
7 minute read
Climate-Conscious Building
Creating a Net-Zero Home with Low Embodied Energy
The view of 16 North Belgium Lane from the deck side.
DON NICHOLSON PHOTOS
BY DON NICHOLSON B ecky and Noell Tin split their time between Asheville and Charlotte with work projects in both cities, and 16 North Belgium Lane in West Asheville was planned as their second home.
After struggling to find a home within the existing Asheville stock that had the size and configuration they needed, they saw available land in the net-zero subdivision we are developing at Green Path Commons and were intrigued by our strong personal commitment to climate action.
The Tins had been sympathetic to actions that curb climate change, but had not studied the topic in depth. Central to their decision to have us design a net-zero home for them were the climate concerns expressed by their children.
They approached net-zero building as a grand adventure; their enthusiasm matched ours. They learned the nuances of the home’s envelope, thermal bridging, heat pumps, and the importance of a home’s basic energy efficiency relative to that of rooftop solar.
We worked with them to design a small 850-square-foot house that flows seamlessly to the deck, yard, and adjoining community garden and pavilion. Their experience illustrates how important it is for builders to introduce their clients to the merits of energy-efficient homes and enlist them to spread the word.
Our longstanding approach to energy efficiency — LED lights, ENERGY STAR®-certified appliances, mini splits with high SEER (seasonal energy efficiency ratio of 33) and HSPF (heat seasonal performance factor of 14), heat pump water heater, heat pump dryer, R-30 walls and R-65 ceiling — gave the project a Home Energy Rating System (HERS) Score without solar of 28.
The solar photovoltaic (PV) system on the roof brings the HERS down to 1. The elements work together; the thermally tight envelope allowed us to use just two small single-head mini splits. This is possible because heat has time to diffuse from room to room before slowly dissipating through the walls and ceiling. A small PV array of 3.55kW is needed to power the home.
We decided to support the house on helical piles instead of concrete footers. Helical piles are stout galvanized steel pipes with a twist of steel plate at the end (15-inch diameter). The pile is like a giant twist drill bit that can be screwed into the ground by a track hoe with a torque drive. They are often used for poor soils, such as fill dirt. Our soil is great soil, so why use helical piles? Concrete foundations contribute significantly to greenhouse gas; steel is less offensive. The end of life for a helical pile is to be unscrewed and reused or recycled.
Helical piles affect the work site in a positive way. Even before finalizing the house plan, we graded then seeded the sloping lot to provide a building area. The process was clean, automatic and systematic. We had a nice area with U-brackets sticking up every eight feet, ready for girders, and no piles of dirt.
The 700-square-foot deck looks towards the community garden. Our target was to integrate the home with this setting. We
Project Team
Builder — Nicholson and Sun Helical Piles — Goliath Tech WNC Engineering — Engineering Support Services Solar Contractor — C.M. Wilson Inc. Insulation — Pisgah Insulation HVAC Contractor — General
Heating & Air Conditioning HVAC Equipment — R. E. Michel Electrical — Crown Electric Heat Pump Water Heater —
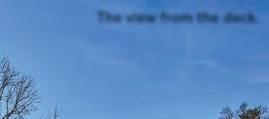
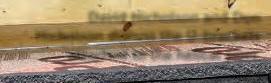
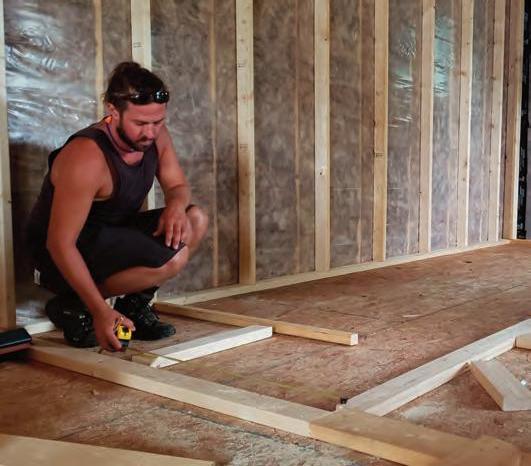
Watch a video tour of of this home at greenbuilt.org.
kept the deck low; no railing required. A low deck results in a low but critical crawl space. The ground in the insulated crawl space gives a source of heat for the heat pump water heater (HPWH). A HPWH has a carbon footprint that is a quarter that of either a gas or a typical electric water heater.
To support a low-pitch roof, we stand sheathed 2x4, 24-inch o.c. perimeter walls and span them with plywood I-beams. To accelerate this stage, we use 24-inch-by24-inch windows that require neither jack studs nor headers. Every eliminated stud improves thermal resistance. It’s a waterproof empty box; a perfect arrangement for checking the whole envelope and making it into an airtight volume.
The walls are R-15. The stud bays are free of any obstacles and insulating is very fast. We cover the insulated wall with 6-mil poly caulked at top and bottom.
Readers may be alarmed at the mention of a plastic vapor barrier because of condensation problems that plagued some homes. This is totally different; the vapor barrier is sandwiched between two layers of R-15 where the temperature is always moderate, and not cold enough to result in condensation.
We built a second R-15 interior perimeter wall. The underside of the roof and the band are sprayed, 2.5 inches of closed cell foam, and R-49 fiberglass batts go in. The spray foam seals the top of the poly. Sealing penetrations in the subfloor makes the envelope almost free of infiltration except at doors and windows. The home has six doors; to maintain low infiltration, all windows are fixed glass.
The home has an air change per hour, ACH50, of 1. Considering that the house is long and small, this is an excellent value. It is much easier to get a low ACH50 on a large blockish home because it has much more air volume, yet it doesn’t have much more in the way of exterior surface, doors, and windows.
The house is topped with 3.55kW of bifacial PV. Most PV has photo active layers on one face and the other is opaque; bifacial PV has active layers on front and back. We were eager to gain some experience with bifacial even though its application on this home, flush mounted on the roof, will generate only a small additional amount.
Adopting heavy insulation allows us to take advantage of single-head mini splits. We use only two mini splits to heat five rooms; because of the performance of the thermal envelope, the heat has plenty of time to diffuse from room to room before it slowly diffuses to the outside.
If we can source them, we will switch to R-13 cellulose batts. Cellulose is superior to fiberglass; it has a negative carbon footprint. Unfortunately, batts are not available locally; they are available by the truckload from Michigan.
The Green Built Homes rating system does not assign points for low embodied energy, but does offer credit for calculating and offsetting it. Embodied energy relates to the greenhouse gases generated in making the stuff a home is composed of; for example, concrete, wood, appliances, and solar panels. It is very hard to evaluate embodied energy. It is this author’s policy position that there should be a federal carbon price, which would give a market signal informing builders about the carbon footprint of materials. (Learn more at energyinnovationact.org.)
Small homes use less energy to operate and take less energy to build, and their materials have lower embodied energy. Is this reflected by HERS? No! A big home with a low HERS Score can use more energy than a small home with a high HERS Score. Net zero, as a designation, is an equalizer between big and small homes, and this project achieved Green Built Homes’ Platinum Net Zero level of certification.
Climate alarms are sounding louder and louder. It is imperative to reduce the size of our homes, reduce embodied energy, and promote net zero.
Don Nicholson is retired from
Oak Ridge National Laboratory, where he was a theoretical physicist for thirty years. He continues to work in that field as a research professor in the Department of Physics and
Astronomy at the University of North Carolina Asheville. In 2015, he and his son, Donald, formed Nicholson and Sun, a residential building company dedicated to climate solutions. Connect with
Don at nicholsonandsun.com.
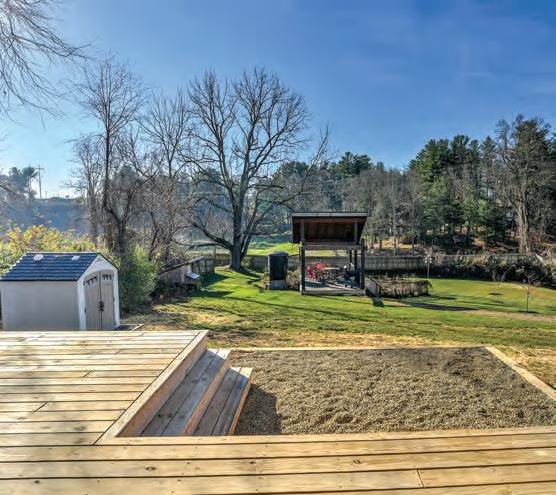
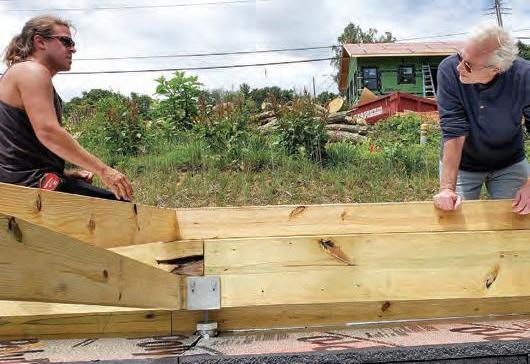
David Nicholson and Don Nicholson discuss the U-brackets attached to the helical piles.
At this point, the house is a waterproof, airtight box. Note the staggered stud wall with sandwiched air barrier.