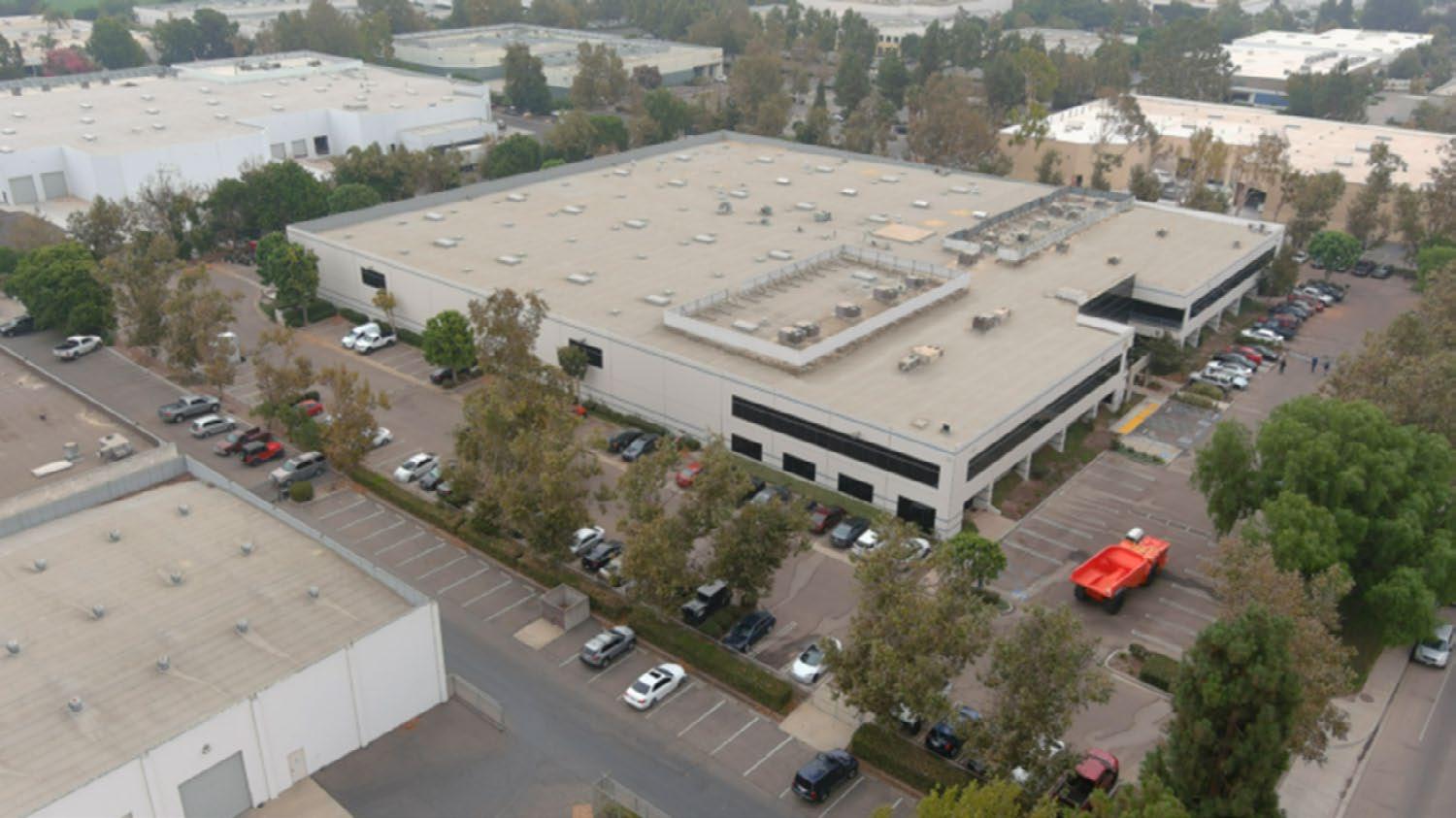
17 minute read
Sandvik Needs To Be Applauded In Underground Mining: Established A New and Commendable Bat- tery System Safety Standard
THE LEAD
"Sandvik's state-of-the-art battery system facility in Camarillo, California, boasts 100 MWh of annual battery production capacity, as well as acting as a training and customer visitor center with a test ramp that has a 20% grade and a whole area for mucking on the property"
Sandvik Needs To Be Applauded In Underground Mining
Established A New and Commendable Battery System Safety Standard
The TasTe and need for baTTery-elecTric vehicle (bev) soluTions in The mining industry have increased tremendously in the 3.5 years since Sandvik bought Artisan Vehicle Systems. From discussions that were primarily focused on North America and concerned the testing of BEVs, the industry has advanced to talk about commercial, fleetsized applications that will be implemented all over the world.
With the award of its largest BEV contract to date—a 20-piece equipment order from Canadian company Foran Mining—Sandvik itself emphasized this in July. The industry's increased emphasis on underground electrification using batterypowered machinery has also raised the volume and complexity of concerns around battery system safety.
(BHEV) Battery and Hybrid Electric Vehicles Business Unit of Sandvik Mining and Rock Solutions is more than ready to conduct these discussions, according to Jakob Rutqvist, the unit's VP of Strategy and Commercial.
As an early adopter, "it's up to us to disseminate the lessons learned and assist the industry in educating itself regarding battery safety and engaging with the stakeholders involved in the supply chain," he said.
Over the past few years, Sandvik has operated BEVs in mining for hundreds of thousands of hours with the aid of Artisan. The Artisan battery system architecture, which has been developed to adapt to both mining market demands and battery technology, has provided support for this.
“In addition, we create in-house battery systems, which gives us a lot of control over the design”, says Brian Huff, Vice President of Technology for the BHEV business unit. “Compared to an OEM that uses batteries made for automotive or industrial applications, where those bigger quantities tend to drive design decisions, we can be much more responsive to the market in terms of making modifications to the design.”
"We don't have that divergence of attention; we act in a mining-appropriate manner."
Sandvik invested in a cutting-edge battery system plant in Camarillo, California, with a 100 MWh yearly battery production capability, as a result of doing what is "good for mining." With a test ramp that has a 20% grade and a large area for mucking on the site, this same building serves as a training and customer visitor center.
Regarding the latter, Huff stated: "We will test every product that leaves the shop and undertake a lot of development work — as a result, our development cycle has sped up." Additionally, as part of its commitment to the mining industry, Sandvik invested in a battery system platform that, in terms of safety, considers the challenges of operating machines in underground mines.
Right Chem Quality Cells
Starting at the cell level, Sandvik's battery system has an inherent level of safety. To secure a steady supply of high-quality battery cells that would easily fit into its battery system architecture, Artisan teamed up with China-based CALB back in 2015. After seven years, half of which were spent pretending to be Sandvik, Huff finds no reason to alter his ways. Consistency and high-quality cells are important for battery system safety, he noted. "That is accomplished through high-volume production coupled with automation and quality production controls. "CALB, which manufactures several batteries for buses and stationary applications both in China and internationally, has completed all compliance and testing on its cells and satisfies all safety criteria." The battery cell manufacturer was also a pioneer in the development of lithium iron phosphate (LFP)-based batteries, and Huff is keen to highlight the advantages of adopting such battery chemistry in terms of safety.
Huff states, "Our approach to battery safety, which is a component of the standardised Sandvik method for safety with ISO and other standardisation bodies, is to look, first, at minimising the severity of a potential incident or removing the hazard. For us, lowering the severity of a thermal runaway entails making a chemical decision.”
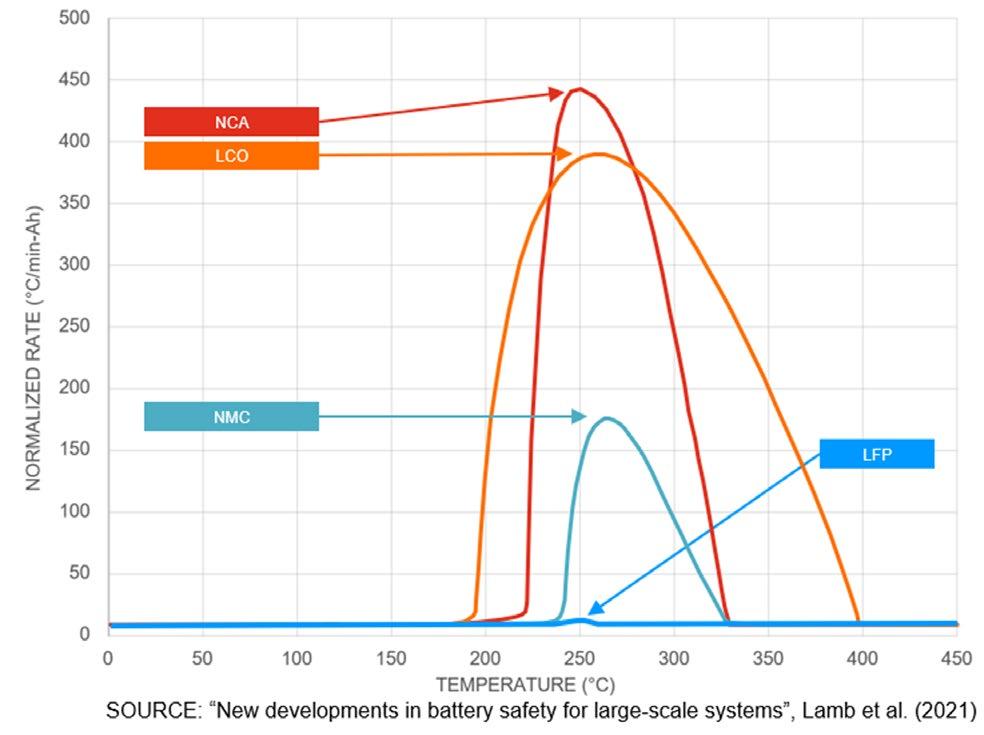
THE LEAD
When the temperature inside a battery increases to the limit that a chemical reaction starts occurring inside the battery, a chain reaction known as thermal runaway takes place. This chemical process generates heat, which raises the temperature and prompts other chemical reactions and heat production. Batteries may melt, become irreparably damaged, or, in extreme cases, ignite and start fires due to excessive heat generation at a rapid rate.
Thermal runaway preventions are frequently the first item battery companies highlight in safety briefings due to their propensity to result in such an occurrence.
It is simple to illustrate Huff's point when the main commercial battery chemistries are plotted against the heat-release-rate (HRR) on a graph (see graph below). According to Sandvik, the rate of temperature rise (HRR) measures the severity of a thermal event; the higher the HRR, the more difficult it is to contain an incident.
In light of all of this, the company claims that containment is more feasible due to the LFP's rate of temperature rise, which is over 100 times lower than that of other batteries with chemistries like nickel-manganese-cobalt (NMC), lithium-cobalt oxide (LCO), and lithium-nickel-cobalt-aluminum (NCA). LFP-based cells have released a flammable gaseous electrolyte during thermal runaway testing, but they do not self-ignite during conventional safety tests, according to Sandvik.
The safety advantages of employing LFPbased batteries have also been emphasized in tests on batteries looking at the production of toxic pollutants. Compared to far greater levels generated from NMC- and lithium-ion-manganese-oxide (LMO)-based batteries, emissions of substances such as carbon monoxide, nitrous oxides, and hydrogen fluoride were modest, according to a US CDC nail penetration test.
"In Sandvik's battery system design, a battery cell (far left) is placed into a battery module (second from left), which is then incorporated into a battery pack (second from right). This pack is then enclosed in a cage (far right)."
PASSIVE SAFETY, INTRINSIC SAFETY
In terms of safety measures, the battery chemical selection falls under the category of "severity reduction," but Sandvik's approach to battery system safety goes further than that.
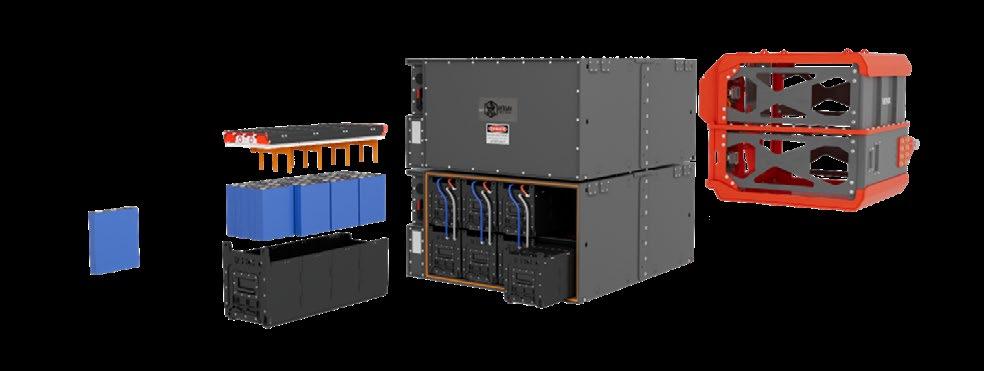
The risk of the hazard occurring is then decreased by design controls, according to Huff. This is where engineering steps in; the best design controls are frequently passive and intrinsic, implying you need not take any action in the occurrence of an incident. Starting in the cell, Sandvik's locker contains numerous such controls.
High-reliability vents on the cells in Sandvik's battery systems minimize pressure build-up in the event of thermal runaway. The firm claims that this removes the possibility of a case rupture or burst. Additionally, they include a laser-welded aluminum casing with insulation made of mylar and polycarbonate that provides mechanical safety and thermal conduction.
In contrast, a shutdown separator coating is intended to melt if the interior of the cell exceeds 110–130°C. This will stop the passage of ions, stop the current, and stop the temperature from rising further. In order to restrict dendrites and give structural support to avoid shrinkage and maintain the separation of the electrodes, a second porous ceramic separator coating that melts at 160–175 °C and bonds with a polypropylene electrode separator is needed.
Huff elaborates, saying that dendrite formation is a result of excessive current, charging too quickly, charging in cold conditions, and aging. Additionally, excessive growth has the potential to cause an electrical short, which could trigger a thermal runaway.
According to Sandvik, these cells are put into a battery module that runs at low voltage for safe servicing, has isolating foam potting to block moisture and prevent

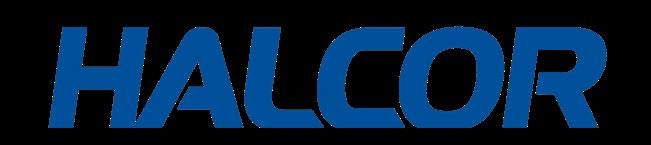
HALCOR PRODUCTS Copper tubes with or without lining or industrial insulation for applications in: • Drinking water and heating networks • Underfloor heating and cooling • Gas and medical distribution networks gases • Cooling and air conditioning systems • Solar energy applications • Various industrial applications Halcor is the copper tubes division of ElvalHalcor S.A. and together with four more companies form the copper segment of ElvalHalcor S.A. that specializes in the production, processing and marketing of copper and copper alloys products with dynamic commercial presence in the European and global markets. For more than 80 years, Halcor has been offering innovative and added-value solutions that meet contemporary client demands in fields, such as plumbing, HVAC&R, renewable energy, architecture, engineering and industrial production.
The copper segment of ElvalHalcor S.A. is composed of six subsidiaries and seven associates/joint ventures, based in Greece, Belgium, Bulgaria, Romania and Turkey, while it operates a total of five production plants in Greece, Bulgaria and Turkey.
The copper segment of ElvalHalcor S.A. develops and distributes a wide range of products, including copper and copper-alloy rolled and extruded products with Halcor being the sole producer of copper tubes in Greece. High quality in production is achieved through strict controls applied throughout the production process. With a consistent quality focus, the company implements an ISO 9001:2015 Certified Quality Management System and leverages high technologies and expert staff.
As a result of the Group’s strategic investments in research & development, Halcor is recognized as one of the leading copper producers globally, setting new standards in copper processing. The company maintains a consistent focus on quality and environmental protection and a strong commitment to the principles of sustainable development. In this context, all production facilities in the Group’s plants leverage advanced technologies to bring in the market innovative products that are energy efficient and environmentally friendly.
For more information, please visit our website www.halcor.com
THE LEAD
isolation faults, and offers thermal conduction to transfer heat from a hot cell and distribute it throughout the entire module to reduce temperature rises, and provides protection against mechanical and environmental damage.
Then, these modules are integrated into a battery pack, which has mechanical safeguards like a 6-mm steel enclosure, a non-conductive coolant to regulate temperature during charging, and gore vents and drains to prevent pressure build-up. These safeguards allow vented gases to expel air in the enclosure and fluids to drain rather than collect, all of which limit the entry of dust and contaminants.
According to the business, the redundant design of the battery pack contactors enables the circuit to be severed in the event of an over/under voltage, isolation fault, over temperature, or over current. A high-voltage interlock loop (HVIL) system might also do this. Last but not least, the addition of 600 A fuses offers defense against overcurrent and harm from exterior shorts.
The battery pack is also housed in a cage, which according to Sandvik, provides strong mechanical protection, mobility, and swappability. It also allows for easy access to the pack modules without requiring the disassembly of the cage.
Post Design Designs
We begin with the presumption that design controls, no matter how effective, should never be thought to be 100% effective, according to Huff. "For example, you cannot simply address the problem by ignoring the possibility of thermal runaway. It isn't realistic, especially in a mining context where damage, accidents, and human error can happen.
This prompts the business to discuss the active controls that are part of its battery system. Monitoring is the beginning of it all, Huff added. It might examine voltage and temperatures, including case temperature, terminal temperature, and conductor temperature. HVIL, isolation, temperature, and currents, connects the battery, and communicates the status. However, the system is not responsible for putting the controls and restrictions into place.
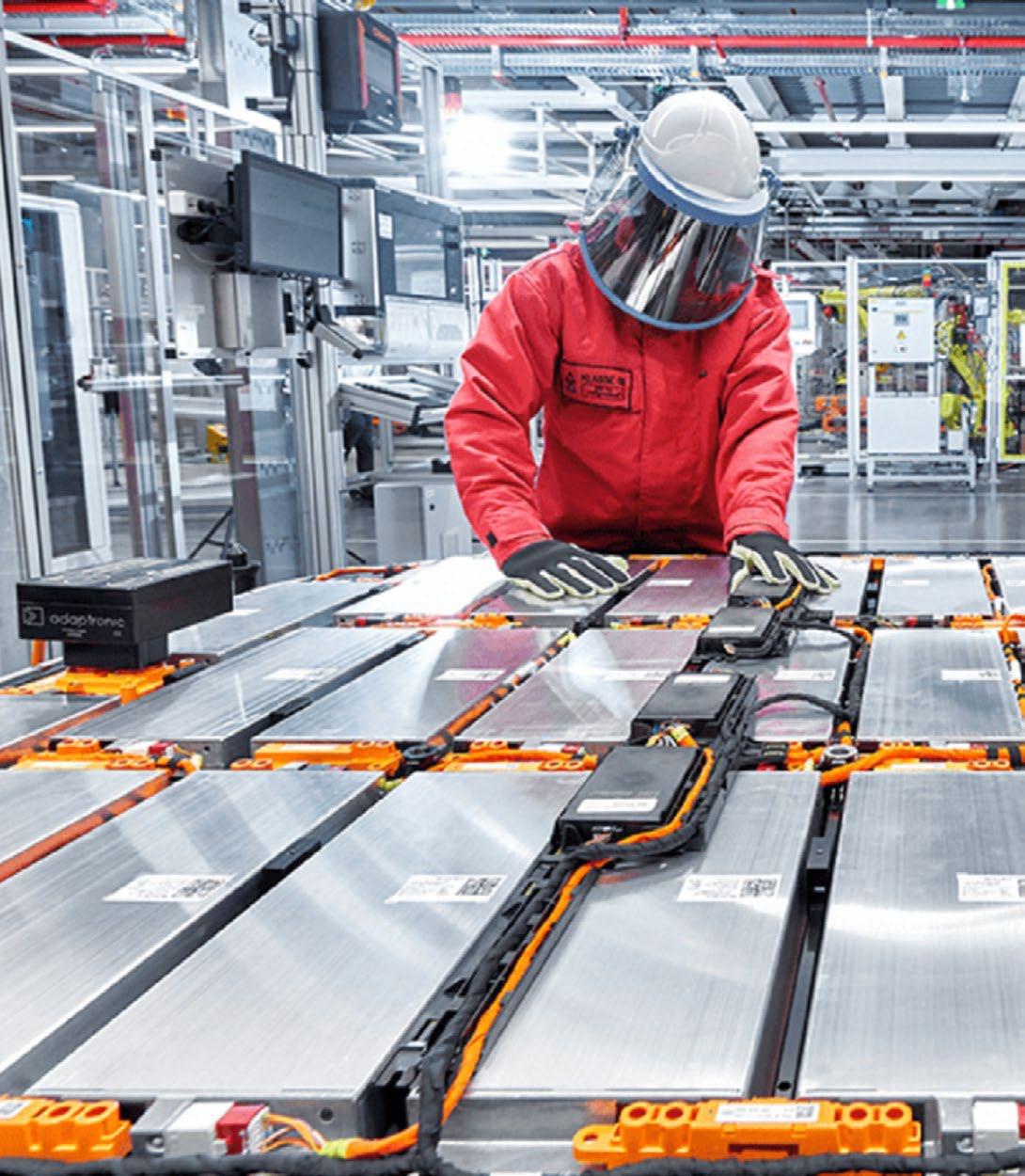
"Embedded" monitoring software on the battery and "remote health monitoring" applications are the first development priorities post-integration.
Huff. "The battery system controller communicates what the limits are, such as only 400 A in discharge owing to the heat, for example.
As a last option, the battery system controller opens its connectors and disconnects power if the MCU is unable to do so (for example, by drawing too much current).
The battery monitoring system (BMS) controls cell balancing, regulates cell voltage and temperature (including case, terminal, and conductor temperatures), and transmits information to the BSC. Akkurate, a battery analytics company that Sandvik acquired earlier in the year and its remote battery diagnostic and prognostic platforms will be integrated into the BHEV business unit, further enhancing this monitoring. Although you can often reduce external dangers, Huff stated that such monitoring can only go so far in assuring safety from within the system. In terms of electrical failure modes, he said that monitoring-based functions may help prevent overcharging and over-discharging but couldn't shield against deformation, mechanical harm, or intrusion from external objects. This is where the "suppression" component is relevant. For its fire suppression system, Sandvik uses a chemical emulsion with a potassium base that is electrically non-conductive. It works by injecting an aerosol agent into the battery pack interior, which chemically prevents combustion and halts a possible fire in its tracks.
"These suppression systems came in and did the job we prescribed for them in a couple of previous occurrences, which were minor," Huff said. They are not intended to put out a widespread battery fire; rather,
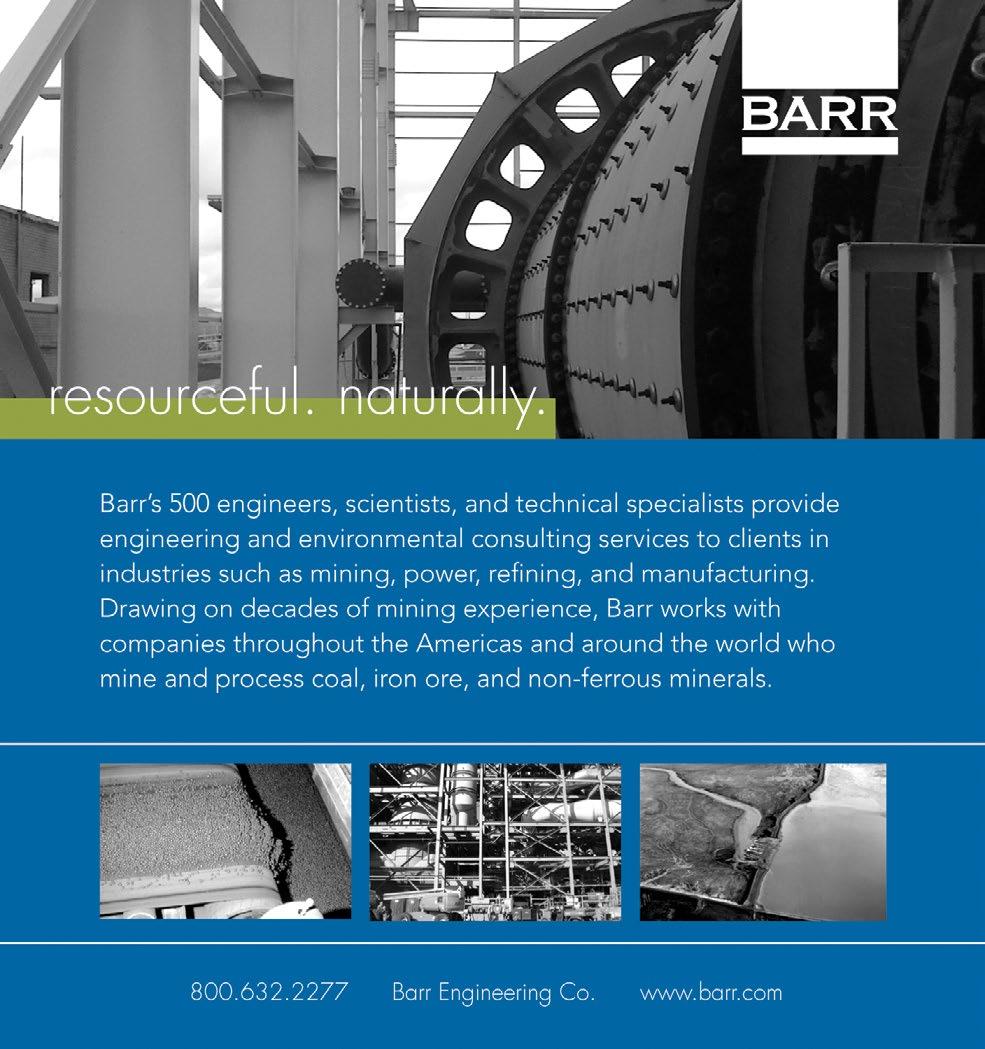
Equipping the mining industry with legal services since 1893.
∙ Mineral purchase agreements, leases and options ∙ Land assembly and mineral rights acquisition ∙ Severed mineral registration and title work ∙ Environmental permitting and compliance
° MINING & MINERALS LAW ° ›› Paul Kilgore ›› Paul Loraas
THE LEAD
(BHEV) Battery and Hybrid Electric Vehicles Business Unit of Sandvik Mining and Rock Solutions is more than ready to conduct these discussions, according to Jakob Rutqvist, the unit's VP of Strategy and Commercial.
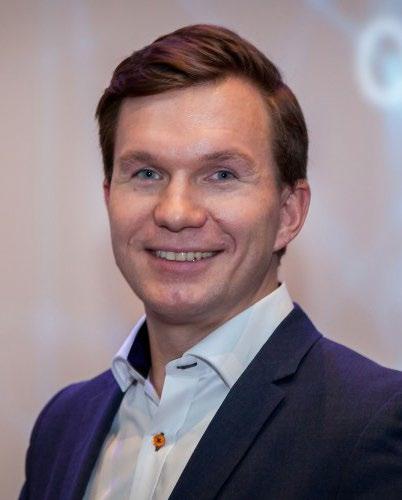
the safety barriers are the chemistry choice and the additional passive controls we have built-in.
All Stones Unturned
According to Huff, the company frequently looks beyond industry standards and regulations when designing features in, which is shown in the company's threestep safety process and its emphasis on risk reduction for its clients.
According to him, "the volume and value proposition of our products affect the needs for battery system design." "We're not attempting to cut costs here by, say, reducing enclosure thickness or changing a design element to be more cost-effective.
"Safety and dependability are far more crucial than how much it costs to make the system," On board its battery systems, there are numerous instances of this safety-design-over-cost mentality. For instance, to reduce the risk of an electrical short, the company has minimized the usage of wires and designed as much as feasible with busbars. The live conductors won't be engaged by any "casual" contact from operators or service professionals because all of these busbars are powder coated and electrically shielded.
The business has included safety measures when it comes to monitoring isolation. In the beginning, isolation monitoring for battery systems was required to warn technicians of the risk of an electrical shock in the event of an isolation problem, according to Huff.
In addition, it can serve as a precursor to a greater current short circuit when an isolation fault occurs with a resistance below a specific threshold. After conducting some investigation, Huff and his team determined that 5,000 ohms was the proper threshold for this specific risk.
"You can create a short circuit with enough power to melt some of the protective materials in the battery system and potentially accelerate this to a much higher current short circuit," the expert explained. "If you have a 5,000-ohm isolation fault in a location and have a direct connection from another point to the chassis." Differentiated action is necessary for response to this second isolation monitoring factor.
He explained that shock hazards are a warning condition in which people need to be made aware of the danger and instructed to act differently. A short circuit risk, also known as a low impedance isolation issue, requires a different approach. For us, this entails either finding the defect and shifting the modules to isolate the fault or shutting down the unit and doing so. The business can accomplish this because Artisan battery systems are made to be disassembled into individual batteries and carried separately as needed.
Over the past five years or so, "a few battery fires reported in mines, involving various sorts of equipment," Huff added. The two that I am aware of had everything to do with isolation issues and nothing to do with a BMS reaction. Therefore, a crucial factor is how you treat a battery in this situation.
Advantages of backward compatibility
Huff, a co-founder of Artisan, can contextualize the mining offer more effectively than most due to his experience electrifying heavy-duty commercial vehicles and the automotive industry, two industries that Artisan served before focusing on underground mining.
The required level of serviceability, he noted, is a crucial distinction. "Mining is a very different world; you are so far removed from a tidy business with everything you need and room to work. Mining does not have the same infrastructure that is available for vehicles.
"At mine sites, there is a lot of pressure to complete the work on-site using the tools you have with you. If you don't have the specific tool, you usually make do without it or invent one. You must have a product made
specifically for that setting, and we have done just that. The standardization and commoditization of Sandvik's battery systems occur at the cell level, leaving the company flexible to adjust and customize in response to the needs from the mining industry.
Mining clients "count in hundreds, not thousands, if you take the market at a battery system level," he said. "Our largest customers are quite huge, and they want to have a say in the development and specifications for the battery system. Our typical client is substantial, and they expect to be very close to us when it comes to product and the product development.
"We don't want to be intermediaries for the battery system design, but we're pleased to be middlemen for the battery cell." This has made it possible for the business to benefit from advancements in battery technology as they have happened over the previous several years and moving forward.
At the Macassa gold mine in Ontario, Canada, which has one of the largest battery-electric fleets in the world, Haley-Anna Blinn, who is currently a BEV Applications Specialist at the Sandvik BHEV business unit, has been on the receiving end of this.
"The battery space is changing so much all the time," she added. "Despite my short involvement of barely five years, I have witnessed significant progress. "We understand this, so it's critical that we design our systems to support future design modifications or even battery chemistry advancements in terms of energy density.
"With the older models of equipment, there was once a switch in the cell supplier, which led to cells with a different form factor. "While this adjusted the number of cells in a module according to their characteristics, the adjustment was made without any noticeable disruption when the cells were scheduled for refreshment. From the standpoint of battery system design, the module was backward compatible due to its identical form factor.
According to Blinn, the new cells also managed to boost performance by roughly 20%. The Sandvik BEV customers could be in line for comparable step-change improvements in the future given the average battery cell life of 3-5 years, battery performance continuing to advance exponentially over a similar timeframe, and the internal funding resources of the Sandvik Group.
The business can also make more subtle adjustments to its battery systems based on the current functioning.
Technicians may modify the system at the factory to the conditions they will probably encounter underground by using sophisticated modeling software and a databank that dates back to the beginning of Artisan's BEV voyage. This goes beyond just restricting the speed to safeguard the battery system and the drivers. “We may set these settings at the manufacture since, depending on the duty cycle, some mines may be better suited to a slower charge than others, according to Blinn. According to the operational conditions underground, some mines might impose a temperature limit that exceeds the preset limits we program. To ensure that the system operates differently during operation, we can make those changes.”
Since the obvious teething issues with the introduction of BEVs at underground mines have been resolved over the past decade or so, Sandvik is entering a consolidation period where minor adjustments to the system design will be made rather than complete overhauls. The company's mining-focused, safety-conscious battery system design philosophy continues to set it apart at a time when mining companies demand improved performance and uptime from these machines to meet their own electrification and productivity goals.
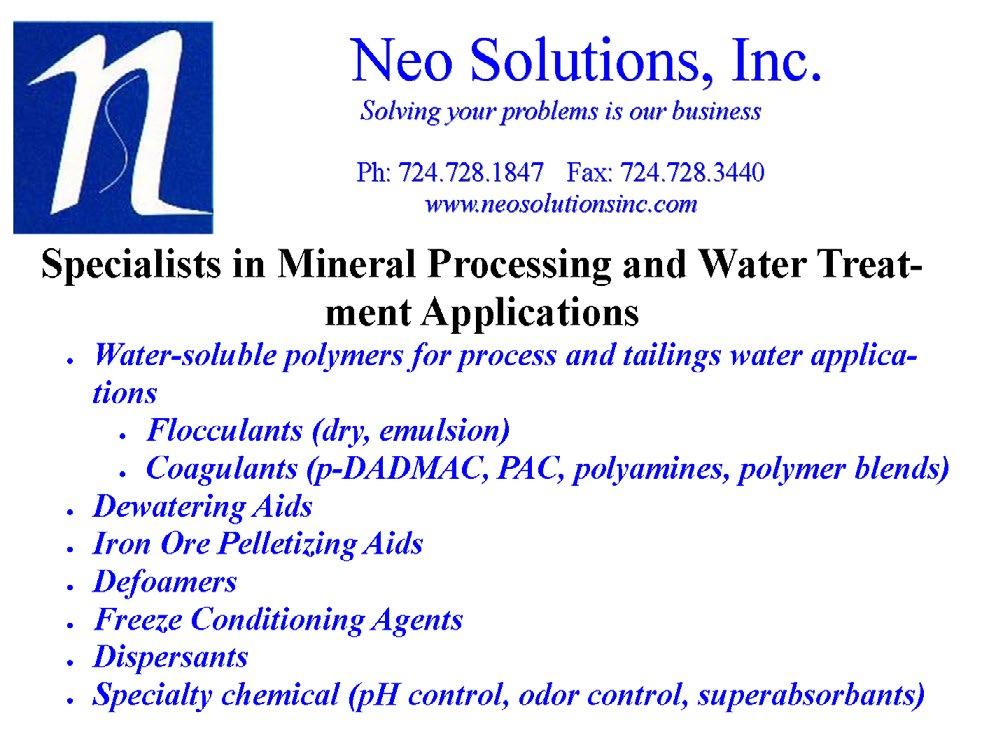