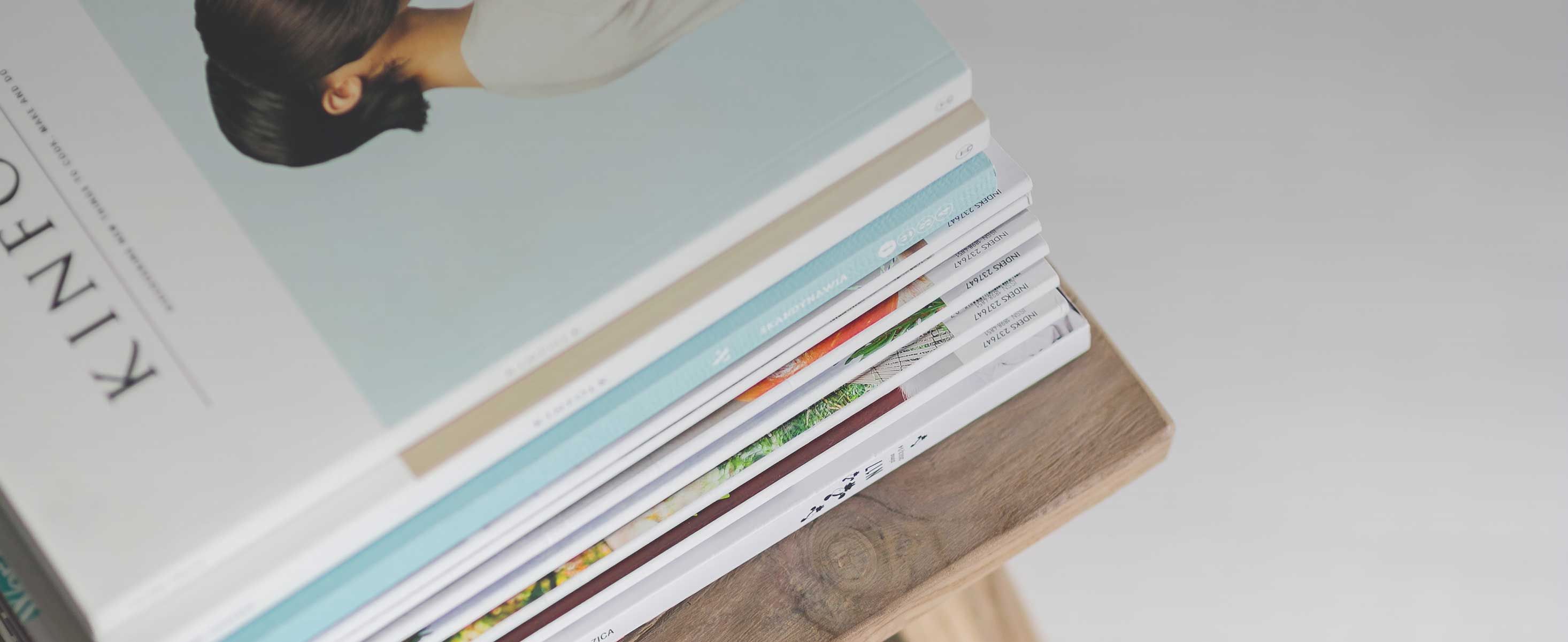
4 minute read
FINISHING
The site finishing of doors, windows and ventilators shall assure two purposes: a) protection of the metal (in the case of ungalvanized material), b) decoration of the assembly (for both galvanized and ungalvanized material )
Site finishing shall consist of the application of an undercoat and a finishing coat of paint, after any necessary touching up.
Advertisement
In the case of ungalvanized surfaces, the undercoat need not necessarily contain rust-inhibitive ingredients as it is not in direct contact with the steel. It shall however be highly resistant to moisture and to physical and chemical disintegration by the weather, and compatible with the priming coat used by the manufacturer. Lead-based paints are generally suitable, but in case of doubt, the manufacturer shall be consulted.
In the case of galvanized surfaces, the primary consideration for the undercoat is to obtain good adhesion. Adhesion to newly galvanized work is difficult to obtain, and consequently natural and chemical etching or the application of a suitable primer shall be carried out before applying finishing coats. Natural etching is achieved by weathering for several months before painting. The main disadvantage here is being able to judge when the frames have been sufficiently weathered. Chemical etching is achieved by treating with a copper-free mordant solution; these mordants are usually based on phosphoric acid The main disadvantage of this method is the entrapment of mordant solution in crevices where it can destroy the coating and even promote corrosion The safest method is by application of a primer based on calcium plumbate, where all that is necessary is to clean down (normal practice) before applying the paint. The calcium plumbate content of the pigment in such a primer shall be not less than 70 per cent.
The final finishing coat, chosen to suit the decorative scheme shall also conform to the above composition to a lesser degree. It shall be a tough, hard, smooth paint designed for external use, and compatible with the undercoat.
Care shall be taken to lee that the putty receives. adequate coatI of paint and shall be dry and hard before painting. It is advisable to carry the paint slightly beyond the edge of the putty-glass junction line to be certain of sealing the junction line
On no account shall non-ferrous parts, that is, handles, stay , catches, etc, be painted
Paint shall not be applied to working parts, such as handle pins, hinge pins, etc, where it can impede free action.
N O R M A L C O N D I T I O N S G O V E R N I N G F I X I N G
The fixing and glazing contractor shall cut holes to brick or hollow concrete block; where fixing is to steelwork or reinforced concrete, the hole shall be left ready in the correct position by the general contractor in accordance with the drawing to be provided by the manufacturer of doors and windows.
The fixing and glazing contractor shall fix the units to prepared openings with sills ready in position If openings are not made to size, are not plumb, etc, it shall be the responsibility of the general contractor to correct these openings
The fixing and glazing contractor shall be responsible for grouting and making good of doors, windows or ventilators, into openings; all rendering and plastering work in the reveals shall, however, be carried out by the general contractor.
It is usual for all necessary scaffolding to be provided, erected and dismantled free of charge for the fixing contractor by the general contractor.
The fixing and glazing contractor shall not be responsible for washing down or cleaning glass panes, He shall, however, when finishing the work leave doors, windows, ventilators and the glass panes clean and free from any dirt, putty or other adhering material.
The fixing and glazing contractor shall not be responsible for painting the doors, windows and ventilators,
S o m e o t h e r t y p e s o f S t e e l
Structural steel is durable and strong. It can be transformed into any shape including but not limited to I-Beam, L shape, T shape, and Z shape. This type of steel can be constructed in no time on the construction site. High-rise buildings and skyscrapers are constructed using structural steel but it’s also used for garages and large agricultural buildings.
Rebar steel is also known as reinforcing steel. Rebar is made from different alloys and grades of steel. Stainless steel rebar is rust-resistant and used in poured concrete driveways and construction of buildings. It’s commonly used as a tension device for reinforced concrete structures. Rebar steel is made from carbon steel. It’s also used as a tensioning device to reinforce other masonry structures. This type of steel is durable, resistant and stiff. Rebar is very useful because of its recyclable tendencies.
Alloy steel has had small amounts of one or more alloying elements such as manganese, silicon, nickel, copper, chromium, titanium, and aluminium added to it. This mix gives out properties that aren’t found in regular carbon steel. Alloy steel is usually more responsive to heat and mechanical treatments than carbon steel. Alloy steel is pretty popular because of its ease of processing, good mechanical properties, and availability.
Light gauge steel is used in modular construction, storage, light-steel framed buildings, and loads from walls above and resisting lateral wind loads S o m e o t h e r t y p e s o f S t e e l
Mild steel is also known as plain-carbon steel. It’s steel with a carbon content of up to 2.1% by weight. Mild steel is also used in steel building constructions. It’s durable and strong and makes for a sturdy establishment. Mild steel is also very flexible which doesn’t allow it to crack when it's bent. Due to its strength, it’s more suitable for buildings. This type of steel is able to withstand earthquakes making it very popular in earthquakeprone areas.