
14 minute read
HAD y HAC: incidencia en la reducción de indicadores de insustentabilidad en obras de arquitectura
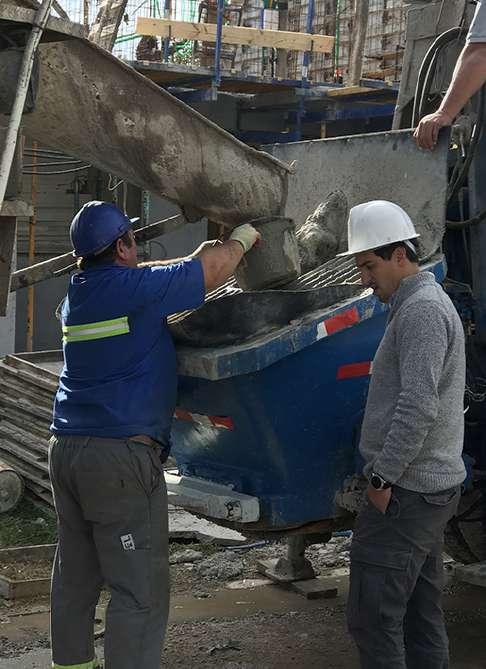
Figuras 39 y 40: Extracción de muestra de HAC para realizar los ensayos a pie de obra.
Advertisement
Figuras 41 y 42: Ensayo de cono de flujo y T50.
Hormigón autocompactante - Madelón Iglesias
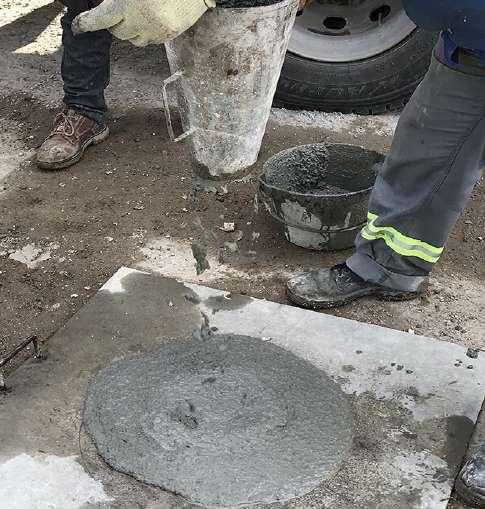
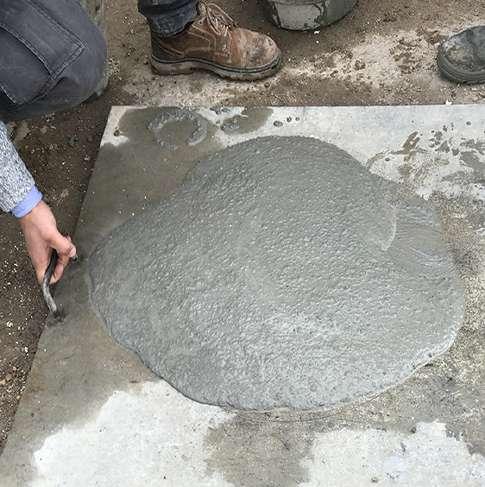
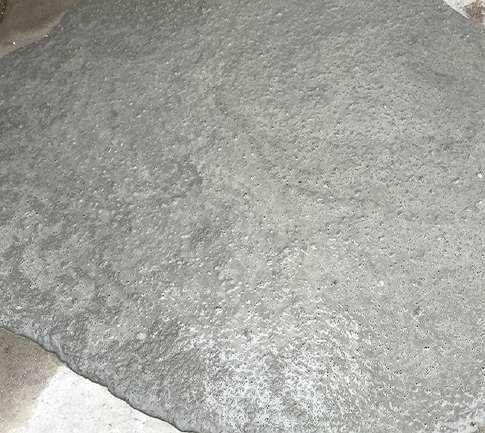
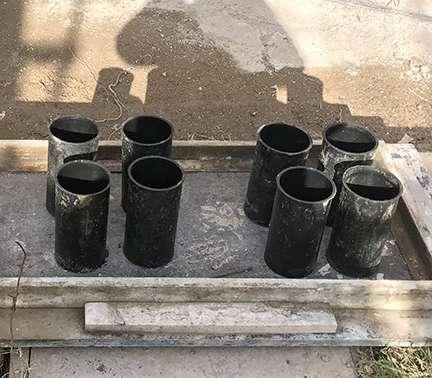
Figura 43: Ensayo de índice de inspección visual VSI 0 Figura 44:Probetas listas para llenado
Figura 45 y 46: Probetas del HAC etiquetadas, para enviar al Laboratorio posterior al fraguado

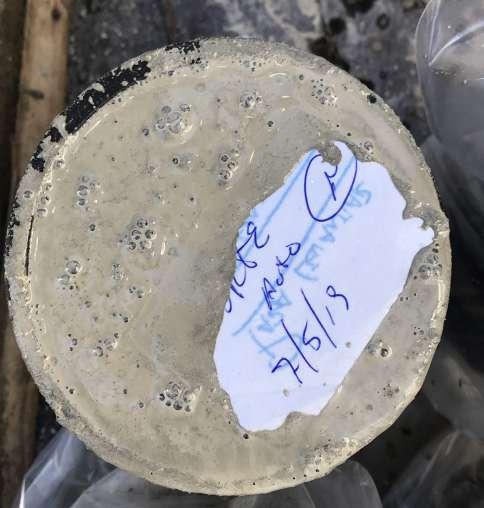
se vacíe completamente y se controla el tiempo que demora en alcanzar el diámetro de 50 cms. Este primer ensayo de denomina T50, y su límite máximo es que llegue en menos de 8 segundos.
Una vez alcanzado este diámetro, se realiza el ensayo de Inspección visual tolerándose los índices 0 y 1, rechazando el 2 y 3. En el caso que el día de llenado, estuviese presente uno de los laboratoristas de Concrexur, se permite que realice correcciones sobre el VSI 2.
En este ensayo se verifica la exudación y la existencia o no de segregación en el borde, para ello se verifica que no haya bordes sin árido grueso.
Se mide en dos diámetros perpendiculares, el diámetro final, se promedia y se acepta un diámetro entre los 65 y los 75 cm.
El día de visita a obra, día de llenado de muros de planta baja de una de las viviendas, se obtuvo un explayamiento de 70 cm y T50 de 6 segundos. El VSI fue de índice 0.
La dirección de obra, posee reglas generales sobre la temperatura en tiempos fríos en los días de llenado.
Se suspende el hormigonado siempre que:
• Que dentro de las 48 horas siguientes, pueda descender la temperatura media del ambiente por debajo de los 0ºC. A estos efectos, el hecho de que la temperatura ambiente a las 9 de la mañana, hora solar, sea menor de 4ºC, se puede tomar como suficiente para prever que dentro del plazo indicado se alcanzará el límite de temperatura establecido anteriormente. • Que la temperatura de los moldes o encofrados sea menor a 3ºC. • También tienen precauciones para los días
Figura 47y48: Transición de puntales y losa (flp), al otro día del llenado, posterior al desencofrado.
Hormigón autocompactante - Madelón Iglesias
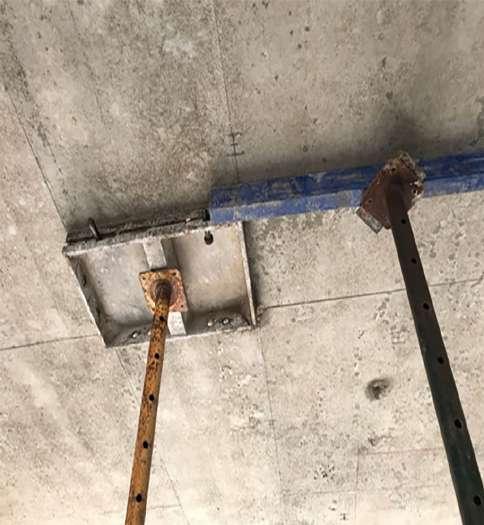
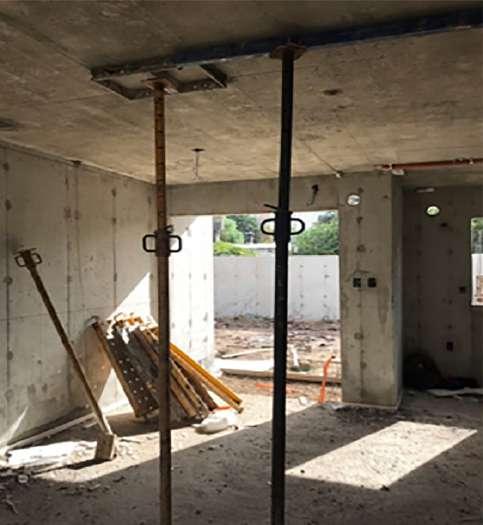
calurosos, temperatura del aire mayor a 30ºC: • El tiempo de mezclado no puede exceder el mínimo especificado y el tiempo para el mezclado y colocación serán los mínimos posibles. Si las temperaturas son críticas, las operaciones de colocación del hormigón se realizarán de tarde. • Las operaciones de colocación, son interrumpidas cuando la temperatura, velocidad del viento y humedad relativa ambiente impidan realizar las operaciones de colocación y compactación en forma adecuada, o perjudiquen la calidad del hormigón de la estructura. • No se permite hormigonar con temperaturas mayores a 40ºC o si se hormigona con temperaturas mayores a 35ºC, se deberá prever un curado mediante riego de las superficies expuestas.
En obra se tienen dos juegos de moldes, correspondientes a planta baja y otro a planta alta, todas las viviendas se realizan con este juego, por lo que se llena por sector, apareciendo juntas de hormigonado. Considerando esto, las juntas las ubican en las partes menos comprometidas de la estructura y orientadas de manera que los esfuerzos previstos para la pieza en esa sección, se desarrollen normalmente a la junta y de manera que tiendan a su unión con el nuevo material a colocarse. Para asegurar la mejor adherencia entre las partes de hormigón en contacto, se trata de que queden ásperas y bien limpias al recibir el hormigón fresco del siguiente llenado.
El sistema Forsa de encofrados, posee piezas de unión entre los muros y las losas, así como piezas de transición entre el puntal y la losa. Por lo que tenemos una etapa de desencofrado de las formaletas de losas (FL) y otra de desapuntalado de las formaletas puntales (FLP).
Se retiran de las formaletas de losa FL al otro día del llenado, dejando en su lugar las formaletas
Figuras 49 y 50: Acopio de encofrado metálico en obra

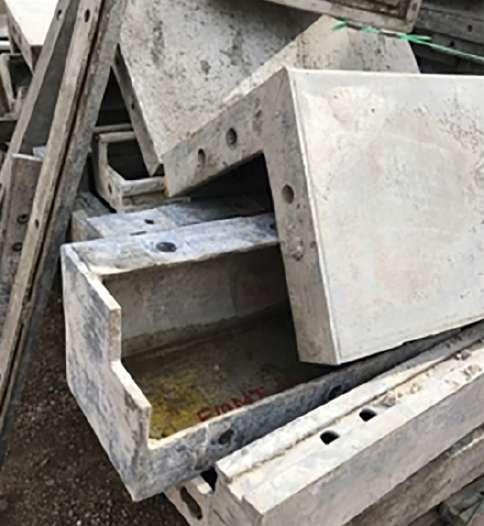
de losa puntal (FLP) hasta obtener la resistencia característica mínima necesaria para poder desapuntalar, que se consigue a los 7 días.
Para el desencofrado de las FL de las losas de planta alta, para esta tipología, es necesario contar con una resistencia mínima de 12 kg/cm2 para el desencofrado de las formaletas de aluminio.
En las losas de planta baja, para las losas que soportan las cargas de los muros de planta alta, se considera como mínimo una resistencia de 48 kg/ m2, para una separación máxima entre apoyos de FLP de 1,5 m, antes de realizar el llenado de los muros de planta alta.
No es menor en este sistema, el espacio que ocupan estos encofrados, y el tiempo de limpieza y etiquetado de los moldes. Se reutilizan los moldes, cada molde tiene un plano, y todas las viviendas usan los mismos moldes. Se realiza como una producción en serie. El propio sistema consta con pasarelas de apoyo para la construcción de la planta alta, las mismas se fijan en los pases y con las corbatas del propio muro.
Se evita el uso de la estructura durante los primeros días, se toman precauciones especiales para no arrojar cargas o acumular sobre ellos materiales de cualquier índole.
Los parrilleros se llenan con el mismo sistema, la malla y los separadores, con moldes más chiquitos, con las corbatas para posicionar los moldes. El sistema tiene un alineador, para corregir la posición de los mismos.
La utilización de Hormigón Autocompactante, les permite cumplir con los plazos estipulados para la obra. Su colocación en los encofrados es muy rápida, con menor cantidad de mano de obra, lo que también en este punto les permite ahorrar una cantidad importante.
Les permite desencofrar al otro día y tener un acabado de la superficie perfecto. En algunas viviendas, esto no se logro debido a imperfecciones de los moldes, y como es de nuestro conocimiento el HAC rellena y copia toda la superficie del encofrado.
La obra comenzó en Diciembre 2018, se estima que finalice en Diciembre 2019. Son 30 apartamentos, 28 duplex, y 2 casas simples. 58 llenados de HAC, posteriores a la cimentación que se realizó en hormigón convencional. Se llenan muros y losas en el mismo llenado.
Se encofran y se llenan dos casas por semana, 70 m2 por dúplex, cada superficie de llenado es de 35 m2. Cuatro llenados por semana, con un total de 48 m3 (0,3 m3 H / m2).
Se conformaron dos equipos de trabajo, uno para trabajar con los moldes sobre planta baja y otro sobre planta alta, de esta forma se formaban a los distintos equipos en los sectores, de forma que cada cuadrilla repitiera su trabajo, durante toda la obra, y así eliminar márgenes de error. Un equipo de 7 personas para planta baja y 7 personas para planta alta.
El HAC acompaña la lógica constructiva del sistema Forsa. Estas viviendas tienen un proceso constructivo muy concreto, sumamente específico, lo que le permite tener tiempos de obra menores a los realizados en construcción tradicional. A modo de resumen de lo ya expuesto, luego de realizarse la cimentación, la platea en este caso, se erige la malla electrosoldada, a la que ya se fijan los negativos en poliestireno expandido para abastecimiento y pases de ductos de ventilación. Se fijan también los caños corrugados para el enhebrado posterior de la eléctrica. Se coloca el encofrado y se llena. Una vez desencofrado, se pasa a la colocación de cañería sanitaria y enseguida de la prueba hidráulica, se tapan con arena y portland, se enhebra la eléctrica (al otro día del llenado) y se realizan terminaciones. No hay revoques, al interior es enduído y al exterior como ya se ha citado, revoque termoaislante y pintura. Las carpetas interiores se realizan con un hormigón autonivelante. Se colocan puertas de madera, aberturas de aluminio y pisos de porcelanato, y con eso finaliza el proceso de construcción de estas viviendas.
Hormigón autocompactante - Madelón Iglesias
Según los datos proporcionados por el Arq. Jefe de Obra, el costo m2 con forsa y el hormigón autocompactante, para este proyecto está en el entorno de los USD 1000/m2, mientras que si lo hicieran en tradicional sería, USD 1600/m2. El costo del juego de encofrado de 30 m2 con el cual se están haciendo las viviendas es de USD300.000.
7. Agradecimientos
En primer lugar agradecer al Sr Daniel Ognibene, encargado de programación y logística de empresa Concrexur, quien me puso en contacto con el Sr Felipe Parry y el Ingeniero Martin Ceroni, ambos pertenecientes a la misma empresa, quienes me concedieron la entrevista de aproximación al Hormigón Autocompactante.
Al Ingeniero Martín Ceroni, quien me otorgó una visita guiada por la planta de producción del HAC, donde pude presenciar las distintas etapas del proceso, así como también el Laboratorio de control e investigación que posee la misma empresa. Quien también me permitió el acercamiento a la obra Aires del Norte, siendo Concrexur la empresa de suministro del HAC.
Al Arq. Joaquín Aguerre, jefe de obra en Empresa Norte, responsable de la obra Aires del Norte, quien me permitió la visita a obra el día de llenado de HAC, compartiendo su experiencia, y quien me proporcionó planos y memorias de la obra.
8. Referencias bibliográficas
[1]Sergio García-Gasco Lominchar, Vicente Mas Llorens, Eduardo Sáez-Bravo Picón. 2009. Piel de hormigón. Aspectos técnicos y estéticos del hormigón autocompactante.
[2]Dr. Ingeniero Manuel Burón Maestro, Dr. Ingeniero Jaime Fernández Gómez, Ingeniero Luis Garrido Romero.2006. “Hormigón autocompactante. Criterios para su utilización” IECA Nº 887 (Abril).
[3]Ester B. Bermejo Nuñez. 2009. “Dosificación, propiedades y durabilidad en Hormigón Autocompactante para edificación.” Ph.D. tesis, Universidad Politécnica de Madrid.
[4] E. B. Bermejo Núñez, A. Moragues Terrades, J. C. Gálvez Ruiz y M. Fernández Cánovas. 2008. “Permeabilidad y porosidad en hormigones autocompactantes” Anales de Mecánica de la Fractura 25, Vol. 2. [5]CasasUru, Memoria constructiva particular, Proyecto Aerosur 2. 2018.
[6]UNIT. 1998. UNIT-NM 33:1998. “Hormigón – muestreo del hormigón en estado fresco”.
[7]UNIT. 1998. Norma UNIT 69:1998. “Hormigón - Extracción, preparación y ensayo de testigos de estructuras de hormigón.
[8]UNIT. Norma UNIT 1082:2002. “Hormigón. Procedimiento para la preparación y el curado de probetas.
[9]UNIT. Norma UNIT NM 77:1998.”Hormigón. Preparación de las bases de probetas y testigos cilíndricos para el ensayo de compression”.
[10]UNIT. Norma UNIT NM 101:1998. “Hormigón. Ensayo de compresión de probetas cilíndricas”

Figura 54: Acceso a planta Concrexur. Figura 55: Primer Boca de carga.

En la visita a la planta de Concrexur, se observó las distintas etapas del proceso dentro de producción, hasta la carga del camión que lo transporta a la obra, así como también los distintos ensayos que se le realizan al cemento, y al HAC para la formulación de la correcta dosidificación y el control de calidad de los mismos.
Es una única planta con tres bocas de carga. Se realizan aproximadamente 500 m3 por día de producción de hormigón. Una de las bocas nuevas carga autocompactante, la otra el hormigón convencional y la más antigua se usa exclusivamente para hormigón de pavimentos.
La más antigua tiene 4 depósitos. Asciende el material a las 4 cajas, donde pesan los áridos, caen por gravedad a la caja de abajo donde está la balanza, suspendida en celdas de carga, y tiene para 4 tipos diferentes de áridos. Tiene un
Figura 56: Boca de carga 2. Figura 57: Boca de carga 3.
Hormigón autocompactante - Madelón Iglesias
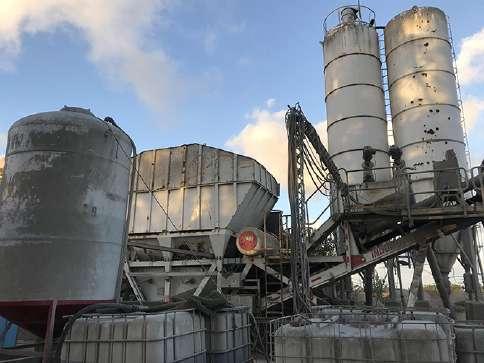
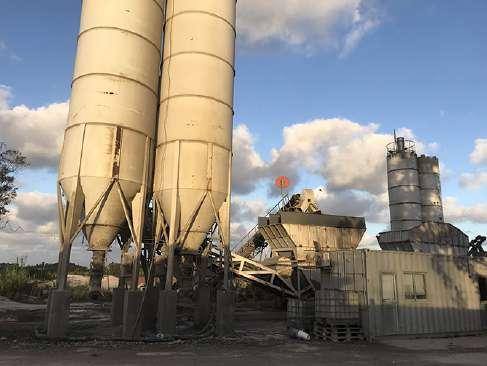
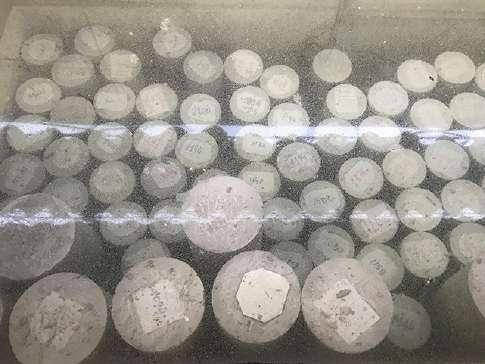
Figuras 58, 59, 60: piletas de curado de probetas de hormigón y de cemento, con termostato y resistencia que permiten controlar la temperatura del agua de curado.
Figura 61: equipo Washington.
compartimento para piedra 20-30mm, otra para 5-20, y otra para arena previamente mezclada, gruesa y fina, más o menos 70-30%.
Las nuevas bocas, tienen compartimentos separados, arena gruesa, arena fina, pedregullo y gravilla. Son dos tolvas, una tiene escoria y la otra tiene cemento. Se realiza un control estricto en la descarga de ambas. Del depósito cae a las celdas de cargas y de ahí cargan a los camiones.
El equipo Washington, nos permite medir el aire contenido en el hormigón. Se mide dos o tres veces por semana. El volumen del equipo es de 7 lts calibrado en %, es un manómetro pero calibrado en % de aire. Con pedregullo el criterio
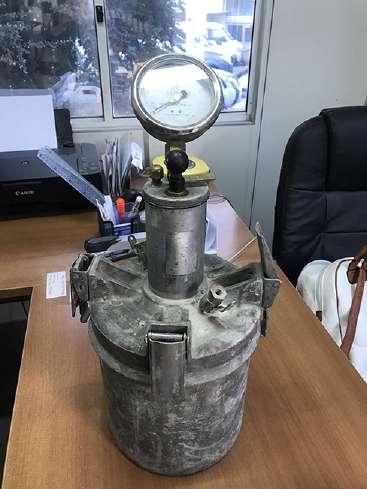
Figura 62: Prensa de probetas de cemento. Tracción por flexión y compresión.
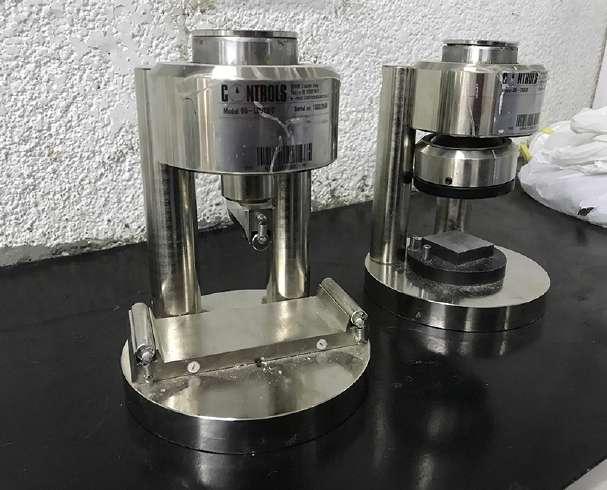

Figura 63: Ensayo de finura de cemento (izquierda).
Figura 64: Mesa de sacudidas, para compactación de las probetas de cemento (centro). Figura 65: Ensayo de fraguado del cemento
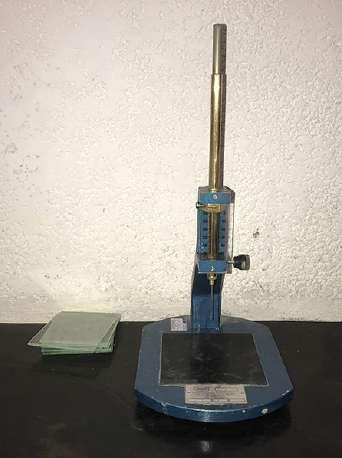
de aceptación es 2 y 2,5 %, y con gravilla como es el caso del HAC entre 3, 3,5% de aire. Con la misma carretilla que extraen para realizar el ensayo del cono de flujo y probetas, contemplan los 7 litros para el equipo de Washington. En el ensayo de finura de cemento por ensayo de vacío, se realiza con un tamiz al que se tapa, y lo que queda retenido en el tamiz se mide. Se ensaya con tamiz de 45 y 75 micras, el de la foto es de 45. A todas las tolvas de cemento se les hace el ensayo de finura.
Figura 51: Equipo de rayos x (composición química del cemento). Figura 66: Consolas de control de plantas, del área de programación.
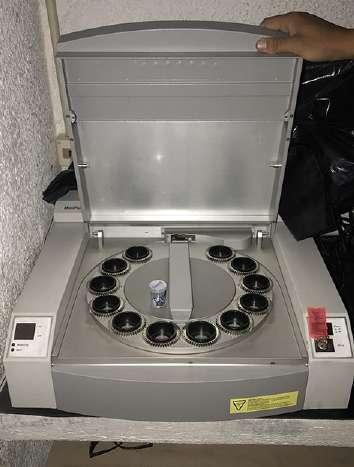

HORMIGONES ESPECIALES (2019)
Utilización de hormigón autocompactante
Altamira centenario - edificio de viviendas
Mariana Morales1
1. e-mail: mail

El presente trabajo toma como caso de estudio una obra en construcción correspondiente a un edificio de 30 viviendas promovido por la Agencia Nacional de Vivienda y amparado en la ley VIS. Esta ubicado en el barrio La Blanqueada sobre la calle Centenario esquina Escuder Núñez.
Desarrolla: Grupo Vinsoca Sur Entrega: Agosto 2019.
Ubicación: La Blanqueada, Av. Centenario 2954 esq. Pedro Escuder Núñez Comodidades: 30 Unidades de 2 y 3 dormitorios.
Información extraída de sitio web: www. siserviciosinmobiliarios.com.uy
GENERALIDADES
La obra comenzó en Enero del 2018 cuenta con Subsuelo, Planta baja y 8 niveles por encima de la misma. Actualmente se encuentra en etapa de terminaciones.
El sistema constructivo utilizado, es el llamado SISTEMA FORSA que consiste en encofrados metálicos de aluminio, que componen losas y muros, siendo estas completamente de hormigón armado.
La empresa participa de todas las etapas del proyecto, encargandose desde la compra del terreno, el proyecto arquitectónico, la construcción del mismo y posteriormente la venta de las unidades.
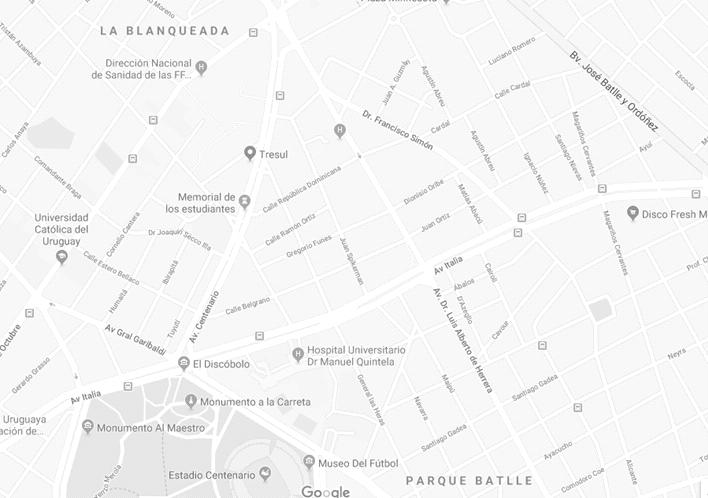

Utilización de hormigón autocompactante - Mariana Morales
RECAUDOS GRÁFICOS DEL PROYECTO
Considerando la utilización en obra del sistema de encofrado Forsa, y teniendo en cuenta que la empresa trabaja en todas las etapas del proceso, el proyecto arquitectónico se articula en función a la utilización de la modulación según las medidas de los moldes, generando tanto en las habitaciones como en las medidas de aberturas y pasillos, tamaños múltiplos de la modulación Forsa, para de esta forma facilitar en la etapa de obra las tareas de encofrado y evitar adaptaciones engorrosas del sistema.
Algunas de las estrategias proyectuales son: generar ventanas de piso a techo, para eliminar los moldes pequeños como antepechos, habitaciones cuyas dimensiones sean múltiplo de 60cm (ancho de formaleta de muro). Generar muchetas en muros exteriores para albergar luego la aislación térmica y emplacado de placa de yeso. PLANTA TIPO Niveles 1 al 7


En Planta baja se ubican 2 unidades de 2 y 3 dormitorios, espacio de estacionamiento al aire libre y lugar de juegos infantiles, la planta tipo plantea 4 unidades por nivel 3 de ellas de 2 dormitorios y 1 de 3 dormitorios, todas se encuentran conectadas por un pasillo
Utilización de hormigón autocompactante - Mariana Morales

de acceso abierto que “balconea” al espacio común en Planta Baja. El último nivel está destinado al Salón de usos múltiples (SUM) y a terrazas barbacoas privadas de las unidades del 7mo nivel.