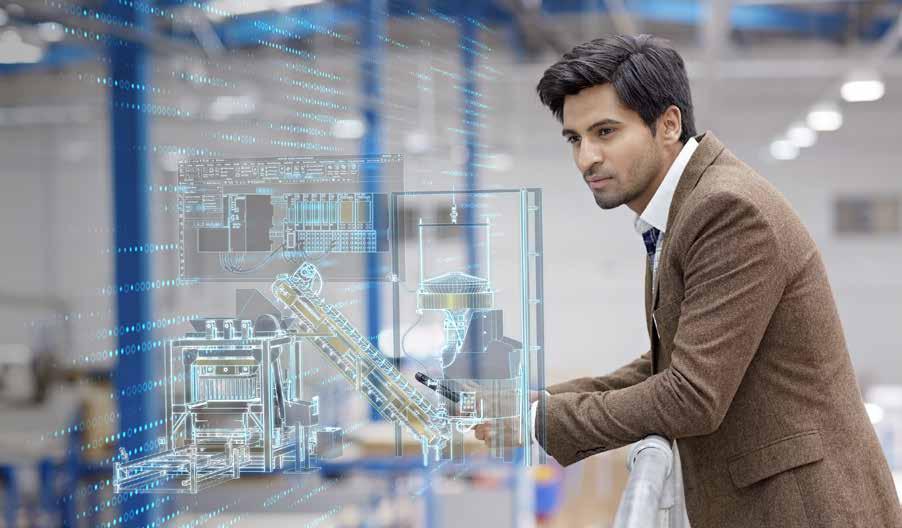
10 minute read
NEW TECH
What Is Advanced Machine Engineering?
Innovative technologies are rapidly advancing machine engineering processes, driving positive change in the industry, prompting companies of all sizes to meet the challenges and trends facing machinery manufacturers. These trends include consumer driven customization, resulting in smaller lot sizes and product life spans; smart machines that provide an order of magnitude increase in information flow; hyper automation that leverages vast amounts of data to automate machine functions; and global competition from more flexible, agile startups.
In response to these trends, advanced machine engineering (AME) has come to the fore in the past few years. It focuses on ensuring greater certainty in the development of next-generation machines by fostering collaboration among the multiple disciplines required to create today’s advanced machines. It also reduces ramp-up time to production through virtual design and commissioning, resulting in better upfront validation, shorter 28 |
commissioning times and more immediate productivity. Equally important, advanced capabilities are now available to manage the entire bill of materials for all options and variants for advance machine builder support throughout its product life, from the engineering design through manufacturing, and service life.
AME Key Differentiators Let’s examine each of these powerful capabilities that form AME’s essential differentiators that are positively impacting the machine industry.
Multi-disciplinary design – Today’s machines are no longer primarily a mechanical piece of equipment. Electrical motors and rotary equipment to move camshaft gears are driven by software and PLC codes, thus accelerating performance-based programs in recent years. The software is adaptable to conditions on the floor enabling the machine to react to real-time sensor readings. As more
mechanical capabilities and features are being replaced by software, machine designers must take into equal account the mechanical, electrical and fluids aspects of machine design.
Multi-disciplinary design encompasses the complexities of building a machine, including engineering the design and manufacturing. It creates a single source of truth in design to address the back-and-forth process that exist between engineering silos. Blending capabilities and skill sets in a more collaborative environment ensures quality output of the machine design – so everything works together and has its place. It is more of an art form than simply bolting on electrical, sensors and cable-runs. Since it is an integrated solution, it creates harmony in the multi-disciplinary design that did not exist when disciplines were in silos.
Virtual machine simulation and commissioning is the second differentiator provided by advanced machine engineering. This refers to how the machine proves itself or validates the software code in the virtual world before physically operating on the factory floor.
The behavior of the machines is being driven by software, which is why simulating the code running on a virtual twin of the machine generates substantial dividends in time and resources. With virtual commissioning, the PLC software validates in a managed environment with a full modular product development strategy. Now machine builders can have the simulation upfront and link the software to the modules. This set up is a groundbreaking achievement for companies to be competitive in this space.
dynex hydraulic products
high pressure checkball piston pumps… Dynex high pressure hydraulic pumps with positive-seating checkball valves provide better wear and high volumetric efficiency. Pumps operate at pressures to 20,000 psi. Checkball pumps are ideal for hydraulic systems with demanding conditions and accommodate more force in a smaller package. At lower pressures, they provide the life and performance margin essential in critical environments. Checkball fixed displacement pumps offer flows from 0.22 to 60 U.S. gpm at 1800 rpm. directional control valves… • HP Pattern Spool Valves — Simple spool valves eliminate complex valve circuits for fourway control in high pressure systems. HP03 pattern valves are rated for 15 U.S. gpm at 10,000 psi, HP05 pattern rated from 5 to 25 U.S. gpm at 8000 psi. • NFPA/ISO Pattern Valves — Smooth spool movement with fourland design offers low pressure drop with large internal flow passages. 5000 psi valves rated to 165 U.S. gpm. • VST Series Seated Valves — High pressure with low leakage.
Reliable shifting with non-silting ball-on-seat design. • Explosion Proof Option — Solenoids with special enclosures designed for use in hazardous locations. UL and CSA approved. • Accessory Sandwich Valves — Mounts under directional valves, saves space, reduces weight and provides flexibility locating valves.
7355 N. Lawndale Ave., PO Box 6, Skokie, IL 60076 Phone: 847-676-2910 Fax: 847-676-0365
Moreover, virtual simulation provides a physical safety aspect because if the machine collides in the virtual world, it is substantially safer and less costly to fix than on a physical machine. Virtual commissioning drives the behavior of the motors, integrating that into the kinematics. This is powerful because a mechanism on a machine might move faster than expected, leading to an actual impact load greater than what was anticipated. Replicating the kinematics in virtual commissioning uncovers potential hazards leading to a swift resolution.
Furthermore, by embracing virtual commissioning and visualization, machine builders bring customers into a virtual reality to interact with the machine in its digital form. From a financial perspective, this pays huge dividends because no one purchases a machine sight unseen. Also, they will not purchase it merely on a claim of virtually simulation via running software code. Therefore, a customer needs to substantiate that a machine works before it is shipped to their plant.
A prime example of virtual commissioning is Tronrud Engineering, who for more than 40 years have developed, produced and delivered innovative machines and equipment. A digital twin of the new machine allows their designers, engineers, and programmers to work simultaneously and continuously interact and share their knowledge. By implementing virtual commissioning and simulation, Tronrud Engineering has reduced their commissioning time up to 70 percent, while compressing their engineering time by 25 percent. A substantial benefit to their bottom line.
char-lynn hydraulic products
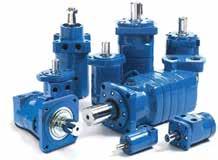
low speed high-torque motors… The Char-Lynn motor range consists of three major types based on the valving used to distribute fluid through the Orbit gear set (geroler or gerotor), Spool Valve, Disc Valve and VIS (Valve-in-Star). A variety of displacement sizes are available in each of the three motor types to provide a wide range of speeds and torques.
steering control units… offer these advantages: • Minimal steering linkage reduces cost, provides design flexibility. • Complete isolation of load forces from the control station. • Continuous, unlimited control action with low output torque. • Wide selection of control circuits and meter sizes. • Works with many kinds of power steering pumps or fluid supply.
gear pumps… Eaton Series 26 gear pumps with 13-tooth gears minimizes flow ripple to reduce noise and vibration. Bearing lubrication system uses inlet oil rather than high pressure oil, improving volumetric efficiency and power output. The 13 available displacements and many mounting configurations provide for an easy retrofit. Other series available.
7355 N. Lawndale Ave., PO Box 6, Skokie, IL 60076 Phone: 847-676-2910 Fax: 847-676-0365
Multi-disciplinary BOM and configuration management – A third differentiator of advanced machine engineering is the multidisciplinary bill of materials (BOM) for machine builders as they create more sophisticated, smart machines. It gives manufacturers greater flexibility to respond to customer demands for customization, as most modern machines are configured-to-order.
Every machine, and every order, that a machine builder receives is often a new project. Consequently, machine builders need a way to track the diverse options, and variants, for integrating requirements along with project and change management, while managing the entire BOM throughout the product life. From the original engineering design, through manufacturing and then managing that machine bill of materials throughout its service life.
A level of planning capability is required for each engineering discipline, providing a more agile approach. Also, there is a need for traceability of customer requirements, engineering requirements and activity that is performed by the mechanical design engineer, electrical engineer and controls engineer for executing the project. This includes the journey from a high-level customer requirements specification document through the BOM structure and attaching it to the actual task that is necessary for the deliverable.
This process provides a level of capability for ensuring and reducing the risk in meeting customer requirements, enabling sophisticated software solutions that are implemented into every machine.
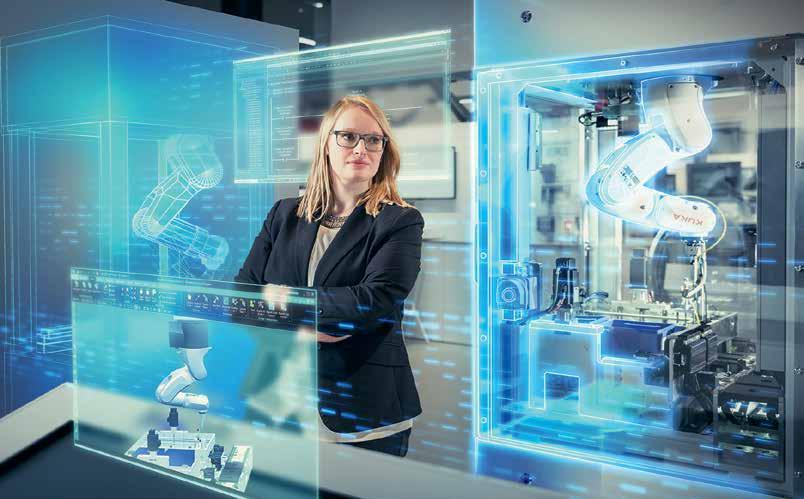
Smarter Machines, Smarter Code, Smarter Software Advanced software is a necessity for machine manufacturers facing competitive globalization, shrinking margins, rapidly expanding customization, environmental and government regulations, as well as Industry 4.0 and other smart factory initiatives. In the face of these significant challenges, machines must be smarter.
The core requirement includes machine design innovation in the operation and development process. Being good versus great depends on the quality and innovation in the automation code. Having great code provides intuitive user interfaces, promoting ease of use and taking advantage of new hardware capabilities. It’s using software algorithms to help machines move faster, more safely with less physical stress on components.
However, having well-written code is not good enough.
Current machines have enormous complexity in the lines of code. It is critical to test that code in a virtual world, running it through all use cases before loading it on a physical machine. Companies are under pressure to deliver highly customized machines rapidly, with added complexity. It’s no longer possible to rely on, and safely physically validate the machine.
Every machine is released to the customer with a set of binaries representing the compiled machine operation and user interface code. With conventional practices, programmers scramble to get last-minute changes to the code locked in before the machine ships. In this chaotic environment, it is imperative to retain a locked version
of the final code to use for several purposes – service, catastrophic backup, lessons learned for future machines and upgrades to previous machines in the field.
Therefore, having a code repository is not enough. Each software variant must be traceable and retrievable via the serial number for the machine bill of materials. A machine’s life needs traceable records of all upgrades in hardware and software representing the machines’ living digital twin.
Advanced Machine Engineering Moving Forward Advanced machine engineering solutions are emerging that address the challenges and trends facing the machinery industry. These include multi-discipline design, virtual machine simulation and commissioning and multi-disciplinary BOM and configuration management. The Xcelerator portfolio in Siemens Digital Industries Software suite of products provides a full suite of solutions to empower machine builders and suppliers with the essential tools to compete successfully, helping industrial machinery companies to transition seamlessly to create tomorrow’s complex, efficient machines.
ABOUT THE AUTHOR:
Bill Davis is the acting Industrial Machinery and Heavy Equipment Industry leader for Siemens Digital Industries Software. His experience and insights have been acquired from a career spanning 30 years in engineering and operations management with machinery and heavy equipment companies. Bill holds a master’s degree in Business Administration from Marquette University, with a concentration in Operations Management and Strategic Marketing, as well as a Bachelor of Science degree in Mechanical Engineering from Milwaukee School of Engineering.
IF YOU HAVE AN EDGE… WE HAVE A TRIM!

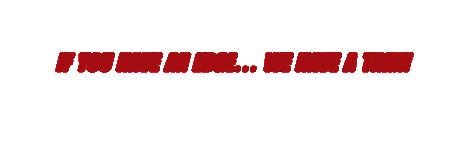
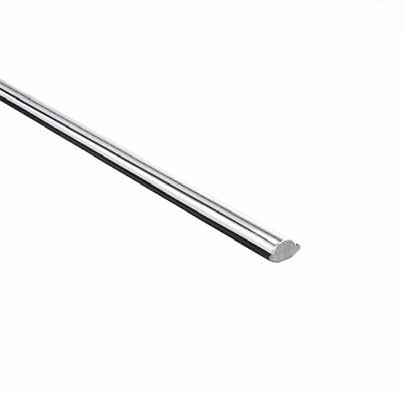
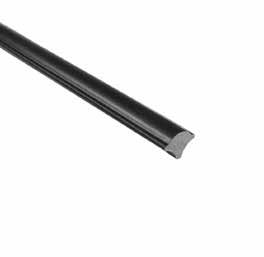
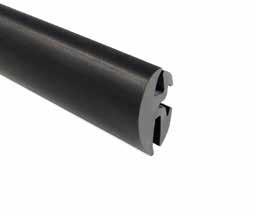

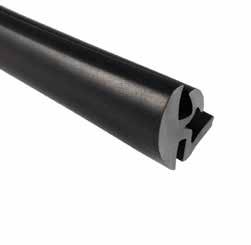
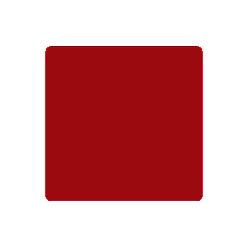
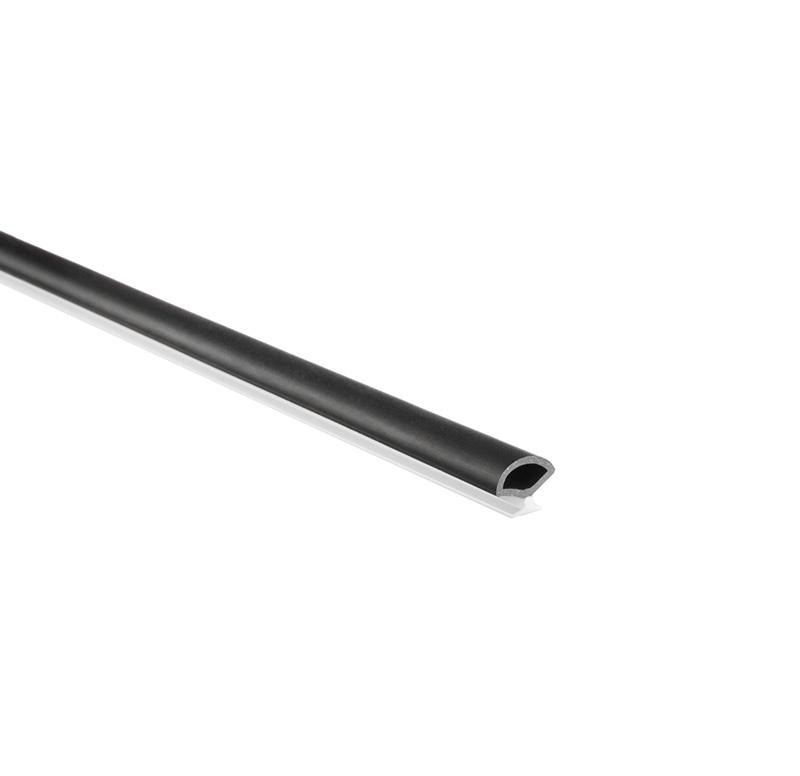
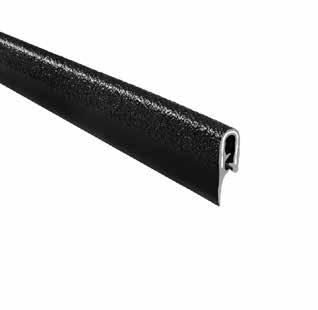
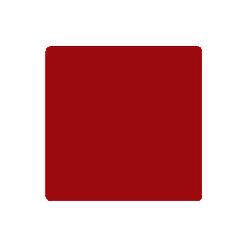
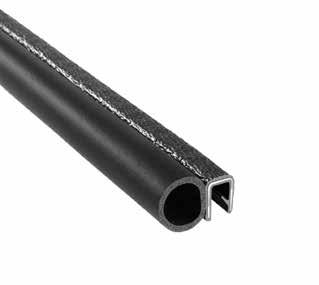

FREE SAMPLES FREE CATALOG Test Our Trims and Seals for Quickly View Our Most Popular
Fit and Function Lines of Trims and Seals DESIGN ASSISTANCE Let Us Help You Find the Right Trims and Seals
Same Day Shipping on Thousands of Parts
CALL US TODAY! 800-663-9507

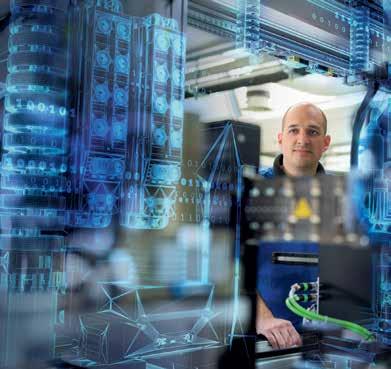
HEADQUARTERS 6855 HERMOSA CIRCLE BUENA PARK, CALIFORNIA 90622
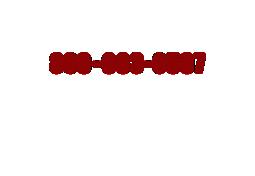
MIDWEST MANUFACTURING 1642 GATEWAY COURT ELKHART, INDIANA 46514