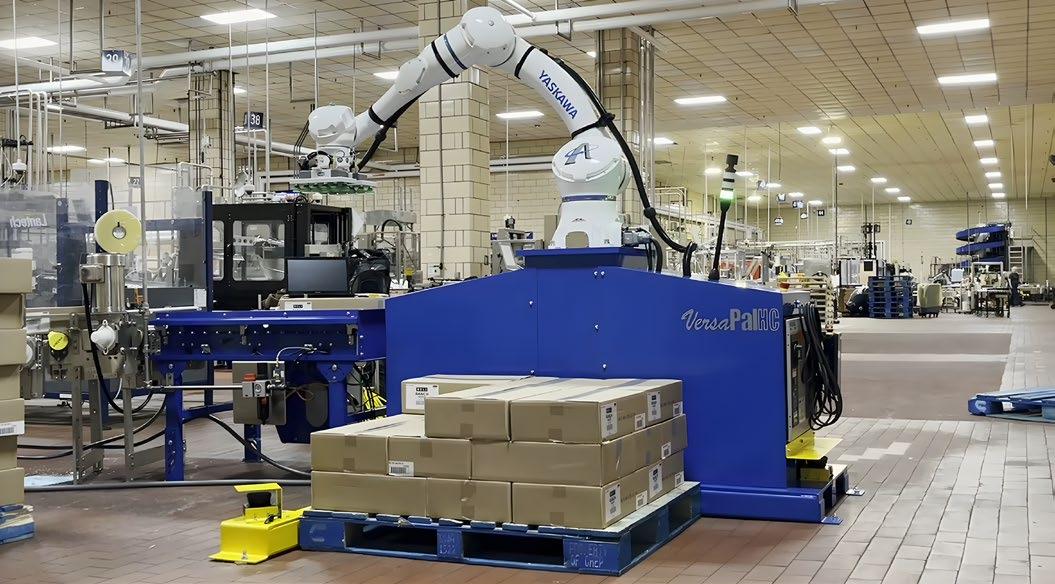
14 minute read
Robotic Roadmapping: Tips for Production Workflow Optimization
By: Chris Caldwell, Product Manager at Yaskawa America Inc. – Motoman Robotics Division
Faster, cheaper and more efficient – these are concepts that every manufacturer is tasked with maintaining without sacrificing product quality. achieving process success for a more resilient operation, however, takes dedication and resources. Key to this organizational turnaround is the concept of workflow optimization, where production processes are streamlined in such a way that risk is mitigated and throughput is optimized. Companies that can successfully implement innovative concepts and new technologies will be primed for maximum production agility.
Forward-thinking decision makers are realizing this. So much so, that many are embracing trends toward workflow optimization for continued business performance. From tech investment for end-to-end value delivery to enterprise resource planning (ERP) for data-driven optimized planning, much can be encompassed into this concept. However, streamlining processes and optimizing capacity at a large scale rarely happens without the presence of flexible robotic automation. From faster cycle times for optimal production output to reduced part rework for improved product quality, the strategic planning that goes into robot integration is key.
Robotic Roadmapping
Whether decision makers are choosing to implement a complete system from end- to-end or they are looking to integrate a single workcell to alleviate an operational bottleneck, there are multiple concepts to consider where continuous improvement and workflow for automation are concerned:
Understand the “Why”
Outlining key objectives to better understand production needs before robot selection will help drive the project from start to finish. From adding production capacity, to tackling quality concerns and meeting on-time demand, to gaining competitive advantage, raising additional revenue and much more, listing all relevant end goals and working from those will guide the decision making process. Important questions to ask at this stage include:
» What is the motivation behind capital investment?
» How will short-term or long-term success be measured?
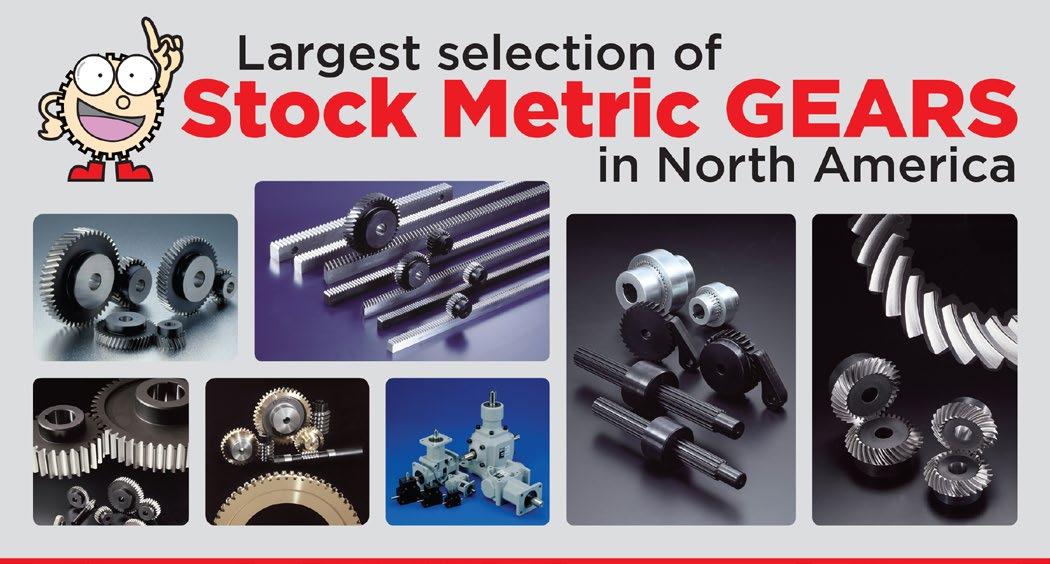
» What are key performance indicators?
» What are the target cycles per minute/day/hour and acceptable failures per day/hour/minute?
Being honest with answering these questions, and others, goes a long way to determining system type. Depending on target goals, application requirements and floorspace constraints, a faster system with limitations may be necessary versus a slower yet perfect system.
Know the Process
While it may seem obvious, having a clear understanding of the production process and what it is needing to thrive is a must. Whether via in-house research or by recruiting the expertise of a robot professional during a site audit, it is important to weigh questions like the following:
» How will automation be utilized (i.e., single-step vs. end-to-end, or somewhere in between)?
» How much flexibility does the application require?
» Is a stationary system needed or is a mobile robotic platform in order?
» How “smart” or cutting-edge does the system and tooling need to be?
» How controlled are infeeds and outfeeds?
The compilation of answers will dictate robot usage and system design. Keep in mind that current production layouts that use more fixed or hard automation will most likely be less complicated to automate. Random layouts with multiple infeeds and outfeeds, on the other hand, will up the complexity factor.
Cultivate Employee Buy-In
Perhaps as important as defining clear cut goals is motivating internal employees and valued stakeholders to grasp the idea of robotic automation and work hard to help fulfill the vision. To pursue unmotivated individuals, decision makers might want to provide answers to the following:
» What are the quality of life benefits that the automation will bring?
» What job advancement opportunities will be available as a result of internal robot use?
» What kind of training will be provided to robot operators?
Regarding the ladder concept of training, companies may choose to appoint, or even hire, a “workcell champion.”
This employee – fully dedicated and accountable for integration, programming utilization and maintenance of the robot system – is instrumental, and can be advantageous in helping decision makers garner support for meeting project deliverables.
Partner for Performance
To save on time, effort and resources, it is always advised to work with an experienced robot integrator or supplier. Inviting a knowledgeable expert into your facility to meet the production team and perform a site audit will get the project off to a smooth start, as well as answer any questions about production bottlenecks, worker safety, robot peripherals, etc. Keep in mind, every production floor is unique, and questions to be mindful of are:
» What is the technical feasibility of the task I want to automate? Is there a better way?
» are there other areas on our production floor that would easily benefit from robotic automation?
» Is my process common among other companies or significantly unique that automation may be breaking new ground?
With respect to technical feasibility, if the task in question cannot logically and safely be addressed, finding another option is in order. Moreover, having a skilled individual assess current production can help address other areas for automation that may have been overlooked.
automation Inspiration
While a majority of manufacturers looking to improve workflow will have a pre-planned idea as to what application they would like to automate, it is not uncommon for select companies to be unsure of where to begin. This “cold turkey” approach to robotic automation can be overwhelming, but again, enlisting the professional know-how from a skilled robotics integrator or supplier can help guide the robot selection and integration process. For decision makers searching for the right place to implement robotic automation, here are some popular robot installations to inspire:

Palletizing
The relatively simple process of end-of-line palletizing is often the best place for manufacturers to start. Highly repetitive, this back-breaking application that typically involves moving uniform boxes from a conveyor to a pallet is perfect for robotic automation. Plus, the process can be further simplified via easy-to-use software that enables users to generate even the most complicated package and pallet layouts offline. For environments that demand more flexibility, heavy-payload collaborative robots with plug and play tool flange capability for quick changeover are being used. These fenceless systems are ideal for providing consistent and cost-effective palletizing in low- to medium-speed settings.
Picking and Placing adding a bit of difficulty to the mix is the concept of pick and place, where individual items are placed in trays or onto a conveyor for further packaging down the line. Often utilizing intuitive software and feature-rich vision technology to identify, orient and place objects with speed and precision, this process can definitely serve to improve cycle times.
Picking and Packing
For operations looking to move trays from a pick and place process, or load singulated or grouped items into bigger cartons, picking and packing can be an ideal place to start for new robot users. Keep in mind that while picking and packing can be achieved using clever conveyor and tooling designs for uniform products, the sortation of mixed items adds complexity and will require the use of sophisticated peripherals.
Sortation
Considered the “holy grail” of unloading, sortation of unstructured, mixed objects is one of the most complex tasks to automate. However, intelligent robot systems using a mix of various technologies, including Human Machine Interfaces (HMI), a I software and 3D vision, are modernizing this process and making it more accessible than ever – allowing robots to pick up objects quickly and reliably with minimum human intervention. Easily integrated with a wide range of traditional equipment, high-speed induction systems are especially helpful for reducing production bottlenecks where rapid sortation and singulation for downstream processes are concerned.
Machine Tending
Whether making agricultural, appliance or automotive components, robots excel at the transfer of parts for optimal production flow. Collaborative robots with Power and Force Limiting technology are well-suited in busy settings where there is the potential for harmful contact situations. Easily integrated with existing automation or machinery, cobot systems using speed and separation monitoring (i.e., laser scanners and light curtains) for safety zone monitoring are ideal.
Welding
For operations that require welding, optimizing product throughput may be as simple as adding a single robot arm – as this has the potential to reduce the cycle time per part in half, while maintaining the footprint of the workcell. New robot users on the other hand may want to consider a complete welding workcell. From ultra-compact options for adding capacity to pre- engineered efficiency workcells that are geared toward mitigating labor shortage and quality concerns, multiple solutions exist. Growing in popularity for this task is the use of human-collaborative robots. From highly portable weld carts that are easily rolled-up to large workpieces to complete collaborative workcells that are fully equipped with an industrial pedigree cobot, integrated weld package, intuitive weld interface, arc flash protection,
Additive Manufacturing a driving force for advanced prototyping and production, the use of 3D printing is an extremely beneficial application for manufacturers looking to reduce lead times. Ideal for making one-off parts or fixtures, being able to adapt and leverage design freedom with less labor and raw materials is quickly making this a shop floor must have. From plastic to plaster, the variety of compatible materials available for 3D printing is also advantageous for fulfilling unique application requirements. Basic desktop 3D printers and those with stair stepper motors are giving way to servo-controlled 3D printers with high resolution feedback. Moreover, the use of six axis robots with few limitations for printing unique angles is growing, causing manufacturers to take a second look at the possibilities this process and technology can bring to the shop floor. Companies, like aDDiTEC, are taking this concept a step further by offering an intuitive human machine interface (HMI) with a high-performance robot. This enables the unique ability to process two wire materials in a single part, along with the ability to print power and wire materials at that same time, making this process ideal for the creating of highly complex components from demanding materials. While the robotic system chosen to optimize operations will obviously depend on the task at hand, these applications provide a glimpse of what is within reach. Overall, the use of robotic automation is most often an expedient, cost-effective
aIMS Metrology Brings Full Range Of Turnkey, Software-Supported 5-a xis CMM Technology To Eastec 2023
The drive to propel growth through data-informed decisions has made coordinate measuring machines (CMM) with infinite 5-axis probe head positioning a fixture on the shop floor. aIMS Metrology will demonstrate its turnkey 5-axis CMM systems and single source software platforms at Booth #3251. The OEM’s Revolution Series Summit 10.10.10, LM and HB provide accurate, flexible three-dimensional inspection of small to large in-process and post-process parts on the shop floor, in the lab or in an automated cell.
aIMS’ lab-grade LM offers multi-sensor capabilities with Renishaw’s REVO-2 delivering measuring speeds up to 500 mm/second and data collection rates of up to 4,000 points per second for increased part throughput. The mobile HB, fitted with Renishaw’s 5-axis PH20, can be placed on or near a production line to provide dimensional verification and process flow monitoring in real time. The Summit’s large part inspection capacity (40 in. from left to right, top to bottom and front to back) can accommodate REVO-2’s RVP vision and SFP2 surface measurement. aIMS’ designs minimize wear and tear for zero maintenance and use 110/220-volt outlets, eliminating the need for shop air.
“We’re a single source provider that builds and assembles our CMMs in the U.S.,” says Mark Gearding, aIMS co-owner and vice president. “We have an in-house service group and application team that allows us to customize the CMM to a job shop or fabricator’s needs. That includes programming, custom holding fixtures, tooling, automation, service and support.”
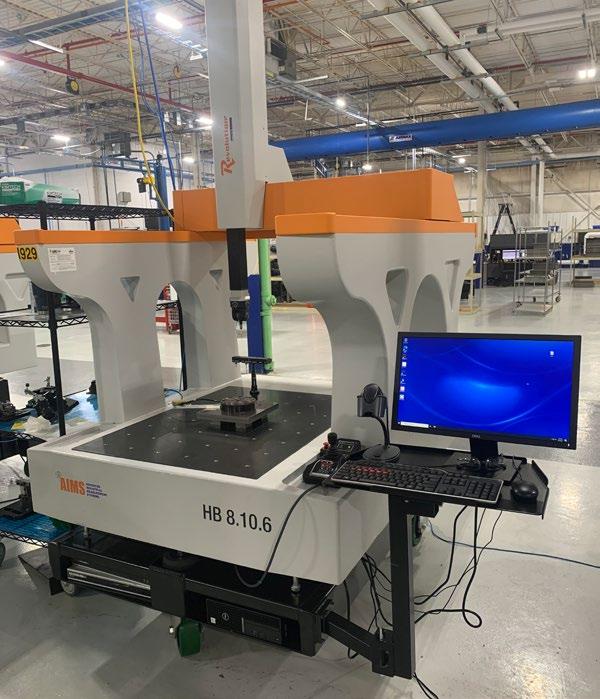
Raw material and labor shortages and the need to understand what is happening on the shop floor at any given moment, mean fabricators can’t afford to run 20 or 30 parts before the first part is inspected.

“We’re seeing more and more applications where a turnkey system from a support perspective is the best solution,” Gearding says. “Our 5-axis CMMs coupled with the right software package are helping job shops and fabricators implement an Industrial Internet of Things model where integrated measurement technology can effectively contribute to more efficient manufacturing processes through connectivity. Multisensor inspection requirements will continue to grow in order to adapt to ongoing product changes. We are one of the few OEMs that can provide a true shop floor turnkey package along with the service and support.”
Treat. Cure. Clean. Repeat…With Baldwin
Baldwin Technology Company Inc. — a one-stop source for high-performance treating, cleaning, curing, coating and inspection solutions — introduced a groundbreaking solution that makes maintenance and cleaning of its pioneering corona surface treatment technology easier than ever at ICE Europe 2023.

Baldwin provides printers, converters and manufacturers with expertise and a broad range of market-leading innovations that offer superior results and enhance the economic and environmental efficiency of production processes. Solutions on display at ICE included corona surface treatment systems, automated cylinder cleaning systems, LED-UV curing, roto-spray systems, and technologies for color management and defect detection. Common to all the technologies is that they increase productivity, reduce waste, improve working conditions and provide full control of producing flawless products. With easy automation and compatible software, Baldwin’s technologies are seamlessly integrated with one another. By stacking their tech with Baldwin, converters can compound the benefits of Baldwin’s solutions and achieve superior results.
Baldwin will be showcasing the “Easy Change” feature for its corona treatment systems, which allows for a seamless replacing of electrodes and a rapid cleaning and removal of fiber and dust residues. Easy Change results in a complete cleaning in just seconds, reducing downtime to a minimum. Cleaning with Easy Change does not require a special skill set or tools – anyone can do it!
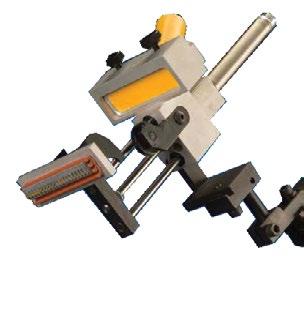
“We provide tailor-made corona treatment systems perfectly adapted for each converting process,” said Baldwin Technology product manager alexander Rau. “The new Easy Change feature makes the process efficient and smooth, and our operators have never been happier.” also at ICE, Baldwin featured its automated FilmCylinderCleaner™, which consistently and efficiently cleans debris from the surface of process cylinders, ending the need for hand-cleaning. By automating this process, film extruders avoid stopping the line for debris buildup on the cylinder surface, eliminating restart waste and web-breaks, and dramatically increasing operator safety. By enabling shorter production changes, the FilmCylinderCleaner increases output and efficiency, while improving quality.
“Customers don’t want to clean these large cylinders by hand,” Matthias Knoch said. “The demands for a safer working environment, quality output, reduced downtime and increased production capacity are driving the industry to adopt automated solutions. Baldwin’s automated FilmCylinderCleaner is a proven, easy win that offers the added benefit of dramatically reducing the risk of damaging cylinder surfaces.”
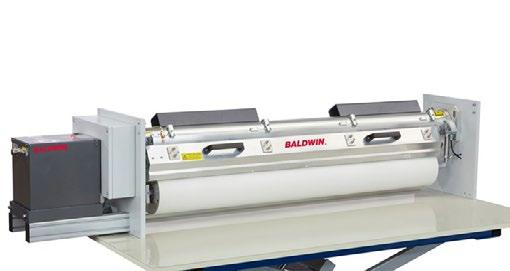
For more, visit baldwintech.com.
BIG DaISHOWa introduces MEGa 12DS power chuck for heavy-duty end milling a secure, jet-through coolant supply enables improved surface finish, smoother chip evacuation, extended tool life, and better cooling and lubrication of tools.
BIG DaISHOWa has announced a new addition to the MEG a DOUBLE POWER CHUCK lineup for heavy-duty end milling: the MEG a 12DS. Designed for trochoidal milling with anti-vibration end mills, the MEG a 12DS series features high rigidity and gripping strength and is available in BBT30/40, HSK-a , C for metric and BCV40 for inch.
The Mega Double Power Chuck system features an expanded contact diameter of the nut to the flange, which provides the highest rigidity—as if the chuck and nut were one solid piece. This superior rigidity ensures heavy duty machining without chatter.
The MEG a Series high-speed milling chucks are precision ground and balanced, with all components specifically designed for high-speed applications. Like the full MEG a DOUBLE POWER CHUCK lineup, the new MEG a 12DS series enables max of 30,000 RPM.
CaPTURE 3D Increases Throughput and Productivity
with the New Modular ZEISS ScanBox Series 5 for automated Quality Control
The ZEISS ScanBox Series 5 is a collection of turn-key intelligent 3D scanning and inspection robotic solutions designed to adapt to the changing needs of modern industrial environments
CaPTURE 3D, a ZEISS company and the leading provider of innovative 3D digitizing solutions in the U.S., announced the ZEISS ScanBox Series 5 — the latest addition to its collection of automated 3D scanning and inspection solutions designed and developed for industrial environments. The new series replaces the former proven and successful ScanBox Series 5 models with further enhanced optical 3D measuring machines featuring a modular concept designed to meet the demands of modern production, such as a new faster robot module for increased scanning speed, an integrated control tower for greater efficiency, a rotation table with a load capacity of up to two tons, and modular components for an adaptable floorplan layout.
Developing a reliable automation strategy continues to be a critical success factor for modern manufacturers to meet the demands of the changing landscape while improving quality control and dimensional inspection, whether near-line, at-line, or in-line production. The ZEISS ScanBox Series 5 solves this need with its aTOS 5 high-speed 3D sensor compatibility and an easy-to-program and operate interface to program complex measurements with the touch of a button.
“In today’s manufacturing environment, having the right automation strategy is key to increasing throughput and productivity while minimizing costs. The ZEISS ScanBox Series 5 capitalizes on strengths that already have made the series part of our customers’ success while upgrading essential features to deliver an automated solution that saves companies time and money,” said C aPTURE 3D General Manager Richard White.
The new model series consists of three off-the-shelf versions for different part or tooling size requirements: ZEISS ScanBox 5110, ZEISS ScanBox 5120, and ZEISS ScanBox 5130. The previous ScanBox Series 5 solutions are widely used within the aerospace, automotive, consumer goods, medical, and power generation industries to digitize and inspect parts ranging from turbine blades, knee implants, injection molded components, assemblies, and automotive sheet metal panels, to aerospace structures.
Meets the ScanBox Standard: Integration of Hardware and Software for Full Automation
ZEISS ScanBox Series 5 features the aTOS 5 blue light 3D scanner for the fast digitalization of various complex parts such as plastics, metals, or castings. The automated solution offers two entrance options to fit the user’s unique needs. The robot module consists of a FaNUC M20iD/25 robotic arm secured on a floor mount. Users with little to no robotics experience can easily plan and program measuring sequences using the Virtual Measuring Room (VMR) software module. By programming the measuring routine within the VMR, the robot intuitively moves the aTOS 5 sensor to optimal scanning positions, enabling the fully automated execution of measurement sequences. after importing the CaD data and the corresponding measurement plan, the software computes the required sensor positions and robot paths. With a complete, detailed geometric digital twin of the physical part, users can compare the data against the CaD model and visualize GD&T deviations and details like trimming and hole positions. Users can display inspection results in a comprehensive report with images, tables, diagrams, texts and graphics for detailed trend/SPC analysis.
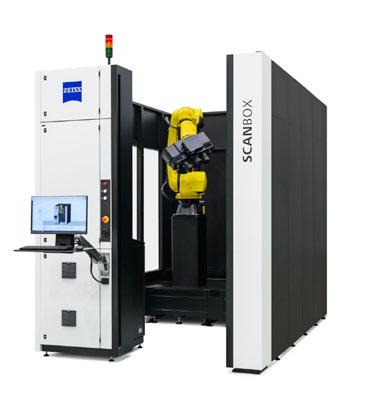
Modular Concept Adapts to Changing Customer Needs
The control tower, rotation table and robot modules are identical across each ZEISS ScanBox Series 5 model, allowing users to expand the layout by adding additional working areas or components as needs change. The entrance of the 5110 and 5120 models can be equipped with either a door or a safety light curtain. The 5130 model is always supplied with a safety light curtain to accommodate larger test components, such as automotive sheet metal closures. a pallet loading system can supplement the ZEISS ScanBox 5120 and 5130 models. Positioning pins enable the fast and reproducible loading of pallets for increased throughput.
Ergonomically Optimized Features
The operator station includes a new variable swivel arm incorporated into the control tower. The swivel arm allows the user to adjust the table height to operate the automated 3D scanning solution either sitting or standing.
ZEISS ScanBox Series 5 is available now through C aPTURE 3D. For more information or to schedule a demo, visit: www.capture3d.com
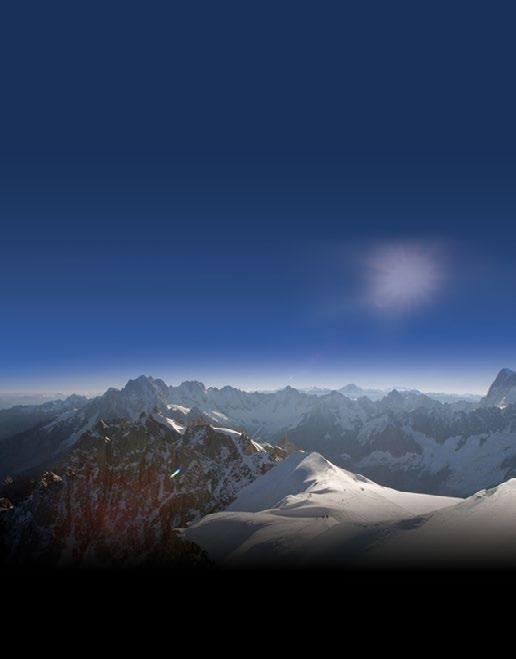
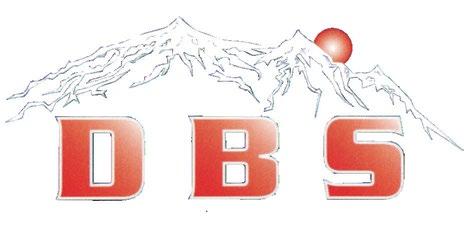
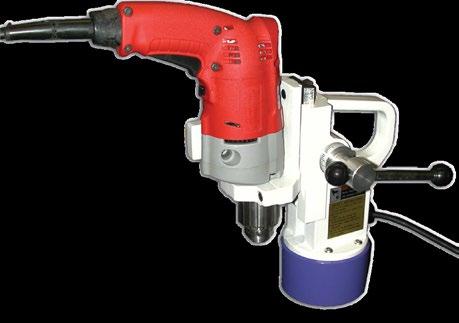
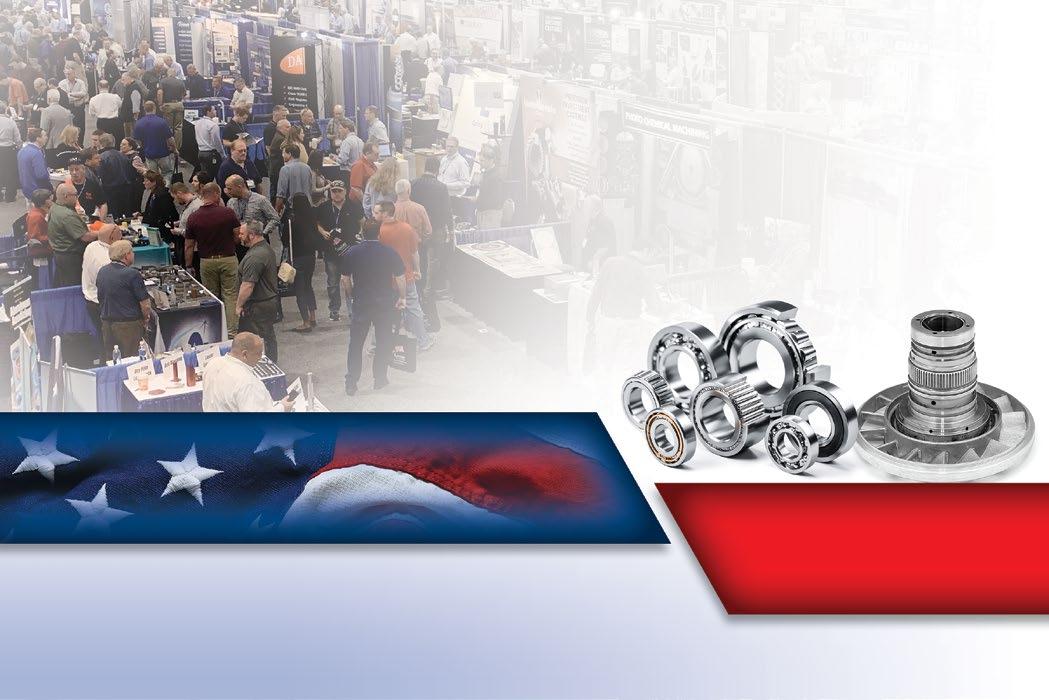

ENM’s PT16F is a LCD tachometer and hour meter combination with extra functions such as a job timer, service timer, and ability to set various firing patterns. The meter also keep track of the maximum RPM which can help in early detection of issue with engine. The unit has an IP67 rating which will protect against dust and water and will work in various environments
ENM’s PT16F is a LCD tachometer and hour meter combination with extra functions such as a job timer, service timer, and ability to set various firing patterns. The meter also keep track of the maximum RPM which can help in early detection of issue with engine. The unit has an IP67 rating which will protect against dust and water and will work in various environments.
LCD TACH/HOUR METER PT16 SERIES
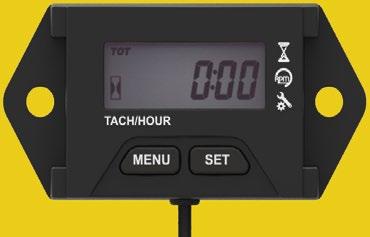


ENM’s PT16F is a LCD tachometer and hour meter combination with extra functions such as a job timer, service timer, and ability to set various firing patterns. The meter also keep track of the maximum RPM which can help in early detection of issue with engine The unit has an IP67 rating which will protect against dust and water and will work in various environments
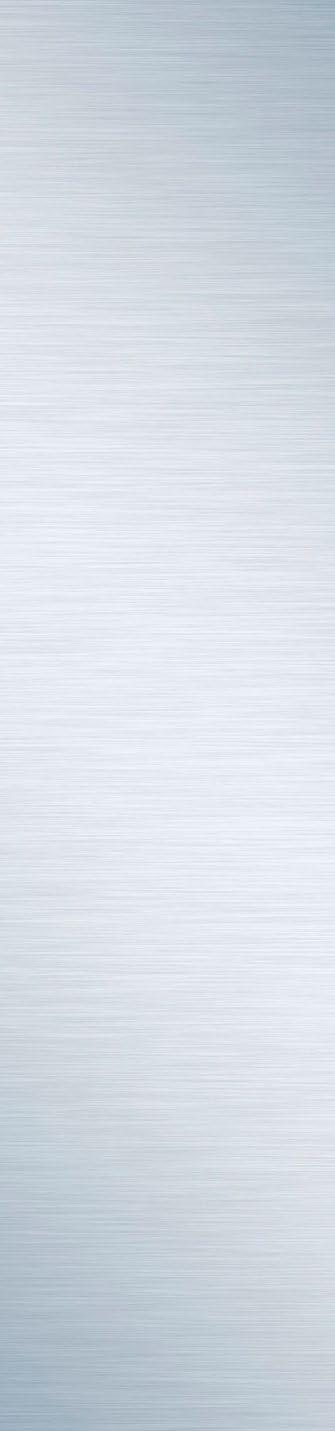
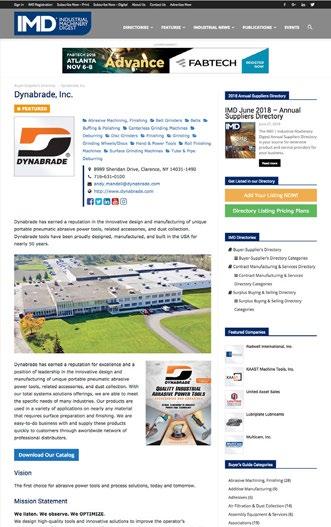
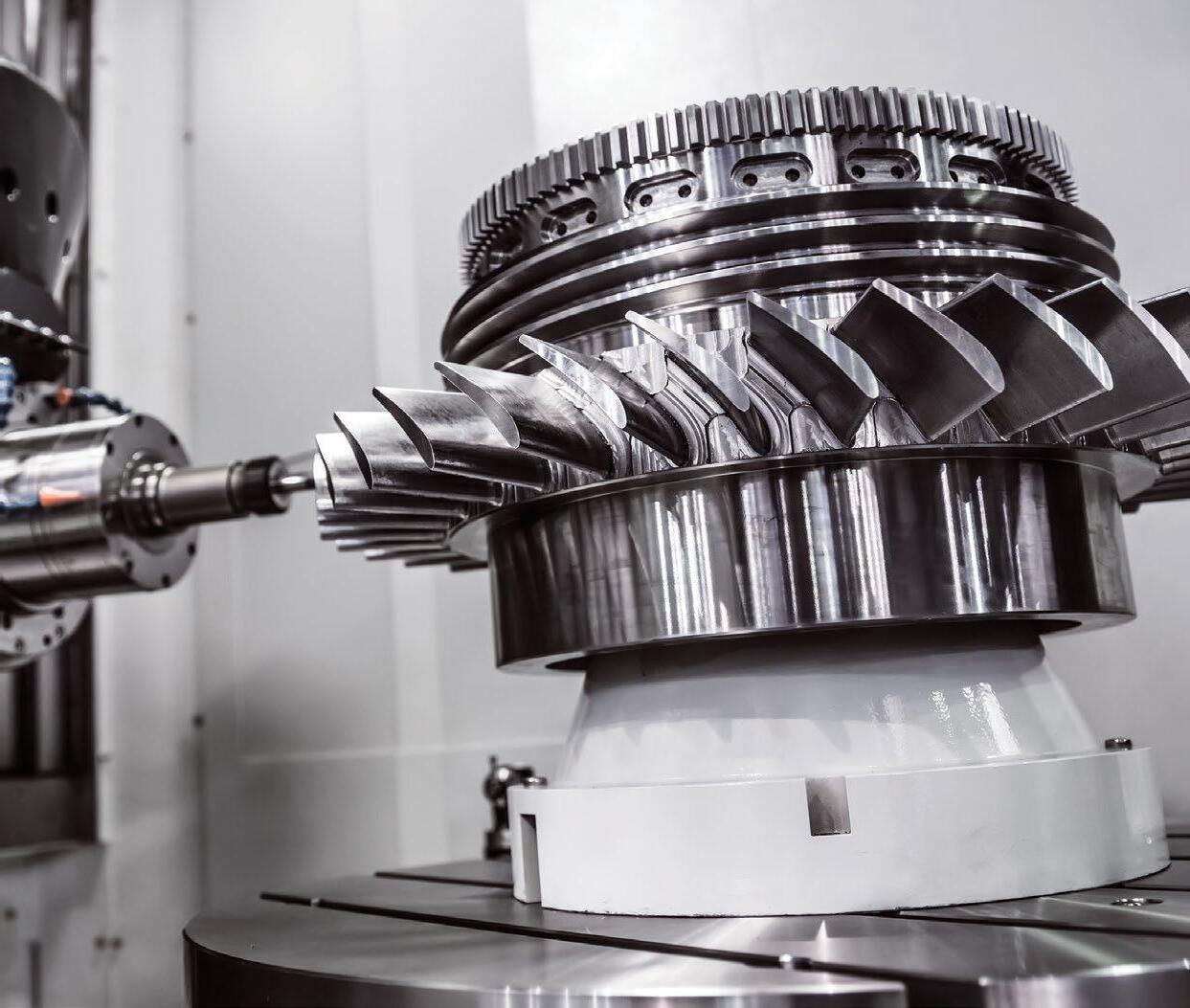