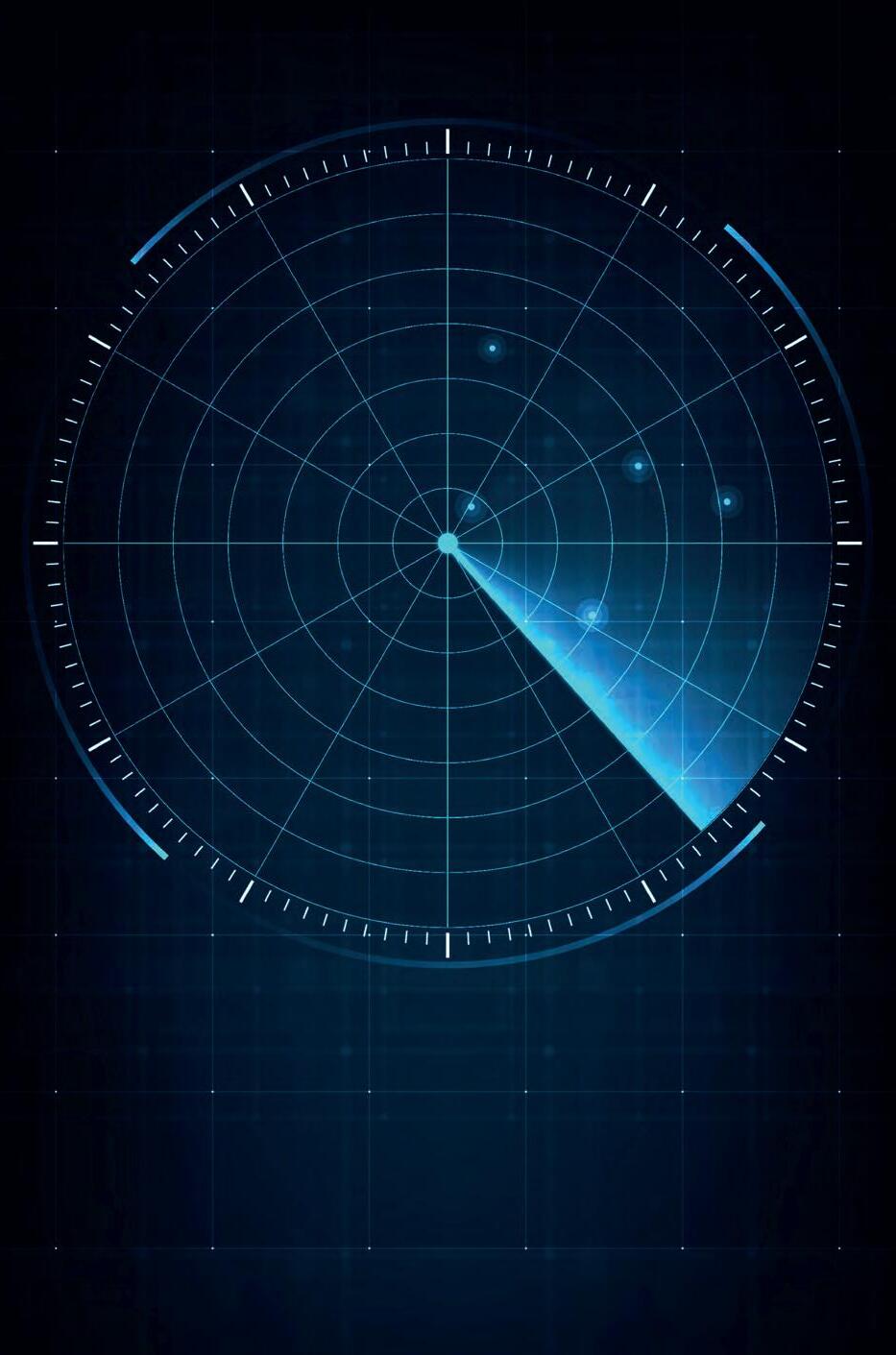
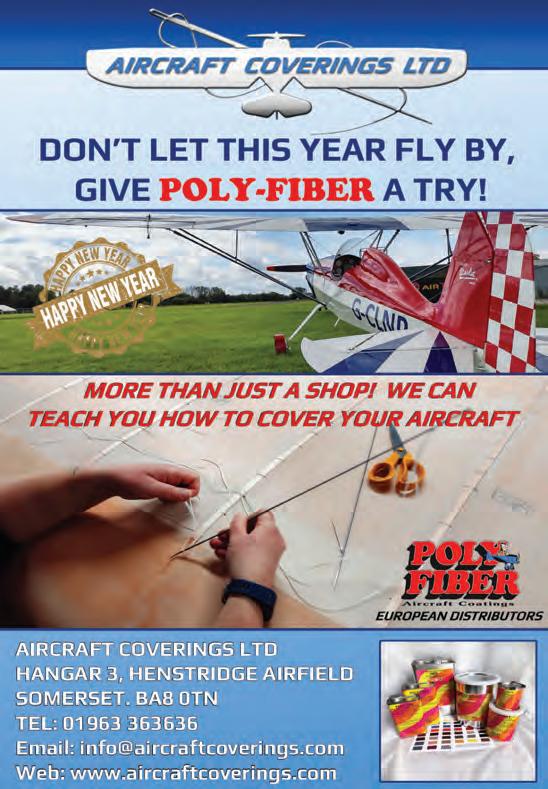