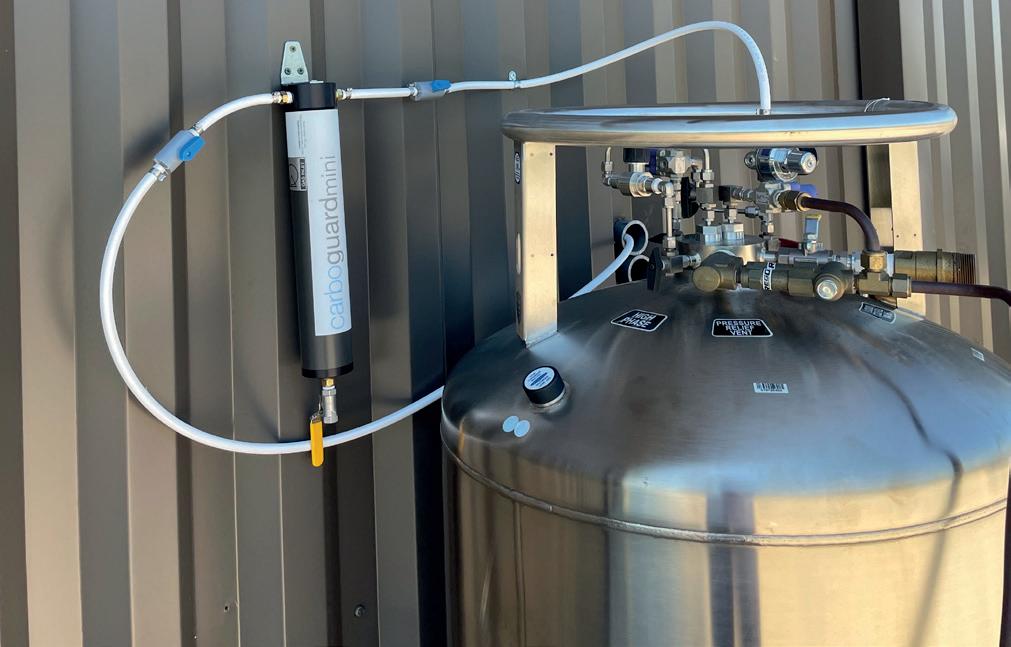
4 minute read
Risks to quality and food safety from CO2 shortages
Shortages of carbon dioxide (CO2) recently made headlines in Europe, and sometimes quality can be overlooked in the trade-off when the availability of supply is lacking. When this happens, it creates risks in the supply chain and shows the need for greater awareness of quality and food safety when disruptions occur.
Background
In Europe, CO2 used by the food and beverage industry is produced as a by-product from only three traditional sources. The primary products made by these sources are ammonium nitrate production (nitrogen fertilizer), ethanol production (industrial fermentation) and hydrogen production (steam methane reforming). All sources face frequent economic and seasonal challenges for production operations to remain viable. This includes increased energy costs, raw material shortages and seasonal demand for the primary products (e.g., fertilizer).
This requires careful planning and cooperation between the parties responsible for CO2 supplied to the food and beverage Industry, from the company operating the raw gas source of by-product CO2 and from the suppliers of the CO2 to the food and beverage industry. The bulk industrial gas producer who buys, processes and distributes the CO2 is also responsible for the quality, supply contracts and the supply chain of the food and beverage to end users.
CO2 shortages
Disruption to the CO2 supply chain is caused when the producer of the raw gas by-product and the industrial bulk gas company do not foresee an extreme event, such as an unplanned plant stoppage, issue with a raw material, energy price hikes, military unrest or power failure.
Summer of 2021 CO2 shortage
The recent disruption in the United Kingdom was well publicized, and it’s an event that could easily have been predicted. More than half of the U.K.’s bulk CO2 comes from two fertilizer plants when one company (the United Statesbased CF Industries) shut down a plant in the summer of 2021. A perfect storm occurred when several of the largest sources in mainland Europe were forced to shut down effectively cutting off the supplementary supply. A temporary arrangement was put in place to restart one of the CF Industries plants after a deal was reached in early October between the U.K. government and CF Industries, but this is by no means a permanent solution to the problem. Since this deal was struck CFF has announced the permanent closure of its plant in Ince Cheshire and the mothballing of its largest plants in Bellingham, Teeside, it is not expected that this plant will re-start its CO2 business as it has been earmarked for Carbon Capture and sequestration. How the combined output of over 1000 tons per day of beverage grade CO2 is to be replaced is yet to be determined.
Source-specific impurities
When CO2 is produced, it contains chemical impurities specific to that source, e.g., ethanol fermentation contains high amounts of ethanol in the raw CO2. A lot of care is taken by the bulk industrial gas producer to monitor the condition of the incoming raw gas as it enters their purification process. This process reduces the number of impurities to levels well below the requirements of the food and beverage industry to make the CO2 safe for us to consume. Because CO2 is the only industrial gas we consume, the quality is tightly controlled and certified.
The quality of the final product is controlled by sophisticated analytical equipment that controls quality in discreet batches and sequentially numbers the batch for traceability. The delivery tankers are also analysed to provide a certificate of analysis and conformity to the standard in which it has been produced and sold by, e.g., EIGA, ISBT and/or any customer specific requirements.
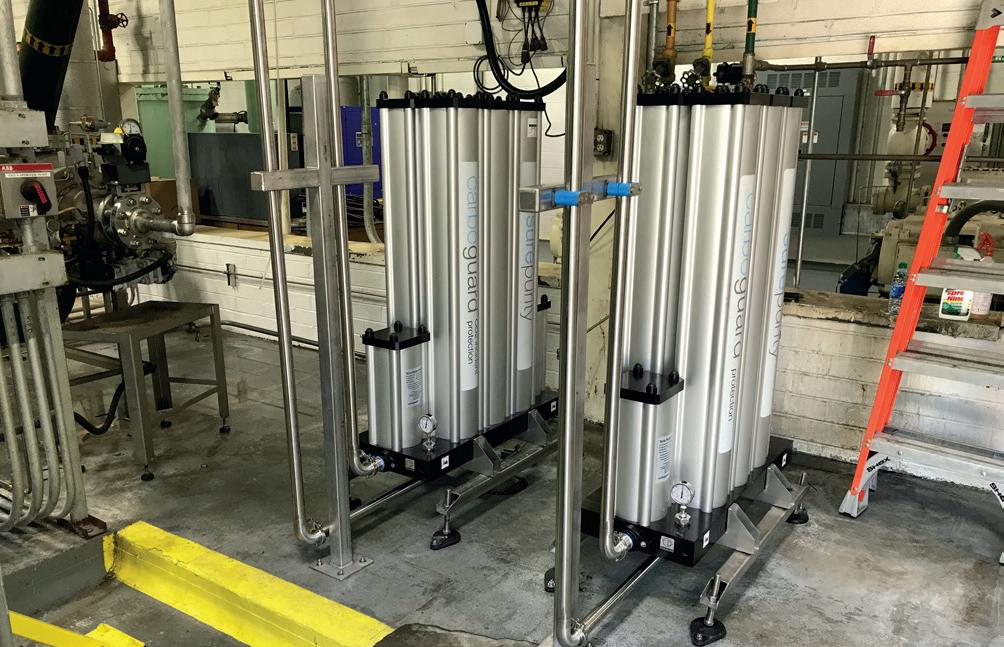
New sources and their challenges
Environmental initiatives, sustainability goals and consumer pressure have led to the development of several new sources of CO2 being developed. The most publicized and attractive new source developing is from the anaerobic digestion (AD) of highly convertible biomass. Although the primary output from one of these plants is methane, the upgrading process creates a valuable co-product stream of biogenic carbon dioxide.
Some challenges exist with this source scaleup. There’s limited output because it would take more than 100 average-size AD plants to replace one CF Fertilizer plant. Since a small AD plant with CO2 production can cost £10M-£15M , investment in capital equipment can also be an issue. There are also some negative perceptions about where this CO2 comes from (if people only consider the AD feedstock and not the actual methane upgrading process). There’s also a lack of historical data on CO2 quality. But, ultimately, the economics are now swinging in favour of AD.
Distribution and handling
Distribution of liquified bulk gases can be complex at the best of times, but in a stressed or disrupted supply chain getting CO2 from point A to point B becomes even more challenging, as greater distances have to be covered and multiple forms of transport become involved such as carrier ships, rail and road tankers. When the number of hands of custody increase, then the opportunities for contamination of perfectly good product also increase.
Sub-distribution hospitality F&B service end users
The hospitality food and beverage service, fast food outlets, bars, restaurants, hotels etc are served by a network of independent distributors, that buy the liquified gas in bulk from the Gas Producer and then deliver a range of gases in refillable cylinders (or store based micro-bulk dewar tanks) to the end user. Contamination of the cylinders can occur when beverages back flow into the empty cylinder, or ingress from the atmosphere, if a cylinder minimum pressure valve is not used, corrosion and deterioration will occur. Fillable microtanks are permanently installed on-site for many years without any cleaning or build-up of contamination.

The certificate of analysis of the CO2 can be traced from the bulk industrial gas supplier to the batch of final product at the source. However, very little or no information on CO2 quality is traceable in cylinders or micro-bulk permanent tanks intended for beverage use. A lack of understanding on how to achieve full end-to-end traceability is the most challenging issue to address.
Managing the Risk
The risks to your business depend on how your CO2 was sourced, produced, monitored, distributed and how many times the product was transferred, as well as the cleanliness of the processing and the management of the contamination risks.
Point of Use multiple barrier polishing filters are an effective, low cost solutions that remove both trace chemical impurities in the CO2 and any physical contaminants from the supply chain. Products such as the Carboguard from Sure Purity come in a variety of sizes suitable for a soft drink bottling plant or brewery’s needs all the way down to a miniaturised version of the technology suitable for a bar, tap room or drive-thru fast-food restaurant.
For more information go to www.surepurity.com
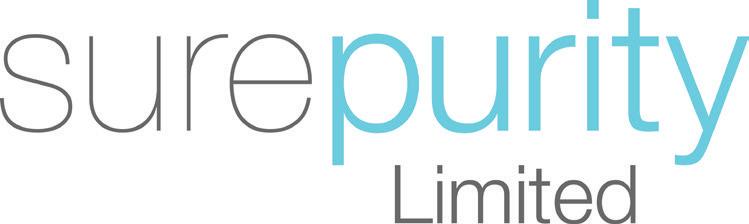