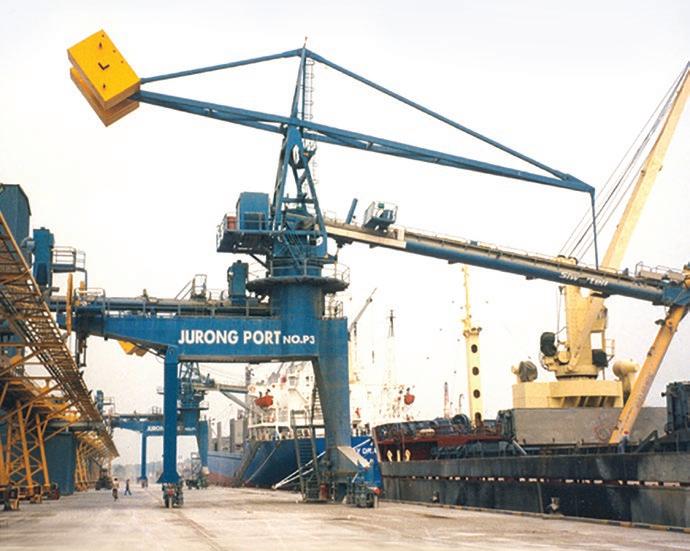
6 minute read
News in brief
NEWS IN BRIEF
New Siwertell ship unloaders extend dust-free cement handling in Singapore
A prestigious new order will see Bruks Siwertell deliver three new Siwertell ship unloaders to Jurong Port in Singapore. The trio will join existing Siwertell technology, delivered in the late 1990s, and together they will ensure the environment-friendly handling of Singapore’s cement imports.
Singapore upholds strict environmental standards in cement handling and Jurong Port works closely with local government authorities on establishing requirements and measures to minimize fugitive dust from any industrial operations, and maintaining operational safety standards. As the world’s largest common-user cement terminal for over twenty years, Jurong Port’s Cement Terminal started off with three high-capacity Siwertell ship unloaders that collectively met the cement handling needs of multiple smaller import terminals. “With the evolution of technology and equipment, Jurong Port is delighted to work with Bruks Siwertell to take our terminal’s capabilities and standards further in our vision of becoming a next-generation multi-purpose port,” says Tan Wee Meng, Chief Technical Officer, Jurong Port. “This is a very positive endorsement of our Siwertell ship unloading technology, ” says Ola Jeppsson, Bruks Siwertell Sales Manager, APAC. “The new units, like all Siwertell unloaders are totally enclosed, and will secure the continuation of extremely efficient, high-capacity cement handling for the port, without dust emissions or spillage, so no cement is wasted “It is now time to retire two of those hard-working unloaders,” continues Jeppsson. “They have served the terminal well for over two decades, and their proven performance was a deciding factor in the port once again opting for Siwertell technology. The new units will continue their legacy of impressive through-ship efficiencies and will work along-side one of the older units, which will remain in service. Together they will handle Singapore’s cement import volumes.”
Like their predecessors, the three new ST 490-M screwtype rail-traveling unloaders will each discharge cement, fly ash and cement slag from vessels up to 50,000 dwt at a continuous rated capacity of 800t/h.
Two of the new unloaders are scheduled for delivery in May 2022 and the third by the end of 2022. All will be fully assembled prior to delivery and transported by heavy-lift ship. Final commissioning and performance tests will be
carried out in Jurong Port. and the environment is protected.
A trio of new ship unloaders will join existing Siwertell technology, delivered to Jurong Port in the late 1990s
The USA-based Colonial Group has ordered a new highcapacity Siwertell ship unloader. The fully enclosed system will deliver dust-free cement handling for the company’s Savannah, Georgia, terminal, and supports Colonial’s cement import growth. “Environmental credentials were a strong factor in securing the contract,” says Ken Upchurch, VP Sales and Marketing,
Port-mobile unloader expands material range
The latest market-changing Siwertell ship unloader, the port-mobile unloader, can now offer totally enclosed, highefficiency dry bulk material handling to the alumina, cement and soya meal sectors, as well as grain. “The port-mobile unloader was initially launched to challenge the limitations of pneumatic discharge systems used in grain handling,” says Jörgen Ojeda, Director, Mobile Unloaders, Bruks Siwertell. “However, we realized that, as well as ensuring high-capacities, no spillage and close-to-zero dust emissions, it delivers many distinct benefits when handling all these materials. Bruks Siwertell. “The unloader will be installed near a historic, very sensitive, downtown location; any industrial activities in the area must comply with strict environmental protection regulations.
“The Siwertell unloader offered this capability, along with impressive through-ship efficiencies, making it the ideal machine,” continues Upchurch. “Also, by working closely with Colonial and its engineering team, we were able to develop a customized solution that will work within the operator’s existing infrastructure.
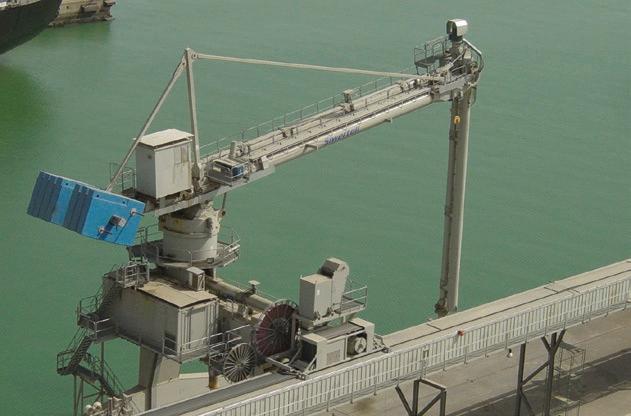
Colonial’s new Siwertell unloader will deliver dust-free cement handling at a rated capacity of 800t/h “Furthermore, the combined capabilities now offered by the merged Bruks Siwertell Group, provide Colonial with local support that is unmatched by others,” he adds.
Colonial increases Savannah Terminal unloading capacity
The Siwertell 490 F-type ship unloader offers a rated cement handling capacity of 800t/h and can discharge vessels up to Panamax size. They have proven capabilities in dry bulk handling installations worldwide and have been specially engineered to be lighter than other systems in their capacity
class, offering significant cost savings in jetty reinforcements. “This is Colonial’s first Siwertell ship unloader,” Upchurch notes. “The company was impressed by the technology and the machine’s flexibility, enabling it to handle various designs and capacities of geared vessels.”
Machine components will be delivered to Savannah for assembly in May 2021 and the unloader is planned for com-
missioning by August 1, 2021.
The Siwertell port-mobile ship unloader can handle alumina, cement, soybean meal and grain
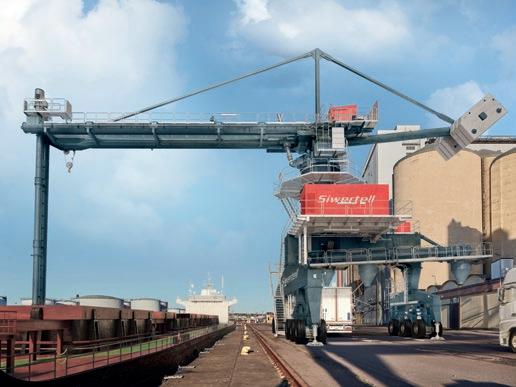
“One of the greatest advantages of unloading dry bulk, especially more delicate cargoes, with screw-conveyor technology is the low material degradation rates, minimizing the production of powdery fines,” explains Ojeda. “Like all Siwertell unloaders, port-mobile units offer a steady conveying velocity, with no particle collisions or crushing forces, which is in contrast to the cargo degradation concerns that traditionally accompany pneumatic unloaders.”
Fines, produced when materials degrade, are problematic for many dry bulks, but for alumina, the cost of smelting is
Service tower added to ship unloader range
A new service product, which will substantially simplify and lower the cost of fitting replacement screws on marketleading Siwertell ship unloaders, has been launched. “All our equipment, including service strategies, benefits from decades of continuous research, development and improvement, and the latest product is a service tower for replacing screw sections on our Siwertell ship unloaders,” says Björn Ohlsson, Manager, Bulk Terminals Design and Engineering, Bruks Siwertell. “It offers a number of key advantages,” he explains. “Principally, the service tower eliminates the need for cranes, which are traditionally used to lift the screws. This reduces dramatically increased by their presence, and for grains and soya beans, the quality of whole shipments can be downgraded; significantly impacting profits.
“For operators looking for a flexible, port-based system, and needing to discharge large vessels at a high capacity, then our new port-mobile unloaders are a fantastic, extremely cost-effective option,” adds Ojeda.
The port-mobile unloader is available in two sizes, a 400t/h and
600t/h model; both can discharge vessels up to 60,000 dwt. costs and improves the overall safety of the operation. Also, because the tower is specifically designed for the task, the whole process is faster; various screw lengths and sizes can be accommodated using adaptors.”
Replacement screws are placed and fitted into the tower’s lowered screw-holding cradle, specifically matched to the dimensions of the screw. A winch raises the cradle and screw into an upright position. When in place, the new screw is locked into position and the outer diameter bearing wings are assembled. The same procedure is repeated with the next screw section. Removal and disassembly of the screws are achieved using the same equipment, but in reverse.
“Although specifically designed for screw replacements, it can also be built with additional levels to service and inspect other areas of the vertical conveyor,” notes Ohlsson. “For any new or existing unloader, this is an extremely cost and time effective addition to any operator’s service portfolio.”
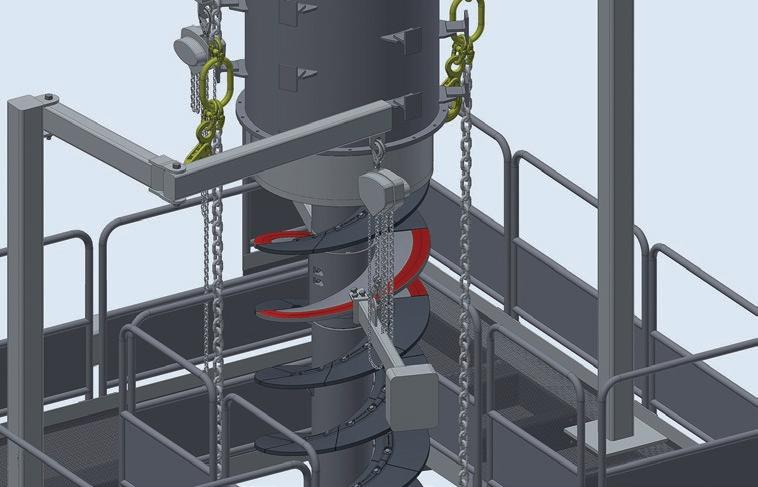
The new service tower eliminates the need for cranes, with replacement screws winched into place