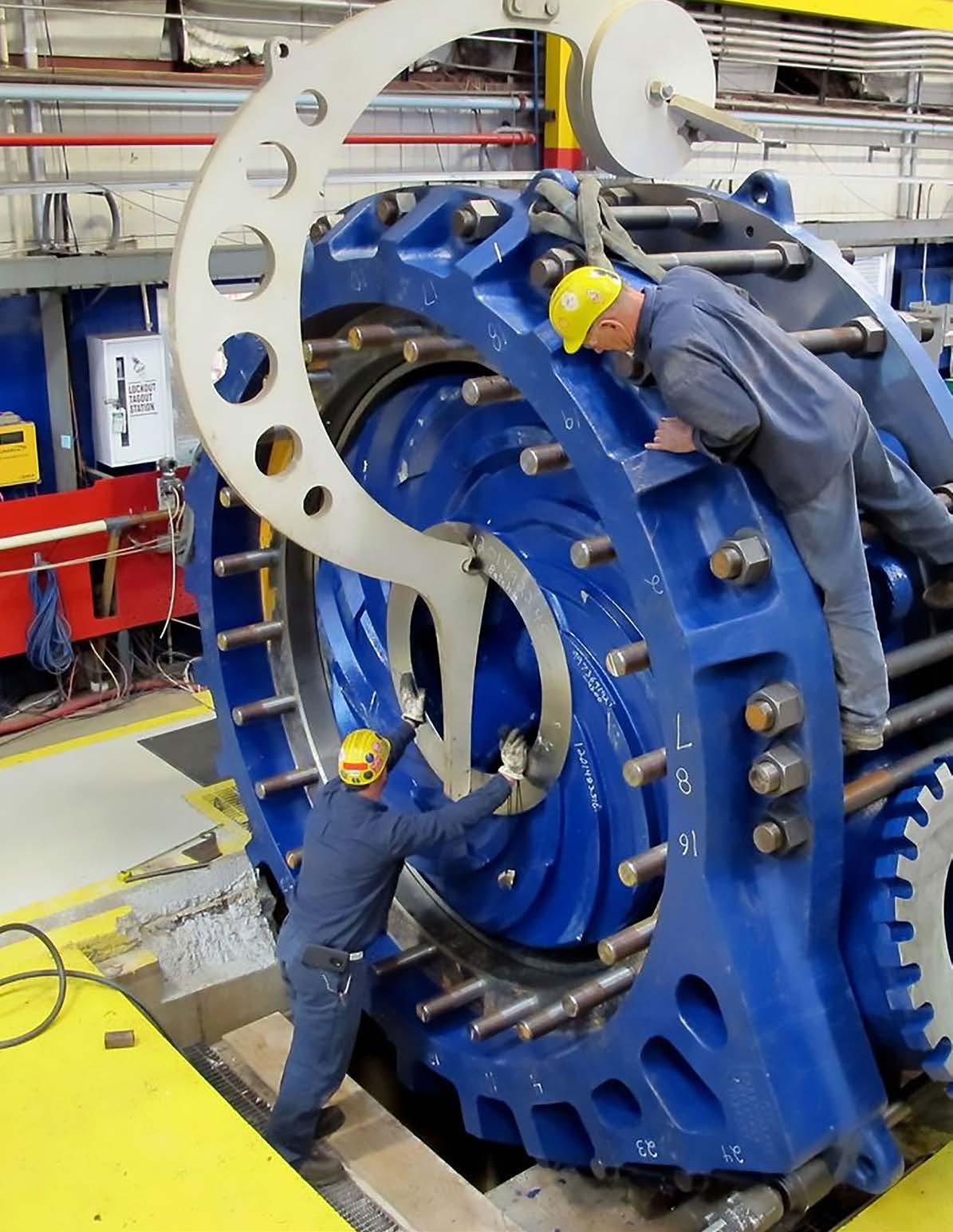
7 minute read
Flying the New Bar with Pumps: A New Level
EQUIPMENT
Flying the New Bar with Pumps: A New Level
KSB, A LEADING PUMP MANUFACTURER, DESCRIBES HOW ITS MDX SLURRY PUMP FOR MILL CIRCUITS IMPROVES EFFICIENCY AND WEAR LIFE.
Within the pump industry, it is generally acknowledged that the extraction of minerals from rock places the highest demands on fluid handling equipment.
Pumps must not only deal with violent slurries and constantly changing working environments that cause unnecessary wear, but they must also provide the highest standards of reliability.
As a result, manufacturers have responded by developing highly advanced, heavy-duty slurry pumps capable of lowering total cost of ownership, increasing performance, and minimising downtime.
Mining is not a sector in which pump companies can dabble on the side; they must be completely committed. This dedication starts with research and development, which drives constant improvements in pump and material www.skillings.net | 25
EQUIPMENT
technology, implements new technology such as artificial intelligence, machine learning, and remote sensing, and enhances complex parts' manufacturability.
Pumps for SAG and ball mill circuits, mill discharge, cyclone feed and screen pumping, hydro-transport, and tailings booster stations are available from reputable pump companies.
To have the best and most efficient products for transporting slurry, the pump manufacturer must have experience in hydraulic design, mechanical design, wear technology, and materials technology. They should also be willing and able to work with their customers during the pumps' lifecycle to provide the best results and value for money.
HEAVY-DUTY SLURRY PUMPS ARE NEEDED FOR AGGRESSIVE SLURRIES
“While no two slurries are the same, all slurries place extreme demands on pumps,” says Jonathan Samuel, vicepresident, sales and marketing, for KSB in hard rock mining. “Slurry pumps used for solids transport have to move a variable composition of rocks, sands and chemicals.
Under such abrasive and corrosive conditions, pump parts can wear out very quickly. When pump parts wear out before planned outages, the entire production process comes to a grinding 26 | SKILLINGS MINING REVIEW April 2021
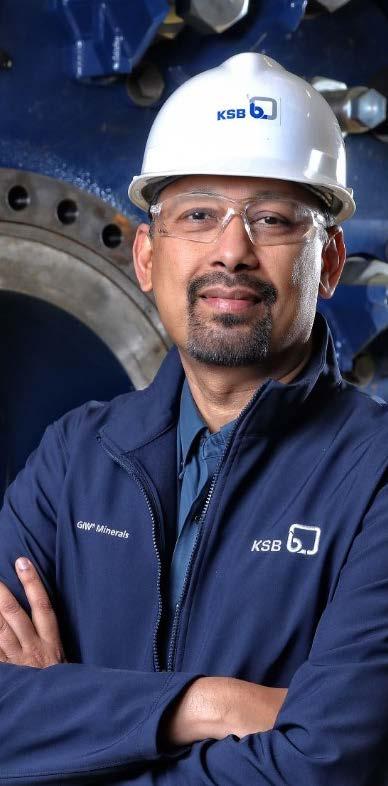
halt, resulting in exorbitant costs and production losses. That means reliability is essential in any slurry transport system.”
For more than 130 years, the KSB Group has been serving the mining industry, and it is now engaged in mining operations all over the world. The mining operation's headquarters are at the GIW Industries plant in Grovetown, Georgia, where some of the world's largest centrifugal slurry pumps for hard rock mining, dredging, and the oilsands industry have been constructed, tested, and manufactured for many years. For any application in mining, GIW manufactures a wide range of slurry pumps in various materials.
In addition to slurry pumps, the KSB Group offers a wide range of process pumps that can be used in various non-slurry applications in mines and minerals processing plants. Submersible bore well pumps, vertical turbine pumps, horizontal split case pumps, multi-stage high-pressure pumps, single-stage horizontal pumps, and other types of pumps are available.
EXPERIENCE OF HARD ROCK
The mill circuit, to a large degree, is where the most extreme duty conditions in hard rock mining can be found, and this places significant demands on pumps. The abrasive nature and density of the slurry being pumped can cause early component wear, resulting in component failure and costly mill downtime.
This means that the pump's architecture and materials must be able to handle solids-laden slurries while still providing stability and long wear life. The slurry must move through the pump with as little wear as possible on the tubing, liners, impeller, and shaft sealing mechanism. They must also be able to deliver high flow rates and endure harsh operating conditions.
It becomes possible to establish a head/quantity and efficiency curve essential for efficient mill operation by adding features that resolve them. Since the pump is matched to operating cycle times with mill outages, efficiency is maximised and operating costs are reduced. A lower specific speed design, a slurry diverter, a variety of high chrome white irons, and multiple suction liner configurations are just a few of the important features that KSB offers in its MDX slurry pump for mill circuits.
PUMP PRODUCTION MDX
Even under varying flow conditions, a large diameter impeller allows for slower pump operation, which increases the wear life of wet-end components. By reducing particle recirculation between the impeller and the liner, a slurry diverter greatly extends the life of the suction liner.
“The diverter is based on the theory that if particles can be excluded from the nose gap, wear life is enhanced,” explains Jonathan Samuel. “Research has shown that internal velocity and pressure gradients between the impeller shroud and the suction liner can allow particles to migrate toward the suction eye.
These solids contribute to the wear-induced degradation of the gap between the suction liner and the impeller. As this gap grows, wear rates increase and pump efficiency is reduced.” The particle flow was confirmed in laboratory tests at the GIW plant, which
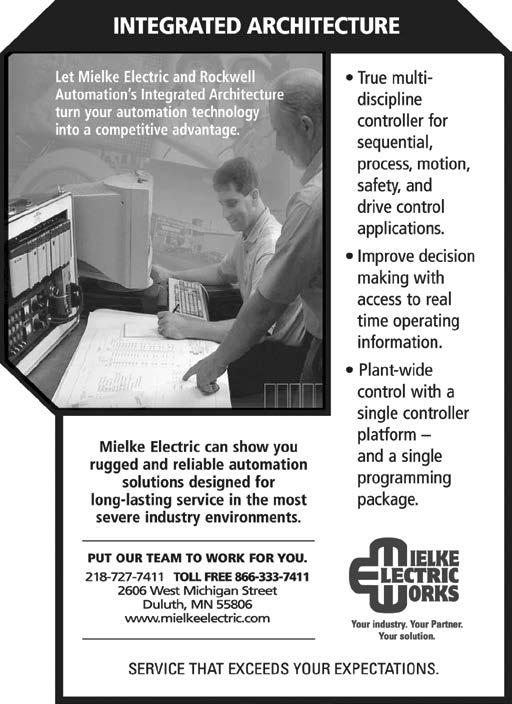
EQUIPMENT
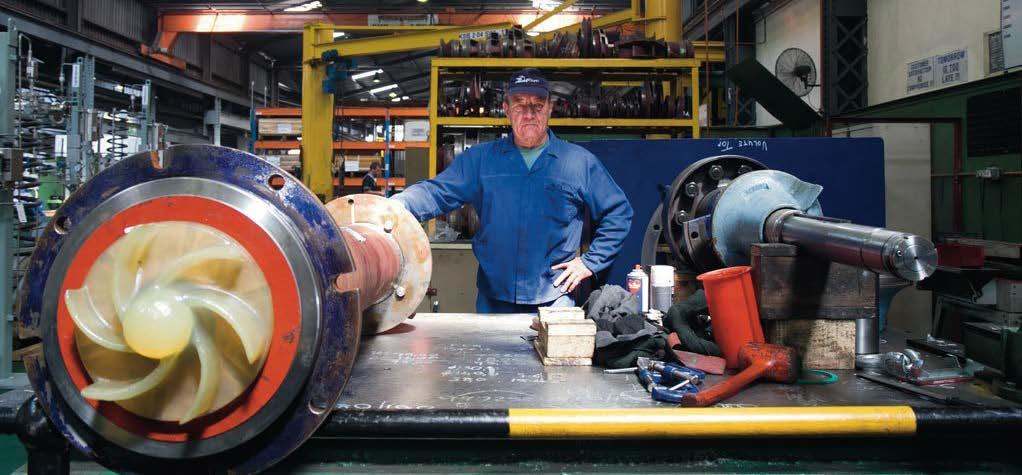
Photo by Duane Daws
led to the creation of various methods to combat it. The flow path of particles can be reversed by ‘diverting' them away from the suction liner of the pump.
The result is the KSB-patented slurry diverter, which greatly increases the MDX pump's average service life when processing the same number of ore.
Slower speeds and the development of the slurry diverter aren't the only features that give the MDX pump wear resistance. The impeller inlet's proprietary architecture enables both liquid and solid phases to exist in the slurry.
By giving the pump a deep base circle, you can reduce abrasion by minimising violent particle impingement. Oversized shrouds improve vane efficiency by adding a clearing action between the impeller and the suction liner, reducing recirculation and wear. The adjustable suction liner allows the user to maintain a close nose distance, improving wear life and increasing efficiency.
This is extremely beneficial to the plant operator because it reduces costs by aligning operating cycle times with mill outages. The MDX pumps have thicker cross-sections in the wet end components, which allows for a long and stable pump life. To combat wear caused by velocity problems, GIW also offers multiple configurations of Suction Liner nature.
GIW's dedication to materials research and development has resulted in the creation of a range of high chrome white irons that provide consumers with a variety of choices based on their ore characteristics, operating philosophy, and production objectives.
“The MDX has an established and successful position globally for mill discharge pumps, e.g., in SAG mill, ball mill discharge, cyclone feed and screen feed application,” Samuel says. “It is more than capable of delivering flows of up to 14,000 m³/h, heads of 45m at slurry densities in excess of 1.65.”
Customers in the hard rock mining industry want a pump that can handle a wide range of duty conditions while still providing full throughput at the lowest possible cost. Now that the MDX has a large foreign installation base, KSB is working hard to meet and surpass these high standards.
1. 1. Visit Us Online At: Visit Us Online At: www.skillings.net. Select Subscribe Tab. www.skillings.net. Select Subscribe Tab. 2. 2. Fax The Completed Card 888-261-6014Fax The Completed Card 888-261-6014 3. 3. Call: 909- 962-7321 x 4Call: 909- 962-7321 x 4 4. 4. Mail The Completed Card. Mail The Completed Card.
MINING INFO YOU DON’T HAVE TO DIG FOR....
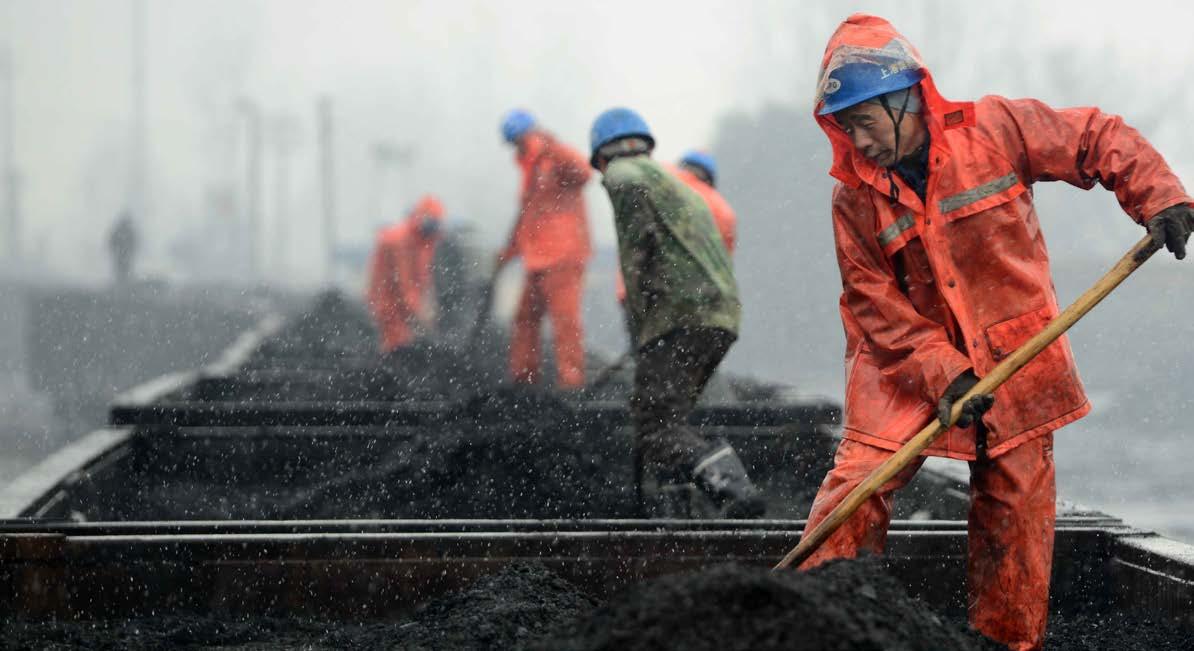
SUBSCRIBE NOW FOR IRON ORE MINING NEWS AND MORE
SUBSCRIPTION INFORMATION
............................................................................................................ .........................................................Suite........................................... City:..............................State:..........................Zip:.............................. Phone............................. Fax .............................................................. E-Mail .................................................................................................
c Amount Enclosed.......................................................................... c Please Bill Me Card Number: .....................................................................................
Exp. Date: ...................... c Visa c MaterCard c American Express CVS No. (Security Code): ....................................................................
SUBSCRIPTION RATES (ALL FUNDS IN U.S. DOLLARS)
Check ( ) your choice of Subscription.
SKILLINGS MINING REVIEW
One-Month: c $72 BY AIR MAIL One-Month: c $109
SKILLINGS MINING REVIEW DIGITAL
One-Month: c $4.95
SKILLINGS MINING REVIEW
International Rates (outside the US) One-Month: c $250 BY AIR MAIL: One-Month: c $335
Return This form to
