
9 minute read
WORKFORCE DEVELOPMENT
ZOLLER Inc.
By Russ Willcutt
ZOLLER was founded just outside of Stuttgart, Germany in 1945. Alfred Zoller realized that recovering from the devastation of World War II would require a great deal of remanufacturing, repairs, and re-engineering involving everything from household appliances to automotive parts. The company developed and manufactured its first presetter in 1963, which quickly gained market acceptance throughout Europe and soon accompanied the machine tools that were sold into the United States, paving the way for ZOLLER to establish its North American headquarter in Ann Arbor, Michigan, in 1997, led by Alexander Zoller. It is now a thirdgeneration family-owned global enterprise.
Recognizing the need to be near its customers, wherever they are located, ZOLLER has 20 dedicated facilities providing service and stocking parts around the world. Along with a mix of authorized distributors and sales agents, it enjoys a global footprint, always sensitive to the societal expectations that might call for a locally based staff familiar with the surrounding dialect and customs. According to Dietmar Moll, director of business development, automation, and smart factory solutions, the company has four distinct product lines. “Tool Presetting is our number-one category, especially since it was really the basis of our original

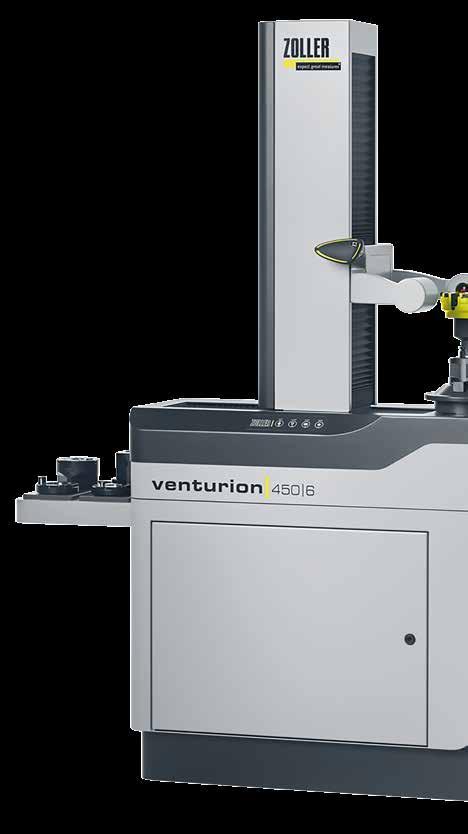
product lineup,” he says. “We offer both vertical and horizontal devices, and more than 45,000 have currently been sold around the world. Then there is Inspection and Measuring, with categories including universal measuring machines, process-oriented measurement, and Automation Solutions.”
The fourth category, Tool Management, has existed for quite some time in the form of storage solutions for tool rooms, but the advent of automation, AI, and sophisticated software has ramped up advances within this area, making it ripe for R&D investments and industrial collaboration, particularly with machine too OEMs and cutting tool manufacturing. Tool Management systems have evolved to the point where manual loading can be held to an absolute minimum, with all tool monitoring, replacement, and mounting handled automatically by these precise, integrated systems. Automation has also been developed to handle other “non-valueadded” procedures such as tool delivery to a machine’s work area, providing ergonomic benefits, and process streamlining.

Describing ZOLLER as “a customer-centric” company, Rita Conroy-Martin, director of marketing, says educational resources are constantly in development, and while live events do still occur, the coronavirus has made the importance of digital interaction apparent. “The ZOLLER Training Academy, headed up by Michael Stepke, offers both live and virtual training seminars to current and potential customers, and we also host webinars that are then archived online. We collaborate with our sales team, who work on the front lines alongside our customers, to develop content for these webinars based on end-user comments. This allows us to address their concerns directly, to keep our content fresh, and also to pick up on pointers that we can utilize to improve our own technologies.”
Conroy-Martin adds that, with the company marking its 75th anniversary, it will be kicking off the celebration by hosting a three-day online live event from September 15-17, 2020, that will be broadcast from its headquarters in Ann Arbor. The event will be rife with educational content and special promotions while also underlining an important message.
“We want to emphasize that in addition to being the largest manufacturer of presetters in the world, we have evolved into a solutions-based company across the entire spectrum of cutting tools,” according to Moll. “Our upcoming celebration will be an opportunity for us to demonstrate how that has been achieved.”
For more information go to zoller.info/us.

Knowledge Is Power
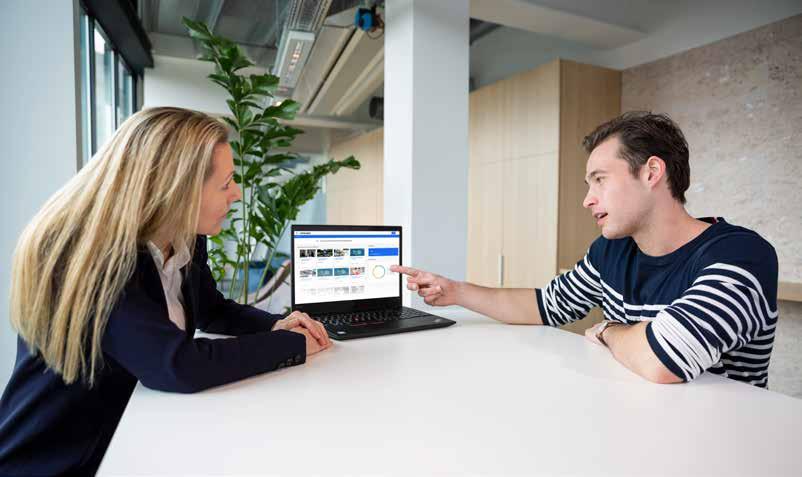
Overcoming 3D Printing Barriers to Adoption
By: Greg Elfering, President of Ultimaker Americas
Over the past six months, every industry in the world has been impacted in some capacity by the COVID-19 pandemic. Standard operating procedures and 2020 projections were quickly scrapped as companies realized they were operating on a new playing field that has never been traversed or even imagined. Through all the hardship and adaptation businesses faced, there was one clear lesson to be learned; organizations must accelerate their utilization and investment in their digital transformation plans. Specifically, those in manufacturing realized the previously stable global supply chains and operations could actually be overpowered by the unknown. Meanwhile, many other businesses and medical organizations were caught off guard, a beacon of support made its way to the forefront: 3D printing.
While the world watched as the 3D printing community rushed to the aid of hospitals across the country to help supply them with essential personal protective equipment, other businesses realized the versatility of additive manufacturing. Not only were hospitals able to become more self-sufficient as they shortened supply 22 |
chains, but they also saw flexibility in production and ease of access. As a result they were able they were able to print millions of copies of personal protective equipment during the pandemic to fix the shortages that were running rampant in healthcare organizations across the country. Due to the pandemic, Forbes predicts that over the next 18 months, manufacturing will experience five years’ worth of innovation. 3D printing technology is a key component of this trend, and as we move forward, companies will need to consider both hardware and software solutions as well as education of the technology to deliver tangible results in a shorter time than what they currently experience.
Knowledge Gap Remains a Key Barrier to Entry Although this technology is primed and ready to be widely adopted across a wide variety of industries, its biggest obstacle is a lack of knowledge. According to the 3D Printing Sentiment Index, a survey of professionals across industries, two-thirds of US businesses that could potentially benefit from 3D printing do not use the technology at all, while only one in ten believe that they have progressed to a
mature stage in their implementation of the technology. In fact, 69 percent of the professionals surveyed cited knowledge as the most frequent barrier to enter the market. Of those professionals, 40 percent also brought up a lack of necessary skillsets to properly leverage 3D printing. Lastly, just 16 percent of professionals said they would describe their level of knowledge regarding this technology as advanced or expert - demonstrating that the greater majority think their understanding is basic or rudimentary.
The Role of Software In Bridging the Gap While those statistics might sound daunting, what they really demonstrate is a massive opportunity for growth. Businesses have already begun capitalizing on the opportunity but so many are still unsure of where to begin. The knowledge around 3D printing is attainable, but in general, most do not know where to go to seek information. Fortunately, companies in this sector are geared towards accelerating the world’s transition towards global digital manufacturing and making their resources accessible to those who would like to learn more. Software offerings for 3D printing provide an ecosystem that enables organizations to print the exact parts they need, when they need it, and where they need it, which allows them to capitalize on their return on investment.
Any company that is considering 3D printing should be well equipped with the necessary information and tools. With software, hardware, and materials working together effectively, users can ramp up quickly and streamline processes efficiently. 24 |

One of the key aspects of beginning a proper 3D printing operation is the software. For example, Ultimaker’s 3D printing software, Cura, can be utilized to prepare CAD for 3D printing. Cura is open-sourced, meaning that it is available to third-party users and individuals as well as those who already have an Ultimaker printer. Users can download free software like this to gain a better understanding of the technology behind 3D printing. Developed as easy to use software, both experienced and novice 3D printers can take advantage of the offerings to prepare 3D models for print within minutes. To help novice makers understand this technology better, the software has built-in tools and tips to assist with features that would usually require in-depth technical knowledge.
While the open-sourced software is able to put the technology in the hands of the end-users allowing them to test the capabilities of themselves and the ability of the 3D printing technology, there are still other educational opportunities that can help close the knowledge gap. To help businesses uncover how 3D printing can benefit their business now and in the future, Ultimaker launched the 3D Printing Academy. These eLearning modules are designed to bring any level employee up to speed for any sort of role or responsibility in the growing 3D printing market. With role-specific courses, users will be able to train and develop deep knowledge and skillsets that immediately impact their day to day efforts. Additionally, all of the courses have remote learning capabilities so those who enroll do not need to physically be on-site to receive their education.
Recently released Ultimaker Essentials, an enterprise IT solution to overcome barriers in additive manufacturing, comes with three additional eLearning courses. Those who adopt 3D printing often learn to produce only one item and do not realize the full capabilities of the technology. The Academy lessons were launched in an effort to educate people and foster their development in the 3D printing space to the point where they can become a certified maker and scale up the technology in their own organizations. Users can collaborate, iterate, and innovate faster than ever before so their organizations can overcome real-time challenges faced every day.
If companies did not already realize that global supply chains and manufacturing workflows could easily be disrupted, the pandemic surely made them recognize this potential issue. The transition to digital distribution and local manufacturing is Modex 8in x 4.75in Ad Amanda.pdf 1 13/02/2020 17:33 imminent and 3D printing companies are focused on increasing

education across potential users. Removing the final barriers and gaps of knowledge will help companies unlock the full potential that 3D printing provides. With both software that provides millions with the opportunity to openly work on projects and eLearning courses to strengthen the knowledge of users, the time for greater 3D adoption is now.
For more information, visit www.ultimaker.com
SAFETY | STORAGE | EFFICIENCY 877-COMBI-56 COMBILIFT.COM
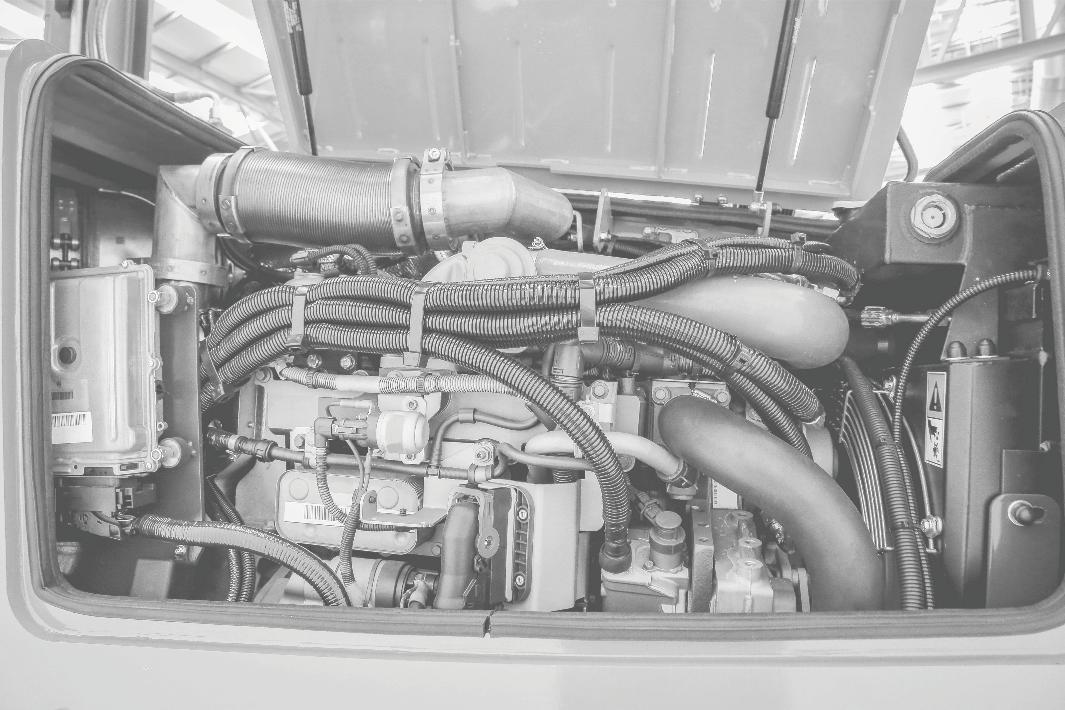
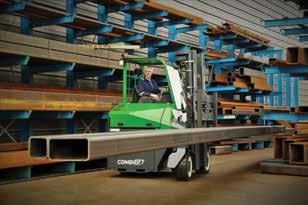
Save up to 100% more storage Before you invest in upgrading the infrastructure of your warehouse find out how Combilift could dramatically increase storage, improve productivity and enhance safety. Our warehouse design consultancy service is FREE and without obligation. When combined with our material handling products we can deliver possible space savings of up to 100%. So contact us today to arrange a virtual site survey!
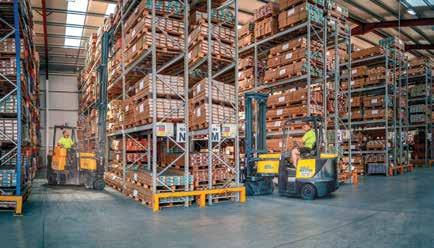

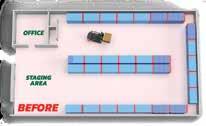
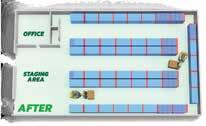