WIND DOGGERFARMBANK C A breakthrough for Low-carbon Copper
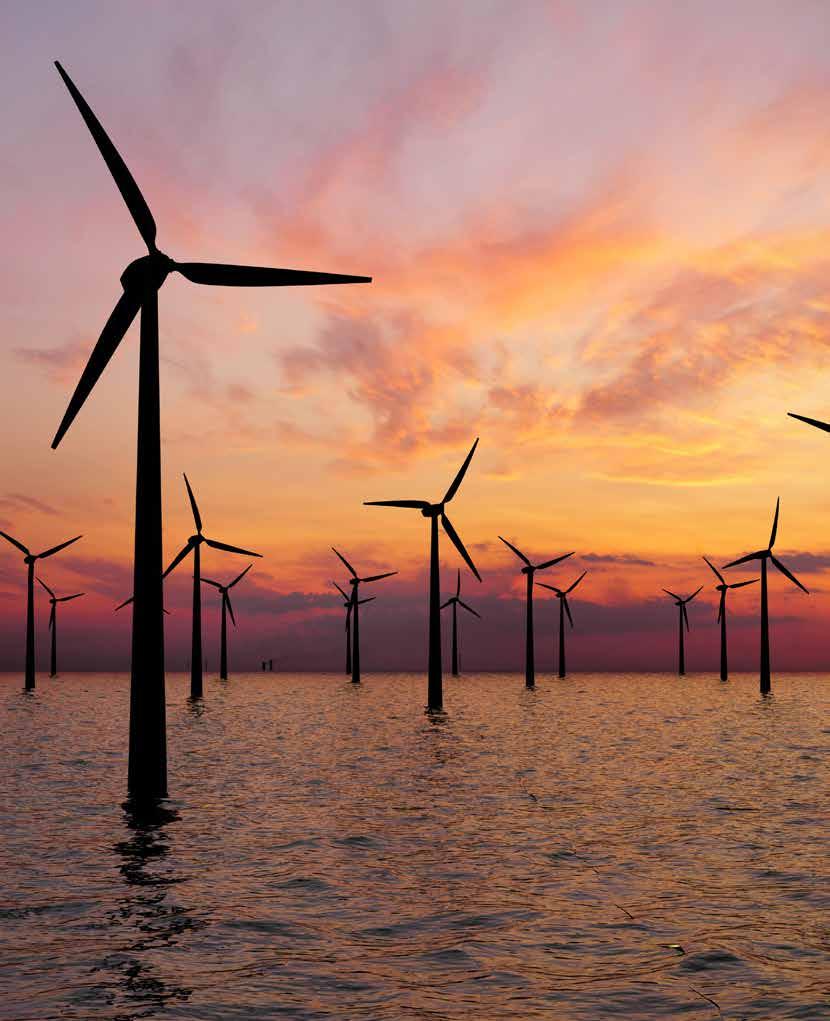
CUTTING EMISSIONS BY 23,000 TONS
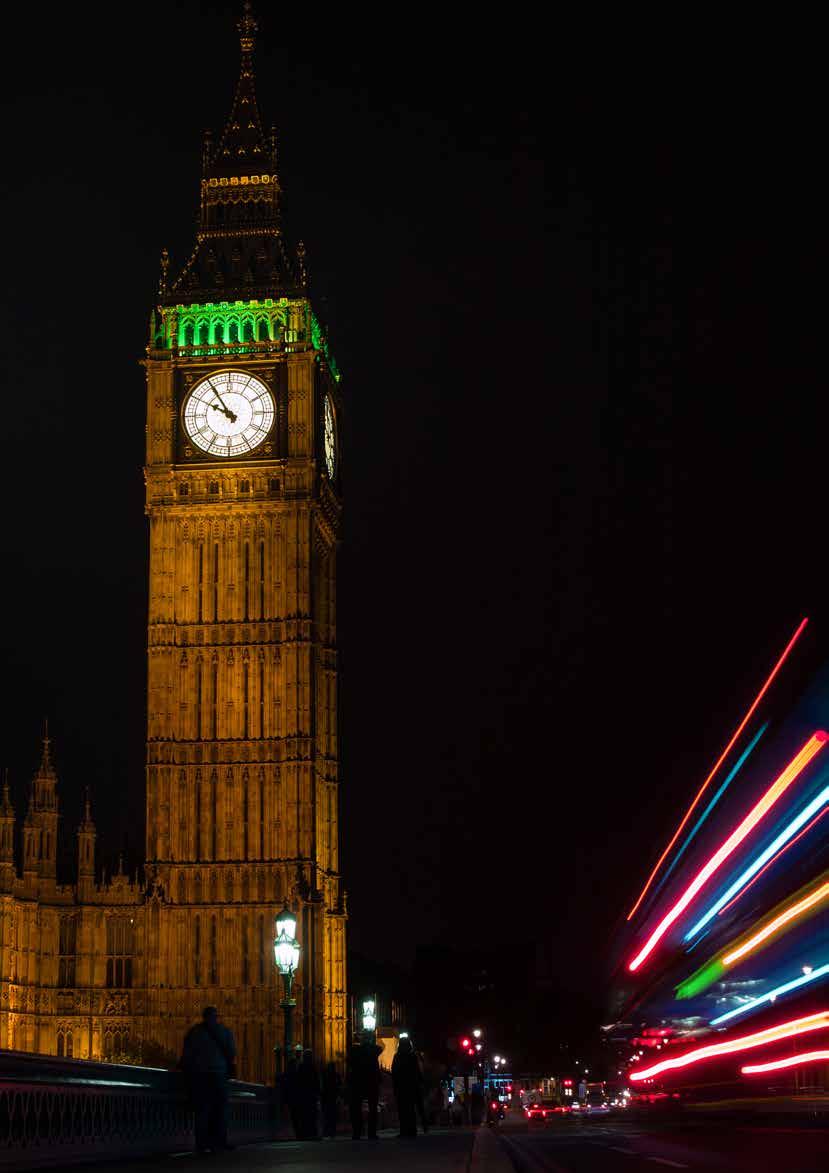
For the Dogger Bank C project, the third phase of the world’s largest offshore wind farm, three Scandinavian companies have worked together closely: Boliden, Elcowire and NKT. Low-carbon Copper will be used for the high-voltage cables at Dogger Bank C that will help power the equivalent of six million British homes.Each of the three companies adds their expertise to these cable solutions – Low-carbon Copper causes less than half of the carbon emis sions over its production processes, compared to the global average footprint for standard copper. 23,000 tons of CO2 is equivalent to 7,700 average family cars driven for 1 year.* *an average family car emits about 3 tonnes of CO2 every year.
LOW-CARBON COPPER
The carbon emissions reductions from using Low-carbon Copper include:
LOW-CARBON COPPER
Read more about the emissions reductions on next page 4
Dogger Bank C, with an installed generation capacity of 1.2GW, has a development area of around 560km2, and is 196km from shore. Connection will be at a substation at Teesside. The previous projects, Dogger Bank A and B, with a combined generation capacity of 2.4GW, connect to the existing substation Creyke Beck in the East Riding of Yorkshire.
The copper cathodes that Elcowire uses in its pro duction come from mines and smelters in Sweden, Finland and Norway. Production there has under
gone a substantial transformation due to electri fication and automation of various stages of the process.TheLow-carbon Copper has also been made possible by a very efficient ore concentration process and a world-class green energy mix. ”Elcowire set an example by producing semifinished and finished products that have a low impact on nature and the climate. We are proud to be in the lead for this transition,” says Paul Gustavsson, Elcowire’s CEO.
WHAT IS LOW-CARBON COPPER AND HOW IS IT ACHIEVED?
Dogger Bank, once a land mass uniting Britain with continental Europe, but since the last Ice Age a well-known sandbank, is the stage for an impres sive renewable energy project, the world’s largest offshore wind farm.
The reduced CO 2 emissions of Elcowire’s Lowcarbon Copper have been validated by third party, and will help customers to achieve their emission reduction targets faster and more efficiently. Paul Gustavsson comments: ”As Northern Europe’s leading provider of copper wire products Elcowire is devoted to supporting our planet’s shift to greener energy sources and raw materials,” he says. ”We focus on developing solutions that enable electrification of transport, expanding solar and wind power sources and the widespread growth of a modern and sustainable infrastructure. Offering Low-carbon Copper solutions from our production is a great move towards that goal.”
After completion the wind park will power the equivalent of 6 million British homes. The project owners SSE, Equinor and Eni Plenitude predict completion during 2025.
Step 1: From the copper mines (Boliden)
ACCELERATE YOUR JOURNEY TOWARDS A LOWER CARBON FOOTPRINT
The Dogger Bank Offshore Development Zone, including the three phases A, B and C, is located between 125 and 290 km off the east coast of Yorkshire, and extends over approximately 8,660km². Water depths range from 18 m to 63 m.
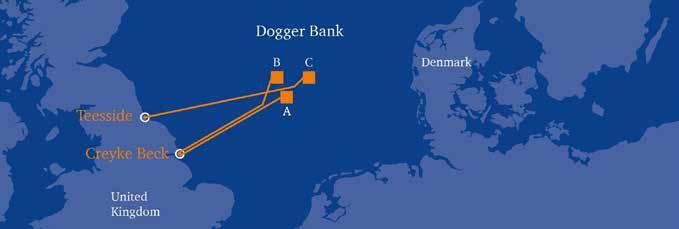
Step 2: Producing the copper wire (Elcowire)
Step 3 & 4: Producing the high-voltage cable and placing it on the seabed (NKT)
LOW CARBON COPPERLOW-CARBON COPPER
The third step takes place at cable manufacturer NKT in Karlskrona where the Low-carbon Copper wire is drawn to the desired dimension and stranded to the conductor. The high-voltage cable is produ ced and tested using 100 percent renewable electri city, which is further reducing the product carbon footprint.
The 270 km of cables for Dogger Bank C is loaded onboard the cable-laying vessel NKT Victoria directly at the factory. The cable system is then transported and installed at the seabed. NKT Victoria is one of the world's most advanced and fuel-efficient cable-laying vessels and compared to other large cable laying vessels it is capable of less than half of their CO 2 emissions.
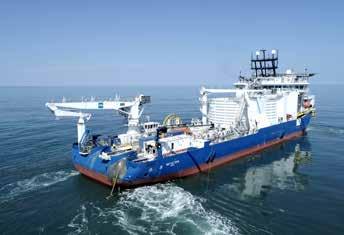
How the carbon footprint is lowered in the Dogger Bank C project
An electrified train travels 1,350 km through Sweden to deliver the raw material, copper cathodes, to copper solutions company Elcowire’s advanced production facility where the Low-carbon Copper wires to be used in the final cable solution are produced.
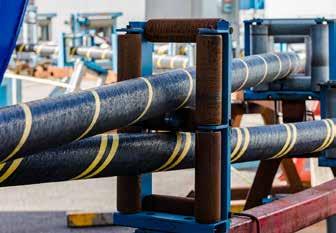
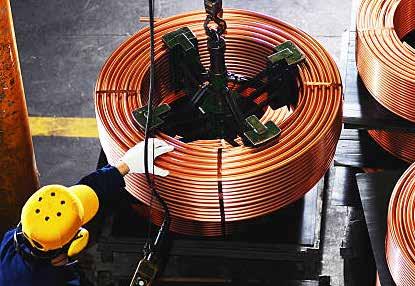
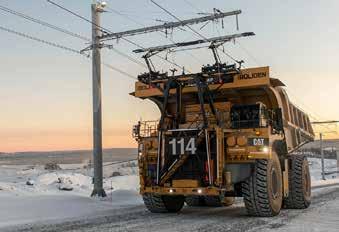
First part of project takes place in the north of Sweden. Here, metal company Boliden has deve loped an efficient mining process with electrified vehicles and only fossil-free energy sources –mainly from hydropower – throughout its lean, and very efficient processes. Finally, there are also sustainable transports.
1
3 4
2
A BREAKTHROUGH FOR LOW-CARBON COPPER
• Elcowire has replaced forklifts from diesel to electric.
The footprint has been calculated in accordance with the GHG Protocol Product Standard and ISO 14064-3 with support from Sphera. It has also been verified to comply with the GHG Protocol and reviewed according to the princip les of ISO 14064-3 by a third party, Intertek.
”HOW CAN YOUR NUMBERS BE LOWER THAN AVERAGE?”
When calculating the CO 2 footprint, Scope 1, 2 and 3 emissions have been included. All cate gories in the Greenhouse Gas Protocol with a relevant impact on the final carbon footprint from cradle-to-Elcowire gate are included.
The mines and smelters where our copper cathodes are produced achieve a lower CO2 footprint than the industry average due to higher efficiency and level of electrification, in combination with fossil-free energy sources.
”WHAT DO YOU INCLUDE IN YOUR CO 2 FOOTPRINT?”
”WHERE ARE THE ELCOWIRE LOW-CARBON COPPER CATHODES PRODUCED?”
Our Low-carbon Copper has less than half of the global average CO 2 emissions per kg of copper quoted by the International Copper Association (ICA).
The Dogger Bank C project, the third phase of the world’s largest offshore wind farm, becomes a landmark for sustainability. It introduces Lowcarbon Copper solutions as the new standard for large renewable energy projects. And the compa nies behind this – Boliden, Elcowire and NKT – all play important roles in the process.
”WHO BENEFITS FROM ELCOWIRE’S LOW-CARBON COPPER OFFERING?”
ELCOWIRE’S LEAN PRODUCTION
• The electric train that delivers the copper
”WHAT IS LOW-CARBONELCOWIRECOPPER?”
LOW-CARBON COPPER
An important step toward the net-zero vision for carbon emissions in the European society
cathodes to Elcowire’s site from Boliden returns back north to Boliden in Rönnskär with electronic scrap from Helsingborg, collected from the rest of Europe. The scrap is used for producing copper cathodes from recycled copper.
”HOW DO YOU ENSURE THAT THE NUMBERS ARE CORRECT?”
We are offering Low-Carbon Copper to custo mers that value an efficient improvement supporting policies and fulfilling obligations for lowering their CO 2 footprint.
Our Low-carbon Copper cathodes are produced at Rönnskärsverken in Sweden and Harjavalta in Finland by Boliden.
• Copper scrap from the production of wire rod is used internally or sent to Boliden for recycling (a proof of circular thinking).
• Elcowire has adapted its approach to decrease the downtime of its equipment and optimzed the maintenance schedule. This is in fact a good thing for the equipment and prolongs its lifecycle.
Q&A about Elcowire’s Low-carbon Copper products
LESS THAN HALF OF THE GLOBAL AVERAGE CO 2 EMISSIONS PER KG OF COPPER QUOTED BY THE INTERNATIONAL COPPER ASSOCIATION (ICA).
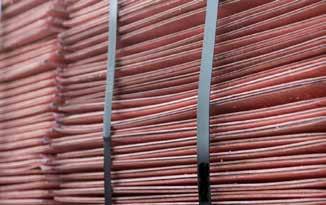
The production of copper from cradle-to-Elcowiregate includes Boliden’s mining and milling, transpor tation, smelting, casting, rolling and refining. GHG emissions from mining and milling include all three scopes. Smelting, casting, rolling and refining include scope 1 and 2, while transportation and all other input materials used in the process of producing metals are scope 3 emissions also included in the calculation.
LOW-CARBON COPPER
”
CEO PAUL GUSTAVSSON
The reporting protocol that was used for verifica tion is the Greenhouse Gas Protocol – Product Life Cycle Accounting and Reporting Standard. The product was also validated and reviewed against the general principles in ISO 14064-3 Standard (Greenhouse Gases – Part 3: Specification with Guidance for the Validation and Verification of Greenhouse Gas Assertions)
VALIDATED PROCESS FOR LOW-CARBON COPPER
LOW-CARBON COPPER FACTS & FIGURES
The significantly lower CO 2 emissions of the Low-carbon Copper are verified through several validation processes.
As one of the leading European suppliers of copper products, we are committed to sustainable copper sourcing. We are developing advanced technologies to provide outstanding energy-saving products with maximum useful life to enable sustainable solutions.”
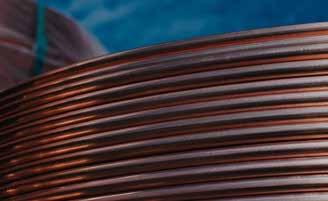

The calculated emissions from 1 kg of Low-carbon Copper from Elcowire is 1.7 kg. This compares to less than half of the global average emissions from 1 kg of copper.When calculating the footprint, Scope 1, 2, and 3 emissions have been included, i.e. all categories in the Greenhouse Gas Protocol with a relevant impact on the final product carbon footprint, from cradle to Elcowire gate.
Energy efficiency is a key indicator to save natural resources and reduce emissions.

Elcowire’s energy efficiency – showing energy consumed per tonne of product – has steadily decreased since 2018.
SUSTAINABILITYLEADERSHIP With its sustainability performance 2021, Elcowire displayed positive development over time regarding all its key indicators and footprints, establishing the company as a sustainability leader in its business. 402006080 0.60.40.200.40.30.20.10 Total(GWh)energy 2018 202120202019 Energy(kWh/t)intensity Natural gas Electricity 201005152530 Safety Group 2018 20202019 LTIFR Number of accidents 100,00040,00020,000060,00080,000120,000Totalwater(m 3) 2018 202120202019 7 since%2018 5 since%2018 Water intensity (m3/t) 12,0009,0006,0003,000015,00018,000 CO2 emissions(tons) 20212020 Scope 1 emissions Scope 2 emissions since-9%2020 0.60.40.20 Natural gas Electricity 201005152530 Safety Group 2018 202120202019 LTIFR Number of accidents 100,00040,00020,000060,00080,000120,000Totalwater(m 3) 2018 202120202019 5 since%2018 Water intensity (m3/t) 12,0009,0006,0003,000015,00018,000 0.120.100.080.060.040.020 CO2 emissions(tons) 20212020 CO2 i (COntensity 2/t) Scope 1 emissions Scope 2 emissions since-9%2020
Elcowire helps customers reduce their carbon footprint by offering low-carbon solutions.
Elcowire aims to be a sustainability leader in its business, and therefore the internal as well as the product carbon footprints are of course strategically vital.The carbon footprint of Elcowire’s production processes decreased by 9 percent since 2020.
RAILROD
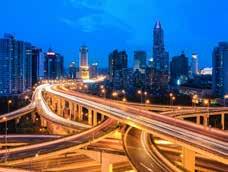
CONTACTS
We are one of the leading suppliers in Europe, developing products and services based on wire rod for the electrical and infrastructure industry with copper and aluminum solutions. Operations are located in Sweden and Germany. Elcowire consists of five business units: Rod, Wire & Strands, Rail, High Voltage and Specials. We employ 400 people and our headquarter is located in Helsingborg, Sweden. Elcowire is part of Liljedahl Group.
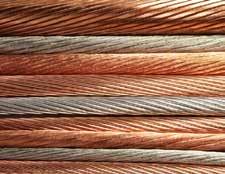
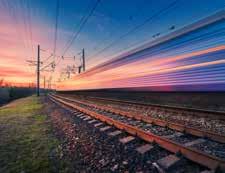

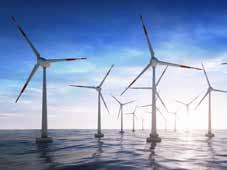
HIGH VOLTAGE
WIRE & STRANDS
Elcowire Group AB Box 914, SE-251 09 Helsingborg, Sweden Phone: +46 (0)42 195300 info@elcowire.com elcowire.com
SPECIALS