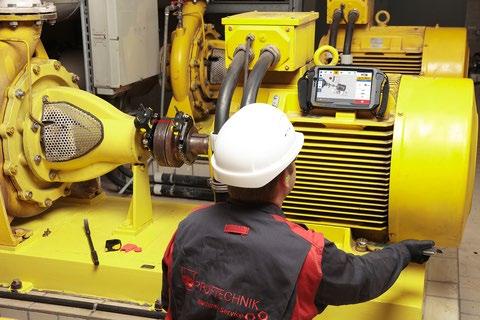
9 minute read
PRODUCT SHOWCASE
Fluke 831 Laser Shaft Alignment Tool Simplifies Precision Shaft Alignment, Saving Thousands in Downtime and Energy Waste
The powerful alignment tool makes it practical to align most machines in the facility, not just a select few Misalignment causes at least half of all damage to rotating machinery, but instead of fixing the problem, teams often just treat the symptoms of misalignment by replacing bearings, couplings, and seals because they think alignment takes too long. The new Fluke 831 Laser Shaft alignment Tool makes shaft alignment easy with an intuitive guided user interface that enables quick and complete shaft alignment without advanced training or complicated programs.
While it’s easy to use, the Fluke 831 is still powerful enough for the skilled technician, letting them cover more machines with all the functionality needed on the plant floor — from thermal growth calculations to user defined tolerances and more.
The Fluke 831 features:
» High performance and precise results — It leverages powerful features, like unique extend mode to handle gross misalignment and an integrated thermal growth calculator that automatically factors the dynamic machine changes into the result.
» Quick setup and intuitive user interface — Its quick setup and tablet-like, intuitive guided user interface make the Fluke 831 laser alignment tool more user-friendly than any other conventional measurement method. align coupled shafts in quick, easy steps.
» adaptive alignment — enables maintenance and reliability teams to address the full variety of horizontal, angular, and vertical alignment challenges.
» Share data via the cloud — Its integrated WiFi cloud solution easily transfers data from the Fluke laser alignment tool to the arC 4.0 PC software.
The Fluke 831 allows shaft alignment to become a regular part of the maintenance routine leading to less energy consumption through the elimination of reaction forces inside rotating machinery, increased reliability, reduction in costs through a decrease of spare parts and extended parts life, and increased maintenance intervals due to longer machine life.
For more information on the Fluke 831 Laser Shaft alignment Tool, visit: www.fluke.com
HNA Live Launches AI and 3D Cloud Solution for Manufacturers
HN a Live, a data analytics company serving manufacturing and real estate industries, has selected CL ea , a I/IOT platform from S eCO MIND uS a LLC (www.secomind.ai) for their innovative cloud solution that combines a I and 3D technology to optimize manufacturing facility productivity.
Manufacturing 4.0 is transforming the way manufacturers manage and optimize their operations, from product design and production to distribution and customer satisfaction. HNa LIVe offers granular, privacyprotected, real-time insights into the performance efficiencies and bottlenecks of operations, safety, and quality in the manufacturing space.
"The digital transformations are notoriously difficult to scale up across networks of factories, the pressure to succeed is intense. With CLea we can rapidly enable manufacturers to capture benefits across the entire manufacturing value chain" — Cooper Mojsiejenko, Chief e xecutive Officer at HNa Live.
HNa Live makes use of LIDar and other data collection technologies to precisely measure and create 3D models for manufacturing whether it's plant movement, working parts in process, or a building's entire operation. HNa .Live's cutting-edge technology provides more accurate real-time 3D modeling for a manufacturer's business strategy.
"CLea enables connecting and cloud managing any hardware for smart control, monitoring, and actionable insights. HNa Live is enabling manufacturers to increase production capacity, reduce material losses, improve delivery lead times, and reduce their environmental impact. We are very excited to be part of their journey", — a jay Malik, CeO of SeCO Mind uSa
For more information: https://hna.live For more information: https://secomind.ai/
New Robotmaster plugin
75 percent reduction in programming time, the new plugin allows users to use a robot programming method that can automatically identify and resolve programming errors that could otherwise go unnoticed when using a manual process.
robotic programming for Mastercam CAD/CAM software users
streamlines
Hypertherm a ssociates, a u.S. based manufacturer of industrial cutting products and software, today announced a new software plugin from its robotmaster® brand.
The plugin makes it easy to convert Mastercam C aD/C a M data into an optimized, error-free robotic program. Once installed, users can import C aD files, tool paths, data, and process-specific information directly into robotmaster. They can then synchronize files so changes made to the original Mastercam file are transferred to robotmaster without needing to reprogram. In addition to a
“We’ve always said that you shouldn’t need advanced programming knowledge or robotics expertise to use robotmaster. We wanted to provide an easy way, for those who are using C aD/C a M software, to program a robot,” said Natalie adams, a product marketing manager for the Hypertherm a ssociates Software Group. “This new plugin streamlines the robotic programming process so Mastercam users can maximize their productivity and remain competitive through the rapid adoption of automation.”
The Mastercam plugin is made possible by robotmaster bridge, functionality found in robotmaster 2023, that allows seamless integration between a user’s chosen
C aD/C a M software and robotmaster. It is the first of many robotmaster plugins Hypertherm a ssociates plans to introduce.
The new robotmaster plugin for Mastercam supports Mastercam 2023, the current release, as well as Mastercam 2021 and 2022. a nd while the new plugin streamlines robotic programming for Mastercam customers, those looking for a standalone solution can simply rely on robotmaster's integrated C aD/C a M functionality. The software allows customers to import the C aD model for their part and generate toolpaths directly within robotmaster without the need for separate C aD/C a M software. To learn more, please visit www. robotmaster.com.
JTEKT Offers New HMC Series
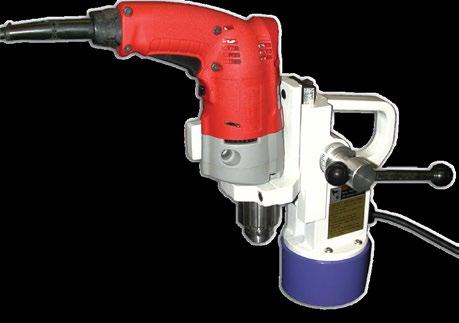
JTeKT Toyoda a mericas Corporation has recently introduced its FH5000 series of three high-speed horizontal machining centers (HMC), including the FH5000S HMC with 800X800X880 mm (X, y, Z) strokes, 900mm workpiece diameter, and 1100mm workpiece height capacity. The FH5000 series machines include a 500mm table capable of handling 1000 kg loads.
"With this series, Toyoda meets the growing demand for producing components with high metal removal rates, short cycle times and superior surface finishes," said a company spokesperson.
Toyoda's FH5000S HMCs with 60-tool aTC capacity are designed for speed and production reliability, featuring a 15,000 rPM, 50 HP (37 kW), 303 Nm (223 ft-lbs.) high acceleration spindle. The 40-taper spindle is designed with four ceramic bearings at the front of the spindle for increased rigidity and reduced vibration. Its patented hydraulic preload system brings the spindle up to 15,000 rPM less than one second without spindle warm-up, ideal for aluminum processing. The larger machines in the FH5000 series are equipped with a 50-taper spindle, 45 tools, and a longer X axis travel.
This machine is equipped with a direct drive b-axis table featuring an index time (90°) of 0.7 seconds. The FH5000 machining centers with the spindle design, preload system and high torque features, allows machine shops to take advantage of more aggressive, high-volume machining in a compact footprint, according to the company.
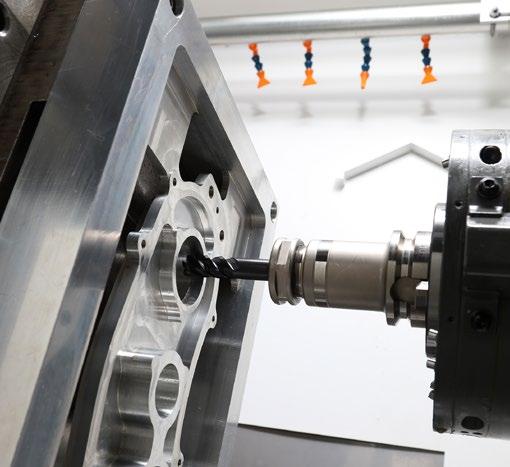
easily programmed, the H5000 series features the TOyOPuC-Touch panel through which the operator can monitor the machine, see operating data including energy consumption, and edit as required.
KUKA to Showcase Automation for Human/ Machine Collaboration at ATX West
During the aTX West 2023 show, KuK a robotics will showcase several new technologies geared specifically for safely automating those manufacturing processes where humans interact with robots on a regular basis. a mong those technologies are the new Lbr iisy cobot, the new KuK a KMP 600-S diffDrive automated mobile platform and the company’s Lbr iiwa robot incorporated into an automated mobile robotic material-handling system.
referred to as Sensitive Cobotic technology, KuK a’s Lbr iisy represents the future of automation. The cobot is readyto-use automation that quickly and easily integrates into any manufacturing application from pre-defined production processes to open, unstructured work environments with unpredictable conditions from one job to the next. a s the perfect collision-free coworker, KuK a’s new KMP 600-S diffDrive mobile platform takes intralogistics to a new level – especially in the consumer goods manufacturing industry. The platform provides a new automated guided vehicle system with high-speed support for production intralogistics and a payload of up to 600 kg. at the same time, the KMP 600-S diffDrive is ideally equipped for the tough everyday environment of industrial production. Its IP 54 design always enables it to work reliably even under adverse conditions – including water spray and dust.
Whether loading/unloading machines, assembling components or packaging, the cobot provides increased versatility and can be immediately operated by anyone from an automation expert to a cobotics newcomer. Featuring various operator levels, the user-friendly system adapts to the corresponding level of user knowledge. ready to use right out of the box, the Lbr iisy allows for use in more applications than ever before, including those so simple that most wouldn’t think they could be automated. Operating the iiQK a .OS system and supported by the iiQK a ecosystem, the Lbr iisy is ready for use in a matter of minutes – depending on pre-configured options – from unpacking to productive work. a s such, the cobot also eliminates long training times or having to learn complex programming techniques.
With six axes, a 3-kg payload, 600-mm maximum reach and 18.8-kg overall weight, the Lbr iisy is well suited for overcoming the challenges posed by confined workspaces. KuK a also offers the Lbr iisy in 11-kg and 15-kg payload versions.
For maximum safety and flexibility all KuK a mobile platforms, including the KMP 600-S, guarantee employees maximum freedom of movement without the need for safety fencing. Laser scanners mounted at the front and rear provide maximum safety and allow for high speeds in all directions of travel when cycle times require it. additionally, the KMP 600-S diffDrive uses eight safety zones at both the front and rear – customizable for vehicle speeds and specific applications.
Developed in partnership with the world's largest semiconductor fabricators, the mobile robotic solution KuK a demonstrated at aTX West reliably transfers materials in areas unsuitable for traditional automated material handling systems. a s the first of its kind, the KuK a mobile robotic wafer-handling system for human/machine collaboration offers an ideal solution for material transport of 200mm or 300mm wafer boxes and SMIF boxes, open cassette machine loading and unloading.
The system combines a KuK a Lbr iiwa 14 r820 Cr robot mounted on one of the company‘s KMP 200 Cr automated mobile platforms. both the robot and mobile platform are cleanroom class ISO 3 rated and feature advanced safety and navigational functionality. For simplicity and ease of use, the solution is completely integrated with one controller for the robot, platform and navigation as well as one software solution for all three Norstat now offers a full line INDuCTIVe SeNSOrS that offer a nominal sensing distance that is 2 times higher than standard inductive sensors.
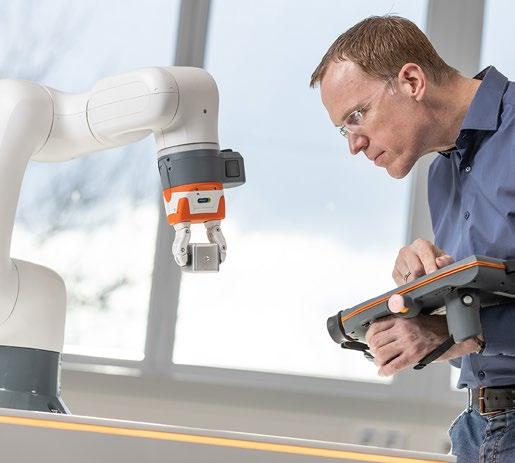
These PSL INDuCTIVe SeNSOrS by Sense have been redesigned to provide increased sensing distance
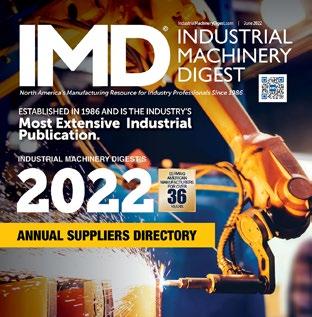
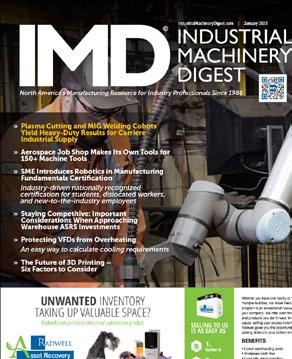

( up to 2x greater ) over their conventional inductive sensors while still maintaining a low cost factor. These PSL INDuCTIVe SeNSOrS are constructed with either stainless steel or brass housings in 12, 18 or 30mm sizes with sensing distances of up to 24mm and are available in either PNP or NPN direct current models. They have short circuit protection as well as reverse polarity protection and are available with high visibility LeD trigger indication. electrical connection is via cable or 4 pin M12 connector and various cable lengths are available.
The PSL INDuCTIVe SeNSOrS have a protection rating of IP 67 or IP 69K, can operate in temperatures from -25°C to +70°C and are certified for explosive atmospheres of combustible dust making them ideal for industries such as furniture manufacturing, textiles, or warehouses as well as for the handling of grains, cotton, linen, magnesium or aluminum metallic dust, charcoal dust, mineral coal, petroleum coke or carbon and chemical dusts. Contact Norstat for additional information, pricing, and availability.
For additional information: www.norstat.com
OMEGA Announces Expansion of Groundbreaking, Non-Invasive Temperature Sensor Technology, Now Available for Use on Plastic Pipes
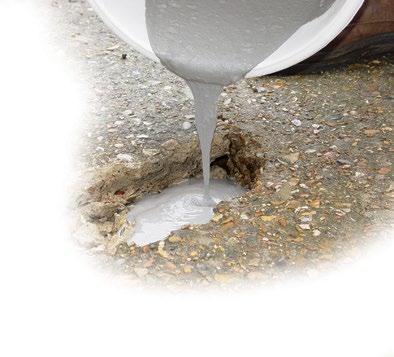
High-accuracy, non-invasive HaNI Temperature Sensors for use on plastic pipes install in seconds and never breach the pipe - no penetration, no risk of contamination award-winning HaNI Sensors precisely measure the temperature of media inside a pipe in seconds without ever breaching the pipe. This means no drilling, no cutting, no epoxies, and, most importantly, no downtime. a nd, because HaNI Sensors never come into contact with the process media, there is no risk of contamination or drift associated with sensor buildup, wear, breakage, corrosion, or damage from wake frequencies or water hammer. already making waves for innovation, HaNI Sensor expansion to plastic pipe applications marks further advancement of this patent-pending breakthrough technology.
OMeG a engineering, a leader in temperature measurement innovation for over 60 years, is announcing the launch of the latest version of its HaNI Clamp-On Temperature Sensor: the HaNI Clamp Sensor designed specifically for plastic pipe applications.
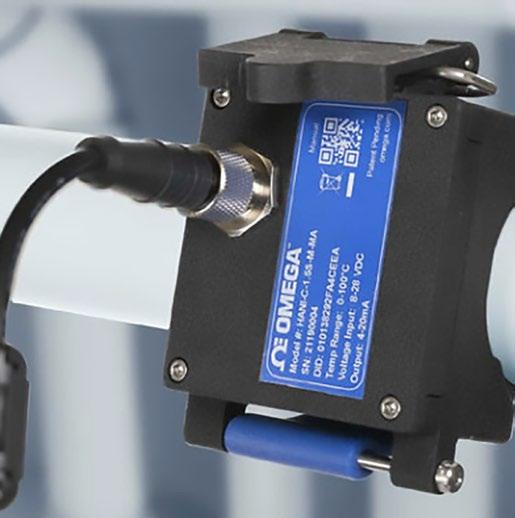
Previously available only for metal pipe applications, this newest version of the HaNI Sensor is the only industrial-grade, high-accuracy, non-invasive temperature sensor on the market today for plastic pipe applications.
"Plastic pipes have a very low thermal conductivity, so it is very difficult to try and read temperature through them," says Ken Leibig, Director of engineering at OMeG a "With the proprietary algorithm we've developed, HaNI sensors do what few even thought was possible: they install with the ease of a surface sensor while offering the high accuracy and high performance of a traditional immersion sensor. a nd now, with our newest model, the HaNI is becoming even more universal in its application - not to mention the fact that it is the only non-invasive sensor on the market capable of measuring temperature of media moving through a plastic pipe."

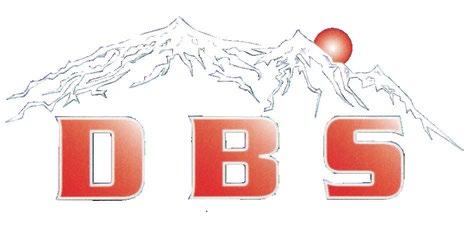
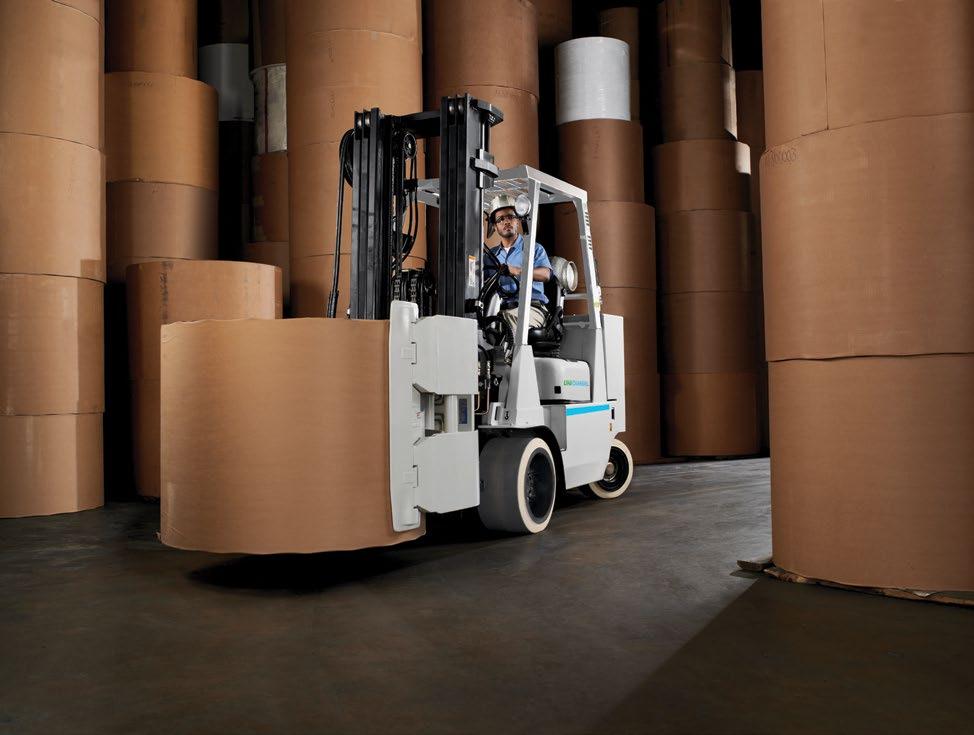
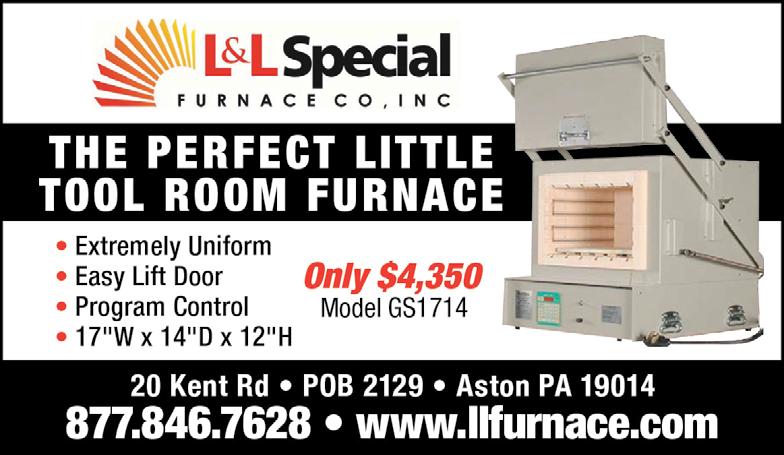
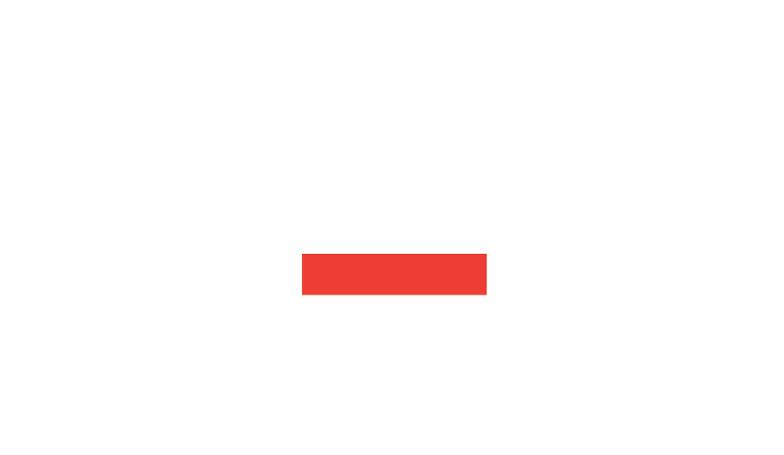

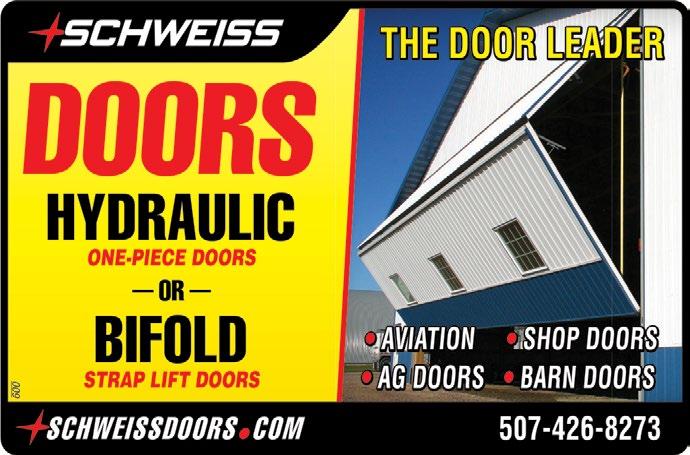
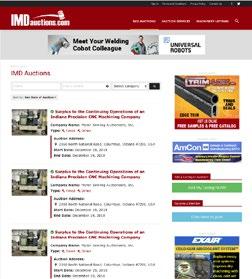
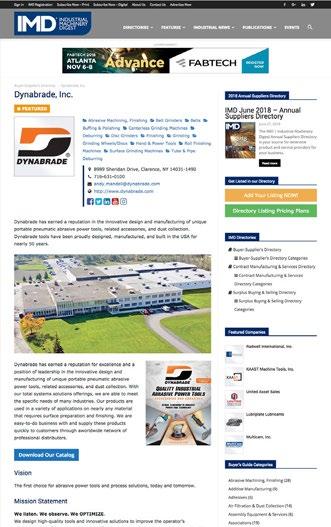