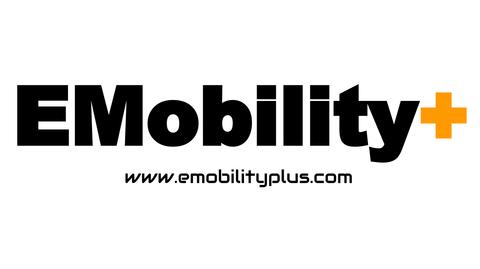
3 minute read
UNDERSTANDING CAPACITY FADE
In recent years, the popularity of lithium-ion (Li-ion) batteries has grown significantly They are found in devices ranging from cellphones and laptops to even cars This is largely due to advantages such as higher energy density and voltage capacity, as well as lower self-discharge rates compared to other rechargeable batteries
However, if we expect this technology to assume an important role in defining the future of transportation and energy storage, the issue of capacity fade in Li-ion batteries needs to be addressed Capacity fade (or capacity loss) in Li-ion batteries refers to the reduction in performance that occurs in the battery over the course of its lifetime Battery performance declines with time and use Eventually, the performance becomes unacceptably low, rendering the battery unusable Capacity fade has especially great implications in automotive applications since the battery cost is fairly high and customers have largely come to expect a service life that compares favorably to combustion engines
Advertisement
As per the U S Advanced Battery Consortium, an electric vehicle (EV) battery is expected to have a lifetime of 15 years and function up to 1000 cycles For EV manufacturers to work toward this goal, they need to have the ability to understand and accurately predict capacity fade The considerable complexity of Li-ion batteries and the interplay between their physical and chemical phenomena make this a difficult task In such a scenario, modeling and simulation play an important role in providing much-needed understanding
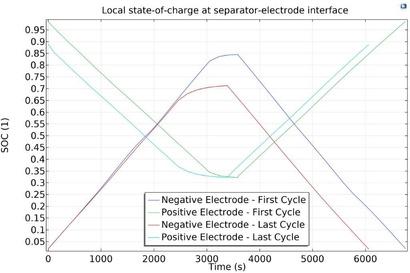
Modeling Capacity Fade
Experiments, often costly and time-consuming, are impractical when it comes to understanding capacity fade Besides, experimental results fall short compared to the physical insights that electrochemical and mathematical modeling affords. Therefore modeling and simulation play a crucial role in designing experiments as well as in evaluating the results from experiments Experimentation is reserved for the validation of the models
Modeling and simulation can provide pertinent insights into mechanisms such as lithium plating, particle cracking, and electrolyte decomposition These can help in understanding the impact of factors such as SEI layer growth and Li inventory on the capacity fade, thus serving as a reliable guideline in the development of strategies to mitigate capacity fade for given drive cycles
For example, Figure 2 shows how the capacity based on the amount of cyclable lithium and the nominal 1C discharge capacity decreases continuously While the fade rate is higher during the initial cycles, both capacities decay similarly about 20% during the 2000 cycles of the study This indicates that a loss of lithium, rather than an increased film resistance due to the SEI layer growth, is the primary contributor to the 1C discharge capacity fade.
Battery aging can occur due to either calendar aging or cycle aging Calendar aging is a function of the length of time that the battery is used However, the self-discharge rates of a cell also depend on parameters such as the operating temperature and state of charge (SOC) Several operational conditions can lead to accelerated capacity fade in Li-ion batteries Repeated cycling can lead to the decomposition of the electrolyte Repeated intercalation and deintercalation during charge and discharge can also lead to the expansion and contraction of electrode particles, which in turn can lead to electrode particle cracking This can bring about a decomposition of the initial solid electrolyte interphase (SEI) layer followed by an “uncontrolled” increase in the SEI layer SEI layer growth is one of the major reasons for cell degradation. In general, the SEI layer is useful, since it protects the anode against degradation, thus ensuring stable performance However, when this layer is subjected to repeated cycling and elevated temperatures, it can become unstable and see uncontrolled growth Overcharge and discharge can also lead to lithium plating, which in turn results in the loss of cyclable lithium in the cell It should also be noted that all of the phenomena discussed here are highly temperature dependent, with most of them accelerating at higher temperatures For instance, studies show that cell life can reduce to half when the operating temperature is maintained at 35oC instead of 25oC However, lower temperatures can also be detrimental to certain aspects of battery performance As an example, charging at low temperatures can accelerate lithium plating The various phenomena involved, and their interdependence can be understood either by performing extensive experimentation, mathematical modeling, or physics-based modeling
Experiments, often costly and time-consuming, are impractical when it comes to understanding capacity fade Besides, experimental results fall short compared to the physical insights that electrochemical and mathematical modeling affords Therefore, modeling and simulation play a crucial role in designing experiments as well as in evaluating the results from experiments Experimentation is reserved for the validation of the models
Modeling and simulation can provide pertinent insights into mechanisms such as lithium plating, particle cracking, and electrolyte decomposition These can help in understanding the impact of factors such as SEI layer growth and Li inventory on the capacity fade, thus serving as a reliable guideline in the development of strategies to mitigate capacity fade for given drive cycles
For example Figure 2 shows how the capacity based on the amount of cyclable lithium and the nominal 1C discharge capacity decreases continuously While the fade rate is higher during the initial cycles, both capacities decay similarly about 20% during the 2000 cycles of the study This indicates that a loss of lithium, rather than an increased film resistance due to the SEI layer growth, is the primary contributor to the 1C discharge capacity fade
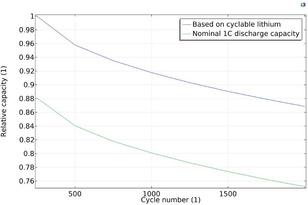
