
4 minute read
Blueprints for Going Green
Green Built Homes Checklist Clarifies Steps to Better Building
BY KAT MCREYNOLDS A s I sat down to plan my first duplex build as a general contractor, the vague aspiration of “building green in Asheville” became a dizzying stream of questions.
In what neighborhood should I build? What site layout would zoning allow? What are the most durable materials for siding, countertops, flooring? Which paint should I use? What color? What sheen? How many gallons? Have I eaten yet this week?
Every home is the culmination of countless decisions, and building sustainably can add a layer of complexity. While I initially wondered whether the Green Built Homes certification would add hurdles, I eventually found the opposite to be true. If code-built homes are a D-minus, the Green Built Homes checklist provides a detailed study guide for earning an A.
The checklist
Managed by the Green Built Alliance, this voluntary, state-wide program gives builders a framework to track eco-friendly upgrades to both the construction process and the home itself. Participants must meet 16 prerequisites like air sealing to 5 ACH 50 and testing for radon. Beyond that, all checklist items are optional and assigned a point value. Within eight categories like site or building envelope, contractors must earn a minimum number of points, and a cumulative total determines how each home ranks — from simply certified to the highest platinum level.
For newcomers to green building, the level of specificity within the checklist is invaluable. A numerical good-better-best figure is provided for several metrics, like U-values, which measure a window’s ability to insulate. An average U-value of 0.32 or less earns one point, while lower (better) Uvalues of 0.29 and 0.25 earn two and three points respectively. Guideposts like these give instant meaning to specification sheets, allowing builders to more readily compare products.
Perhaps the greatest program benefit, though, is the involvement of a third-party energy rater. Hired by the builder, this person conducts inspections at key times and serves as a consultant on the home’s green potential. In my case, speaking to energy raters during blueprint drafting led to an important upgrade from 2x4 to 2x6 exterior walls. I also communicated with the rater during purchasing to ensure that fixtures and finishes were aligned with our goals.
The cost
Cost, of course, is a factor for anyone considering the Green Built Homes program, especially as our community faces serious affordability issues.
Unfortunately, the answer to exactly how much extra certification costs is an obnoxious, “it depends.” To start, it depends on what the homeowner would have done in the absence of the program.
Many product lines are already moving toward sustainability by default, like increasingly prevalent
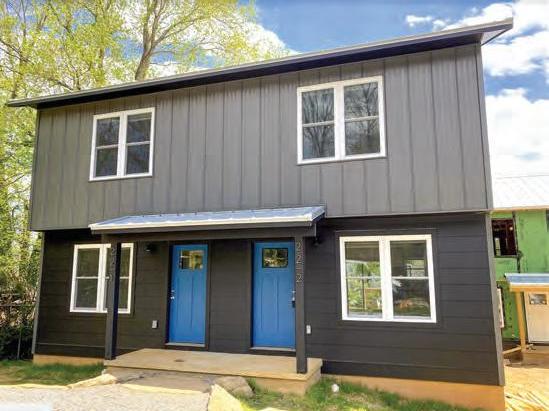
The author found the Green Built Homes certification checklist provided a detailed study guide for taking a high-quality and low-footprint approach to
her first project. KAT MCREYNOLDS PHOTO
— Eric Hurley, instructor, Asheville-Buncombe Technical Community College
ENERGY STAR®-certified appliances, light fixtures with LED bulbs, and faucets with modest flow rates. In those cases, little or no marginal cost is incurred for a certified home.
Other costs are subject to fluctuating market conditions. During the framing of our duplex in October 2020, for instance, a 2x6 stud was priced at $5.66, while a 2x4 stud was $6.78. By using 2x6 walls, I actually saved on framing materials but spent a few hundred dollars more on insulating thicker walls. Lumber prices have changed drastically since then and will continue to torment estimators for the foreseeable future.
Fortunately, in my case, rebates from Duke Energy and the City of Asheville are expected to at least cover fees for program enrollment and energy-rater services.
The next steps
In some ways, the Green Built Homes program highlights our community’s thriving green-building scene. We have a healthy pool of suppliers and product lines; local subcontractors that are wellversed in their contributions toward sustainability; and free or cheap options for recycling certain building byproducts.
Still, we can and should improve. I had to cringe when I sent a large pile of drywall to the landfill after searching fruitlessly for a regional recycling center. I also discovered the wafer-thin dividing line between sustainability and hoarding, as the crawlspace at my personal residence became a marshalling yard for styrofoam and wood scraps. Asheville GreenWorks accepts styrofoam at its periodic Hard 2 Recycle events, which are wonderful for the community but not a scalable solution for builders.
The inroads to sustainability continue to multiply in the field of construction, and the Green Built Homes checklist serves the important purpose of helping builders to plot their own path.
Here’s hoping that more contractors across the state will decide to lean on this resource and to keep building better. Kat McReynolds is owner of Green Room Builders, which specializes in new construction of compact, green built projects, including small multi-family rental homes. We select materials and finishes for durability, sustainability, low maintenance and a minimalist aesthetic.
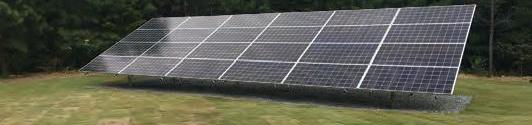
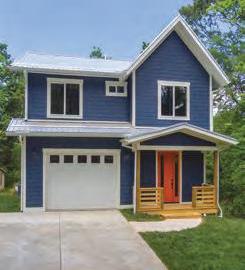

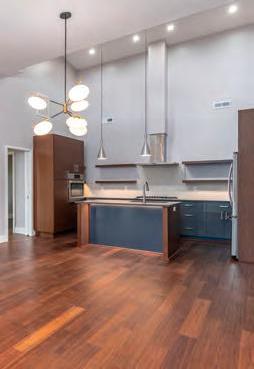
WWW.SUREFOOTBUILDERS.COM
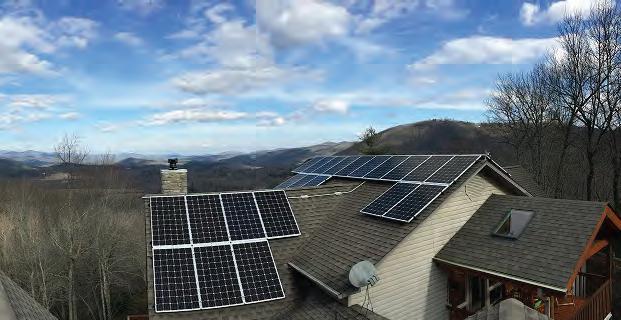
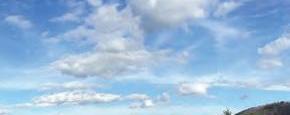
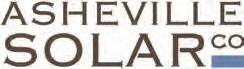
We are a family-owned residential and light commercial solar installation company focusing on sustainable idealism, a personal customer experience, and an unwavering commitment to quality workmanship.
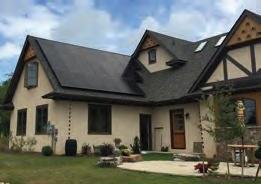