
7 minute read
OILGEAR HYDRAULIC PRODUCTS
AXIAL PISTON PUMPS… Oilgear open loop axial piston pumps are offered in a variety of models and displacement sizes to match required performance. Models include both medium and high horsepower, medium and heavy duty, low viscosity pumps, plus a series of multiple fixed delivery pumps. Of the many industries Oilgear serves, a primary one is mobile and off-highway applications. Oilgear pumps are recognized for high performance in the toughest environments. Their heavy duty designs resist contamination as well as operating on low viscosity specialty fluids.
VARIABLE PUMPS…
Whatever the application, Oilgear has the ideal pump to fulfill the requirements.
MULTIPLE FIXED DELIVERY CHECK VALVE PUMPS…
• High pressure to 15,000 psi
• Heavy duty construction
• High contamination tolerance
• Operation on low viscosity fluids
• Multiple deliveries up to three displacements from a single pump and reducing costs, AI can help manufacturers to stay competitive in a globalized market.
What is the difference between automation of equipment through code-driven decisions and AI use of equipment?
AI: The main difference between automation of equipment that has code-driven decisions and AI use of equipment is that code-driven decisions are based on pre-programmed instructions, while AI-powered decisions are based on machine learning and data analysis.
In code-driven automation, the equipment is programmed to make decisions based on a set of rules. For example, a robot may be programmed to pick up a part only if it is the correct size and shape. This type of automation is very efficient and can be used to perform repetitive tasks with high accuracy. However, it is not very flexible and cannot adapt to changes in the environment or the product being produced.
AI-powered automation, on the other hand, uses machine learning to learn from data and make decisions on its own. For example, an AI-powered robot may be able to learn to pick up different types of parts, even if they are not the same size or shape. This type of automation is more flexible and can adapt to changes in the environment or the product being produced. However, it is also more complex and requires more data to train.
In general, code-driven automation is a good choice for tasks that are repetitive and do not require a lot of flexibility. AI-powered automation is a good choice for tasks that are more complex and require the ability to adapt to changes.
Here are some examples of how code-driven automation and AI-powered automation are used in manufacturing:
Code-driven automation:
» A robot that is programmed to pick up a part only if it is the correct size and shape.
» A machine that is programmed to weld two pieces of metal together.
» A conveyor belt that is programmed to move products from one station to another.
AI-powered automation:
» A robot that can learn to pick up different types of parts, even if they are not the same size or shape.
» A machine that can learn to adjust its settings to produce different products.
» A system that can predict when equipment is likely to fail and take preventive action.
As AI technology continues to develop, we can expect to see more and more AI-powered automation in manufacturing. AI has the potential to make manufacturing more efficient, productive, and competitive.
What is your view on Industry 5.0 and how is it being deployed?
AI: Industry 5.0 is the fifth industrial revolution, which is characterized by the integration of artificial intelligence (AI), the Internet of Things (IoT), and other advanced technologies into manufacturing processes. The goal of Industry 5.0 is to create more intelligent, flexible, and sustainable manufacturing systems.
There are a number of ways that Industry 5.0 is being deployed. One way is through the use of smart factories. Smart factories use AI, IoT, and other technologies to collect and analyze data from machines and equipment. This data can then be used to improve production efficiency, quality, and sustainability.
Another way that Industry 5.0 is being deployed is through the use of collaborative robots. Collaborative robots, also known as cobots, are robots that can work safely alongside humans. Cobots can be used to automate tasks that are dangerous or repetitive, freeing up human workers to focus on more creative and strategic tasks. Industry 5.0 is still in its early stages, but it has the potential to revolutionize manufacturing. By integrating AI, IoT, and other advanced technologies, manufacturers can create more intelligent, flexible, and sustainable manufacturing systems. This can lead to increased productivity, improved quality, and reduced costs. Here are some specific examples of how Industry 5.0 is being deployed:
» Siemens: Siemens is a German multinational conglomerate that specializes in the production of industrial machinery and electronics. Siemens has been a pioneer in the development of Industry 5.0, and it has deployed a number of Industry 5.0 solutions in its own factories. For example, Siemens has deployed a smart factory in its wind turbine manufacturing plant in Denmark. The smart factory uses AI, IoT, and other technologies to collect and analyze data from machines and equipment. This data is then used to improve production efficiency, quality, and sustainability.
» General Electric: General Electric is an American multinational conglomerate that specializes in the production of aircraft engines, medical equipment, and power generation equipment. GE has been a major investor in Industry 5.0, and it has deployed a number of Industry 5.0 solutions in its own factories.
For example, GE has deployed a smart factory in its aircraft engine manufacturing plant in the united States. The smart factory uses AI, IoT, and other technologies to collect and analyze data from machines and equipment. This data is then used to improve production efficiency, quality, and sustainability.
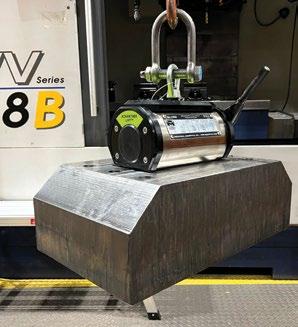
» Rockwell Automation: Rockwell Automation is an American multinational corporation that specializes in the production of industrial automation products and services. Rockwell Automation has been a leader in the development of Industry 5.0, and it offers a number of products and services that enable manufacturers to deploy Industry 5.0 solutions. For example, Rockwell Automation offers a suite of products and services that enable manufacturers to collect and analyze data from machines and equipment. This data can then be used to improve production efficiency, quality, and sustainability.
» Dassault Systèmes: Dassault Systèmes is a French multinational software company that specializes in the development of 3D design and engineering software. Dassault Systèmes has been a major investor in Industry 5.0, and it offers a number of products and services that enable manufacturers to deploy Industry 5.0 solutions. For example, Dassault Systèmes offers a suite of products and services that enable manufacturers to create digital twins of their products and processes. Digital twins can be used to simulate and optimize manufacturing processes, which can lead to increased productivity, improved quality, and reduced costs.
» PTC: PTC is an American multinational software company that specializes in the development of product lifecycle management (PlM) software. PTC has been a leader in the development of Industry 5.0, and it offers a number of products and services that enable manufacturers to deploy Industry 5.0 solutions. For example, PTC offers a suite of products and services that enable manufacturers to create digital twins of their products and processes. Digital twins can be used to simulate and optimize manufacturing processes, which can lead to increased productivity, improved quality, and reduced costs.
These are just a few of the many companies that are deploying Industry 5.0 solutions. As the field of Industry 5.0 continues to evolve, we can expect to see even more companies offering products and services that enable manufacturers to deploy Industry 5.0 solutions.
So you mentioned Digital Twin. What are the latest innovations in Digital Twin Simulation?
AI: Digital twins are virtual replicas of physical objects or systems that can be used to simulate their behavior and performance. They are increasingly being used in a wide range of industries, including manufacturing, healthcare, and energy.
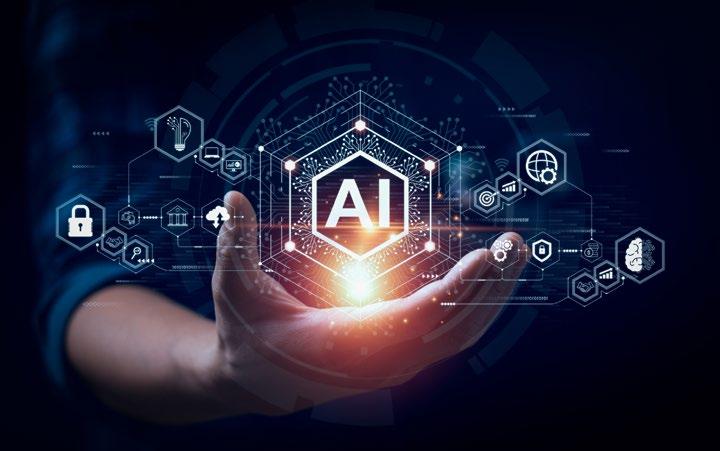
Here are some of the latest innovations in digital twin simulation:
» The use of artificial intelligence (AI) and machine learning (Ml): AI and Ml are being used to improve the accuracy and efficiency of digital twin simulations. For example, AI can be used to identify patterns in data that would be difficult for humans to see. Ml can be used to automate tasks such as data collection and analysis.
» The use of cloud computing: Cloud computing is making it easier and more affordable to create and maintain digital twin simulations. Cloud-based platforms provide access to powerful computing resources and large datasets.
» The use of open-source software: Open-source software is making it easier for businesses and organizations to create and use digital twin simulations. Open-source software is often free or low-cost, and it is available to anyone who wants to use it.
These are just some of the latest innovations in digital twin simulation. As the technology continues to develop, we can expect to see even more innovative and disruptive applications in this field.
Here are some specific examples of how digital twin simulation is being used today:
» Manufacturing: Digital twins are being used in manufacturing to improve product design, optimize production processes, and predict failures. For example, General Electric uses digital twins to simulate the performance of jet engines. This allows the company to identify potential problems before they occur, which can save the company money and improve the safety of its products.
» Healthcare: Digital twins are being used in healthcare to improve patient care, develop new treatments, and simulate the performance of medical devices. For example, the Mayo Clinic uses digital twins to simulate the behavior of the human heart. This allows the clinic to test new treatments and procedures without having to put patients at risk.
» Energy: Digital twins are being used in the energy industry to optimize power grids, improve the performance of power plants, and reduce energy consumption. For example, the Tennessee Valley Authority uses digital twins to simulate the performance of its power grid. This allows the company to identify potential problems and make changes to the grid before they cause outages.
These are just a few examples of how digital twin simulation is being used today. As the technology continues to develop, we can expect to see even more innovative and disruptive applications in this field. And then we were done. I’m sure AI was tired and so was I. Interestingly, the AI has a need for affirmation at the end of every topic response which seems very human, don’t you agree?