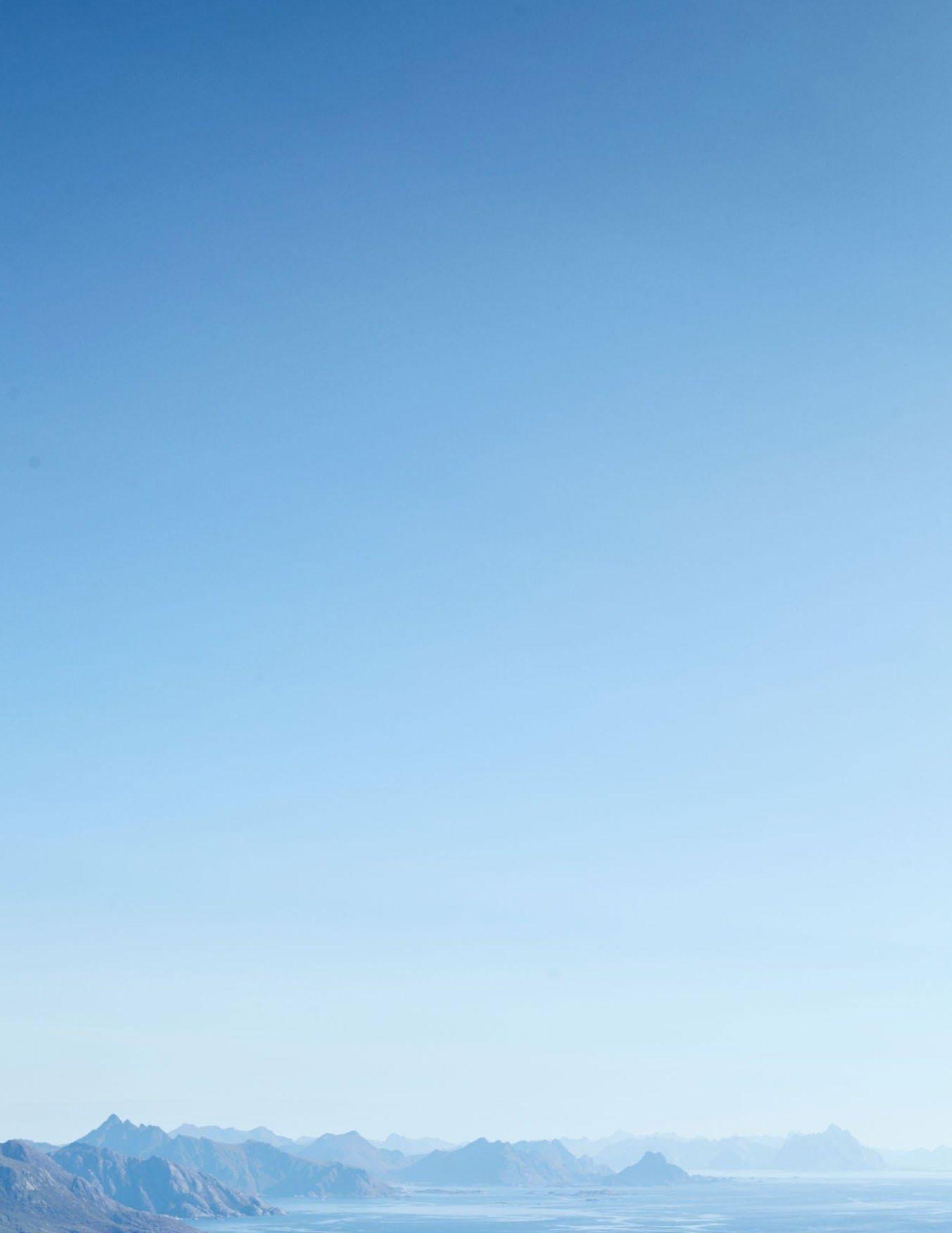
3 minute read
Thyssenkrupp Revolutionizes
the Industry with the World’s First rail-running conveyor system for Tier 1 Copper miners
Thyssenkrupp, a global engineering conglomerate, announced today that it will construct the world’s first rail-running conveyor (RRC) system for a Tier 1 copper miner.
This development is expected to revolutionize the mining industry. This revolutionary system will transform the way mining operations are conducted, delivering unprecedented efficiency and cost-effectiveness.
The objective of the partnership between Thyssenkrupp and the Tier 1 copper miner is to address industry-wide issues such as high costs, limited accessibility, and environmental concerns. By implementing the rail-running conveyor system, they will expedite the transport of copper ore from the mine site to the processing facility, drastically reducing the operational complexities associated with conventional hauling techniques.
The rail-running conveyor system functions on a network of rails installed along the mining site, allowing for continuous transport of ore-laden containers. This results in significant cost savings and enhanced operational efficiency by eliminating the need for conventional truck transportation. In addition, this system reduces the environmental impact by emitting fewer greenhouse gases than conventional mining transportation methods.

Thyssenkrupp’s Rail Running Conveyor system utilizes cutting-edge technology to ensure seamless integration with existing infrastructure, thanks to the company’s extensive experience in engineering and mining solutions. The adaptability of the system enables it to surmount terrain restrictions, curves, and inclines, maximizing output while minimizing downtime and maintenance.
The Tier 1 copper miner recognized the game-changing potential of this innovation and collaborated with ThyssenKrupp to implement the rail-running conveyor system in their mining operations. Both businesses are dedicated to operational excellence and sustainability, making this partnership a natural choice.
The advantages of the rail-running conveyor system are not limited to cost savings and environmental benefits. The implementation of this technology will generate new employment opportunities and improve worker safety. With the automated and controlled operation of the system, the reliance on manual labor for transportation activities will be drastically reduced, thereby mitigating potential risks and hazards associated with conventional mining transportation.
Advantages
The successful implementation of Thyssenkrupp’s Rail Running Conveyor system promises to revolutionize not only the copper mining industry but also the mining industry for other minerals. This innovation has the potential to establish global benchmarks for operational efficiency, sustainability, and safety in mining operations.
The rail-running conveyor system from Thyssenkrupp represents a significant advancement for the mining industry. This innovative solution will pave the way for more sustainable and economically viable mining practices by eradicating the inefficiencies and environmental impact of traditional transportation methods. With its innovative technology and the support of a Tier 1 copper miner, Thyssenkrupp is positioning itself as an industry pioneer for revolutionary change rail-running.
Revolutionizing Mining Transportation: An In-Depth Look at How the Rail Running Conveyor System Works
ThyssenKrupp's Rail Running Conveyor (RRC) system is a groundbreaking advancement in the mining industry, revolutionizing how materials are transported while prioritizing efficiency and environmental sustainability. This innovative system operates on a network of specialized rails strategically placed throughout mining sites, disrupting the conventional reliance on trucks for transportation.
At the heart of the RRC system are transport units equipped with wheels that travel along these rails, enabling the efficient conveyance of substantial quantities of materials, such as copper ore. These units are engineered to adapt seamlessly to various site constraints, including curves and inclines, ensuring compatibility with existing infrastructure. One of the system's most significant advantages is its automation and control, reducing the need for manual labor and mitigating transportation-related risks in mining operations. This enhances worker safety, minimizes outages, and optimizes productivity while reducing operational expenses.
Loading and unloading stations strategically located along the rail network further accelerate the transportation process by minimizing manual labor, ultimately boosting overall productivity. Moreover, the RRC system offers substantial cost savings by eliminating the need for conventional truck transportation, reducing petroleum costs, maintenance expenses, and labor requirements.
Beyond economic benefits, the RRC system aligns with global initiatives to reduce emissions and minimize the environmental impact of industrial practices. It emits fewer greenhouse gases compared to conventional vehicle transportation, making it an environmentally sustainable choice for mining operations. Importantly, the implementation of the RRC system creates new job opportunities within the mining industry. As transportation becomes less reliant on manual labor, there is an increased demand for skilled employees to operate and maintain the system. This shift towards advanced technology supports the growth and development of the mining industry.
ThyssenKrupp's Rail Running Conveyor system has the potential to transform not only copper mining but also other mineral extraction operations. By setting new industry standards for operational efficiency, sustainability, and safety, this technology is expected to have a global impact on mining practices. In summary, the Rail Running Conveyor system from ThyssenKrupp is reshaping the mining transportation landscape by substituting traditional vehicle transportation with an automated rail network. This innovative solution maximizes efficiency, reduces costs, and minimizes environmental impact, propelling the mining industry toward environmentally and economically sustainable practices. The future of mining transportation has arrived with the RRC system, setting the stage for a more efficient, safer, and greener mining industry.