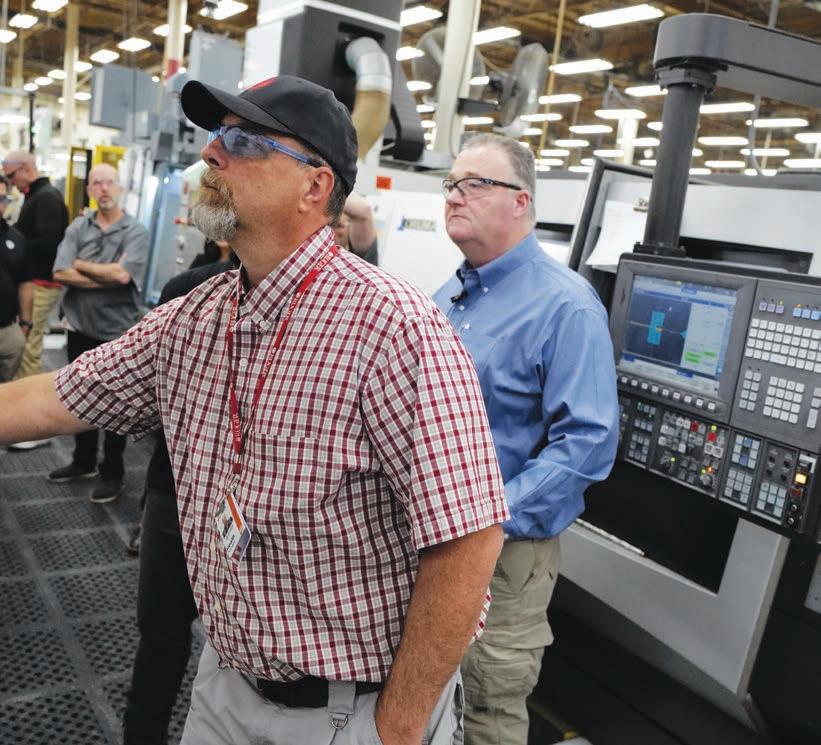
3 minute read
The Well-Oiled Machine
Ruger uses lean manufacturing techniques to efficiently create new products.
Bringing industry-leading firearms into the world requires a well-oiled machine made up of designers, engineers, and other professionals deploying some of the most advanced manufacturing techniques and tools available. Development and production at Ruger Firearms are unparalleled, thanks in large part to long-time team members such as chief manufacturing engineer Heath Putnam. With more than 30 years of engineering experience, Putnam plays a key role in creating and refining strategic engineering and manufacturing processes at Ruger.
Before joining Ruger Firearms in 2013, Putnam spent two decades leading engineering teams in the automotive, industrial valves, and power-generation industries. As might be expected, he witnessed countless advances during that time.
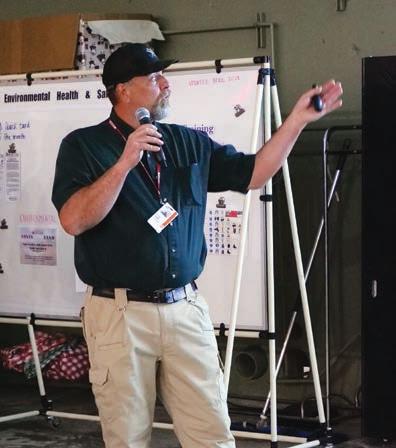
“Technology for design and metal cutting has really evolved. It blows my mind when I think about all of the changes that I’ve seen,” Putnam says. “Design in manufacturing is changing so fast—I’m really excited to see what comes next.”
Lean and Effective
Ruger Firearms employs lean manufacturing, a method that minimizes waste while maximizing productivity and value for Ruger’s customers. It’s an approach that Putnam has helped implement and hone during his 10 years with the company.
“Lean manufacturing is something I’m really passionate about. It’s doing more with less, so we try to provide our customers with as much value as possible,” Putnam explains. “We want to help our folks work more efficiently. We want to use fewer machines, less tooling, and less time to manufacture our firearms.”
Ruger uses Takt Time to construct their manufacturing processes. (Takt Time is a tool for setting the pace and rhythm of a manufacturing process to align with customer demand.) The manufacturer also practices a mistakeproofing technique called poka-yoke (a Japanese colloquial term that basically means avoiding careless mistakes). A good example is how associates load a machine; they are trained to do it correctly the first time, every time.
Product development at Ruger incorporates lean manufacturing from the outset. As new firearms, accessories, and shooting technology are conceived, manufacturing is taken into account during the earliest design phases.
“We use this symbiotic and collaborative relationship of the product engineers and the manufacturing engineers from day one right through the development. It allows the product development and the process design development to go along simultaneously. That gives us a lot shorter time to launch,” he says. “As a project moves forward and moves toward launch, we flex resources in and out depending on the needs of the project at that point.”
The core product development teams at Ruger include designers, multiple product engineers, manufacturing engineers, a project manager, and others. The engineers are often based at different facilities across the country, but thanks to Ruger’s robust digital communication infrastructure, they are able to work together.
“We can leverage our extra bandwidth, because in any given moment, we may only have one or two engineers that actually have some time to start a new project. If there’s one or two engineers in New Hampshire, and there’s one or two engineers in Mayodan, and there’s one or two engineers in Prescott, we can leverage a good team by doing that,” Putnam says. “We started doing a lot more collaboration during the COVID years because that forced us to collaborate using digital means more.”
Tackling Engineering Challenges
Developing new products in any industry presents engineering challenges. To help overcome those inevitable obstacles, Ruger relies on Failure Mode and Effects Analysis (FMEA), a tool that identifies and addresses potential problems before they ever arise. Essentially, FMEA anticipates what could possibly go wrong in the future.
“We do our due diligence at the beginning of the project and throughout the new product development process with a collaboration of product designers and manufacturing engineers working together in sort of a give and take,” Putnam says. “A lot of problems are taken care of before they actually occur. Using our new process development, we really don’t have huge problems, especially near the end of the project.”
Mentoring Young Engineers
As chief manufacturing engineer, Putnam spends a lot of time training and mentoring Ruger’s engineers and operations personnel. In addition to sharing lean manufacturing concepts, he teaches manufacturing and design analysis software, problem solving, cutting-tool technology and selection, and more.
“I’m really passionate about lean. I’m really passionate about engineering in general. It’s nice to be able to give some of that knowledge and history back to younger engineers,” Putnam says. “When I was younger, I had some really good mentors and I think that’s another reason why I like to help young engineers. I’ve grown personally by mentoring newer, younger engineers and, hopefully, they’ve gained something from me.” (RUGER.COM)
Besides sharing lean manufacturing concepts, Putnam also teaches manufacturing, design analysis software, and problem solving.
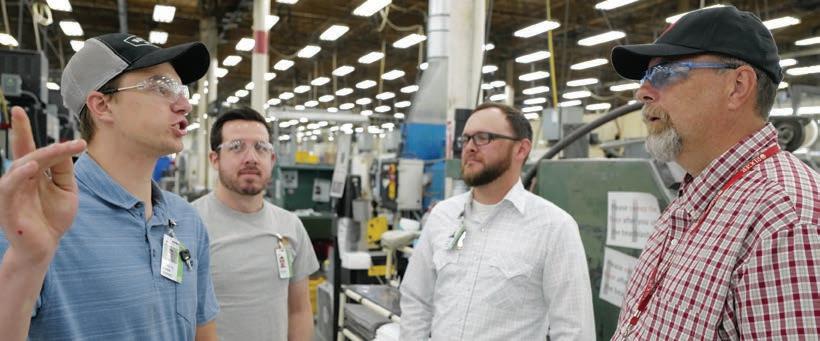
Editor’s Note: Additional research for this article conducted by Miles Hall.
THERE ARE AMMO PLANTS CAPABLE OF PRODUCING NEARLY FOUR MILLION ROUNDS A DAY. THAT’S NOT US. WE ARE A CRAFT AMMUNITION MAKER, and you can’t automate craft.
Our process is slow, on purpose.
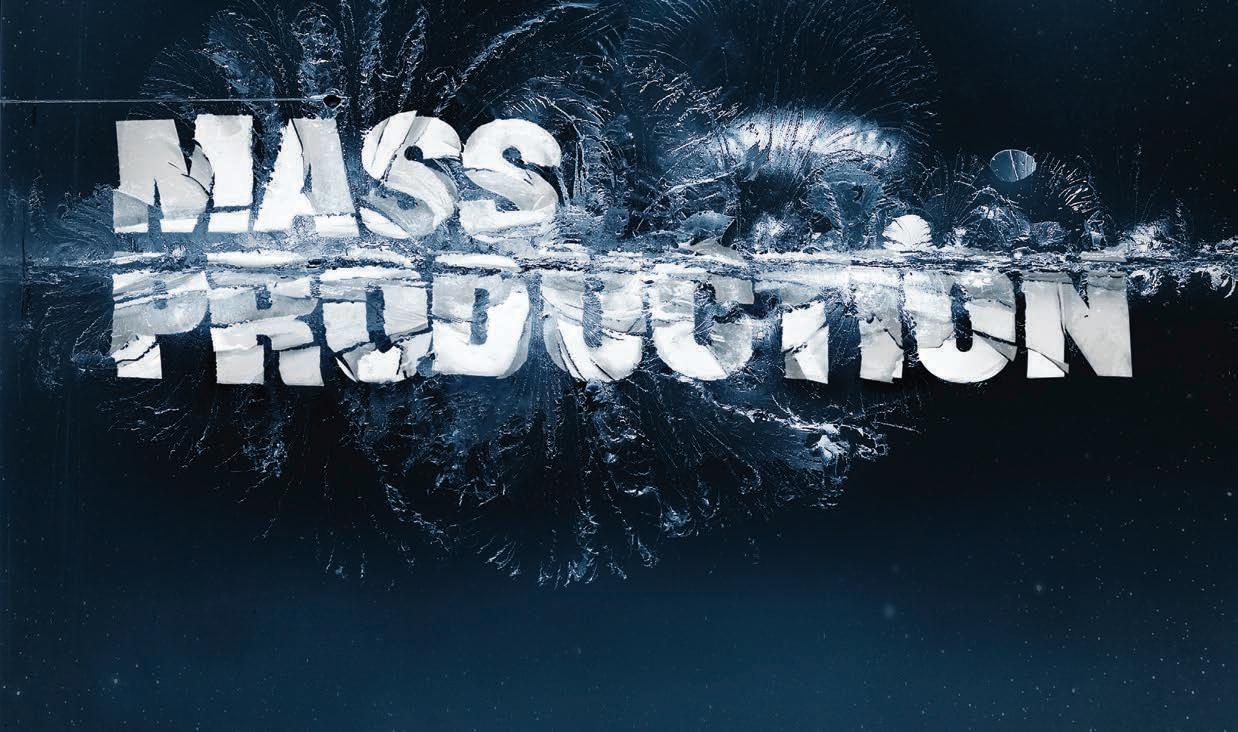
SLOW SO WE CAN WATCH EACH ROUND BEING MADE. SLOW SO THAT EVERY SINGLE ONE CAN BE HELD AND INSPECTED BY HAND BEFORE EARNING OUR NAME.
WE PRODUCE IN SMALL QUANTITIES, EACH OF OUR STATIONS CRAFTING NO MORE THAN 20,000 ROUNDS PER DAY. WE’RE A BOUTIQUE AMMO COMPANY IN THAT SENSE. more is not better. better is better.
OUR PRODUCT HAS BEEN COMPARED TO HANDMADE JEWELRY, BECAUSE IT’S MADE BY PEOPLE WHOSE CRAFT TOOK YEARS TO DEVELOP. AND YOU CAN’T recreate craft in any kind of artificial way.