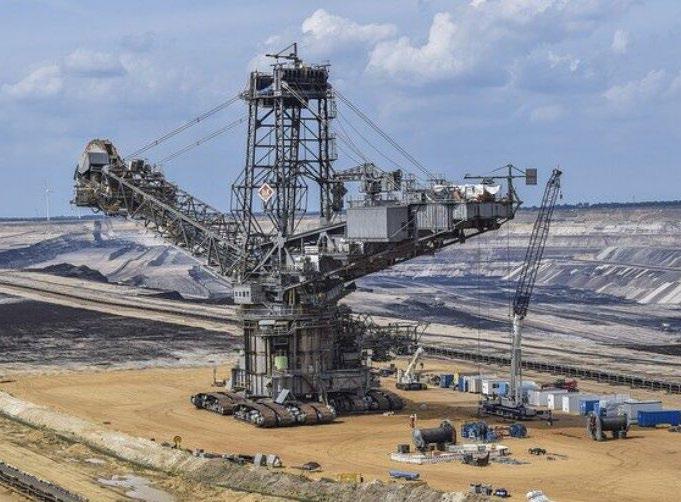
4 minute read
The Pilbara’s most techno logically advanced mine is Gudai-by Darri's Rio Tinto
SPECIAL FOCUS
The Pilbara’s most technologically advanced mine is Gudai-by Darri's Rio Tinto
The state-of-the-art Gudai-Darri mine operated by Rio Tinto has begun operations in Western Australia's Pilbara region. Rio Tinto's 17th iron ore mine, with a capacity of 43 million tonnes annually, has been delivered after 14 million hours of labor since development got underway in April 2019.
With some of the most cuttingedge machinery, including a robotic ore sample laboratory that gives visibility of the ore grades out of the mine within minutes, it is the company's most technologically advanced iron ore mine in the area. There are autonomous trucks, trains, and drills, which are common in many of Rio Tinto's Pilbara mines, as well as a virtual processing plant that enables teams to swiftly test various scenarios before putting them into practice.
Gudai-Darri combines a number of advances, such as
Robotic drills and vehicles
Three CAT MD6310 autonomous drills and 23 CAT 793F autonomous haul trucks are both available at Gudai-Darri. Using sensors, the trucks use real-time ore tracking to give live dig face progression, and the drills' data-informed modeling contributes to building more precise evaluations of the ground's current conditions and enhancing safety. Rio Tinto is developing the creation of emission-free autonomous haul vehicles in partnership with Caterpillar. It is envisaged that the world's first operational deployment of Caterpillar 793 zero-emissions autonomous haul trucks will take place at Gudai-Darri after development is complete.
Gudai-Darri anticipates increasing iron ore production volumes beginning in the second half of this year and reaching capacity in 2023. The mine has an expected life of more than 40 years.
One-third of the mine's electricity requirements will be met by a 34-megawatt solar farm being constructed by Rio Tinto, with completion scheduled for August 2022.
A one gigawatt solar and wind power project in the Pilbara, which may be seven times bigger than Western Australia's
The first autonomous water carts in the world
The new vehicles, which Caterpillar and mine operations jointly developed, are largely used for dust suppression on the job site, increasing productivity by allowing mine operations to digitally track water use and decrease waste. When the location's dry and dusty circumstances are detected by the vehicle's sophisticated onboard technology, water is applied to the roads to maintain their condition.
Autonomous locomotives (AutoHaul)
The first fully automated long-distance, the heavy-haul rail network in the world, AutoHaul, went into full operation in June 2019. Remote operators are keeping an eye on the driverless train from the Operations Center in Perth, which is more than 1500 kilometers distant.
First rotatable bucketwheel reclaimer from Rio Tinto
Reclaimer maintenance typically necessitates a protracted stoppage while several components are taken out. This patented global first will make it possible to replace the complete bucket wheel module for care, increasing safety and effectiveness. Laboratory for robotic ore sampling
Our mine is integrated with the highly automated Gudai-Darri laboratory. Production samples (both lump and fines) are conveyed into the lab from the sampling station by a robot, who then moves them to the automated production cell. The excellent sight of the ore grade being stacked up on-site will be made possible by this facility.
Robots in a warehouse for heavy mobile equipment
Four automatic guided vehicles (AGVs) made to automate the handling of pallet frames are housed in the heavy mobile equipment (HME) warehouse. With the addition of laser obstacle scanners and auto-stop features, AGVs will lessen manual handling while increasing safety in the warehouse. Field mobility without paper
The business is utilizing technology to give its employees access to real-time data while they are on the job, linking teams to one another, to projects, and assets. Team members may access many of the apps they need in the field using tablets, eliminating the need for paper-based systems and cutting down on nonessential travel.
The team members will be able to visually traverse the digital asset, organize their work using a (to scale) 3D model, and examine or download related technical data and papers thanks to this asset, which will be a first for Rio Tinto. A feature-rich, interactive 3D environment is created using the same digital asset data for virtual reality training. A solar farm
The solar farm has roughly 83,000 photovoltaic solar panels, which are used to turn sunlight into power. When construction is finished in August, the facility's capacity, which is up to 34MW, should be able to meet about a third of the mine's typical electrical needs.
largest solar farm, is also being developed by the iron ore miner. Premier of Western Australia Mark McGowan claimed that the multi-billion dollar investment would strengthen the state's economy and create thousands of employment over the course of the mine's 40-year life.
Western Australia has a strong economy, a highly qualified workforce, and world-class mineral resources that are supported by industry-leading mining and logistics infrastructure. In light of this, our state is positioned for the future, he remarked. representatives of the Pilbara Traditional Owners, the Banjima People, Mines, and Petroleum, claimed that Rio Tinto's creativity and sustainability served as a model for mines of the future.
"Once the new solar farm is finished, it will be able to supply Gudai-Darri with one-third of its operational energy requirements. This will cut annual carbon dioxide emissions by 90,000 tonnes, or about the same as 6,000 Australian dwellings, he added.