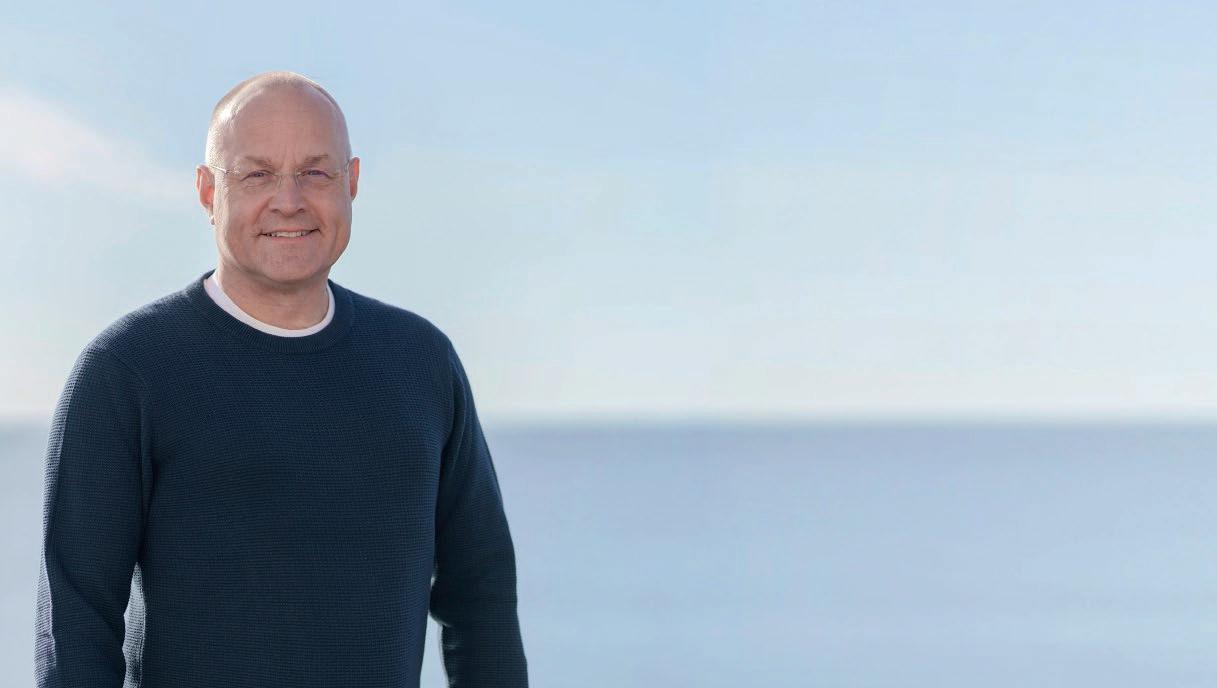
9 minute read
OUR SUSTAINABILITY AGENDA: INTENSIVE, AMBITIOUS AND COLLABORATIVE
Over the last eighteen months, Bruks Siwertell has significantly deepened its sustainability agenda, developing a robust, measurable and accountable sustainability strategy, which is now road-mapped with goals and ambitions in place
SINCE THE COMPANY’S FOUNDING , Bruks Siwertell has always been proud of the environmental credentials built into its technology. But in today’s world, every business in industry must acknowledge how much work there is to do to address climate change.
“We work in environmentally intensive industries, so this is a challenge,” says Peter Jonsson, CEO, Bruks Siwertell Group. “But it is a challenge that Bruks Siwertell Group is taking on. Our main aim is to set the sustainability standard for the industries that we serve. This includes the dry bulk handling, woodprocessing and forestry sectors.
“Our sustainability work is assessed from an environmental, social, and governance (ESG) perspective,” Jonsson continues. “It is also linked to the seventeen United Nation’s Sustainable Development Goals (SDGs), nine of which have been identified as areas of focus following a recent analysis.”
SDGs are designed to guide reflection and action on the most critical challenges, and opportunities facing humanity and the natural world. The toolbox for achieving them is the UN Global Compact principles. Bruks Siwertell’s sustainability work supports and integrates these into the Group’s policies and processes.
A busy, but rewarding year
Last year, we really started to formalize our sustainability journey, laying the foundation for this work. It has been wonderful to see our personnel’s interest and commitment to it,” Jonsson notes. “We have also recently released our first full sustainability report.”
In brief, over the last eighteen months, Bruks Siwertell Group has: appointed a sustainability team with representation from all business units; conducted a Group-wide materiality analysis, including risk analysis and stakeholder dialogues; developed a multi-year sustainability strategy at Group level and a sustainability policy; developed local action plans; and vastly increased the awareness of its sustainability work in general. drive a more sustainable world, preserving it for future generations,” Halling adds.
“This intensive program has been critical to understanding the baseline environmental impact of the business, and the company’s potential to improve across all areas of sustainability,” explains Anna Halling, Chief Strategy Officer, Bruks Siwertell Group.
“We have also developed a new line of communication and graphics: Handling The Future. ‘Handling’ is a key word within the company, with equipment transferring dry bulk materials and processed wood in ports, forests and industrial settings and facilities.
Getting down to details
The Group-wide materiality analysis was essential in mapping Bruks Siwertell’s sustainability strategy and has resulted in challenging but clear focus areas, with set ambitions to be achieved by 2030.
Bruks Siwertell’s environmental focus areas are product development, as well as energy, waste and emissions reductions. Work is underway to review electricity consumption by installing energy-efficient lighting and appliances in all offices and advocating renewable energy sources where possible. These measures have resulted in a reduction in the Group’s electricity consumption. The Group has also continued the phasing out of heating oil, in favor of certified renewable electricity.
The Group’s carbon footprint is reported according to the guidelines in Greenhouse Gas (GHG) Protocol scopes 1 and 2, and despite the increase in business activities during 2022, total energy consumption, measured in MWh, has been reduced by eight percent since 2021.
“We hope this new campaign represents our sustainability aims in a clear way. For us, Handling The Future means that we will do what we can, and what it takes now, to
“We are also working to reduce our greenhouse gas emissions throughout the value chain,” says Halling. “This year, each company within the Group will carry out climate calculations throughout their operations, and include direct and indirect emissions. This will enable us to prioritize actions in the areas where we can do the most good.”
CASE ONE: DIGITAL SOLUTIONS DELIVER NEW OPPORTUNITIES
As part of the company’s research and development strategy, digital tools and functions are being developed. Launching this year is Siwertell Smartview, a cloud-based industrial Internet of things (IIoT) system planned for phased integration into Siwertell technology.
Initially for introduction on new equipment deliveries, Siwertell Smartview will collect data during unloading and loading operations, which will provide detailed analysis of equipment performance, availability and reliability. In due course, the tool will be available for all Siwertell technology such as ship unloaders, including port-mobile and road-mobile units, and ship loaders.
The tool can monitor real-time operational parameters such as tons of material handled, average capacity, tons of material remaining in the vessel’s holds during unloading, and the overall duration of operations. All information can be simply accessed through a personal computer (PC), tablet or smartphone.
A significant element of Siwertell Smartview is its ability to generate a number of different reports, which not only enhances operational awareness, but also brings Siwertell expertise directly into the terminal as and when it is needed.
Ambitious but achievable goals
Bruks Siwertell has set a target of reducing greenhouse gas emissions by 50 percent by 2030, compared to a base level established in 2019.
“In addition to this, we have set other ambitious and measurable environmental protection targets. By 2030 we are aiming to: switch to 100 percent renewable electricity; bring the amount of waste generated in our global business units to zero; and ensure 90 percent circularity in our entire product range. These will be achieved through product development, and reducing waste from our operational emissions and energy use,” Halling highlights.
“Seeking circular solutions are important to reduce the overall environmental impact of the business and are therefore priority issues for Bruks Siwertell,” Halling continues. “Our service teams carry out repairs and maintenance to extend the service life of equipment and contribute to a reduction in waste. Service teams also ensure that customers understand how equipment is best operated and maintained, with optimal settings that lead to energy savings.
FOCUS AREAS
» Product development
» Reduce and limit CO₂ and greenhouse gas emissions
» Reduce energy use
» Reduce waste
FOCUS AREAS
» Health and safety
» Employee satisfaction
» Diversity and inclusion
“To support these efforts from offices upwards, we are looking for solutions where the waste contractor can be a partner, who in addition to the management of existing and relevant waste fractions, can also offer functions for measurement, follow-up and development.”
A priority: happy, healthy people
The company’s focus areas for the social element of its sustainability work comprise health and safety, personnel satisfaction and diversity and inclusion. “We recognize that happy, healthy people are fundamental to good business, and we are embracing this philosophy,” Halling stresses.
In 2022, Bruks Siwertell introduced a system for Groupwide employee satisfaction surveys. The results are recorded as an employee Net Promoter Score (eNPS), which is scaled from -100 to 100. The eNPS value is one of Bruks Siwertell’s new key figures. It has only been measured once before, delivering an eNPS score of 25, which demonstrates good levels of satisfaction, but by 2030, the aim is to raise this to a target score of 30.
MEASURABLE GOALS
» 50% reduction in CO₂ emissions
» 90% circularity of products
» Zero waste in our office units
» 100% renewable energy
MEASURABLE GOALS
» Zero workplace accidents
» 30 eNPS score
» 30% female managers
FOCUS AREAS
» Anti-corruption
» Supply chain management
» Management systems
MEASURABLE GOALS
» 100% compliance with Codes of Conduct for both suppliers and customers
» 100% of work processes updated and improved
ENVIRONMENTAL SOCIAL GOVERNANCE
As well as raising personnel satisfaction, by 2030 Bruks Siwertell is aiming for zero workplace accidents, and boosting gender equality by having at least 30 percent managers who identify as female.
A clear signal from the top
The third aspect of Bruks Siwertell’s sustainability work is governance and the sustainability focus areas within this are anti-corruption, supply chain management and management systems. These are essential to ensure that the company steers in the right direction. Bruks Siwertell’s main directives and goals have been evaluated and set by its owners, JCE Invest AB and Cargotec Sweden AB, and the senior management board.
“We recognize the urgency of the issues that we are working on. With our long-term ambition to set the sustainability standard for the industries that we serve, it is easier to drive towards this when owners and management have a common understanding of the importance of the issue,” Jonsson says. “Our measurable governance goals by 2030 have been set as 100 percent compliance with Codes of Conduct for both suppliers and customers and 100 percent of work processes updated and improved.”
Sustainable value chains
Bruks Siwertell already delivers ship unloaders, loaders and conveyors that possess the key elements for environmental protection: no spillage; minimal dust emissions; low noise levels; equipment reparability and longevity; low energy-consumption demands; and extremely high through-ship efficiencies, which maximize vessel turnarounds leading to the increased efficiency of dry bulk trades. Many of these elements extend to the Group’s wood-processing systems as well.
At each point of technological development, the environmental impact of equipment has been addressed, but this is not a static process. Sustainability encompasses much more than an environmental lens and extends throughout the value chain. Bruks Siwertell’s value chain comprises nine key areas: innovation and development; sales to customers; construction; materials and suppliers; assembly and manufacturing; distribution and transport, products in use; service, repair and maintenance; and recycling.
CASE TWO: AUTOMATED, ENCLOSED SYSTEMS ENSURE ENVIRONMENTAL AND EFFICIENCY GAINS
In 2022, Bruks Siwertell completed a project with an American customer in the corrugated board industry. All its facilities are certified according to the USA’s Sustainable Forestry Initiative (SFI), a certification that ensures that the forest is managed in an environmentally friendly, socially responsible and economically sustainable way.
The operator needed a complete raw material receiving and transfer system to modernize an existing and costly, partly manually handled woodyard for one of its US-based paper mills. In response, Bruks Siwertell designed an automated, enclosed solution to handle sawdust, wood chips and bark, which increased efficiency and reduced operating costs. Inventory control was also improved, as well as maintaining consistency in material quality within the pile.
Environmental gains were significant as the automated systems eliminated the need for the continuous use of diesel-powered machines to manage the piles, and dust emissions were reduced in comparison with mobile systems. Dust emissions were further reduced with the use of Bruks truck-receiving technology, specially designed to accommodate a covered hopper and equipped with dust collectors.
Traditional conveyor equipment was also replaced with an energy-efficient, fully enclosed low-friction conveying system, which minimizes material degradation and further dust formation. As the air-supported conveyor system eliminates the need for traditional rollers, maintenance requirements and costs were also significantly lowered.

The chain starts with understanding customer needs and market knowledge, driving the company’s development projects. This is a continuous process, occurring during projects where customers require specific solutions that are adapted to their operational requirements.

The sale of equipment happens through representatives, partners, and dealers, with lead times dependent on the equipment and customer requirements. This is followed by the construction phase, and can comprise project-based, tailormade or standardized products.
Critical elements in the cycle
External collaborations with suppliers are critical and set within the Group’s Code of Conduct framework, enabling long-term, successful relationships. This includes materials suppliers as well. The majority of Bruks Siwertell’s products can be manufactured by completely or partly recycled materials, with assembly or manufacturing from these materials taking place as close to customers as possible, reducing the impact of transport.
Transport, both in the form of deliveries to the factory and the distribution of products and systems to the customer, is mainly carried out by truck freight. In specific circumstances, container vessels or break bulk vessels are used because of the size of the equipment, and when ship unloaders are delivered fully assembled, this is carried out via heavy-lift vessels.
Our products are used, for example, in port operations, forestry settings, sawmills, power plants and pulp and paper industries. These are challenging environments with high demands on efficiency, reliability and safety. A key part of a product’s ongoing performance is service, repair and maintenance. A commitment to through-life care underpins Bruks Siwertell’s delivery promises. Once equipment, which is predominantly steel, has reached the end of its service life, the majority can be recycled.
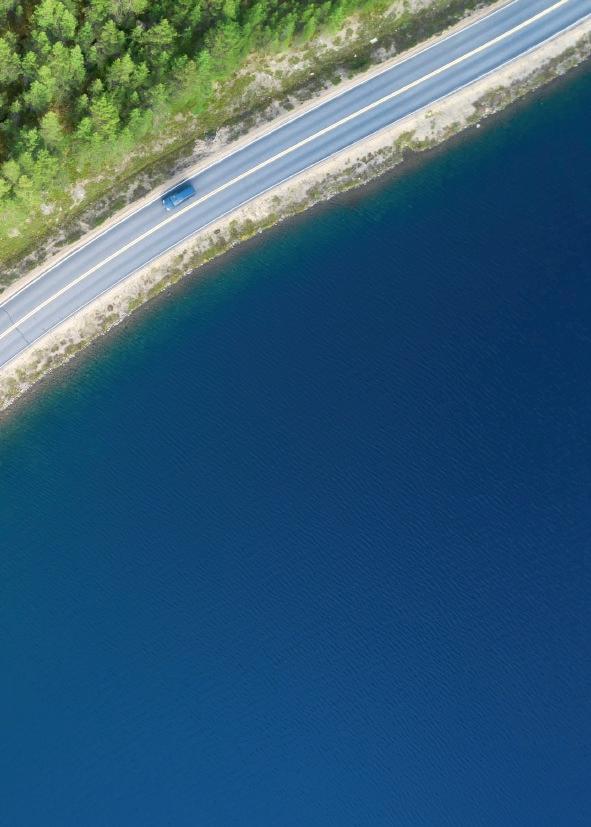
No stopping us now
“Over the past year, we have set our strategy and carried out extensive mapping and planning work. This year it is time to move from plan to action. Going forward, it is important that we continue to ensure that we have sufficient resources for this work and maintain the current commitment to continue to motivate our personnel. We will do this by communicating the impact that they are having.
“The intensity of Bruks Siwertell Group’s sustainability work will continue and is constantly developing as we learn more. If targets are achieved, we will set tougher ones,” concludes Jonsson.
Join Our Journey
Stakeholders underpin the business and Bruks Siwertell’s sustainability work. Therefore, this year the company is looking to extend and expand stakeholder dialogues and initiatives.
“Our sustainability journey is not one we want to do, or can do, alone; we hope that as many of our customers, suppliers, business partners and other stakeholders as possible join us in these efforts,” says Anna Halling, Chief Strategy Officer, Bruks Siwertell.
To further Bruks Siwertell’s sustainability work, and ensure that the dry bulk handling industry is sustainable as possible, Bruks Siwertell would welcome:
• ideas for partnerships around sustainable joint initiatives
• ideas and feedback on where research and developments should be focused. This could connect to operational requirements or increased restrictions in specific industry environments
• ideas about sharing how to achieve Bruks Siwertell Group’s 2030 goals
• knowledge sharing, including examples and inspiration about initiatives that have enabled other stakeholders to already achieve set sustainability targets
If you are interested in participating or have any other relevant ideas that you would like to share, please contact: Anna Halling, Chief Strategy Officer. anna.halling@bruks-siwertell.com